轴系船台安装原则工艺资料.docx
《轴系船台安装原则工艺资料.docx》由会员分享,可在线阅读,更多相关《轴系船台安装原则工艺资料.docx(19页珍藏版)》请在冰豆网上搜索。
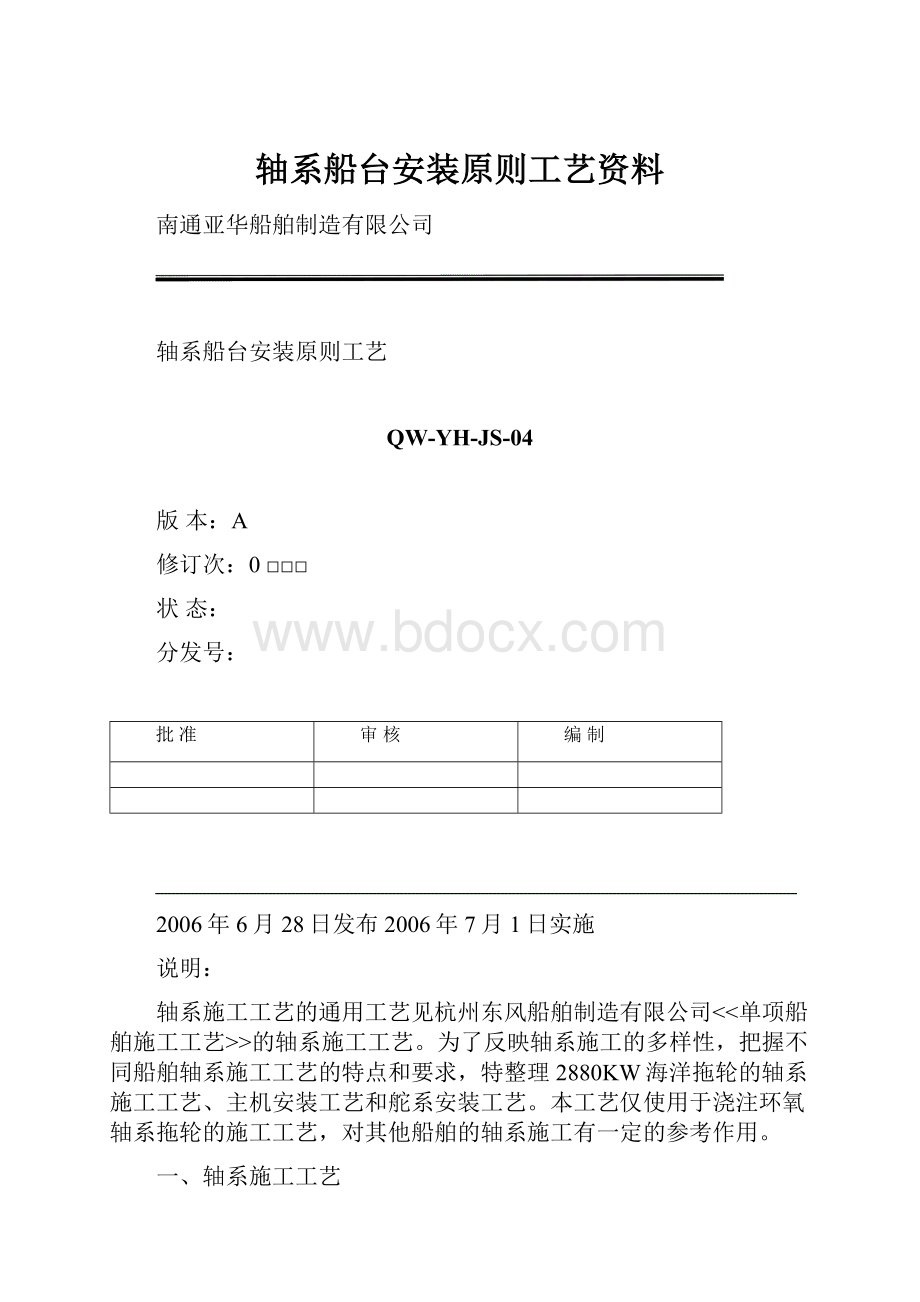
轴系船台安装原则工艺资料
南通亚华船舶制造有限公司
轴系船台安装原则工艺
QW-YH-JS-04
版本:
A
修订次:
0□□□
状态:
分发号:
批准
审核
编制
2006年6月28日发布2006年7月1日实施
说明:
轴系施工工艺的通用工艺见杭州东风船舶制造有限公司<<单项船舶施工工艺>>的轴系施工工艺。
为了反映轴系施工的多样性,把握不同船舶轴系施工工艺的特点和要求,特整理2880KW海洋拖轮的轴系施工工艺、主机安装工艺和舵系安装工艺。
本工艺仅使用于浇注环氧轴系拖轮的施工工艺,对其他船舶的轴系施工有一定的参考作用。
一、轴系施工工艺
1、施工依据
(1)JR601-420-1主机齿轮箱安装图
(2)JR601-425-0轴系布置图
(3)JR601-021-010A机舱结构图
(4)JR601-021-08A尾部结构图
(5)JR601-021-020A艉轴架图
(6)JR601-424-72中间轴系安装图
(7)JR601-425-6尾管前轴承座
(8)JR601-425-7尾管中轴承座
(9)*JR601-425-1艉轴尾管总装置图
(10)*JR601-425-2中间轴
(11)*JR601-425-3螺旋桨轴
(12)*JR601-425-4螺旋桨轴联轴节
(13)*JR601-425-5防渔网装置
(14)*JR601-401-4JS轴系校中计算书
(15)*JR601-234-01导管及支架结构图
带*为资料未到
2、轴系简介
本船采用中机舱型双推进轴系布置。
轴系总长为19542mm。
主推进轴系分左右各一组,每组轴系包括推力轴和推力轴承(均在齿轮箱内),一根中间轴,一根螺旋桨轴和一只中间轴承及一组尾管装置。
在机舱后壁(28#),还设置JT4174-84隔舱填料函一付,中间轴前部设接地装置一套。
轴系中心线与基线平行,距基线1550mm,主机曲轴中心线距基线2140mm,双轴系对称距中为2700mm。
2.1、轴
2.1.1、中间轴为中空轴锻钢制成,整体法兰。
采用圆柱形紧配螺栓与其他轴联接。
2.1.2、螺旋桨轴为中空轴,由调距桨制造厂提供。
桨轴内孔直径按制造厂标准加工。
桨轴内孔装调距机构的2根液压油管。
桨轴后端为整体法兰,与调距桨桨毂法兰相配,并用紧配螺栓联接。
桨轴前端以液压无键联接的可拆联轴节与中间轴连接。
螺旋桨调距伺服液压油由齿轮箱提供。
2.1.3、联轴节和联轴节螺栓
轴系上所有的联轴节都配有锻钢紧配螺栓,联轴节紧配螺栓的直径,联轴节法兰厚度以及法兰根部的过渡直径均由制造厂根据CCS规定的要求提供。
2.2、轴承
2.2.1、本船两根中间轴各由一只中间轴承支承。
轴承体上设有油封装置以防漏油。
铸铁轴承壳体两半合成,上、下半体内均为浇白合金的轴瓦。
2.2.2、尾管轴承
尾管采用Ø560×12无缝钢管。
尾管前、中、后轴承为油润滑的白合金轴承,前、中轴承处设圆筒形铸钢轴彀,后轴承为铸钢美人架轴彀,尾管后轴承装有遥测温度传感器。
2.2.3、尾管密封
尾管采用辛泼莱斯型油润滑密封装置,后密封并装有较为可靠的防渔网装置。
双轴密封装置分别设有尾管密封重力油柜。
3.轴系船台安装基本方法
3.1、采用拉线找中,焊接定位方法。
拉出#40~-2#的钢丝线,并计算出相应轴系另件处的挠度,对尾轴架、尾管中轴承座、尾管前轴承座进行定位焊接,并对中间轴承座、齿轮箱座及主机座的位置进行检查。
尾轴架、尾管中、前轴承座不需要镗孔,该轴承与内孔均采用环氧胶接。
轴承座加工时,应按图加工浇注环氧用的轴承固定螺孔、透气孔和浇注孔。
3.2、中间轴及轴承安装按轴系校中计算书要求进行。
3.3、为保证轴系施工精度,机舱分段在制造和合拢时应对主机、齿轮箱座的位置、尺寸严格控制。
4.轴系理论线确定
4.1拉线找中应具备的条件
4.1.1、主船体及艏楼合拢装焊完毕后,收火矫正、密性试验结束;首楼和主甲板上的舷墙、挡板、尾滚筒装焊结束;舵踵、上舵承座及护管装焊结束,密试合格。
4.1.2、船体交机时应准确标出FR19、FR28壁上的中心线和1550水线以及距中2700的垂直十字线;在船尾板和0#肋位外板上设船中线标记。
4.1.3、大合拢时尾部的临时支撑加强全部拆除。
4.1.4、振动作业及有严重干扰的其它作业应停止。
4.1.5、拉线找中应在晚间或阴雨天进行,以避免强烈光照产生的船体变形,影响轴系中心线的正确性。
4.2、拉线找中
4.2.1、初步拉线的目的
4.2.1.1、初步确定轴系中心的位置。
4.2.1.2、检查轴系和舵系中心线的相交度。
4.2.1.3、初步确定主机、齿轮箱、中间轴承的位置和其垫片的厚度。
4.2.2、拉线的操作和测量
4.2.2.1、按拉线示意图,在-2#、40#距中2700mm处设首、尾拉线架各两付,然后根据19#、28#船体标记放出钢丝线,钢丝线选用Ø1mm、19#琴钢丝,挂重90KG。
4.2.2.2、用水平管复测0#、40#处二钢丝与船体基线的平行度确保28#中心线距基线为1550mm;用样棒或卷尺复测距中2700mm的情况,并调整到最佳位置。
4.2.2.3、检查轴系中心线与舵系中心线的偏移值和垂直度。
偏移值(相交度)≤3mm,垂直度≤1/1000。
4.2.2.4、按下述公式计算各测量点挠度。
Y=g×x(L-x)/2×G式中Y=挠度(mm)
g=钢丝线单位重量(g/m)
L=钢丝两基准点间的距离(M)
X=所求挠度到基准点的距离(M)
G=挂重
本船选用Ø1mm、19#琴钢丝,g=6.17g/m,挂重90KG。
计算各测量点挠度(见拉线示意图)。
4.2.2.5、以28#隔仓挠度值作为修正量(4.44mm),计算各测量点修正挠度值。
修正挠度值(mm)=挠度-修正量(4.44mm)。
4.2.2.6、钢丝线调整完毕,需经质检部认可。
并在23#39#内底板上用洋冲打上标记,垂直测量钢丝线与该标记的距离,记录备查。
5.尾管轴承座安装
5.1、按轴系布置图(JR401-425-0)、尾部结构图(JR601-021-08A)、尾轴架图(JR601-021-020A)、导管及支架结构图(JR601-234-01),在船壳上画出尾轴架、导管支架、中轴承座开孔位置,制作开孔样板开孔。
在19#油舱壁上开出尾管前轴承座孔,在28#机舱后壁画出轴心延长十字线,并开出隔舱填料函孔。
5.2、按图定位导管,配装导管架复板、筋板,导管架与船体连接处采用双面深熔焊,焊接应对称进行,以减少导管中心位置的变化。
焊后导管中心偏差应控制在3mm之内。
5.3、尾管安装定位
5.3.1、尾管分前、后两段,前段约2110mm,后段约6210mm,直径为Ø560×12的无缝钢管。
5.3.2、尾管在安装之前应进行冲砂或酸洗处理,以消除氧化皮,处理后应涂石油树脂保养。
5.3.3、尾管前、中轴承座应与前段尾管、后段尾管按图在平台上预先组装好形成总成。
5.3.4、前后段尾管在与前、中轴承座组装时应将油温遥测传感器保护管(Ø10×1)预先装好,但在后段尾管开口处断开并配好管接头,并按说明书要求焊接固定夹具。
(固定夹具间距≤1500mm)
5.3.5、后段尾管前端距中轴承座后端~200下部向后开400×400mm四角为R50工艺孔一只,配制500×546×12四角为R100的板,并将546mm尺寸按尾管外圆加工成圆弧复板一块,备用。
5.3.6、将尾管总成从后向前串入15#、19#孔中,先伸向前,待尾轴架定为位后,再按图要求定位,用调整顶柱,并在后段尾管上设一辅助吊架,使前、中轴承座中心与轴系中心同心。
5.4、尾轴架定位,用葫芦和花篮螺栓将尾轴架吊起,然后调整中心使其与轴系中心同心,将尾轴总成,后端与其前端套上按5.3.6方法,定位尾管总成,并复测其与19#壁,主机铰制孔中心的相对位置,确认无误后绑牢,配装筋板、复板。
5.5焊接艉轴架、尾管中轴承座、尾管前轴承座及尾管。
为控制焊接变形,烧焊时先将尾轴架、尾管轴彀连成整体焊好,然后先焊前轴彀与19#舱壁,再焊尾轴架,最后焊中轴彀。
尾轴架复板、筋板焊接时须对称进行,同时密切注意变化情况,调整焊接顺序。
焊后其中心偏差应控制在3mm之内。
6.尾管轴承安装
6.1、复核各轴承座中心位置及间距尺寸,尤其是艉轴架后段距螺旋桨中心尺寸580mm,确认无误后,清洁轴承座内孔。
使无油污、锈迹、灰尘。
6.2、前、中、艉轴承就位。
轴承就位时应将遥控测温电缆管插在轴承槽内。
在前、中、艉轴承座上应预先钻攻好定位螺纹孔和灌胶用的浇注、透气孔。
通过定位螺栓调整各轴承,(前轴承座下部定位螺栓应在总成就位时、焊接前旋上),使其中心与钢丝线重合(应扣除该点修正挠度值)。
测量轴承法兰与轴承座端面的间隙,使其控制在15~20mm之内。
6.3、按图钻攻M16,深38,轴承固定螺孔,尾管中轴承处需准备加长钻头和丝攻。
6.4、清洁并复核各轴承中心情况,旋上轴承固紧螺栓,固紧螺栓应涂上脱胶剂(可用牛油或专用脱胶剂)。
6.5在轴承与轴承座之间浇注环氧垫层,轴承两端应采用封堵措施(在环氧树脂公司技术人员指导下工作)。
7.尾管清洁、装油温遥控传感器
7.1、轴承泵胶固化后,清洁尾管。
7.2、断开的后尾段油温遥测传感器护管及固定夹具安装。
7.3、安装油温遥测传感器。
7.4、仔细清洁尾管,提交质检部报验。
8.装桨轴、封工艺孔板、装首尾密封装置
8.1、先将后密封及衬套套在可调桨轴上。
8.2、桨轴由尾向首穿过尾轴承,在艉管工艺孔处帮助桨轴顺利插入中轴承,使桨轴按图示位置就位完毕。
并在轴上做好距舱壁距离的标注。
在串轴前应对轴承及桨轴仔细清洁,在串轴时应不断在轴承处浇注润滑油。
串轴时索具与桨轴接触处一定要有软垫,以防损伤桨轴加工面。
串轴时注意保护,不允许损伤轴承白合金。
8.3、测量尾、中、前三档轴承间隙,记录备查。
8.4、封工艺复板,工艺复板一定要与尾管贴平,尽量减少焊接收缩变形。
8.5、按说明书要求安装首、尾密封装置。
9.安装可调桨轴可拆联轴节
9.1、可拆联轴节采用液压套装,套装时应注意锥形衬套到桨轴的标记距离为50mm。
(详见说明书及图示)
10.安装可调螺旋桨
10.1、桨毂内装润滑油。
10.2、在内场将桨叶用螺栓紧固在桨毂上,要确保密封面的完好和浆彀内的清洁,在每组两个螺栓头部用钢板焊牢。
10.3、将浆彀与浆轴整体按图装在浆轴后法兰上。
11.安装结束后进行尾管压油试验;在尾密封处测量轴承下沉量;在后艉轴架与螺旋浆之间装焊护罩及防渔网割刀。
12.螺旋桨轴固定
12.1、确定螺旋桨轴位置,保证桨毂前端面与艉轴承后端面间距170mm。
(见图示)
12.2、测量液压联轴节前端面至19#壁距离,记录备查。
12.3、用槽钢连接液压联轴节与船体,作临时固定,以免下水时桨轴旋转和前后移位。
*13、船舶下水
13.1、下水后,中间轴校正按轴系校中计算书要求进行。
13.2、隔舱填料函按轴系布置图和产品样本进行安装。
附录1主机安装说明
二、主机安装工艺
1、简介
本船为柴油机推进,双机双浆驱动可调螺旋桨,中机舱型远洋拖轮。
机舱设置中速、四冲程、直列水冷、直接喷射、废气涡轮增压、中冷、不可逆转船用柴油机二台,型号:
VARTSILA8L20,左、右各一台;减速齿轮箱二台,型号:
LAF1162/4.5:
1,互为对称型。
主机最大持续功率(MCR)为1440KW,转速1000r/min。
主机与齿轮箱之间采用高弹性联轴节联接。
二机距船中2700mm,艉轴中心距基线1550mm,主机曲轴中心距基线为1550+590(mm)。
减速齿轮箱、主机垫片均为钢质。
减速齿轮箱用8只/台Ø22铰制螺栓定位。
主机用4付/台侧向支撑及2只/台Ø23双头铰制螺栓定位。
2、主机、减速齿轮箱的初步定位:
2.1、主机定位安装过程中,船上应当无重大设备迁移及压载变更。
2.2、按主机、齿轮箱安装图(JR601-420-1)及轴系布置图划出主机、齿轮箱的安装位置,并根据钢丝线测量垫块总厚度,垫块总厚度应控制在60mm左右,如总厚度≤58mm,则需在允差范围内调整轴系钢丝线或返工相应基座。
3、尾轴提升试验
3.1、船舶下水后,复核浆轴联轴节前端面与19#壁间距,确认无误后,进行尾轴提升试验,轴系对中和提升试验时要避免在太阳照射船体甲板上的环境进行。
按图3AK168621A所示,在浆轴前尾封前距联轴节端面1200处12点钟、3点钟位置各置百分表一只。
3.2、将能显示提升力的提升装置或带压力显示表的千斤顶置于前述浆轴百分表位置下部。
3.3、根据提升试验表1的要求按步提升轴,当轴每一步稳定后记录提升的量和提升力。
注意:
提升时提升力略大于表所列之值,反向下降时的力要略小于表所列之值。
3.4、将结果报告JCLNO并等待答复。
若无非常意外的结果,才能继续对中。
3.5、上述提升试验需由质检部参加并记录整理、发报告。
4、中间轴校正
4.1、中间轴、轴承进舱后,就位时可将浆轴后移~4mm(需作记录),并在中间轴两端0.22(0.22X6000)处设临时调整支承架各一付。
4.2、用软性材料(如木材、软铅)填在上轴瓦与轴颈间将中间轴承上部间隙临时消除,使轴颈紧贴轴承下表面。
4.3、调整临时支承架,使中间轴后法兰与浆轴联轴节法兰的曲折位移值满足:
SAG(位移)=2.24(中间轴低);GAP(曲折)=0.71(下开口)。
4.4、按图配制固定垫片,焊装、拂平、钻孔(钻孔尺寸见7.3),用钢质楔形垫片调整中间轴承,并用代用螺栓临时固定起来。
4.5、固定垫块配制时必须保证使其上平面与中间轴承或齿轮箱脚下平面有1/100的外契度。
按图装焊固定垫块,焊装时应注意楔块斜度的方向,并控制焊接电流,以免变形。
焊脚高度为5mm。
拂磨固定垫块上平面,用小平板或直尺测量,使其平整以保证调整垫块的拂配质量。
4.6、复测其与浆轴法兰的曲折位移值,确认无误后进行齿轮箱校正。
4.7、供货方提供资料中x值(测量用间隙)可取~2mm。
4、减速齿轮箱校正
5.1、将齿轮箱置于图示的轴向位置,用调节螺钉支撑。
5.2、将中间轴内的油管与齿轮箱油管相接(按说明书要求)。
5.3、用调整螺钉调整齿轮箱,使其与中间轴前法兰曲折、位移值满足:
SAG(位移)=2.05(齿轮箱低);GAP(曲折)=0.29(上开口)。
5.4、按图配制固定垫片、焊装、拂平、钻孔(钻孔尺寸见7.3),用钢质楔形垫片填实齿轮箱机脚,并用代用螺栓临时固定起来。
5.5、(同4.5)
6、轴系提升试验
6.1、复核中间轴两端法兰的曲折位移值,确认无误后,拆除中间轴承内临时软性垫块。
6.2、用代用螺栓将浆轴、中间轴、齿轮箱法兰联接起来,外圆靠对、拧紧。
每档法兰可用代用定位螺栓各二只以保证各法兰的同轴。
6.3、此时测量用间隙x值已消除,浆轴应回复到原定位状态。
6.4、(同3.1~3.5)根据提升试验表2的要求进行。
7、中间轴承、减速齿轮箱安装
7.1、轴系提升试验JCLNO认可后,进行中间轴承、减速齿轮箱调整垫片拂磨、安装工作。
7.2、对称、分批脱开临时固定的楔形钢质垫片。
加工、拂配调整垫块,用涂色法检查每25X25mm2接触点不少于3点。
用厚薄规检查要求垫块各接触面有70%的周长上0.05mm插不进,个别地方插入深度不超过20mm。
套钻或划线取出调整垫片钻孔。
7.3、钻孔尺寸详见安装图,铰制孔底孔尺寸:
中间轴承为ф25;齿轮箱为ф20.5。
7.4、铰孔、括平上、下端面,配制铰制螺栓。
8、轴系完整
8.1、拆除浆轴、中间轴、齿轮箱法兰的临时联接螺栓,按轴系说明书资料要求进行液压油管和联轴节的联接。
8.2、正式联接浆轴、中间轴、齿轮箱。
安装螺栓时必须仔细清洁轴、孔。
并在螺栓园柱、螺纹部位和螺母接触平面处涂上MoS2(二硫化钼)。
8.3、螺栓装好后,按要求的扭矩拧紧螺母。
联轴节较制螺栓螺母的拧紧扭矩为50N-M。
8.4、按隔舱填料函的有关资料安装隔舱填料函。
该座板的端面应与轴系中心线垂直,其不垂直度应不大于0.5‰。
8.5、按图示要求安装轴系接地装置。
8.6、按主机说明书要求装配油器。
9、主机的安装定位
9.1、主机飞轮与减速齿轮箱之间采用主机厂提供的橡胶高弹性联轴节。
由于高弹性联轴节已预先与齿轮箱输入轴、主机飞轮后端预装过,因此,主机定位时需保证齿轮箱输入轴法兰凸面与飞轮凹面间距198mm。
9.2、将专用工具(磁性靠表架及百分表)固定在齿轮箱输入轴法兰上,百分表指针靠到主机飞轮凹面内周及平面上,转动齿轮箱输入轴,测量主机飞轮凹面的圆周、平面的跳动量,求得主机安装的曲折、位移值。
高弹联轴节的对中要求:
径向偏移(位移)≤0.50mm,轴向偏移(间距)≤±0.50mm,轴线偏移(曲折)≤0.58mm。
9.3、主机的位置确定可借助于千斤顶或顶升螺栓来完成,千斤顶或顶升螺栓的数量及布置视现场需要而定。
9.4、按主机齿轮箱安装图焊接主机侧边支撑架,焊接时应注意支撑斜块的方向(向首楔紧),考虑到焊接应力引起的变形,要求焊接程序尽量对称,焊接分多层焊接,上道焊层结束待冷却后,才能进行下道焊层焊接。
9.5、主机垫块配制同4.5、7.2。
9.6、主机固定
9.6.1、按9.2方法及要求复核主机位置。
9.6.2、按主机齿轮机安装图要求钻孔(Ø21.5mm)8只/台,并将孔的上下端面刮平(Ø36mm),将件13螺栓按图紧固。
9.6.3、件号9双头铰制螺栓2只/台,孔铰制Ø23mm,按铰孔尺寸配制螺栓。
9.6.4、按图纸要求紧固螺栓,按9.2方法测量对中情况,并提交报验。
9.7、主机支撑块止动斜块拂配,用色油检查,要求接触均匀,接触面积≥80%,捶击斜块就位。
要求0.05mm塞尺插不进,然后旋紧支撑螺栓。
10、高弹性联轴节安装
10.1、仔细清洁齿轮箱输入端法兰、飞轮凹面。
10.2、按主机说明书图20-60538-91、20-60538-92安装顺序装复高弹性联轴节。
提升试验1
进行提升试验时先熟悉提升试验的过程。
按表测量并记录对中数据,并报告给JCLNO。
左舷/右舷
环境温度
--------℃
太阳照射
是/不是
船舶浮态
是/不是
螺旋桨入水
满/-----%
尾部吃水
--------m
首部吃水
---------m
临时支撑测量所得的力:
----------(N/kp/lbf)
联轴节未接前,检查尾管轴承,进行提升试验:
要求的提升力
提升时测量的提升力
提升时测量时百分表读数
下降时测量的提升力
下降时测量的提升力
[N]
[kp]
[N][kp]
垂直(1/100mm)
水平(1/100mm)
[N][kp]
垂直(1/100mm)
水平(1/100mm)
0
0
2000
200
2500
250
3000
300
3500
350
4000
400
4500
450
5000
500
5500
550
6000
600
6500
650
7000
700
7500
750
8000
800
9000
900
10000
1000
12000
1200
14000
1400
注意:
测量时,提升时实际测量的值不能小于要求测量的数值,下降时实际测量的值不能大于要求测量的数值。
力采用牛顿(N)或千克力(kp)在单位。
提升试验2
进行提升试验时先熟悉提升试验的过程。
按表测量并记录对中数据,并报告给JCLNO。
左舷/右舷
环境温度
--------℃
太阳照射
是/不是
对中值
GAP[mm]
开口处GAP
SAG[mm]
轴高
法兰联接;
推进轴-齿轮箱
上/下
推进轴/齿轮箱轴
法兰联接,检查尾管轴承,进行提升试验2:
要求的提升力
提升时测量的提升力
提升时测量时百分表读数
下降时测量的提升力
下降时测量的提升力
[N]
[kp]
[N][kp]
垂直(1/100mm)
水平(1/100mm)
[N][kp]
垂直(1/100mm)
水平(1/100mm)
0
0
2000
200
3000
300
3500
350
4000
400
4500
450
5000
500
5500
550
6000
600
6500
650
7000
700
8000
800
9000
900
10000
1000
12000
1200
14000
1400
16000
1600
18000
1800
20000
2000
注意:
测量时,提升时实际测量的值不能小于要求测量的数值,下降时实际测量的值不能大于要求测量的数值。
力采用牛顿(N)或千克力(kp)在单位。
三、舵系安装工艺
1.总则
1.1、本船为双机、双浆、双舵、舵杆中心位于0#肋位,两舵杆中心间距纵中剖面左右分别为2700mm,舵系结构为流线型悬挂平衡舵。
.
1.2、舵机为南京航仪二厂生产的75KN.M摆缸式电动液压舵机。
1.3、本船采用拉线定位、下舵承轴彀镗孔安装工艺。
1.4.1、舵系拉线定位条件,同DF601-425-001。
1.4.2、舵系拉线应与轴系拉线同时进行。
1.4.3、舵踵下舵承本体制造时内孔应放15mm镗孔余量(注油孔可预制好);上舵承座面板内孔放15mm,厚度放5mm镗孔余量。
2.舵系拉线
2.1、按舵系布置图(JR601-230-02)拉线。
在主甲板0#肋位距中2700mm,各开Ø510工艺孔一只(工艺孔板保存备用),设上拉线架各一付。
在船台上(轴系线以下)相应位置设下拉线架各一付。
用Ø1mm琴钢丝从主甲板通过上舵承座、下舵承、轴系钢丝线,在下部挂重50KG,拉出舵系钢丝线。
2.2、调整舵系钢丝线,使其在0#肋位上距舯2700mm.检查其与轴系钢丝线的相交度≤3mm,垂直度≤1/1000。
按此舵轴中心线将舵踵及下舵承本体的组合定位并焊接。
焊接完成并该处密性试验结束后,检查上