先进激光视觉传感技术及其在焊接中的应用.docx
《先进激光视觉传感技术及其在焊接中的应用.docx》由会员分享,可在线阅读,更多相关《先进激光视觉传感技术及其在焊接中的应用.docx(12页珍藏版)》请在冰豆网上搜索。
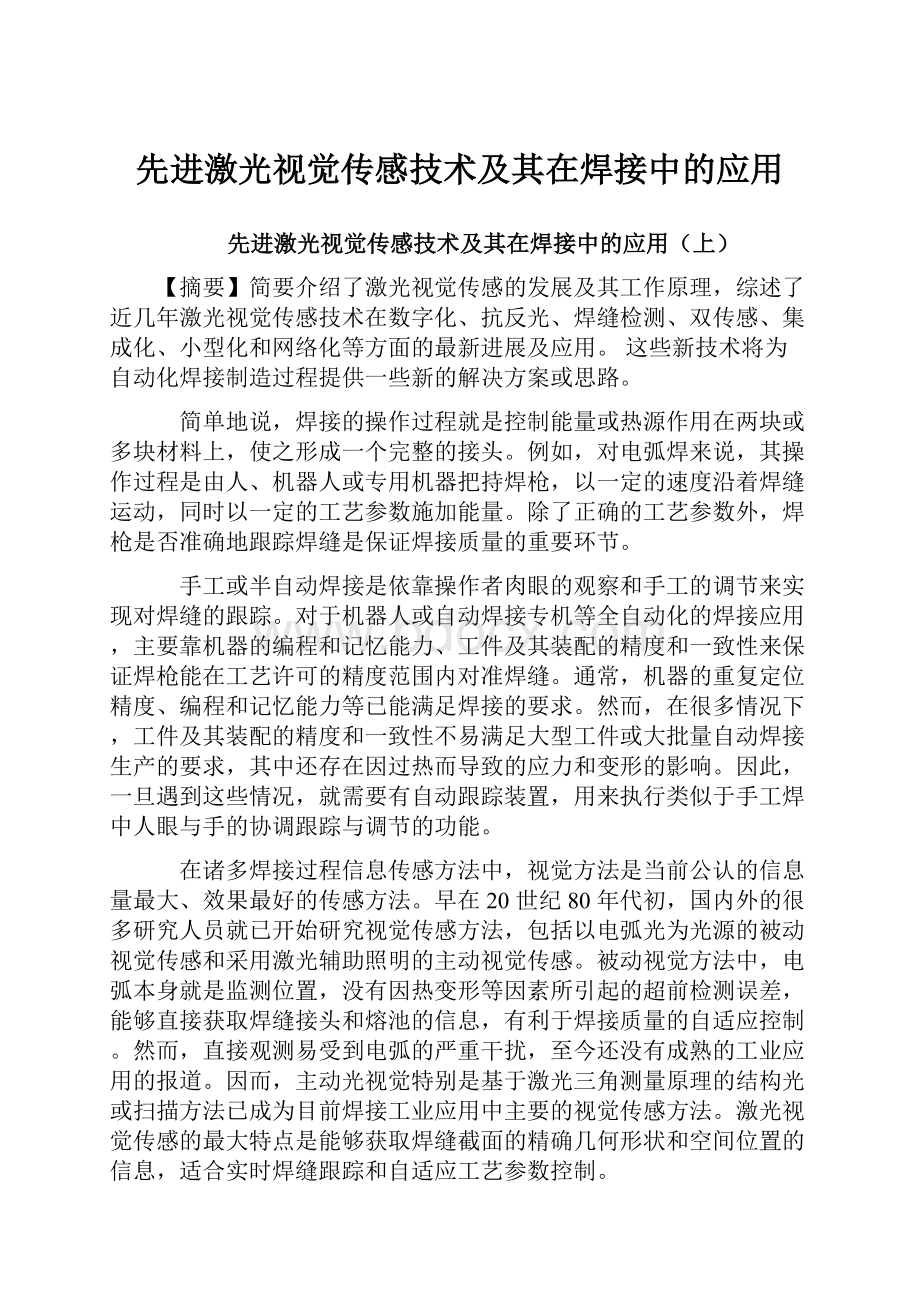
先进激光视觉传感技术及其在焊接中的应用
先进激光视觉传感技术及其在焊接中的应用(上)
【摘要】简要介绍了激光视觉传感的发展及其工作原理,综述了近几年激光视觉传感技术在数字化、抗反光、焊缝检测、双传感、集成化、小型化和网络化等方面的最新进展及应用。
这些新技术将为自动化焊接制造过程提供一些新的解决方案或思路。
简单地说,焊接的操作过程就是控制能量或热源作用在两块或多块材料上,使之形成一个完整的接头。
例如,对电弧焊来说,其操作过程是由人、机器人或专用机器把持焊枪,以一定的速度沿着焊缝运动,同时以一定的工艺参数施加能量。
除了正确的工艺参数外,焊枪是否准确地跟踪焊缝是保证焊接质量的重要环节。
手工或半自动焊接是依靠操作者肉眼的观察和手工的调节来实现对焊缝的跟踪。
对于机器人或自动焊接专机等全自动化的焊接应用,主要靠机器的编程和记忆能力、工件及其装配的精度和一致性来保证焊枪能在工艺许可的精度范围内对准焊缝。
通常,机器的重复定位精度、编程和记忆能力等已能满足焊接的要求。
然而,在很多情况下,工件及其装配的精度和一致性不易满足大型工件或大批量自动焊接生产的要求,其中还存在因过热而导致的应力和变形的影响。
因此,一旦遇到这些情况,就需要有自动跟踪装置,用来执行类似于手工焊中人眼与手的协调跟踪与调节的功能。
在诸多焊接过程信息传感方法中,视觉方法是当前公认的信息量最大、效果最好的传感方法。
早在20世纪80年代初,国内外的很多研究人员就已开始研究视觉传感方法,包括以电弧光为光源的被动视觉传感和采用激光辅助照明的主动视觉传感。
被动视觉方法中,电弧本身就是监测位置,没有因热变形等因素所引起的超前检测误差,能够直接获取焊缝接头和熔池的信息,有利于焊接质量的自适应控制。
然而,直接观测易受到电弧的严重干扰,至今还没有成熟的工业应用的报道。
因而,主动光视觉特别是基于激光三角测量原理的结构光或扫描方法已成为目前焊接工业应用中主要的视觉传感方法。
激光视觉传感的最大特点是能够获取焊缝截面的精确几何形状和空间位置的信息,适合实时焊缝跟踪和自适应工艺参数控制。
一、激光视觉传感的原理
激光视觉传感的基本原理就是光学的三角测量原理,如图1所示。
激光束照射到目标物体的表面,形成一个光斑点,经过摄像头上的透镜在光敏探测器上产生一个像点。
由于激光器与摄像头的相对位置是固定的,当激光传感器与目标物体的距离发生变化时,光敏探测器上的像点位置也相应发生变化,所以根据物像的三角形关系可以计算出高度的变化,即测量了高度变化。
当激光束以一定的形状扫描(扫描方式)或通过光学器件变换以光面的形式在目标物体的表面投射出线形或其他几何形状的条纹(结构光方式),在面阵的光敏探测器上就可以得到表征目标截面的激光条纹图像,如图2所示。
而当激光传感器沿着物体表面扫描前进时,就能得到所扫描表面形状的轮廓信息。
所获得的信息可用于焊缝搜索定位、焊缝跟踪、自适应焊接参数控制、焊缝成形检测等。
二、激光视觉传感的新进展及其应用
目前,已在焊接中应用的激光视觉传感器主要有扫描和结构光两种形式。
扫描方式主要有线形扫描和圆形扫描,其中圆形扫描的图像处理方式要复杂一些。
相对而言,对于反光的处理,扫描方式比结构光方式要容易。
此外,扫描方式传感器的视场深度大,可达280mm或更大。
但受到扫描激光斑点的影响,扫描激光传感器的精度,尤其是横向分辨率相对较低,通常>0.3mm。
同时,受机械扫描的影响,扫描速度不高。
扫描式激光传感器大多只用于大厚度工件的焊缝跟踪和自适应控制。
在高精度和高速度跟踪或检测中应用的激光视觉传感器大多为结构光方式的传感器。
因此,以下主要以ServoRobotInc.(赛融公司)的新技术为例介绍激光视觉传感器的新近进展及应用情况,其主要进展体现在数字化、抗反光、焊缝检测、双传感、多层焊、集成化、小型化和网络化等方面。
1.数字化
本文的数字化主要指图像的获取和处理方面。
最初的激光传感器中采用的图像获取器件为模拟的CCD,通常其图像获取的最高帧率为60帧/s或30帧/s,因而图像处理或输出控制等算法也随之受到限制。
随着电子与信息技术的发展,如图3所示,激光传感器中的图像获取器件逐渐采用了更为先进的数字CMOS器件,图像获取的帧率最高可达3000帧/s或10000帧/s,为高速和高精度的传感创造了条件。
同时,采用了数字化技术可以很方便地实现对数字图像目标区域的裁剪,消除临近焊缝夹具的其他特征对焊缝识别的干扰。
所以,在工件表面光亮、接头旁边有夹具影响或激光焊、焊缝成形与缺陷检测等高速传感要求的场合,采用数字CMOS图像探测器件的激光视觉传感器具备了采用模拟CCD的传感器所无法达到的性能。
2.抗反光技术
由于采用了数字化技术,除了成像质量大幅提高外,在图像处理上也可以采用一些更好的算法,从而能很好地消除铝合金、不锈钢、镀锌板等光亮表面反光的干扰,清晰地识别角焊缝、V形坡口等接头的细节,如图4所示。
在实现精确跟踪的同时,准确测量接头的间隙、错边和坡口截面积等几何参数。
图4a中激光条纹照射到不锈钢角焊缝表面,图4b为未采用抗反光技术获得的图像,图4c为采用抗反光技术获得的图像。
图5是TX/S数字激光视觉传感器在航天铝合金大型构件自适应焊接中的应用实例。
激光视觉传感器检测待焊坡口的几何信息,实现焊枪的自动对中及高度的自动调整,同时根据检测到的坡口间隙和截面积自动优化焊接参数并在线调整。
图5a显示了自适应焊接系统的主要构成。
图5b显示了TX/S传感器及其在非常光亮的铝合金V形坡口上的检测结果,完全消除反光的影响并准确测量出间隙、错边和截面积等参数。
3.焊缝检测
利用高速和高精度的激光视觉传感器扫描焊缝表面,可以得到焊缝表面的3D图像,通过一定的算法可以测量焊缝成形的几何参数如焊缝宽度、余高、焊趾角度等,还可探测咬边、焊瘤和表面气孔等缺陷,如图6和图7所示。
ARC—SCAN和LAS—SCAN传感系统分别用于弧焊和激光焊等焊缝或密封缝的检测,符合6σ质量控制的需求。
4.双传感技术
在焊缝检测时,除了要检测焊缝宽度、余高、咬边等焊缝成形有关的几何参数,还要检测焊缝上细小的气孔等表面缺陷。
采用双传感技术的激光视觉传感器在焊缝上投射一道激光条纹,由两个传感器来获取测距图像。
如图8所示,其中一个传感器的视场较大,用于检测焊缝成形参数,另一个传感器的视场较小但具有较高的分辨率,集中在焊缝表面,用于检测焊缝上可能的细小气孔。
图9是采用双传感技术的PX—10/25激光视觉传感器进行轿车车身激光钎焊焊缝自动检测的照片。
5.多层焊功能
激光视觉传感的多层焊功能是专门针对大厚板多层多道焊的焊缝跟踪与自适应参数调整的需求而开发的。
根据不同的参数设置,激光传感器可以识别根部焊道和随后各层焊道的轮廓图像,获得焊缝的跟踪点,并能根据焊缝坡口的截面规划每一焊道的焊接参数。
多层焊功能既可用于焊接专机,也可用于机器人焊接。
但由于不同厂家的机器人对多层多道焊功能的支持是不一样的,所以,目前只有一部分机器人可以和激光视觉传感的多层焊功能配合使用。
图10是采用M—SPOT激光视觉传感器的推土机构件的机器人自适应多层焊接的照片。
6.集成化
激光视觉传感的集成化体现在3个方面:
多功能的集成、不同传感方法的集成和传感器与控制器的集成。
(1)多功能的集成Digi—Las系统就是多功能集成的典型代表。
如图11所示,系统集成了焊前接头装配检验、高速焊缝跟踪、激光焊接头、自适应过程参数控制、激光焊熔池监视、焊后焊缝质量检测六种功能。
Digi—Las采用了一前一后的两个激光视觉传感器,中间为激光焊接聚焦装置和监视焊接熔池的CCD。
前面的激光条纹用于检测并记录反映装配质量的错边、间隙及接头位置等参数,并实现高速焊缝跟踪功能和激光焊接过程参数的自适应调整功能。
后面的激光条纹用于检测焊缝的几何形状和焊接缺陷并进行记录。
图12是Digi-Las激光焊接头在汽车TWB激光拼焊中应用的照片。
(2)不同传感方法的集成图13所示的Digi—I/S
传感器在激光视觉传感的基础上集成了电弧声音传感器。
传感器在具有激光视觉传感的焊缝跟踪与自适应焊接参数控制功能的同时,还能探测电弧发出的声音,用于MIG/MAG焊短路过渡等的过程质量监控。
图14所示的Robo—Pal传感器内部集成了超声传感器,可实现长距离的位置探测,有两个十字交叉的激光视觉传感实现对目标物体的精确定位。
这种传感器主要用于机器搬运、装卸等。
(3)传感器与控制器的集成随着电子技术的发展,现在的激光视觉传感技术已经可以把激光传感器的控制器部分集成到传感器的内部,从而使激光视觉传感系统使用和维护更为简单,同时降低成本。
图14中的Robo—Pal传感器内部已经集成了系统的控制系统。
图15所示的Sense—i/D传感器的控制系统也已经嵌入传感器内部,传感器可向外提供模拟接口、数字IO接口和以太网接口,可以方便地和机器人或专机进行配套集成。
7.小型化
在很多自动化焊接应用中,工件的形状或者工装夹具很复杂,这就降低了焊枪的可达性。
因此,希望传感器的体积越小越好。
随着集成度的提高,出现了很多小体积的传感器,当前体积最小的激光视觉传感器,包括防飞溅保护装置在内,其大小尺寸仅为35mm×34mm×125mm。
8.网络化
随着精益生产、网络制造等先进制造思想的发展与推广,制造企业对设备网络化功能的需求也越来越多,激光视觉传感也从原有的单机系统向网络化的方向发展。
新型的激光传感器或系统已经具有工业以太网接口,可以很方便地与机器人或CNC专机、PLC、焊接电源及PC等构成一个网络化的生产制造系统。
图16和图17分别是适合机器人和CNC专机的IT—WELDTM网络平台。
IT—WELD网络平台可以驱动多激光传感头,实现网络化的激光视觉和过程控制,从而实现智能制造过程。
三、结语
在市场竞争的驱动下,自动化的焊接生产制造过程对传感技术、质量监控与保证技术的需求越来越迫切。
在很多自动化焊接制造场合,没有传感器和自动检测手段,生产质量和成本将是难以接受的。
以上所述的激光视觉传感新技术正是为满足自动焊接过程的需求而在近几年内发展起来的。
在电弧焊、激光焊及火焰切割或等离子切割等领域,它们已为焊接工业提供了焊缝搜索定位、焊缝跟踪、焊接参数自适应控制、焊缝成形及缺陷的检测等许多可靠的工业应用。
这些新技术将为自动化焊接制造过程提供一些新的解决方案或思路。
但是,由于焊接过程传感与控制的复杂性,即使是这些最新发展的激光视觉传感技术,仍难以完全满足各种各样的焊接过程的需求。
因此,目前还有很多的公司或科研机构正为新的、更为可靠的或者成本更低的传感技术和手段而努力。