黄汉军转椅底盘线控手柄固定器的模具设计.docx
《黄汉军转椅底盘线控手柄固定器的模具设计.docx》由会员分享,可在线阅读,更多相关《黄汉军转椅底盘线控手柄固定器的模具设计.docx(29页珍藏版)》请在冰豆网上搜索。
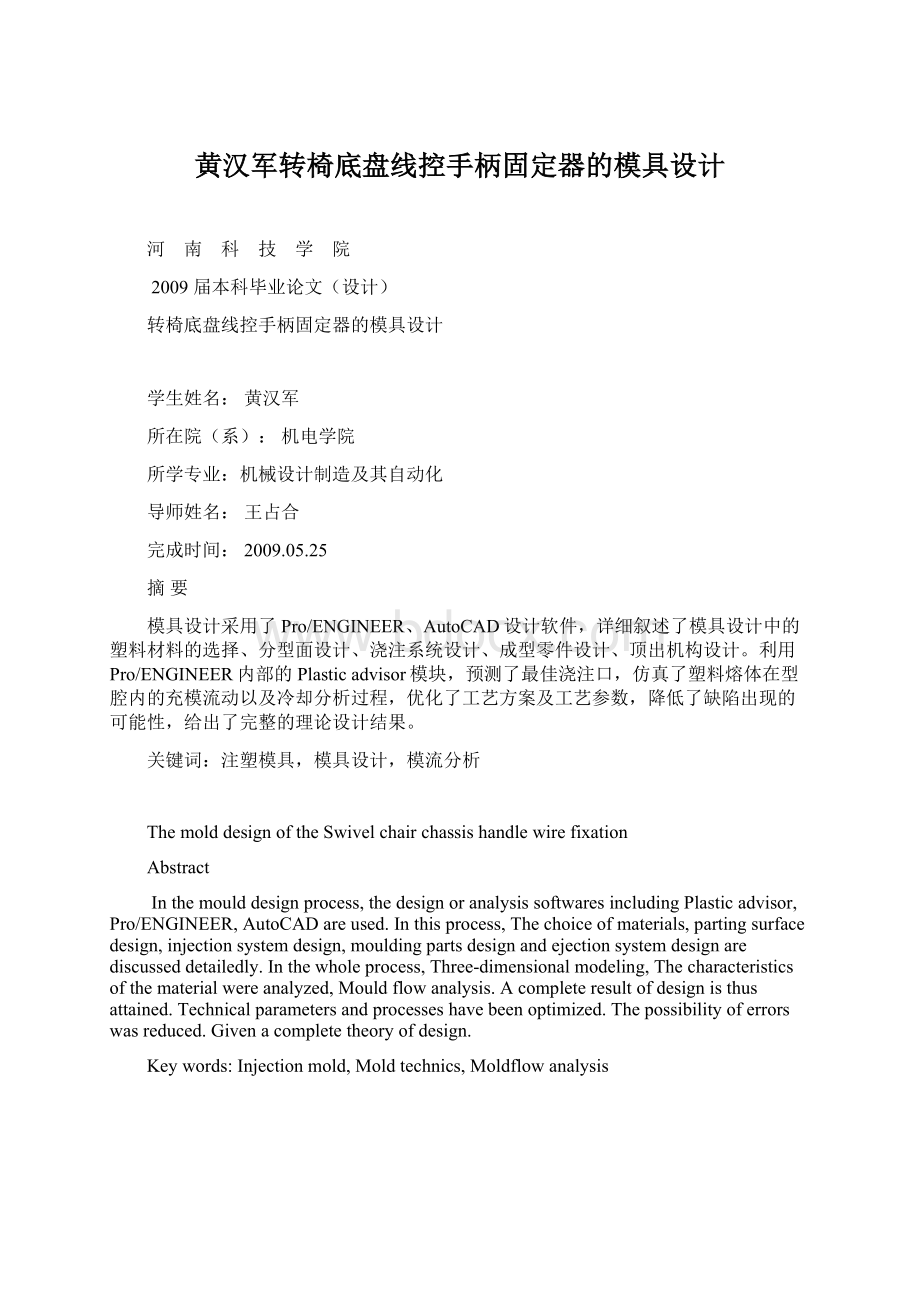
黄汉军转椅底盘线控手柄固定器的模具设计
河 南 科 技 学 院
2009届本科毕业论文(设计)
转椅底盘线控手柄固定器的模具设计
学生姓名:
黄汉军
所在院(系):
机电学院
所学专业:
机械设计制造及其自动化
导师姓名:
王占合
完成时间:
2009.05.25
摘要
模具设计采用了Pro/ENGINEER、AutoCAD设计软件,详细叙述了模具设计中的塑料材料的选择、分型面设计、浇注系统设计、成型零件设计、顶出机构设计。
利用Pro/ENGINEER内部的Plasticadvisor模块,预测了最佳浇注口,仿真了塑料熔体在型腔内的充模流动以及冷却分析过程,优化了工艺方案及工艺参数,降低了缺陷出现的可能性,给出了完整的理论设计结果。
关键词:
注塑模具,模具设计,模流分析
ThemolddesignoftheSwivelchairchassishandlewirefixation
Abstract
Inthemoulddesignprocess,thedesignoranalysissoftwaresincludingPlasticadvisor,Pro/ENGINEER,AutoCADareused.Inthisprocess,Thechoiceofmaterials,partingsurfacedesign,injectionsystemdesign,mouldingpartsdesignandejectionsystemdesignarediscusseddetailedly.Inthewholeprocess,Three-dimensionalmodeling,Thecharacteristicsofthematerialwereanalyzed,Mouldflowanalysis.Acompleteresultofdesignisthusattained.Technicalparametersandprocesseshavebeenoptimized.Thepossibilityoferrorswasreduced.Givenacompletetheoryofdesign.
Keywords:
Injectionmold,Moldtechnics,Moldflowanalysis
3.手控器的注塑成型工艺性分析……...…………………………………………………………2
附录:
……………………………………………………………………………………………..29
1绪论
转椅底盘线控手柄固定器(以下简称手控器)是中高档办公用椅的重要部件,起着方便控制椅子底盘倾斜角度的作用。
该固定器采用注塑工艺生产,因此设计一套生产效率高,产品质量好,生产成本低的模具十分必要。
2手控器的结构特点与材料选用
2.1手控器的结构特点
手控器的外形图见图1,零件图见图2。
图1手控器的三维图
图2手控器的二维图
2.2材料选择:
该塑件是日用品,承受外力的几率不大,如冲击载荷、振动、摩擦等情况比较少;塑件的工作温度是室温。
这使得在材料选择时对热变形温度,脆化温度,分解温度的要求降低;作为一种日用品,生产批量应该是大批大量生产,这样,就必须考虑生产成本和模具寿命,在材料的选择时要综合各种因素;此外,塑料都会老化,作为一种光学用品,还要考虑到材料的光氧化等问题。
经分析,本塑件基本不怎么受较大的冲击力,外观方面要求也不是特别高,本塑件材料采用PA66。
材料简介:
PA66又称尼龙66;聚己二酸己二胺;nylon66,缩写NY66。
化学式:
[-NH(CH2)6-NHCO(CH2)4CO]n-
性状:
半透明或不透明乳白色结晶形聚合物,具有可塑性。
密度1.15g/cm3。
熔点252℃。
脆化温度-30℃。
热分解温度大于350℃。
连续耐热80-120℃,平衡吸水率2.5%。
能耐酸、碱、大多数无机盐水溶液、卤代烷、烃类、酯类、酮类等腐蚀,但易溶于苯酚、甲酸等极性溶剂。
具有优良的耐磨性、自润滑性,机械强度较高。
但吸水性较大,因而尺寸稳定性较差。
外观为白包或带黄色颗粒状
密度(g/cm3)1.10-1.14
拉伸强度(MPa)60.0-80.0
络氏硬度118
冲击强度(kJ/m2)60-100
静弯曲强度(MPa)100-120
马丁耐热(℃)50-60
弯曲弹性模星(MPa)2000~3000
体积电阻率(Ωcm)1.83×1015
介电常数1.63
PA66在聚酰胺材料中有较高的熔点。
它是一种半晶体-晶体材料。
PA66在较高温度也能保持较强的强度和刚度。
PA66在成型后仍然具有吸湿性,其程度主要取决于材料的组成、壁厚以及环境条件。
在产品设计时,一定要考虑吸湿性对几何稳定性的影响。
尼龙66提供了各种特性的最佳平衡性,并且是所有尼龙中最强状的。
3手控器的注塑成型工艺性分析
3.1拔模斜度分析
塑件在成型过程中,塑料从熔融状态转变为固体状态,将会产生一定量的尺寸收缩,从而使塑件紧紧的包在模具型芯和型腔中凸起的部分上。
为此必须考虑内外壁有足够的拔模斜度,pro/e分析的拔模检测,拔模角度为1.5°。
见图3所示:
图3拔模斜度分析图
3.2型腔数量及排布:
考虑这个塑件体积方面不是很大,且表面质量方面要求不高,为了提高生产效率,所以型腔数量选择一模两腔,初步排版见图4,
图4型腔排布图
采用对面对称的排布方式,因为左右有侧抽,选择对称排布,可以让两个滑块自由向外移动。
3.3分型面的设计
本塑件主要分模包括上下分型和两个侧抽,主分型面则设计在塑件对称的中心面上,左右侧抽分型面则是设计在两个侧孔的位置,大滑块的侧抽分型面就选择在塑件底部U形的面和几个螺丝孔部分,图5、图6可以表示得很清楚:
图5总分型图
图6各个分型面
3.4浇注系统设计
3.4.1浇注系统的组成
浇注系统是指模具中从注射机喷嘴开始到型腔为止的塑料流动通道,其由主流道、分流道、浇口及冷料穴组成。
3.4.2浇注系统设计原则
浇注系统的设计是注塑模具设计的一个重要环节,占有非常重要的地位,它的设计合理与否对注塑的成型周期和制件质量(几何特征、物理性能、尺寸精度等)都有直接影响。
因此,浇注系统的作用是保证塑料熔体顺利、平稳地填充到型腔当中,在这个过程中,把压力充分地传递到各个部位,以便于获得组织紧密、外形清晰的塑料制件。
由于浇注系统在模具设计中的重要地位,所以设计时应遵循如下原则:
(1)型腔布置和浇口开设的部位应对称,防止溢料现象的产生;
(2)型腔和浇口的排列要合理,尽量地缩小模具的外形尺寸;
(3)流程应尽可能短,断面尺寸适当(太小则压力及热量损失大,太大则塑料耗费大),且应尽量减小弯折,降低压力损失,缩短填充时间;
(4)对多型腔应尽可能使塑料熔体在同一时间内进入各个型腔的深处及角落,即分流道尽可能采用平衡式布置;
(5)在满足充满型腔的前提下,浇注系统的容积应尽量小,以减少塑料的耗量;
(6)浇口位置要适当,尽量避免冲击嵌件和细小的型芯,防止型芯变形,浇口的残痕不应影响塑件的外观;
(7)浇注系统的排气要良好,能够顺利地引导熔融塑料填充到型腔的各个深度,不产成涡流和紊流,并能使模腔内的气体顺利排除。
3.4.3主流道设计
主流道是指从注射机喷嘴与模具接触的部位起,到分流道为止的这一段。
主流道结构如图7,图8所示
图7主流道接口三维图
图8主流道接口二维图
熔融塑料首先经过主流道,所以它的大小直接影响塑料的流速及填充时间。
主流道的断面形状常为圆形。
主流道截面面积过小,塑料在流动过程中冷却面积相对增加,热量损失大,粘度增加,流动性下降,成型压力损失大,造成成型困难;如主流道截面面积过大,会使流道容积加大,塑料耗量增多,而且会使塑料流动过程中压力减弱,冷却时间延长,容易产生紊流或涡流,使塑件产生气孔,影响塑件的质量。
一般对于流动性好,塑件较小,主流道要设计得小些;流动性差,塑件较大,主流道要设计得大些。
主流道的基本尺寸通常取决于两个双方面:
第一个方面,所使用的塑料种类,所成型的制品质量和壁厚大小。
其表如3-1:
表3-1制品质量和壁厚大小参考表
制品质量/g
D1/mm
R/mm
~20
3
0.5
20~40
4
1
40~150
5
1
150~300
6
2
300~500
8
2
500~1500
10
2
第二个方面,注塑机喷嘴的几何参数与主浇道尺寸的关系如图9所示。
热塑性塑料的主流道衬套与注塑机喷嘴的尺寸:
主流道始端直径φB=φA+(0.5~1)mm,球面凹坑半径
mm,半锥角a为
,尽可能缩短长度L(小于60mm为佳)。
图9浇口套与注塑机喷嘴关系
本套模具主流道设计要点是:
1.为便于凝料从主流道中拉出,主流道设计成圆锥形,其锥角
=2°,内壁粗糙度为Ra=0.63
,整个主流道都在衬套中,并未采取分段组合形式。
2.主流道大端处是根据注塑机的喷嘴头来设计的,呈圆角,其半径R=11mm,以减小料流在转向时过渡的阻力。
3.为使熔融塑料从喷嘴完全进入主流道而不溢出,应使主流道和注塑机的喷嘴紧密接触,主流道对接处设计成半球形凹坑,其半径R=X+(1~2)mm,X=10mm,取R=11mm。
其主浇道小端直径d2=d1+(0.5~1)mm,取d2=6mm。
流道应保持光滑的表面,避免留有影响塑料流动和脱模的尖角毛刺等。
3.4.4分流道设计
分流道是指主流道与浇口之间的这一段,它是熔融塑料由主流道流入型腔的过渡段,也是浇注系统中通过断面积变化和塑料转向的过渡段,能使塑料得到平稳的转换。
从压力损失考虑,由于在同等断面积时的圆形周边比正方形的短,因此料流阻力小,压力损失也小。
电器盒塑料件的体积较大,特别是长度较长,所以压力是否足够对充模成功与否具有较大的影响,所以这里应该采用U形截面的分流道。
U形分流道断面的深度一般H=2r(r为圆的半径),斜角a=5°-10°分流道的表面不要求很光,表面粗糙度一般达到Ra3.2~1.6即可,因为分流道的表面不光滑,就能使熔料的冷却皮层固定,有利于保温。
分流道的分布如图10所示
图10分流道的分布图
3.4.5浇口设计
浇口又称进料口或内流道。
它是分流道与塑件之间的狭窄部分,也是浇注系统中最短小的部分。
它能使分流道输送来的熔融塑料的流速产生加速度,形成理想的流态,顺序、迅速地充满型腔,同时还起到封闭型腔防止熔料倒流的作用并在成型后便于使浇口与塑件分离。
本设计采用普通侧浇口,又称边缘浇口,一般开设在分型面上,,它能方便调整充模时的剪切速率和浇口封闭时间,因而在国外称之为标准浇口,应用非常广泛。
测浇口一般取宽1.5-5mm,厚0.5-2mm,长0.7-2mm,侧浇口可以根据塑件的形状特点灵活的选择浇口的位置,来改善填充条件,不像其他浇注系统一样有很大的限制,如框形或者环形塑件,可以从外侧进料,而当内部有足够空间位置时也可以从内侧进料,这种可以使模具更紧凑,流程缩短,一般适用于一模多腔,能大大强高生产效率,减少浇注系统耗量而且除去浇口方便,本塑件量大而且对质量要求不是非常高,很符合侧浇口的使用环境,如图11:
图11浇口设计图
3.4.6冷料穴设计
冷料穴是用来储藏注射间隔期间产生的冷料头的,防止冷料进入型腔而影响塑件质量,并使熔料能顺利充满型腔。
冷料穴又叫冷料井。
卧式或立式注塑机上注塑的冷料穴一般都设置在主流道的末端,即主流道正对面的动模上,直径稍大于主流道大端直径,以利冷料流入,当分流道较长时,可将分流道的尽头沿前进方向稍延长的部分作为冷料穴。
本模具冷料穴分流道不怎么长,所以把冷料穴设置在主流道末端,如图12所示:
图12冷料穴设计
4模具结构设计
模具主要有分型块,下面为动模板,下模板主要有大滑块部分,有个T型槽部分。
4.1动模板的设计如图13、图14
图13动模板设计三维图
图14动模板设计二维图
4.2定模板的设计如图15、图16
图15定模板设计三维图
图16定模板设计二维图
4.3大滑块的设计
大滑块,因为是一模两腔的设计,本来两个滑块合并为一个,因为滑块比较大,所以采用了两根斜导柱的结构,这样受力更均匀,容易脱模,如图17、图18
图17大滑块三维图
图18大滑块二维图
4.4左右滑块的设计
左右滑块道理一样,结构和大滑块相似,如图19、图20所示:
图19左右滑块三维图
图20左右滑块二维图
两个滑块都用了斜导柱的形式,斜导柱抽芯是最常用的一种方式,他具有结构简单,安全可靠,制造方便等特点,具体动作原理下文在做详细介绍
5模具机构设计
主要有标准模架设计、滑块机构的设计、导向与定位机构设计、顶出系统的设计。
5.1标准模架的选择
应用proe里面一个插件EMX,设计出本套模架的基本框图可见如图21:
图21模架的基本框图
图中可以看见每块模板的高度,而且宽度是250长度是400,这两个数据室根据型腔的长度宽度设计的,图22是模架总体三维图
图22模架总体三维图
5.2滑块机构设计
本设计过程中滑块都采用斜导柱的形式进行脱模,图23为合模状态时
图23合模状态图
合模时滑块的斜面和定模板的斜面接触,起到定位的作用,滑块嵌在动模板的T型槽里,开模时滑块就受到向下的力,因为滑块和斜导柱是斜面接触,力作用在垂直于斜面上,进而可以分解为垂直和水平方向的力,水平方向的力就可以驱使滑块向左右移动,受力图如图24所示
图24受力图
F拉是动模板给滑块的力,F斜则是因为F拉作用在斜面上而形成的力,因为力的作用是相互的,因而会产生一个反作用力,也就是图中所示的F反,利用理论力学知识可以很简单得把力分解成水平和垂直的力,即Fx和Fy,力Fx可以驱使滑块向右移动,继而打到脱模的效果,下面为开模后的示意图如图25
图25开模后的示意图
5.3导向与定位机构
注射模的导向机构主要有导柱导向和锥面定位两种类型。
导柱导向机构用于动、定模之间的开合模导向和脱模机构的运动导向。
锥面定位机构用于动、定模之间的精密对中定位。
导柱:
国家标准规定了两种结构形式,分为带头导柱和有肩导柱,大型而长的导柱应开设油槽,内存润滑剂,以减小导柱导向的摩擦。
若导柱需要支撑模板的重量,特别对于大型、精密的模具,导柱的直径需要进行强度校核(如图26)。
导套:
导套分为直导套和带头导套,直导套装入模板后,应有防止被拔出的结构,带头导柱轴向固定容易(如图27)。
设计导柱和导套需要注意的事项有:
(1)合理布置导柱的位置,导柱中心至模具外缘至少应有一个导柱直径的厚度;导柱不应设在矩形模具四角的危险断面上。
通常设在长边离中心线的1/3处最为安全。
导柱布置方式常采用等径不对称布置,或不等直径对称布置。
(2)导柱工作部分长度应比型芯端面高出6~8mm,以确保其导向与引导作用。
(3)导柱工作部分的配合精度采用H7/f7,低精度时可采取更低的配合要求;导柱固定部分配合精度采用H7/k6;导套外径的配合精度采取H7/k6。
配合长度通常取配合直径的1.5~2倍,其余部分可以扩孔,以减小摩擦,降低加工难度。
(4)导柱可以设置在动模或定模,设在动模一边可以保护型芯不受损坏,设在定模一边有利于塑件脱模。
图26导柱三维图27导套三维
5.4顶出系统设计
注射成型每一循环中,塑件必须准确无误地从模具的凹模或型芯上脱出,完成脱出塑件的装置称为脱模机构,也称顶出机构。
脱模机构的设计一般遵循以下原则:
(1)塑件滞留于动模边,以便借助于开模力驱动脱模装置,完成脱模动作。
(2)由于塑件收缩时包紧型芯,因此推出力作用点尽量靠近型芯,同时推出力应施于塑件刚性和强度最大的部位。
(3)结构合理可靠,便于制造和维护。
本设计使用简单的推杆和推管脱模机构,因为该塑件的分型面简单,结构也不复杂,采用推简单的脱模机构可以简化模具结构,给制造和维护带来方便。
在对脱模机构做说明之前,需要对脱模力做个简单的计算。
,图28、图29为本设计的顶杆及顶杆的位置
图28每个产品用四根顶杆顶出
图29顶杆顶出模型图
顶杆的顶出位置放在了产品的四根加强筋上面,不会影响外观,而且顶出的力均匀,有利于脱模
6其它辅助系统的设计
6.1温度调节系统设计
在注塑成型过程中,模具的温度直接影响到塑件成型的质量和生产效率。
由于各种塑料的性能和成型工艺要求不同,模具的温度要求也不同。
普通的模具通入常温的水进行冷却,通过调节水的流量就可以调节模具的温度,为了缩短成型周期,还可以把常温的水降低温度后再通入模内,可以提高成型效率。
对于高熔点,流动性差的塑料,流动距离长的制件,为了防止填充不足,有时也在水管中通入温水把模具加热。
PS推荐的成型温度为170~280℃,模具温度为20~70℃。
6.1.1温度调节对塑件质量的影响
(1)采用较低的模温可以减小塑料制件的成型收缩率;
(2)模温均匀,冷却时间短,注射速度快可以减少塑件的变形
(3)对塑件表面粗糙度影响最大的除型腔表面加工质量外就是模具温度,提高模温能大大改善塑件的表面状态;
温度对塑件质量的影响有相互矛盾的地方,设计时要根据材料特性和使用要求偏重于主要要求。
6.1.2对温度调节系统的要求
(1)根据塑料的品种确定是对模具采用加热方式还是冷却方式;
(2)希望模温均一,塑件各部同时冷却,以提高生产率和提高塑件质量;
(3)采用低的模温,快速,大流量通水冷却效果一般比较好;
(4)温度调节系统应尽可能做到结构简单,加工容易,成本低廉;
从成型温度和使用要求看,需要对该模具进行冷却,以提高生产率。
6.2.设计原则
(1)尽量保证塑件收缩均匀,维持模具的热平衡;
(2)冷却水孔的数量越多,孔径越大,则对塑件的冷却效果越好;
(3)尽可能使冷却水孔至型腔表面的距离相等,与制件的壁厚距离相等,经验表明,冷却水管中心距B大约为2.5~3.5D,冷却水管壁距模具边界和制件壁的距离为0.8~1.5B。
最小不要小于10。
(4)浇口处加强冷却,冷却水从浇口处进入最佳;
(5)应降低进水和出水的温差,进出水温差一般不超过5℃
(6)冷却水的开设方向以不影响操作为好,对于矩形模具,通常沿宽度方向开设水孔。
(7)合理确定冷却水道的形式,确定冷却水管接头位置,避免与模具的其他机构发生干涉。
如图30
图30冷却系统设计图
7塑件模流分析
利用Pro/ENGINEER的外挂软件塑料顾问(PlasticAdvisor),还可以对已设计完成的模具的流动及充填情况进行分析研究,以便在模具投入制造之前就发现存在的设计问题,并有目的地进行改进设计,减少设计失误造成的不必要损失。
7.1注塑时间分析如图31
图31时间分析图
7.2注塑压力分析如图32
图32注塑压力分析图
7.3注塑表面流动如图33
图33注塑表面流动图
7.4注塑时表面温度如图34
图34注塑时表面温度图
7.5冷却质量如图35
图35冷却质量图
7.6表面缩痕估计如图36
图36表面缩痕估计图
7.7分析的总体结果
运用CAE技术,我们对本产品充模情况进行分析。
分析的内容主要有充模时间,模具行腔内的压力分布,模具行腔内的温度分布情况,可能出现的熔接痕和气泡等。
根据分析结果我们可以更好的对模具结构进行修模和优化。
以下为注塑条件的部分参数
MoldTemperature:
60.00deg.C
MeltTemperature:
280.00deg.C
充填阶段结果摘要:
最大注射压力(10:
500)=170MPa
充填阶段结束的结果摘要:
充填结束时间=1s
机械打开时间=5s
总重量(制品+流道)=51.45g
最大锁模力-在充填期间=16.6120tonne
8模具总装图
8.13D爆炸图如图37、图38
图37爆炸图
(一)
图38爆炸图
(二)
8.2装配明细表如图39
图39装配明细图
(1)浇注口衬套
(2)定模底座(3)衬套(4)水线喷嘴(5)定模板(6)斜导柱(7)顶杆(8)左右滑块(9)大滑块(10)动模板(11)导柱(12)支撑板(13)复位杆(14)弹簧(15)顶板(16)动模底座(17)顶杆固定板(18)垫板
9结束语
1.在模具设计初始阶段采用模流分析软件对整个模具设计进行优化。
可以设计浇注系统并进行最佳浇注口的分析、充模温度、表面缩痕估计等,为设计做出提前预判和可靠的参照。
2.利用Pro/ENGINEER软件完成了产品的外形设计,分型面设计、浇注系统设计、成型零件设计、顶出机构设计。
首先在Pro/E模具模块里作出分型面,利用分型面得出动、定模,初步出三维造型,最后导入工程图中并转化到AutoCAD中进行修改并完善,继而出二维图纸,从而得出完整的理论设计结果。
分析时采用Pro/ENGINEER内部的Plasticadvisor模块预测了最佳浇注口,仿真了塑料熔体在型腔内的充模流动以及冷却分析过程,预测了缺陷产生的临界条件,优化了工艺方案及工艺参数,降低了缺陷出现的可能性。
采用这些软件进行设计分析,优化了设计的参数和缩短了设计时间,提高了生产效率。
致谢:
设计过程中遇到许多的问题,在众多师友的帮助下予以解决。
首先要感谢王老师和公司同事对我的指导和督促,王老师给我指出了正确的设计方向,使我加深了对知识的理解,同时也避免了在设计过程中少走弯路,王老师的督促使我一直把毕业设计放在心理,保证按质按量的完成。
要感谢同事,是大家营造了良好的学习环境,在做设计的过程中互帮互助,使我的CAD和PRO/E操作水平比以前有了很大提高,同时较全面的掌握了Word的编辑功能
大学生活至此划上了圆满的句号,在河南科技学院这块土地上有众多莘莘学子辛勤的耕耘,在这块土地上我健康快乐的成长,我永远不会忘记可亲的同学,我永远记得这片土地。
参考文献
[1]中国塑料机械信息网WWW.SLJX.CN首页,行业咨询,2006-4-19.
[2]詹友刚编著.PRO/ENGINEER中文野火版3.0基础教程[M].清华大学出版社.
[3]DevelopingTrendforPlasticandPlasticMold[M].RubberPlasticsMachineryTimes.2007
[4]张祥杰等编著.PRO/ENGINEER模具设计WILDFIRE[M].中国铁道出版社,2004.
[5]《塑料模具技术手册》编委会编著.塑料模具技术手册[M].机械工业出版社,2001.
[6]伍先明等编著.塑料模具设计指导[M].国防工业出版社,2006.
[7]陈万林塑料模具设计与制作教程北京:
希望电子出版社
[8]葛正浩注塑模具设计北京:
化学工业出版社,2007.669~70
[9]王颖.CAD技术在模具行业的应用及其发展方向[J].天津理