药用包装材料工艺汇总.docx
《药用包装材料工艺汇总.docx》由会员分享,可在线阅读,更多相关《药用包装材料工艺汇总.docx(9页珍藏版)》请在冰豆网上搜索。
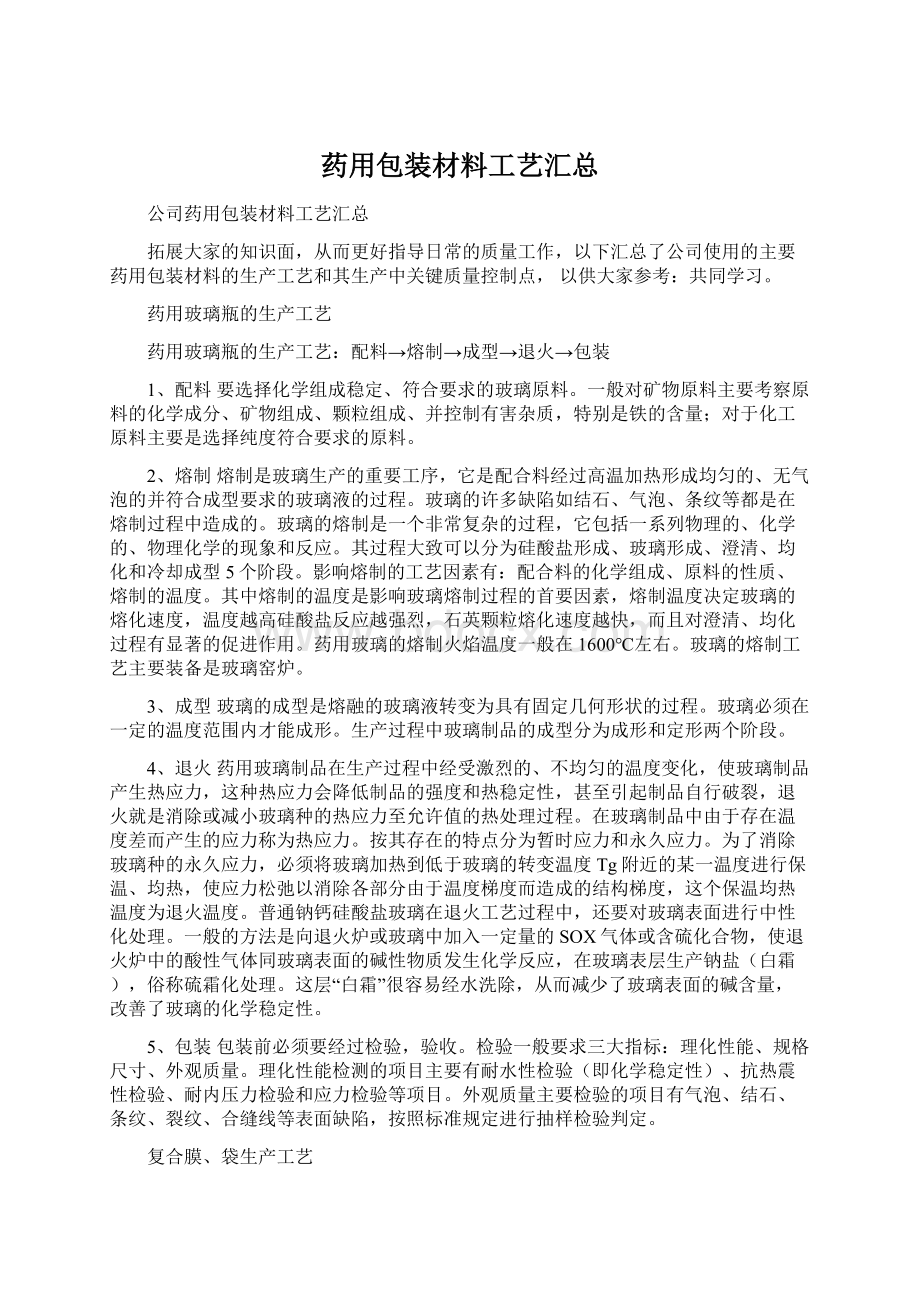
药用包装材料工艺汇总
公司药用包装材料工艺汇总
拓展大家的知识面,从而更好指导日常的质量工作,以下汇总了公司使用的主要药用包装材料的生产工艺和其生产中关键质量控制点,以供大家参考:
共同学习。
药用玻璃瓶的生产工艺
药用玻璃瓶的生产工艺:
配料→熔制→成型→退火→包装
1、配料要选择化学组成稳定、符合要求的玻璃原料。
一般对矿物原料主要考察原料的化学成分、矿物组成、颗粒组成、并控制有害杂质,特别是铁的含量;对于化工原料主要是选择纯度符合要求的原料。
2、熔制熔制是玻璃生产的重要工序,它是配合料经过高温加热形成均匀的、无气泡的并符合成型要求的玻璃液的过程。
玻璃的许多缺陷如结石、气泡、条纹等都是在熔制过程中造成的。
玻璃的熔制是一个非常复杂的过程,它包括一系列物理的、化学的、物理化学的现象和反应。
其过程大致可以分为硅酸盐形成、玻璃形成、澄清、均化和冷却成型5个阶段。
影响熔制的工艺因素有:
配合料的化学组成、原料的性质、熔制的温度。
其中熔制的温度是影响玻璃熔制过程的首要因素,熔制温度决定玻璃的熔化速度,温度越高硅酸盐反应越强烈,石英颗粒熔化速度越快,而且对澄清、均化过程有显著的促进作用。
药用玻璃的熔制火焰温度一般在1600℃左右。
玻璃的熔制工艺主要装备是玻璃窑炉。
3、成型玻璃的成型是熔融的玻璃液转变为具有固定几何形状的过程。
玻璃必须在一定的温度范围内才能成形。
生产过程中玻璃制品的成型分为成形和定形两个阶段。
4、退火药用玻璃制品在生产过程中经受激烈的、不均匀的温度变化,使玻璃制品产生热应力,这种热应力会降低制品的强度和热稳定性,甚至引起制品自行破裂,退火就是消除或减小玻璃种的热应力至允许值的热处理过程。
在玻璃制品中由于存在温度差而产生的应力称为热应力。
按其存在的特点分为暂时应力和永久应力。
为了消除玻璃种的永久应力,必须将玻璃加热到低于玻璃的转变温度Tg附近的某一温度进行保温、均热,使应力松弛以消除各部分由于温度梯度而造成的结构梯度,这个保温均热温度为退火温度。
普通钠钙硅酸盐玻璃在退火工艺过程中,还要对玻璃表面进行中性化处理。
一般的方法是向退火炉或玻璃中加入一定量的SOX气体或含硫化合物,使退火炉中的酸性气体同玻璃表面的碱性物质发生化学反应,在玻璃表层生产钠盐(白霜),俗称硫霜化处理。
这层“白霜”很容易经水洗除,从而减少了玻璃表面的碱含量,改善了玻璃的化学稳定性。
5、包装包装前必须要经过检验,验收。
检验一般要求三大指标:
理化性能、规格尺寸、外观质量。
理化性能检测的项目主要有耐水性检验(即化学稳定性)、抗热震性检验、耐内压力检验和应力检验等项目。
外观质量主要检验的项目有气泡、结石、条纹、裂纹、合缝线等表面缺陷,按照标准规定进行抽样检验判定。
复合膜、袋生产工艺
复合膜的组成:
基材、层合胶黏剂、阻隔材料、热封材料、印刷与保护层涂料。
常用的复合膜结构为:
表层/黏合层1/中间阻隔层/黏合层2/内层热封层。
复合膜的工艺流程:
印刷→干法复合→挤出复合→固化→分切→制袋→包装
1、印刷控制要点:
张力控制、温度及速度控制、油墨使用调整与控制。
2、干法复合干法复合是指用各种涂复法将胶黏剂溶液涂布在薄膜基材表面后通入干燥烘道内使胶黏剂溶剂挥发,在薄膜表面形成不含溶剂的均匀胶黏剂层(厚约1.5至5um),再在复合部与第二基材复合。
控制要点:
温度的设定、张力控制、速度控制、胶的调配使用及涂布量控制、固化程度控制。
3、挤出复合控制要点:
设定各工艺系数、涂布量控制等。
4、分切控制要点:
张力和梯度的控制、压力控制、纠偏及尺寸控制、速度控制、成品表面质量控制。
5、制袋控制要点:
热封温度的设定与控制、张力的设定和调整、切刀调整、速度调节。
复合膜、袋的主要检测项目有外观尺寸,密封阻隔性能(水蒸气透过率、气体透过率),机械性能(剥离强度、热合强度、拉断力和断裂伸长率)、卫生性能(残留量、蒸发残渣、高锰酸钾消耗量和重金属含量、二氨基甲苯的检测、微生物数)和其他性能(耐压性能、渗透检测、摩擦系数、耐热性、附着力、跌落试验、撕裂力、抗冲击性能试验、抗针孔强度、耐油脂性、相容性试验)。
铝箔的生产工艺
药用铝箔(俗称PTP铝箔)一般有保护层(印刷层)铝箔层(印刷层)黏合层等组成,但最基本的组成必须有保护层、铝箔层、黏合层。
铝箔的生产需要通过铝箔印刷机、涂布机、分切机、包装机等设备联合作业才可以完成该材料的生产过程。
生产工艺:
备料→印刷→烘干→OP涂布→烘干→VC涂布→烘干→分切→内包→外包→入库
彩色药用PTP铝箔的开发生产,主要是利用药用PTP铝箔在生产过程中涂布保护剂和黏合剂这一特点,将各种颜色的颜料或染料均匀地分散到保护剂和黏合剂体系中,使药用PTP铝箔的保护层和黏合层呈现不同的色彩。
生产彩色药用PTP铝箔的主要问题是颜料原料的选择。
由于药用PTP铝箔是用于药品,一次性医用品及某些食品的包装,所选择的颜料一定要对人体无害,并且在保护层和黏合层中状态要稳定、耐溶剂、耐迁移性要好,不会污染所包装的药品、医用品或食品。
此外,由于药用PTP铝箔在涂布、印刷及泡罩包装过程均需高温加热,所以对颜料的耐热性要求也比较高。
不合格的PTP铝箔产品具体主要表现为以下几个方面的质量问题:
1、不涂印刷层保护剂(OP保护层)未按标准生产
这是最常见,也是最突出的质量问题。
在铝箔表面印刷文字图案后涂保护层,其目的在于①防止表面的油墨层磨损脱落,同时提高泡罩时的耐热性。
②防止PTP铝箔在收卷时外层油墨与内层的胶黏剂接触而造成药品被污染。
③防止铝箔表面的自身氧化变质。
如果供应商不涂OP保护层,结果造成药品生产企业在泡罩热封时候经常发现印刷文字图案模糊不清,容易脱墨。
简单的判定方法是:
裁一块PTP铝箔,然后用打火机对OP面进行烧烤几秒钟,如发现OP面无变化,或有黑色烟渍,一经擦拭即脱落,表示是没有涂OP保护层的不合格产品。
如发现OP面变黄,并出现像光环一样的花纹,经擦拭不会脱落,表示为涂了OP保护层的产品。
一般OP涂布量达到(1±0.5)g/m2
2、聚氨酯胶黏剂(VC胶黏剂)黏合层不均匀
黏合面VC剂涂层是否均匀,有无漏涂,将直接影响泡罩包装的封合质量,即密封性能。
简单判定方法:
在光线充足的地方,用肉眼观察,如发现有清晰线状的直线条纹,或非常短的间断或不间断的直线横纹,即为不合格产品。
3、针孔度超标
PTP铝箔针孔是因为穿透性缺陷,影响铝箔的阻隔性(阻气性、阻湿性、阻光性),使被包装的药品受氧气、水蒸气或光线的影响而降低药效,严重时甚至变质不能使用,简单方法判定:
对着光线充足的地方用肉眼观察有无针孔漏光或用针孔检查台检查。
4、印刷质量达不到要求
常见的问题是印字模糊不清,印刷错位特别是套印。
铝箔的主要检测项目:
外观、宽度和厚度、针孔度、保护层的耐热性、胶黏剂的涂布量检测、胶黏剂的热封强度、PTP铝箔耐破裂强度、菌检及化学性能测定、异常毒性等。
PVC的生产工艺
PVC硬片主要由聚氯乙烯树脂添加一定的加工助剂,通过挤出、压延等加工方法生产出来的符合药用要求的一种包装材料。
PVC硬片的原料主要有PVC树脂、稳定剂、加工助剂、增强剂、润滑剂、增塑剂等。
1、由于PVC硬片有安全方面的要求,因此选用的PVC树脂的VCM含量必须小于5ug/cm2
2、稳定剂稳定剂的作用是阻止聚氯乙烯在高温下分解,使加工过程正常进行。
PVC加工所用的热稳定剂主要是有有机锡类,但PVC硬片只能用硫醇甲基锡和辛基锡。
3、增强剂PVC塑料有一个很大的缺点就是它的脆性,这将阻碍它的使用。
为了改善它的脆性,必须在加工过程中加入增强剂(也称抗冲改性剂),提高它的抗冲击强度,保证在二次加工中的正常使用。
目前国内主要使用的抗冲改性剂是MSB(甲基丙烯酸甲酯-丁二烯-苯乙烯共聚物)。
配方PVC硬片主要由PVC树脂、助剂组成,实际上PVC硬片中含有90%左右的PVC树脂,助剂只是占很少一部分,具体成分如下:
PVC树脂,88%至92%;稳定剂,1.5%;增强剂,4.5%;加工助剂,1%至1.5%;增塑剂,0至1%;润滑剂,1.5%至2%。
所有配方中的原料选用都要符合药用的要求。
所以制药企业在确定由药品包装材料生产企业提供PVC硬片前,必须进行稳定性和相容性试验,一旦确定应与药品包装材料生产企业协定不能随意改变PVC硬片的原料和配方。
PVC硬片生产工艺主要有压延法和挤出法。
1压延法工艺流程。
PVC树脂和助剂按配比加入高速搅拌釜中捏合,待温度升至100至120℃后卸入冷却搅拌釜中,冷却至50至80℃后卸入预混料中间槽,预混料经挤出机在120至180℃温度下预塑化成熔融胶块,再在二辊炼塑机上进一步塑化,完全塑化的熔融胶块通过带式输送机加入压延机成型,成型温度为190至210℃,引离辊将成型的片材从压延机最后一只辊筒剥离,片材再经冷却、收卷后,用分切机裁切成各种不同规格的产品,片材厚度是通过调节压延机辊筒间隙来实现的。
2挤出法工艺流程。
预混料配制的工艺和压延法一致,片材成型是经挤出机和模头挤出成型,再冷却、收卷,分切成各种不同规格的产品。
片材厚度是通过调节模唇间隙来实现的。
PVC硬片生产的主要设备有高速捏合机、挤出机、炼塑机、四滚压延机、分切机等。
PVC硬片检测项目和检测设备
检测项目
检测设备
厚度
千分卡
宽度
钢直尺
拉伸强度
拉力试验机
落球冲击破碎率
落球冲击试验机
加热收缩率
电热恒温干燥箱
剥离力
热封仪、拉力试验机
水蒸气透过量
调温调湿箱
氧气透过量
气体透过率测试仪
涂布量
电光分析天平
卫生性能
气相色谱仪、箱式电阻炉等
细菌检验
生化培养箱、压力蒸汽消毒器等
异常毒性
---------
扭断式防盗螺旋铝盖
对于扭断式防盗螺旋铝盖的总体要求是密封性能要好,开启方便、清洁卫生、外形新颖美观、有特殊行业要求的还要有耐清洗、耐高温的要求。
其特点是使用方便,可以按不同的剂量分次使用,里面配以不同的密封性材料如:
橡胶塞、胶垫或PE、PVC塑垫等。
它的结构是在铝的圆周上做成6-8个等分的连接点,连接点宽度约0.8mm左右,同时滚上1-2条雷司便于拧旋,通过瓶口封盖机将铝盖封上并制成螺纹(因铝材较软,容易与螺纹瓶口一起成型)。
当使用时,延逆时针方向拧盖,铝盖的上部分沿着螺纹旋转,将铝盖下口部分的几个连接点扭断,达到开启目的,因这种瓶盖一次性扭断,所以又称防盗盖。
它的缺点是对铝盖的材质要求较高,如果过软,扭断力不容易掌握或扭不断,铝材过硬又给铝盖加工带来不便;此外,铝盖的印刷也有一定的要求,对图案的对中性和涂层牢度均有严格要求。
生产工艺:
制版印刷→铝盖冲压成型→铝盖滚花→清洗→检验→封袋→装箱
制版印刷的好坏直接关系到该类产品的生产质量;铝盖冲压时应有较好的定位基准和定位手段,以防铝盖中心和印刷中心的不一致;铝盖的滚花工艺也相当重要,滚刀应经常修磨,保证铝盖圆周方向的连接点均匀,接口处间隙清晰。
防盗螺旋铝盖的清洗工艺与普通铝盖清洗相同,主要是洗掉铝盖表面的油污和铝屑。
主要生产设备:
冲床、滚压机、清洗槽、脱水机、烘箱。
产品标准GB/T14803-1993《包装容器扭断式铝防盗瓶盖》
检测项目
检测设备
检测方法
尺寸
0-125mm游标卡尺
用测量卡胶将被测部位卡住,以不落下为准
外观
目测及手感,视其印刷质量及瓶盖口是否有毛刺
表面涂膜
涂膜外观用目测,涂膜硬度按GB/T6739-1996《涂膜硬度铅笔测定法》的规定检测
密封性能
轧盖机、密封试验仪
常压瓶盖试验:
在瓶中装入浓度为75%的染色酒精至标注容量,将瓶盖封装后,在常温清水中倒置8h后观察其密封性。
承压瓶盖试验:
瓶盖在适用的瓶口上封装,置入密封试验仪中,在500kpa气压下保压1分钟,观察瓶口有无气泡溢出。
开启性能
扭力仪、封盖装置
将瓶盖及衬垫或胶塞分别盖在相应的玻璃瓶上,用轧盖机封盖后,用扭力仪测定扭断时的力矩。
塑料瓶和塑料瓶盖
药用塑料瓶(盖)的配方是由主要原料聚合物和少量辅助原料(助剂)所组成。
1、聚乙烯(PE)聚乙烯是由乙烯单体聚合而成。
根据其制法与结构性质不同可分为低密度(高压)聚乙烯(密度为0.910-0.935g/cm2)和高密度(低压)聚乙烯(密度为0.935-0.965g/cm2)。
聚乙烯树脂无毒、无色、无味、无臭。
聚乙烯的密度主要是由聚乙烯的分子链结构、结晶度决定的。
聚乙烯分子链中支链数越少,结晶度越高,密度越大,随着密度的增加,材质硬度增加,气密性提高,水蒸气渗透性下降,透明性能下降,抗应力破裂性能减弱。
聚乙烯化学稳定性好,不受强酸,强碱和大多数溶剂的影响,它耐寒性,耐磨性,阻湿性较好,但阻味性、耐油性较差,高密度聚乙烯(HDPE)的耐油性稍好一些。
2、聚丙烯(PP)聚丙烯是由丙烯单体聚合而成的,它无毒、无色、无味、无臭。
密度为(0.900-0.915g/cm2),是最轻的塑料。
与HDPE相比,屈服强度,抗张强度大、硬度高、弹性率也高。
抗应力破裂性能优越。
除了热的芳香族或鹵化物溶剂能使它软化外,聚丙烯的化学稳定性好,包括能耐强酸,强碱和大多数有机物。
聚丙烯气密性,蒸汽阻隔性能优良,甚至优于HDPE,它的熔点高达175℃,特别适用于制作需要高温消毒灭菌的塑料瓶。
聚丙烯主要缺点是透明性差,耐寒性差,低温时很脆。
为降低脆性,生产中在普通级的PP料中掺入一定比例的PE等原料。
塑料瓶的生产工艺:
分别称、配料→混合→贮存、送料→加料→塑化→注射→吹型→脱瓶→火焰处理→内包装→外包装
1)配合料的制备工艺由于药用塑料瓶的质量要求高,因此原料配制成为制瓶工艺过程中必须严格控制的首要环节。
配料包括原料的预处理、称量、混合、输送等。
首先,应该稳定原料牌号、规格和产地。
进厂原、辅料经检验合格方可使用。
有时原料因运输、装卸而受潮或混入机械杂质,这时就需采取干燥、过筛、除铁、分拣等措施。
如果采用聚碳酸酯(PC)、聚酯(PET)等作主原料,则必须制定严格的干燥制度,以保证它的成型工艺。
其次,按配方原料准确称量,进厂袋装或桶装原料一般虽有规定的质量,但为保证准确,有必要进行复称。
要注意称量设备磅秤、电子称大小、形式、自动化程度及精度。
随后,多种原料按一定的程序依次加入混合机中,在一定时间内完成混合,特别注意的是在更换配方或生产有色瓶、透明瓶时,必须清洗混合机,输送器具、料仓等,若要加回料,则应使用同质清洁回料,并保持适当和稳定的比例。
2)加料、塑化配好的料输送到注吹机料斗内,通过多段加热和螺杆的转动输送、搅拌作用完成塑化。
3)注射工艺熔融的塑化料通过大喷嘴注入集料管,再经过集合支管小喷嘴注入注射模中的芯棒上,制成型坯,经适度冷却使型坯表面固化,此时瓶颈已完全成型,由于是高压注射成型,瓶口平整光洁,不产生飞边。
4)吹塑工艺打开压机,升起中心塔台及相连的模芯棒,芯棒夹持着型坯转入吹塑模。
然后关闭吹塑模。
从芯棒通入洁净的压缩空气,将型坯吹胀并紧贴吹塑模型腔内壁,经短暂冷却定型成塑料瓶形。
5)脱瓶吹制结束,塔台升起,塔台及相连的芯棒又夹持着瓶子转入脱瓶工位,由一组对应的脱瓶板卡住瓶颈,将瓶子从芯棒上脱离。
6)火焰处理、自动计数、落瓶成型好的塑料瓶自行排放在输送机上,该输送机通过履板式输送带边输送边理瓶,通过两组煤气灯头对瓶身外壁进行火焰处理,改变瓶身表面极性,随后逐个通过自动计数器和落瓶,进入专用箱内。
达到设定数量后,计数器会自动复零、重新计数,同时变位落瓶进入另一个专用箱内。
火焰处理要注意煤气灯头的位置和开关调节,要严防瓶子歪倒,瓶子着火燃烧,火焰处理输送机与注吹成型机联动,可按需调节。
火焰处理目的是去除塑料瓶表面所带极性,以使用普通胶水、糨糊粘贴标签。
7)内包装、外包装初检合格的塑料瓶,经适当冷却后,先用洁净的塑料袋内包装,塑料袋内放入产品合格证后扎口,随后通过传递窗小心送出洁净车间,用纸箱外包装。
塑料盖的生产工艺:
分别称、配料→混合→贮存、送料→加料→塑化→注射→保压、冷却→脱模→内包装→外包装
1)配合料的制备塑料瓶盖的原辅料处理要求和加工过程与瓶身料制备要求基本相仿。
要注意的是瓶身主原料是吹塑级的,而瓶盖主原料是注塑级的,同种原料融体指数不同。
因此原料在贮存、堆放使用时要严格分开,要有明显识别的标志,包括各种回料,要按配方准确配制。
2)注塑工艺
①加料配合料由密闭溜管道输送到注塑机顶部料斗(或人工加料),机器开动后,随塑化器料桶内螺杆转动,料斗内的料不断进入料筒,完成给机器加料过程。
②塑化塑化是从料斗进入料筒的塑料配合料在料筒中受热达到流动状态并且有良好可塑性的过程。
其要求是塑料在进入模腔前达到规定的成型温度,并在规定时间内提供足够量的熔融塑料(塑化量)。
熔料各点温度应均匀一致,不发生热分解,以确保塑料盖的物理性能和连续生产的需要。
③注射先是将塑化良好的熔体在螺杆的推压下注入模具(注射过程),融料在注射进模腔时要经过喷嘴,主(分)流道、浇口、阻力很大,注射压力损失大30%-70%,故工艺要求必须要有足够大的注射压力,保障充模安全。
然后是模塑阶段,即充模、压实、倒流和浇口固化4个步骤。
注入模腔的塑料熔体经冷却定型为塑料盖子。
④冷却、脱模冷却脱模阶段是从浇口的塑料完全冻结起到盖子从模具中脱出的阶段。
脱模又分强脱模直接脱出和用专用脱模装置推杆帮助脱出的。
⑤包装
主要检测项目和主要检测设备
检测项目
检测设备
外观
色泽均一,表面光洁、平整、不允许有变形和明显的擦痕。
不允许有沙眼、油污、气泡,瓶口应平整光滑。
鉴别(红外光谱和密度)
红外分光光度计
密封性
密封性试验装置
振荡试验
振荡仪
水蒸气渗透
恒温恒湿箱、万分之一天平
炽灼残渣
马弗炉
溶出物试验
恒温水浴锅、PH计、紫外分光光度计、恒温干燥箱
微生物限度试验
空气洁净室、超净台、薄膜过滤器、高压蒸汽消毒器
异常毒性
清洁级小鼠饲养设施
..