过程控制水槽实验指导书打印版.docx
《过程控制水槽实验指导书打印版.docx》由会员分享,可在线阅读,更多相关《过程控制水槽实验指导书打印版.docx(30页珍藏版)》请在冰豆网上搜索。
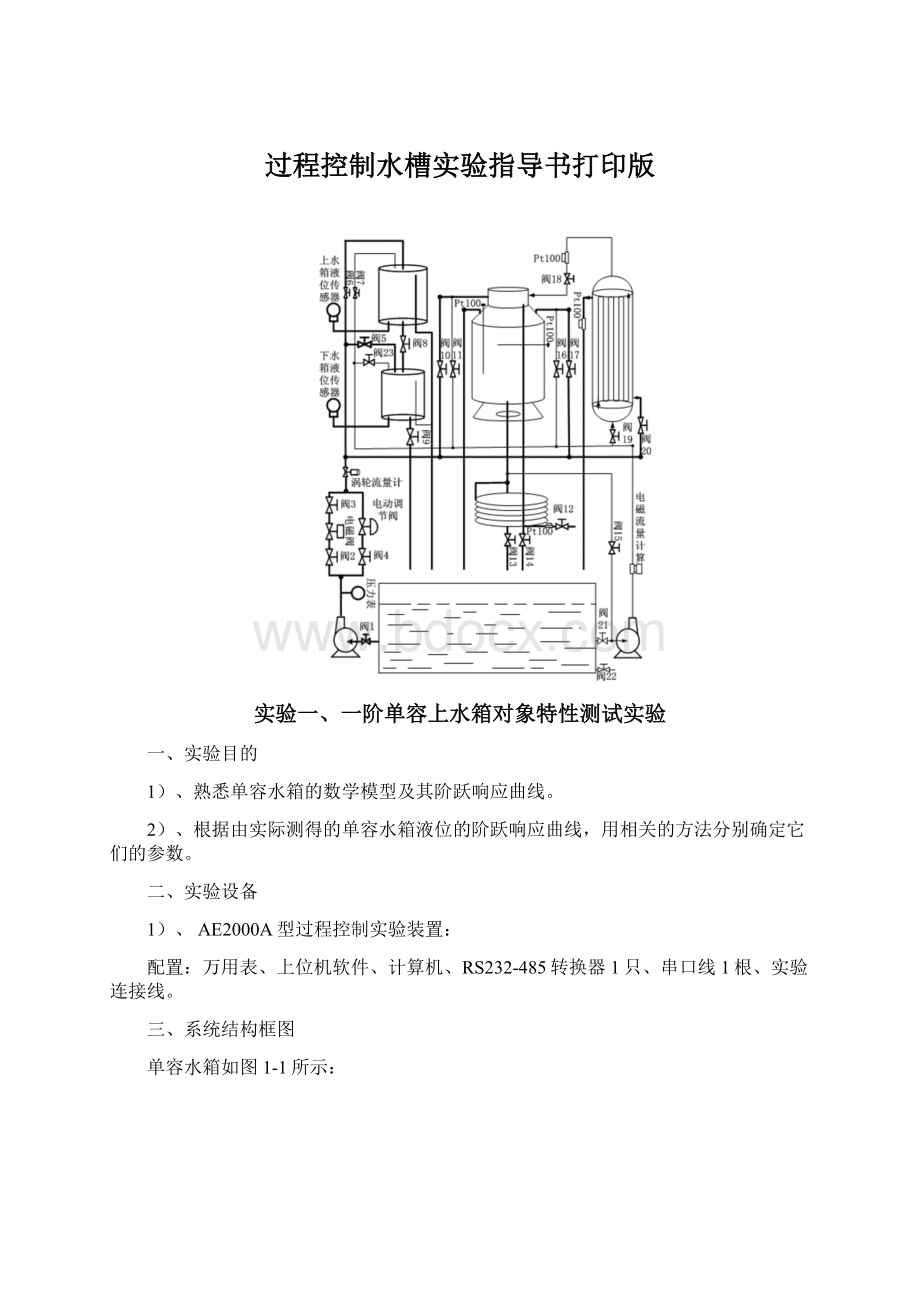
过程控制水槽实验指导书打印版
实验一、一阶单容上水箱对象特性测试实验
一、实验目的
1)、熟悉单容水箱的数学模型及其阶跃响应曲线。
2)、根据由实际测得的单容水箱液位的阶跃响应曲线,用相关的方法分别确定它们的参数。
二、实验设备
1)、AE2000A型过程控制实验装置:
配置:
万用表、上位机软件、计算机、RS232-485转换器1只、串口线1根、实验连接线。
三、系统结构框图
单容水箱如图1-1所示:
图1-1、单容水箱系统结构图
四、实验原理
阶跃响应测试法是系统在开环运行条件下,待系统稳定后,通过调节器或其他操作器,手动改变对象的输入信号(阶跃信号),同时记录对象的输出数据或阶跃响应曲线。
然后根据已给定对象模型的结构形式,对实验数据进行处理,确定模型中各参数。
图解法是确定模型参数的一种实用方法。
不同的模型结构,有不同的图解方法。
单容水箱对象模型用一阶加时滞环节来近似描述时,常可用两点法直接求取对象参数。
如图1-1所示,设水箱的进水量为Q1,出水量为Q2,水箱的液面高度为h,出水阀V2固定于某一开度值。
根据物料动态平衡的关系,求得:
在零初始条件下,对上式求拉氏变换,得:
式中,T为水箱的时间常数(注意:
阀V2的开度大小会影响到水箱的时间常数),T=R2*C,K=R2为单容对象的放大倍数,R1、R2分别为V1、V2阀的液阻,C为水箱的容量系数。
令输入流量Q1的阶跃变化量为R0,其拉氏变换式为Q1(S)=RO/S,RO为常量,则输出液位高度的拉氏变换式为:
当t=T时,则有:
h(T)=KR0(1-e-1)=0.632KR0=0.632h(∞)
即h(t)=KR0(1-e-t/T)
当t—>∞时,h(∞)=KR0,因而有
K=h(∞)/R0=输出稳态值/阶跃输入
式(1-2)表示一阶惯性环节的响应曲线是一单调上升的指数函数,如图1-2所示。
当由实验求得图1-2所示的
图1-2、阶跃响应曲线
阶跃响应曲线后,该曲线上升到稳态值的63%所对应时间,就是水箱的时间常数T,该时间常数T也可以通过坐标原点对响应曲线作切线,切线与稳态值交点所对应的时间就是时间常数T,其理论依据是:
上式表示h(t)若以在原点时的速度h(∞)/T恒速变化,即只要花T秒时间就可达到稳态值h(∞)。
五、实验内容和步骤
1、设备的连接和检查:
(1)、关闭阀23,将AE2000A实验对象的储水箱灌满水(至最高高度)。
(2)、打开以丹麦泵、电动调节阀、涡轮流量计组成的动力支路至上水箱的出水阀门:
阀1、阀4、阀7,关闭动力支路上通往其他对象的切换阀门:
阀2、阀6、阀11、阀18、阀21。
(3)、打开上水箱的出水阀:
阀9至适当开度。
(4)、检查电源开关是否关闭
2、系统连线图:
1-3、实验接线图
1)、电源控制柜里的三相电源空气开关、单相Ⅰ空气开关、单相泵电源开关打在关的位置。
2)、电动调节阀的~220V电源开关打在关的位置。
3)、智能调节仪的~220V电源开关打在关的位置。
4)、如图1-3所示:
将I/O信号接口板上的上水箱液位的钮子开关打到OFF位置。
5)、将上水箱液位+(正极)接到任意一个智能调节仪的1端(即RSV的+极),上水箱液位-(负极)接到智能调节仪的2端(即RSV的负极)。
6)、将智能调节仪的4~20mA输出端的7端(即+极)接至电动调节阀的4~20mA输入端的+端(即正极),将智能调节仪的4~20mA输出端的5端(即-极)接至电动调节阀的4~20mA输入端的-端(即负极)。
3、启动实验装置
1)、将实验装置电源插头2接到380V的三相交流电源。
2)、打开电源三相带漏电保护空气开关,电压表指示380V。
3)、打开总电源钥匙开关,按下电源控制柜上的启动按钮,即可开启电源。
4、实验步骤
1)、开启单相Ⅰ空气开关,根据仪表使用说明书和液位传感器使用说明调整好仪表各项参数和液位传感器的零位、增益,仪表输出方式设为手动输出,初始值为0。
2)、启动计算机MCGS组态软件,进入实验系统相应的实验如图1-4所示:
1-4、实验软件界面
3)、双击设定输出按钮,设定输出值的大小,或者在仪表手动状态下,按住仪表的STOP键将仪表的输出值上升到所想设定的值,这个值根据阀门开度的大小来给定,一般初次设定值<25。
开启单相泵电源开关,启动动力支路。
将被控参数液位高度控制在20%处(一般为7cm)。
4)、观察系统的被调量:
上水箱的水位是否趋于平衡状态。
若已平衡,应记录调节仪输出值,以及水箱水位的高度h1和智能仪表的测量显示值并填入下表。
仪表输出值
水箱水位高度h1
仪表显示值
0~100
cm
cm
5)、迅速增加仪表手动输出值,增加5%的输出量,记录此引起的阶跃响应的过程参数,它们均可在上位软件上获得。
以所获得的数据绘制变化曲线。
T(秒)
水箱水位
h1(cm)
仪表读数
(cm)
6)、直到进入新的平衡状态。
再次记录平衡时的下列数据,并填入下表:
仪表输出值
水箱水位高度h1
仪表显示值
0~100
cm
cm
7)、将仪表输出值调回到步骤5)前的位置,再用秒表和数字表记录由此引起的阶跃响应过程参数与曲线。
填入下表:
t(秒)
水箱水位
h1(cm)
仪表读数
(cm)
六、实验报告要求
(1)作出一阶环节的阶跃响应曲线。
(2)根据实验原理中所述的方法,求出一阶环节的相关参数。
七、注意事项
(1)本实验过程中,阀8不得任意改变开度大小。
(2)阶跃信号不能取得太大,以免影响正常运行;但也不能过小,以防止因读数误差和其他随机干扰影响对象特性参数的精确度。
一般阶跃信号取正常输入信号的5%~15%。
(3)在输入阶跃信号前,过程必须处于平衡状态。
八、思考题
(1)在做本实验时,为什么不能任意上水箱出水阀变化阀的开度大小?
(2)用两点法和用切线对同一对象进行参数测试,它们各有什么特点?
实验二、上水箱液位PID整定实验
一、实验目的
1)、通过实验熟悉单回路反馈控制系统的组成和工作原理。
2)、分析分别用P、PI和PID调节时的过程图形曲线。
3)、定性地研究P、PI和PID调节器的参数对系统性能的影响。
二、实验设备
1)、AE2000A型过程控制实验装置、上位机软件、计算机、RS232-485转换器1只、串口线1根。
2)、万用表一只
三、实验原理
图2-1、实验原理图
图4-1为单回路上水箱液位控制系统。
单回路调节系统一般指在一个调节对象上用一个调节器来保持一个参数的恒定,而调节器只接受一个测量信号,其输出也只控制一个执行机构。
本系统所要保持的参数是液位的给定高度,即控制的任务是控制上水箱液位等于给定值所要求的高度。
根据控制框图,这是一个闭环反馈单回路液位控制,采用工业智能仪表控制。
当调节方案确定之后,接下来就是整定调节器的参数,一个单回路系统设计安装就绪之后,控制质量的好坏与控制器参数选择有着很大的关系。
合适的控制参数,可以带来满意的控制效果。
反之,控制器参数选择得不合适,则会使控制质量变坏,达不到预期效果。
一个控制系统设计好以后,系统的投运和参数整定是十分重要的工作。
一般言之,用比例(P)调节器的系统是一个有差系统,比例度δ的大小不仅会影响到余差的大小,而且也与系统的动态性能密切相关。
比例积分(PI)调节器,由于积分的作用,不仅能实现系统无余差,而且只要参数δ,Ti调节合理,也能使系统具有良好的动态性能。
比例积分微分(PID)调节器是在PI调节器的基础上再引入微分D的作用,从而使系统既无余差存在,又能改善系统的动态性能(快速性、稳定性等)。
但是,并不是所有单回路控制系统在加入微分作用后都能改善系统品质,对于容量滞后不大,微分作用的效果并不明显,而对噪声敏感的流量系统,加入微分作用后,反而使流量品质变坏。
对于我们的实验系统,在单位阶跃作用下,P、PI、PID调节系统的阶跃响应分别如图4-2中的曲线①、②、③所示。
图2-2、P、PI和PID调节的阶跃响应曲线
一、实验内容和步骤
1、设备的连接和检查:
(1)、将AE2000A实验对象的储水箱灌满水(至最高高度)。
(2)、打开以丹麦泵、电动调节阀、涡轮流量计组成的动力支路至上水箱的出水阀门:
阀1、阀4、阀7,关闭动力支路上通往其他对象的切换阀门:
阀2、阀6、阀11、阀18、阀21。
(3)、打开上水箱的出水阀至适当开度。
(4)、检查电源开关是否关闭。
2、系统连线如图4-3所示:
图2-3、上水箱液位PID参数整定控制接线图
1)、三相电源、单相Ⅰ空气开关打在关的位置。
2)、智能调节仪的~220V的电源开关打在关的位置。
3)、将I/O信号接口板上的上水箱液位的钮子开关打到OFF位置。
4)、将上水箱液位+(正极)接到任意一个智能调节仪的1端(即RSV的正极),将上水箱液位-(负极)接到智能调节仪的2端(即RSV的负极)。
5)、将智能调节仪的4~20mA输出端的7端(即正极)接至电动调节阀的4~20mA输入端的+端(即正极),将智能调节仪的4~20mA输出端的5端(即负极)接至电动调节阀的4~20mA输入端的-(即负极)。
3、启动实验装置
1)、将实验装置电源插头接到380V的三相交流电源。
2)、打开电源三相带漏电保护空气开关,电压表指示380V。
3)、打开总电源钥匙开关,按下电源控制屏上的启动按钮,即可开启电源
4)、开启单相Ⅰ,调整好仪表各项参数(仪表初始状态为手动且为0)和液位传感器的零位。
5)、启动智能仪表,设置好仪表参数。
(一)比例调节控制
1)、启动计算机MCGS组态软件,进入实验系统选择相应的实验,如图4-4所示:
图2-4、实验软件界面
2)、打开电动调节阀和单相电源泵开关,开始实验。
3)、设定给定值,调整P参数。
4)、待系统稳定后,对系统加扰动信号(在纯比例的基础上加扰动,一般可通过改变设定值实现)。
记录曲线在经过几次波动稳定下来后,系统有稳态误差,并记录余差大小。
5)、减小P重复步骤4,观察过渡过程曲线,并记录余差大小。
6)、增大P重复步骤4,观察过渡过程曲线,并记录余差大小。
7)、选择合适的P,可以得到较满意的过渡过程曲线。
改变设定值(如设定
值由50%变为60%),同样可以得到一条过渡过程曲线。
8)、注意:
每当做完一次试验后,必须待系统稳定后再做另一次试验。
(二)、比例积分调节器(PI)控制
1)、在比例调节实验的基础上,加入积分作用,即在界面上设置I参数不为0,观察被控制量是否能回到设定值,以验证PI控制下,系统对阶跃扰动无余差存在。
2)、固定比例P值(中等大小),改变PI调节器的积分时间常数值Ti,然后观察加阶跃扰动后被调量的输出波形,并记录不同Ti值时的超调量σp。
表二、不同Ti时的超调量σp
积分时间常数Ti
大
中
小
超调量σp
3)、固定I于某一中间值,然后改变P的大小,观察加扰动后被调量输出的动态波形,据此列表记录不同值Ti下的超调量σp。
表三、不同δ值下的σp
比例P
大
中
小
超调量σp
4)、选择合适的P和Ti值,使系统对阶跃输入扰动的输出响应为一条较满意的过渡过程曲线。
此曲线可通过改变设定值(如设定值由50%变为60%)来获得。
(三)、比例积分微分调节(PID)控制
1)、在PI调节器控制实验的基础上,再引入适量的微分作用,即把软件界面上设置D参数,然后加上与前面实验幅值完全相等的扰动,记录系统被控制量响应的动态曲线,并与实验
(二)PI控制下的曲线相比较,由此可看到微分D对系统性能的影响。
2)、选择合适的P、Ti和Td,使系统的输出响应为一条较满意的过渡过程曲线(阶跃输入可由给定值从50%突变至60%来实现)。
3)、在历史曲线中选择一条较满意的过渡过程曲线进行记录。
(四)、用临界比例度法整定调节器的参数
在实现应用中,PID调节器的参数常用下述实验的方法来确定。
用临界比例度法去整定PID调节器的参数是既方便又实用的。
它的具体做法是:
1)、待系统稳定后,逐步减小调节器的比例度δ(即1/P),并且每当减小一次比例度δ,待被调量回复到平衡状态后,再手动给系统施加一个5%~15%的阶跃扰动,观察被调量变化的动态过程。
若被调量为衰减的振荡曲线,则应继续减小比例度δ,直到输出响应曲线呈现等幅振荡为止。
如果响应曲线出现发散振荡,则表示比例度调节得过小,应适当增大,使之出现等幅振荡。
图4-5为它的实验方块图。
图2-5、具有比例调节器的闭环系统
2)、在图4-5系统中,当被调量作等幅荡时,此时的比例度δ就是临界比例度,用δk表示之,相应的振荡周期就是临界周期Tk。
据此,按下表可确定PID调节器的三个参数δ、Ti和Td。
图2-6、具有周期TK的等幅振荡
表四、用临界比例度δk整定PID调节器的参数
调节器参数
调节器名称
δk
Ti(S)
Td(S)
P
2δk
PI
2.2δk
Tk/1.2
PID
1.6δk
0.5Tk
0.125Tk
3)、必须指出,表格中给出的参数值是对调节器参数的一个初略设计,因为它是根据大量实验而得出的结论。
若要就得更满意的动态过程(例如:
在阶跃作用下,被调参量作4:
1地衰减振荡),则要在表格给出参数的基础上,对δ、Ti(或Td)作适当调整。
二、实验报告要求
1)、画出单容水箱液位控制系统的方块图。
2)、用接好线路的单回路系统进行投运练习,并叙述无扰动切换的方法。
3)、用临界比例度法整定调节器的参数,写出三种调节器的余差和超调量。
4)、作出P调节器控制时,不同δ值下的阶跃响应曲线。
5)、作出PI调节器控制时,不同δ和Ti值时的阶跃响应曲线。
6)、画出PID控制时的阶跃响应曲线,并分析微分D的作用。
7)、比较P、PI和PID三种调节器对系统无差度和动态性能的影响。
三、注意事项
1)、实验线路接好后,必须经指导老师检查认可后方可接通电源。
四、思考题
1)、实验系统在运行前应做好哪些准备工作?
2)、为什么要强调无扰动切换?
3)、试定性地分析三种调节器的参数δ、(δ、Ti)和(δ、Ti和Td)的变化对控制过程各产生什么影响?
4)、如何实现减小或消除余差?
纯比例控制能否消除余差?
实验三、二阶双容对象特性测试实验
一、实验目的
1)、熟悉双容水箱的数学模型及其阶跃响应曲线。
2)、根据由实际测得的双容液位阶跃响应曲线,分析双容系统的飞升特性。
二、实验设备
1、AE2000A型过程控制实验装置
配置:
上位机软件、计算机、RS232-485转换器1只、串口线1根、实验连接线。
三、原理说明
图3-1双容水箱系统结构图
如图2-1所示:
这是由两个一阶非周期惯性环节串联起来,输出量是下水箱的水位h2。
当输入量有一个阶跃增加
Q1时,输出量变化的反应曲线如图2-2所示的
h2曲线。
它不再是简单的指数曲线,而是就使调节对象的飞升特性在时间上更加落后一步。
在图中S形曲线的拐点P上作切线,它在时间轴上截出一段时间OA。
这段时间可以近似地衡量由于多了一个容量而使飞升过程向后推迟的程度,因此,称容量滞后,通常以τC代表之。
图3-2、变化曲线
设流量Q1为双容水箱的输入量,下水箱的液位高度h2为输出量,根据物料动态平衡关系,并考虑到液体传输过程中的时延,其传递函数为:
式中K=R3,T1=R2C1,T2=R3C2,R2、R3分别为阀V2和V3的液阻,C1和C2分别为上水箱和下水箱的容量系数。
式中的K、T1和T2须从由实验求得的阶跃响应曲线上求出。
具体的做法是在图2-3所示的阶跃响应曲线上取:
1)、h2(t)稳态值的渐近线h2(∞);
2)、h2(t)|t=t1=0.4h2(∞)时曲线上的
点A和对应的时间t1;
3)、h2(t)|t=t2=0.8h2(∞)时曲线上的
点B和对应的时间t2。
然后,利用下面的近似公式计算式
2-1中的参数K、T1和T2。
其中:
图3-3、阶跃响应曲线
对于式(2-1)所示的二阶过程,0.32〈t1/t2〈0.46。
当t1/t2=0.32时,可近似为一阶环节;当t1/t2=0.46时,过程的传递函数G(S)=K/(TS+1)2(此时T1=T2=T=(t1+t2)/2*2.18)
四、实验步骤
1、设备的连接和检查:
(1)、开通以丹麦泵、电动调节阀、涡轮流量计以及上水箱出水阀1、阀4、阀7、阀9所组成的水路系统;关闭通往其他对象的切换阀2、阀6、阀11、阀18、阀21。
(2)、将下水箱的出水阀10开至适当开度。
(3)、检查电源开关是否关闭。
2、系统连线
接线如图3-4所示:
图3-4、实验接线图
1)、三相电源、单相Ⅰ空气开关打在关的位置。
2)、智能调节仪的~220V的电源开关打在关的位置。
3)、将I/O信号接口板上的上水箱液位的钮子开关打到OFF位置。
4)、将下水箱液位+接到任意一个智能调节仪的信号输入端1(即RSV的+极),下水箱液位-(负端)接到智能调节仪的2端(即RSV的-极)。
5)、将智能调节仪的~20mA输出端的7端(即+极)接至电动调节阀的4~20mA输入端的+端(即正极),将智能调节仪的4~20mA输出端的5端(即-极)接至电动调节阀的4~20mA输入端的-(即负极)。
3、启动实验装置
1)、将实验装置电源插头接到380V的三相交流电源。
2)、打开电源三相带漏电保护空气开关,电压表指示380V。
3)、打开总电源钥匙开关,按下电源控制屏上的启动按钮,即可开启电源。
4、实验步骤
1)、开启单相Ⅰ空气开关,下水箱液位传感器输出信号为1~5V电压信号,调整好仪表输入规格参数与其他各项参数,开始校准液位传感器的零位和增益,仪表输出方式设为手动输出,初始值为0。
2)、启动计算机MCGS组态软件,进入实验系统相应的实验,界面如图3-5所示:
图3-5、实验软件界面
3)、开启单相泵电源开关,启动动力支路,手动将仪表的输出值迅速上升到小于等于10,将被控参数液位高度控制在30%处(一般为5cm)。
4)、观察系统的被调量——水箱的水位是否趋于平衡状态。
若已平衡,应记
录调节仪输出值,以及水箱水位的高度h2和智能仪表的测量显示值并填入下表。
仪表输出值
水箱水位高度h2
仪表显示值
0~100
cm
cm
5)、迅速增加仪表手动输出值,增加10%的输出量,记录此引起的阶跃响应的过程参数,均可在上位软件上获得各项参数和数据,并绘制过程变化曲线。
T(秒)
水箱水位
h2(cm)
仪表读数
(cm)
6)、直到进入新的平衡状态。
再次记录测量数据,并填入下表:
仪表输出值
水箱水位高度h2
仪表显示值
0~100
cm
cm
7)、将仪表输出值调回到步骤5)前的位置,再用秒表和数字表记录由此引起的阶跃响应过程参数与曲线。
填入下表:
T(秒)
水箱水位
h2(cm)
仪表读数
(cm)
8)、重复上述实验步骤。
五、注意事项
1)做本实验过程中,阀V2不得任意改变开度大小。
2)阶跃信号不能取得太大,以免影响正常运行;但也不能过小,以防止影响对象特性参数的精确性。
一般阶跃信号取正常输入信号的5%~15%。
3)在输入阶跃信号前,过程必须处于平衡状态。
六、实验报告要求
1)作出二阶环节的阶跃响应曲线。
2)根据实验原理中所述的方法,求出二阶环节的相关参数。
3)试比较二阶环节和一阶环节的不同之处。
七、思考题
1)在做本实验时,为什么不能任意变化下水箱出水阀的开度大小?
2)用两点法和用切线法对同一对象进行参数测试,它们各有什么特点?
实验四、上水箱下水箱液位串级控制实验
一、实验目的
1)、掌握串级控制系统的基本概念和组成。
2)、掌握串级控制系统的投运与参数整定方法。
3)、研究阶跃扰动分别作用在副对象和主对象时对系统主被控量的影响。
二、实验设备
1)、AE2000A型过程控制实验装置:
上位机软件、计算机、RS232-485转换器1只、串口线1根。
2)、万用表一只
三、实验原理
上水箱液位作为副调节器调节对象,下水箱液位做为主调节器调节对象。
控制框图如图4-1所示:
4-1、上水箱下水箱液位串级控制框图
四、实验内容和步骤
1、设备的连接和检查:
(1)、打开以丹麦泵、电动调节阀、涡轮流量计组成的动力支路至上水箱的出水阀门:
阀1、阀4、阀7,关闭动力支路上通往其他对象的切换阀门:
阀2、阀11、阀18、阀21。
(2)、打开上水箱和下水箱的出水阀:
阀9和阀10至适当开度。
(3)、检查电源开关是否关闭
2、系统连线图:
图4-2、实验接线
1)、电源控制板上的三相电源、单相Ⅰ的空气开关、单相泵电源开关打在关的位置。
2)、电动调节阀的~220V电源开关打在关的位置。
3)、智能调节仪的~220V电源开关打在关的位置。
4)、如图4-2所示:
将I/O信号接口板上的下水箱液位的钮子开关打到OFF位置,上水箱液位的钮子开关打到ON位置。
5)、将下水箱液位+(正极)接到任意一个智能调节仪的1端(即RSV的+极),下水箱液位-(负端)接到智能调节仪的2端(即RSV的-极)。
智能仪表的地址设为1,软件定义调节仪地址为1的调节器为主调节器,调节仪地址为2的调节器为副调节器。
6)、将主调节仪的4~20mA输出接至I/O信号面板的转换电阻上转换成1~5V电压信号,再将此转换信号接至另一调节仪(副调节器)的1端和2端作为外部给定,上水箱液位信号转换为0.2~1V的信号后接入副调节器的3、2两端。
调节器输出的4~20mA接电动调节阀的4~20mA控制信号两端。
3、启动实验装置:
1)、将实验装置电源插头接到380V的三相交流电源。
2)、打开电源三相带漏电保护空气开关,电压表指示380V。
3)、打开总电源钥匙开关,按下电源控