附录世界常用钢号对照表解析.docx
《附录世界常用钢号对照表解析.docx》由会员分享,可在线阅读,更多相关《附录世界常用钢号对照表解析.docx(32页珍藏版)》请在冰豆网上搜索。
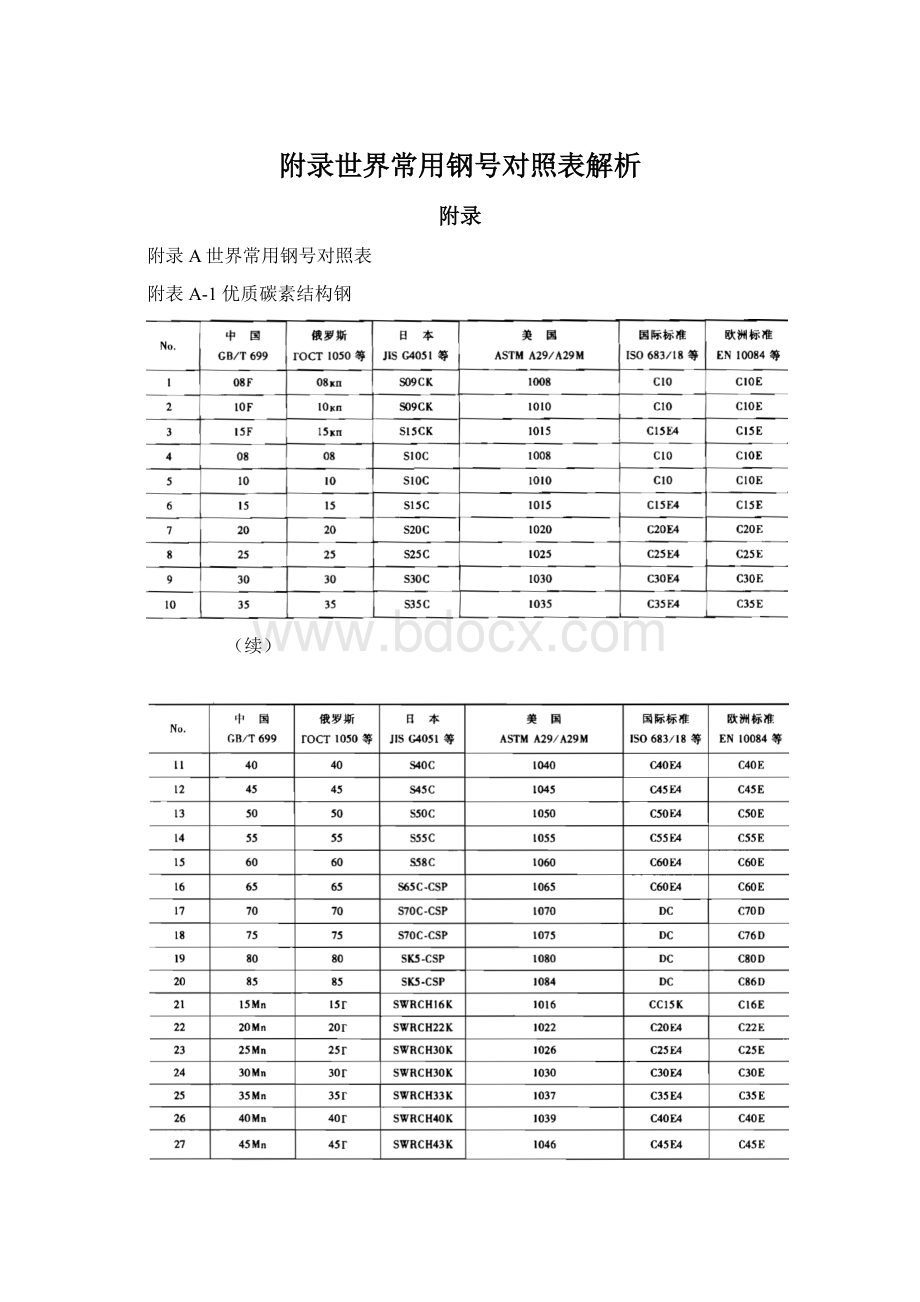
附录世界常用钢号对照表解析
附录
附录A世界常用钢号对照表
附表A-1优质碳素结构钢
(续)
(续)
附表A-2合金结构钢
(续)
(续)
(续)
(续)
附表A-3弹簧钢
(续)
附表A-4高碳铬轴承钢
附表A-5碳素工具钢
(续)
附表A-6合金工具钢
(续)
(续)
附表A-7高速工具钢
(续)
附表A-8不锈钢标准钢号对照表
(续)
(续)
(续)
附表A-9耐热钢
(续)
(续)
附录B新、旧标准拉伸性能符号对照
金属材料的拉伸性能及其符号的新标准《金属材料室温拉伸试验方法》(GB/T228-2002)合并且代替《金属拉伸试验方法》(GB/T228-1987)、《金属薄板(带)拉伸试验方法》(GB/T3076-1982)和《金属拉伸试验试样》(GB/T6397-1986)三个标准。
新标准与旧标准在性能名称与符号对照列于下表。
附录B-1新、旧标准拉伸性能符号对照
附录C全书图表一览
第1章钢铁热处理基础
图1-1Fe-Fe3C合金相图
表1-1Fe-Fe3C相图中的特征点
表1-2Fe-Fe3C相图中的特性线
表1-3Fe-Fe3C相图中各相的特性
表1-4热处理常用的临界温度符号及说明
图1-2Fe-Fe3C相图中常用的热处理工艺加热区间
表1-5铁碳合金中各种组织的力学性能
图1-3合金钢按用途分类
表1-6生铁产品牌号示例
表1-7专用结构钢的前缀符号
表1-8专用钢材产品用途、特性和工艺方法表示符号
表1-9优质碳素结构钢牌号和优质碳素弹簧钢牌号示例
表1-10合金结构钢和合金弹簧钢示例
表1-11其他钢牌号示例
表1-12过冷奥氏体转变类型及主要特征
表1-13常用钢材过冷奥氏体等温转变图的类型
图1-4不同马氏体量时碳含量与淬火硬度的关系
表1-14常用钢种淬火硬度与临界直径
表1-15部分钢不同截面尺寸的淬火硬度(HRC)
表1-16常用淬火介质的淬火烈度H值(cm-1)
表1-17加热计算经验公式及碳钢和合金钢的加热系数
表1-18高速钢在盐浴炉中淬火的加热系数
表1-19工模具钢在不同介质中的加热时间及加热系数
表1-20节能计算法使用的钢件加热时间计算表
表1-21不同钢种加热时间计算表
表1-22电耗定额计算及考核公式
表1-23表1-22中公式各符号含义
表1-24工艺折算系数
表1-25加热方式系数
表1-26生产方式系数
表1-27工件材料系数
表1-28常用热处理工艺装载系数
表1-29燃料消耗定额计算及考核公式
表1-30表1-29中公式各符号的含义
表1-31工艺折算系数
表1-32加热方式系数
表1-33常用热处理工艺装载系数
表1-34钢的临界温度经验公式
表1-3550个常用钢种的回火经验方程
表1-36正火与退火工艺分类及应用范围
表1-37常用钢回火脆性温度范围(℃)
表1-38淬火冷却方法分类与应用范围
表1-39回火工艺名称与应用范围
表1-40调质件加工预留余量
表1-41轴类零件热处理时外圆预留磨削余量
表1-42套类零件热处理时预留磨削余量
表1-43中碳钢套类零件内孔预留余量
表1-44中碳钢套类零件外经及高度预留余量
表1-45高碳钢套类零件内孔预留余量
表1-46高碳钢套类零件外经及高度预留余量
表1-47渗碳钢套类零件内孔预留余量
表1-48渗碳钢套类零件外经及高度预留余量
表1-49合金钢套类零件内孔预留余量
表1-50合金钢套类零件外经及高度预留余量
第2章常用钢材热处理工艺数据
表2-1碳素结构钢牌号和性能
表2-2碳素结构钢新旧牌号对照
表2-3优质碳结构钢磷、硫含量和低倍组织要求
表2-4优质碳素结构钢临界点温度及常规热处理工艺参数
表2-5合金结构钢牌号与化学成分
表2-6合金结构钢临界点温度及常规热处理工艺参数
表2-7低合金高强度结构钢牌号与性能
表2-8低碳马氏体型钢热处理工艺和力学性能
表2-9低碳马氏体钢淬火临界直径
表2-10弹簧钢化学成分
表2-11弹簧钢临界点温度及常规热处理工艺参数
表2-12轴承用钢化学成分
表2-13轴承用钢临界点温度及常规热处理工艺参数
表2-14碳素工具钢化学成分
表2-15碳素工具钢残余元素的控制
表2-16碳素工具钢临界点温度及常规热处理工艺参数
表2-17合金工具钢化学成分
表2-18合金工具钢临界点温度及常规热处理工艺参数
表2-19高速工具钢化学成分
表2-20高速钢临界点温度及常规热处理工艺参数
表2-21奥氏体型不锈钢和耐热钢化学成分
表2-22奥氏体-铁素体型不锈钢和耐热钢化学成分
表2-23铁素体型不锈钢和耐热钢化学成分
表2-24马氏体型不锈钢和耐热钢化学成分
表2-25沉淀硬化型不锈钢和耐热钢化学成分
表2-26奥氏体型不锈钢热处理工艺与性能参数
表2-27铁素体型不锈钢常规热处理工艺与性能参数
表2-28奥氏体-铁素体钢常规热处理工艺与性能参数
表2-29马氏体型不锈钢退火热处理工艺与性能参数
表2-30马氏体型不锈钢淬回火热处理工艺与性能参数
表2-31沉淀硬度不锈钢热处理工艺参数
表2-32奥氏体型耐热钢热处理工艺与性能参数
表2-33铁素体型耐热钢热处理工艺与性能参数
表2-34马氏体型耐热钢退火工艺与性能参数
表2-35马氏体型耐热钢热处理工艺与性能参数
表2-36铸造碳钢牌号和化学成分
表2-37铸造碳钢力学性能
表2-38低合金铸钢件牌号和化学成分中硫、磷含量
表2-39低合金铸钢件力学性能要求
表2-40铸造碳钢和低合金铸钢件完全退火热处理工艺
表2-41铸造不锈钢化学成分
表2-42铸造不锈钢力学性能
表2-43耐蚀铸造不锈钢热处理规范和力学性能
表2-44非标准铸造不锈钢牌号、热处理工艺、性能和应用
表2-45新型齿轮钢化学成分(质量分数,%)
表2-46典型新型齿轮钢的临界点温度和热处理工艺参数
表2-4720CrMoH渗碳淬火有效硬化层深度与碳浓度
表2-4820CrNi2MoH渗碳淬火有效硬化层深度与碳浓度
表2-49部分冷镦、冷挤压用钢热处理工艺与性能
表2-50高压锅炉用钢热处理规范
表2-51汽轮机叶片用钢热处理规范
第3章表面加热热处理
表3-1感应加热方法的分类
表3-2工件直径、合理的淬火层深度与电流频率的关系
表3-3几种典型服役条件下的零件表面硬化层深度要求
表3-4淬硬层深度与电流频率的关系
表3-5根据淬硬层深度和工件直径选择频率的依据
表3-6轴类零件表面加热比功率的选择
表3-7根据淬硬层深度选择加热时间与比功率
表3-8不同材料推荐的感应淬火温度及通常希望的表面硬度①
表3-9常用钢种表面淬火时推荐的加热温度(喷水冷却)①
表3-10部分零件感应加热表面淬火时的冷却方式及介质
表3-11几种常用钢感应加热表面淬火件炉中回火规范
表3-12感应加热回火需要的大约功率密度
表3-13各种感应回火应用的功率、频率选择
表3-14火焰淬火适用钢铁材料
表3-15用于火焰淬火的燃料气
表3-16烧嘴移动速度、气体消耗量与硬化层深度
表3-17常用材料火焰表面淬火加热温度
表3-18火焰表面淬火件回火工艺参数
表3-19激光热处理工艺参数选用原则
表3-20激光热处理工艺参数对硬化层的影响
表3-21常用典型材料的激光热处理工艺
表3-22常用钢激光热处理后的硬度
表3-23电子束表面淬火的基本工艺方法和淬硬层的组织性能
表3-24电子束淬火工艺参数
表3-2542CrMo钢电子束表面淬火效果
第4章化学热处理
表4-1常用化学热处理方法及其作用
表4-2常用结构钢的渗碳热处理规范及性能
表4-3几种有机液体的产气量
表4-4一些常用有机物质的碳当量
表4-5几种有机液体在不同温度下分解产物的组成
表4-6几种滴注剂单参数控制的最大碳势偏差①
表4-7常用吸热式气体成分(体积分数)
表4-8几种类型氮基渗碳气氛的成分(体积分数)
表4-9常用渗碳钢预备热处理工艺及热处理后硬度
表4-10气体渗碳工艺参数
表4-11液体渗碳盐浴组成及使用效果
表4-12常用固体渗碳剂组成
表4-13固体渗碳装箱及装炉
表4-14固体渗碳及渗后热处理
表4-15常用防渗碳涂料
表4-16渗碳后热处理工艺
表4-17常用渗氮钢的钢种
表4-18常用材料的渗氮温度、表面硬度和渗氮层深度范围
表4-19常用渗氮钢的调质处理工艺及调质后力学性能
表4-20常用气体渗氮工艺方法和特点
表4-21结构钢和工具钢气体渗氮工艺规范
表4-22纯铁、碳素钢的抗蚀渗氮工艺
表4-23不锈钢和耐热钢气体渗氮工艺规范
表4-24离子渗氮工艺规范
表4-25几种常用钢种的离子渗氮工艺
表4-26常用结构钢碳氮共渗处理规范及性能
表4-27常见气体碳氮共渗介质
表4-28气体碳氮共渗热处理工艺过程
表4-29结构钢碳氮共渗的盐浴成分及处理规范
表4-30几种钢液体碳氮共渗渗层深度与保温时间的关系
表4-31几种碳氮共渗后的热处理工艺及其适用范围
表4-32气体氮碳共渗常用渗剂
表4-33气体氮碳共渗工艺
表4-34保温时间对氮碳共渗层深度与表面硬度的影响
表4-3570%甲酰胺+30%尿素氮碳共渗效果
表4-36几种典型的氮碳共渗盐浴及其效果
表4-37盐浴氮碳共渗工艺
表4-38不同温度保温1.5h氮碳共渗层深度
表4-39盐浴氮碳共渗层深度与表面硬度
表4-40部分材料常用离子氮碳共渗层深度及硬度
表4-41温度对20钢、45钢和40Cr钢离子氮碳共渗层的厚度和硬度的影响
表4-42常用的粉末渗锌剂及处理工艺
表4-43常用气体渗铬介质与处理工艺
表4-44常用液体渗铬盐浴成分与处理工艺
表4-45常用固体渗铬剂成分与处理工艺
表4-46真空渗铬工艺
表4-47几种粉末渗铝剂成分与处理工艺
表4-48渗硫剂成分及工艺参数
表4-49几种气体渗硼剂与工艺
表4-50熔盐渗硼成分与工艺
表4-51几种粉末渗硼剂配方及工艺
表4-5245钢常用粉末渗硼剂成分与渗硼工艺
表4-53渗硅、钛、铌、钒、锰的方法及性能
第5章铸铁的热处理
表5-1各种铸铁名称、代号及牌号表示方法实例
表5-2灰铸铁件化学成分
表5-3灰铸铁金相组织控制范围
表5-4灰铸铁件热处理加热温度/℃
表5-5典型灰铸铁消除应力工艺处理参数
表5-6灰铸铁消除应力程度、加热温度与时间的关系
表