钢结构方案.docx
《钢结构方案.docx》由会员分享,可在线阅读,更多相关《钢结构方案.docx(12页珍藏版)》请在冰豆网上搜索。
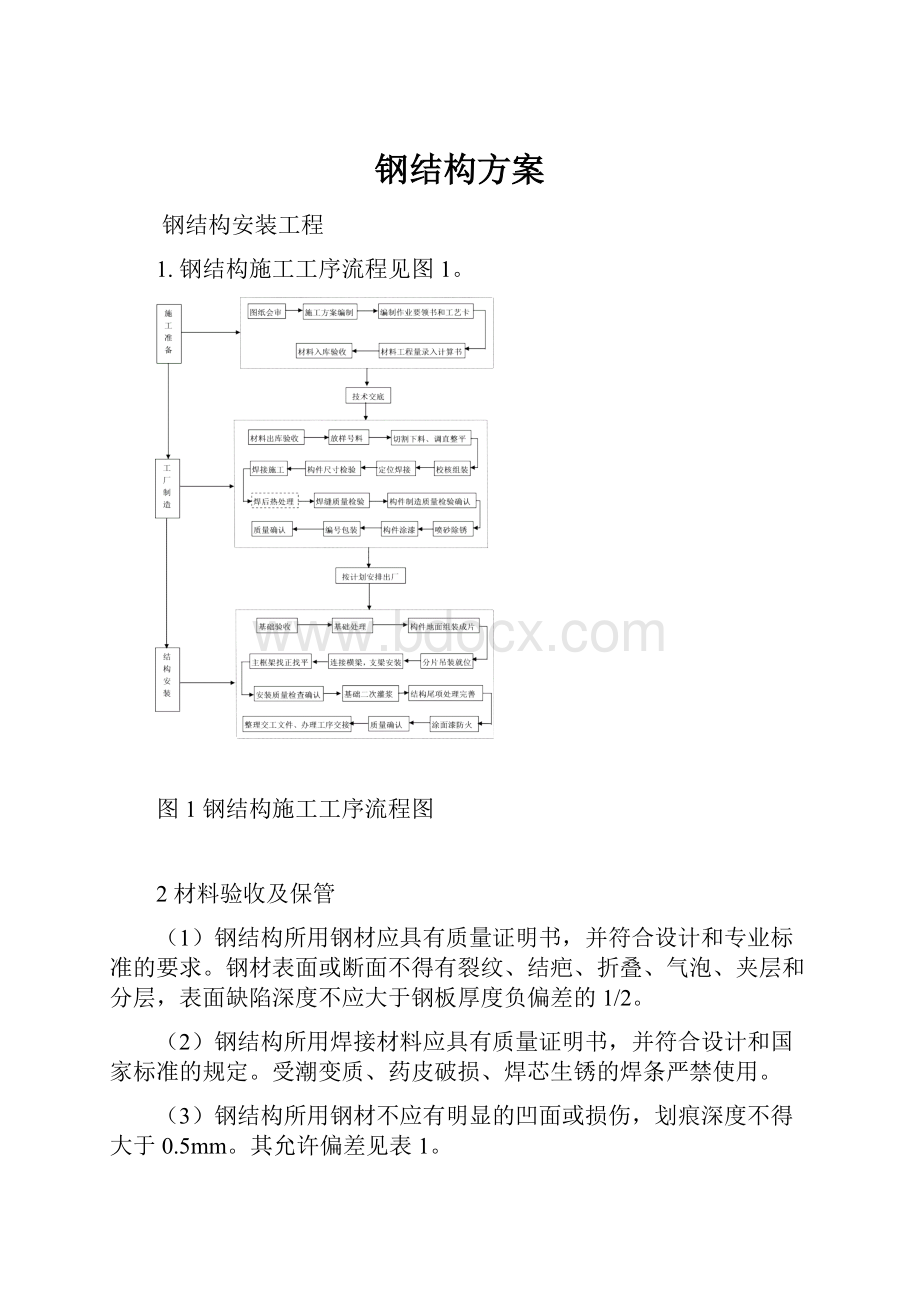
钢结构方案
钢结构安装工程
1.钢结构施工工序流程见图1。
图1钢结构施工工序流程图
2材料验收及保管
(1)钢结构所用钢材应具有质量证明书,并符合设计和专业标准的要求。
钢材表面或断面不得有裂纹、结疤、折叠、气泡、夹层和分层,表面缺陷深度不应大于钢板厚度负偏差的1/2。
(2)钢结构所用焊接材料应具有质量证明书,并符合设计和国家标准的规定。
受潮变质、药皮破损、焊芯生锈的焊条严禁使用。
(3)钢结构所用钢材不应有明显的凹面或损伤,划痕深度不得大于0.5mm。
其允许偏差见表1。
(4)钢材应按钢种、钢号和规格分别验收、标识、堆放和保管,并做好收发台帐和管理工作,螺栓、螺母的保管应做好防锈蚀。
(5)运用计算机区域网络建立材料台账,对材料的入库、发放、使用进行全过程控制。
钢材的允许偏差表1
项目
允许偏差
图例
钢板的
局部平
面度
δ≤14(mm)
1.5(mm)
δ>14(mm)
1.0(mm)
型钢弯曲矢高
L/1000
且≤5.0(mm)
角钢肢的垂直度
b/100双肢栓接
角钢的角度不得
大于90°
槽钢翼缘对腹板
的垂直度
b/80(mm)
工字钢、H型钢翼缘
对腹板的垂直度
b/100
且≤2.0(mm)
3钢结构制造
(1)利用计算机软件放样,放样、号料应根据工艺要求预留制作及组装时的焊接收缩余量及切割、刨边和铣平等加工余量。
样板应经质量检查部门确认合格后方可使用。
(2)H型钢结构的节点板,加劲板,梁端盖板及异形板均应采用计算机样板号料。
(3)放样和样板的允许偏差应符合表2的规定。
放样和样板的允许偏差表2
项目
允许偏差
平行线距离和分段尺寸
±0.5mm
对角线差
1.0mm
宽度、长度
±0.5mm
孔距
±0.5mm
加工样板的角度
±20
(4)号料的允许偏差应符合表3的规定
号料的允许偏差表3
项目
允许偏差(mm)
零件外形尺寸
±1.0
孔距
±0.5
(5)零、部件要求采用机械加工;采用半自动或自动切割机切割时。
其允许偏差应符合表4的规定。
气割的允许偏差表4
项目
允许偏差(mm)
零件宽度、长度
±3.0
切割面平面度
0.05δ且≤2.0
割纹深度
0.2
局部缺口深度
1.0
(6)钢柱底板地脚螺栓孔、吊车梁螺栓孔等,应采用机械方法加工,加工成型的螺栓孔允许偏差见表5。
螺栓孔允许偏差表5
项目
允许偏差(mm)
直径
01.0
圆度
2.0
垂直度
003且≤2.0
螺栓孔孔距允许偏差见表6。
螺栓孔孔距允许偏差表6
项目
允许偏差(mm)
≤500
501~1200
1200~3000
>3000
同一组内任意两孔间距
±1.0
±1.5
相邻两组的端孔间距
±1.5
±2.0
±2.5
±3.0
(7)螺栓孔的允许偏差超过上述规定时,不得采用钢块填塞,可采用与母材材质相匹配的焊条补焊后重新制孔。
(8)板材、型材的拼接,应在组装前进行,所有板材、型材的拼接缝均采用45o斜接。
焊接H型钢翼缘板拼接焊缝和腹板拼接焊缝间距应大于200mm,腹板、翼板对接的允许偏差见表7。
焊接坡口采用氧乙炔焰切割,并用砂轮清除坡口表面氧化皮,坡口型式见表8。
腹板、翼板对接的允许偏差表7
项目
允许偏差(mm)
厚错边量
Δδ≤0.1δ且≤1.0
宽度错边量
腹板
≤1.0
翼板
≤2.0
坡口型式选用表表8
基本型式
选用厚度(mm)
基本尺寸(mm)
6~16
6~9
9~16
55o5o
55o5o
b
11
21
p
1+10
21
16~60
16~60
b
21
p
21
(9)构件组对采取就近原则,避免构件二次倒运。
构件组装前,零、部件应经检查合格。
连接接触面和沿焊缝边缘每边30~50mm范围内的铁锈、毛刺、污垢应清除干净;构件的组装应在部件组装、焊接、矫正后进行。
构件组装顺序应根据结构型式、焊接方法及焊接的顺序等因素确定,尤其要考虑焊接变形的影响,避免出现组焊后产生不可弥补的变形。
构件焊接连接组装的允许偏差见表9。
构件焊接连接组装的允许偏差表9
项目
允许偏差(mm)
图例
对口错边()
/10且≤3.0
间隙(a)
±1.0
搭接长度(a)
±5.0
缝隙()
1.5
高度(h)
±2.0
垂直度()
b/100且≤2.0
中心偏差(e)
±2.0
型
钢
错
位
连接处
1.0
其它处
2.0
箱形截面高度(h)
±2.0
宽度(b)
±2.0
垂直度()
b/100且≤3.0
(10)结构件制造完成后,应立即进行质量检查确认,合格后按构架的名称和件号编号,并按构架的类别按顺序堆放和保管,以便于结构件的顺利出厂。
4钢结构安装
(1)钢结构安装前应对建筑物的定位轴线、基础轴线和标高、地脚螺栓位置等进行检查,并办理书面交接验收手续。
基础验收应由总承包商或监理单位会同土建施工单位和安装施工单位联合进行。
(2)基础支承面、地脚螺栓的允许偏差应符合表10规定。
支承面、地脚螺栓的允许偏差表10
项目
允许偏差(mm)
支承面
标高
±3.0
水平度
L/1000
地脚螺栓
螺栓中心偏移
5.0
螺栓露出长度
+20.0
0
螺栓长度
+20.0
0
预留孔中心偏移
10.0
(3)钢构件运输时,应根据长度、重量选用车辆,钢构件在车辆上的支点,两端伸出的长度及绑扎方法均应保证钢构件不产生变形,不损伤涂层。
(6)应按种类、型号、安装顺序分区存放并做好标识,钢构件存放时应采取措施防止变形。
(7)钢结构安装、校正时,应根据风力、温差、日照等外界环境和焊接变形等因素的影响。
采取相应的调整措施。
(8)钢结构的柱、梁、支撑就位后,应立即进行校正,固定,并应形成稳定的空间体系,防止变形。
(9)钢柱安装时,每节柱的定位轴线应从地面控制轴线进接引上,不得从下层柱轴线引上。
(10)钢结构及其平台、梯子安装的允许偏差符合表11、12的规定。
钢结构安装的允许偏差表11
项目
允许偏差(mm)
图例
柱轴线对行列定位轴线
的平行位移和扭转位移
5.0
柱基准点
标高
有吊车梁
的柱
-5.0~+3.0
无吊车梁
的柱
-8.0~+5.0
柱垂直度
高度H≤10m
高度H>10m
10
H/1000且≤25.0
梁柱层间对角线之差
(L1-L2)
5.0
相邻柱间距离(a)
±5.0
梁标高()
±3.0
梁水平度()
L/1500且≤5.0;
L为梁长
梁中心位置偏移()
±2.0
相邻梁间距(b)
±4.0
平台、钢梯子和防护钢栏杆外形尺寸允许偏差表12
项目
允许偏差(mm)
平台长度和宽度
±5.0
平台两对角线差|L1-L2|
6.0
平台表面平面度(1m范畴内)
6.0
横梁长度(l)
±5.0
钢梯宽度(b)
±5.0
钢梯安装孔距离(a)
±3.0
横梁纵向挠曲矢高
L/1000
踏步间距(a1)
±5.0
栏杆高度
±5.0
栏杆立柱间距
±10.0
5普通钢结构施工工艺技术
(1)普通钢结构宜在地面拼装成片状或网状构架后吊装,就位后立即把紧地脚螺栓,并用揽风绳临时固定,待钢结构的梁、支撑就位后,立即进行校正,固定,并应形成稳定的空间体系,防止变形。
(2)钢柱脚宜采用座浆法安装。
在基础中央设置一块钢垫板(厚度12~16mm,规格约为100*100mm),用无收缩水泥或CGM浆料按图纸标高找正、找平,预制好的构件吊装就位后,找正、找平、把紧螺栓,见图2。
(3)钢结构安装形成空间刚度单元后,应及时对柱底板和基础顶面的空隙采用无收缩水泥二次浇灌。
灌浆时应确保灌满灌实。
6.大型钢结构施工工艺技术
(1)大型钢结构应根据构件的规格重量及机械的吊装能力采用单柱吊装或拼装成片状后吊装,钢结构的柱、梁、支撑就位后,立即进行找正,固定地脚螺栓,并应形成稳定的空间体系,防止变形。
(2)钢柱脚采用垫板支承。
垫板应设置在靠近地脚螺栓的柱脚底板加劲板或柱肢下,每根地脚螺栓侧应设1~2组垫板,每组垫板不多于5块。
垫板与基础面和柱底面的接触应平整、紧密。
二次灌浆前应将垫板间焊接固定,见图3。
(3)钢结构安装形成空间刚度单元后,及时对构架安装几何尺寸进行检查确认,合格后立即柱底板与基础顶面的空隙采用无收缩水泥灌浆,灌浆时应确保灌满、灌实。
图3钢结构垫铁设置示意图