钢结构工程施工方案.doc
《钢结构工程施工方案.doc》由会员分享,可在线阅读,更多相关《钢结构工程施工方案.doc(45页珍藏版)》请在冰豆网上搜索。
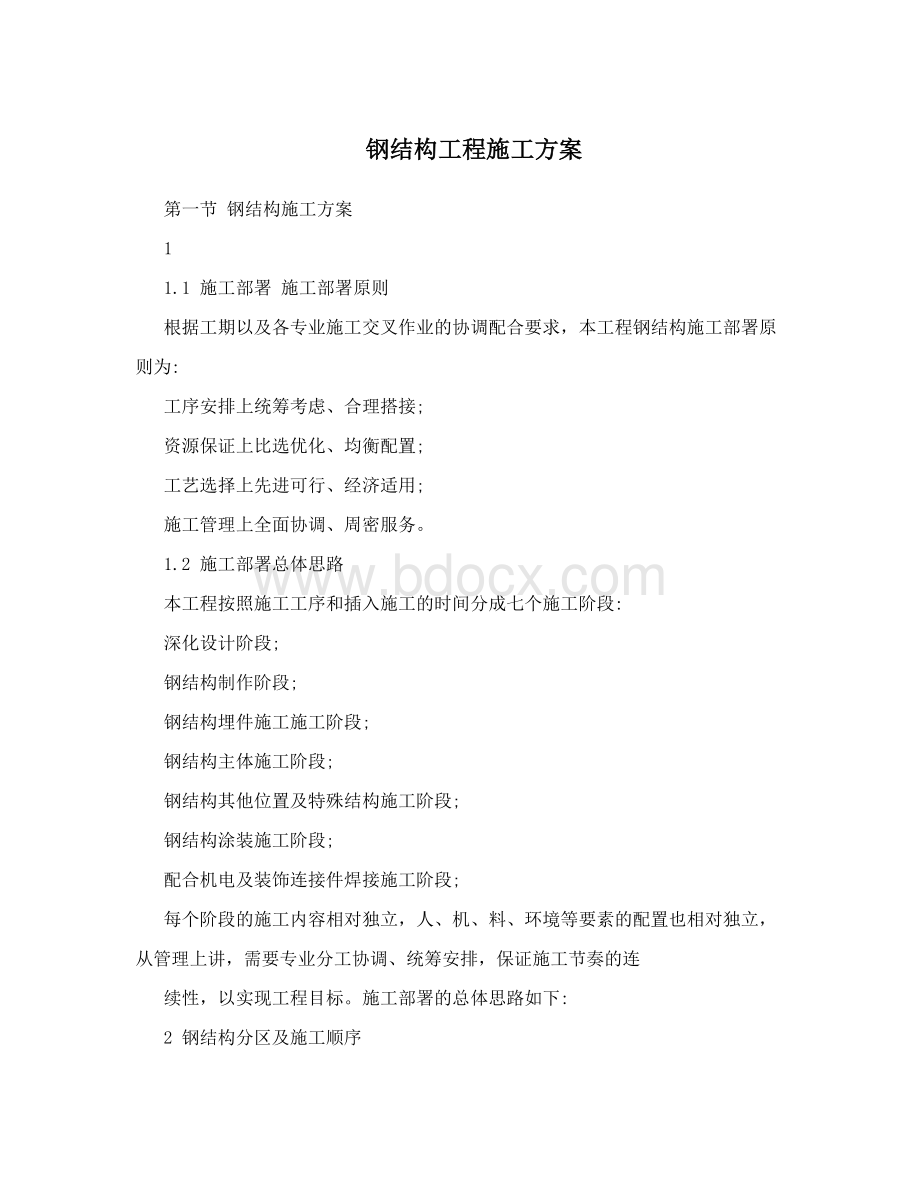
钢结构工程施工方案
第一节钢结构施工方案
1
1.1施工部署施工部署原则
根据工期以及各专业施工交叉作业的协调配合要求,本工程钢结构施工部署原则为:
工序安排上统筹考虑、合理搭接;
资源保证上比选优化、均衡配置;
工艺选择上先进可行、经济适用;
施工管理上全面协调、周密服务。
1.2施工部署总体思路
本工程按照施工工序和插入施工的时间分成七个施工阶段:
深化设计阶段;
钢结构制作阶段;
钢结构埋件施工施工阶段;
钢结构主体施工阶段;
钢结构其他位置及特殊结构施工阶段;
钢结构涂装施工阶段;
配合机电及装饰连接件焊接施工阶段;
每个阶段的施工内容相对独立,人、机、料、环境等要素的配置也相对独立,从管理上讲,需要专业分工协调、统筹安排,保证施工节奏的连
续性,以实现工程目标。
施工部署的总体思路如下:
2钢结构分区及施工顺序
根据整个工程特点及其汽车吊行走路线的情况,本工程将综合车间(扩建)工程分成四个相对施工区域组织施工。
钢结构平面安装顺序按照先安装钢柱再安装钢梁的顺序进行。
从厂房的中间位置开始向两侧扩展安装,四个施工区域同步施工,安装时要形成稳定空间单元。
每一单元按照先钢柱,后钢梁的顺序进行。
完成一个作业区后要及时进行测量、校正、高强螺栓安装、焊接。
钢结构平面施工顺序
3施工方法
本工程钢结构采用4台70t汽车吊,先将部分需要地面拼装的钢梁和钢柱提前拼装完成,之后按照先安装钢架的钢柱,在安装钢柱的同时安装钢梁的顺序施工。
3.1
3.1.1各阶段施工顺序部署深化设计组织管理
钢结构深化设计涉及工厂制作,过程运输,现场安装,同时在现场安装时还应考虑与土建,机电设备、给排水、暖通等多个专业的交叉配合。
为保证构件的加工制作、长途运输、现场安装的顺利进展,保证钢结构的施工质量,在钢结构安装项目部下专门设置钢结构深化设计部,对钢结构进行深化设计管理,确保工程质量。
3.1.2深化设计对制作工艺的考虑
1)深化设计前进行工艺评审
制作工艺图是钢结构加工制作的直接指导文件,钢构件加工制作前,首先需要对制作工艺评审,得出可实施的具体方案。
深化设计前,深化人员应和工艺人员熟悉图纸,对图纸中的信息进行整理,开展工艺评审,物资、商务、生产、检测等相关部门共同参与,对重难点部位的制作工艺进行分析,如特殊的板材、板幅要求、检测要求做等予以明确,并提出相关建议,对暂时不明确的问题由深化设计负责人与设计、现场、业主等进行沟通,在深化设计前形成合理的工艺评审文件,在深化设计图中得以体现。
2)深化建模、出图时要考虑工艺制作方案
深化建模过程中应紧密结合制作工艺方案。
深化设计人员要了解零部件的工厂加工方法,车间施工用器具的使用方法,零部件的工厂组装顺序,厚板的焊接处理方法、季节变化对加工制作的影响。
通过对这些的了解使建模时在依据原设计意图的前提下,结合工艺方案,对节点进行构造设计与处理等。
深化图纸中应提供工艺方案所需的所有信息,图纸是对模型的直观表现,是制作工艺的基本资料,所以深化出图工作尤为重要。
这就要求深化人员应在图纸中明确的表示构件组装所需的尺寸、零部件编号、数量、材质,各种孔洞的尺寸规格,特别是焊缝的形式,除深化总说明之外特殊构件的要求、说明。
3)深化设计对安装、运输的考虑
A构件分段分节的合理性
分段分节是深化设计建模前首先考虑的基本问题。
深化设计前,应和运输、安装等相关单位沟通协调,充分考虑运输的方法、现场布置和吊重
能力、现场条件,对安装的分段分节进行核对。
检查构件是否超出吊装要求的范围,如果超重应及时和安装沟通,划分合理的分段分节以便进行图纸深化。
B对安装现场临时措施进行合理深化
在深化设计前期,应和安装单位沟通协调,对每种构件吊装措施设计进行交底。
(1)本工程钢柱吊耳设置原则如下:
在钢柱上下口各设置四块带吊装孔的耳板。
连接板、耳板材质均为Q345B,焊缝为全熔透一级焊缝,角焊四周包边。
(2)钢梁吊装措施:
3.1.3深化设计对应力集中的考虑
构件在制作过程中,应考虑消除应力集中问题,不但要做好焊前预热,焊后保温等措施外,在深化设计阶段,同样需对各个部件的相关部位在构造上进行处理,以达到消除应力集中的目的。
例如因板厚度、宽度不同的对接需按要求进行过度处理;工厂焊接、现场焊接的相关部位,需按照规范要求设计合理的弧形过焊孔;深化建模时应多和设计沟通,尽量避免焊缝交叉;消除应力集中现象。
3.1.4沉降量补偿值的考虑
对于本工程,钢柱构件应考虑竖向荷载作用下的累计沉降量的影响,可通过现场施工过程中测量得出的精准数据,根据施工阶段,对沉降量值做明确的说明,并反馈到深化设计,最终在工厂制作时将钢柱作加长补偿,但具体的沉降量值需事先得到原设计、业主、监理等各方的统一意见。
3.2
3.2.1钢结构加工制作准备加工制作总体部署
A加工制作总体思路
本工程主要构件为H型截面构件,构件截面形式均为常规截面形式,构件尺寸也均为常规尺寸,我司的H型钢生产线能很好的满足本工程构件加工制作的要求。
我司将充分发挥本单位雄厚的制作实力,配合总包单位,按照工期以及利用现场可利用场地,做好本工程构件的加工制作及运输计划。
3.3
3.3.1钢结构加工制作加工制作工艺技术准备
1)加工制造工艺流程总流程
3.3.2钢材前期加工通用工艺
1)钢板矫正
A为保证本工程钢构件的加工制作质量,钢板如有较大弯曲、凹凸不平等问题时,应先进行矫正,钢材矫平后的允许偏差见下表:
B碳素结构钢在环境温度低于-16?
、低合金结构钢在环境温度低于-12?
时不应进行冷矫正。
C采用加热矫正时,加热温度,冷却方式应符合下表的规定:
(注×:
不可实施;?
:
可实施.上述温度为钢板表面温度,冷却时当温度下降到200~400?
时,须将外力全部解除,使其自然收缩。
)
D矫正后的钢板表面,不应有明显的凹面或损伤,划痕深度不得大于0.5mm,且不应大于该钢板厚度负允许偏差的1/2。
2)A切割加工
材料的切割加工使用下列设备加工:
零部件加工
切割工艺参数按下表选取:
火焰切割原则上采用自动火焰切割机或半自动火焰切割机,自动(半自动)切割无法实施的位置可以在加靠模的情况下采用手工火焰切割。
钢材切割面或剪切面应无裂纹、夹渣、分层和大于1mm的缺棱。
气割加工的零件允许偏差应符合下表的规定:
机械剪切的允许偏差应符合下表的规定:
B材料的拼接
所有零件尽可能按最大长度下料,同时注意材料的利用率。
图上有注明拼接时,按图施工,但拼接接头必须避开构件或开孔边缘200mm以上。
图上没有注明拼接时,拼接位置应在内力较小处,一般可留在节间长度1/3附近。
H形钢翼缘板拼接长度不应小于2倍板宽,且钢板长度最短不得小于800mm。
腹板拼接长度?
600mm。
接缝与节点位置、高强螺栓连接板边缘、开孔距离必须?
200mm。
翼缘板与腹板接缝需错开200mm以上。
板对接时,应检查以下几个方面合格后方可施焊:
C端部铣平加工
钢柱现场焊接的下段柱顶面内的隔板应进行端部铣平加工;端部铣平加工应在矫正合格后进行。
钢柱端部铣平采用端面铣床加工,零件铣平加工采用铣边机加工。
端
部铣平加工的精度应符合下表的规定:
D坡口加工
构件的坡口加工,采用半自动火焰切割机进行。
坡口面应无裂纹、夹渣、分层等缺陷。
坡口加工后,坡口面的割渣、毛刺等应清除干净,并应打磨坡口面露出良好金属光泽。
坡口加工的允许偏差应符合下表的规定:
坡口加工质量如割纹深度、缺口深度缺陷等超出上述要求的情况下,须用打磨机打磨平滑。
必要时须先补焊,再用砂轮打磨。
E制孔
零件上高强度螺栓孔应采用摇臂钻床、自动数控钻床加工。
型钢上高强度螺栓孔采用三维钻床加工或用磁力钻钻模板进行钻孔加工。
普通螺栓孔采用摇臂钻床、自动数控钻床加工。
梁腹板设备孔开孔采用数控火焰切割机在零件下料时切割加工。
底脚螺栓孔,原则上采用钻孔方式加工;直径在φ80mm以上地脚螺栓孔可采用数控火焰切割加工,加工后应清理割渣并用磨头打磨孔壁符合精度要求。
钻孔后孔周围的毛刺、飞边等须用打磨机清除干净。
螺栓孔直径控制如下:
螺栓孔孔壁表面粗糙度Ra不应大于25μm,其允许偏差应符合下表的规定:
螺栓孔孔距的允许偏差应符合下表的规定:
F高强度螺栓连接摩擦面的加工
高强度螺栓连接摩擦面的加工,采用喷砂或抛丸加工处理。
高强度螺栓连接摩擦面应保持干燥、整洁,不应有飞边、毛刺、焊接飞溅物、
焊疤、氧化铁皮、污垢等。
加工处理后的摩擦面,应采用塑料薄膜包裹,以防止油污和损伤。
在钢构件制作的同时,按制造批为单位进行抗滑移系数试验,抗滑移系数?
0.45,并出具试验报告。
同批提供现场安装复验用抗滑移试件。
3)厚板切割
A厚板切割的注意点:
因钢板较厚,钢材的上下受热不均匀、操作不当容易引起不能沿厚度方向割穿,造成切割失败;燃烧反应沿厚度方向需要一定时间,切割氧在下部纯度较小,后拖量增大;
熔渣较多,容易造成在切口处堵塞;在切割过程中如果中断,再次切割由于熔融的氧化铁不能及时排出去,厚板重新起割极为困难。
B厚板切割的主要工艺措施:
1)实现厚板切割最主要的保证措施是向气割区供给足够且稳定的氧气,所需切割氧流量Q可按下式估算;Q=0.09~0.14t(t为板厚);
2)切割氧压力要调节适当,保证能及时把氧化铁吹排出去。
压力宜高不宜过低,否则后拖量较大,出现割不透的现象;
3)切割开始后,在切割过程中必须连续切割;
4)切割速度按以下曲线进行:
切
割
速
度切割时间(秒)
为了保证有足够的预热温度,最好采用乙炔气体;
切割采用等压式割嘴或外混式割嘴,其中后者切割效果较好,割嘴号码为5~7号;
为了保证切割面的质量,应至少留有20~40mm切割引线。
C厚板切割工艺参数
D厚板切割工艺要点
可以通过观察厚板下部出渣情况来判断切割氧的压力是否合适,
如果出渣速
度较快,在板背面粘沾量较少,听到“噗噗”声音,表明氧气压力,切割速度适中;如果在板背面粘沾量较多,表明切割速度较慢、氧气压力较小或预热温度较高;
厚板的切割一旦在起始切割点割透,只要保持稳定的速度和气体压力,切割效果将会很好。
具体是先把割嘴切割氧风线的位置外移于至板边0.5mm,对钢板加热,加热到亮红色后,切割氧调节阀全打开,再缓慢提高切割速度,稍作停留,观察是否能割透,待割透后,继续前行并逐步提高切割机速度,待切割稳定后,将速度稳定在一定值上;
中间有圆孔的切割,先要用磁力钻在起始点先钻φ10~φ14的工艺孔,然后再切割;
为了确保厚板切割的准确性,应在切割前先对其模拟切割,并用石笔
跟踪把模拟线描出来,校验其尺寸是否符合要求,然后再进行真正切割。
4)
A基本要求
组装准备:
组装前按施工详图要求检查各零部件的标识、规格尺寸、形状是否与图纸要求一致,并应复核前道工序加工质量,确认合格后按组装顺序将零部件归类整齐堆放。
选择基准面作为装配的定位基准。
清理零部件焊接区域水分、油污等杂物。
组装时的注意事项:
组装或组装焊接时,正确使用直角定位卡具等以保证组装质量。
组装时应注意构件的保护,避免母材损伤。
角焊接部分尽可能连接紧密,对接焊接时根部间隙、衬垫板的间隙及零部件的错边在装配时要特别注意。
对接接头坡口的组装,在操作时应避免错边或电弧擦伤。
组装出首批构件后应进行首件认可,经认可合格后方可组装。
组装精度:
装配时应采取适当的拘束以控制焊接变形,并应加放焊接收缩余量以及合适的反变形以控制构件尺寸,保证形