乙苯工艺流程说明.docx
《乙苯工艺流程说明.docx》由会员分享,可在线阅读,更多相关《乙苯工艺流程说明.docx(11页珍藏版)》请在冰豆网上搜索。
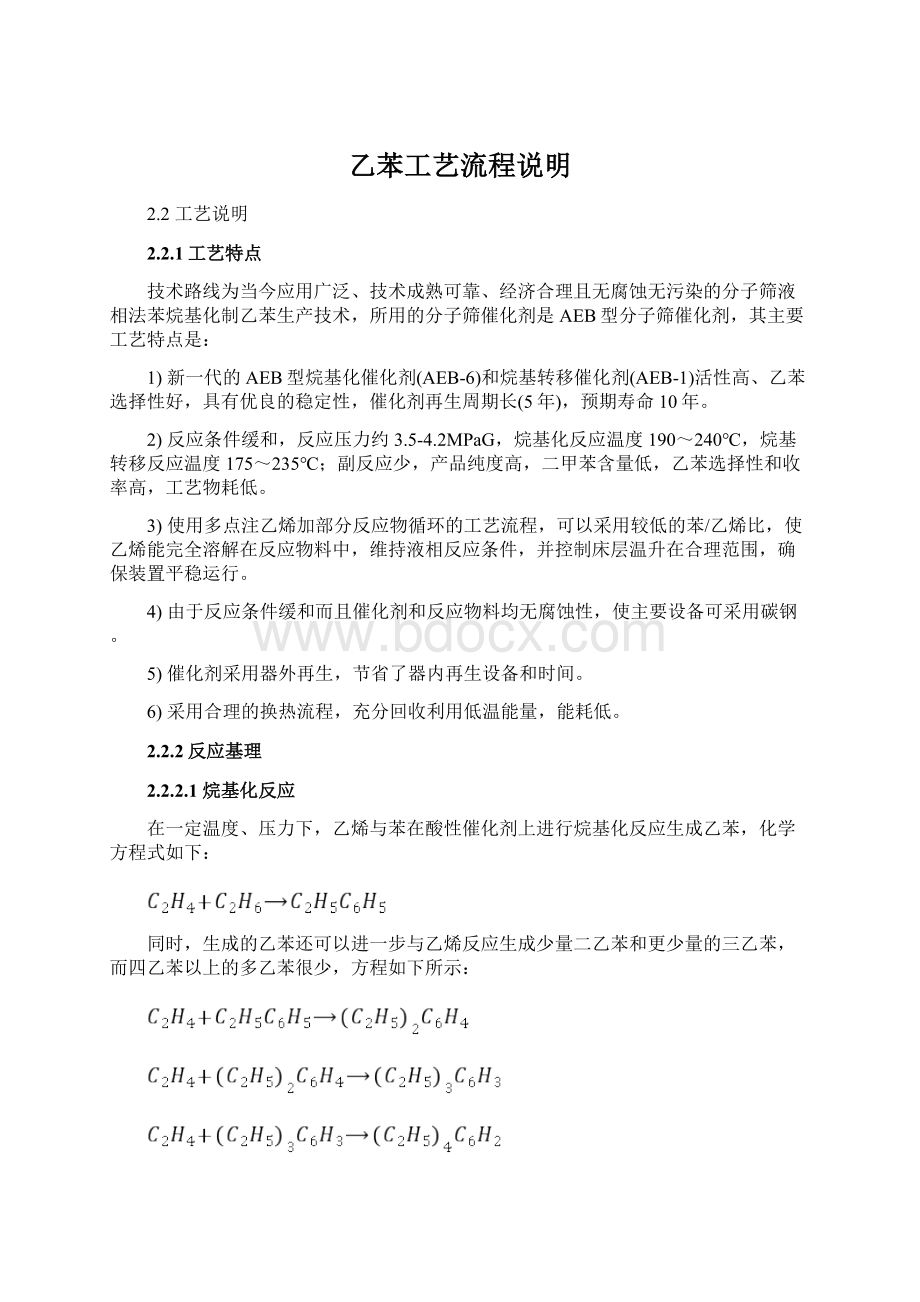
乙苯工艺流程说明
2.2工艺说明
2.2.1工艺特点
技术路线为当今应用广泛、技术成熟可靠、经济合理且无腐蚀无污染的分子筛液相法苯烷基化制乙苯生产技术,所用的分子筛催化剂是AEB型分子筛催化剂,其主要工艺特点是:
1)新一代的AEB型烷基化催化剂(AEB-6)和烷基转移催化剂(AEB-1)活性高、乙苯选择性好,具有优良的稳定性,催化剂再生周期长(5年),预期寿命10年。
2)反应条件缓和,反应压力约3.5-4.2MPaG,烷基化反应温度190~240℃,烷基转移反应温度175~235℃;副反应少,产品纯度高,二甲苯含量低,乙苯选择性和收率高,工艺物耗低。
3)使用多点注乙烯加部分反应物循环的工艺流程,可以采用较低的苯/乙烯比,使乙烯能完全溶解在反应物料中,维持液相反应条件,并控制床层温升在合理范围,确保装置平稳运行。
4)由于反应条件缓和而且催化剂和反应物料均无腐蚀性,使主要设备可采用碳钢。
5)催化剂采用器外再生,节省了器内再生设备和时间。
6)采用合理的换热流程,充分回收利用低温能量,能耗低。
2.2.2反应基理
2.2.2.1烷基化反应
在一定温度、压力下,乙烯与苯在酸性催化剂上进行烷基化反应生成乙苯,化学方程式如下:
同时,生成的乙苯还可以进一步与乙烯反应生成少量二乙苯和更少量的三乙苯,而四乙苯以上的多乙苯很少,方程如下所示:
理论上讲,从二乙苯一直到六乙苯都可以生成,但是由于苯环上乙基不断地增加,生成四乙苯、五乙苯、六乙苯的难度加大。
这一方面是因为苯环上乙基之间位阻增大,另一方面是因为多乙苯的分子结构越大越妨碍其在催化剂颗粒内的扩散,那么发生进一步反应的机会就越少。
所以,实际上生成的四乙苯很少,而五乙苯、六乙苯几乎没有。
由于目的产物是乙苯,因此在反应系统中应尽量控制多乙苯的生成,特别是四乙苯以上物质的生成。
除以上的反应外,主要的副反应有乙烯与两个苯环发生耦合反应生成二苯基乙烷,乙烯、苯或芳烃自聚生成多环化合物等重质物。
显然,这些物质的生成将降低乙苯产品的收率,增加物耗,因此要最大可能地减少这些副反应的发生。
上述反应是强放热反应,其中乙烯和苯的反应热约为1072.6kJ/kg乙苯。
反应热将使物料及催化剂床层的温度升高,为使烷基化反应在最佳条件下进行,需采取措施,不断取走多余的热量,控制反应温度和床层温升在合适的范围内。
在反应条件下,乙烯是以气相存在的。
由于气相乙烯极易在催化剂上发生聚合反应而生成大分子烯烃或高聚物,一方面增加了物耗,另一方面导致催化剂失活,缩短催化剂寿命。
因此,必须使乙烯完全溶解在反应进料中,保证烷基化反应在液相中进行。
虽然可以采用大量苯循环来解决上述问题,但导致分馏系统投资和能耗的增加。
因此,为了保证乙烯溶解、控制床层温升,同时满足苯烯比3.0的工艺条件,采用过量苯和部分反应产物循环与多点乙烯进料相结合的方法,既降低了苯烯比、减少了能耗,还可保证物耗没有增加。
2.2.2.2影响烷基化反应的主要因素
影响烷基化反应的主要因素包括反应温度、苯烯比、乙烯空速和原料杂质。
反应压力对催化剂活性、选择性的影响不大。
反应压力高,有利于乙烯的溶解,但也不宜太高,否则会增加投资和能耗。
因此,应根据维持反应系统完全处于液相状态的要求,确定合适的反应压力。
反应温度是影响反应的重要因素。
试验表明,在较低温度下,乙苯选择性高,但是催化剂的活性较低;随着反应温度升高,催化剂的活性增加,但乙苯选择性下降,当反应温度升到240、250℃时,乙苯选择性反而增加。
这是因为在上述条件下,催化剂的烷基转移性能得以发挥,生成的多乙苯又与过量苯转化成为乙苯,提高了乙苯的选择性。
值得注意的是,反应温度过高,将使重质物增多,乙苯收率下降。
根据以上分析,烷基化反应的温升应控制在适当范围内(小于40℃),以保证最有效地发挥催化剂的活性和稳定性。
烷基化反应的正常操作温度是200~245℃。
苯烯比是指反应原料苯与乙烯的摩尔比。
试验表明,苯烯比越大,乙苯选择性越高,多乙苯选择性越低;反之,则乙苯选择性下降,多乙苯选择性增加,增加的多乙苯虽然可通过烷基转移反应转化为乙苯,但处理量增大。
另外,苯烯比过低,将使生成的重质物增多。
因此,苯烯比的大小将直接影响装置的能耗和反应结果。
设计的烷基化反应的苯烯比是3.0。
乙烯空速低,有利于提高乙苯的选择性。
但催化剂装量大,生产成本高。
应根据催化剂的性能,确定适宜的乙烯空速。
原料杂质对烷基化反应的影响主要表现在对催化剂寿命的影响。
原料乙烯和苯中的碱性氮化物将占据催化剂的酸性中心,造成催化剂失活,极大地减少催化剂的寿命。
通常采用白土对原料苯进行预处理。
另外,反应物中少量的溶解水对维持催化剂活性稳定性是有益的,但如果长期使催化剂处于高水含量的反应物中,对催化剂的寿命极为不利。
最佳的反应物中水含量是100~200ppm。
因此,必须严格控制原料中的杂质含量。
2.2.2.3烷基转移反应
烷基化反应中产生的少量多乙苯(主要是二乙苯、三乙苯)可在一定的温度、压力条件和酸性催化剂的作用下,通过与苯发生烷基转移反应,转化成为乙苯,从而提高乙苯收率。
其主要方程式如下:
理论上讲,所有的多乙苯都可以进行烷基转移反应,但实际上受分子筛孔道及扩散的限制,四乙苯以上的多乙苯几乎不发生烷基转移反应。
烷基转移反应是可逆的二级反应,接近热力学平衡。
由于烷基转移反应的热效应很小,因此反应器催化剂床层中几乎没有温升。
同烷基化反应一样,烷基转移反应也是发生在分子筛催化剂的酸性活性中心上。
除了生成乙苯外,还可生成重质化合物,从而导致物耗增加,乙苯收率下降,因此应最大可能地减少副反应的发生。
工艺要求烷基转移反应在液相条件下进行。
2.2.2.4影响烷基转移反应的主要因素
影响烷基转移反应的主要因素包括反应温度、苯与多乙苯分子比、空速和原料杂质。
反应压力是根据保证在全液相反应条件下操作来确定的,它对烷基转移反应的结果没有影响。
反应温度是控制催化剂活性的主要工艺参数之一。
温度越高,催化剂活性越高。
当催化剂逐渐失活时,即烷基转移反应器多乙苯单程转化率下降,可通过逐步提高温度使其活性恢复。
设计反应温度的范围是175~235℃。
需注意的是:
升温可以提高烷基转移反应的速率,但如果升温速度太快,将导致催化剂失活速度加快,使用周期缩短,因此必须严格控制反应温度和升温速度。
通常是根据反应系统中多乙苯产量平衡来确定适宜的反应温度。
进料中苯量增加可以获得较高的多乙苯转化率和乙苯选择性。
但过多的苯在系统中循环将增加苯塔的负荷,增加能量消耗。
设计的烷基转移反应苯与多乙苯分子比为8。
由于烷基转移反应是热力学平衡控制,降低空速,增加反应的停留时间有利于提高多乙苯的转化率。
但空速也不宜过低,否则催化剂装量过多,增加了成本。
烷基转移反应时,进料中水含量与反应温度的控制关系密切。
如果水含量过高,需要增加反应温度。
通常苯中水含量无需控制,但需时常监测,并据此调整反应温度。
一般反应进料中的水含量为50~150ppmwt。
2.2.3工艺流程说明
乙苯单元工艺流程主要包括烷基化反应、烷基转移反应、苯原料精制、乙苯精馏等部分。
乙苯单元的工艺原则流程图见附图POSM-10-N-8001~POSM-10-N-8007。
2.2.3.1烷基化工艺流程
1)正常操作工况下的烷基化工艺流程
烷基化反应系统的作用是将苯和乙烯转化为乙苯和多乙苯。
本装置设计的烷基化反应的苯烯比为3.0。
为了更好地控制烷基化反应器的温升,保证乙烯的溶解,减少催化剂的积炭,延长催化剂的使用寿命;以及为了提高烷基化反应的乙苯选择性,烷基化工艺设计采用三反七段加循环的流程。
通过调整各段乙烯进料与循环物料的流量,保证乙烯的溶解和各段催化剂床层的温升在适当范围。
设计烷基化反应器为绝热反应器,共三台,第一台反应器中有一段催化剂床层,第二台反应器中有二段催化剂床层。
第三台反应器中有四段催化剂床层。
要求反应器在足够的压力下操作,以维持反应在全液相状态下进行。
乙烯按一定的比例分成7份,分别进入7段催化剂床层中,原料苯从第一烷基化反应器依次通过第二、第三烷基化反应器,物流的流向均为自下而上。
在第二烷基化反应器的出口使部分物流返回到第一烷基化反应器的入口,可增大反应原料对乙烯的溶解,设计第一烷基化反应器与第二、第三烷基化反应器各段乙烯进料之比是1.3186:
1.3186:
1,三台反应器的温升均小于40℃。
在本工艺设计中,由于苯烯比仅为3.0,烷基化反应系统放出的热量大于需要提供的热量。
因此在每台反应器之间设置取热装置,以保证满足适宜的反应条件。
第一烷基化反应器的出料用于发生0.45MPaG的蒸汽,第二烷基化反应器的出料先预热烷基化反应原料苯,多余的热量再发生0.45MPaG的蒸汽,第三烷基化反应器中段出料先加热烷基转移反应的进料,再发生0.45MPaG的蒸汽,第三烷基化反应器的出料直接送入乙苯精馏工段。
因烷基转移反应温度需要随着催化剂活性的降低而逐渐提升,当反应温度达到235℃时,需将第三烷基化反应器的出口温度提高至245℃,以满足加热烷基转移进料的要求。
烷基化反应原料苯来自乙苯精馏工段。
正常工况下,烷基化反应原料苯与第二烷基化反应器的出料换热后就能达到第一烷基化反应器入口温度;开工时,则用开停工加热器预热苯进料。
来自界外的乙烯被分别送入第一、第二和第三烷基化反应器各段,与苯进行烷基化反应。
在第一烷基化反应器、第二烷基化反应器下段和第三烷基化反应器的1、3段,乙烯与苯在反应器外的静态混合器中混合,而第二烷基化反应器上段和第三烷基化反应器的2、4段,乙烯与苯在反应器内混合。
2)切换工况下的烷基化工艺流程
由于第一烷基化反应器的催化剂受原料杂质的影响最直接,更易失活,为保证装置满足5年的运转周期,设计了第一烷基化反应器可切出更换催化剂的流程(切换流程)。
即:
将第一烷基化反应器与其余二台反应器隔离,单独更换催化剂。
换剂期间,另二台烷基化反应器仍可继续操作。
此时,乙烯与苯分别在第二和第三烷基化反应器中的六段催化剂床层上发生烷基化反应,在苯进料量不变的条件下,通过调整各段乙烯进料与循环物料的流量,乙苯装置操作负荷仍可达到100%。
设计切换工况时第二、第三烷基化反应器各段的乙烯进料量之比是1.385:
1.385:
1:
1:
1:
1,反应器各段的温升约23℃。
2.2.3.2烷基转移工艺流程
烷基转移反应系统的作用是将回收的多乙苯转化成目的产物乙苯。
烷基转移反应在一台绝热反应器中进行,反应器中有三段催化剂床层。
反应器要在足够的压力下操作,以维持反应在全液相状态下进行。
烷基转移反应器的进料包括来自乙苯精馏工段的回收苯和多乙苯混合物。
它们经第三烷基化反应器中段出料加热到反应温度后,进入烷基转移反应器发生反应。
原料苯中的水含量对催化剂寿命和反应结果影响较大,需严格控制。
烷基转移反应的反应热很小,整个催化剂床层的温度几乎相同,反应器出料直接送入乙苯精馏工段。
2.2.3.3催化剂处理
本装置内不设催化剂再生系统。
烷基化催化剂和烷基转移催化剂都采用器外再生方式,再生周期5年。
烷基化催化剂的初装量约51.0吨,预留部分待更换的烷基化催化剂约为9.2吨。
每台反应器的催化剂在卸出前,反应器都需经过排放、减压,排净物料(大部分是苯),然后通入过热蒸汽对催化剂进行吹扫,使苯含量小于10ppm,再用约180℃的热氮气吹扫,置换出蒸汽和吸附的水分,最后用空气使催化剂床层降温。
2.2.3.4苯原料预处理
由于苯原料中的杂质,特别是碱性氮化物,对催化剂活性及稳定性的影响很大,装置内设有白土处理器和分子筛处理器,以尽量减少杂质的影响,延长催化剂的使用。
补充的新鲜苯通过白土处理,脱除碱性氮化物,然后由热的乙苯产品加热至151℃左右,再进入分子筛处理器中,进一步吸附其中的杂质,经分子筛剂处理后的苯送入苯塔回流罐。
白土和分子筛剂使用一段时间失效以后,需用0.45MPaG的过热蒸汽和180℃热氮气进行处理,用蒸汽、氮气吹扫、置换后,排放气(氮气)中苯含量应小于10ppm。
卸出的白土可回收处理。
设计白土处理器二台,切换操作;分子筛处理器一台。
2.2.3.5乙苯精馏
乙苯精馏工段共有四个塔,其中苯塔、乙苯塔、多乙苯塔,用于分离反应产物中的苯、乙苯、多乙苯和残油,脱非芳塔用于除去反应物中的不凝气、水和轻非芳烃。
反应产物中未反应的苯在苯塔塔顶回收,苯塔塔顶蒸汽部分冷凝后产生0.45MPaG蒸汽。
苯凝液一部分作为苯塔回流,其余与补充的新鲜苯和脱非芳塔塔釜物料一起返回到第一烷基化反应器。
另外,由于塔顶回收苯中水含量超过烷基转移反应工艺的要求,故烷基转移反应的进料苯从苯塔上部第四板抽取。
苯塔回流罐中未冷凝的气体直接送入脱非芳塔底部,塔顶蒸汽经冷凝冷却,非芳烃(富含苯)凝液大部分作为塔的回流,少量的凝液间歇排至芳烃抽提装置回收其中的苯。
不凝气(甲烷、乙烷等轻烃)排入火炬管网。
原料苯中带入的少量水,从脱非芳塔回流罐的分水包中被分离出来。
脱非芳塔塔底物料则返回苯塔回流罐。
苯塔塔底物料送至乙苯塔,塔顶得到合格的乙苯产品。
乙苯塔塔顶蒸汽冷凝后产生0.45MPaG蒸汽。
乙苯凝液一部分作为乙苯塔回流,另一部分作为乙苯产品经能量回收、并冷却到40℃后,送至乙苯产品储罐。
乙苯塔塔底物料被送至多乙苯塔,从塔顶回收多乙苯。
该塔为减压塔,在减压操作条件(40kPaA,148℃)下,塔顶多乙苯蒸汽冷凝冷却后产生0.29MPaG的低压蒸汽,多乙苯凝液一部分作为回流返回塔中,另一部分由多乙苯泵送到烷基转移反应系统进行烷基转移反应。
多乙苯产品还可冷却后送至中间罐区的多乙苯罐。
多乙苯塔顶冷凝器中部分未冷凝的蒸汽和不凝气经冷凝、冷却后,凝液进入回流罐,不凝气经真空泵排至界外处理。
多乙苯塔塔底有少量的高沸物残油排出,经冷却后送往POSM装置重燃料油罐。
苯塔、乙苯塔、多乙苯塔的再沸器都采用4.2MPaG的高压蒸汽作热源,脱非芳塔不需要再沸器。
2.2.4工艺流程叙述
2.2.4.1烷基化和烷基转移反应
来自界外的乙烯,按一定的比例分成7份,分别送至R-10801进料混合器(M-10801)、R-10802进料混合器(M-10802)、第二烷基化反应器(R-10802)中部、R-10803一段进料混合器(M-10803)、第三烷基化反应器(R-10803)二段入口,R-10803三段进料混合器(M-10804)、第三烷基化反应器(R-10803)四段入口。
各部分乙烯分别由流量调节阀控制,其流量比例是1.3186:
1.3186:
1.3186:
1:
1:
1:
1。
来自苯塔回流罐的烷基化反应原料苯,其流量由流量调节阀控制,在烷基化原料苯换热器(E-10802)中与第二烷基化反应器出料换热后,经E-10801旁路进入R-10801进料混合器。
在开工时,E-10801用作原料苯的加热器。
第二烷基化反应器(R-10802)的部分出料作为循环物料,经烷基化反应循环泵(P-10801)提压,由流量调节阀控制其流量,与原料苯和乙烯在R-10801进料混合器(M-10801)中充分混合,然后进入第一烷基化反应器(R-10801)。
正常操作时,反应器R-10801的入口温度可通过调节E-10802壳程物料的流量来控制,温度为210℃;而开工时,需要调节E-10801的加热蒸汽量。
来控制R-10801的入口温度。
进入第一烷基化反应器(R-10801)下段的物料自下而上通过催化剂床层并发生反应,出料温度为232℃,经过R-10801出料冷却器(E-10806)冷却至202℃,并产生0.45MPaG的蒸汽,然后与一定量乙烯在R-10802进料混合器(M-10802)中混合。
通过调节冷却器E-10806旁路的流量,控制第二烷基化反应器入口温度为200℃。
第二烷基化反应器的进料——烷基化液自下而上通过催化剂床层并发生反应,在反应器的中部,物料与进入的乙烯混合,并继续发生反应。
因反应放热,反应器R-10802的温度升高约40℃。
第二烷基化反应器(R-10802)的另一部分出料在烷基化原料苯换热器(E-10802)中与原料苯换热,再经R-10802出料冷却器(E-10803)冷却并产生0.45MPaG的蒸汽,达到反应所需温度后,与一定量乙烯在R-10803一段进料混合器(M-10803)中混合。
调节E-10803旁路的流量,控制第三烷基化反应器(R-10803)的入口温度为200℃。
混合进料在第三烷基化反应器(R-10803)中自下而上通过第一段催化剂床层并反应,然后与通入的乙烯在器内混合,继续向上通过第二段催化剂床层并发生反应。
反应器R-10803一、二段的温度升高约40℃。
该部分烷基化反应产物从第三烷基化反应器(R-10803)第二段的出口引出,先进入烷基转移原料加热器(E-10805)加热烷基转移反应原料,再经R-10803中间冷却器(E-10804)冷却,并产生0.45MPaG的蒸汽,然后与一定量乙烯在R-10803三段进料混合器(M-10804)中混合。
调节E-10804旁路的流量,控制烷基化混合物在第三烷基化反应器(R-10803)第三段床层的入口温度为200℃。
反应物料自下而上通过第三段床层并反应,而且在第三、四段床层之间与通入的乙烯混合、继续进行反应。
第三烷基化反应器(R-10803)的出料在压力控制下,送入苯塔(T-10801)。
通过控制第三烷基化反应器出口的压力来保证烷基化反应系统完全处于液相状态。
第三烷基化反应器出口压力控制为3.55MPaG。
在切换工况下,部分乙烯与烷基化反应原料苯、以及循环物料(第二烷基化反应器出口的部分物料)混合后,直接进入第二烷基化反应器进行反应,第二和第三烷基化反应器按正常工艺流程操作。
烷基转移反应器(R-10804)的进料包括来自多乙苯塔回流罐(D-10805)的循环多乙苯、苯塔侧线抽出的烷基转移原料苯。
多乙苯的进料量采用流量控制,原料苯的流量根据多乙苯的流量采用比值控制。
进料混合物在烷基转移原料加热器(E-10805)中与烷基化液换热至所需的温度(初期175℃,末期235℃),然后进入烷基转移反应器(R-10804)。
反应器的进料温度通过调节烷基转移原料加热器(E-10805)旁路中烷基转移进料的流量来控制。
由于催化剂在生产过程中将缓慢失活,需要不断提高反应温度以维持其活性。
反应物料自下而上经过催化剂床层进行烷基转移反应,整个床层的温度几乎相同。
烷基转移反应器的出料在压力控制下送入苯塔,通过压力控制来保证烷基转移反应器中的物料完全处于液态。
2.2.4.2苯原料预处理和乙苯精馏
来自界区外的新鲜苯,需经过白土处理器(R-10805A/B)和分子筛处理器(R-10806)进行原料的预处理,其中的碱性氮化物被吸附。
经过处理的新鲜苯与乙苯产品在乙苯/新鲜苯换热器(E-10814)中被加热至151℃后,与苯塔顶冷凝器(E-10809)的出料混合,进入苯塔回流罐。
苯塔回流罐(D-10802)的液位与分子筛处理器的出料流量串级控制。
烷基化和烷基转移反应产物经过压力控制阀之后,呈汽液两相状态进入苯塔(T-10801)。
苯塔(T-10801)塔顶汽相馏分在苯塔顶冷凝器(E-10809)中部分冷凝,并产生0.45MPaG的蒸汽。
来自脱非芳塔(T-10804)塔釜的苯以及经白土和分子筛剂处理的补充新鲜苯,与呈汽液两相的苯塔顶冷凝器(E-10809)的出料在管线中混合,进一步冷凝该物流。
两相流进入苯塔回流罐(D-10802)。
在苯塔回流罐(D-10802)中汽液分离,一部分凝液在流量控制下经苯塔回流泵(P-10804)送回塔顶作回流,另一部分作为原料苯,在流量控制下,由烷基化原料苯泵(P-10802)送至烷基化原料苯换热器(E-10802),返回烷基化反应系统。
苯塔回流罐(D-10802)设有分水包,以收集非正常状况下分离出的游离水,收集的污水先排入地下分液罐,再适时排放到污水处理系统。
烷基转移反应的原料苯由烷基转移原料苯泵(P-10803)从苯塔上部第4块板抽出,控制一定的流量与多乙苯在R-10804进料混合器(M-10805)中混合,进入烷基转移反应系统。
苯塔塔顶压力与苯塔顶冷凝器壳程的压力串级控制。
需要时,塔顶压力也可与苯塔回流罐的气相出料量串级控制。
苯塔再沸器(E-10808)采用4.2MPaG的蒸汽加热,塔灵敏板温度与加热蒸汽流量串级,通过调节蒸汽流量,控制灵敏板的温度。
蒸汽凝液送入装置的凝液回收系统。
苯塔塔釜液位和塔釜出料流量串级控制,塔釜物料送至乙苯塔。
来自苯塔回流罐(D-10802)的蒸汽在流量控制下进入脱非芳塔(T-10804)的底部。
脱非芳塔(T-10804)塔顶蒸汽在脱非芳塔顶空冷器(E-10810)中冷凝冷却至55℃,再在脱非芳塔顶水冷器(E-10811)中冷却至40℃。
其流出物进入脱非芳塔回流罐(D-10803),从罐中分出的不凝气排至火炬。
因含有少量的游离水,冷却的液体将分为油相和水相。
聚集在分水包中的水,在液位控制下排入地下排液罐(D-10811),经地下罐沉降后,用排水泵打到全厂污水处理系统。
油相由苯及非芳烃组成,这些非芳是随原料苯带来的,并在脱非芳塔回流罐中逐渐富集。
在液位控制下,脱非芳塔回流罐(D-10803)中大部分物料经脱非芳塔顶泵(P-10805),送回塔内作回流。
并根据非芳累积量的多少,适时将少量的非芳烃物料(富含苯)由非芳烃输送泵(P-10812)送至界区外,防止系统中非芳烃积累。
塔底物料在液位控制下,经脱非芳塔底泵(P-10806)送至苯塔回流罐。
塔顶压力采用分程控制器控制,该分程控制器在需要时向火炬中排出不凝气体或补充氮气。
苯塔(T-10801)塔底物料以汽液两相进入乙苯塔(T-10802),塔顶汽相馏分在乙苯塔顶冷凝器(E-10813)中全部冷凝,并产生0.45MPaG蒸汽。
E-10813中冷凝的液体进入乙苯塔回流罐(D-10804),经乙苯塔顶泵(P-10807)升压后,一部分凝液作为回流在流量控制下返回乙苯塔塔顶;另一部分为乙苯产品,在乙苯塔回流罐(D-10804)的液位控制下先与补充新鲜苯在乙苯/新鲜苯换热器(E-10814)换热至92℃左右,再经乙苯产品空冷器(E-10816)和乙苯产品冷却器(E-10815)冷却到40℃,送入中间罐区的乙苯产品罐。
乙苯塔再沸器(E-10812)采用4.2MPaG的蒸汽加热,塔的灵敏板温度与蒸汽流量串级,通过调节蒸汽的流量来控制灵敏板的温度。
蒸汽凝液送入POSM装置的凝液回收系统。
乙苯塔塔釜液位和塔釜出料流量串级控制,塔底物料送至多乙苯塔。
采用分程控制器控制乙苯塔塔顶压力,该分程控制器在需要时排放不凝气到界外处理(可焚烧)或补充氮气。
乙苯塔塔底物料呈气液两相进入多乙苯塔(T-10803),多乙苯塔是减压塔,由多乙苯塔真空泵(SP-10801)维持真空操作,真空泵以多乙苯作密封介质。
采用分程控制器,调节从真空泵出口返回真空泵入口的循环流量或补充氮气以控制多乙苯塔的压力。
多乙苯塔真空泵分离的气相物流经真空密封罐(D-10808)排放到界区外(由工程设计单位结合POSM装置统一考虑);液相物流主要是多乙苯,返回多乙苯塔顶泵(P-10809)的入口。
另外,从多乙苯塔顶泵(P-10809)的出口,间歇引出少量多乙苯经多乙苯密封液冷却器(E-10823)冷却后,作为循环液供真空系统使用。
多乙苯塔塔顶汽相馏分在多乙苯塔顶冷凝器(E-10818)中冷凝冷却至148℃左右,并产生0.29MPaG的低压蒸汽,冷凝液进入多乙苯塔回流罐(D-10805)。
多乙苯塔顶冷凝器中部分未冷凝的蒸汽和不凝气,在多乙苯塔尾气冷凝器中经冷却水冷却至40℃后,冷凝液进入回流罐,一部分多乙苯在流量控制下由多乙苯塔顶泵(P-10809)送回多乙苯塔作回流;其余的多乙苯在流量控制下,由多乙苯泵(P-10810)送回烷基转移反应系统。
在多乙苯塔回流罐(D-10805)液位的控制下,合格的多乙苯物料经多乙苯产