光学冷加工.docx
《光学冷加工.docx》由会员分享,可在线阅读,更多相关《光学冷加工.docx(32页珍藏版)》请在冰豆网上搜索。
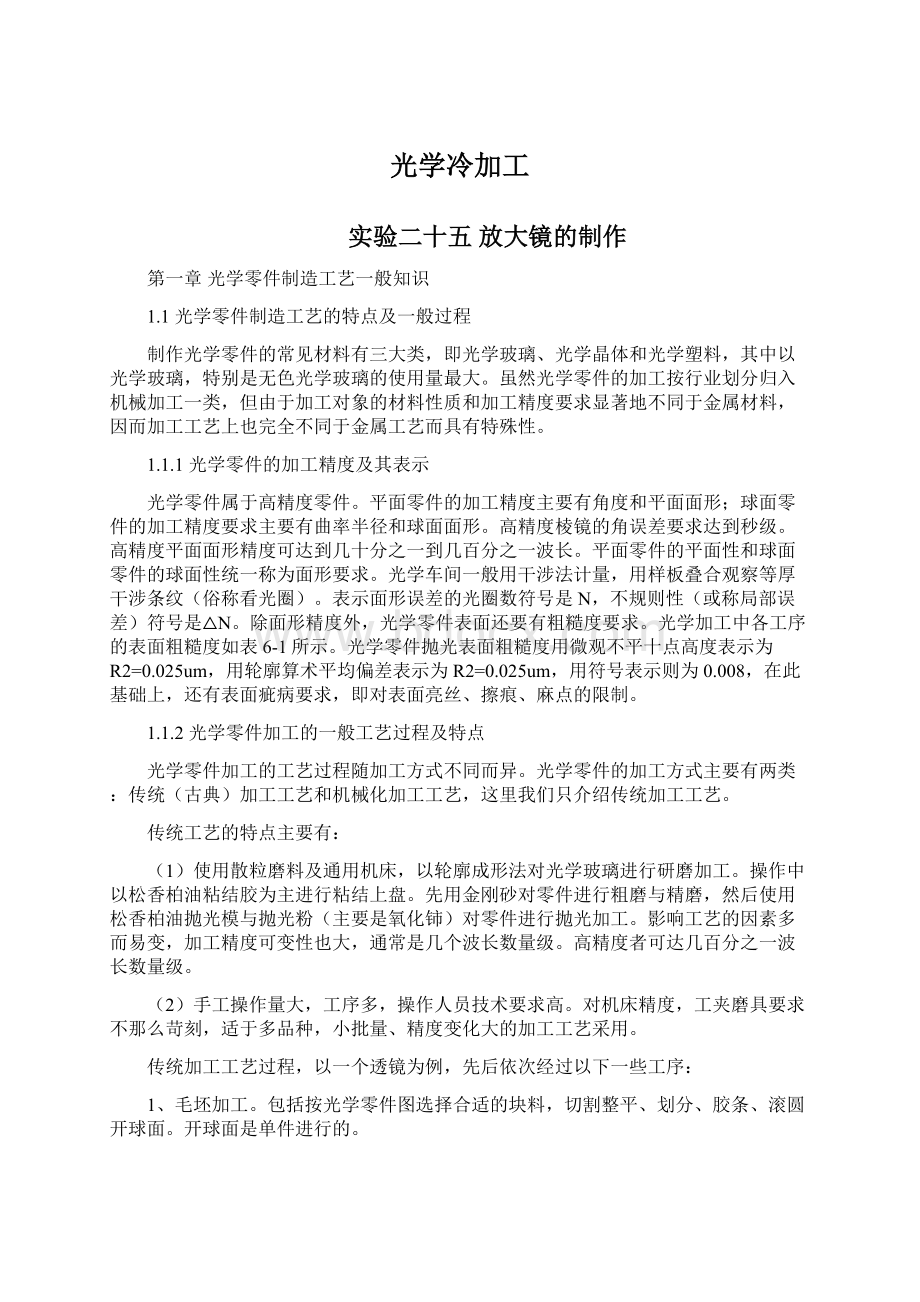
光学冷加工
实验二十五放大镜的制作
第一章光学零件制造工艺一般知识
1.1光学零件制造工艺的特点及一般过程
制作光学零件的常见材料有三大类,即光学玻璃、光学晶体和光学塑料,其中以光学玻璃,特别是无色光学玻璃的使用量最大。
虽然光学零件的加工按行业划分归入机械加工一类,但由于加工对象的材料性质和加工精度要求显著地不同于金属材料,因而加工工艺上也完全不同于金属工艺而具有特殊性。
1.1.1光学零件的加工精度及其表示
光学零件属于高精度零件。
平面零件的加工精度主要有角度和平面面形;球面零件的加工精度要求主要有曲率半径和球面面形。
高精度棱镜的角误差要求达到秒级。
高精度平面面形精度可达到几十分之一到几百分之一波长。
平面零件的平面性和球面零件的球面性统一称为面形要求。
光学车间一般用干涉法计量,用样板叠合观察等厚干涉条纹(俗称看光圈)。
表示面形误差的光圈数符号是N,不规则性(或称局部误差)符号是△N。
除面形精度外,光学零件表面还要有粗糙度要求。
光学加工中各工序的表面粗糙度如表6-1所示。
光学零件抛光表面粗糙度用微观不平十点高度表示为R2=0.025um,用轮廓算术平均偏差表示为R2=0.025um,用符号表示则为0.008,在此基础上,还有表面疵病要求,即对表面亮丝、擦痕、麻点的限制。
1.1.2光学零件加工的一般工艺过程及特点
光学零件加工的工艺过程随加工方式不同而异。
光学零件的加工方式主要有两类:
传统(古典)加工工艺和机械化加工工艺,这里我们只介绍传统加工工艺。
传统工艺的特点主要有:
(1)使用散粒磨料及通用机床,以轮廓成形法对光学玻璃进行研磨加工。
操作中以松香柏油粘结胶为主进行粘结上盘。
先用金刚砂对零件进行粗磨与精磨,然后使用松香柏油抛光模与抛光粉(主要是氧化铈)对零件进行抛光加工。
影响工艺的因素多而易变,加工精度可变性也大,通常是几个波长数量级。
高精度者可达几百分之一波长数量级。
(2)手工操作量大,工序多,操作人员技术要求高。
对机床精度,工夹磨具要求不那么苛刻,适于多品种,小批量、精度变化大的加工工艺采用。
传统加工工艺过程,以一个透镜为例,先后依次经过以下一些工序:
1、毛坯加工。
包括按光学零件图选择合适的块料,切割整平、划分、胶条、滚圆开球面。
开球面是单件进行的。
2、粗磨加工。
使表面粗糙度及球面半径符合细磨要求。
传统工艺中粗磨是单件进行的。
一般采用传统工艺加工的工厂中,粗磨车间往往包括毛坯加工。
3、上盘:
粗磨之后,经清洗,将一个个透镜毛坯按同半径组合成盘。
即依靠粘结胶把分散的透镜固定在球形粘结膜上,应注意的是成盘时要使每一个透镜毛坯的被加工面都处于同一半径的球面上。
4、细磨抛光工序。
在加工第一表面时,细磨到抛光过程中一般是不需拆盘的,即一次一盘完成。
操作中,先使用粒度依次变细的三至四道金钢砂将被加工面研磨到抛光要求的表面粗糙度,然后清洗,进行抛光。
抛光是用一定半径的抛光模加抛光粉进行。
一面加工完毕后,涂上保护膜,翻面再进行上盘。
细磨抛光加工第二表面。
5、定心磨边工序。
透镜加工过程中会出现光轴和定位轴偏离(称为偏心)。
定心磨边的任务是消除偏心,并使侧圆柱面径向尺寸达到装配要求。
传统工艺的磨边常在光学定心磨边机上进行。
6、镀膜工序,对表面有透光要求的透镜,要加镀增透膜。
球面反射镜要镀反射膜。
有的还要镀其它性质的薄膜,依使用要求由设计决定。
7、胶合工序。
对成象质量要求较高的镜头,往往采用几块透镜胶合而成。
胶合应在镀膜以后进行。
以上这些工艺过程可简略表示如下:
选料——切割——整平——胶条——滚圆——开球面——粗磨球面——上盘——细磨——抛光——下盘;第二面上盘——细磨——抛光——下盘——定心磨边——镀膜
1.2光学工艺安全操作知识
光学加工由于精度高,加工对象特殊,必须在专门的光学车间内进行。
因此,除了遵守一般的机械加工规则外,还必须遵守光学加工所特有的安全操作要求。
1.2.1光学车间的特点
在光学零件加工过程中,大多数工序对温度、湿度、尘埃、振动、光照等环境因素是敏感的,特别是高精度零件和特殊零件的加工尤其如此。
因此,光学车间都是封闭形,并要求恒温、恒湿、限制空气流动、人工采光,防尘。
1、温度对光学工艺的影响
恒温是光学车间一个明显特点之一。
这里包括恒温温度及波动范围两个问题。
光学车间各工作场所由于要求不同,对恒温温度及其波动范围的要求是各不相同的。
(1)温度对抛光效率与质量的影响
由于抛光过程中存在的化学作用随温度升高而加剧,因而升温会提高抛光效率。
但由于古典工艺中采用的抛光模制模用胶、粘结胶等主要由松香和沥青按一定配比制成,一定的配比只在一定的温度下使用。
而且它们对温度的变化较为敏感,温度过低,抛光模具与零件吻合性不好;温度过高,抛光模具抛光工作面变形。
这两者将使加工零件的精度难以保证,具体表现在光圈难以控制和修改。
实践得出:
抛光间的温度一般应控制在22℃±2℃为宜。
(2)检验对室温的要求
温度的波动直接影响检验精度。
一方面因为精密光学仪器对温度的波动很敏感;另一方面被检零件不恒温时,检具和零件间有温差会直接影响读数精度。
所以,检验室必须恒温,并且也应控制在22℃±2℃范围内。
2、湿度对光学工艺的影响
在光学零件加工过程中,凡要求恒温或空调的地方,均因控制湿度所需。
因为,水份蒸发速度直接影响湿度恒定状态。
湿度过低,易起灰尘,零件表表清擦时也易产生静电而吸附灰尘,影响其光洁度。
特殊零件如晶体零件的加工以及光胶工艺等,对湿度的要求尤为严格。
光学加工过程中室内温度一般应控制在60%左右。
3、防尘
由于光学零件对表面质量即表面光洁度和表面疵病有极高的要求,所以光学车间的防尘问题也特别突出。
灰尘在抛光时会使零件表面产生道子、划痕、亮丝;在镀膜时,会使膜层出现针孔、斑点、灰雾;在刻划时会引起刻线位置误差、断线等。
灰尘来源主要有:
外间空气带入;由工作人员衣物上落下(粒径一般在l一5μm左右,直径小于1μm的灰尘,往往不能依靠自重降落,而长时间悬浮于空气中,影响产品质量);
不洁净的材料、辅料、工夹具等带入;生产过程中产生的灰尘(光学车间的净化条件,若按室内含尘的重量浓度要求,应控制在毫克/米3的数量级。
胶合室的要求更严,一般以颗粒浓度作为要求,达到粒数/升的数量级)。
1.2.2光学生产安全操作规则
由于光学车间的特殊性和光学零件加工的高精度要求,学生进入光学车间实习时,必须遵守以下安全技术及操作规则:
1、进入光学车间,特别是进入细磨、抛光、检验、磨边、胶合、镀膜、刻划等工作间时,应穿白色工作服,戴工作帽,穿专用鞋子或干净拖鞋,以防止将室外灰尘带入光学车间;
2、在操作过程中禁止用手指直接触摸光学表面,需要拿起光学零件时,手指也只能接触光学零件的侧面或非工作面。
因为手指上留有汗渍、各种有机酸、盐类等对光学表面有害物质,它们往往会使光学零件表面受到侵蚀。
如果不小心触摸后,必须立即用脱脂纱布或脱脂棉花蘸上酒精、乙醚混合液擦拭干净;
3、为保持光学车间的恒温条件,不能在一个工作场所聚集过量人员,致使周围气温上升。
门窗也不能随意打开;
4、开机前,须先检查机床设备、工夹具是否完好。
发现电机有异常现象或其它机械毛病时,应立即拉开电闸或停机检查。
安装、拆卸零件和夹具时,机床主轴必须完全停止转动;
5、为了清洗光学零件和其它工作需要,光学车间常常使用或临时存放多种易燃物质,如溶剂汽油、无水酒精、乙醚等。
因此光学车间必须严格注意防火,加热设备必须远离上述物质。
为了防火,同时也为了空气卫生,光学车间内严格禁止吸烟;
6、在加工过程中,粗砂禁止带入细砂,细砂禁止带入抛光区,因此在换砂以后,在磨砂完毕进入抛光前,必须对工件、工夹具、工作台等进行彻底清洗,以防砂子带入使工件表面出划痕、亮丝,破坏光洁度;
7、在上盘、下盘,或其它需要加热光学零件情况时,不可使零件急热急冷。
加热时应注意零件升高的温度必须控制在材料的退火温度以下。
由于电炉表面温度已接近或超过许多材料的退火温度,所以不能将光学零件直接放置在电炉盘上加热,必须垫上衬垫;
8、在未了解实习所用机床及仪器设备的操作规范前,不允许擅自开动机床,试看试用有关的仪器设备。
也不允许操作不在实习范围内的仪器与设备,以免造成损坏和人身不安全事故。
1.3光学零件和光学零件图
光学零件是光学制造最后完成的目标,光学零件图是加工和检验的依据,所以在加工之前必须熟悉光学零件图及相应的技术指标、符号、尺寸等的含义。
1.3.1光学零件及有关术语、符号
光学工艺使用的图纸,通常有光学零件图、胶合部件图、工序图(毛坯图、粗磨图、抛光图等).其中光学零件图规定了加工时所必须的全部资料,包括外形尺寸,材料、技术要求及其它需说明的各项内容如图(1—11)、图(1—12)、图(1—13)所示。
其它工艺图纸均按光学零件图画出,标注各工序完工后的尺寸和检验要求。
绘制光学零件工艺图样的一般原则是:
光学零件的光轴用点划线表示,一般水平放置,光线方向应自左向右,零件一般对称于光轴放置,圆零件只画出沿光轴剖开的剖面图。
图纸左上角的表格依次列出对玻璃的要求和对零件的加工要求,包括面形精度,表面质量等.零件的外形尺寸,有关技术要求在图上注明或在图纸下方用文字或符号注明。
常用符号、术语说明如下:
N光圈数符号。
表示被检的零件表面和样板标准表面曲率半径偏差时产生的干涉条纹数(通称光圈)数目;
ΔN光圈局部误差符号,表示表面形状的局部误差;
ΔR样板精度等级符号.即样板曲率半径实际值对名义值的偏差量符号;
B(P)光学零件表面疵病符号,也称为光洁度。
光学零件工作表面的粗糙度一般都要求达到R1=0.025μm,旧标准为V14。
在此基础上还需限制表面上存在的亮丝、擦痕、麻点,应与机械加工中的光洁度概念区分开。
C(X)透镜偏心差符号,亦称透镜的中心偏差符号。
用透镜表面的球心对透镜定位轴的偏离量表示;
π尖塔差符号。
表示反射棱镜的棱向误差;
θ平行差符号。
玻璃平板两表面间的不平行度;
S屋脊棱镜双角差符号。
屋脊棱镜屋脊角有偏差时造成的双象差的程度;
d透镜中心厚度;
φ透镜的口径;
镀膜符号:
④为增透膜,②为增反镜;
Δnd玻璃材料折射率允许误差,包括对标准值的允差和同一批玻璃中的一致性允差。
Δ(nF—nC)色散允差,与Δnd一样同样包括二项:
光学均匀性:
玻璃内因折射率渐变造成的不均匀程度,影响零件的鉴别率,以鉴别率表示;双折射:
玻璃存在应力时呈现各向异性,产生双折射现象,以双折射光程差表示;纹:
玻璃中的化学不均匀区,因折射率不同于主体而出现丝状或层状的疵病,块料玻璃有从三个方向检查的,也有二个或者一个方向检验的;气泡:
玻璃体内残留气泡程度,有大小与个数两项指标。
1.4光学零件的加工余量
1.4.1加工余量的基本概念
在光学零件加工过程中,为了从玻璃毛坯获得所需要零件的形状、尺寸,表面必须预留一定量的玻璃层,这一定量的玻璃层就称为加工余量。
加工余量的正确给出是十分重要的,如果给出的余量小,则加工不出符合技术要求的零件;如果余量太大,又会造成材料与工时的浪费。
根据光学零件加工工序,零件的加工余量分为:
锯切余量、整平余量、滚圆余量、粗磨余量、细磨及抛光余量、定中心磨边余量;在每一工序之后给下一道工序留下的余量称为中间工序的余量;由加工中各个中间工序的余量所组成的余量总和称为总加工余量;鉴于各工序的加工特点不同,需要很好地研究如何合理地规定各道工序的加工余量。
1.4.2确定加工余量的原则
光学零件的绝大部分余量都是借助于散粒磨料或固着磨料磨除去的。
在研磨过程中,磨料对玻璃表面施加压力,形成一定的破坏层,往后的细磨、抛光等各道工序就是要除去这一破坏层,使玻璃表面形成符合要求的光学表面。
因此,确定加工余量的原则应该是每道工序中除去的余量等于上一道工序产生的破坏层深度Fn-1,与本道工序产生的破坏层深度之差.玻璃经过第一道砂粗磨后,表面产生凹凸层hc和破坏层Fc,破坏层最深处以AA’表示;当第二道砂粗磨时,产生凹凸层h1和破坏层F1,而破坏层深度应与AA’线重合,而其加工余量应为图中的△1,显然△1等于Fc与F1之差。
以后各道磨料的研磨加工余量均可类推,最后一道磨料的精磨所产生的h与F都己相当细微,因此,应该使最后一道磨料中的F略微超出AA线。
然后通过抛光除去残余的相当微细的破坏层。
余量的表达式为:
必须指出:
根据上述原则计算的余量只是理论值,实际上还应该结合加工的具体情况给予适当地放大。
1.4.3各工序余量的确定
1、锯切余量与公差
锯切余量与锯片的侧向振动、锯片厚度、锯切深度等因素有关,可按表1—1选取。
表1—1锯切余量
锯切深度
(mm)
散粒磨料锯切余量mm
金刚石锯片锯切余量mm
锯片厚度1mm
锯片厚度2mm
锯片厚度1mm
锯片厚度2mm
〈10
10~65
〉65
1.5
2.0
2.5
3.0
3.2
3.6
1.5
1.8
2.2
2.5
2.7
3.0
锯切的尺寸公差取±0.2~0.5mm。
2、整平余量
整平时,磨去玻璃层的厚度,决定于毛坯玻璃的厚度,表面不平程度及其它表面疵病大小,一般加工中单面整平余量取0.2~0.6mm;
3、磨外圆加工余量与公差
磨外圆余量是指将整平后的方料,按其边长磨到圆直径之间的磨去量,根据磨外圆的加工机床与零件尺寸不同,可按表1-2确定,磨外圆公差可按表1-3确定。
表1-2磨外圆余量
零件直径mm
加工种类
〈7
无心磨床
0.4~0.6
7~40
手搓滚圆
外圆磨床
改装车床
1.5~2.0
1.5~2.0
2.0~2.5
〉40
外圆磨床
改装车床
2.0~3.0
2.5~4.0
表1—3磨外圆公差
加工方法
外圆公差mm
不同柱度mm
无心磨床
手搓滚圆
外圆磨床
改装车床
0.05
0.10
0.05~0.10
0.10~0.20
0.01
0.01~0.10
0.05
0.10
4、研磨、抛光余量与公差
研磨的余量与被加工零件开关和尺寸、毛坯的种类、机床精度等因素有关。
抛光余量十分微小,它与精磨余量一起给出。
(1)用散粒磨料研磨时,粗磨余量参考表1-4:
表1-4散粒磨料粗磨余量
零件
毛坯种类
加工面形状
透镜直径或长方形零件边长(mm)
单面余量
0~25
25~40
40~65
〉65
1
2
1
2
1
2
1
2
透镜
球面型料
凸面和凹面
0.2
0.3
0.3
0.4
0.4
0.6
0.6
0.6
块料
凸面
0
0
0
0
凹面
h
h
h
h
平面镜
平面型料
平面
0.2
0.4
0.3
0.5
0.4
0.6
0.6
0.9
棱镜
型料和锯料
平面
0.5
0.5
0.6
0.6
0.7
0.7
0.9
0.9
(2)用固着磨料研磨时,粗磨铣切余量参考表1—5,对于棱镜,考虑到修磨角度,余量应当增大。
表1—5固着磨料粗磨余量
种类
零件直径
直径
直径
单面余量(mm)
双凸透镜
0.15
0.20
平凸透镜
0.075
0.10
双凹透镜
有平台
1
0
无平台
0.1
0.15
平凹透镜
0.05
0.075
(3)精磨抛光余量及公差
精磨和抛光的余量:
一般采用的数据为,零件直径≤10mm时,单面余量取0.15~0.20mm,零件直径>10mm时,单面余量取0.20~0.25mm。
高速精磨余量一般取0.1mm。
3、定心磨边余量
凹透镜的定心磨边余量参考表1—6选取。
对于凸透镜当其直径与凹透镜尺寸相同时,可选取比表1—6低一级的余量。
表1—6凹透镜定心磨边余量
透镜直径(mm)
1.5~2.5
2.5~4
4~6
6~10
10~15
15~25
25~65
65~100
>100
加工余量(mm)
0.4
0.6
0.8
1.0
1.2
1.5
2.0
2.5
3
1.4.4光学零件毛坯尺寸的计算
各工序的加工余量确定之后,就可计算出毛坯的尺寸。
1、透镜的毛坯尺寸计算
对于双凸透镜可按下式计算:
t=t0+2(p1+p2)
对于凹凸透镜可按下式计算:
t=t0+2(p1+p2)+h
对于双凹透镜可按下式计算:
t=t0+2(p1+p2)+h1+h2
式中:
t——毛坯的厚度;
t0——透镜的中心厚度;
p1——精磨抛光余量(单面);
p2——粗磨余量(单面);
h1、h2――凹面的矢高。
2、棱镜的毛坯尺寸计算
棱镜的种类虽多种多样,但都可认为是若干个三棱镜的组合,所以只需分析三棱镜毛坯尺寸的计算。
第二章光学零件制造工艺实习
2.1光学零件的粗磨成型工艺
2.1.1粗磨及其要求
一、概述
1、什么是粗磨
将玻璃加工成透明的光学表面,无论采用传统工艺还是机械化工艺,均需要经过三大基本工序:
即粗磨、细磨(精磨)、抛光。
粗磨是将玻璃块料或型料毛坯加工成具有一定几何形状、尺寸精度和表面粗糙度的工件的工序。
按国内一般情况,粗磨工序是包括毛坯加工分工序的,而狭义的粗磨是仅指在已基本成型的毛坯上研磨表面,使其表面形状(如球面半径)和表面粗糙度满足下一步上盘细磨要求的那一部分工作。
这里所述粗磨则指较广的范围,即从由块料加工毛坯开始,因此它所包含的分工序相应地要比成型毛坯的多一些。
2、粗磨的要求
粗磨的要求是随零件的种类不同而不同的。
对于球面零件,粗磨加工的要求是:
一定的曲率半径、中心厚度、中心偏不超过某一范围;完工后的表面粗糙度要求达到3.2(R1=3.2μm)相当于旧标准光洁度等级为V5;对于平面零件,粗磨加工的要求是:
一定的角度、厚度、外形尺寸;完工后的表面粗磨度一般应比球面零件的要求高一些。
二、粗磨工艺的机床、设备与辅料
传统工艺用机床采用散粒磨粒加工,主要种类有:
(1)割料机:
主要结构为一高速旋转的铁片圆盘,下置一个砂桶,用手推动玻璃进行锯割,俗称泥锯;
(2)粗磨机:
该机床由一电机通过皮带驱动主轴转动,主轴上端装有平模或球模,主轴转速可以利用塔轧变速,研磨时可根据工件加工余量的大小,向平模或球模添加不同粒度的磨料与水的混合物。
玻璃的磨除量和表面凹凸层与磨料粒度、磨料种类、磨料供给量、机床转速及压力等因素有关。
该机只有一个主轴,故又称单轴机,若有两个主轴则称粗磨二轴机。
三、粗磨量具
根据粗磨精度情况,量具使用范围如下:
(1)钢尺:
用于划线、切料、核料、测量;
(2)分厘卡:
0—25mm规格,用于凸透镜中心厚度测量;25mm以下的外圆及棱镜尺寸测量;加装测量头还可测量凹透镜的中心厚度;25~50mm规格,用于25—50内各种外圆尺寸、棱镜尺寸测量;
(3)游标卡尺:
用于零件直径、长度、高度、内径等大于50mm的尺寸测量;
(4)百分表:
测量零件深度、平行度、凹透镜中心厚度;
(5)角尺:
包括直角尺、调整角尺(角规)、万能角尺,用于测量零件角度,是棱镜加工的必备量具;
(6)刀口尺:
用于检验平面零件的平面性;
以上量具校正时应用三级块规。
四、粗磨磨料
粗磨磨料最常用的是金刚砂,其主要成份为Al2O3、SiO2、Fe2O3等,系天然矿物产品。
磨料生产中,对于粗细不同的磨料是用其粒度来表示的。
按国家标准规定,对用筛选法获得的磨料粒度号用一英寸长度上的筛孔数目命名,如60、80、120、280。
号数越大,磨料越细;较细的磨料用水选法分级,以实际尺寸命名粒度号。
如W。
、W20、Wo等,号数越大,磨料越粗。
由于各种粒度的磨料实际上是一群粒径在一定范围内的混合体,因此,对磨料的质量还要求要有一定的粒度均匀性。
五、粘结材料
用于粘结零件,是一种零件粘结和装夹辅助材料,常用的有柏油和松香。
按一定比例配合熬制成的火漆、松香和黄蜡配制的粘结胶等,其主要指标是针入度和软化点。
软化点越高,针入度越小,胶则越硬.对于粘结胶,软化点约为上盘温度,而适宜使用的室内温度则应低于此值,粘结胶软化点应大于80℃。
2.1.2粗磨磨具
粗磨磨具包括加工用的研磨模、倒角模和装夹粘结用的粘结模。
加工模具又称工具,多用铸铁制造;粘结模又称夹具,常用铝合金或铸铝制成,按其外形可分为球面和平面两类,各种球面模具的主要差别在于球面半径精度和模具的矢高,不同模具原则上不能通用。
平面模具主要指标是其口径大小,通用性较大。
一、球面零件的粗磨
A、球面零件粗磨工艺过程
球面零件粗磨工艺过程根据所用毛坯的类型及加工方式的不同而不同。
1、块料毛坯:
传统工艺下的球面零件粗磨工艺过程,可由下列工序构成:
(1)锯料(切割):
按零件毛坯尺寸进行锯切;
(2)整平:
磨去锯切时留下的不平痕迹;
(3)切片(或割方):
按零件直径毛坯尺寸切片割方;
(4)胶条:
按零件厚度方向胶成长条;
(5)滚圆:
用手工方法将胶条磨去棱角再滚磨成圆柱,或装在专用机床上直接按尺寸要求磨外圆;
(6)拆胶、清洗:
胶条拆开获得若干单个圆形玻璃片;
(7)磨球面(俗称开R):
将圆片平表面按图纸要求磨成球面;
(8)倒角:
磨去锋利的边缘;
(9)清洗送检。
2、型料毛坯:
型料毛坯一般是已具有圆片形状的玻璃料或是热压成型的球面玻璃料两种,对于型料毛坯一般是采用机械化工艺加工,其工序过程有:
(1)型料检验型料是一定质量的光学玻璃经热加工后的产品,其理化性质常有改变,因此用料时,一定要按图纸要求逐项检验,合格方可使用;
(2)上盘将型料上刚性盘装夹
(3)铣磨球面用金刚石磨轮在铣磨机上进行铣削形成球面;
(4)粗磨修整这一工序主要用于部分机械化工艺中,即成盘铣磨好的球面零件,下盘后要单只粗磨修整并倒角,方能送古典式细磨工序加工。
B、主要工序操作方法
1、锯料(切割):
锯料的目的是将大块料锯切成小块或片状,以利下道工序加工。
可按以下步骤完成。
(1)选料:
根据图纸上对材料提出的各项指标要求,认真细致地选择,不可出错,稍有差错,加王后即成废品,既费工又费料,因为以后各道工序一般不再检查,也很难检查。
(2)划线:
划线的尺寸是图纸上零件要求的名义尺寸,总的加工余量与锯缝宽度三部分之和。
双凸透镜划线尺寸计算:
厚度划线尺寸:
6(图纸上名义尺寸)+0.3(细磨抛光余量)+0.2(粗磨余量)+1(整干余量)+2(锯缝宽度)=8.5。
式中:
单位是毫米(mm);
直径划线尺寸:
30(图上名义尺寸)+1.5(磨边余量)+1(滚圆余量)+1(磨方余量)+2(锯缝宽度)=35.5。
(3)锯切:
在泥锯上锯切;先检查机床是否正常,砂桶内有无合适的砂浆,工作台是否可靠。
然后开动机床,手持玻璃沿靠板缓缓推进切割;对较薄的玻璃块,为防止最后崩边可预先胶上一块保护玻璃再行切割。
若在金刚石锯片切割机上切割,先按操作说明书检查机床是否正常,锯片装夹是否紧固,冷却液是否流通。
然后装夹玻璃,调整好位置,开动电机自动切割。
(4)锯切操作注意事项
a、锯片不平直时:
应先调整平直,轴上安装要正确、可靠;
b、进料时,应对准锯缝,锯片和玻璃接触线不应过长,并应从玻璃边缘开始切割;
c、用手握住玻璃时,不应有上下与左右方向的跳动,切割开始与结束时用力要轻,以防崩边;
d、锯大的玻璃块料时,切到中间应调转180º再切;
e、锯下的余料,必须即时