10万立方油罐正装法施工课件.docx
《10万立方油罐正装法施工课件.docx》由会员分享,可在线阅读,更多相关《10万立方油罐正装法施工课件.docx(43页珍藏版)》请在冰豆网上搜索。
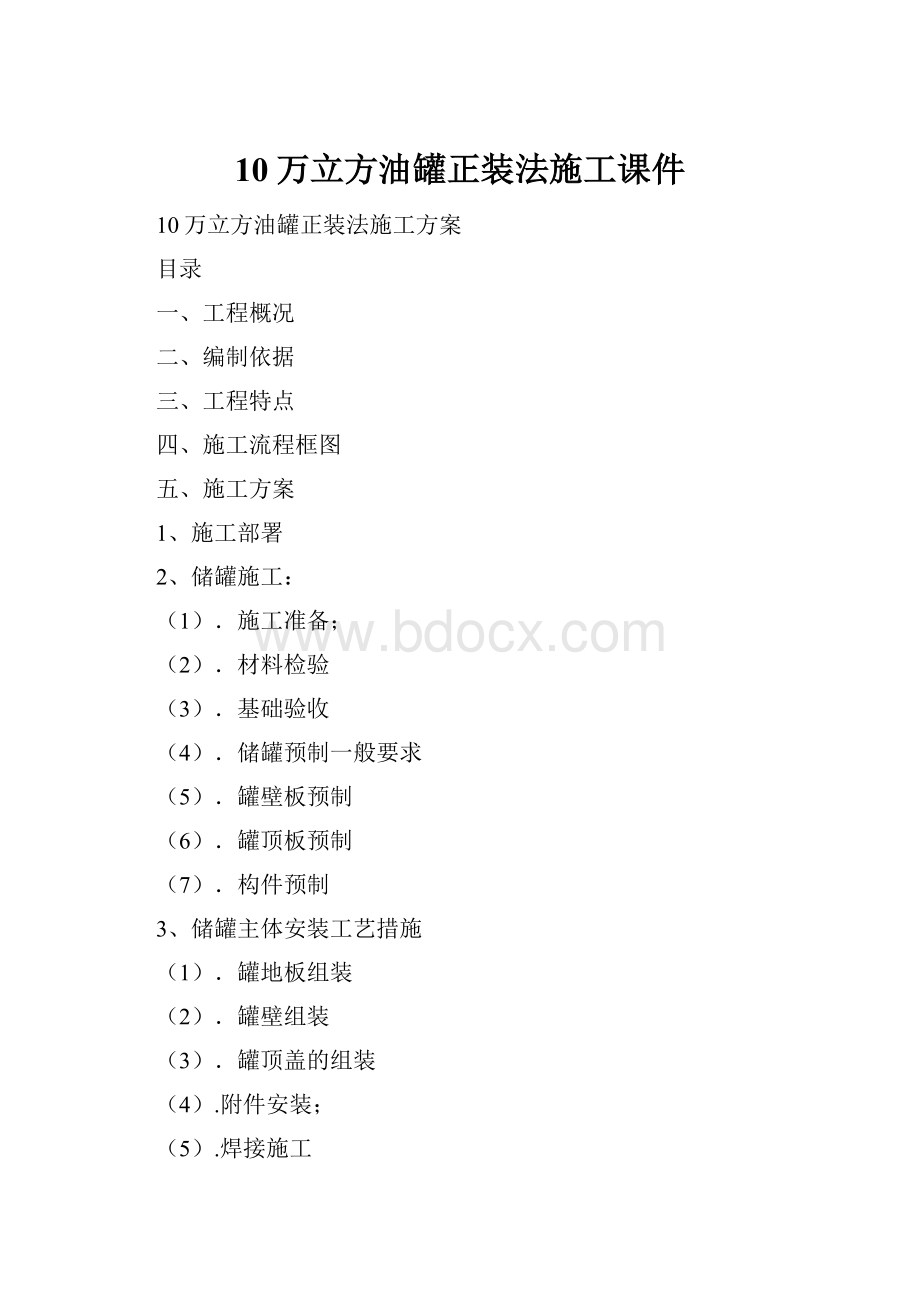
10万立方油罐正装法施工课件
10万立方油罐正装法施工方案
目录
一、工程概况
二、编制依据
三、工程特点
四、施工流程框图
五、施工方案
1、施工部署
2、储罐施工:
(1).施工准备;
(2).材料检验
(3).基础验收
(4).储罐预制一般要求
(5).罐壁板预制
(6).罐顶板预制
(7).构件预制
3、储罐主体安装工艺措施
(1).罐地板组装
(2).罐壁组装
(3).罐顶盖的组装
(4).附件安装;
(5).焊接施工
(6).焊接顺序
4、充水试验
5、防腐工程
6、绝热工程
7、施工机械及机具
六.安全管理与安全保障
七;安全技术管理措施
八.主要施工用手段用料
10万立方油罐安装方案
一、工程概况
1.简述
本工程为新增2台100000m3油罐,本工程在2009年 月 日开工,计划于2009年 月 日竣工,单台罐重量约为2100吨。
本施工方案针对承担两台罐施工的工况进行编制。
本次施工新建2台100000立方汽油罐制作安装;油罐顶板及底板(除边缘板)均为搭接,罐底边缘板、罐壁立缝、环缝为对接。
其主体结构形式为立式油罐,该结构的主要特点是,焊接量大、焊接质量要求高、焊接变形控制要求严,因此要求施工人员严格按照施工方案、施工技术交底卡进行施工。
确保油罐优质、高效、按期完成。
二、编制依据
1设计施工图;
2合同、招标文件;
3GBJ128-90《立式圆筒钢制焊接油罐施工及验收规范》;
4GB50235-97《工业金属管道工程质量验收规范》;
5GB50236-98《现场设备、工业管道焊接工程施工验收规范》;
6SH3501-1997《石油化工剧毒、可燃介质管道施工及验收规范》;
7JB4730-94《压力容器无损检测》;
8SH3046-923《石油化工立式圆筒形钢制焊接储罐设计规范》;
9SH3048-1999《石油化工钢制焊接储罐设备抗震设计规范》;
10 Q/HD0026-1995《立式圆筒钢制焊接储罐铠装式外防腐保温工程施工及验收规范》;
11GB4053.2-1993《固定式钢斜梯》;
12GB8923-88《涂装前钢材表面锈蚀等级和除锈等级》;
13SH3530-93《石油化工立式圆筒形钢制储罐施工工艺标准》;
14公司质量管理手册及程序文件
15罐体基本参数
容积(m3)
内径×壁厚
(米)
材质
设计温度
设计压力(MPa)
介质
100000
Φ80
(8~25)
Q235-B
16MnR
常温
常压
汽油
16工程施工总工期:
2台10×104m3双盘浮顶油罐 个月。
17主要工程量
单台罐工程量见下表:
名称及工程内容
规格
数量
重量
(T)
材质
备注
底 板
边缘板
钢板20×1600×6300
40张
63.320T
SPV490Q
中幅板
钢板11×3000×14800
111张
425.57
Q235-A.F
小计(T):
488.894
罐
壁
板
第一层
钢板32×2440×12600
17张
131.291
SPV490Q
钢板32×2440×6300
6张
23.168
SPV490Q
第二层
钢板27×2440×12600
20张
130.320
SPV490Q
第三层
钢板21.5×2440×12600
20张
130.780
SPV490Q
第四层
钢板18.5×2440×12600
20张
89.300
SPV490Q
第五层
钢板15×2440×12600
20张
72.400
SPV490Q
第六层
钢板12×2440×12600
20张
57.920
SPV490Q
第七层
钢板12×2440×12600
20张
57.920
SPV490Q
第八层
钢板12×2400×12600
20张
56.980
Q235-A
第九层
钢板12×2400×12600
20张
56.980
Q235-A
包边角钢
[100×10
20张
4.728
Q235-A
小计(T):
784.787
浮
顶
主要钢板
钢板4.5×1800×9000
583张
334.000
Q235-A.F
主要钢板
钢板4.5×1600×4600
182张
47.320
Q235-A.F
主要钢板
钢板4.5×1400×6500
20张
6.440
Q235-A.F
主要钢板
钢板4.5×1300×6300
46张
13.294
Q235-A.F
主要钢板
钢板6×1600×9000
15张
10.170
Q235-A.F
杵架
约50.0
小计(T):
461.224
其它
转动浮梯、平台、盘梯、抗风圈、加强圈
165.0
单台罐金属总重量约(T):
1900.000
名称及工程内容
工程量
主要附件
进口浮顶排水系统(两条8#排水管)
1套
进口一次密封(机械式)
1套(250m)
进口二次 密封
同上
刮蜡装置(与一次密封配套进口)
同上
搅拌器(进口)
3台
三、工程特点
100000m3双盘浮顶储罐的主要设计参数如下:
储罐高度(H)21800mm 内 径:
80000mm
有效容积:
100536m3 储 物:
原油
设计压力:
常压 设计金属温度:
—150C
使用储物温度:
+500C储罐由九带壁板组成,板厚由下至上分别为32mm,27mm,21.5mm,18.5mm,15.0mm,12.0mm,12.0mm,12..0mm,12.0mm,其中下七带板的材质为SPV490Q,最上二带板的材质为Q235-A。
底板为T字型排板,对接而成。
罐底边缘板材质为SPV490Q,厚度为20mm,中幅板材质为Q235-A,厚度为10mm,浮顶为Q235-A.F。
罐壁外设2道加强圈和2道抗风圈。
罐内壁底部采用喷砂除锈后涂防腐漆,罐外壁防腐保温,外包压型彩板。
罐设有中央排水管、集水坑、量油管、罐壁人孔,搅拌器孔、浮顶人孔,船舱人孔,通风阀,呼吸阀,紧急排水管,消防现场,加热系统,刮蜡系统,密封和挡风系统,转动浮梯,踏步盘梯等。
18、气象条件
该地区年平均温度为10.50C,夏季平均温度为22.40C,冬季平均温度为0.90C。
相对湿度为65%。
年正常施工工期300天以上,冬雨季若采取相应措施后,可实现全天候施工。
19、工程水、电及其它动力供应条件
现场施工用电,用水由业主提供电源和水源,施工用压缩空气由施工单位配置空压机。
现场施工用水因经过一个冬季,因此应在现场埋地敷设,埋深应超过800mm。
四、施工流程框图
图3-1施工流程图
五、施工方案
1、施工部署
为保证工程在2009年 月份罐区工程投用,必须发挥我公司多年参加施工建设的管理经验,精心组织,加强协调和管理,充分发挥我公司机具装备的优势和职工一专多能的能力,进一步激励广大职工发扬团结、开拓、求实、奉献的“十建精神”,实现工程的宏观控制目标。
2、根据以上工程的具体情况,工程将分为三个主要施工阶段进行部署,各个施工阶段的主攻目标和主要形象进度见表
基础验收→底板铺设、焊接→第一节壁板组焊→第二节壁板组焊→大角缝及龟甲缝组焊→浮船安装开始→第三节壁板组焊→第四节壁板组焊→第五节壁板组焊→第六节壁板组焊→第二道加强圈组焊→第七节壁板组焊→第八节壁板组焊→第一道加强圈组焊→第九节壁板组焊→第一道抗风圈组焊接→浮船及浮船附件安装完毕→包边角钢及护栏组焊→其它附件安装→充水试验→清罐→交工验收。
主要形象进度表
工期
第一施工阶段
(第一月)
第二施工阶段
(第二~四月)
第三施工阶段
(第五、六、七月)
主攻目标
施工准备机具进现场主抓油罐预制底板焊接完
力保油罐
主体安装完
油罐扫尾充水试验、防腐保温工程竣工验收
进度要求
1.施工暂设施工完
2.熟悉图纸、编制施工组织设计和施工方案
3.油罐浮顶预制
4.盘梯、浮梯预制
1.油罐壁板安装完
2.浮顶焊接完,浮舱气密完
3.油罐附件安装完
1.油罐附件安装
2油罐充水试验
3浮顶支柱调整
4油罐内清扫封闭
5油罐防腐保温完
2、 储罐施工:
1.施工准备;
a.根据设备制作图样,编写详细的施工方案,编制详细的材料、配件预算进行施工材料准备。
b.准备现场临时加工厂:
安装好卷板机、剪板机、电焊机、空压机等机械设备。
c.搭设好预制钢平台,并根据方案要求制作工装、卡具和器具,所用计量器具应全部调校合格并在有效期内。
d.组织施工作业人员认真熟悉施工图样,进行详细的技术交底,了解施工方法、技术要求。
2.材料检验
a现场制作设备用钢板、配件、钢管、紧固件等,应具有质量合格证明书,当无合格证或对合格证有疑问时,应对材料、配件进行复验,合格方可使用。
b焊接材料(焊条、焊丝)应具有质量合格证书。
其合格证检测内容和结果应符合相应国家标准规定,否则应进行复验,合格方可使用。
C材料表面锈蚀、薄量、划痕深度与钢板实际负偏差之和,应符合响应国家标准规定.存放过程中,应防止钢板产生变形,严禁用带棱角的物件下垫。
D设备的小型接管、法兰、人孔、手孔、紧固件等配件,均在专业加工厂加工成品交付现场使用,配件交付时应具有产品质量合格证。
3.基础验收
底板铺设前,应先会同有关部门对罐基础整体几何尺寸、表面标高、坡度等进行验收
(1)基础中心标高允许偏差为±20mm
(2)支撑罐臂的基础表面,每3m弧长内任意两点的高差不得大于12㎜.
(3)沥青砂层表面应平整密实,无明显的隆起、凹陷及贯穿裂纹。
(4)验收完毕应办理基础中间交接手续。
4.储罐预制一般要求
(1)放样、下料前应根据设备制作图样进行排版,按排版图进行放样和下料。
(2)材料放样应采用1:
1实样放样,放样时应根据工艺要求预留焊接缩和加工裕量。
(3)板材下料可采用火焰切割下料,机械剪切下料。
(4)板材边缘加工面应平滑,不得有夹渣、分层、裂纹及熔渣等缺陷.火焰切割坡口产生的表面硬化层应磨除。
(5)罐在预制放样、下料组装及检验过程中所使用的样板应符合下列规定:
—样板采用0.5~0.7㎜的镀锌铁皮制作,样杆采用1.5~2㎜厚,宽30~40㎜的扁铁制作。
—当构件的曲率半径小于或等于12.5m时,弧形样板的弦长不得小于1.5m。
曲率半径大于12.5m时弧形弦长不得小于2m。
—直线样板的长度不得小于1m。
—测量焊缝角变形的样板,其弦长不得小于1m。
—样板、样杆周边应光滑整齐。
弧形大样板为避免其变形,可作加固处理。
—样板制作完毕后,用铅油在样板上标出正、反面及所代表的的构件名称、部位、规格,并妥善保管。
—号料前,应核对钢板材质、规格,钢板放置要平。
在钢板上定出基准线,然后划出长度、宽度的切割线,经检查后,在切割线上打上样冲眼,并用色笔作出标记,在切割线内侧50㎜处划出检查线,同时在钢板上角标明罐号、排版编号、规格与边缘加工等符号。
底圈罐壁与罐底边缘板角焊接缝的坡口型式应严格按照图纸要求进行施工。
B.罐底板排版图应符合下列要求:
—外圈边缘板直径比设计直径放大0.1℅—0.2%。
—边缘板沿罐底半径方向的最小尺寸不得小于700㎜。
—中幅板宽度不得小于1m,长度不得小于2m。
—底板任意相邻焊缝之间距离不得小于200㎜。
—弓形边缘板尺寸的测量部位如图5-3,其允许偏差应符合表5-2的要求。
图5—3罐底板弓形边缘板测量图
弓形边缘板尺寸允许偏差(㎜) 表5-2
测量部位
允许偏差
长度AB、CD
±2
宽度AC、BD、EF
±2
对角线之差|AD-BC|
≤3
C.中幅板尺寸允许偏差应符合表5-3的要求。
中幅板(罐壁板)尺寸允许偏差(㎜) 表5-3
测量部位
环缝对焊(㎜)
板长AB(CD)≤10m
环缝搭接(㎜)
宽度AB、BD、EF
±1
±2
长度AB、CD
±1.5
±1.5
对角线之差AD-BC
≤2
≤3
直线度
AC、BD
≤1
≤1
AB、CD
≤2
≤2
中幅板(罐壁板)尺寸测量部位
D.罐底板铺设前,要清除表面的泥土、油污、其下表面涂刷两边沥青防锈漆,四周留出50㎜不予涂刷。
E.底板采用对接接头,条形垫板。
F.中幅板焊接时应先焊短焊缝,第一层焊道应采用分段退焊或跳焊法。
5.罐壁板预制
(1)壁板预制前应绘制排版图,排版图应符合下列要求:
—各圈壁板的纵缝宜向同一方向逐圈错开,其间距宜为板长的1/3,且不小于500㎜。
—底圈壁板纵向焊缝与罐底边缘板的对接焊缝之间的距离不得小于200㎜。
—罐壁开孔接管或开孔接管补强板外缘与罐壁纵向焊缝之间距离不得小于200㎜;与环向焊缝之间的距离不得小于100㎜。
—包边角钢对接接头与罐壁纵向焊缝之间的距离不得小于200㎜。
—壁板宽度不得小于500㎜,长度不得小于1m。
—壁板宽度变更时,各圈壁板厚度不得小于壁板变化圈上相应高度的厚度。
(2)罐壁板采用净料法进行预制,壁板的周长按下式进行计算:
L=∏(Dī+f)-nb+na+∑△………………………
(1)
式(1)中:
L—壁板周长(㎜)
Di—罐内径(㎜)
f—罐壁厚(㎜)
b—对接接头间缝(㎜)
a—每条焊缝收缩量(㎜)一般为2~3㎜
△—每块壁板长度偏差值(㎜)
n—单圈壁板的数量
(3)壁板下料允许偏差与底板中幅板相同。
(4)壁板应在滚板机上进行卷制,辊的轴线与壁板长度相互垂直,并随时用样板检查。
壁板卷制后应直立在平台上,水平方向用弧样板检查,其间嬉不得大于4㎜。
垂直方向用直线样板检查,其间嬉不得大于1㎜。
(5)在卷制壁板时,应用吊车或吊装机具配合,防止在卷制过程中使已卷成的圆弧回直或变形,卷制好的壁板应用专用台架运输、存放。
(6).罐顶板预制
(1)罐顶板预制时要绘制排版图,且应符合下列要求;
———顶板任意相邻焊缝的间距大于200㎜
———单块顶板本身的拼接,可采用对接。
(2)拱顶的顶板及加强筋,应进行成行加工。
加强筋用弧形样板检查,其间隙不得大于2㎜,加强筋与顶板组焊时,应采取防变形措施。
加强筋的拚接采用对接街头时,应加垫板,且必须完全焊透。
(7).构件预制
(1)加强圈、包边角钢等弧形构件加工成型后,用弧形样板检查,其间隙不得大于2㎜,放在平台上检查,其翘曲变型不得超过构件长度的0.1﹪且不大于4㎜。
(2)热炜成型的构件不得有过烧、变质现象,其厚度减簿量不应超过1㎜。
3、储罐主体安装工艺措施
(1).罐地板组装
(1).罐底板铺设前,要清除表面的泥土、油污、其下表面涂刷两边沥青防锈漆,四周留出50㎜不予涂刷。
(2)罐底板由中幅板和边缘板组成,罐底板采用对接接头,条形垫板。
基础验收合格证,确定方位画出中心线,得出中点、画出垫板,边缘板安装位置线,其中边缘板安装铺设按设计直径和基础坡度长度外加收缩余量来确定半径。
边缘板铺设间隙外侧为6㎜,内侧为8㎜。
(3)板铺设时,按照排版图从中心向四周铺设。
边缘板依安装位置线铺设,垫板与相邻两块底板中的一块先点焊,底板与垫板应贴紧,其间隙不大于1㎜。
(4)幅板组对时,其间隙控制在4—6mm之间。
地板与垫板之间的点焊应按焊接技术措施规定的次序严格执行。
(5)幅板焊接时,应先焊短焊缝,后焊长焊缝,第一层焊道应采用分段退焊或跳焊法。
搭接角焊缝至少焊两遍。
(6)底板焊接完后,检查凹凸度,凹凸变形的深度不应大于变形长度的2%,且不应大于50mm,并对所有焊接进行真空试验,试验负压值应符合图纸要求。
(2).罐壁组装
(1)壁板采用正装组装。
随着工程施工进度对基础进行沉降观测,并做好记录。
发现问题及时停止施工,处理好后再继续施工。
(2)壁板组装前,应对预制的壁板进行复验,按排版图号对号入座,需要校正时,防止出现锤痕。
(3)壁板组装时应保证内表面平齐,错边量应符合表5-4要求。
内表面错边量允许偏差 表5-4
项目
板后(mm)
错差量允许偏差(mm)
纵向焊缝
δ≥10
1.5
纵向焊缝
δ<10
1/10δ且不大于1.5
环向焊缝
δ≤8
1.5
环向焊缝
δ>8
1/5δ且不大于3
组装焊接后,罐壁的局部凹凸变形要小于3mm,焊缝的角变形用1m长的弧形样
板检查要≤10mm。
顶圈壁板的组装允许偏差见表5-5所示。
顶圈壁板的组装允许偏差 表5-5
项 目
允许偏差(mm)
相邻两壁板上口水平度
2
整个圆周上任意两点水平度
6
壁板的铅垂度
3
顶圈壁板1m高处内表面任意点半径
±13
(4)罐壁的焊接,应先焊纵焊缝,后焊环焊缝。
当焊完相邻两圈壁板的纵焊缝后再焊其间的环焊缝。
在壁板组立前,在存运胎架上安装好帽,龙门板及蝴蝶板,如右图示。
壁板的吊装用履带吊车进行,并使用吊梁。
第一带壁板组对前,按施工图划线安装组对档板。
(5)壁板逐张组对,每张安装2个加减丝以调节壁板垂直度。
安装纵缝组对卡具,及方楔,以将壁板固定。
整圈壁板全部组立后调整壁板立纵组对错边量,上口水平度及壁板的垂直度符合以要求,并检查1m高处任意半径的偏差不超过±32mm。
二至九带板的组装方法参照第一带壁板的组装。
环缝应安装组对用龙门板、槽钢。
如图。
(6).组装第二带板前在第一带板上搭设简易脚手架,以后组对上一带板时在下带板上搭设同样的脚手架,在罐人孔处搭设斜梯,以供上下脚手架。
在浮顶施工时将浮顶下面的斜梯拆除,浮顶上面的斜梯逐层搭设,每台罐三层脚手架循环使用。
(7)壁板焊接先焊立缝,再焊环缝,立缝焊接前,先焊上定位龙门板,见左图示,然后拆下立缝组对卡具。
立缝的坡口型式是:
24.5mm及以上厚的壁板立缝为X型坡口,其余V型坡口。
焊接时,先焊外部,后焊内部,立缝下端150mm焊缝采用手工焊,其余为自动焊,立缝焊接上端加熄弧板,见左图示。
大角焊缝焊接前安装防变形卡具如左下图示。
焊缝内外侧手工打底,用角焊自动焊机(LT-7)焊接内外盖面焊缝,同时外部附加钢板,作为焊机运行的轨道。
其焊接顺序为:
内外侧第一道手工打底——外侧自动焊——拆内侧固定块及方楔子——内侧自动焊。
1
环缝焊接均采用埋弧自动焊方法进行。
15mm以下壁板环缝为单V型坡口,18mm以上为X型坡口,均需要双面焊接,先焊外侧焊缝,外侧焊后,罐内侧卡具拆除,用自动碳弧气刨方法进行清根,然后用砂轮打磨,如果清根深度达到焊缝厚度的2/3,要用手工焊方法进行补焊,清理完后,进行内侧环缝焊接。
(8)圈壁板的内半径按下式计算:
Rb=(RI+nα/2απ)cosθ ……………………
(2)
式
(2)中Rb——顶圈壁板安装内半径(mm)
Ri——罐内半径
N——顶圈壁板立缝数量
α——每条立缝焊接收缩量(mm)
θ——基础坡度夹角。
(9)按顶圈壁板安装内半径,在罐底板上划出圆周线及每张壁板上的安装位置线,并在安装圆内侧100mm处划出检查圆线,打上样冲眼,并用白油漆做出标记。
(10)圆壁板安装圆周线,每隔1m在内侧焊上挡板,在安装圈外侧60mm处同样焊上挡板,作为组装卡具用限位。
(11)罐壁组焊完毕后其总体几何尺寸应符合表5-6的要求。
罐体总体几何尺寸允许偏差(mm) 表5-6
序号
检查项目
允许偏差
1
罐壁高度
0.5%H
2
罐壁垂直度
0.4H且≤50mm
3
各圈壁板1m高处内半径
±13
(3).罐顶盖的组装
a.固定顶安装;
(1)固定顶安装前,应按规定检查保边角钢的半径偏差。
(2)罐顶支撑柱的垂直度允许偏差,不应大于柱高的0.1%,且不应大于10mm。
(3)顶板应按画好的等分线对称组装。
顶板搭接宽度允许偏差为±5mm。
b.浮顶组装;
(1)浮顶的组装,宜在临时支架上进行。
(2)浮顶板搭接宽度允许偏差为±5mm。
(3)外边缘板的搭接宽度允许偏差为±5mm。
3.内浮顶组装应按设计要求执行。
(4).附件安装;
(1)罐体的开孔接管应符合规范要求;开孔补强板的曲率,应与罐体曲率一致;开孔接法兰的密封面不应有焊瘤和疤痕,法兰的密封面应与接管的轴线垂直,且保证法兰面垂直或水平,法兰的螺栓孔应跨中安装。
(5).焊接施工
a.
(1)凡是定位焊接及工卡具的焊接,由合格焊工担任。
其焊接工艺应与正式焊接相同。
引弧不应在母材或完成的焊道上。
(2)焊接长度不应小于30㎜;焊接前应检查组装质量,清除坡口面,充分达到干净干燥无污染物。
(3)板厚大于6㎜的搭接角焊缝,应至少焊两遍。
(6).焊接顺序
(1)罐底的焊接。
应采用收缩变形最小的焊接工艺及焊接顺序,中幅板焊接时。
先焊短焊缝。
后焊长焊缝。
(2)弓形边缘板的对接焊缝采用手工焊。
先焊其外侧300mm焊缝,如右下图:
打底焊后进行渗透检查,以第二层开始每层错开50~70mm,焊接完成,上部磨平,进行磁粉和真空试漏检查,边缘板对接焊缝的其余部分在大角焊缝焊完后进行。
为控制焊接引起的角变形和控制外部的成形,须安装防变形龙门板,并在边缘板外部焊缝处焊接引弧块。
中幅板的焊接采用手工焊打底、埋弧自动焊盖面成型。
在焊接长缝时,采用防变形措施。
距边缘板2m范围内焊缝暂留不焊接,在与边缘板组对后再焊接。
边缘板剩余部分对接焊缝焊接,在焊第二层环缝前将卡具拆下,进行焊接。
焊完后,切割出