10T锅炉双碱法.docx
《10T锅炉双碱法.docx》由会员分享,可在线阅读,更多相关《10T锅炉双碱法.docx(18页珍藏版)》请在冰豆网上搜索。
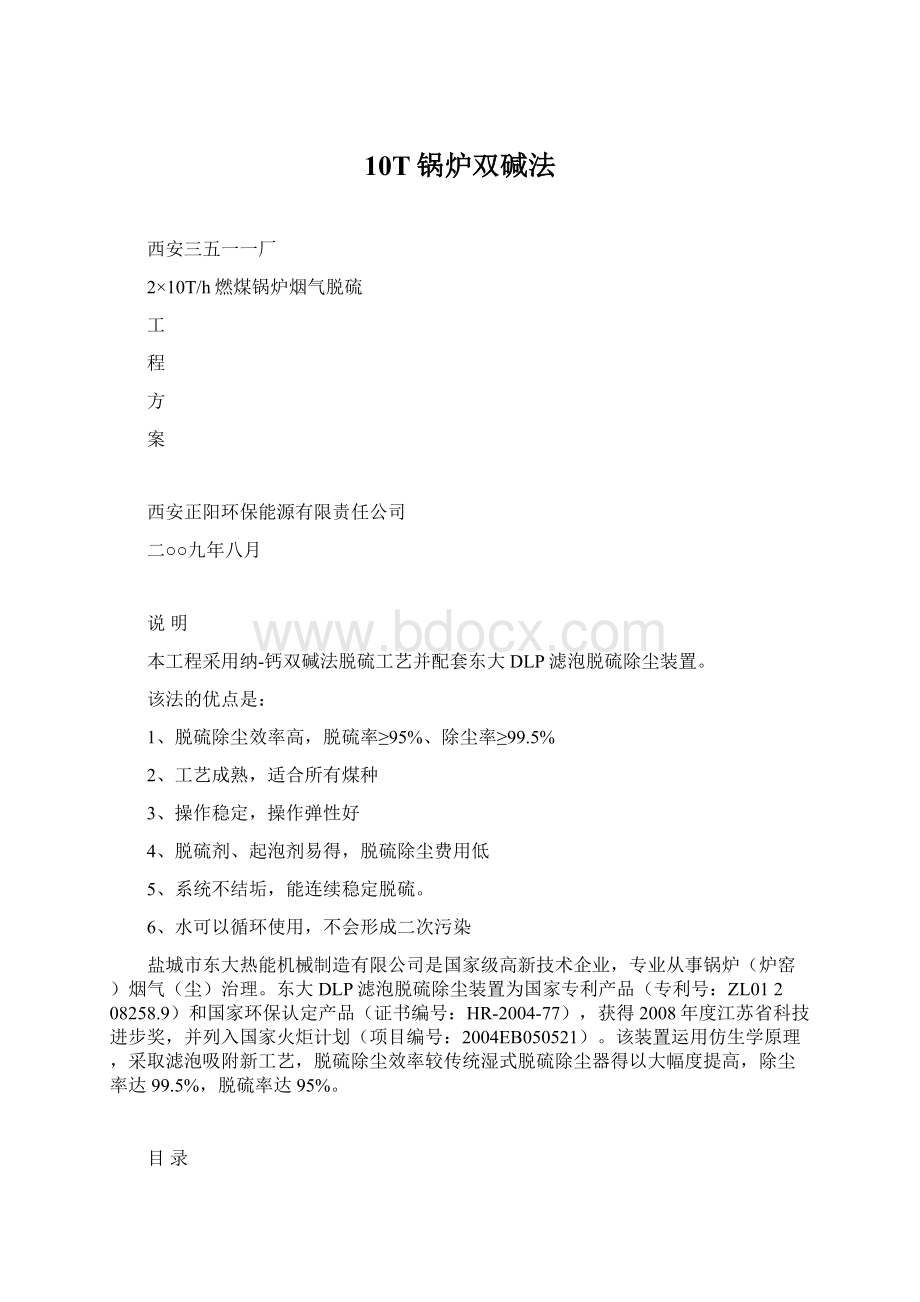
10T锅炉双碱法
西安三五一一厂
2×10T/h燃煤锅炉烟气脱硫
工
程
方
案
西安正阳环保能源有限责任公司
二○○九年八月
说明
本工程采用纳-钙双碱法脱硫工艺并配套东大DLP滤泡脱硫除尘装置。
该法的优点是:
1、脱硫除尘效率高,脱硫率≥95%、除尘率≥99.5%
2、工艺成熟,适合所有煤种
3、操作稳定,操作弹性好
4、脱硫剂、起泡剂易得,脱硫除尘费用低
5、系统不结垢,能连续稳定脱硫。
6、水可以循环使用,不会形成二次污染
盐城市东大热能机械制造有限公司是国家级高新技术企业,专业从事锅炉(炉窑)烟气(尘)治理。
东大DLP滤泡脱硫除尘装置为国家专利产品(专利号:
ZL01208258.9)和国家环保认定产品(证书编号:
HR-2004-77),获得2008年度江苏省科技进步奖,并列入国家火炬计划(项目编号:
2004EB050521)。
该装置运用仿生学原理,采取滤泡吸附新工艺,脱硫除尘效率较传统湿式脱硫除尘器得以大幅度提高,除尘率达99.5%,脱硫率达95%。
目录
1.设计原则、依据、指标及范围………………………………4
1.1设计原则……………………………………………………4
1.2设计依据……………………………………………………4
1.3设计治理目标………………………………………………5
1.4工程范围……………………………………………………5
2.脱硫工艺选择…………………………………………………6
2.1常用烟气脱硫工艺比较……………………………………6
2.2湿法脱硫工艺评价与方案选择……………………………8
3.方案确定……………………………………………………13
4.工艺流程……………………………………………………13
5.工艺设计……………………………………………………14
5.1脱硫塔系统…………………………………………………14
5.2脱硫剂制备系统……………………………………………14
5.3脱硫浆液循环处理系统……………………………………15
6.平面设计………………………………………………………15
7.基础处理………………………………………………………16
8.抗震设计………………………………………………………16
9.主要设备清单…………………………………………………16
10.系统运行费用分析…………………………………………17
1.设计原则、依据、指标及范围
1.1设计原则
1.1.1严格执行有关环境保护政策,确保锅炉烟气排放达到国家和地方标准;
1.1.2脱硫剂、起泡剂必须来源广、价格低,以降低脱硫除尘运行费用;
1.1.3不产生二次污染;
1.1.4合理进行平面布置,充分考虑物流人流通畅、管理维护方便等因素。
平面布置将经过实地勘测后,由我司提出初步意见,再与厂方协商,最后敲定。
1.2设计依据
1)《中华人民共和国环境保护法》
2)《环境空气质量标准》(GB3095)
3)《大气污染物综合排放标准》(GB16297)
4)《锅炉大气污染物排放标准》(GB13271)
5)《采暖通风和空气调节设计规范》(GBJ19-88)
6)《机械设备安装工程施工及验收规范》(TJ231-78J)
7)《工业管道工程施工及验收规范》(GBJ235-82)
8)《通风与空调工程施工及验收规范》(GBJ243-82)
9)《建筑安装工程质量检验评定标准》(通用机械设备安装工程)(TJ305-75)
10)《低压配电装置及线路设计规范》(GBJ54-83)
11)《通用用电设备配电规范》(GBJ50055-93)
13)甲方提供的资料数据。
1.2.1基础数据
表1-1单台10T/H燃煤锅炉基础数据(估算)
项目名称
单位
数值
备注
炉型
T
10
燃煤
数量
台
2
标况烟气流量
m3/h
30000
蒸汽温度
℃
400
耗煤量
T/年
10000
SO2初始浓度
mg/Nm3
1000
引风机
m3/h
30000
风压3187Pa
1.3设计治理目标
表1-2主要设计指标
脱硫率(%)
≥95%
SO2排放浓度(mg/Nm3)
≤50
脱硫系统阻力降(Pa)
<1000
1.4工程范围
1.4.1烟气脱硫除尘工艺流程的确定;
1.4.2非标设备的设计与制作;
1.4.3电气设计与安装;
1.4.4标准设备的选型与购置;
1.4.5负责土建部分工艺设计、施工;
整个工程内容可划分为:
脱硫剂制备供应系统、脱硫塔系统、氢氧化钠置换系统、脱硫浆液循环处理系统,石膏脱水系统,控制系统。
1.4.6所有设备部件的运输;
1.4.7所有设备的安装、调试;
2.脱硫工艺选择
2.1常用烟气脱硫工艺比较
近几十年来全世界研究的脱硫工艺多达上百种,但真正在工业上应用的仅十来种(见表2-1)。
表2-1常用烟气脱硫工艺比较表
序号
工艺名称
工艺原理
工艺特点
应用情况
1
石灰石/石灰-石膏湿法
利用石灰浆液洗涤烟气,使石灰与烟气中SO2反应生成亚硫酸钙,脱去烟气中的SO2,再将亚硫酸钙氧化反应生成石膏。
优点:
脱硫率高≥95%、工艺成熟、适合所有煤种、操作稳定、操作弹性好、脱硫剂易得、运行成本低、副产物石膏可以综合利用,不会形成二次污染;
缺点:
一次性投资较高。
国内外应用最为广泛,使用比例占到80%以上。
2
简易石灰石/
石灰-石膏湿法
简易湿法烟气脱硫工艺的脱硫原理和普通湿法脱硫基本相同,只是吸收塔内部结构简单(采用空塔或采用水平布置),省略或简化换热器。
优点:
投资和占地面积比较小;
缺点:
脱硫率低,约70%。
国外应用较少,国内有应用实例
3
海水脱硫法
利用海水洗涤烟气吸收烟气中的SO2气体。
优点:
脱硫率比较高≥90%、工艺流程简单,投资省、占地面积小、运行成本低;
缺点:
受地域条件限制,只能用于沿海地区。
只适用于中、低硫煤种、有二次污染。
国内外均有部分成功应用实例(深圳西部电厂)
4
旋转喷雾
干燥法
将生石灰制成石灰浆,将石灰浆喷入烟气中,使氢氧化钙与烟气中的SO2反应生成亚硫酸钙。
优点:
工艺流程比石灰石-石膏法简单,投资也较小。
缺点:
脱硫率较低(约70-80%)、操作弹性较小、钙硫比高,运行成本高、副产物无法利用且易发生二次污染(亚硫酸钙分解)。
国内外均有少数成功应用实例(黄岛电厂)
5
炉内干法
喷钙
直接向锅炉炉膛内喷入石灰石粉,石灰石粉在高温下分解为氧化钙,氧化钙与烟气中的SO2反应生成亚硫酸钙。
优点:
工艺流程比石灰石-石膏法简单,投资也较小。
缺点:
脱硫率较低(约30-40%)、操作弹性较小、钙硫比高,运行成本高、副产物无法利用且易发生二次污染(亚硫酸钙分解)。
国内外均有少数成功应用实例(抚顺电厂)
6
炉内喷钙-尾部增湿法
直接向锅炉炉膛内喷入石灰石粉,石灰石粉在高温下分解为氧化钙,氧化钙与烟气中的SO2反应生成亚硫酸钙。
为了提高脱硫率,在尾部喷入水雾,增加氧化钙与烟气中的SO2反应活性。
优点:
工艺流程比石灰石-石膏法简单,投资也较小。
缺点:
脱硫率较低(约70%)、操作弹性较小、钙硫比高,运行成本高、副产物无法利用且易发生二次污染(亚硫酸钙分解)。
国内外均有少数成功应用实例(抚顺电厂)
7
烟气循环
流化床
在流化床中将石灰粉按一定的比例加入烟气中,使石灰粉在烟气当中处于流化状态反复反应生成亚硫酸钙。
优点:
钙利用率高、无运动部件、投资省。
缺点:
脱硫率较低(≤80%)、对石灰纯度要求较高、国内石灰不易保证质量、烟气压头损失大、由于加料不均匀会影响锅炉运行。
国内外均有少数成功应用实例
8
活性炭法
使烟气通过加有催化剂的活性炭,烟气中的SO2经催化反应成SO3并吸附在活性炭中,用水将活性炭中的SO3洗涤成为稀硫酸同时使活性炭再生。
优点:
脱硫率较高(≥90%)、工艺流程简单、无运动设备、投资较省、运行费用低。
缺点:
副产物为稀硫酸,不适宜运输,只能就地利用消化。
活性炭定期需要更换。
国内外均有少数成功应用实例(四川豆坝电厂)
9
电子束法
将烟气冷却到60℃左右,利用电子束辐照;产生自由基,生成硫酸和硝酸,再与加入的氨气反应生成硫酸铵和硝酸铵。
收集硫酸铵和硝酸铵粉造粒制成复合肥。
优点:
脱硫率较高(≥90%)、同时脱硫并脱硝,副产物是一种优良的复合肥,无废物产生。
缺点:
投资高,因设备元件不过关,大型机组应用较困难。
国内外均有少数成功应用实例(四川成都热电厂、北京热电厂)
10
脉冲电晕法
将烟气冷却到60℃左右,利用高压电场辐照;产生自由基,生成硫酸和硝酸,再与加入的氨气反应生成硫酸铵和硝酸铵。
收集硫酸铵和硝酸铵粉造粒制成复合肥。
优点:
脱硫率较高(≥90%)、同时脱硫并脱硝,副产物是一种优良的复合肥,无废物产生。
缺点:
投资高,因设备元件不过关,大型机组应用较困难。
尚处于试验当中。
2.2湿法脱硫工艺评价与方案选择
2.2.1影响脱硫效率的因素分析
本公司长期致力于湿法烟气脱硫除尘的研究,从理论和实践两个方面总结出影响湿法烟气脱硫效率的因素有以下几条:
2.2.1.1界面浓度
脱硫液界面浓度应愈低愈好。
因此连续供给的脱硫液成为必须,可以通过流动的水膜、喷射的雾滴、移动的滤泡来实现。
2.2.1.2液气比
要实现脱硫液对烟气中二氧化硫的最大吸收,必须有充足的吸收液。
理论上认为当液气比达到15时脱硫率可接近100%,但是同时带来脱硫除尘设备经济性问题,以及脱硫产物的处理。
事实上,我们希望最小的液气比达到最大的吸收效果。
这就要求脱硫液在除尘脱硫塔内要实现最大比表面积,而实现最大比表面积的方法有三种即:
A、水膜。
由于水膜的厚度可小至几个微米级,单位体积的脱硫液的表面积由于厚度的降低而放大。
B、水雾。
使单位体积的脱硫液雾化成更加微小的颗粒。
C、水泡。
由于水泡的膜厚仅为几微米以下,且滤泡中包有烟气,泡膜内、外层都能充分与烟气接触,因而是实现脱硫液最大比表面积的最佳途径。
2.2.1.3吸收剂
由于气体溶质与溶剂发生化学反应,因而吸收剂对吸收过程有很大的影响,不同的吸收剂与SO2反应的速度也不一样。
好的吸收剂使SO2进入吸收液后很快因化学反应而消耗掉。
使吸收液的平衡分压降低,甚至可以为零,从而使吸收推动力大大增加,吸收速率大为提高。
选择好的吸收剂对脱硫效率的影响是显著的,常用的吸收剂有CaO、Ca(OH)2、NaOH、Na2CO3、NH3H2O等。
2.2.1.4吸收剂用量
吸收剂的种类和进塔浓度由设计者选定,而吸收剂用量和出塔溶液中吸收质浓度需通过计算确定。
充足的吸收剂用量,是保证吸收反应充分进行的前提。
由于常用钙基脱硫剂,我们常用钙硫比来表述吸收剂用量。
2.2.1.5烟气与吸收剂吸收反应时间
毫无疑问,由于吸收速率及化学反应速度的关系,必须使含硫烟气与吸收剂有充足的吸收反应时间,才能确保吸收反应的进行,因此烟气在吸收塔内的停留反应的时间,必须依上述几个因素确定,一般为2-5m/s。
在设计时,根据烟气流量,吸收反应的时间就决定了吸收塔的高度和烟气的速度。
而烟气流速则因不同的吸收塔结构要求又有所不同,设计时应充分考虑。
2.2.1.6吸收塔结构
同样的吸收剂在不同结构的吸收塔中吸收效果有所不同,因此,应充分考虑吸收塔结构对脱硫效率的影响。
有填料层的吸收塔结构通常会优先考虑,但是,有填料层吸塔式旋流板结构的除尘脱硫装置在脱硫除尘过程中由于有固态物产生,常常堵塞填料层,造成装置运行阻力的增加,并严重影响脱硫除尘效果。
而滤泡腔体则突破了传统结构设计,使脱硫塔结构十分简单,不存在固态物堵塞的可能,因此,与有填料层的吸收塔相比具有明显的结构上的优势。
2.2.2常用脱硫吸收剂的比较
湿法脱硫是一种化学吸收反应,吸收剂对吸收过程有很大的影响,不同的吸收剂与SO2反应的速度也不一样,常用的吸收剂有:
氢氧化钠或碳酸钠、氧化镁、钠-钙双碱、氨、海水、石灰乳等。
2.2.2.1氢氧化钠(NaOH)或碳酸钠(Na2CO3)作为吸收剂脱硫,存在如下诸多问题:
A、如果将脱硫后的产物亚硫酸钠回收利用,存在流程过长、回收费用过高、副产品无销路等问题;
B、脱硫剂消耗量大,脱硫成本很高;
C、增加水处理费用——本项目钠碱脱硫剂脱硫后,每年将产生大量亚硫酸钠(Na2SO3),如直接排放,大量具有还原性能的SO32-将使环境水体的COD大大升高,势必造成对环境水体的严重污染,这是绝对不允许的;若作污水处理后排放,则处理费用可能不低于烟气脱硫费用,企业难以承受。
2.2.2.2氧化镁作为吸收剂脱硫:
由于氧化镁来源有限,且氧化镁脱硫后,如果不将脱硫剂循环使用而将脱硫产物直接排放,必将对环境水体造成严重污染;如果象国外氧化镁脱硫那样循环利用脱硫剂,则流程很长,设备繁多,投资极大,占地面积大,因此,本项目不宜采用氧化镁法;
2.2.2.3海水作为吸收剂脱硫:
海水通常呈碱性,具有天然的酸碱缓冲能力及吸收SO2的能力,当SO2被海水吸收后,再经处理氧化为无害的硫酸盐而溶于海水。
硫酸盐是海水的天然成分,经脱硫而流回海洋的海水,其酸性成分只会稍有提高,流入海洋后这种差异就会消灭,但海水脱硫必须以工厂座落于海边为前提。
2.2.2.4氨作为吸收剂脱硫:
氨是一种良好的碱性吸收剂,其吸收反应是气——气反应,吸收反应速度快,反应完全,但氨的价格相对于低廉的石灰石来说是太高了。
过高的运行成本使氨法脱硫的推广应用受到极大影响,在脱硫应用中极少。
2.2.2.5钠-钙双碱法脱硫:
用NaoH作吸收剂脱硫,用Ca(OH)2作为NaoH的再生剂。
其主要化学反应及反应式如下:
(1)吸收2NaOH+So2→Na2So3+H2O
(2)再生Na2So4+Ca(OH)2→2NaOH+CaSo4
2.2.2.6石灰乳作为吸收剂脱硫:
脱硫产物是硫酸钙(石膏),可容易地从脱硫系统中分离出来,不会对环境水体造成污染,不存在脱硫废水的处理问题;这种脱硫剂是价格低廉的石灰石,脱硫成本低,企业能承受,且这种方法技术成熟,可靠性高。
2.2.3常见吸收塔结构比较
双碱法脱硫工艺,选择不同结构的吸收塔对脱硫除尘效果、操作的方便性及使用寿命均有十分重要的影响。
在烟气湿法脱硫除尘技术发展进程中,先后出现过旋风水膜吸收塔、文丘里洗涤吸收塔、旋流塔板吸收塔、滤泡腔体吸收塔等,这些不同的吸收塔各具特点。
2.2.3.1旋风水膜吸收塔:
适合用于处理烟气量大,含尘浓度高的场合。
但对飘尘的捕集能力差,而且使用水膜脱硫,含硫气体不能充分与吸收剂接触,脱硫效率低,使用脱硫剂量大。
2.2.3.2文丘里洗涤吸收塔:
利用文丘里管高压引射雾化原理,使脱硫液雾化成微小颗粒,从而增大脱硫液比表面积。
增加脱硫液与烟尘的接触能力。
然而,当脱硫液被雾化成微小颗粒后,本身极易被引风引出,而成为事实上的排放,控制雾化微料在80μm以上时,能大大减少被引出的机会,但脱硫效率差。
2.2.3.3旋流塔板吸收塔:
它解决了文丘里与旋风水膜的弱点,气液接触面大,传质效率高,脱硫效果有较大提高;但由于塔内结构中含有填料层,脱硫产物易在塔内形成结垢和堵塞,需经常清洗、更换塔层,使用效果受到极大影响。
2.2.3.4滤泡腔体吸收塔:
它利用仿生学原理,由滤泡发生器在吸收塔腔体内部产生大量的滤泡。
这些滤泡具有很大的比表面积和很强的吸附性以及粘性。
当烟气从这些滤泡中通过时,大量的滤泡提供了充足的传质面积,当烟气从滤泡中通过时烟气中的SO2与滤泡中的碱性介质发生反应被吸收脱除。
3.方案确定
根据上述分析,本工程拟采用纳-钙双碱法脱硫工艺,以氢氧化钠为吸收剂,氢氧化钙为氢氧化钠的再生剂,并采用滤泡吸收塔。
结合工程的实际情况,提出以下设计方案:
2台10T/H锅炉各配置一座脱硫塔,选用DLP-I-2/10,2台脱硫装置共用一座脱硫浆液循环池及其它辅助系统。
4.工艺流程
锅炉烟气经旋风段进入DLP滤泡吸收塔腔体。
当烟气从滤泡中通过时,烟气中的SO2与滤泡中的碱性介质发生反应被吸收脱除。
其工艺流程如下:
滤泡脱硫
沉降室
烟气
净空气排入大气
烟气调质
滤泡发生器
沉淀池
出渣
起泡剂
回水池
氢氧化钙
回水
氢氧化钠
补水
5.工艺设计
5.1脱硫塔系统
5.1.1DLP-I-2/10吸收塔:
直径2.2m,高6.5m,塔内主要部件均采用316L不锈钢制作。
5.1.2出口烟道:
现场配制。
5.2脱硫剂制备系统
本方案采用氢氧化纳作脱硫剂,氢氧化钙为再生剂要求粒度小于150目,CaO的含量大于80%。
袋装氢氧化钠用人工送入料斗,经螺旋给料机送进溶液池;同时向溶液池加入补充水。
通过调节螺旋给料机速度控制氢氧化钠加入量,浆液浓度由加入溶液池的氢氧化钠和补充水量予以控制,制浆过程连续进行。
制备好的浆液通过泵送入脱硫循环池。
溶液池:
钢筋砼,长6米、宽4米、高1.5米,地下建筑(高出地面0.5m);
5.3脱硫浆液循环处理系统
5.3.12台脱硫除尘装置配置三台脱硫循环泵,一台备用。
5.3.2脱硫石膏的处理
在脱硫循环池的主沉淀区采用原除渣系统,沉淀池中的硫酸钙混合物通过除渣系统排出,脱水后脱硫石膏可作为水泥厂的原料,剩下的废水经多级沉淀后回到清水区。
在脱硫循环池的清水区配置1台清水泵,用于补充脱硫循环池中损失的水份.
5.3.3PH值自动控制
脱硫循环池内脱硫液的PH值采用国外进口PH自动控制系统进行检测与控制,当检测的PH值小于给定PH值时,自动增大氢氧化钠溶液进入循环池流量;反之,当检测的PH值大于给定PH值时,自动减小进入循环池氢氧化钠溶液流量。
6.平面设计
整个脱硫系统按功能可分为氢氧化钠制备系统、脱硫塔系统、脱硫浆液循环处理及再生系统、石膏脱水系统和控制系统。
主要设备和构筑物有:
氢氧化钠料斗、振动给料装置、溶液池及搅拌器、泵、脱硫塔及出口烟道、脱硫循环池及搅拌器、脱硫循环泵、除雾器、控制系统及设备基础。
平面布置按工艺流程,根据现场情况进行设计。
7.基础处理
整个系统除设备基础外,还有溶液池、脱硫浆液循环池等土建内容。
8.抗震设计
按《建筑抗震设计规范》(GBJ11-89)执行。
9.主要设备清单
序号
设备名称
数量
备注
1
集料斗
2座
2
振动给料装置
2台
3
搅拌机
2台
4
溶液泵
2台
5
溶液池
2座
6
脱硫塔体
2座
7
脱硫循环泵
3台
一用一备
8
塔内除雾器
2台
9
氧化压缩风机
2台
10
氧化空气均分装置
2台
11
脱硫循环池
1座
12
冲洗泵
2台
13
PH控制器
1台
含传感器
14
控制柜
1台
10.系统运行分析
10.1本方案达到的主要技术经济指标
序号
项目名称
指标
备注
1
烟气流量
60000m3/h
2台
2
烟气温度
150℃
3
SO2排放浓度
<50/Nm3
4
NaoH
3.6kg/h
5
SO2脱除量
57kg/h
6
Ca/S
1.05
7
石灰粉用量
65.5kg/h
纯度按80%
8
石膏产量
153.2kg/h
9
耗水量
2.415t/h
10.2主要工艺计算及脱硫综合成本分析
10.2.1主要工艺计算
10.2.1.1烟气中SO2含量
进入脱硫塔前的烟气温度按145℃进行计算。
烟气中的SO2含量为:
M=60000Nm3/h×1000mg/Nm3=60kg/h
10.2.1.2脱硫量
根据要求,SO2排放从1000mg/Nm3减为50mg/Nm3即为达标,经计算为脱硫率95%,则实际脱去二氧化硫量为:
60kg/h×95%=57kg/h
实际排放量为:
60-57=3kg/h
10.2.1.3氢氧化钠用量
Y1=57×40/64=35.625kg/h
按实际消耗量的10%计算,则氢氧化钠用量为3.6kg/h。
需CaO量
Y2=57×1.05×56/64=52.4kg/h
10.2.1.4每小时需脱硫液量
该脱硫系统要求脱硫率达95%,另液气比高、脱硫除尘效果好,故液气比取2L/M3。
每小时需脱硫液量为:
Qy=60000m3/h×2L/M3=120T/h
单台10T/H锅炉每小时需脱硫液量为:
Qy=30000m3/h×2L/M3=60T/h
10.2.1.5脱硫液池容积
按一小时循环一次计算:
Qy
则脱硫液池容积V=×η=120M3
ρ
10.2.1.6石膏生成量计算
按全部硫100%转化为石膏,则最大石膏生成量为:
SO2+Ca(OH)2+1/2O2CaSO4·2HO2
172
Mmax=57×=153.2kg/h
64
10.2.2脱硫综合成本
10.2.2.1
氢氧化钠用量3.6kg/h
按市价:
2500元/T计,成本为3.6×2.5=9元/h
石灰耗量
纯度按80%计,Mcao=65.5kg/h
按市价:
230元/T计,成本为65.5×0.23=15.1元/h
10.2.2.2循环水耗量
由生成物石膏带走的水M153.2×10%=15.32kg/h
脱硫塔内蒸发水分按循环水量的2%计:
M2=120T×2%=2400kg/h
总消耗水M=M1+M2=15.32+2400=2415kg/h
按2元/T计,成本为2.415×2=4.83元/h
10.2.2.3起泡剂耗量
使用AE起泡剂按循环水量的十万分之一计算,起泡剂用量为:
MQ=0.4kg/h
按市价6000元/T计,则起泡剂成本为
MQ×6元/kg=2.4元/h
10.2.2.4电费
脱硫系统总功耗为W=75kw
每小时耗电估算:
D=η×W=0.8×75=56KWh
按0.7元/KWh计算:
电费为0.56×56=31.36元/h
上述费用总计,脱硫总成本为:
TS=
(1)+
(2)+(3)+(4)=62.69元/h