第十一章 零件典型表面的切削成形方法.docx
《第十一章 零件典型表面的切削成形方法.docx》由会员分享,可在线阅读,更多相关《第十一章 零件典型表面的切削成形方法.docx(25页珍藏版)》请在冰豆网上搜索。
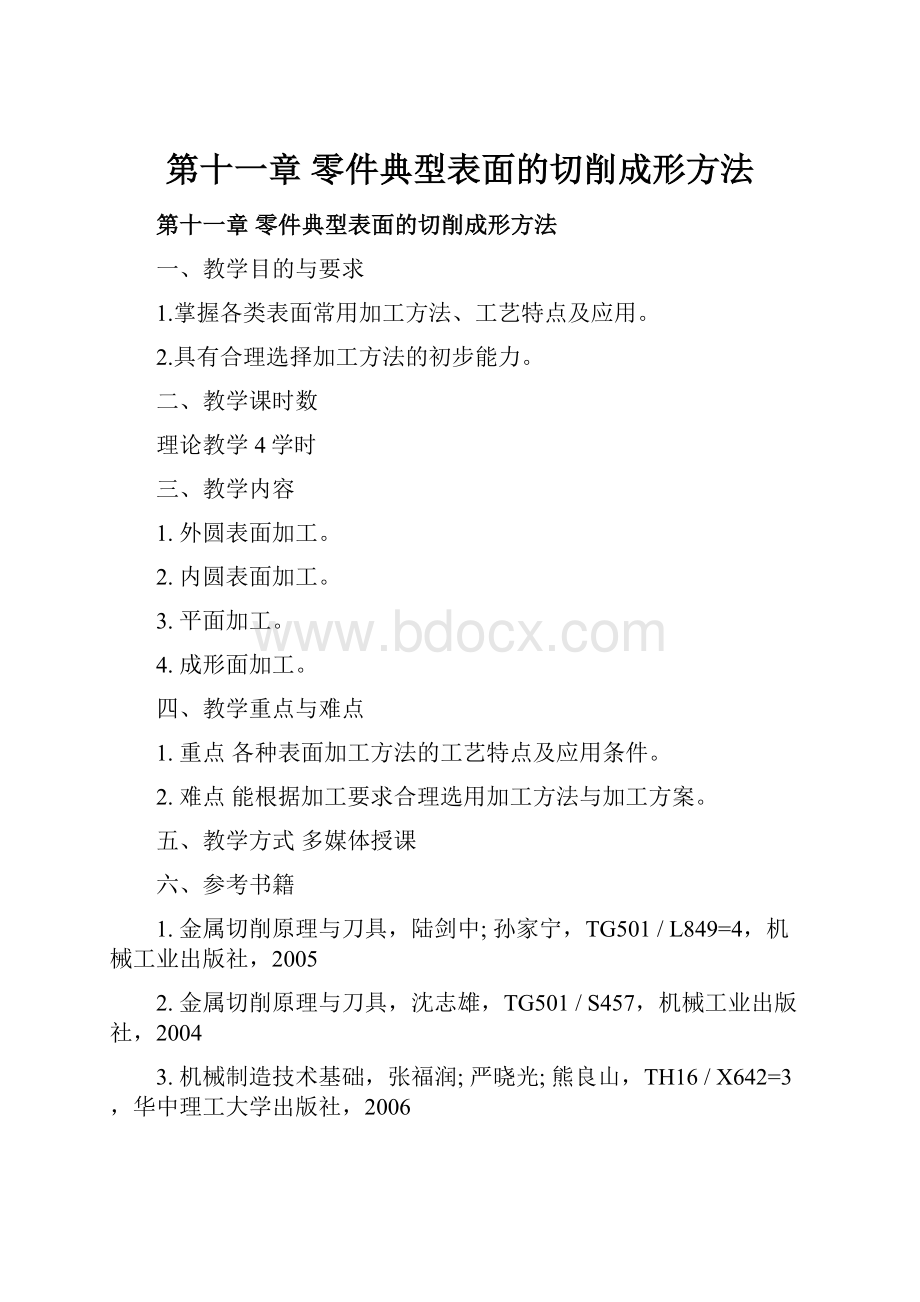
第十一章零件典型表面的切削成形方法
第十一章零件典型表面的切削成形方法
一、教学目的与要求
1.掌握各类表面常用加工方法、工艺特点及应用。
2.具有合理选择加工方法的初步能力。
二、教学课时数
理论教学4学时
三、教学内容
1.外圆表面加工。
2.内圆表面加工。
3.平面加工。
4.成形面加工。
四、教学重点与难点
1.重点各种表面加工方法的工艺特点及应用条件。
2.难点能根据加工要求合理选用加工方法与加工方案。
五、教学方式多媒体授课
六、参考书籍
1.金属切削原理与刀具,陆剑中;孙家宁,TG501/L849=4,机械工业出版社,2005
2.金属切削原理与刀具,沈志雄,TG501/S457,机械工业出版社,2004
3.机械制造技术基础,张福润;严晓光;熊良山,TH16/X642=3,华中理工大学出版社,2006
4.机械制造技术基础,黄健求,TH16/H845,机械工业出版社,2006
第十一章零件典型表面的切削成形方法
零件→种类多,形状各异→最基本的几何表面组成→加工方法不同
本章内容:
典型表面的加工方法、加工方案。
第一节外圆表面加工
轴、套、盘等回转体类零件最基本的组成表面。
主要技术要求:
尺寸精度、表面粗糙度,
圆度、圆柱度、同轴度等。
一、外圆表面的车削
1.常用车床类型及应用范围
⑴普通车床
比例较大;
特点是通用性强,加工内容广,但生产率低;
主要应用于单件小批加工。
⑵六角车床
转塔刀架能安装较多数量的刀具,轴向、径向定距切削装置,适合加工较复杂的回转类零件,生产率高。
适用于较大批量加工较复杂的中小型零件。
⑶自动、半自动车床
自动化程度高,生产率高。
但是需要设计、制造专用靠模、凸轮等自动控制元件,调整也较复杂费时,生产准备周期长。
适用于大批量生产。
⑷立式车床
适于加工直径大而长度短的大型盘、套类零件,在重型机械制造部门应用较多。
⑸数控车床
自动化程度高、效率高,程序控制;
灵活性、适应性强,技术复杂,造价高。
适用于中小批量加工形状较复杂的回转体类零件。
2.车床上常用夹具及应范围
⑴三爪自定心卡盘
能保证三个卡爪同步径向移动,可自动定心且夹紧迅速。
适应于各种回转体零件的装夹,但定位精度不高,夹紧力较小。
⑵四爪单动卡盘
每个卡爪都是单独移动,夹紧可靠,适用各种形状的工件。
不能自动定心,找正比较困难。
常用于形状特殊的轴类和盘类中、小型零件的单件小批加工。
⑶顶尖支承
左端卡盘装夹,右端顶尖支承:
用于外圆表面的粗车和半精车。
两端顶尖支承:
用于精车。
特点是加工出的各段外圆表面间有较高的同轴度。
P242图11-1
⑷花盘、弯板安装P242图11-2
单独使用花盘:
用于定位面与车床主轴垂直的形状复杂件。
花盘与弯板配合:
用于定位面与车床主轴平行的较复杂件。
3.外圆表面车削的工艺特点
⑴与外圆磨削相比,切削量大,效率高,加工精度和表面质量不如磨削,车削常用于中等以下硬度表面的粗加工和半精加工。
⑵一次装夹中可以车出回转体类零件上较多的表面,容易保证各加工表面的相互位置精度。
⑶车刀结构简单,制造、刃磨容易,装夹方便,加工成本低,车削是一般外圆表面最常用的加工方法。
二、外圆表面磨削
1.常用外圆磨床及应用
⑴普通外圆磨床P216图10-22
工件以顶尖孔定位在两顶尖间装夹,多用于轴类零件外圆表面及用心轴装夹的盘、套类零件外圆的加工。
⑵无心磨床P243图11-3
首件磨削时调整较费时,适于较大批量加工直径不大的小型轴、销类零件。
以加工表面本身定位磨削,故不能提高的位置精度,也不适于加工断续的(如带键槽、平台)外圆面。
2.外圆磨削方式
⑴纵磨法(如图11-4所示)
⑵横磨法P244图11-5
⑶深磨法P244图13-6
采用修整成锥面或带台阶的砂轮,以较小的纵向进给量、较大的磨削深度磨削,生产率较高,加工质量介于纵横磨法之间。
适用于长度和直径尺寸都较大、刚性好、余量大而硬度又较高的外圆表面,以磨代车,粗精加工合一的条件下。
3.高质量磨削
⑴高速磨削
采用特制高强度、大直径的砂轮,配以高速电机,使磨削速度达到80~120m/s。
加工精度、表面质量和生产率都高于一般磨削,是一种高效、高质量的磨削。
但此法要求机床具有较高的精度和足够的刚性,以保证高速磨削条件下的平衡性。
由于产生的切削热量多,工件表面温度高,需要机床配备有充分的冷却液循环装置,以免使加工表面过热而烧伤。
⑵高表面质量磨削
在高精度或精密磨床上,采用细粒度的砂轮,经过精细修整后,磨粒微刃的等高性好,在摩擦、抛光等综合作用下,可使工件表面粗糙度达到Ra值小于或等于0.01μm。
此法与研磨等其他光整加工方法相比,不仅效率高而且可提高加工表面的形状精度和位置精度,但机床费用较高。
4.外圆表面的光整加工
目的是达到更高的加工精度和更好的表面质量。
⑴研磨P245如图11-7
小批量的外圆研磨是在车床上用研具加研磨剂手工进行的。
研具材料要比工件软些,在压力作用下使部分磨粒嵌入研具工件面表层,产生对工作表面的切削作用。
常用研具材料有铸铁、青铜等。
研磨剂由极细的磨料和研磨液组成。
研磨液用煤油加机油或植物油,再加入适量化学活性较强的油酸、脂肪酸等。
工艺特点:
①微量切削作用,油酸或脂肪酸的化学氧化作用,切削力更小,切削热少,能达到很高的尺寸精度,很低的表面精糙度,还可以提高加工表面的几何形状精度。
②工件与研具间位置不固定,而是随机的,不能提高相互位置精度。
③研磨与高质量磨削相比生产率低,但不需要精密复杂、昂贵的设备,且方法简单,容易保证加工质量。
⑵超级光整P245图11-8
工件作低速转动,磨头沿工件轴向作较低频率和较小幅度往复运动的同时,还沿着工件轴向做缓慢的进给运动。
切削痕迹是很细密复杂的交叉网纹,故超级光磨能获得很低的表面粗糙度,但不能提高形状精度和位置精度。
工艺特点:
①半自动加工,不仅工人劳动强度比手工研磨低,且一人可兼管几台机床,劳动生产率也较高。
②由于超级光磨磨头的结构特点,与研磨要比,更适于直径和长度尺寸较大的外圆表面的超精加工。
⑶抛光
抛光是用涂有抛光膏的高速旋转的弹性抛光轮对工件表面进行光整加工的方法。
抛光膏由磨粒和油脂混合而成,其作用与研磨剂相同。
三、外圆表面加工方案及应用条件P247图11-9
1.粗车—半精车—精车
加工精度、表面粗糙度要求较低(IT7、Ra0.8μm),中等以下硬度外圆表面。
2.粗车—半精车—粗磨—精磨
加工精度、表面粗糙度要求较高(IT6、Ra0.16μm),需淬硬外圆表面。
3.粗车—半精车—精车—金刚石车
精度要求高、低硬度外圆表面。
4.粗车—半精车—粗磨—精磨—研磨(超精加工、砂带磨、镜面磨或抛光)
在加工路线2的基础上又加进研磨、超精加工、砂带磨、镜面磨或抛光等精密、超精密加工或光整加工,以减少表面粗糙度、提高尺寸精度、形状和位置精度为主要目的,抛光、砂带磨等以减少表面粗糙度为主。
第二节内圆表面(孔)的加工
主要指圆柱形的孔。
加工条件差:
受孔尺寸的限制,刀具刚性差,排屑、散热、冷却、润滑都比较困难。
孔可以采用固定尺寸刀具加工。
技术要求:
尺寸精度(孔径、孔深)、
形状精度(圆度、直线度、圆柱度)、
位置精度(同轴度、平行度、垂直度)、
表面粗糙度等。
一、孔的分类
1.按用途分
⑴非配合孔
螺钉孔、螺栓孔的底孔、油孔、气孔、减轻孔等;
一般要求加工精度较低,在IT12以下;
表面质量要求也不高,表面粗糙度Ra值大于10μm。
⑵配合孔
如套、盘类零件中心部的孔,箱体、支座类零件上的轴承孔都有要求较高的加工精度(IT7以上)和较高的表面质量(Ra<1.6μm)。
2.按结构特点分
按结构特点可分为通孔、盲孔;
大孔、中小孔;
光孔、台阶孔;
深孔,一般深度孔。
二、用固定尺寸刀具加工孔
1.钻孔
钻孔是在实心材料上加工出孔的方法。
刀具为钻头,一般用麻花钻。
P248图11-10
机床:
车床——回转体类中心孔;
镗床——箱体配合孔系;
钻床——一般孔。
钻孔特点:
横刃前角为负值,主切削刃愈接近芯部前角愈小,且两刃不易磨得对称,排屑槽深,刚性差;
切削条件差,切削深度大,散热条件差,排屑困难,易划伤已加工表面,刀具易磨损等。
应用:
加工精度要求低的中小直径尺寸的孔(75㎜以下)。
2.扩孔
对已有孔(钻、铸、锻出)进行再加工。
目的:
扩大孔径,提高孔的加工精度和表面质量。
扩孔钻的结构。
P249图11-11
与麻花钻相比:
无横刃、切削刃多、前角大、排屑槽浅、刚性好、导向性好等结构特点,且切削深度小、切削力小、散热条件好、切削平衡等切削特点,故扩孔的加工质量优于钻孔。
精度达IT9~13,表面粗糙度Ra值为1.25~40μm。
扩孔钻直径一般最大为100mm。
3.铰孔
对已有的孔进行精加工的方法。
机械铰孔:
车床、钻床、镗床;
手工铰孔。
铰刀的结构。
P249图11-13
手动铰刀较机动绞刀:
切削部分锥角小,
切削刃、修光刃长,
便于定位、省力,
4.拉孔
在拉床上进行的,孔的形状、尺寸由拉刀截面轮廓保证。
圆孔拉刀的结构。
P250图11-14
适于拉削的孔型。
P250图11-15
用孔本身定位,不能修正孔的位置误差;
生产效率高;
拉刀结构复杂,制造周期长,费用高。
应用:
多用于大批大量生产中。
三、镗孔
⑴镗刀P251图11-16
单刃镗刀:
焊接式——多用于中小孔;
机械式夹固式——多用于大孔。
浮动镗刀:
为可调式结构。
⑵机床
车床:
常用于加工回转体零件中心部位的孔和小型支座类零件上的孔。
镗床:
常用于镗箱体上的一系列具有位置精度和位置尺寸要求的轴承孔。
P251图11-17
⑶特点
灵活性大,应用范围较广,可进行孔的粗加工、半精加工,也可以精加工;
可镗通孔、光孔,也可镗盲孔、台阶孔;
可以镗各种直径的孔,更适宜镗大直径的及有相互位置精度要求的孔。
常用的大多为单刃镗刀,并采用试切法加工,故与铰孔、扩孔、拉孔相比生产率较低。
四、磨孔
一般在内圆磨床上进行,工件用卡盘或专用夹具装夹。
磨削条件不及外圆磨削有利,加工质量和生产率低于外圆磨削。
适应性强,应用范围广;
磨孔适用于中等以上硬度表面,尤其是淬火后高硬度的孔。
磨孔是工件淬硬后对孔进行精加工的主要方法之一。
五、孔的光整加工
1.孔的研磨
可涨式研磨棒。
P252图11-19
常为手工操作,效率低,工人劳动强度大,应用较少,仅用于小孔的单件小批量的光整加工。
2.孔的珩磨P252图11-20
同时切削的磨条数量较多,加工过程为半自动化,生产率较高,在大批量生产中应用较多。
又因为珩磨机结构简单,精度要求不高,设备费用低,因此珩磨具有较好的经济性。
珩磨的应用范围较广,适于孔径为15~500mm的孔,更适于加工孔径与孔深比大于5的深孔,如汽车、拖拉机发动机缸体活塞孔及飞机起落架作动筒的孔等。
六、孔的加工方案及应用范围P253图11-21
1.钻孔
实体材料上孔的唯一加工方法。
主要用于小孔(直径小于50mm)。
2.钻一扩
应用于孔径较大但精度要求又不高的孔。
3.钻一铰
应用于孔径较小,加工精度要求较高的各种加工批量的标准尺寸和大批量加工非标准尺寸的孔。
4.钻一扩一铰
应用条件与钻一铰基本相同,不同点在于孔径较大。
5.钻(粗镗)一半精镗一精镗—浮动镗或金刚镗
适用于精度要求高,但材料硬度不太高的钢铁零件或有色金属件的孔加工。
特别是位置精度要求较高的孔系加工。
6.钻(粗镗)一半精镗一磨一珩磨(研磨)
适用于加工过程中需要淬硬的工件孔的精加工,其中珩磨用于较大直径深孔的终加工,研磨用于较小直径孔的终加工。
7.钻一拉
第三节平面加工
平面是圆盘形、板形零件的主要表面,也是箱体零件的主要表面之一。
一、平面类型及技术要求
1.平面类型
外平面:
板、箱体零件的外表面,轴盘、套零件的端面。
内平面:
槽内平面图11-22,孔内平面图11-23。
2.技术要求
平面与基准间的尺寸精度,平面本身的平面度、直线度及与其他表面间的平行度、垂直度、倾斜度等位置精度,表面粗糙度。
二、平面的车削
轴、盘、套等回转体零件的端面,一般都采用车削加工。
端面与外圆或孔在一次安装中同时加工完成,以保证位置精度。
三、平面的铣削
铣削是平面加工应用最广的一种。
中小型零件上的平面:
通常在卧式铣床或立式铣床上进行。
立式铣床:
除可加工一般平面外,还可加工不通槽、半通槽及梯形槽、燕尾槽。
卧式铣床:
易采用多刀组合加工台阶平面,以提高生产率。
大型零件上平面:
可在龙门铣床上进行加工。
加工方法:
周铣P255图11-24
端铣P255图11-25
混合铣:
沟槽P255图11-25
端铣特点:
同时参加切削的刀齿数量多,主切削刃担负主要切削工作,刀尖圆弧和副切削刃修光,刀杆短粗,刚性好。
因此端铣的加工效率和质量都比周铣高,所以平面铣削中端铣用得较多。
四、平面的刨削
刨削也是平面的主要加工方法之一。
中小型零件的平面:
在牛头刨床上加工;
大型零件的平面:
在龙门刨床上加工。
用刨削加工的平面有板、箱体等零件上的外表平面,还有台阶平面和各种截面形状的通槽,如梯形槽、V形槽、燕尾槽等。
常见刨刀的形状及应用P256图11-26
刨削特点:
生产率较低:
刨刀为单刃刀具,往复直线运动,返回是为空程。
刀具切入时有冲击,换向时要克服惯性力,致使切削速度的提高受到限制。
刀具和机床结构简单、价格低、调整方便、适应性强,刨削狭长平面时也可得到较高的生产率。
五、平面的插削与拉削
孔内平面(如孔内键槽、四方孔、六方孔)的加工一般在插床(立式刨床)和拉床上进行。
P256图11-27
1.插削特点:
插削生产率和加工质量都较低;
刀具结构简单、造价低、刃磨容易,加工适应性强;
不仅可以加工通孔的孔内平面,也可以加工盲孔的内平面;
不仅可以加工中小直径尺寸的孔内平面,更适于加工大孔的孔内平面。
适用于各种孔内平面的单件、小批量加工。
2.拉削特点
拉削孔内平面和孔内槽不仅加工精度高,生产率也高;
拉刀结构复杂,制造、刃磨费用都高,适应性也不如插削广。
拉削也用于中小尺寸外表平面的大批量加工,其中较小尺寸的平面用卧式拉床,较大尺寸的平面用立式拉床加工。
适于中等尺寸通孔内平面和孔内槽的大批量加工。
六、平面的磨削
主要用于加工质量要求高或高硬度外表平面的加工。
平面磨床:
立轴式:
端磨,轴向受力,故刚性好,可以采用较大磨削用量,再加之砂轮与工件接触面积大,切削效率也高。
但表面质量不太高,多用于粗磨、半精磨。
卧轴式:
周磨,砂轮与工件的接触面积小,切削速度高,排屑与散热条件好,因此加工表面质量优于端磨,但加工效率较低,多用于工件的精磨。
七、平面的研磨
表面质量高,尤其当两个配合平面要求很高的密合性时,常用研磨法加工。
手工研磨:
效率低,但加工表面质量可以达到比机械研磨更高的要求,适用于小型零件平面的单件、小批量加工。
机械研磨:
效率高且劳动强度小,用于中小型零件的较大批量加工。
八、平面加工方案P258图11-28
1.粗车—半精车—精车—金刚车
用于精度要求较高但不需淬硬及硬度低的有色金属回转体零件端面的加工。
2.粗车—半精车—精车—精密磨
用于精度要求较高且需淬硬的回转体零件端面的加工。
3.粗刨—半精刨—宽刃精刨、刮研或研磨
用于未淬火的大型狭长平面,如机床床身导轨的加工,以刨代磨减少工序周转时间。
刮研是获得精密平面的传统加工方法。
在大批量生产的一般平面加工中有被取代的趋势,但在单件小批量生产或修配工作中,仍有广泛应用。
4.粗铣—半精铣—精铣—高速精铣
用于中等以下硬度要求的一般平面的加工。
5.粗铣(刨)—半精铣(刨)—粗磨—精磨—研磨(精密磨、砂带磨或抛光)
用于加工质量要求特别高且需淬硬的工件平面的加工,如块规(量具)工作面等。
6.粗拉—精拉
用于大批量加工硬度不高的中小尺寸外表平面的加工,如沟槽、台阶面。
对于加工精度不太高、生产批量不大的各类孔内平面和孔内槽,可以采用钻、插加工。
第四节成形面的加工
成形面主要指各种非圆形曲面:
⑴回转体成形面P259图11-29
⑵直线成形面P259图11-30
⑶立体成形面P259图11-31
一、成形面的加工
1.成形刀具法P260图11-32
成形刀具有与工件形面相应的形状和尺寸的主切削刃。
在车、铣、刨、拉、磨等加工中都可应用,所用刀具为成形车刀、成形铣刀、成形刨刀、拉刀、成形砂轮等。
共同特点:
操作简单,生产率高。
成形刀具的设计、制造比一般刀具复杂,需要较长的生产准备周期和较高的费用,一般应用于较大批量生产中。
2.运动轨迹法加工成形面
成形面是由刀具与工件相对运动的轨迹形成。
三种方法:
⑴按划线或样板加工
通有机床,由人工控制刀具或工件的纵、横向进给,按事先在工件上划好的加工表面轮廓线或样板模线进行加工。
较难保证加工精度,生产率低,工人劳动强度大,并需由技术熟练的工人操作,但此法不需要专门设计、制造成形刀具和靠模,灵活性大,用于单件、小批量加工。
⑵靠模法加工P260图11-33
由靠模装置控制普通刀具或工件按靠模工作面曲线运动,使之加工出所需要的形状和尺寸。
可在普通机床上加靠模装置进行,也可在专门的仿形机床上进行,前者使用通用机床,但加工质量和生产率不如后者。
需要设计制造专用靠模,需要较长的生产准备时间和较高的费用,故适用于较大尺寸形面的较大批量加工。
⑶程序控制法加工成形面
在数控制机床上,由控制系统按输入的程序进行自动加工完成所需成形面。
改变加工形面形状、尺寸只需改变输入的程序即可,因此与靠模法相比生产准备时间短,费用低,灵活性大。
机床费用高,技术复杂,适用于加工对象更换频繁、形面复杂的中小批量加工。
3.成形刀具与运动轨迹复合成形法
成形面是由刀具的形状与工件、刀具间相对运动轨迹复合而成,如展成法加工齿轮中的插齿加工,不仅插齿刀的齿形要符合相应模数齿轮的齿形,而且插齿刀与工件间还必须强制保持一定的转动速比关系,才能加工出所需要的齿轮齿形。
二、螺纹加工
牙形种类和尺寸规格多,应用广泛。
如联接螺纹分为普通螺纹、英制螺纹和管螺纹等;传动螺纹分为梯形螺纹、锯齿形螺纹、矩形螺纹等。
公差等级共分12级,其中1级最高、最难以加工,12级最低。
应用的螺纹公差等级大都在4-8级之间,3级以上和9级以下的很少应用。
1.车螺纹
螺纹车刀,车床,P261图11-34所示。
工件与刀具间的运动要严格按一定的速比关系进行,即工件每转一转,刀具沿工件轴线方向相应移动一个螺距(单头螺纹)或导程(多头螺纹)。
除大量加工细长的丝杠车床外,一般零件上的螺纹都可在普通车床上加工。
工艺特点:
⑴适应性强
车床上能加工各种形状和尺寸的螺纹,且刀具简单,费用低。
⑵加工精度较高
由于车削过程连续、平稳,加工精度一般可达6级,Ra<1.6μm,加工精度最高达4级,Ra<0.8μm。
⑶生产率较低
走刀次数多,对刀、测量都比较费时。
当采用螺纹梳刀车削螺纹时,由于刀齿较多,生产率有所提高。
⑷对工人技术水平要求高
螺纹车刀的刃磨、安装要求较严格,车刀在每次走刀后退回时要求操作者动作要特别熟练、快捷,所以操作者要有较高的技术水平。
应用:
普通车床车螺纹适于尺寸较小的非标准螺纹和尺寸较大、精度较高、小批量的螺纹加工。
2.铣螺纹
专门螺纹铣床,螺纹铣刀P262图11-35
铣刀齿多、转速快、切削量大,故比车螺纹生产率高。
螺纹铣削的加工精度可达7级,Ra可达1.6μm。
⑴盘状铣刀铣螺纹
安装铣刀和工件时,铣刀轴线与工件轴线必须成一λ角度(螺纹的螺旋升角)。
盘状铣刀铣螺纹主要用于精度不太高的较大螺距的长螺纹的终加工和较精密螺纹的预加工。
⑵梳状铣刀铣螺纹
梳状铣刀可以看作是多个盘形铣刀的组合。
加工时,铣刀转动为切削运动,工件只需转一转,同时铣刀沿工件轴线方向移动一个螺距(当铣刀长度和工件长度接近时),即可铣出整个螺纹。
实际中考虑到铣刀有切入、退出等运动,工件需多转一定的角度。
梳状铣刀加工螺纹效率高,主要用于加工螺旋升角较小,牙形为三角形的短尺寸螺纹。
3.用丝锥、板牙加工螺纹
⑴攻丝
丝锥似纵向开有沟槽(形成切削刃和容屑槽)、头部带有锥度(切削部分)的螺杆。
攻丝前需按要求尺寸加工出螺纹底孔。
⑵套扣
板牙是加工或校正外螺纹用的刃具。
板牙外形似钻有三个孔(形成切削刃和容屑槽)的螺母,且孔的端部具有30°~60°锥角,以起到切削前引导定位作用。
用板牙加工螺纹又称套扣。
可以在车床上进行也可以在钻床上进行。
特点:
操作简单,生产率高,加工费用低。
加工精度不太高,攻丝为6-8级,套扣为7-8级,表面粗糙度Ra为1.6-6.3μm。
应用:
用于各种批量加工公称直径小于16mm的标准螺纹和较大批量加工非标准尺寸螺纹。
4.滚压法加工螺纹
滚压加工螺纹属于无屑加工。
⑴滚丝P263图11-39
用滚丝轮在滚丝机上加工螺纹称为滚丝。
⑵搓丝P263图11-40
用搓丝板在搓丝机上加工螺纹称为搓丝。
滚压螺纹主要特点:
生产率特别高,滚丝每分钟可加工10-60件,搓丝比滚丝更高,每分钟可加工120件。
加工精度可达3~6级,表面粗糙度Ra为0.2-0.8μm。
滚压螺纹纤维组织连续,密度大、强度高、耐用,并且设备简单,材料利用率高。
滚压螺纹的缺点是受滚丝轮和搓丝板齿面硬度的限制,只适于加工硬度不高、塑性好、中小直径和齿高不太大的外螺纹,不适加工内螺纹、方牙螺纹和薄壁零件上的螺纹。
5.磨螺纹
磨螺纹是螺纹的精加工方法,采用轮廓经过修整的砂轮在专门的螺纹磨床上进行,其加工精度可达3-4级,表面粗糙度可控制在Ra0.2-0.8μm。
由于螺纹磨床结构复杂,精度高,加工效率低,加工费用高,所以磨螺纹一般用于加工硬度高的精密螺纹,如精密丝杠,测量用螺纹、螺纹丝锥等。
三、齿轮加工
摆线形面、渐开线形面,最常见的是渐开线形面。
1.渐开线的形成及齿轮主要参数
⑴渐开线的形成P264图11-41图11-42
齿轮转动时,渐开线上各点圆周线速度方向与该点法线方向的夹角称为压力角。
同一条渐开线上各点压力角不同,渐开线与齿轮分度圆(直径为d)相交点的压力角称为齿轮的压力角,标准渐开线齿轮的压力角α为20°。
db=dcosα=mzcosα
⑵齿轮的主要参数
模数,齿数,压力角。
2.圆柱齿轮的精度
《渐开线圆柱齿轮精度》国家标准(GB10095—1988)
⑴传递运动的准确性
要求齿轮在一转范围内,其最大转角误差限制在一定范围内,以保证从动件与主动件协调,速比变化小,传递运动准确。
⑵传动的平衡性
要求齿轮传动瞬时传动比变动不大,因为瞬时传动比的突变会引起齿轮传动冲击、振动和噪声。
⑶载荷分布的均匀性
要求齿轮啮合时齿面接触良好,以免引起应力集中,造成局部磨损或断裂,影响齿轮使用寿命。
⑷传动侧隙
要求齿轮在啮合时,轮