炼油工艺技术总结.docx
《炼油工艺技术总结.docx》由会员分享,可在线阅读,更多相关《炼油工艺技术总结.docx(22页珍藏版)》请在冰豆网上搜索。
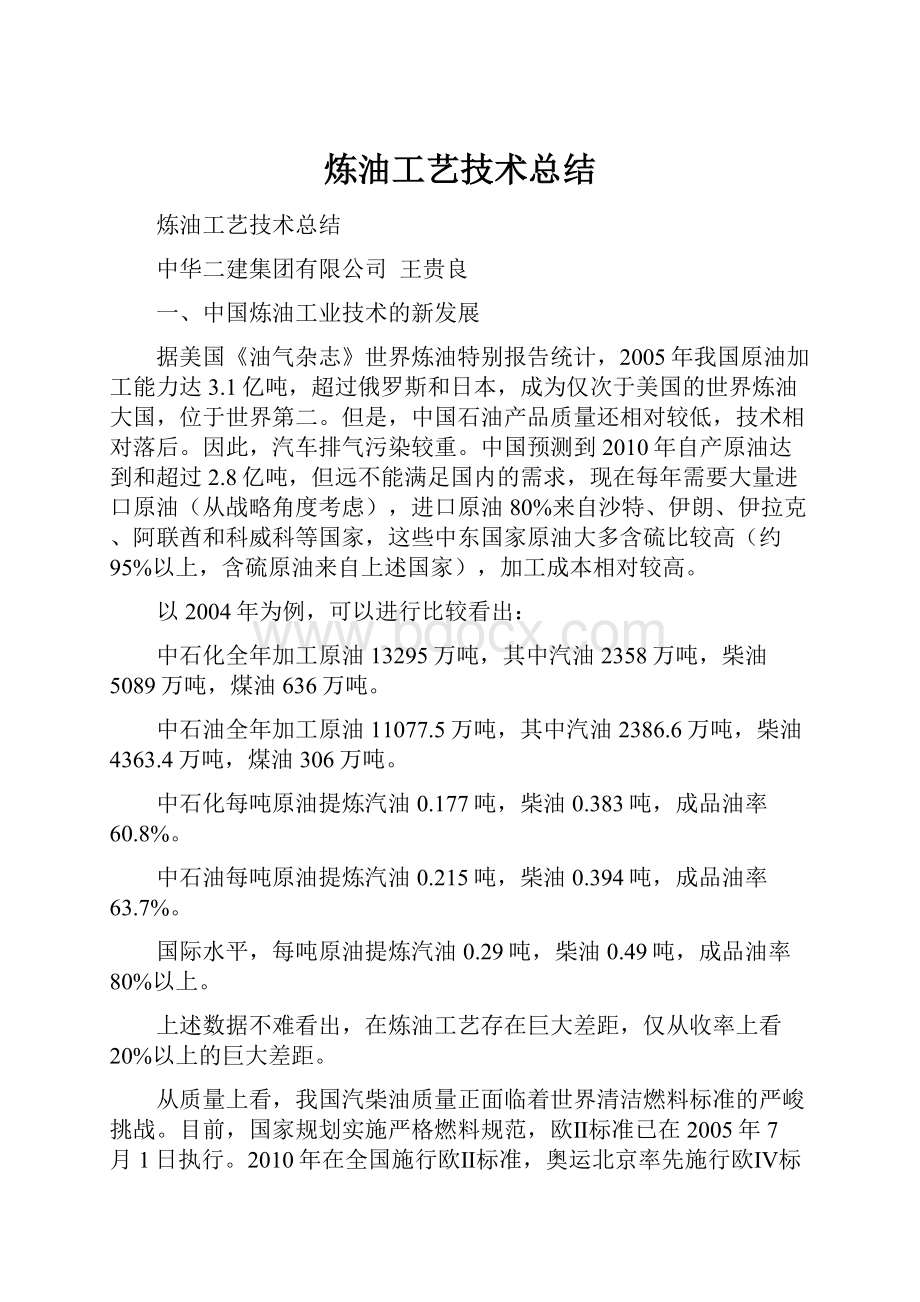
炼油工艺技术总结
炼油工艺技术总结
中华二建集团有限公司王贵良
一、中国炼油工业技术的新发展
据美国《油气杂志》世界炼油特别报告统计,2005年我国原油加工能力达3.1亿吨,超过俄罗斯和日本,成为仅次于美国的世界炼油大国,位于世界第二。
但是,中国石油产品质量还相对较低,技术相对落后。
因此,汽车排气污染较重。
中国预测到2010年自产原油达到和超过2.8亿吨,但远不能满足国内的需求,现在每年需要大量进口原油(从战略角度考虑),进口原油80%来自沙特、伊朗、伊拉克、阿联酋和科威科等国家,这些中东国家原油大多含硫比较高(约95%以上,含硫原油来自上述国家),加工成本相对较高。
以2004年为例,可以进行比较看出:
中石化全年加工原油13295万吨,其中汽油2358万吨,柴油5089万吨,煤油636万吨。
中石油全年加工原油11077.5万吨,其中汽油2386.6万吨,柴油4363.4万吨,煤油306万吨。
中石化每吨原油提炼汽油0.177吨,柴油0.383吨,成品油率60.8%。
中石油每吨原油提炼汽油0.215吨,柴油0.394吨,成品油率63.7%。
国际水平,每吨原油提炼汽油0.29吨,柴油0.49吨,成品油率80%以上。
上述数据不难看出,在炼油工艺存在巨大差距,仅从收率上看20%以上的巨大差距。
从质量上看,我国汽柴油质量正面临着世界清洁燃料标准的严峻挑战。
目前,国家规划实施严格燃料规范,欧Ⅱ标准已在2005年7月1日执行。
2010年在全国施行欧Ⅱ标准,奥运北京率先施行欧Ⅳ标准,环境大为改观。
要解决上述两个问题,就必须走炼油高新技术之路。
(一)走深加工(渣油催化技术)技术
渣油催化裂化中国目前加工能力约9300万吨,其中包括1800万吨常压渣油(AR),1300万吨减压渣油,渣油的催化裂化(RFCC)已成为重油转化的重要装置,但产品质量和技术受到环境保护的严重挑战,必须开发FCC——即将重油转化轻馏分油的核心技术。
(二)加氢技术发展方向
加氢裂化装置是改变产品结构(除馏分中的硫氮氧的化合物)生产中间馏分油的重要方法,它可使炼油与石油化工更好地结合为芳烃生产和蒸汽裂解,提供原料,它可直接加工含硫减压瓦斯油(VGO)俗称蜡油加氢,可将润滑油基础油改质为APⅡ和Ⅲ类润滑油,有利于提高产品和副产品的质量。
二、炼油厂的分类
可分为四类:
(一)燃料油型:
生产汽油、煤油、轻重柴油和锅炉燃料。
(二)燃料润滑油型:
除生产燃料油外,还生产各种润滑油。
(三)燃料化工型:
以生产燃料油化工产品(合成塑料、合成纤维、合成橡胶基本原料等化工原料)。
(四)燃料油润滑油化工产品型综合型炼油厂,既生产各种燃料化工原料或产品,同时又生产润滑油。
三、炼油工艺简介
(一)常压蒸馏和减压蒸馏工艺
常压蒸馏和减压蒸馏通常称为常减压,常减压蒸馏基本属物理过程,原料油在蒸馏塔里按蒸发能力分成沸点范围,不同的油品(称为馏分),这些油有的经调合,加添加剂后以产品形式出厂,相当大的部分是后续加工装置的原料,因此,常减压蒸馏又被称为原油的一次加工(包括三个工序:
脱盐、脱水;常压蒸馏、减压蒸馏)。
原油的脱盐、脱水简称预处理。
从油田送往炼油厂的原油往往含盐(主要是氯化物)带水(溶于油或呈乳化状态),可导致设备腐蚀,在设备内壁结垢和影响成品油的组成需在加工中脱除。
常用的办法是加破乳剂和水,使油中水集聚,并从油中分出,而盐份溶于水中加以高压电场配合,使形成较大水滴顺利除去。
(二)催化裂化工艺(炼油厂核心工艺)
催化裂化是在热裂化工艺发展起来的,是提高原油加工深度,生产优质汽油、柴油最重要的工艺操作,原料范围主要是原油蒸馏或其它炼油装置的350℃—540℃馏分的重质油。
催化裂化工艺有三部分组成,即:
A:
原料油催化裂化
B:
催化剂再生
C:
产物分离
催化裂化所得产物经分馏后可得到气体、汽油、柴油和重质馏分油,有部分油反回反应器,继续加工称为回炼油,催化裂化的操作条件改变或原料波动(主要是指压力温度)可使产品组成发生变化。
催化裂化的反应为:
裂化反应
原料油→干气+LPG+汽油+LCO+油浆+焦炭
再裂化反应
干气+LPG+汽油+焦炭
要多产LPG,除尽量提高重油裂化(一次反应)的LPG产率外,需再把其所产汽油和部分LCO再裂化(二次裂化)。
汽油再裂化主要是汽油中的烯烃裂化;LCO裂化主要是增加生焦量,以供反应所需热量。
因此重油裂化反应需要有较高的汽油产率,汽油中又须富含烯烃,以便提供二次裂化作原料。
这样一次反应所得LPG加上二次裂化所得的LPG总和将比一般的工艺多。
要达到一次反应多产LPG又多产富含烯烃的汽油,工艺和催化剂都须同时改进。
工艺方面需采用有利于减少氢转移反应,降低焦炭和干气产率的技术;催化剂方面主要是要有好的重油裂化能力、氢转移活性低、焦炭和干气产率低。
(三)催化重整工艺
催化重整(简称重整)是在催化剂和氢气的存在下将常压蒸馏所得轻汽油转化成含芳烃较高的重整汽油过程。
A:
如果以80℃—180℃馏分为原料产品为高辛烷值汽油。
B:
如果以60℃—165℃馏分为原料,产品主要是苯、甲苯、二甲苯等芳烃。
这些都是生产合成塑料、合成纤维和合成橡胶的基本原料。
重整过程副产氢气可做为炼油厂加氢操作的氢源,重整的反应条件是反应温度为490℃—525℃,反应压力为10-20公斤。
重整可分为原料预处理和重整两部分。
工艺流程见附图:
(四)加氢裂化工艺
在高压氢气存在下进行,需要催化剂,把重质原料转化成汽油、柴油和润滑油,加氢裂化由于有氢气存在原料转化的焦碳少,可除去有害的含硫氮氧的化合物,操作灵活,可按产品需求调整,产品收率高而且质量好。
工艺流程见上煤油(柴油)加氢装置流程图。
(五)延迟焦化工艺
延迟焦化是在较长反应时间下,使原料深度裂化,以生产固体石油焦碳为主要目的,同时获得气体和液体产物。
延迟焦化用的原料主要是高沸点的渣油。
延迟焦化主要操作条件是原料中热约500℃,焦碳塔在稍许正压操作下,改变原料和操作条件可以调整汽油柴油裂化原料油,焦碳的比例。
现今较为先进的工艺是采用催化裂化-延迟焦化组合工艺,将油浆部分或全部甩出,焦化装置掺炼油浆,焦化蜡油送催化装置回炼。
采用此组合工艺,催化装置可提高处理量,并能适应更差的原料或掺炼更多的渣油,提高总体轻油收率,焦化装置又能生产针状焦。
具体工艺流程图如下:
(六)炼厂气的加工工艺
原油一次加工和二次加工的各生产装置都有气体产生,总称为炼厂气,就组成而言,主要有氢、甲烷、由2个碳原子组成的乙烷和乙烯、由3个碳原子组成的丙烷和丙烯、4个碳原子组成的丁烷和丁烯等。
它们主要用途是作为生产汽油的原料和石油化工原料以及生产氢气和氨。
发展炼油厂气加工的前提是要对炼厂气先分离、后利用。
炼厂气经分离作化工原料的比重增加,如分出较纯的乙烯可做乙苯,分出较纯的丙烯可做聚丙烯等。
三、工艺管道、设备特点
(一)加氢反应、催化反应、烷基化反应和催化高温脱氢反应的反应操作压力和操作温度都较高,多数在高温、高压、深冷条件下运行,介质中乙烯、苯、乙苯、脱清液、多乙苯、氢和硫化氢等同时并存,对工艺管道设备腐蚀严重,主要设备及相应的工艺管道采用Cr5Mo、Cr9Mo、15CrMo等耐热钢、铬18镍8、304、316L等不锈钢材质,以及国外X12Ni5等特殊钢材,特别是Cr5Mo、Cr9Mo、15CrMo为马氏体耐热钢,具有明显的空气淬硬倾向和焊后易出现延迟裂纹,对焊接质量要求高,施焊时要严格执行本钢种的焊接规范和预热、热处理规范。
(二)加氢反应器属于冷壁式反应器、其内壁衬一层隔热衬里,能起到降低壁温的作用,从而大大减轻氢与硫化氢的腐蚀,预热氢反应器属于热壁性筒式反应器,内衬0Cr13不锈钢复合钢板,施工质量要求严。
本工程加热炉较多,由于加热炉炉管外受火焰直接加热,管内介质温度高、压力大,同时受氢和硫化氢的腐蚀,使用条件苛刻,并且炉管安装时最后留下封闭段固定焊口受炉壁和左右炉管空间障碍,施焊困难,需采取相应措施。
(三)主要传动设备有循环氢压缩机、预加压氢增压机、预加压氢增压机、尾气压缩机、乙烯压缩机、冷冻机等,机构复杂、运行速度高、运转负荷大。
设备对中找正精度高、受外界温度影响大、对找正时的外界温度要求苛刻。
(四)重整装置主要设备有四台重整加热炉、两台往复式压缩机、一台离心式压缩机。
煤柴油加氢装置主要设备气提塔、洗涤塔、新氢和循环氢压缩机、加氢反应器。
塔类中、燃料气洗涤塔为填料塔,其余为浮阀塔。
产品气提塔内衬不锈钢。
(五)深冷装置中的20000m3深冷罐是引进德国TGE公司的深冷储藏工艺,不但技术上有特点,而且技术含量也很高,储罐的设计工作温度-114℃以下,罐的主体分内外两层,外罐直径35m,高36m,外罐顶为大型龙骨结构,内罐直径34m,材质为X12Ni5,储罐基础为硬性基础,直径为34m,圆形承台,由177根柱支撑,支柱底部由井字梁连接成一体,圆形承台平整度控制在±3mm内,圆形承台厚700mm,整个基础浇注成一个整体,难度非常大。
(六)换热器分为浮头式和U型管式两种,大部分为卧式。
(七)工艺管道内部清洁度要求高,管道焊接影响因素多、要求严,需要选择责任心强、技术好、发挥稳定的一批曾接受过培训的焊工承担焊接工作,并从各个方面严加控制。
(八)电气仪表防爆设计、DCS自动控制,检测点多、自控水平高。
工程量大,控制回路多,时间紧,往往开工晚,要求竣工早,必须有打硬仗、最后冲刺的突击准备。
四、工程难点、关键点分析
(一)工程难点
结合我公司工程管理经验、经过对装置工艺流程和操作条件分析,我们认为本装置的难点主要有:
1、预热氢反应器、重整反应器、烷基转移反应器、塔类等大型设备的吊装;
2、循环氢压缩机、预加压氢增压机、尾气压缩机、乙烯压缩机、冷冻机安装调试;
3、四台重整加热炉施工;
4、火炬塔的施工;
5、高压管道、合金钢管道的焊接和热处理控制;
6、管道内部清洁度的控制;
7、仪表安装调试。
(二)工程的关键点
1、设备基础施工,特别是冷罐基础施工;
2、压缩机组的安装找正和调试;
3、耐热钢管道的焊接和热处理控制;
4、管道内部清洁度的控制;
5、自动化仪表的连锁及复杂控制回路的调试;
四、主要施工方法
1.大型设备(大件)吊装施工方法
1.1简述
装置中有较多的大型设备,主要是大型反应器、大型塔类设备、加热炉类设备等需要使用大型吊车进行吊装,同时亦有部分设备需要大型吊车现场分段吊装。
1.2吊装方法:
整体到货设备(大件)采用大型吊车整体吊装;分段到货设备(大件)现场组焊整体吊装;超大型设备(大件)采用双机抬吊。
1.3吊耳、索具选用
吊耳、索具的合格使用是吊装安全的保证,吊耳、索具使用必须符合如下要求:
⑴吊耳使用宜直接自标准规范中选用,若由制造厂设计或自行设计必须有设计说明和计算书并经相关部门审批。
⑵吊耳的结构形式:
反应器宜使用吊盖式吊耳;一般立式塔、容器使用管式吊耳,反应器、塔底部递送辅助吊耳可使用板式吊耳;卧式容器、换热器可不设吊装吊耳。
⑶吊装使用的索具宜直接从专业厂家购买,尽量使用吊带、无接头钢丝绳圈、压制绳扣,由制造厂购买的索具必须具有合格证书,使用时不得超过索具注明的吊装重量。
⑷使用钢丝绳吊装,必须对吊物、索具进行仔细核算,计算依据、安全系数要符合规范规定,所用钢丝绳、卡具必须有合格证明文件。
1.4吊装
⑴设备吊装时,吊装的指挥和操作人员必须接到吊装令。
⑵吊装时,主吊车先起吊,辅助吊车后起,起吊要缓慢平稳,若发生负荷报警或严重超重,必须立即检查原因,查出原因并处理后,经检查合格方可再行吊装。
⑶主、辅吊车将吊件吊离支撑物后,应及时将支撑拆除。
⑷主吊车按方案要求进行提升并向辅吊车的脱钩位置旋转,辅助吊车随着主吊车的提升向前递送,到脱钩位置辅吊车松钩摘除吊索。
⑸主吊车吊设备向安装位置(基础)方向旋转,设备在旋转过程中不得离地面过高。
吊到基础前,吊车提升达到安装高度后,将设备旋转到基础上方安装就位。
⑹设备落到基础上,吊车不松钩,进行设备找正,找正完毕把紧地脚螺栓,吊车松钩摘钩,设备吊装结束。
⑺对分段吊装的设备,分段设备吊到基础前提升时要安排专人控制溜绳,防止设备旋转或悠荡出现意外。
分段设备吊装到位后,要随即进行找正并进行焊接固定,分段设备进行间断焊接牢固方可摘除吊钩。
⑻设备吊装完毕,将吊钩摘除后,吊车移位,进行设备附属结构的完善。
分段吊装设备进行焊接、检测和其它检验工作。
2.压缩机组安装施工方法
2.1简述
压缩机组称为生产装置的心脏,其正常运转是保证装置正常运行、生产的先决条件。
在炼油装置中主要使用的压缩机有往复式和离心式二种。
2.2安装方法:
垫板采用机械方法加工,其表面粗糙度不得低于Ra5。
机组采用无垫铁安装技术,CGM灌浆料灌浆,用激光对中仪进行机组对中找正,油系统全部氩弧焊打底焊接,化学清洗油冲洗。
2.3离心式压缩机安装
2.3.1机组安装
※施工技术要求
(1)地脚螺栓安装有如下要求:
①地脚螺栓光杆部分应无油污,螺纹部分应涂抹黄油。
②在孔内呈垂直自由状态。
③安装后螺栓螺纹伸出1.5~3个螺距。
④螺母、垫圈、底座相互间接触紧密。
⑤地脚螺栓光杆和锚板刷防锈漆。
⑥钢制锚板、锚板与托着的螺母之间点焊固定。
(2)离心压缩机组就位、找平、找正
①压缩机为整体供货,压缩厂房端部留有吊装区且压缩机整体质量不超过桥式起重机负荷,利用厂房内桥式起重机整体吊装就位,否则采用吊车一次吊装就位。
②压缩机机组就位前,清理机组底座底面,螺钉固定悬挂板。
③吊装就位后,调整机组底座纵、横中心线与基础中心基准重合,其允许偏差不大于5mm。
④调整地脚螺栓和顶丝,使底座标高达到设计标高,其偏差不大于3mm;用框式水平仪在机组精加工面上测量机组水平度,纵向水平度允许偏差不大于0.05mm/m,横向水平度偏差不大于0.1mm/m;找平时,底座上所有调整顶丝应均匀调节,使机组载荷均布,防止底座变形,影响找平。
(3)离心式压缩机同往复式压缩机一样采用无垫铁安装,方法和要求同样如前。
(4)汽轮机安装:
①检查设备本体不得有裂纹、气孔,未浇满、夹层等缺陷。
焊件不得有变形、裂纹等缺陷。
②检查轴颈圆度、圆柱度、径向跳动,允许偏差不大于0.01mm。
③检查推力盘的表面粗糙度Ra≤0.8μm,端面跳动应小于0.015mm,测出推力总间隙,应符合制造商出厂文件要求。
④检查轴瓦与瓦背的紧力(或间隙)值,应符合制造商出厂文件要求。
⑤机壳中分面应光滑,无沟槽、划痕、锈蚀等缺陷。
⑥塞尺检查轴瓦与轴径处间隙,应符合制造商出厂文件要求。
⑦按制造商出厂技术文件要求,测量汽轮机其他部位间隙
2.3.2单机试车
※汽轮机单试
⑴汽轮机调节保安系统的静态调试
①汽轮机调节、保安系统的静态调试应在制造厂现场代表指导下进行,按厂家要求准备好调试所需的工器具。
②系统通油前检查、确认并标定各运动机构的静态位置及行程指针刻度位置。
③操作危急遮断器进行挂闸和打闸试验,手动打闸时测主汽门速关阀的关闭时间。
④按制造厂技术文件要求调整汽轮机调速系统各工作点位置,做出各工况的性能曲线。
⑤启动盘车泵,做盘车器电动联锁试验,保护动作准确、可靠。
⑵汽轮机的启动、试运转
①试运行前的准备工作:
脱开汽轮机与压缩机之间的联轴器,装好联轴器保护罩。
机组辅助系统达到投用条件,油系统联锁共检合格并确认投入。
汽轮机主蒸汽管线吹扫合格。
汽封冷却器试抽真空符合汽轮机厂家要求。
检查、调整并记录汽轮机膨胀批示器和轴位移指示器的膨胀和位移值。
启动油系统检查其工作参数是否达到要求。
启动盘车油泵,盘车30min检查有无刮、碰、卡、涩等现象,如有故障应立即消除。
进汽阀关,打开进汽阀前、后排水阀及汽轮机本体各疏水阀。
②汽轮机的冲动、升速及试验
停电动盘车电机。
启动抽气器,建立汽轮机轴封系统真空。
挂上危急遮断油门,投入速关阀油路系统联锁。
打开速关阀,按下起动按钮,二次油压打开调节汽阀,调速系统自动将汽机转速升至警戒转速。
主蒸汽冲动转子进行暖机,暖机时间不得小于16min。
全面检查机组各轴承温度、振动、轴位移、气缸膨胀等及汽轮机噪音。
如有异常,应立即降速,停机检查。
进汽稳定后,汽轮机的进汽温度大约有50℃的过热度时,即可关小直至停止进汽管上的疏水。
当汽机的蒸汽压力达到比额定背压高约5%时,则就可以打开背压阀门并将背压保安装置投入运行。
检查主机、辅机运行情况,包括声响、轴位移、轴承温度,振动及机体热膨胀等情况。
检查各导向滑动部位应无卡涩现象。
继续开大主汽阀,快速升速,直至转速达到80%额定转速,稳定15min。
若无异常,继续升速,直至转速达到额定转速。
汽轮机在额定转速下连续运行1h,检测汽轮机下列各项要求,符合下列条件则汽轮试运行合格:
a)主机、辅机运行正常,无异常现象
b)轴承进油温度应在45±3℃,润滑油温升不得超过28℃,轴承温度不高于95℃。
c)轴承双振幅不大于30um,超速试验时,振动值不超过43um。
d)主轴位移不得大于0.38mm。
e)汽封抽气真空度稳定。
※调速系统试验
a)使用超速跳闸试验手柄,做超速试验,手动打下危急遮断器手柄后,二次油压应能立即泄放,速关阀及时动作关闭主汽门,各项联锁应准确及时动作。
b)继续开启调节汽阀,转速升至跳闸转速时,检测危急遮断器动作应及时,其动作转速偏差应不大于汽机厂给定数值的2%,当转速超过此标准时,应立即手动打闸停车,同时找出危急遮断器不动作的故障原因,并及时消除。
c)危急遮断器动作后,转速降到额定转速的90%时,将危急遮断器手柄复位,使汽轮机再次升速,反复做三次超速试验。
⑶汽轮机停机
①汽轮机在额定转速下,检测各轴承温度、振动、轴位移、汽缸膨胀等,做好各项试车记录。
②试运行合格后,调速系统置于最小控制转速,手动停车键,打闸停车,泄掉二次油压,速关阀自动关闭主汽门;
③关闭主蒸汽管线上的进汽阀,打开管路上所有排水阀及汽机本体各疏水阀排淋;
④汽轮机打闸停车后,测出汽轮转子的惰走时间,应符合厂家文件规定值;
⑤转子停止后立即启动盘车油泵,转子进行盘车,直至轴承温度降到40±3℃,气缸内温度降90℃以下,才可停盘车;
⑥检查汽轮各滑销位置,各保安装置设置应在启动位置。
2.3.3机组空负荷试运行
⑴连接汽轮机与压缩机联轴器。
⑵微开压缩机入口阀,全开出口阀、放空阀和防喘振阀。
⑶启动压缩机润滑油、密封油系统,调整油温和油压。
⑷按
(2)项启动汽轮机,在额定转速下连续运转2~4小时,检查并记录轴振动及润滑油温升值,不能超过允许范围,机组无异常现象。
2.3.4机组负荷试运转
⑴负荷试运转所用的介质应符合设计或制造商技术文件的规定。
⑵同上方式启动机组。
⑶机组在额定负荷下应连续运转12小时,检查并记录轴振动及润滑油温升值,不能超过允许范围,机组无异常现象,试运行合格。
3.管道施工方案
3.1炼油装置管道工程量大,主要工艺物料多为易燃、易爆、高温、高压介质,因此铬钼耐热钢、不锈钢材质管道使用较多,大量合金钢、不锈钢管道的使用和易燃、易爆、高温、高压的工艺特性,对管道施工的技术、质量管理提出了更高的要求,本方案以高温、高压管道的施工为主线介绍管道预制、安装施工、管理要求。
3.2施工方法:
工艺管道采用工厂化预制加工,分段到现场组装、安装;工厂预制加工采用自动、半自动焊接;现场采用半自动、手工焊接;全部采用氩气保护焊打底、电弧焊盖面焊接;吊车吊装安装。
3.2.1铬钼耐热钢管道焊接
①铬钼耐热钢管道与碳钢、低合金钢管道坡口形式及焊接方法的选用相同。
②耐热钢管道焊接要依据焊接规范要求进行预热,预热达到规定温度后,立即进行底层焊道的氩弧焊打底焊接,打底焊接要求一次连续焊完,焊道要焊透、成型要好,焊道焊肉厚度不得小于3mm;管道的打底焊道焊接完毕,应立即进行填充、盖面焊道的焊接,在整个焊接过程中焊接层间温度必须符合焊接工艺规范要求,若温度低于层间温度要求,应采用措施加热,每条焊缝要一次连续焊接完。
③管道焊接过程中若因故(停电、大风、下雨等)中断焊接,必须按要求采用后热、缓冷等措施。
再行焊接前应进行检查,确认焊道无裂纹后方可按原焊接工艺要求进行预热、加热继续焊接。
④管道焊缝焊完后,若不能及时进行焊后消除应力热处理时,应立即进行300~350℃,15~30min的后热处理,然后保温缓冷。
⑤焊缝消氢热处理和焊后热处理方式均选用电加热法。
加热在坡口两侧均匀进行,加热范围每侧不小于3倍壁厚(S),且不小于50mm,加热温度应在距焊缝75mm处测量。
3.2.2不锈钢管道焊接
①奥氏体不锈钢管道焊接过程中,在保证焊透与熔合良好的条件下,应采用小规范、短电弧、快速焊、窄焊道和多层多道焊工艺进行焊接,层间温度不得超过175℃,必要时,应采取强迫冷却工艺措施。
焊接完成以后,对奥氏体不锈钢焊接接头应进行酸洗与钝化处理。
②对于管径大于18寸的不锈钢管道,使用的气体置换的方式是:
人进入管道内部,沿焊道贴一圈U型紫铜气罩,使用高温胶带在管道内部进行密封,使管道内部隔绝空气,处于紫铜防护气罩的保护之下。
③对于管径小于18寸的不锈钢管道来说,常用的气体置换的方式是使用特制的管口内气体置换装置。
管口内气体置换装置由两段不锈钢堵头、密封胶皮和进出气接头等组成。
3.2.3高压管道的安装
3.2.3.1一般要求:
⑴强调过程质量的控制,对于高压系统,每一道安装法兰,在法兰面检查、法兰安装、垫片安装、螺栓紧固等环节,逐一编制质量控制表,在监理等的检查下进行。
保证高压系统的密封性能,对于高压装置,是事半功倍的头等大事。
⑵做好文明施工,保持管道的内洁,特别对于压缩机的出入口、重要设备的出入口、安装后无法进行拆卸的大口径管道,应在监理及业主的监督下安装、封闭,以避免吹扫时的拆卸。
⑶管道就位后,应及时安装正式支托架,特别对于高温部位、长延长米管道等,逐一核查其规格、形式、数量、位置、预留量等。
⑷对于有缺陷、损伤的法兰密封面,应及时报告、沟通,及时进行研磨等处理,避免问题的积累与隐藏。
⑸应提前编制、沟通好试压方案,在预制安装阶段即做好使用临时垫、假孔板等相应的准备工作,避免试压时的大面积拆卸,造成垫片、螺栓的损伤、浪费。
3.2.3.2安装前的共检内容
⑴预制段管子、管件、阀门内部已清理干净无杂物;
⑵支吊架一次件、仪表一次件施工完,(易于碰坏的可以在安装后进行焊接,但必须开口完);
⑶预制件的几何尺寸、规格符合图纸要求;
⑷安装所用管子、管件、阀门符合要求;
⑸与管道连接的机械、设备已找正合格,二次灌浆、养生完;
⑹预制焊口的探伤、热处理完。
3.2.3.3管道安装
⑴管道预制完毕宜在地面将其装配成组合件,整体安装,以减少高处作业。
⑵管道安装按先装置区,后管带区;先管廊,后设备配管;先大管,后小管;先干线,后支线的施工顺序。
并根据材料、设备、相关专业的影响等适当调整。
⑶管道安装按管道平面布置图和单线图进行,重点注意标高、介质流向、支吊架型式及位置、坡度值、预拉值、管道材质;
⑷临时支吊架应及时拆除并安装正式支吊架。
管架制安严格按图进行,特别是热力管线和机器出入口管线,未经设计书面同意严禁变动其型式或规格、材质。
⑸对于环槽密封面的法兰安装前对密封面及垫片作印痕检查,即在法兰密封面均匀涂抹红丹粉,再放正式垫片转动,转动角度应大于30°,但小于45°,如法兰环槽