安平红亮不锈钢线材厂.docx
《安平红亮不锈钢线材厂.docx》由会员分享,可在线阅读,更多相关《安平红亮不锈钢线材厂.docx(29页珍藏版)》请在冰豆网上搜索。
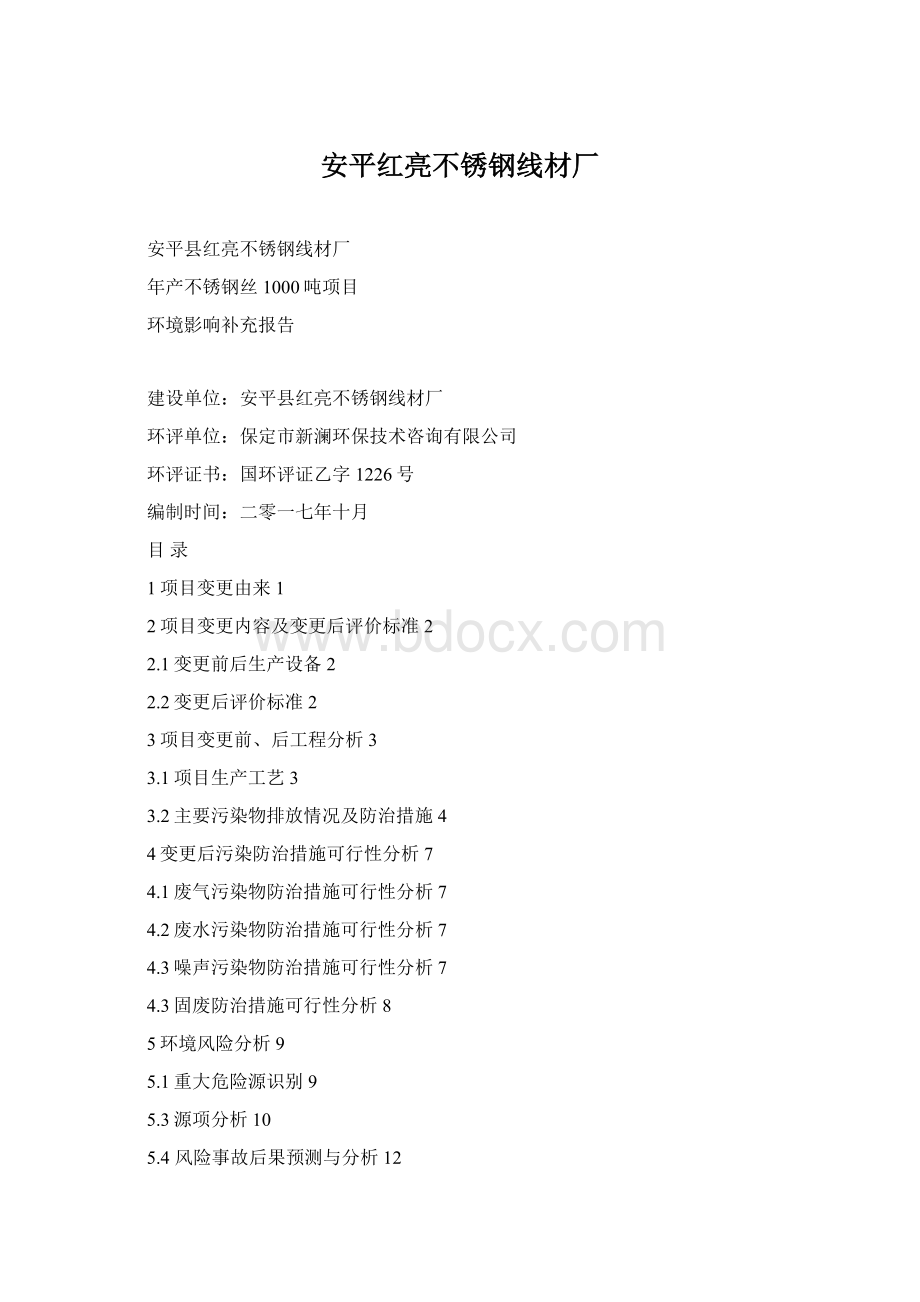
安平红亮不锈钢线材厂
安平县红亮不锈钢线材厂
年产不锈钢丝1000吨项目
环境影响补充报告
建设单位:
安平县红亮不锈钢线材厂
环评单位:
保定市新澜环保技术咨询有限公司
环评证书:
国环评证乙字1226号
编制时间:
二零一七年十月
目录
1项目变更由来1
2项目变更内容及变更后评价标准2
2.1变更前后生产设备2
2.2变更后评价标准2
3项目变更前、后工程分析3
3.1项目生产工艺3
3.2主要污染物排放情况及防治措施4
4变更后污染防治措施可行性分析7
4.1废气污染物防治措施可行性分析7
4.2废水污染物防治措施可行性分析7
4.3噪声污染物防治措施可行性分析7
4.3固废防治措施可行性分析8
5环境风险分析9
5.1重大危险源识别9
5.3源项分析10
5.4风险事故后果预测与分析12
5.5风险防范措施14
6变更前后污染物排放总量变化情况17
6.1原环评中污染物排放总量控制指标17
6.2变更后污染物排放总量控制指标17
6.3变更前后污染物排放总量变化情况17
7变更后建设项目竣工环境保护“三同时”验收内容18
8结论19
8.1变更内容结论19
8.2变更后污染物防治措施及可行性结论19
8.3污染物排放总量控制结论20
8.4变更可行性结论20
附图:
1.项目地理位置
2.项目周边关系图
3、项目平面布置图
附件:
1.安平县行政审批局关于《安平县红亮不锈钢线材厂年产不锈钢丝1000吨项目》审批意见
2项目备案信息表
3委托书
4.承诺函
1项目变更由来
《安平县红亮不锈钢线材厂年产不锈钢丝1000吨项目》环境影响报告表于2017年8月2日通过安平县行政审批局的审批,审批文件见附件,项目至今未验收。
安平县红亮不锈钢线材厂位于衡水市安平县丝网工业园区南区I
-23号,总投资300万元,占地面积为5473m2,年产不锈钢丝1000吨。
由于原项目的环评报告中针对不锈钢丝的生产工艺较为简易,产品质量不合格,根据建设单位提供的材料以及数据,将不锈钢丝的生产工艺进行完善,增加退火工序,使产品质量到达相关产品质量要求。
利用现有厂房、场地新购进氢气无氧退火炉3套、拔丝机50台,用于不锈钢丝产品的生产工序上,新增投资150万元。
根据建设单位提供的资料、现场勘查以及安平县环境保护局的相关要求,受安平县红亮不锈钢线材厂的委托,本公司编制完成了《安平县红亮不锈钢线材厂年产不锈钢丝1000吨项目》环境影响补充报告。
2项目变更内容及变更后评价标准
项目的建设地点、占地面积不发生变化,项目的基本内容见下表。
表2-1项目变更基本情况对照表
序号
项目
变更前
变更后
备注
1
地理位置
安平县丝网工业园区南区IV-23号
安平县丝网工业园区南区IV-23号
不变
2
占地面积
5473m2
5473m2
不变
3
生产规模
不锈钢丝1000吨
不锈钢丝1000吨
不变
2.1变更前后生产设备及原辅材料
2.1.1生产设备变更
项目变更后,新增了3套电退火炉以及50台拔丝机,仅不锈钢丝产品的生产工艺发生变化,具体变更内容见下表。
表2-2项目生产设备变更情况对照表
项目
变更前
变更后
备注
生产设备
拔丝机×25
拔丝机×75
增加50套
退火炉×0
退火炉×3
增加3套
注:
新增退火炉为3套,配套使用AQ型氨分解炉以及400kg的液氨储罐1个、200kg的液氨储存罐3个,完成退火工序。
2.1.2原辅材料变更
项目生产工艺发生变化,增加了退火工序,原辅材料用量发生一定的变化。
具体变更内容详见下表。
表2-3项目原辅材料消耗量情况对照表
项目
变更前消耗量
变更后消耗量
备注
原辅材料用量
线材1000t/a
线材1000t/a
不变
拔丝粉20t/a
拔丝粉20t/a
不变
液氨0t/a
液氨1.92吨
增加液氨的消耗用于退火工序
水96m3/a
水96m3/a
不变
电35.85万kW.h/a
电53.78万kW.h/a
增加
2.2变更后评价标准
变更后,不锈钢丝的生产工艺发生变化,新增的生产工序无新增污染物产生,故污染物的排放标准不发生变化。
3项目变更前、后工程分析
3.1项目生产工艺
3.1.1项目原环评生产工艺
对于外购合格的线材,使用拉丝机进行冷拔,让线材通过比它的直径小一点的孔中强行拉过,则线材直径就会变小,长度会伸长,不断重复这样的加工过程,则线材就会进一步变小,直到满足产品要求,拔丝过程中使用拔丝粉润滑线材。
图1变更前不锈钢丝生产工艺流程及排污节点图
3.1.2变更后生产工艺
变更后的不锈钢丝的生产工艺发生变化,部分产品工艺不发生变化,约有70%的产品进行了拔丝—退火——二次拔丝—二次退火的工艺,详述如下:
项目外购的盘条钢丝为原料,将不锈钢盘条引至拔丝机中进行第一次粗拔,然后牵引至氢气无氧退火炉中进行一次退火,一次退火完成后的钢丝由牵引设备引至冷拔机中进行二次拔丝,二次拔丝完成后进行二次退火,二次退火和一次退火的工序以及设备一致,二次退火完成后,即为项目的产品。
相对比原环评,主要增加了二次拔丝以及两次退火工序,拔丝的原理不发生变化,退火工序利用电退火炉对钢丝进行加热,该退火炉为连续电退火炉,依次经过预热、加热、均热完成连续退火热处理,达到使产品性能提升的效果,项目设置的退火炉配套使用AQ型氨分解炉。
项目退火采用间接加热,退火炉内设有多根铜管,金属丝从铜管中穿过,通过加热铜管使金属丝达到退火的目的。
退火时采用的保护气体为氢气,由氨分解及纯化装置制氢,经管道连接至退火炉。
保护气制备工艺如下:
液氨经管道进缓冲罐后变成氨气,再进AQ型氨分解炉制备。
氨气在氨分解炉中经电加热至800~850℃,在催化剂作用下,氨气进行分解,可以得到H2、N2混合体。
每公斤液氨分解可制得2.64Nm3混合气体,其中约含75%的H2和25%的N2。
本项目催化剂采用的为铁触媒,主要成分为Fe3O4及少量K2O、Al2O3、CaO、MgO,不属于危险废物。
反应方程式为:
2NH3→3H2+N2-21.9千卡
氨分解炉得到的混和气体含有少量杂质,杂质中含水汽约2g/m3,残余氨约1000ppm,为了去除杂质需进行纯化工序,项目纯化装置选择分子筛为吸附材料对混合气体中的水汽和残余氨进行吸附,经分子筛吸附纯化后的气体经输气软管送入退火炉高温管内对不锈钢丝的退火阶段进行保护,再经管口排出,排出的气体主要为氮气和水蒸气。
变更后生产工艺流程图如下:
图2变更后部分不锈钢丝生产工艺流程及排污节点图
3.2主要污染物排放情况及防治措施
变更后,项目部分不锈钢丝的生产工艺发生变化,增加了两次退火工序,本项目退火工序采用电退火炉,退火工序本身无污染物的产生,电退火炉配套使用的液氨分解进行保护,液氨分解后为氢气和氮气,由于氮气为惰性气体,不易被周围环境氧化,直接外排环境空气中,氢气经燃烧后成水蒸气,最终氧化成H2O,余热将水蒸发为水蒸气,排入环境空气中。
无新增废气污染物的排放。
根据项目的变更情况,项目废气污染物的排放及治理措施、废水污染物的排放及治理措施以及固废污染物的排放及治理措施不发生变化,设备的增加会使噪声的源强有变化,由于增加的设备为拔丝机、退火炉等为产噪较小的设备,噪声影响不会明显改变。
综上,将本项目变更后的污染物排放及治理措施进行复述和完善。
3.2.1废气污染物排放情况及治理措施
变更后,项目产生的废气主要为退火工序产生的氮气和水蒸气。
电退火炉配套使用的液氨分解进行保护,液氨分解后为氢气和氮气,由于氮气为惰性气体,不易被周围环境氧化,直接外排环境空气中,氢气燃烧后成为水蒸气,最终氧化成H2O,余热将水蒸发为水蒸气,排入环境空气中。
氮气和水蒸气不作为废气污染物,少量的排放不会对周围环境空气产生明显影响。
综上所述,在采用上述措施后,项目运营期对周围大气环境影响较小。
3.2.2废水污染物的排放及治理措施
变更前后,项目无新增废水的产生。
故复述原环评中废水产生及排放情况。
根据原环评,项目无生产废水产生,废水主要为生活污水。
生活污水为员工盥洗废水,生活污水排放量力0.256m3/d,主要含有COD、SS及氨氮等,主要含有COD、SS及氨氮等,污染物产生浓度分别为200mg/L、150mg/L,20mg/L,生活污水经化粪池处理后通过园区污水管网排至南区污水处理站处理,由南区污水处理厂处理后达到安平县污水处理厂标准,排入安平县污水处理厂进一步处理。
本项目营运期对周围水环境影响较小。
3.2.3噪声污染物的排放及治理措施
项目变更后,设备增加,噪声污染源增加,源强增大。
本项目噪声源主要来自中拔丝机、退火炉等设备噪声,其噪声声级在80~95dB(A)之间,采用低噪声设备并将其布置在厂房内、对振动较大的设备采取减震基础的降噪措施,经采取相应的隔声、降噪措施后可综合降噪25~35dB(A),生产过程中要对设备进行定期检修,保持设备良好的运转状态,尽量降低噪声,再经距离衰减,昼夜均能够满足《工业企业厂界环境噪声排放标准》(GB12348-2008)中3类标准要求,不会对会周边环境产生影响。
3.2.4固废污染物排放情况及治理措施
项目变更后,无新增固废污染物,故将原环评中固废产生及排放情况复述。
根据原环评,项目固废主要为生产过程中产生的金属废料、废催化剂、废分子筛、铁屑,边角料和职工生活垃圾。
生产过程中产生的金属废料、废催化剂、废分子筛,铁屑产生量为20t/a,收集后外售综合利用边角料产生量为2.5t/a,分类收集后外售综合利用;项目劳动定员8人,生活垃圾产生量以0.5kg/d人计,则生活垃圾产生量为1.2t/a,由环卫部门统一处理,最终送安平县生活垃圾卫生填埋场填埋。
本项目产生的固体废物均能得到妥善处置,不会对周边环境产生影响。
4变更后污染防治措施可行性分析
4.1废气污染物防治措施可行性分析
变更后,项目产生的废气主要为退火工序产生的氮气和水蒸气。
退火工序氮气和水蒸气
电退火炉配套使用的液氨分解进行保护,液氨分解后为氢气和氮气,由于氮气为惰性气体,不易被周围环境氧化,直接外排环境空气中,氢气燃烧后成为水蒸气,最终氧化成H2O,余热将水蒸发为水蒸气,排入环境空气中。
氮气和水蒸气不作为废气污染物,少量的排放不会对周围环境空气产生明显影响,无需采用治理措施。
4.2废水污染物防治措施可行性分析
本项目无生产废水产生,无生产废水外排,废水主要为生活污水。
生活污水为员工盥洗废水,水质较为简单,经化粪池处理后通过园区污水管网排至南区污水处理站处理,由南区污水处理厂处理后达到安平县污水处理厂标准,排入安平县污水处理厂进一步处理,处理措施可行。
4.3噪声污染物防治措施可行性分析
变更后,项目生产设备主要为拔丝机、退火炉等设备产生的噪声,通过将设备安置于生产车间内,进行基础减震、厂房隔声。
隔声:
是把一个噪声源或是把需要安静的场所封闭在一个小的空间中,与周围环境隔绝起来,一般噪声值可降低5~10dB(A),具有投资少管理费用低的特点,因此是许多工厂控制噪声最有效的措施之一。
减振:
机器在运转时把振动传到基础、地板甚至整个建筑物,成为噪声源发射噪声,采用减振和软连接等措施可减弱设备传给基础的振动达到降低噪声的目的,一般可降低5~10dB(A),上述降噪声措施在技术上是成熟的。
综上,经过相应的处理措施后,厂界噪声符合《工业企业厂界环境噪声排放标准》(GB12348-2008)3类标准。
4.3固废防治措施可行性分析
项目产生的固体废物主要是金属废料、废催化剂、废分子筛、铁屑,边角料和职工生活垃圾。
金属废料、废催化剂、废分子筛、铁屑、边角料收集后全部外售,生活垃圾由环卫部门定期清理。
所有固废均能合理处置,不外排,措施可行。
5环境风险分析
5.1重大危险源识别
(1)环境风险识别
根据《危险化学品重大危险源辨识》(GB18218-2009)可知本项目主要危险物质为氨和氢气,这些物料在输送、贮存及生产过程中均存在一定的危险性。
《建设项目环境风险评价技术导则》(HJ/T169-2004)物质危险性标准见表5-1。
本工程涉及的主要危险化学品的特性详见表5-2。
表5-1物质危险性标准
类别
LD50(大鼠经口)mg/kg
LD50(大鼠经皮)mg/kg
LC50(小鼠吸入,4小时)mg/m3
有毒
1
<5
<1
<0.01
2
5100.13
25500.5易燃
1
可燃气体——在常压下以气态存在,并与空气混合形成可燃混合物;其沸点(常压下)是20℃以下的物质
2
易燃液体——闪点低于21℃,沸点高于20℃的物质
3
可燃液体——闪点低于55℃,压力下保持液态,在实际操作条件下(如高温高压)可以引起重大事故的物质
爆炸性物质
在火焰影响下可以爆炸,或者对冲击、摩擦比硝基苯更为敏感的物质
表5-2项目所涉及到的危险物质理化性质及危险特性
名称
物化性质
易燃易爆性
毒性
毒性
H2
无色无味气体,熔点-259.2℃,沸点-252.8℃,闪点<-50℃,饱和蒸气压13.33kPa(-257.9℃),相对密度(水=1)0.07(-252℃),相对密度(空气=1)0.07不溶于水,不溶于乙醇、乙醚
易燃气体
急性毒性:
LD50无资料
LC50无资料
-
NH3
无色有刺激恶臭气体,熔点-77.7℃,沸点-33.5℃,饱和蒸气压506.62kPa(4.7℃),相对密度(水=1)0.82(-79℃),相对密度(空气=1)0.6,微溶于水、乙醇、乙醚
--
急性毒性:
LC50350mg/m3
LC501390mg/m3,4小时(大鼠吸入)
低毒性物质
由表5-1和表5-2对照可知,H2为易燃易爆物质,NH3为低于3类的一般毒性物质。
(2)生产设施风险识别
工程主要生产装置和储存装置涉及有毒、易燃、易爆物质,因此对设备及相应管道的承压、密封的要求较高,存在因设备密封件磨损而引起气体泄漏。
通过项目各工序生产工艺流程,主要潜在危险设备及装置情况见表5-3。
表5-3项目主要生产设施风险识别
序号
装置名称
作业特点
风险评价因子
主要危险危害
1
退火炉
高温
H2
中毒、火灾、爆炸
2
氨分解及纯化装置
高温、高压
H2、NH3
中毒、火灾、爆炸
3
液氨储罐
常温
NH3
中毒、火灾、爆炸
(3)重大危险源识别
根据查阅《危险化学品重大危险源辩识》(GB18218-2009)和《建设项目环境风险评价技术导则》(HJ/T169-2004),气体临界量见表5-4。
表5-4危险物质生产场所临界量一览表
危险物质
使用量/生产量(t)
临界量(t)
q/Q值
是否属重大危险源
生产区
贮存区
生产区
贮存区
生产区
贮存区
液氨
0.01
1.0
10
0.001
0.16
否
否
氢
(氨分解)
0.007
-
5
0.001
-
否
否
合计
-
0.002
0.05
否
否
由表5-4分析可知,本项目氢和氨储存量小于《危险化学品重大危险源辩识》(GB18218-2009)中规定的临界量范围,不存在重大危险源。
5.3源项分析
(1)最大可信事故
氨分解制氢生产主要危险因素为火灾、爆炸和中毒。
氨分解制备氢时与氧化剂接触遇到火源时有发生火灾爆炸的危险,引火源包括明火、高热、摩擦或撞击火花、雷电等;存在氨、氢气的设备、管道、阀门损坏或法兰连接处密封不严造成氢气、氨气泄露;装置无防雷、防静电接地设施或设施有缺陷;电气设施、电线电缆出现过负荷、过电流、过热、漏电、短路等情形,均有可能引发火灾或爆炸。
根据有关统计资料结果,储存区事故率最高,按照事故发生部位,储罐阀门损坏导致泄漏占首位,据我国不完全统计,设备容器阀门损坏导致泄漏、爆炸的事故概率在1×10-5/a左右。
(2)事故源项分析
液氨泄漏后一部分液体将会直接发生闪蒸蒸发,其余液体将在罐体附近形成液池,并形成热量蒸发。
假定液氨贮罐因阀门破裂造成泄漏事故后,操作人员在3min内使贮罐泄漏得到控制,并采取有效的收集措施。
裂孔直径为1cm,大气温度为25℃。
由于氨钢瓶为卧式,考虑底部出现裂口,高度取1m。
液氨泄漏速度QL用柏努利方程计算:
式中:
QL——液体泄漏速度,kg/s;
Cd——液体泄漏系数,此值常用0.6~0.64。
A——裂口面积,7.85×10-5m2。
P——容器内介质压力,1.4×106Pa。
P0——环境压力,1.01×105Pa。
g——重力加速度,9.8m/s2。
h——裂口之上液位高度,1m。
液体泄漏后会向环境中蒸发,由于氨的沸点为-33.4℃,故会发生闪蒸蒸发和热量蒸发,没有质量蒸发存在,蒸发速率按下面公式计算。
过热液体闪蒸量可按下式估算:
Q1=F·WT/t1
式中:
Q1——闪蒸量,kg/S;
WT——液体泄漏总量,kg;
t1——闪蒸蒸发时间,s;
F——蒸发的液体占液体总量的比例;按下式计算
式中:
Cp——液体的定压比热,4.6×103J/(kg·K);
TL——泄漏前液体的温度,273K;
Tb——液体在常压下的沸点,240K;
H——液体的气化热,1.37×106J/kg。
热量蒸发的蒸发速度Q2按下式计算:
式中:
Q2——热量蒸发速度,kg/s;
T0——环境温度,298k;
Tb——沸点温度;239.6k;
S——液池面积,m2;
H——液体气化热,1.37×106J/kg;
λ——表面热导系数,W/m·k;
α——表面热扩散系数,m2/s;
t——蒸发时间,s。
经计算可知,液氨的蒸发速率为0.075kg/s。
5.4风险事故后果预测与分析
(1)事故后果计算
①预测模式
预测模式采用《建设项目环境风险评价技术导则》(HJ/T169-2004)中推荐的多烟团模式进行计算:
式中:
C
----下风向地面
坐标处的空气中污染物浓度(mg.m-3);
----烟团中心坐标;
Q--事故期间烟团的排放量;
σX、、σy、σz——为X、Y、Z方向的扩散参数(m)。
常取σX=σy
对于瞬时或短时间事故,可采用下述变天条件下多烟团模式:
式中:
--第i个烟团在
时刻(即第w时段)在点(x,y,0)产生的地面浓度;
--烟团排放量(mg),
为释放率(mg.s-1),
为时段长度(s);
、
、
--烟团在w时段沿x、y和z方向的等效扩散参数(m),可由下式估算:
式中:
和
--第w时段结束时第i烟团质心的x和y坐标,由下述两式计算:
②预测结果分析
建设项目所在地年平均风速1.7m/s,大气稳定度取B、D、E3类稳定度,本评价以此气象条件作为事故影响分析的计算条件。
计算结果见表5-5。
表5-5事故源对下风向不同距离的影响
事故源
污染物
扩散时间
大气稳定度
出现距离
半致死浓度范围
钢瓶
泄漏
氨
3min
B
16.1m
--
D
14.7m
18.9m
E
12.0m
39.4m
从表上可以看出,氨钢瓶泄漏事故时,当扩散时间为3分钟,半致死浓度最大范围为39.4m。
距本项目最近的敏感点为厂址西东北方向610m处的锦绣华城小区,项目采取完善的控制措施后,液氨的泄露不会对其产生影响。
因此,建设单位应加强管理,杜绝氨泄漏事故的发生;万一发生泄漏,立即按规定采取措施,将泄漏时间控制在3分钟以内。
(2)风险值与评价
通常风险定义为:
风险(危害/时间)=事故发生概率(事故/单位时间)×危害程度(危害每次事故)根据所计算内容的特点,在具体计算过程中,按照以下计算事故风险值。
对于泄露事故可采用下式进行计算:
事故风险(死亡人数/年)=半致死百分率区人口数×50%×事故发生概率×出现不利天气概率
环境风险事故具有一定程度的不确定性。
事故发生的条件有很多,事故发生的天气条件千差万别,具有极大的不确定性,发生事故的排放强度有多种可能。
这样对风险事故的后果预测就存在着极大的不确定性。
风险的单位多采用“死亡/年”。
安全和风险是相伴而生的,风险事故的发生频率不可能为零。
通常事故危害所至风险水平可分为最大接受风险水平和可忽略水平。
表5-6列出了一些机构和研究者推荐的最大可接受风险水平和可忽略水平。
表5-6最大可接受水平和可忽略水平的推荐值
机构/研究者
最大可接受水平(a-1)
可忽略水平(a-1)
备注
瑞典环境保护局
1×10-6
化学污染物
荷兰建设和环境部
1×10-6
1×10-8
化学污染物
英国皇家协会
1×10-6
1×10-7
Miljostyrelsen(丹麦)
1×10-6
化学污染物
Travis等(美国)
1×10-6
对于社会公众而言最大可接受风险不应高于常见的风险值。
在工业和其他活动中,各种风险水平及其可接受程度见表5-7。
一般而言,环境风险值的可接受程度,对有毒有害工业以自然灾害风险值,即10-6/a为背景值。
表5-7各种风险水平及其可接受程度
风险值(死亡/a)
危险性
可接受程度
10-3数量级
损伤危险性特别高,相当于人的自然死亡率
不可接受
10-4数量级
操作危险性中等
必须立即采取措施改进
10-5数量级
与游泳事故和煤气中毒事故属同一量级
人们对此关心,愿采取措施预防
10-6数量级
相当于地震和天灾的风险
人们并不关心这类事故发生
10-7~10-8数量级
相当于陨石坠落伤人
没有人愿为这种事故投资加以预防
目前国内液氨装置很多,绝大多数都能安全运行。
根据有关资料,本工程重大风险事故的发生概率在10-5次/a。
通过严格的风险防范措施,可将本项目风险值数量级控制在10-5次/a以下,风险程度是人们所关心的,但在可接受范围之内。
5.5风险防范措施
为使环境风险减小到最低限度,必须加强风险管理,制定完善的风险防范措施,尽可能降低拟建工程环境风险事故发生的概率。
a.建筑安全防范措施
本项目贮存设计严格执行有关防火、防爆规定,储罐周围设防火墙或防火沟等,以减轻火灾时的影响程度。
建筑物的通道宽度严格执行《建筑设计防火规范》(GB50016-2006)等相应规定,主要生产厂房设两个以上安全出入口。
b.生产装置及车间安全防范措施
在生产过程中,应采取以下安全防范措施:
①对设备管道要经常进行维护保养,防止泄漏。
②日常工作中要做好安全检查,不留死角,设备要定期检修,发现问题及时采取补救措施。
③生产厂房室内设备增加强制通风设施。
装置内的设备、管道、建筑物之间保持规定的防火间距。
④制氢间禁止明火,生产中动火要严格执行有关安全管理制度,氢气阀门设置自动报警系统全时段监控,存在易燃气体的