电炉炼钢方坯连铸技术.docx
《电炉炼钢方坯连铸技术.docx》由会员分享,可在线阅读,更多相关《电炉炼钢方坯连铸技术.docx(99页珍藏版)》请在冰豆网上搜索。
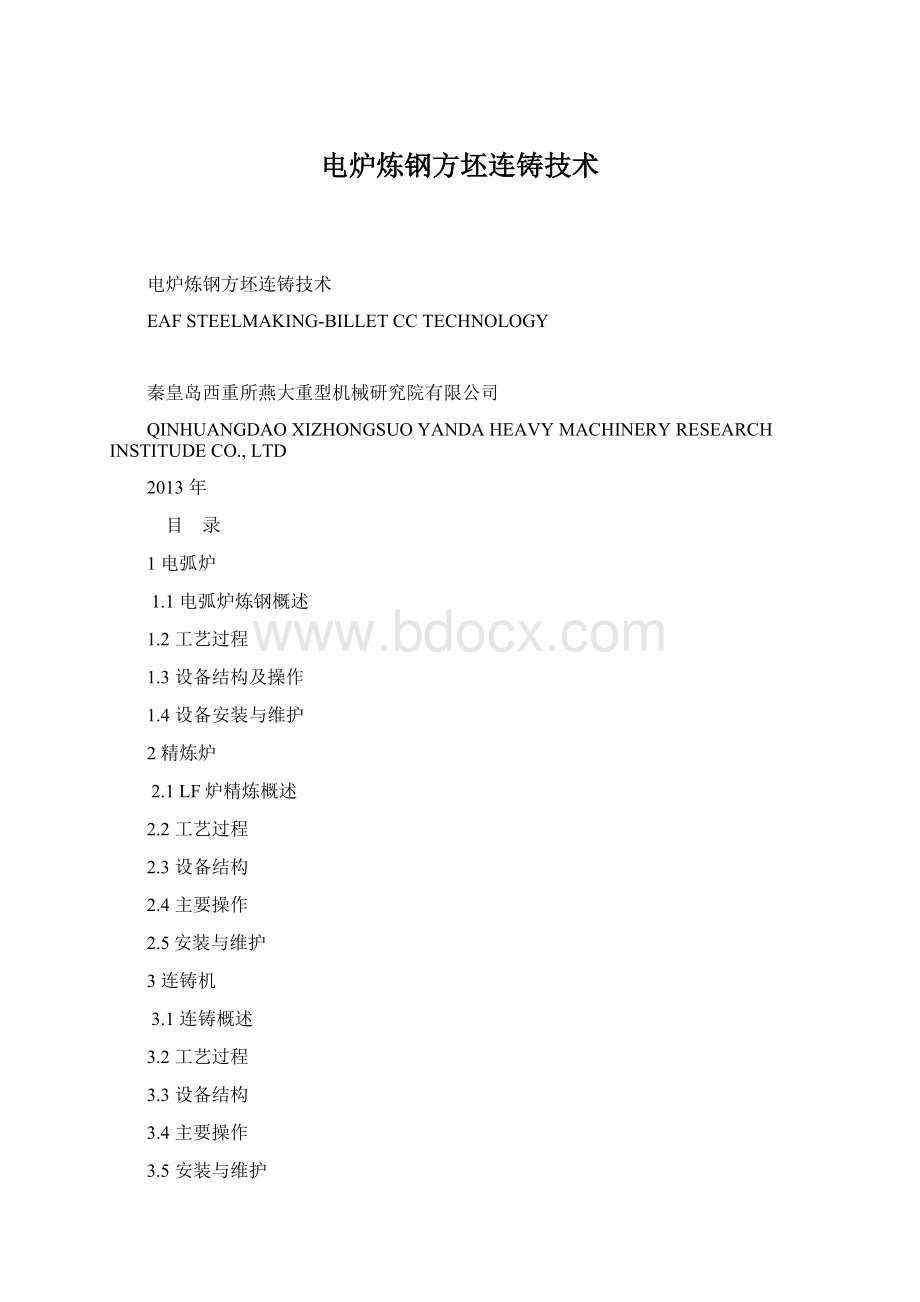
电炉炼钢方坯连铸技术
电炉炼钢方坯连铸技术
EAFSTEELMAKING-BILLETCCTECHNOLOGY
秦皇岛西重所燕大重型机械研究院有限公司
QINHUANGDAOXIZHONGSUOYANDAHEAVYMACHINERYRESEARCHINSTITUDECO.,LTD
2013年
目 录
1电弧炉
1.1电弧炉炼钢概述
1.2工艺过程
1.3设备结构及操作
1.4设备安装与维护
2精炼炉
2.1LF炉精炼概述
2.2工艺过程
2.3设备结构
2.4主要操作
2.5安装与维护
3连铸机
3.1连铸概述
3.2工艺过程
3.3设备结构
3.4主要操作
3.5安装与维护
4烟尘治理
5配套公辅设施
前言
目 录
1.电弧炉3
1.1电弧炉炼钢概述3
1.2工艺过程4
1.3设备设计原理及结构9
1.4LF炉精炼装置的工艺和设备15
1.5连铸工艺30
2.配套公辅设施46
2.1散状原料处理设施46
2.2检化验设施47
2.3热力设施48
2.4燃气设施52
2.5给排水设施57
2.6除尘、通风及空调设施61
2.7供配电设施64
2.8自动化仪表69
2.9电气传动72
2.10电信设施73
2.11土建工程76
2.12总图运输80
3.环境保护与综合利用82
3.1设计依据82
3.2环境概况82
3.3工程概况82
3.4主要污染源、污染物及其控制方案82
3.5环境绿化84
3.6环境管理和环境监测84
3.7环境影响简略分析84
4.劳动安全卫生85
4.1设计依据85
4.2工程概况85
4.3生产中主要职业危险和职业危害因素分析85
4.4劳动安全卫生防范措施86
4.5辅助用室设置89
4.6劳动安全卫生管理及检测机构89
4.7劳动安全卫生投资89
4.8劳动安全卫生设计的预期效果90
5.全厂主主要技术经济指标90
1.电弧炉
1.1电弧炉炼钢概述
电弧炉(简称EAF)炼钢是以电能作为热源的炼钢方法,它是靠电极和炉料间放电产生的电弧,使电能在弧光中转变为热能,并借助电弧辐射和电弧的直接作用加热并熔化金属炉料和炉渣,冶炼出各种成分合格的钢和合金的一种炼钢方法。
图1.1是电弧炉炼钢过程示意图。
随着电炉技术的不断发展,目前电炉冶炼的一个周期主要包括:
补炉与装料、熔化、氧化精炼,去渣,出钢,炉体回倾。
图1.1电弧炉炼钢过程示意图
电弧炉炼钢的特点为:
(1)电能为热源,避免燃烧燃料对钢液污染,热效率高,可达65%以上;
(2)冶炼熔池温度高且容易控制,满足冶炼不同钢种的要求;
(3)电热转换,输入熔池的功率容易调节,因而容易实现熔池加热制度自动化,操
作方便;
(4)电弧炉炼钢可以消纳废钢,是一种铁资源回收再利用过程,也是一种处理污染
的环保技术。
相当于是钢铁工业和社会废钢的回收工具。
(5)炼钢过程的烟气污染和噪声污染容易控制;
(6)设备简单,炼钢流程短,占地少,投资省、建厂快,生产灵活。
1.2工艺过程
1.2.1电炉原材料供应
电弧炉炼钢的原料主要包括废钢,废钢替代品如直接还原铁(DRI)、热压铁块(HBI)、粗铁(Pigiron)、铁水(Moltenpigiron),造渣材料、氧化剂等。
废钢来源一般有三个方面,即钢铁企业在生产过程中的自产废钢、工矿企业在生产过程中的加工废钢、社会生产、生活、国防等废弃钢铁材料的拆旧废钢,如报废汽车、舰船、钢结构桥梁与建筑钢等。
由于连铸技术的发展,连铸比不断提高,切头、切尾越来越少,每吨钢自产废钢大幅减少,钢厂内部回收废钢相应减少。
而来自于社会的废钢原料的最大问题是金属残留元素,主要是残留的Ni,Cr,Mo等合金元素和Cu,Sn,Bi,Sd,Pb等有害元素。
因此,DRI、HBI及粗铁等纯净金属原料成为废钢的主要替代品。
在DRI产量丰富的地区,甚至采用DRI作为全部炼钢铁源。
需注意的是,DRI等纯净铁源有利于高质量、低杂质钢种的生产,同时连续加料方式有利于降低能耗,但其较高的脉石含量会大大增加渣量并导致电耗增大,操作方式与废钢作为主要原料来炼钢有显著不同,将在后续章节具体介绍。
电炉的辅助材料主要由石灰、白云石及碳粉等组成。
碳粉主要用来造泡沫渣,其流量60~450kg/min。
对石灰、白云石及碳粉的化学成分及物理性能要求见表1.2-1、1.2-2、1.2-3。
表1.2-1石灰的化学成分及物理性能
成分
CaO
SiO2
P
S
MgO
粒度(mm)
粉料量
H2O
(%)
≥85
≤0.5
≤0.02
≤0.06
≤3
20~150
≤5
≤0.5
过烧和欠烧率:
≤10%
活性度:
≥350ml/4N-HCl
表1.2-2白云石的化学成分及物理性能
成分
CaO
MgO
粒度(mm)
H2O
(%)
50~60
>32%
3~30
≤0.3
欠烧率:
≤8%
表1.2-3碳粉的化学成分及物理性能
成分
C
S
灰分
H2O
粒度(mm)
(%)
≥80
≤0.1
≤8
≤0.3
≤3mm、0~0.2mm<3%
1.2.2补炉与装料
1.2.2.1补炉
炉衬寿命的长短是多炼钢、炼好钢、节约原材料、降低成本的关键问题。
炉衬是指炉壁、炉底和炉盖。
寿命最低的是炉壁,它的工作条件最差,距电弧近,温度高,又受炉渣的严重浸蚀。
炉衬严重损坏或补炉镁砂未烧结而在往渣中上浮时,渣中MgO颗粒大量增加,渣的流动性变坏,延缓渣钢间的化学反应,钢中夹杂物增加,钢质严重降低。
炉衬一般由碱性材料组成,渣中的碱性氧化物(如CaO、MgO、MnO),对炉衬浸蚀作用小,渣中的酸性氧化物如SiO2、TiO2、ZrO2、P2O5等,对炉衬浸蚀作用大。
炉衬寿命主要与渣中SiO2含量有直接关系,一般在10~20%之间。
从补炉材料来分,有干补和湿补,干补时用镁砂MgO含量<78%或白云石(焙烧过的)和焦油(碳氢化合物)作粘结剂;湿补用的粘结剂为卤水(MgCl2·xH2O)或水玻璃(Na2SiO4·yH2O),常用于损坏严重或坡度大不易补的地方。
沥青和镁砂的配比约为1:
10,卤水或水以玻璃或镁砂的用量以捏成团不松散为宜。
补炉时间因浸蚀的情况和炉子容量而定,一般为3~5分钟。
1.2.2.2装料
装料质量对电弧炉炼钢熔化时间、合金元素烧损和炉衬寿命都有很大影响。
废钢装料应做到快和密实,以缩短冶炼时间和减少热损失。
为了保证炉料熔化的顺利进行,必须装得密实。
炉料分为大料、中料、小料、轻薄料,装料时按一定比例以便一次加入,以减少塌方等。
图1.2-1为电炉炉顶装料图。
图1.2-1电炉炉顶装料图
直接还原铁(DRI/HBI)可通过以下四种不同的方式加入到EAF中:
●通过废钢料篮
●冷DRI通过炉顶开孔连续加料
●HBI可通过预热装置加入(如竖式炉)
●热DRI连续加料
当DRI在金属原料中的比例超过25%,就需要通过炉顶开孔的方式连续加[]。
JeremyA.T.Jones.ConsiderationsforthefeedinganduseofalternativeironmaterialsintheEAF.
图1.2-2为DRI由竖炉热送至EAF的示意图。
由竖炉产生的DRI,一部分热送至EAF,另一部分可经冷却后存储起来,再送至EAF。
图1.2-2DRI热送至EAF示意图
1.2.3炉料的熔化和钢液的氧化精炼
电弧炉炼钢首先需要快速熔化炉料,以便在氧化期和精炼期控制钢液的成份,去除有害的杂质磷、氢、氧和氮,并且去除钢中的非金属夹杂物。
同时尽可能减少钢液吸收气体。
炉料熔化在整个电弧炉炼钢生产工艺中是很重要的时期。
熔化时间占总冶炼时间的50%左右,电能消耗占总耗电的2/3左右,所以加速炉料熔化是缩短熔化时间、提高产量、降低电耗和成本的关键。
1.2.3.1炉料熔化操作
快速熔化和升温是当今电弧炉炼钢最重要的功能。
电能是电弧炉熔化和升温的基本能源。
熔化操作主要是合理供电,适时吹氧和尽快造渣,以实现快速熔化炉料的目的。
合理供电:
开始时供电电流小些,防止电弧向炉膛辐射大量的热,使炉顶局部损坏,当供电5~10分钟以后,电弧已埋入炉料,这时用大最大功率供电。
适时吹氧:
吹氧是利用氧化反应的热加速熔化炉料,吹氧对降低电耗、缩短冶炼时间有显著的效果。
但吹氧过早,氧气和冷炉料起作用小,浪费了氧气。
一般吹固体料时温度在950℃以上时为宜,这时氧和钢铁料的作用快,容易熔化。
一般全固体炉料时,在熔化50%左右时吹氧为宜。
尽快造渣:
覆盖在钢液面上的炉渣能稳定电弧的燃烧,减少钢液散失热量,减缓吸收氢和氮,去除钢液中的磷和硫,吸收上浮到钢液面上的夹杂,减少铁及元素的蒸发等。
连续加料的直接还原铁炼钢中采用造泡沫渣操作。
连续不断的激烈碳氧反应和较大的渣量生成厚泡沫渣,有效地屏蔽和吸收了电弧辐射能,并传递给熔池,提高了加热效率,缩短了冶炼时间,减少了辐射到炉壁、炉盖的热损失。
1.2.3.2钢液的氧化精炼操作
主要目的为:
●去除钢液中的磷,达到规定的限度较低值
●去除钢液中的气体(氢气和氮气):
在氧化结束时把溶解在钢液中的氢降到0.0001~0.0002%范围,氮降低到0.004~0.006%范围
●去除钢液中氧化物夹杂:
利用氧化精炼过程中的钢液沸腾,去除大部分夹杂物,在钢液的氧化精炼可以去除75~90%的夹杂物
●升高钢液温度:
冶炼过程需要较高的温度。
在氧化精炼过程,利用熔池沸腾搅拌作用,有利于钢液加热升温,把钢液温度升高到高于出钢温度10~20℃
●调整钢液的碳含量:
氧化脱碳使钢液沸腾,在氧化精炼结束出钢前,钢液含碳量需要考虑还原精炼加入铁合金,会增加钢水的碳含量。
相反,在钢液碳含量低时可用喷粉增碳。
1.2.4出钢
当钢液满足下述生产条件时即可出钢。
(1)符合该钢种的出钢温度。
(2)钢液[C]、[P]成分控制合格。
出钢温度应根据不同钢种,充分考虑以上各因素来确定。
出钢温度过低,钢水流动性差,不利于出钢过程的钢、渣反应和化渣,同时增加后续精炼的钢液升温任务;出钢温度过高,使钢清洁度变坏,钢中氧、气体含量增高,造成合金消耗量增大。
总之,出钢温度应在能顺利完成后续精炼任务的前提下尽量控制低些。
1.3设备设计原理及结构
电弧炉型式多样。
近年出现的已投入工业化生产的各种新型电炉主要有:
超高功率交流电弧炉;超高功率直流电弧炉;双炉壳电弧炉;带竖井的电弧炉(简称竖炉);Consteel电炉;Danarc电炉
新出现的多种型式的电炉各有其独到的特点,具体可归纳为以下几点:
1)最大限度地节能降耗,采取的措施如下:
●充分利用高温烟气进行有效地废钢预热;
●采用喷吹燃料与氧气助熔及使CO二次燃烧等技术手段,利用化学能代替部分电能。
2)缩短冶炼周期,提高电炉生产率及其生产能力,采用的措施有:
●选择超高功率电炉──炉外精炼──连铸三位一体的短流程工艺路线,由超高功率电炉承担初炼熔化任务,大大缩短冶炼周期,提高了电炉生产率,并实现连铸机多炉连浇。
3)增加对多种“铁源”炉料的适应性,采用的措施有:
●配入高炉铁水、DRI、HBI、熔融还原铁、碳化铁等。
4)控制电炉生产对环境的影响,采用的措施有:
●控制空气污染(烟气及有毒气体)、噪声和对电网“环境”的污染(主要指“闪烁”)。
选择以上几种炉型都是可行的,但具体炉型的选择,要根据工厂的实际条件来确定。
本书主要以DRI为主要的原料的高阻抗电弧炉(超高功率UHP)为重点来介绍。
高阻抗电弧炉机械结构形式采用基础分离式结构、炉盖旋开顶装料、EBT偏心底出钢、高架式布置。
炉体结构为可分离式炉壳、管式水冷炉壁、管式水冷炉盖。
炉体安装3支集束式炉壁烧嘴,1只EBT口碳氧枪,炉门设置水冷碳氧枪。
整体示意图如图1.3-1~1.3~4所示。
设备组成以下将分别介绍。
图1.3-1EAF立面图1
图1.3-2EAF立面图2
图1.3-3EAF立面图3
图1.3-4EAF平面图1
1.3.1炉体
炉子总体结构采用基础分离式结构,高架式布置,可分离式炉壳,管式水冷炉壁,管式水冷炉盖,出钢方式为EBT偏心底出钢,结构见图1.3-5。
炉门配装水冷碳氧喷枪。
1.下炉壳;2.石墨柱;3.炉门框;4.炉门;5.炉门提升机构;6.提升机构护罩;7.上炉壳;8.垫圈;9.螺母;10.管路连接;11.偏心顶盖;12~17.销轴,楔块,垫圈;18.偏心区护栏组件;19.炉衬;20.出港口圈;21.出钢口启闭机构;22~25.螺栓,螺母,平垫,弹垫;26~30.炉壁水冷快
图1.3-5炉体结构图
炉体由上炉壳、下炉壳,炉门机构,EBT出钢机构和管式水冷炉壁组成。
上炉壳常规设计为无缝钢管焊成的框架结构,水冷炉壁安装在框架内,框架还起着水分配器和回水管的作用。
上炉壳安装三支集束式多功能燃料烧嘴枪,位于三个电极的冷区。
多功能燃料烧嘴枪固定支座位于炉壳外侧,其装卸、调整皆很方便。
位于EBT口上方安装1只碳粉枪,用于调整该位置的泡沫渣厚度。
下炉壳是由园筒形炉壳和碟形炉底焊接而成,后部带有出钢箱,其底为偏心底出钢。
当偏心底出钢时需在炉中留10~15%左右的余钢,炉体倾动12-15度即可完成出钢,炉役后期若炉底有凹坑,炉体最大可倾动20度,将残钢倒尽。
水冷炉壁为水冷密排管式结构,共十块,均布在上炉壳上,进出水均设球阀,出水处设水温检测,可监测每块水冷块的出水温度,并能对水冷块的冷却强度进行调整。
总进水有压力传感仪表及温度检测,总进水压力及出水温度皆可在计算机上显示。
上炉壳和下炉壳之间用销轴联接,活炉壳结构,便于拆卸,炉体上有牢固的吊耳,因此炉壳可整体吊出或吊入。
炉门孔设计已考虑了炉门采用炭氧枪操作的空间。
偏心底出钢机构,安装在炉体上,出钢口底板的开启为水冷套液压缸驱动,安全、可靠,也可用人工手动开启。
1.3.2电炉生产能力计算
(1)电炉的冶炼周期
电炉的冶炼周期见表5.1-8。
表5.1-8电炉的冶炼周期
项目
单位
80%DRI+20%废钢
30%DRI+70%废钢
前一炉出钢
min
3
3
炉子准备
min
3
3
调整电极
min
2
2
1号料篮装料
min
2
2
2号料篮装料
min
2
净断电时间
min
10
12
净通电时间
min
50
48
(2)电炉生产能力
电炉座数1座
电炉年运行时间:
7680h
时间利用率:
85%
电炉净运行时间:
6530h
钢水年产量:
312000t
电炉生产能力:
50t/h
电炉冶炼周期:
60min
年生产300000t的连铸坯,需要合格钢水307636t。
电炉年产量可达到312000t合格钢水,完全可以满足连铸坯对钢水的需要。
1.3.3电炉的主要消耗指标
电炉的主要消耗指标见表5.1-9。
表5.1-9电炉主要消耗指标
项目
单位
80%DRI+20%废钢
30%DRI+70%废钢
电耗
kWh/t钢水
560
470
氧气
Nm3/t钢水
34
34
天然气
Nm3/t钢水
3.4
6
碳粉
kg/t钢水
24
10
电极
kg/t钢水
1.8
1.65
压缩空气
Nm3/t钢水
3.0
1.25
铁合金
kg/t钢水
~15
~15
1.3.4有关电炉炉型的确定
近十年来出现了多种十分引人注目的新炉型,基本占据目前全部新建电炉市场。
近年出现的已投入工业化生产的各种新型电炉主要有:
--超高功率交流电弧炉
--超高功率直流电弧炉
--双炉壳电弧炉
--带竖井的电弧炉(简称竖炉)
--Consteel电炉
--Danarc电炉
新出现的多种型式的电炉各有其独到的特点,具体可归纳为以下几点:
--最大限度地节能降耗,采取的措施如下:
☆充分利用高温烟气进行有效地废钢预热;
☆采用喷吹燃料与氧气助熔及使CO二次燃烧等技术手段,利用化学能代替部分电能。
--缩短冶炼周期,提高电炉生产率及其生产能力,采用的措施有:
☆选择超高功率电炉──炉外精炼──连铸三位一体的短流程工艺路线,由超高功率电炉承担初炼熔化任务,大大缩短冶炼周期,提高了电炉生产率,并实现连铸机多炉连浇。
--增加对多种“铁源”炉料的适应性,采用的措施有:
☆配入高炉铁水、DRI、HBI、熔融还原铁、碳化铁等。
--控制电炉生产对环境的影响,采用的措施有:
☆控制空气污染(烟气及有毒气体)、噪声和对电网“环境”的污染(主要指“闪烁”)。
选择以上几种炉型都是可行的,但具体炉型的选择,要根据工厂的实际条件来确定,如:
产品方案、生产规模、原材料条件、能源供应情况、厂址特点、生产操作水平及资金和市场情况等诸多因素来综合研究确定。
鉴于伊朗原料的具体条件,DRI最多可配入80%的前提下,在尽可能节省资金、又使之具备新型电炉上述特点的情况下,推荐采用超高功率交流电弧炉。
全部用废钢作为电炉的原料,电炉使用双炉壳冶炼,则可以预热原料,节约电能,缩短冶炼时间,增加产量。
但由于伊朗电炉全部利用废钢为原料的可能性非常小,如果大量加入DRI,而DRI在高温下预热,会使DRI提前氧化,如若这样,则会给冶炼带来不利因素,会使得炉况恶化,降低金属收得率。
就本条生产线来说,建双炉壳,一方面在设备上需要增加投资,另一方面,其厂房面积也会因设置双炉壳有所增加。
所以本设计中没有采用。
普通超高功率电弧炉设置炉门和炉壁碳、氧喷枪,采用全过程泡沫渣冶炼,可提高电炉的热效率,缩短冶炼时间,减少电极消耗,节省冶炼电能。
为保证产量及提高工厂炼钢技术装备水平,所建电炉具备如下先进技术和配套装备:
☆采用超高功率供电
☆排管式水冷炉壁和水冷炉盖
☆笼形分体式炉壳,炉壳可整体拆卸
☆全液压驱动
☆偏心炉底出钢和留钢留渣操作技术
☆配置氧燃烧嘴和水冷式集束氧枪、全程泡沫渣埋弧冶炼工艺技术
☆导电臂水冷、电极喷淋水冷却
☆向电炉及出钢钢包内机械化加料设备
☆以PLC/PC技术为依托的电炉一级基础自动化系统与二级计算机过程控制系统
1.4LF炉精炼装置的工艺和设备
1.4.1LF原材料、燃料、动力介质的要求与供应
(1)原材料、燃料、动力介质要求
①活性石灰
活性石灰质量要求见表5.2-1所示
表5.2-1活性石灰成分要求
成分
CaO
SiO2
P
S
MgO
粒度(mm)
粉料量
一级(%)
≥90
≤3
≤0.02
≤0.03
≤5
10~50
≤5
过烧和欠烧率:
≤10%
活性度:
≥350ml/4N-HCl
②萤石
萤石成分要求见表5.2-2所示
表5.2-2萤石成分要求
成分
CaF2
SiO2
CaO
S
粒度(mm)
%
≥85
≤4
<5
<0.2
10-50
③铁合金
对铁合金的质量要求:
块度:
10-30mm
成分:
按标准供货
④石墨电极
LF炉对石墨电极的要求
电极技术性能:
电阻率:
6~8m
体积密度:
1.7-1.8t/m3
每节长度:
1800-2400±100mm
⑤氧气
管网压力:
1.6MPa
纯度:
>99.6%
⑥氩气
管网压力:
1.6MPa
纯度:
>99.99%
⑦压缩空气
管网压力:
>0.55MPa
⑧天然气
管网压力:
>8kPa
⑨冷却水
管网压力:
0.6MPa
进水温度:
≤35℃
过回水温度:
<50℃
水质要求见表5.2-3所示
表5.2-3水质要求
序号
项目
单位
LF炉设备冷却(a)
1
PH值
-
6~8
2
硫酸盐
mg/L
<100
3
氯化物
mg/L
<60
4
硬度(CaCO3)
ºDH
10
5
悬浮物
mg/L
20
6
电导率
us/cm
<50
7
总盐
mg/L
8
铁
mg/L
<2
9
碱度
mg/L
<60
10
可溶性固体
mg/L
<300
11
硅
mg/L
<6
12
悬浮物粒径
µm
13
油
mg/L
(2)LF的介质流量要求
介质流量要求见表5.2-4。
表5.2-4介质流量要求
序号
介质名称
单位
数量
备注
1
冷却水,包括
水质a
LF盖
m3/h
160
LF变压器等
m3/h
120
LF事故水
m3/h
60
2
N2,供LF炉设备/仪表
Nm3/h
50
3
O2,包括
设备维修
Nm3/h
25
间断
4
Ar,LF炉底吹
Nm3/h
72
平均值24
5
天然气,包括
设备维修
Nm3/h
15
间断
1.4.2LF炉物料消耗
LF炉物料消耗见表5.2-5。
表5.2-5主要物料消耗
序号
项目
单位
数量
备注
原材料
1
LF炉电极(400)
kg/kWh
0.015
2
铁合金
kg/t钢
20
3
活性石灰
kg/t钢
10
4
萤石
kg/t钢
1
5
LF炉耐火材料
kg/t钢
8
钢包
6
LF炉用铝丝
kg/t钢
0.25
7
LF炉用CaSi丝
kg/t钢
0.6
动力介质消耗
1
冶炼电耗LF炉
kWh/t钢•℃
0.5
2
氩气
Nm3/t钢
~0.3
1.4.3LF炉装置的主体设备特性
本工程根据50t电弧炉的产钢量及冶炼周期,设计采用50t单加热工位双车式LF炉1座。
型式:
双钢包车移动式 公称容量:
50吨
最大处理量:
55吨 最小处理量:
30吨
电极直径:
350mm 电极极心圆直径:
~590mm
电极升降速度:
100mm/s 电极升降行程:
~2400mm
变压器容量:
8000KVA 加热方式:
交流电弧
炉盖形式:
间接排烟全水冷管式双层罩
升温速度:
~4.5℃/min 精炼时间:
~40min
吹氩方式:
采用单块底吹透气砖氩气搅拌
氩气搅拌量:
10~300L/min,压力0.2~1.2Mpa
(1)LF炉主要设备参数
公称容量:
50t
最大处理量:
55t
最小处理量:
30t
钢包自由空间:
~500mm
升温速度:
3-5℃/min
电耗:
0.5kWh/t·℃
电极直径:
Φ400mm
电极节圆直径:
Φ700mm
导电臂形