连接松动的诊断案例分析综述.docx
《连接松动的诊断案例分析综述.docx》由会员分享,可在线阅读,更多相关《连接松动的诊断案例分析综述.docx(16页珍藏版)》请在冰豆网上搜索。
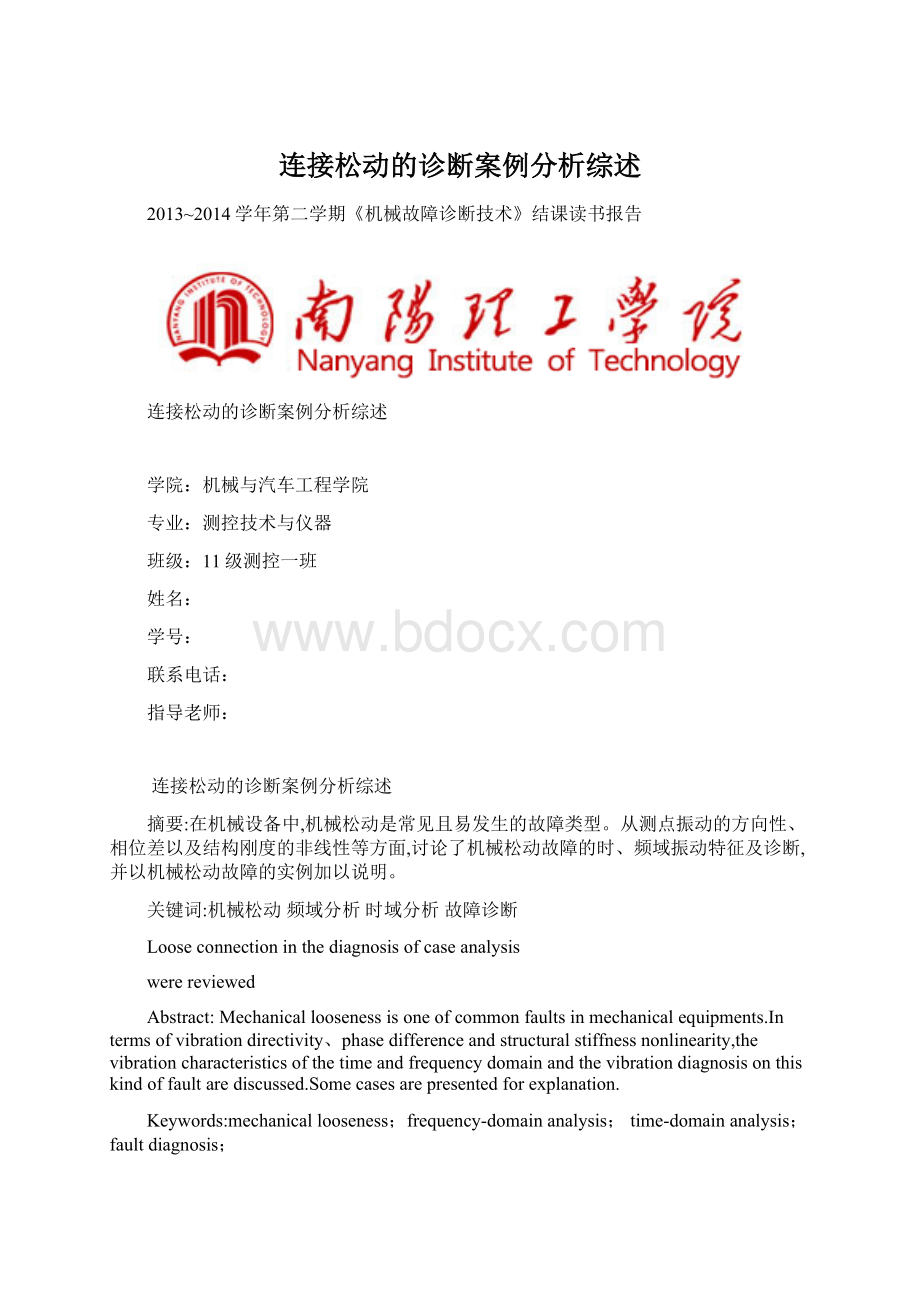
连接松动的诊断案例分析综述
2013~2014学年第二学期《机械故障诊断技术》结课读书报告
连接松动的诊断案例分析综述
学院:
机械与汽车工程学院
专业:
测控技术与仪器
班级:
11级测控一班
姓名:
学号:
联系电话:
指导老师:
连接松动的诊断案例分析综述
摘要:
在机械设备中,机械松动是常见且易发生的故障类型。
从测点振动的方向性、相位差以及结构刚度的非线性等方面,讨论了机械松动故障的时、频域振动特征及诊断,并以机械松动故障的实例加以说明。
关键词:
机械松动频域分析时域分析故障诊断
Loose connection in the diagnosis of case analysis
were reviewed
Abstract:
Mechanicalloosenessisoneofcommonfaultsinmechanicalequipments.Intermsofvibrationdirectivity、phasedifferenceandstructuralstiffnessnonlinearity,thevibrationcharacteristicsofthetimeandfrequencydomainandthevibrationdiagnosisonthiskindoffaultarediscussed.Somecasesarepresentedforexplanation.
Keywords:
mechanicallooseness;frequency-domainanalysis;time-domainanalysis;faultdiagnosis;
前言
机械松动是常见且易发生的故障类型,主要指两种情况,一种是指设备结构框架或底座松动,它带来的后果是引起整个机器松动、振动加剧;另一种情况是零件之间正常的配合关系被破坏,造成配合间隙超差而引起的松动,比如滚动轴承的内圈与转轴或外圈与轴承座孔之间的配合,因丧失了配合精度而造成松动。
机械松动不仅是设备振动的原因,而且还加剧振动状态。
即使只存在小量的不对中或不平衡,由于机械松动的存在可能使设备振动比只存在不对中或不平衡时更大。
以下讨论机械松动故障的振动特征及诊断,并用实例加以说明。
连接松动故障的机理:
振幅由激振力和机械阻抗共同决定的,松动使连接刚度下降,这是松动振动异常的基本原因。
支承系统松动引起异常振动的机理可从两个因素加以说明:
1)当轴承套与轴承座配合具有较大间隙或紧固力不足时,轴承套受转子离心力的作用,沿圆周方向发生周期性变形,改变轴承的几何参数,进而影响油膜的稳定性。
2)当轴承座螺栓紧固不牢时,由于结合面上存在间隙,使系统发生不连续的位移。
现代故障诊断方法:
工程机械运行的状态千差万别,出现的故障也是多种多样,采用的诊断方法也各不相同。
在众多的诊断方法中,比较常用的诊断方法有振动监测诊断方法、无损检测技术、温度诊断方法和铁谱分析方法等。
近十几年来,模糊诊断、故障树分析、专家系统、人工神经网络等新的诊断技术不断出现,故障诊断技术逐步向智能化方向发展。
一、结构框架或底座松动
这类松动包括设备底脚、基础平板和混凝土基础强度刚度不够,出现变形或开裂;地脚螺栓松动等。
这类松动的振动频谱中占优势的是工频(或转速频率),这与不平衡状态相同;但振动幅值大的部位很确定,有局限性,这点与不平衡或不对中情况不同。
另外,还要进一步比较各方向之间的相对幅值,观察它们的相位特性。
例如,轴承座水平与垂直方向振幅、相位差,这类松动的振动具有方向性,在松动方向振动较大,比如垂直方向振动远大于水平方向;水平和垂直方向相位差为0度或180度(而不平衡故障中水平和垂直方向相位差约为90度)。
此时,测量应向下移到设备底脚、基础平板和混凝土基础上,比较不同位置振动在工频(或转速频率)处的幅值、相位。
如果两个位置的振动幅值和相位存在很大差别,说明有相对运动,这可帮助寻找松动源。
需要指出,机械松动导致非线性刚度改变,变化程度与激振力有关,因而松动振动具有非线性特征,其频率成分除了基频(等于转速频率)以外,还产生高次谐波(2、3等)和偶次分频(如1/2、3/2倍基频)振动,频谱结构成梳状;其振动幅值也与负荷有密切关系,将随着负荷增加而增大;其振动状态对转速(即激振频率)的变化反映也很敏感,振动值随转速的增减而表现出无规律的变化,忽大忽小,呈跳跃式变化[1~2]。
案例1某水泥厂原料车间用于收尘作业的一台引风机出现振动异常,且噪声较大,风机转速为1490r/min。
经测试第(4)点振动幅值远大于其它测点(测点布置见图1,测点①~④分别位于电机左右两个端盖和风机两个轴承座上),垂直方向最大振幅为36.76mm/s,水平方向最大振幅为11.05mm/s。
第!
点垂直方向振动的频谱见图2,其频谱结构成梳状,最大峰值在转速频率25Hz处,并伴有2~7倍谐波;特别是在约13Hz,即1/2倍转速频率处有较大峰值,又在转速频率处水平与垂直方向振动的相位差约为10度,初步推断引风机可能存在松动和不平衡故障。
因为分数谐波能量也较高,并有明显高次谐波,则机械松动较不平衡严重。
从机器结构和频谱特征分析,可能是基础松动。
经仔细检查发现靠近风机侧轴承座基础平板地脚螺栓已松动。
重新紧固螺栓后,振动明显降低。
经再测试,最大振幅已降至7.5mm/s,但仍在“警告”范围之列。
此时的振动频谱图中可明显看出能量集中在转速频率处(25Hz)。
经分析它主要是由不平衡引起的。
再对此风机进行现场动平衡,动平衡后立即测试,最大振幅降至2.6mm/s,该风机运行状态已属正常。
图1引风机测点布置图
图2测点④垂直方向振动频谱
案例2山钢集团济钢炼铁厂400m2烧结机2#主抽风机振动数椐及频谱分析(转速870r/min),见表1、2,图3、4.测点:
400m2烧结机2#主抽风机/zcfj4h(水平)。
动态故障分析结论:
400m2烧结机2#主抽风机风机轴承座振动分析。
(1)风机转子存在动不平衡现象,振动位移、速度值较大。
(2)再看垂直振动分析报告。
测点:
400m2烧结机2#主抽风机/zcfj4v(基础垂直测试点)动态故障分析结论:
400m2烧结机2#主抽风机垂直振动故障:
频谱分析为工频,
位移值:
100μm,并查看轴承座底座有油气泡冒出,底座螺栓松动。
2011年8月25日计划检修对转子进行检查,挂灰少许,同时紧固轴承座底角螺栓,振动降低到允许范围内,如果不测试底角螺栓处,单从水平的振动数椐、频谱分析上看,主抽风机转子存在不平衡、不对中现象,如果按此结论下检修工单,处理后振动还是消除不了,错过了计划检修时间,通过测试底角螺栓及时发现松动问题,在计划检修中同步处理,消除了设备隐患。
图3
图4
二、轴承在轴承座中松动或部件配合松动
这类松动包括轴承在轴承座中松动、轴承内部间隙过大和轴承在轴上松动或转动。
通常是由于轴承外套在轴承座压盖内松动,轴承内环在轴上转动,滑动或滚动轴承间隙过大,叶轮轴上松动等引起的[1,3~5]。
案例3(图5)是某水泥厂6组管磨机齿轮减速箱传动示意图,减速箱各轴转频和啮合频率见表3(电机转速为995r/min)。
测点的布置为:
测点①放在轴I轴承座(非电机端)垂直向,测点②③分别放在轴I两轴承座底部水平方向。
表3减速箱各轴转频和啮合频率
图56#组磨齿轮减速箱传动示意图
测点①振动加速度幅值谱,②③两测点加速度时域波形分别如图7、8所示。
由轴I非电机端轴承座垂直向振动加速度信号谱图(图7)可见,谱线非常丰富,在分析的频率范围从低到高都有表现。
幅值从大到小的主要频率成分分别是661.30、991.71、644.68、330.41和16.62Hz等,显然,轴I、(上一级传动齿轮啮合频率(330Hz)及其倍频、三倍频成分占主导,而且倍频、三倍频幅值已远高于啮合基频,在这些频率附近可见陡而窄的边频,说明一级啮合齿轮出现严重磨损。
值得注意的是,16.62Hz谱线幅值较大,在其附近进行细化谱分析(图6),可以看出,除与轴I转频16.50Hz基本一致的16.62Hz峰值外,其右边有幅值较小的倍频(33.24Hz)成分,特别是还有3/2倍频(24.44Hz)成分,其左边也出现1/2倍频(8.31Hz),这种谱线特征表明转轴%非电机端轴承座上机件可能松动,如轴承约束松弛、轴承间隙超差等[1]图8说明转轴I非电机端轴承座上水平振动远高于电机端,并含冲击信号波形,该振动的频谱也明显符合机件松动的特征,即除有明显1和2转速频率峰值外,高次谐波频率成分丰富,还有偶次分频成分。
拆开轴承座压盖检查发现,外环与轴承座之间径向配合间隙超差出现松动。
图6轴I轴承座(非电机端)垂直振动加速度幅值谱在轴I转频(16.50Hz)附近的细化谱
图76#组磨齿轮减速箱轴I轴承座(非电机端)垂直振动加速度幅值谱
图86#组磨齿轮减速箱轴I轴承座底部电机端(信号1)和非电机端(信号2)水平振动加速度波形
三、大型机组松动故障诊断
本文针对邢钢烧结厂大型风机机组的监测,从时域上进行了时域波形特征和振动幅值对比分析,并进行了自相关分析;从幅域上进行了各有量纲和无量纲参数的分析;从频域上用幅值谱呈现的频谱特征进行了对比分析;通过三域分析结果诊断出电机与基础连接松动故障。
案例4邢台钢铁股份有限公司烧结厂的电机与风机直连大型机组,正常运行时各测点的振值较小。
2004年2月上旬,振动呈逐步上升趋势。
为查找故障源消除异常振动,我们对该机组进行了监测分析。
检测发现,测点4处的实测值比其它各测点要大(为正常值的三倍以上),各测点实测值都比正常值大,故对电机测点4重点分析。
一、时域分析
由表",图",图4可知,测点4垂直方向时域波形跳跃较水平方向剧烈,谱峰变宽,通频振动幅值是水平方向的1.58倍,最大瞬时峰值是水平方向的1.5倍。
诊断实践表明,垂直方向振值超过裂纹周期性时闭时开,对振动的影响比较复杂。
出现横向疲劳裂纹时,轴的刚度呈各向异性,振动带有非线性性质。
一倍频和二倍频分量随时间逐渐增大,特别是二倍频分量,随裂纹深度的增加而明显增大。
(1)滑动轴承间隙变大
轴与轴承间隙过大,类似于不对中和机械松动,应注意区别。
此时径向振动较大,特别是垂直径向;可能有较大的轴向振动,止推轴承可能有较高次谐波分量;径向和轴向时域为稳定的周期波形占优势,每转一圈有1~3个峰值;没有较大的加速度冲击现象。
若轴向振动与径向振动大小接近,表明问题严重。
(2)轴承压盖松动
振动频率为转频,并有高次谐波和分数谐波。
振动具有方向性,幅值稳定。
5轴系同轴度差造成轴系不对中的原因很多,如安装误差、调整不够、承载后的变形、机器基础的沉降不均匀等。
转子径向振动以一倍频和二倍频为主,轴向振动在一倍频、二倍频和三倍频处有稳定的高峰,一般可达径向振动50%以上。
若与径向振动一样大或更大,表明情况严重。
(3)其它与一倍频有关的原因
1.电机、风机等底座龟裂,引起刚度变化,易产生共振。
2.联轴器制造安装偏差造成的磨损;不配套的连接螺帽螺栓缺损;联轴器螺帽磨损。
3.转子温度梯度影响。
4.润滑油温度变化引起的失稳。
5.转子或轴承刚性变化。
6.电磁异常。
7.齿轮机构中齿轮的累积制造误差
表4测点2处水平和垂直方向的时域对比
水平方向50%时,应判为机械松动。
利用自相关函数提取随机振动信号中的周期分量,有助于进一步判定故障。
由图1可见,在间隔为60.6ms(16.5HZ)处有时大时小的明显峰值出现,较大处为0.781,表明有松动故障。
二、幅域分析
由表5,图4,图5可知,电机测点2处垂直方向测得的概率密度直方图,其通频振幅是水平方向的1.58倍,均方根值是水平方向的1.42倍,峰值、脉冲、裕度、峭度指标值均比水平方向的测值大。
此对比分析结果进一步表明,电机与基础的连接的确存在松动故障。
三、频域分析
由表6,图6,图7可知,垂直方向上,通频振幅是水平方向的1.58倍,基频振幅是水平方向的1.28倍,与水平方向相比有振值较大的分频
表5测点2处水平方向和垂直方向的幅域分析
表6测点2处水平方向和垂直方向的幅值谱对比
四、紧固件松动故障分析方法
基于小波分析方法提出一种飞行器结构紧固件松动故障分析方法。
该方法通过对振动信号进行连续小波变换得到振动信号能量在时频域的分布,比较正常信号和故障信号频带的变化规律,实现对紧固件松动故障分析。
时频分析结果显示,小波分析方法可以准确跟踪振动过程中信号频率的瞬变特性,且频带清晰,故障特征明显,为今后结构紧固件松动故障分析提供一种有效途径。
该方法对振动信号进行小波分解和重构,得到小波系数在时频域的分布;通过对比紧固件松动前后小波系数的时频分布,得出紧固件松动的具体时刻。
通过对某飞行器设备支架振动试验信号分析,确定了其螺钉松动故障发生的时刻,验证了方法的有效性。
案例5某飞行器设备舱在振动试验后,开舱发现仪器设备从支架上脱落。
试验过程中,由于空间限制在仪器附近并未布置传感器,只在仪器支架后端面布置了振动传感器,监视仪器设备连同支架的振动响应。
试验过程中分别进行了预试验和正式试验,两次试验输入条件谱型一致,正式试验比预试验振动量级高3dB。
图9为预试验及正式试验过程中仪器支架后端面振动传感器敏感到的振动信号。
图9预试验及正式试验振动信号
故障分析:
从图9中可以看出,在正式试验5s后,传感器x向振动信号幅值明显增大,且信号出现不规则的尖峰;y、z向振动信号变化规律与x向一致,但信号幅值增大不明显,传感器敏感到的振动信号表现出明显的非平稳特性。
采用morl小波对图9所示的振动信号进行连续小波分解,得到小波系数在时频域的分布如图2所示。
图10预试验及正式试验振动信号时频图
从图10可看出,预试验振动信号频带清晰,频率分布不随时间而改变,振动信号具有较好的平稳随机特性,可判断此时紧固件未发生松动故障。
同时,设备支架x向振动响应信号能量主要集中在1000Hz,y、z向振动响应信号能量主要集中在400Hz。
比较图10B和10C,z向振动信号的时频图中在1000Hz处存在能量分布,而y向振动信号的时频图中则不存在该频带。
这是由于振动过程中存在交联项,x、y、z各自方向上的振动都会引起另外两个方向的耦合振动。
由于传感器y向与重力方向一致,在试验过程中仪器支架处在舱体结构内部,无法消除支架自重影响,且支架连同仪器设备质量较大,因而在重力场中x向振动引起的y向耦合振动幅值较小。
比较预试验和正式试验振动信号小波变换结果,可以看出正式试验5s后x向振动信号频率下降,同时出现短时宽频信号直至试验结束;y、z向振动信号原有频带未出现变化,5s后出现短时宽频信号直至试验结束。
通过比较分析可以判断紧固件松动故障发生时刻在正式试验5s左右,由于仪器设备与支架之间采用轴向螺钉连接,紧固件发生松动时,设备支架轴向整体刚度明显下降,仪器及支架结构x向振动固有频率降低,导致x向响应信号频率降低;同时由于设备舱内空间有限,舱内仪器之间间隙较小,紧固件发生松动后,仪器设备与支架端部位移增加,与设备舱内仪器、结构件发生碰撞,导致x向响应信号时频图中出现典型的短时宽频撞击信号。
轴向连接紧固件松动对设备支架y、z向整体刚度影响不大,仪器与支架结构y、z向振动固有频率未明显降低,因而y、z向响应信号原有频带未发生变化;紧固件发生松动后,仪器设备连同支架与舱内仪器、件结构发生碰撞,导致y、z向响应信号时频图中出现与x向相似的短时宽频撞击信号。
由于仪器设备与支架之间采用轴向连接,故x向响应信号时频图中碰撞故障特征更为明显。
小波分析方法处理振动信号时,频带清晰,且具有良好的实时性,为振动故障诊断和分析提供了基础;2)小波分析方法可以准确跟踪振动过程中信号频率的瞬变特性,易于观察和提取振动信号中的频率信息,在结构紧固件松动故障分析方面具有较高的实用价值。
五、SVK16-3S空压机异常振动处理
案例6济钢气体公司集中空压机站使用沈鼓生产的SVK16-3S空气压缩机,该空压机为三级压缩,其额定流量15000m3/h、出口压力0.8MPa、入口压力0.103MPa(绝压),电机额定电压6kV、功率1800kW,控制系统采用GEVersaMaxPLC控制系统,轴振动监测采用派利斯振动仪表,其控制盘与空压机本体一同安装在生产现场。
上位监控采用IFix软件,PLC监控数据通过以太网通信与中控室上位计算机通信。
该机2004年8月投产运行以来运行稳定,控制正常,但在近2年的运行过程中发生过几次原因不明的空压机振动联锁停车。
停车后检查发现振动传感器间隙电压偏离8V(有时升高至15V、有时降低至4V),传感器安装及延伸电缆连接无松动,检查传感器有不规则磨损,更换传感器后,重新启动空压机能够稳定运行较长时间。
从振动监测原理分析振动传感器与空压机轴瓦间应存在相对运动,传感器的安装不存在松动现象时只有轴瓦的振动可以导致传感器的损坏和监测参数的变化。
空压机这种不稳定的运行状态成为影响安全生产的重大隐患。
分析处理:
通过调取空压机运行记录观察,空压机振动基本正常。
振动监测数值在10~30μm,无轴瓦振动报警信息。
振动值突然升高的瞬间造成了空压机联锁停车。
根据现象分析造成联锁停车最直接的原因有可能是传感器松动,延伸电缆与传感器、变送器间的连接松动,但检查发现传感器、延伸电缆及其他连接均无松动现象。
考虑到压缩机轴瓦与振动传感器之间的相对位置,认为有可能是空压机确实存在突然的振动升高造成了空压机的联锁停车,但空压机重新启动后运行正常且能稳定运行较长时间又与上述现象矛盾。
为了排除干扰信号对空压机控制系统的影响,重新检查确认了GEVersaMaxPLC控制系统的接地电阻(电阻<4Ω)、屏蔽控制电缆接地良好,这使问题的解决陷入了困境。
进一步对空压机运行振动数据(表1)进行统计分析并绘制振动监测数据趋势图(图1)。
由图1可见,空压机运行在不稳定状态,且1~4级轴瓦振动仪表监测到的空压机振动具有很强的相关性,而空压机3、4级轴瓦振动表现得尤为突出,但振动值距报警设定值(1、2级轴瓦47μm,3、4级轴瓦41.58μm)、联锁停车设定值(1、2级轴瓦61μm,3、4级轴瓦58μm)较远,却突然达到联锁停车值使机组停车,重新启动空压机后又能稳定运行较长一段时间的问题仍没有得到很好的解释。
为此反复检查3级、4级轴振动仪表,在对传感器的拆装过程中发现,在空压机静止状态下4级轴瓦振动传感器也有不规则变形。
振动正常时的电机负荷端垂直方向频谱如图2所示,振动异常时的电机负荷端垂直方向频谱如图3所示。
随后现场对风机调整了负荷,随着负荷的下降电机负荷端垂直方向振动变化如表2所示。
从测得到的全频值来看,电机两端垂直方向振动远大于水平方向,风机两端振动不是很大,从频谱图比较来看,异常振动时产生了大量的分频,振动以1/5、2/5等分频占主导,且随着负荷的下降,振值变化比较明显。
这些特征都和基础或地脚松动的故障特征相吻合,由此可以判断造成该机振动超过报警值的原因为机组基础或地脚松动。
经现场停车检查,发现电机有一颗地脚螺栓已经断裂,更换全部地脚螺栓后,机组运行正常。
表7电机负荷端垂直方向振值随负荷变化情况
总结
上述案例诊断的共同问题是机械松动。
从前五个例子学习到机械松动是引起设备振动的常见故障之一,机械零部件的松动在典型频谱上出现旋转频率的一倍频、二倍频,并时常伴有高谐波分量。
在松动方向振动较大。
机械松动与不平衡、不对中最明显的区别是在典型频谱上还会出现振动能量较高的旋转频率的分数谐波。
在时域上不稳定的非周期信号占优势,可能有大的冲击信号;比较垂直和水平方向的振动,可以发现振动具有高度的方向性。
从例5学习到了小波分析方法处理振动信号时,频带清晰,且具有良好的实时性,为振动故障诊断和分析提供了基础;小波分析方法可以准确跟踪振动过程中信号频率的瞬变特性,易于观察和提取振动信号中的频率信息,在结构紧固件松动故障分析方面具有较高的实用价值。
从今后的发展看,故障诊断技术必须跳出仅针对机械运行过程这个环节的局限性,而应该放在产品的整个生命周期中来统筹考虑,对机械系统的整个寿命周期进行有效的分析,从而提高机械系统的可靠性和可维修性,延长系统的寿命,降低寿命周期费用。
从诊断的方式上来看,传统的诊断方法和理论对单过程、单故障和渐发性故障的简单系统可以发挥较好的作用,对于多过程、多故障和突发性故障以及复杂庞大、高度自动化的大型设备和系统,就具有较大的局限性。
专家系统主要用于复杂的机械系统,能够克服基于模型的故障诊断方法对模型的过分依赖性,人工神经网络对于故障的模式识别具有独特的优点。
将人工智能的理论和方法应用于机械故障诊断,发展智能化的机械故障诊断技术,是机械故障诊断的一个新的途径,成为机械故障诊断的一个重要研究方向。
图书馆参考文献:
[1]易良榘.简易振动诊断[M].北京:
机械工业出版社,2003.
[2]段吉安,黄志开.旋转机械松动故障的非线性力学模型[J].中南工业大学学报,2002,33
(1):
78-81.
[3]夏根福,孙蕙庆.风机不平衡与基础松动故障共存时的振动分析[J]振动与冲击,1995,14
(2):
44-47.
[4]车有向.设备松动故障的诊断[J].中国设备工程,2002,(11):
39-40.
[5]于长伟,任邦军.机械松动导致风机振动的诊断[J].中国设备工程,2004,
(2):
44-45.
[6]夏根福,孙蕙庆.风机不平衡与基础松动故障共存时的振动分析[J].振动与冲击,1995.
[7]于长伟,任邦军.机械松动导致风机振动的诊断[J].中国设备工程,2004.
[8]王宜.设备振动简易诊断技术机械工业出版社.1990
[9]沈庆根.化工机器故障诊断技术.1993
[10]北京京航公司.设备故障诊断技术及应用.1998
[11]黄庆南,杨养花,申秀丽,等.某型发动机涡轮转子前、后挡板连接螺钉松动故障分析[J].航空发动机,2004,30(4):
45-47.
[12]王丹生,朱宏平,鲁晶晶,等.基于压电导纳的钢框架螺栓松动检测试验研究[J].振动与冲击,2007,26(10):
157-160,194.
[13]董广明,陈进,雷宣扬,等.导弹支撑座连接螺栓松动故障诊断的试验研究[J].振动、测试与诊断.2005,25(3):
174-178,236.
[14]张蕾,杜振宴,武利为.基于小波再分配尺度谱的Lamb波时频特性研究[J].强度与环境.2013,(3):
31-35.
[15]符娆,张群岩,赵述元.航空发动机转静子碰摩故障信号用小波分析的方法检测和分析[J].噪声与振动控制,2012
(1):
124-127.
[16]张国渊,卫军朝,闫秀天.非平稳信号短时快变过程的时频分析方法及实现[J].机械科学与技术,2012,31(5):
735-739.
[17]马辉,陈雪莲,李朝峰,等.基于关联维数和小波分析的转子系统碰摩故障分析[J].机械强度,2011,33
(1)