丰田式管理规定培训课程.docx
《丰田式管理规定培训课程.docx》由会员分享,可在线阅读,更多相关《丰田式管理规定培训课程.docx(9页珍藏版)》请在冰豆网上搜索。
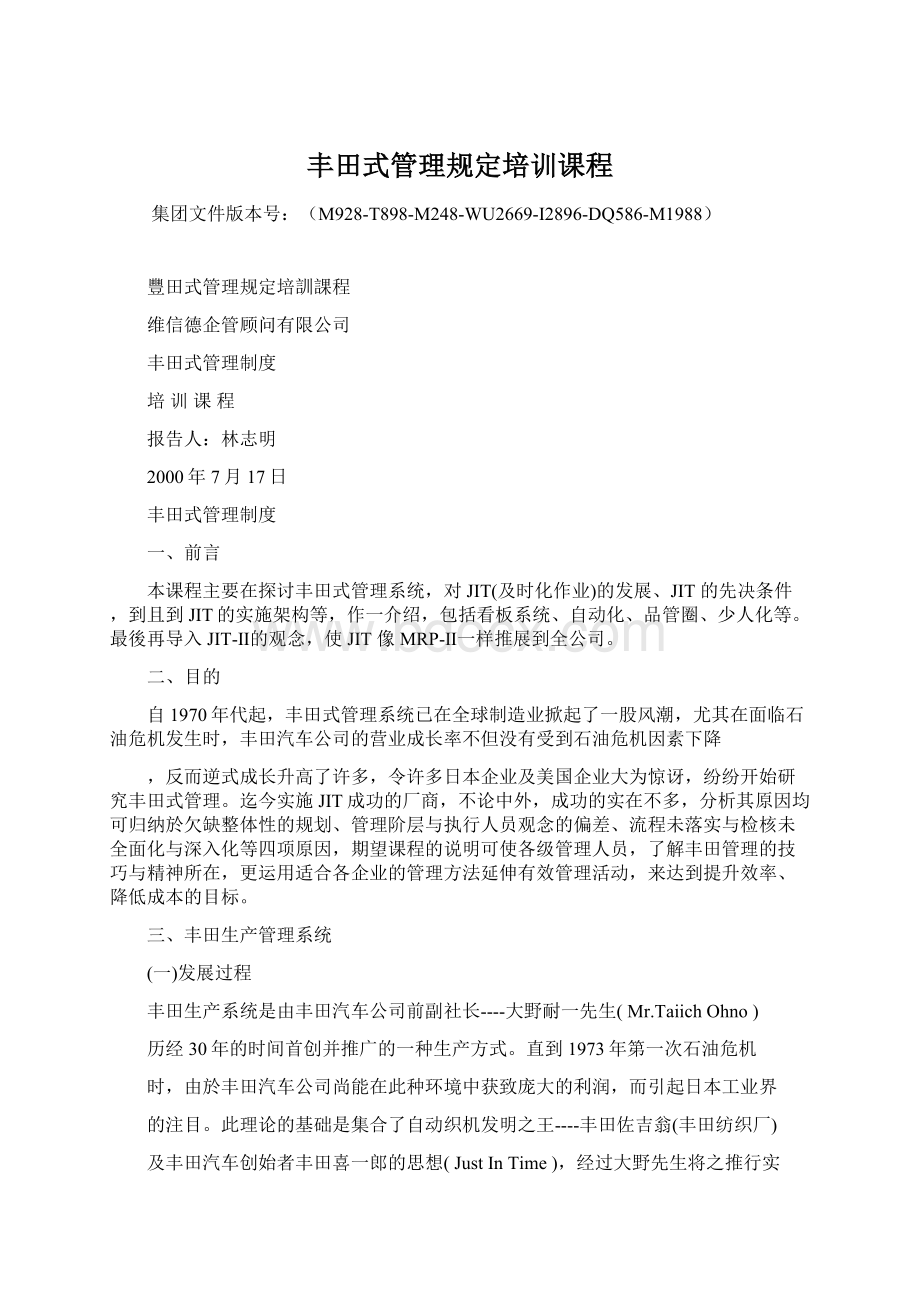
丰田式管理规定培训课程
集团文件版本号:
(M928-T898-M248-WU2669-I2896-DQ586-M1988)
豐田式管理规定培訓課程
维信德企管顾问有限公司
丰田式管理制度
培训课程
报告人:
林志明
2000年7月17日
丰田式管理制度
一、前言
本课程主要在探讨丰田式管理系统,对JIT(及时化作业)的发展、JIT的先决条件,到且到JIT的实施架构等,作一介绍,包括看板系统、自动化、品管圈、少人化等。
最後再导入JIT-Ⅱ的观念,使JIT像MRP-Ⅱ一样推展到全公司。
二、目的
自1970年代起,丰田式管理系统已在全球制造业掀起了一股风潮,尤其在面临石油危机发生时,丰田汽车公司的营业成长率不但没有受到石油危机因素下降
,反而逆式成长升高了许多,令许多日本企业及美国企业大为惊讶,纷纷开始研究丰田式管理。
迄今实施JIT成功的厂商,不论中外,成功的实在不多,分析其原因均可归纳於欠缺整体性的规划、管理阶层与执行人员观念的偏差、流程未落实与检核未全面化与深入化等四项原因,期望课程的说明可使各级管理人员,了解丰田管理的技巧与精神所在,更运用适合各企业的管理方法延伸有效管理活动,来达到提升效率、降低成本的目标。
三、丰田生产管理系统
(一)发展过程
丰田生产系统是由丰田汽车公司前副社长----大野耐一先生(Mr.TaiichOhno)
历经30年的时间首创并推广的一种生产方式。
直到1973年第一次石油危机
时,由於丰田汽车公司尚能在此种环境中获致庞大的利润,而引起日本工业界
的注目。
此理论的基础是集合了自动织机发明之王----丰田佐吉翁(丰田纺织厂)
及丰田汽车创始者丰田喜一郎的思想(JustInTime),经过大野先生将之推行实
施而成的学说。
(二)及时性生产JIT的定义
丰田生产系统的基本理念是弹性地适应需求的变化,也就是在必要的时间,生
产必要数量的产品。
丰田生产的最终目的是藉着成本的降低以创造利益,为了
达此目标,就要排除浪费,如多余的库存、搬运‥等,以降低制造成本。
且藉
着降库存而使各种问题显现,透过解决问题的改善活动及排除浪费的因素实
施,而使制造成本降低,达到丰田管理的主要目标。
除了主要目标外,还有三个次要目标:
1.能适应每月每日的需要变动,兼顾数量与种类的数量管理。
2.每项工程都能提供後面工程良好的品质保证。
3.为达成降低成本,利用人力资源时,也必须提高对人性的尊重目的。
(三)及时性生产JIT的主要架构
生产线的一贯流程,与对市场的数量及种类的需求变化,是藉着「及时化」及
「自动化」来完成。
1.及时化(Justintime):
必要的物品,必要的时候,生产必要的份量。
2.自动化:
能自动检出制程上异常现象的装备,且自动停止装置的机械。
这二个可说是丰田生产的二大支柱。
同样重要的概念还包括了下列两项:
1.适应需求变化而对作业员人数作理性调整的「少人化」。
2.透过作业员的提案改善活动的「品管圈」。
为了实现这4个概念,丰田公司采用下列几个方法:
1.使用「看板制度」以达成及时生产。
2.采行生产、平稳化的方法以适应需求变化。
3.缩短整备时间以减少生产前置期。
4.实施「操作标准化」以达成生产线的平衡。
5.注意机器设备之安排及运用「多能工」以期能保有增减作业人数之弹性。
6.藉着进行小组「改善活动」和,提案制度,以削减作业人数和提高作业员
士气。
7.藉「目视控制」制度以实现「自动化」概念「功能管理制度」以推进全公
司的品质管理。
(四)排除浪费
丰田生产方式可以称为彻底排除浪费的方式。
制造现场通常视浪费为「增加
成本负担之要素」,因此若不重视浪费的问题,将会发生很多不必要的麻烦。
◆常见的浪费有下列七种形式:
1.修改不良品的浪费。
2.生产过剩的浪费,生产过剩将导致增设机器设备、材料预支、多余操作
员金钱的损失、仓库扩大等,百害而无一利。
3.加工的浪费,自己认为最好的方式或工作,其实包含了浪费。
4.搬运的浪费。
5.库存的浪费。
6.动作的浪费:
制造过程中,假如人手、设备、机器之操作而产生找不到
物品,不良品等时,这些都是浪费的主因。
7.等待的浪费:
机器还在加工,後面的人没有工作,空手等待称为等待的浪
费。
◆改善浪费的顺序:
l.表格标准作业:
正确记录,对於日常作业要求必定按照事实写出来。
2.发现浪费:
根据步骤1的确实记录与标准作业做比较找出问题点。
3.改善:
针对浪费的地方找出解决之道
(五)看板制度(Kanban)
看板制度是对各制程的生产量进行控制的一种资讯系统。
这种生产管理,可称为及时生产,但看板制度并不等於丰田生产体系。
1.看板种类
(1)常用的看板有二种:
取用看板及生产订购看板,取用看板是记载後制程应
该向前制程领取的零组件种类和数量。
生产订购看板又被称为生产看板,
则记载前制程必须生产或订购的零组件的种类和数量
(2)供应商看板:
向零件供应商提取零取件。
供应商看板则一律使用条码。
(3)信号看板:
用来载明压铸机,或是锻造工程等批量生产。
2.看板功能
(1)避免生产过剩的浪费。
(2)索取情报、生产指示情报。
(3)目视的管理、道具。
(4)改善的道具一看板太多反而没有效果。
3.看板的使用技术
(1)後工程的运货人员,要将必要领取的数量与货柜,装在叉式起重机或台车
上,而搬到前工程的仓库(零件仓库)A。
(2)後工程的搬运工,於仓库A领取零件之後,须拿开装载货架内的零件生产
指示看板,放入已领取的地方。
(3)搬运人员,於自己所拿开的每一张生产指示看板後,要再挂上一张领取看
板
(4)在後工程作业一开始时,领取看板放置在收容领取看板的地方。
(5)前工程里,在一定时间或生产一定数量的零件时,从看板领取处搜集而来
的生产指示看板,须按仓库拿走的顺序,将这些生产指示看板放在其收容
处才行。
(6)按照放在收容处的生产指示看板顺序,来生产零件。
(7)进行加工零件时,这些零件与其看板,要成对的移动。
(8)在此工程中,每完成零件加工後,其零件的生产指示看板须放置仓库,让
後工程的搬运工随时领走。
4.达成看板的五个原则:
(1)後制程只有在必要的时候,向前制程领取必要数量的必要零组件。
(2)前制程应该只生产足够的量,以补充被後制程提取的零件。
(3)不良品决不送往後制程。
(4)看板的使用数目应尽量减少。
(5)应该使用看板以适应小幅度的需求变动。
5.违反看板规则的影响
(1)看板会发生状况
(2)易产生不良品
(3)增加看板数量
(4)库存增加
(5)不易发现问题点
(6)不需改善
以上的不良结果产生,对於JustInTime实施上的搬运无法运作,当然对生产现场之活性化没有帮助。
(六)自动化
丰田的自动化牵涉到品质管制,因为它使不良品无法通过生产线,并且它也有降低成本,具有因应弹性的生产及对人性更进一层的重要等等的效果。
2.达成自动化的具体技术:
(1)发生异常的时候,停止生产线所使用的特殊设计法。
A.接触式的安全系统
B.整体式的安全系统
C.行动步骤式的安全系统
(2)使作业员习於「自动化」生产的技术
A.防止盲目操作装置:
关闭型式、警示式
B.防呆装置
(3)监视生产及当异常发生的时候,加以修正的手段。
A.视觉控制:
标准操作表、看板、数字显示板和贮存处及仓库的显示板。
3.自动化前必要的注意事项
(1)定期更换机器的配件
(2)定期检查品质
(3)定期补给机油
(4)定期除去粉屑等等
(5)防止异常停止再发生。
以上的维护作业,需靠各维修人员定期并加以注意维修,使有好的设备,才能制造优良的产品。
(七)及时生产
「及时化」就是在必要的时间,把必要的东西(产品)送到需要的地方。
要实现及时化,必须完成下列三项准备:
1.生产平准化
2.作业标准化
3.制程设计。
而看板的任务,则是作为情报传递的资讯系统。
◆生产平准化
所谓生产平准化就是每一个单位制程时间,不管在数量或种类方面都处於平均化的状态。
平准化生产的优缺点:
1.优点:
(1)零件的使用量会安定化。
(2)各工程以及承包企业的生产负荷量会安定化。
(3)可降低制品或工程进行间半制品的库存量。
(4)依据小批量的生产与搬运,单位制品的平均生产占用时间,可以缩减。
2.缺点:
(1)由於各制品的种类大不相同,反而需要有事前的训练,但实际上其作业的
情形,常有延误或零件装置错误的现象。
(2)必须具备能适用各种制品作业的夹具和制造系统。
如:
弹性制造系统
(FMS)、群组技术(GT)。
(3)对於前工程作业,需要以小批量且频繁的领料,而为要缩短库存与占用时
间,有必要缩短调换机件的时间。
(4)当市场需要有大幅度变动时,就会有生产量难以配合的情形。
◆作业标准化
使生产现场有提高生产效率的依据,有管理者管理自己的过程的基础,便是标准作业。
标准作业由下列三个因素所成立。
1.周期时间:
指一件物品必须以多少时间来装配或制造公式为:
一天必需数量=一个月的必需数量/实际工作日数
周期时间=实际工作时间/一天的必需数量
2.作业顺序:
是指作业人员在加工物品时,由材料至制品的次序变化过程。
3.在制品标准存量:
乃指作业过程内最低需要量的半成品,也包括装在机器上
的在内。
◆制程设计
1.把单功能作业员变成多功能作业员。
如:
一人多机、工作轮调、U型生产线
2.缩短特定制品的生产时间。
3.排除各制程间不必要的库存。
4.多功能作业员观念,减少所需的作业员人数。
5.参与工厂整体生产体系的筹划,因而对自己的工作更为满意。
6.每个作业员能从事团队合作而彼此互相协助。
(八)品管圈(QCC)
是指为了解决作业现场存在的问题,而由作业员组成的小团体,自发性并且继续不断地研读品质管理的观念和技术。
其最终目标是要增进作业员的责任感,提供作业员达成生产目标的方法,并使得作业员的技能得以提高成长。
其研究范围包括品质管制、成本降低、设备保养、工厂安全、产业公害等。
三、JIT执行步骤
(一)丰田生产方式的特徵
1.和经营直接有关的公司IE活动:
(1)生产计划予以平准化
(2)生产批量愈小愈佳
(3)彻底做到必需的物料,在必需时才制造必要的数量
2.更重视事实的科学态度
(1)反覆的问5次「why」
(2)使问题一目了然
(3)使解决问题的目的明朗化
(4)即使只有一个不良品,也要想出对策
3.能切身实践的工数减低活动
(1)从作业的改善设备改善
(2)工数与人数、省力化与省人化
(3)所谓的检查就是反省
4.「经济性」为一切的判断基准
(1)设备的稼动率,视生产需要量而定
(2)有余力就练习调换机件
(3)生产现场才是主角
(4)重视应变能力
(二)JIT制造的先决条件
1.使生产排程稳定
2.使工厂集中
3.制造中心的生产产能增加
4.改善生产品质
5.培养多能工
6.透过预防保养,以减少设备故障
(三)改革程序:
1.意识改革一教育训练
2.现场改善之基础:
5S
5S---整理、整顿、清扫、清洁、纪律
3.JIT的纵面改革
生产现状分析---P、Q分析、标准流程、U型生产线、平准化、标准作业
4.横面推展,由一个部门,推展到全公司
(四)JIT成功的七个步骤
l.Educatinandleadership教育和领导力
2.CompanyassessmentofJITelements实行JIT的评估
3.Implementationplan执行JIT的计划
4.Pilotimplementation政策执行
5.Smallgroupimprovementorgamization小团体的改善组织
6.performanceevaluation绩效评估
7.Companywidetransitionandinternalization小组扩大实施,不断转变和
内部化
四、JIT-Ⅱ
JIT-Ⅱ什麽是JIT-Ⅱ它与JIT有什麽关系我们可说JIT的目的是要降低成本
,达到零库存或减少库存的生产方法。
JIT-Ⅱ是一种涵盖後勤工程与运输的及时观念,它的目标是合并人力资源的专家技术运用到规划和协调程序上获得解决的方式
。
这个想法是使物料规划和执行结合,藉着获得可能中断的早期预告来促进所有的操作。
使用JIT-Ⅱ的概念和有关的技术在後勤和运输提供一些改长方法或创造新的概念,如:
新库存位置的创造。
JIT-Ⅱ的好处在工厂内的努力包括
1.同步工程
2.降低成本
3.采购支援到设计工程
举个例子:
公司要用人,可与学校合作,培养专业人才,等学生毕业後,即
可直接到这家公司上班。
这不但是培养人才的方法,而且也可降低人力资源
的浪费。
目前实施JIT-Ⅱ的厂商有GM、GE、IBM、Intel、Whirlpoo1(惠普)
等,且其成效还不错。
五、结论
实施JIT要按步就班,且要确实执行,如果缺乏正确的浪费意识,再怎麽测量时间,怎麽研究动作,都无法改革现场。
因此丰田生产方式不是纸上谈兵,要能在现场找出浪费点,并找寻解决之道,这才是丰田生产方式最重要的手法。
不论中外,虽有许多厂商实行JIT,可是成效都不佳,能成功的只有少数几家;可能的原因有下列几点:
1.不能彻底实施:
虽然他们是实施JIT,但对一些方法或系统并没有了解实施情
况或实施前的准备工作不够,才会导致失败。
2.没有全员共识:
要实施一政策或方案,必须让全体员工了解这种制度,换句
话说就是要加强训练,进行意识改革的工作。
3.不能半途而废:
许多公司在实施後的一段期间内,其成效不佳,就草草结束。
半途而废,这是最常见的情形。
以上的几点是常见的几个原因。
从本文中我们了解到意识改革的重要,且全员参与,
JIT成功的机会较大。
JIT-Ⅱ是末来发展趋势,熟悉此生产系统,对降低成本的目标
,愈易达成。