推荐氮气净化方案.docx
《推荐氮气净化方案.docx》由会员分享,可在线阅读,更多相关《推荐氮气净化方案.docx(8页珍藏版)》请在冰豆网上搜索。
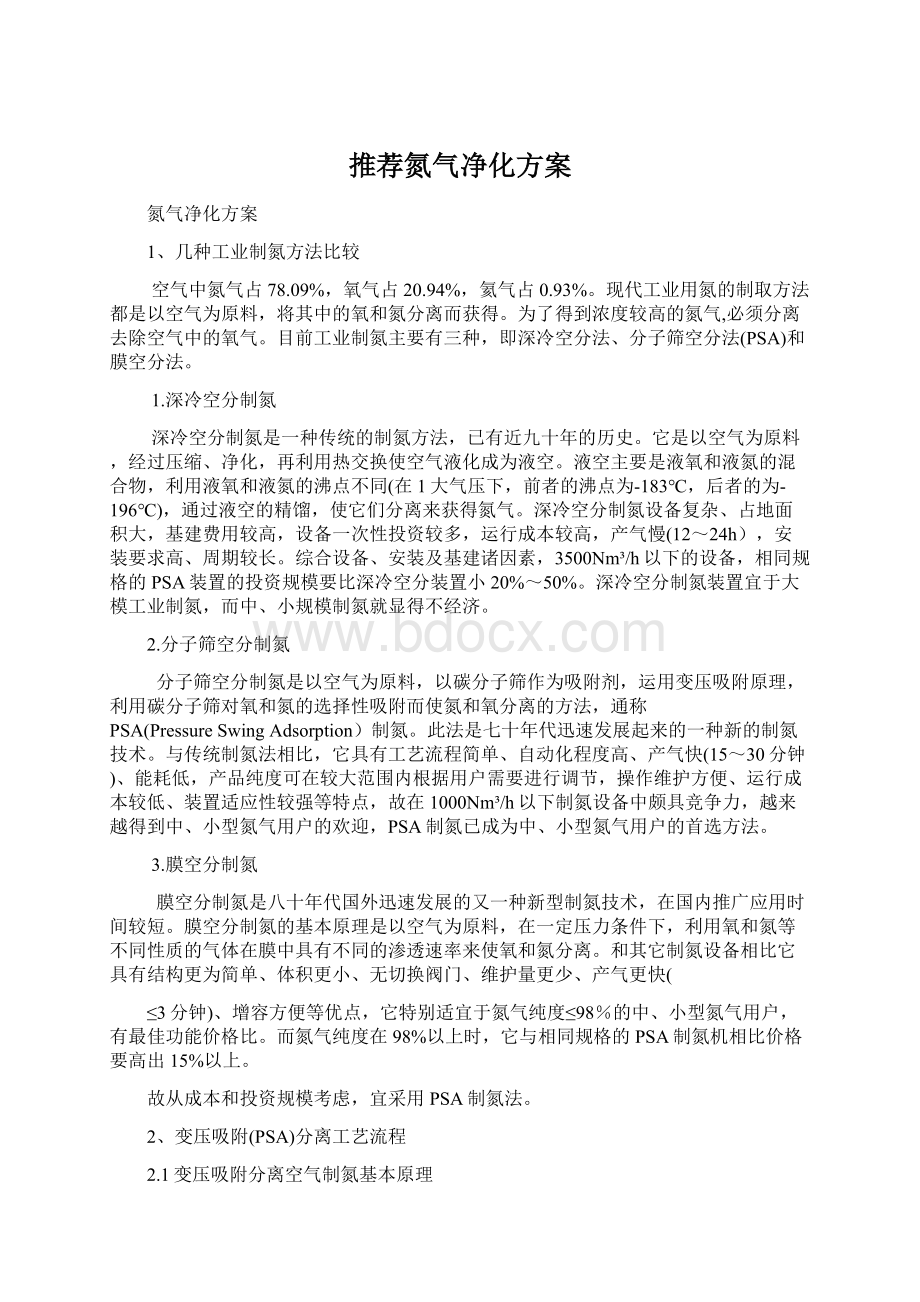
推荐氮气净化方案
氮气净化方案
1、几种工业制氮方法比较
空气中氮气占78.09%,氧气占20.94%,氦气占0.93%。
现代工业用氮的制取方法都是以空气为原料,将其中的氧和氮分离而获得。
为了得到浓度较高的氮气,必须分离去除空气中的氧气。
目前工业制氮主要有三种,即深冷空分法、分子筛空分法(PSA)和膜空分法。
1.深冷空分制氮
深冷空分制氮是一种传统的制氮方法,已有近九十年的历史。
它是以空气为原料,经过压缩、净化,再利用热交换使空气液化成为液空。
液空主要是液氧和液氮的混合物,利用液氧和液氮的沸点不同(在1大气压下,前者的沸点为-183℃,后者的为-196℃),通过液空的精馏,使它们分离来获得氮气。
深冷空分制氮设备复杂、占地面积大,基建费用较高,设备一次性投资较多,运行成本较高,产气慢(12~24h),安装要求高、周期较长。
综合设备、安装及基建诸因素,3500Nm³/h以下的设备,相同规格的PSA装置的投资规模要比深冷空分装置小20%~50%。
深冷空分制氮装置宜于大模工业制氮,而中、小规模制氮就显得不经济。
2.分子筛空分制氮
分子筛空分制氮是以空气为原料,以碳分子筛作为吸附剂,运用变压吸附原理,利用碳分子筛对氧和氮的选择性吸附而使氮和氧分离的方法,通称PSA(Pressure Swing Adsorption)制氮。
此法是七十年代迅速发展起来的一种新的制氮技术。
与传统制氮法相比,它具有工艺流程简单、自动化程度高、产气快(15~30分钟)、能耗低,产品纯度可在较大范围内根据用户需要进行调节,操作维护方便、运行成本较低、装置适应性较强等特点,故在1000Nm³/h以下制氮设备中颇具竞争力,越来越得到中、小型氮气用户的欢迎,PSA制氮已成为中、小型氮气用户的首选方法。
3.膜空分制氮
膜空分制氮是八十年代国外迅速发展的又一种新型制氮技术,在国内推广应用时间较短。
膜空分制氮的基本原理是以空气为原料,在一定压力条件下,利用氧和氮等不同性质的气体在膜中具有不同的渗透速率来使氧和氮分离。
和其它制氮设备相比它具有结构更为简单、体积更小、无切换阀门、维护量更少、产气更快(
≤3分钟)、增容方便等优点,它特别适宜于氮气纯度≤98%的中、小型氮气用户,有最佳功能价格比。
而氮气纯度在98%以上时,它与相同规格的PSA制氮机相比价格要高出15%以上。
故从成本和投资规模考虑,宜采用PSA制氮法。
2、变压吸附(PSA)分离工艺流程
2.1变压吸附分离空气制氮基本原理
利用吸附剂对空气中各组分吸附能力的差异,以及吸附剂的吸附容量随压力变化的特性,可通过加压吸附,减压再生的方式完成空气分离和吸附剂的循环使用的过程。
变压吸附制氮,采用碳分子筛为吸附剂。
由于碳分子筛对氧和氮的吸附速度相差很大,(见图2.1),氧的吸附速度明显大于氮的吸附速度,使氧优先吸附于碳分子筛而与氮气分离,因此,碳分子筛制氮工艺,吸附切换时间较短,一般在60秒左右,设置两个塔,交替吸附、再生,就能完成氧氮分离,在流出相得到产品氮气。
碳分子筛对氧的吸附量随吸附压力的降低而减少,通过减压即可解吸,完成碳分子筛的再生。
图2.1碳分子筛对氧氮的吸附动力学曲线
2.2.工艺流程
其工艺流程如图2.2:
图2.2PSA工艺流程图
原料空气经压缩机压缩至0.8MPa(或以上),经冷却器冷却至常温,再经过滤器过滤油、水后,进入空气缓冲罐,稳压后进入吸附塔(填充碳分子筛),空气中氧、二氧化碳和和杂质气体被吸附,其余组分(主要为氮气)则从出口端流出进入缓冲罐。
吸附塔经过均压(吸附阶段完毕处于高压状态的左塔与处于低压状态的右塔相连,作一段降压,则左塔则为均压,均压后床层内的压力约为原有压力的一半)、减压至常压,脱除所吸附的杂质组分,完成碳分子筛的再生。
两吸附塔循环交替操作,一塔吸附产氮,另一塔解吸再生,可以不间断连续产出产品氮气。
3、变压吸附法主要影响因素
1.气源压力稳定性;
2.碳分子筛性能;碳分子筛是变压吸附制氮的核心,因此应尽量选取性能优良的碳分子筛。
3.管路阀门的运行稳定性和精确性。
4、变压吸附法的一些改进措施
近几年来PSA制氮技术不断发展,装置和流程改进很快,提出了以下一些改进措施。
1.在产品储罐之前增设一个循环气罐及一条旁通管路。
在启动的初期,不合格产品氮不导入氮储罐,而经旁通管路返回吸附塔作吹洗气。
在暂时停车时,可储入循环气罐,保证产品储罐不受污染,缩短了再启动时的供气时间。
2.选用优质碳分子筛或用多种吸附剂分层填装制备高纯氮。
2005年以来,日本的可乐丽碳分子筛进入中国市场,该碳分子筛较适合于生产99.99%以上的氮气。
3.氮——氧联产提高收率,在建立制氮装置或制氧装置的同时,利用排出的富氧尾气或富氮尾气作原料气,再建一套规模相适应的制氧装置或制氮装置。
由于尾气中的富氧或富氮组成高于空气中的组成,这样,联产装置比单独的氧/氮装置的收率可增加10-15%。
若通过改进后的分子筛技术制取氮气还不能满足啤酒生产所需要的99.99%的纯度,则还需要一个高度提纯氮气的过程。
从空气中分离出来的氮气中主要的杂质为氧气,目前采用的除去氧气的措施多是以氢气在一定条件下与氧气反应生成水,达到除去氧气的目的。
氮气净化过程主要由除氧、除水两部分组成。
经搜索阅读相关资料,比较目前已使用的提纯氮气的措施,现初步拟定两种方案。
方案一、催化反应除氧
一、基本原理
将未经净化的氮气称为粗氮,经净化的氮气称为纯氮。
如果在粗氨中加入一定量的H2,在催化剂的作用下,可使杂质氧和氢化合生成水。
通常,为了使除氧反应进行得完全,除氧彻底,H2的加入量必须大于与O2完全化合的量,这部分氢叫做过剩氢。
除氧催化剂必须具备活性高(反应速度快)、比表面积大、选择性好、寿命长及价格低等特点。
工业上常用的除氧催化剂有活性铜催化剂、镍铬催化剂、钯A分子筛、活性氧化铝镀钯以及钯碳纤维等。
1.除氧过程
为了除去普氮中残余的氧气,可以把普氮和氢气混合后通入反应器(氢气从氨分解发生装置或氢气钢瓶获得),反应器中放置的是钯催化剂,在反应器里恒温80~100℃,由于钯催化剂的作用,氢气与普氮中残余的氧气发生反应,其化学反应式如下:
80~100℃
2H2+O22H2O
钯催化剂
反应生成的水气容易被氮气带走,催化剂不致受水气影响而失效,无须再生处理,可长期使用。
普氮除氧后,氮气中含氧量可降低到《5ppm。
2.除水过程
除水过程主要由气水分离器和两只13×吸附干燥器完成。
除氧后的氮气经过冷却器降至室温,由气水分离器除去凝结水,气水分离器利用其断面扩大,流速减慢,流向改变,把凝结水除去。
两只吸附干燥器并联使用以进一步深度干燥,一只工作,另一只再生,通过8只阀门启闭切换来实现。
吸附干燥器里充填13×干燥剂,在常温下工作可以连续运行24小时,再生时将其升温加热至350℃,恒温4~5小时,并不断通入经计量的极少量净化氮气冲洗,停止加热后,让吸附干燥器冷却备用。
2、工艺流程
氮气净化装置的工艺流程如下图所示:
图1.氮气净化装置流程图
氮气与氢气分别由各自的汇流装置,经减压后进入到氮气净化配氢装置。
氮气主气流中配入适量的氢气,混合后,进入到高效氮气净化器的预脱罐内,脱除气体中的油污。
混合后进入反应器。
配氢过程如图2:
图2.配氢气流程图
反应器工作温度控制在80~100℃,普氮中杂质氧与氢气在钯催化剂的作用下生成的水气全部被氮气带走,先经过水冷却器,把氮气降至室温,氮气通过气水分离器时,可以从分离器底部放水阀及时排除氮气中冷凝下来的游离水。
氮气冷凝除湿后,进入两只并联吸附干燥器中,进行深度干燥,然后经过滤器除尘埃颗粒,最后从净化氮出口阀口送往使用点。
吸附干燥系统有左、右2个干燥罐,罐内装有5A分子筛,2罐可互换使用。
当左罐中的干燥剂吸水饱和后,可切换到右干燥罐继续使用,同时分出一部分干纯气体,作为“左干燥”再生载气。
如此左右2个干燥罐切换,设备可连续使用。
吸附干燥系统如图3:
图3.吸附干燥系统示意图
装置中配备微量氧分析仪和微量水份测量仪、连续监测或记录氮气纯度,进行自动控制。
图4.氮气净化器流程图
3、装置的特点
1.本净化氮气的制取是以普氮装置为基础,另加除氧和干燥组件,组件都安装于金属支架上。
2.氮气净化装置中无运动部件,结构简单,操作、维修方便。
3.只要普氮浓度在99%以上,含氧量≤1%时,通过净化装置处理,就能得到99.99%以上浓度的氮气。
4.投资小,能耗低,净化效率高。
它不仅提高了产品质量,而且降低了生产成本。
方案二、直接反应除氧
通常,当氮气中含氧量《0.5%时,可以采用直接化学法除氧。
1.基本原理
直按反应法除氧是采用脱氧剂(如活性金属或金属氧化物)直接与粗氮中的杂质氧发生反应,化合生成金属氧化物,从而除去粗氮中的02。
常用脱氧剂有活性氧化锰(410脱氧剂)。
银x分子筛(201催化剂),活性铜脱氧剂(0603催化剂)以及3093脱氧剂等。
直接化学法除氧的典型流程如图5所示。
在该流程中两个除氧器并联,其中一个进行除氧,另一个进行再生,交替轮换使用。
图5.直接反应法除氧流程
2.脱氧剂选择
通过对北京化工研究院、兰化公司研究院和大连化学物理研究所等几家脱氧催化剂研制单位的调查,我认为大连化学物理研究所研制的SO6HN型脱氧剂用在氮气脱除微量氧上比较合适。
该脱氧剂在小规模工业装置上已广泛应用,有成熟可靠的使用经验,且净化深度深,脱氧容盘大。
在充分论证基础上,最终决定采用506HN型脱氧剂。
506HN(贵金属/锰基变价氧化物)脱氧剂是由贵金属作为活性组分,氧化锰作为氧吸收体的脱氧剂。
锰和铜一样都是变价元素,具有高价和低价,在这个基体上用一些贵金属使得它的脱氧温度和再生温度都比较低,低价金属氧化物吸氧后变成高价金属氧化物,因此性能良好。
该脱氧剂的最大特点是在室温下脱氧,吸氧饱和后升温至75一100℃,用氢气即可还原再生,而且吸氧能力比铜脱氧剂高。
据吉化炼油厂新增设的氮气脱氧装置自1997年9月投用至今,实践证明脱氧效果良好。
脱氧器入口氧体积分数为
,净化后脱氧器出口氧体积分数小于
,再生周期30d以上,各项指标均达到设计值,由于506HN型脱氧剂在室温下脱氧,脱氧器前蒸气加热器仅在冬季气温低时使用,节约了蒸汽。
(注:
专业文档是经验性极强的领域,无法思考和涵盖全面,素材和资料部分来自网络,供参考。
可复制、编制,期待你的好评与关注)