陶瓷制作中地化学问题.docx
《陶瓷制作中地化学问题.docx》由会员分享,可在线阅读,更多相关《陶瓷制作中地化学问题.docx(10页珍藏版)》请在冰豆网上搜索。
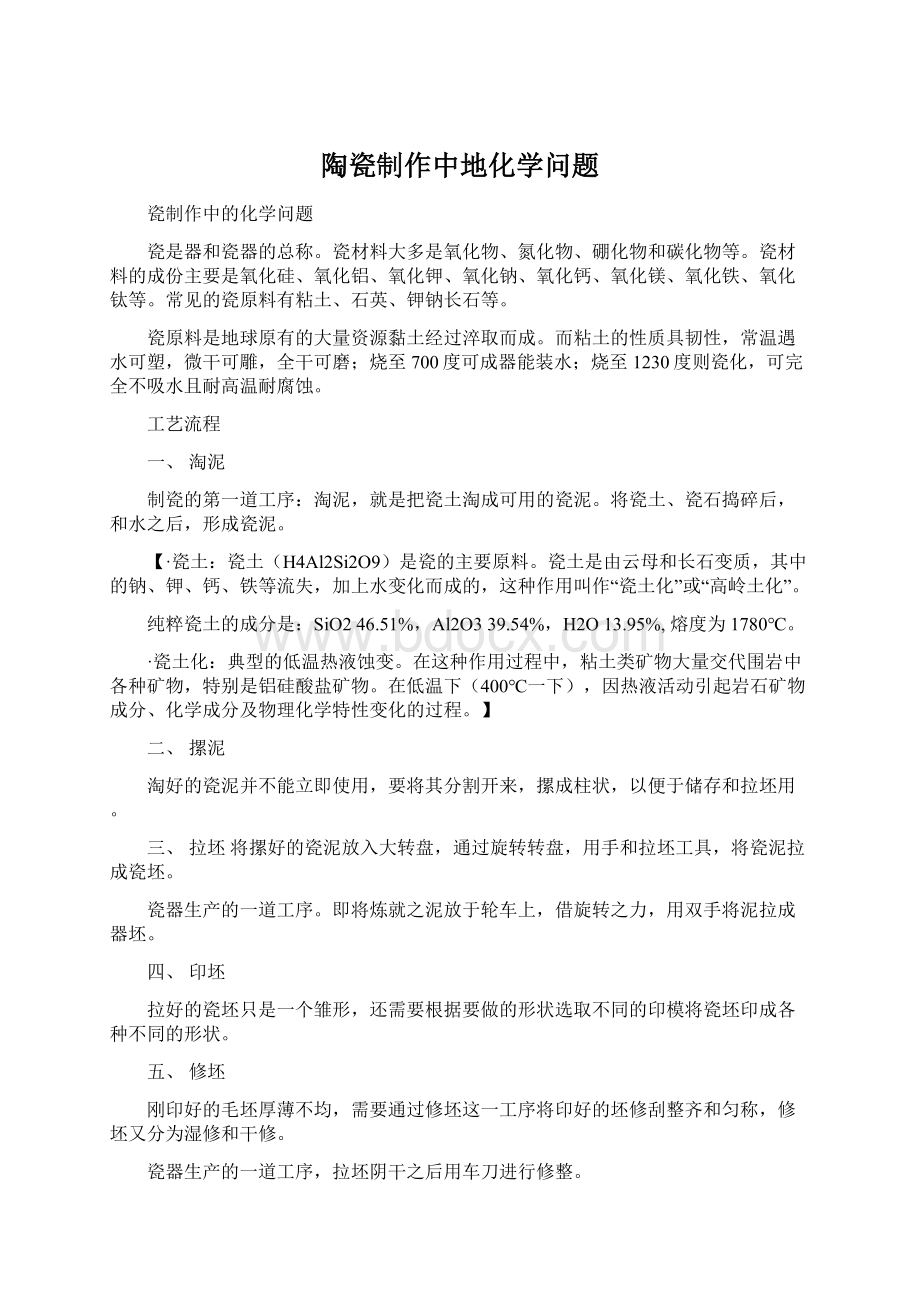
陶瓷制作中地化学问题
瓷制作中的化学问题
瓷是器和瓷器的总称。
瓷材料大多是氧化物、氮化物、硼化物和碳化物等。
瓷材料的成份主要是氧化硅、氧化铝、氧化钾、氧化钠、氧化钙、氧化镁、氧化铁、氧化钛等。
常见的瓷原料有粘土、石英、钾钠长石等。
瓷原料是地球原有的大量资源黏土经过淬取而成。
而粘土的性质具韧性,常温遇水可塑,微干可雕,全干可磨;烧至700度可成器能装水;烧至1230度则瓷化,可完全不吸水且耐高温耐腐蚀。
工艺流程
一、淘泥
制瓷的第一道工序:
淘泥,就是把瓷土淘成可用的瓷泥。
将瓷土、瓷石捣碎后,和水之后,形成瓷泥。
【·瓷土:
瓷土(H4Al2Si2O9)是瓷的主要原料。
瓷土是由云母和长石变质,其中的钠、钾、钙、铁等流失,加上水变化而成的,这种作用叫作“瓷土化”或“高岭土化”。
纯粹瓷土的成分是:
SiO246.51%,Al2O339.54%,H2O13.95%,熔度为1780℃。
·瓷土化:
典型的低温热液蚀变。
在这种作用过程中,粘土类矿物大量交代围岩中各种矿物,特别是铝硅酸盐矿物。
在低温下(400℃一下),因热液活动引起岩石矿物成分、化学成分及物理化学特性变化的过程。
】
二、摞泥
淘好的瓷泥并不能立即使用,要将其分割开来,摞成柱状,以便于储存和拉坯用。
三、拉坯将摞好的瓷泥放入大转盘,通过旋转转盘,用手和拉坯工具,将瓷泥拉成瓷坯。
瓷器生产的一道工序。
即将炼就之泥放于轮车上,借旋转之力,用双手将泥拉成器坯。
四、印坯
拉好的瓷坯只是一个雏形,还需要根据要做的形状选取不同的印模将瓷坯印成各种不同的形状。
五、修坯
刚印好的毛坯厚薄不均,需要通过修坯这一工序将印好的坯修刮整齐和匀称,修坯又分为湿修和干修。
瓷器生产的一道工序,拉坯阴干之后用车刀进行修整。
六、捺水捺水是一道必不可少的工序,即用清水洗去坯上的尘土,为接下来的画坯、上釉等工序做好准备工作。
七、画坯在坯上作画是瓷艺术的一大特色,画坯有好多种,有写意的、有贴好画纸勾画的,无论怎样画坯都是瓷工序的点睛之笔。
八、上釉画好的瓷坯,粗糙而又呆涩,上好釉后则全然不同,光滑而又明亮:
不同的上釉手法,又有全然不同的效果,常用的上釉方法有浸釉、淋釉、荡釉、喷釉、刷釉等。
【·釉又称“釉子”,以石英,长石,硼砂,黏土等为原料,磨成粉末,加水调制而成的物质,用来涂在瓷半成品的表面,烧制后发出玻璃光泽,并能增加瓷的机械强度和绝缘性能。
】
·瓷坯釉相适应原理
瓷坯釉相适应是指瓷制品胎、釉紧密结合成不裂也不脱落的整体的能力。
人们在进行坯、釉料配方设计时,就注意到影响坯釉相适应的诸多因素。
首先,应使釉的膨胀系数略低于坯,使之成为压缩釉层;其次,应使釉具有较大的弹性和抗强度;第三,釉层厚度及釉熔体对坯的润湿程度等等。
然而,无论是坯、釉的膨胀系数,还是弹性、抗强度,都必须首先清楚地知道坯、釉的化学组成,再通过加和性公式计算出来。
原料、釉、坯的化学组成,就要由化学分析来确定。
这对于大多数瓷生产企业,尤其是中、小型企业来说,几乎不可能现场做到。
同时,计算值也是概数,与实际值相差很大,导致有时即使按计算值进行设计的配方,也会产生坯、釉不相适应的状况。
九、烧窑千年窑火,延绵不息,经过数十道工具精雕细琢的瓷坯,在窑经受千度高温的烧炼,就像一只丑小鸭行将达化一只美天鹅。
现在的窑有气窑、电窑、等。
·瓷中的泥土变硬了,就是发生了化学变化的原故。
在高温下,瓷生坯固体颗粒的相互键联,晶粒长大,空隙(气孔)和晶界渐趋减少,通过物质的传递,其总体积收缩,密度增加,最后成为具有某种显微结构的致密多晶烧结体,这种现象称为烧结。
这个过程中包含有物理变化和化学变化。
·坯体的化学变化:
氧化和还原等变化,还原作用多在250-900℃时发生,分解作用多在500-1300℃时发生。
1)碳酸盐的分解。
2)碳素、硫化物及有机物的氧化。
粘土中夹杂的硫化物在800℃左右被氧化完毕。
3)坯体中存在的碳素及有机物在600℃以上才开始氧化分解,并持续到高温,此阶段产生的气体必须完全排除掉,否则会引起坯体起泡。
C+O2→CO2↑
4)强还原阶段(1020-1150℃)。
此阶段坯体的三氧化二铁及硫酸盐在釉层封闭坯体之前得到充分还原与分解。
5)氧化亚铁易与二氧化硅生成易熔的玻璃状物质,促进了坯体的烧结。
·普通瓷坯体在烧成过程中的物进化学变化
瓷坯体的烧成过程十分复杂,无论采用何种工艺(一次或二次烧成等)、何种窑炉烧成,在焙烧过程的各个阶段均将发生一系列物理化学变化。
原料的化学组成、矿物组成、粒度大小、混合的均匀性以及烧成的条件,对于烧成过程的物理化学变化有至关重要的影响。
深入研究和掌握这些变化的类型和规律,才能制定出合理的烧成工艺,选择或设计窑炉,确定相应的热工制度,并为烧成缺陷的分析提供理论依据。
有利于调整配方,改进工艺、设备和操作,达到优质、高产、低耗的目的。
表3-8-1列出了普通瓷坯体烧成过程各阶段的物理化学变化。
一、低温阶段
低温阶段(室温~300℃)也可称干燥阶段。
进入烧成窑炉的坯体一般已经过干燥,但仍含有一定数量的残余水分(约2%以下)。
本阶段的主要作用是排坯体的残余水分,其温度一般在300℃(有的认为是270℃)以下。
随着水分的排除,组成坯体的固体颗粒逐步靠拢,因而发生少量的收缩,但这一收缩并不通货膨胀完全填补水分遗留的空间,故对粘土质坯体表现为气孔率增加、强度提高;对由非可塑性原料制成的坯体(加粘合剂者除外)则表现为疏松多孔、强度降低。
阶段名称
温度围
主要
变化
物理变化
化学变化
低度阶段
室温~~300℃
1.排除机械水
2.质量减少,气孔率增大
-------
氧
化
分
解
阶
段
300~~950℃
1.质量急速减小;
2.气孔率进一步增大
3.硬度与机械强度增加
4.体积稍有变化
1.氧化反应
2.碳素及有机物氧化
3.硫化铁氧化
4.分解反应
①结晶水分解排除;
②碳酸盐及硫酸盐分解;
5.氢氧化铁分解
6.晶型转变:
石英及Al2O3晶型转变
高温阶段
950℃~~最高烧成温度
1.强度增加
2.气孔率降低到最小值
3.体积收缩,密度增大
4.色泽变白,光泽增强
1.继续氧化,分解
2.形成液相及固相熔融
3.形成新结晶相
4.形成低铁硅酸盐
保温阶段
烧成温度下维持一段时间
坯体结构更为均匀致密
1.液相量增多
2.晶体增多长大
3.晶体扩散,固,液相分布更为均匀
冷却阶段
烧成温度~~~室温
1.液相中结晶
2.液相过冷
3.硬度与机械强度增大
---------
本阶段坯体水分含量是影响安全升温速度的首要控制因素.若入窑坯体水分含量超过3%,则必须严格控制升温速度,否则由于水分激烈气化,易导致坯体开裂.若入窑体水分<1%,升温速度可以加快.正常烧成时一般控制在2%.由于本阶段气体中水汽含量较高,故应加强通风使水汽及时排除,有利于提高干燥速度。
应控制烟气温度高于露点,防止在坯体表面出现冷凝水,使制品局部胀大,造成水迹或开裂缺陷。
此外烟气中的SO2气体在有水存在条件下与坯体中的钙盐作用,生成CaSO4析出物CaSO4分解温度高,易使制品产生气泡缺陷。
本阶段坯体基本不发生化学变化,故对气氛性质无特殊要求。
二、中温阶段
中温阶段(300~~~950℃)又称分解与氧化阶段,是瓷烧成过程的关键阶段之一。
瓷坯中所含的有机物、碳酸盐、硫酸盐以及铁的氧化物等,大都要在此阶段发生氧化与分解,此外还伴随有晶型转变、结构水排除和一些物理变化。
1.氧化反应
(一)碳素和有机物的氧化 瓷坯釉原料一般含有不同程度的有机物和碳素,象北方的紫木节土、南方的黑泥等含量较多。
压制成型时,坯体中有时加入了有机添加剂,坯体表面沾有润滑油。
此外燃烧烟气中未燃尽的碳粒可能沉积在坯体表面。
这些物质在加热时均会发生氧化反应。
其反应式为:
C有机物+O2→CO2↑(350℃以上)
C碳素+O2→CO2↑(约600℃以上)
S+O2→SO2(250~~920℃)
上述反应均宜在釉面熔融、气孔封闭前结束,否则就易产生烟熏、起泡等缺陷。
2.铁的化学物氧化
其反应式为:
FeS2+O2→FeS+SO2↑(350~~~450℃)
4FeS+7O2→2FeO3+4SO2(500~~800℃)
FeS2是一种十分有害的物质,应在此阶段把它全部氧化成Fe2O3。
否则,一旦釉面熔融、气孔封闭,再进行氧化、逸出的SO2气体就可能使制品起泡;而生成的Fe2O3又易使制品表面污染成黄、黑色。
3.分解反应
1.结构水的分解、排除
坯料中各种粘土原料和其它含水矿物(如滑石、云母等),在此阶段进行结构水(或称结晶水0的排除。
一般粘土矿物脱水分解的起始温度为200~~300℃左右,但剧烈脱水温度和脱水速度则取决于原料矿物组成、结晶程度、制品厚度和升温速度等。
例如高岭土的脱水温度为500~~700℃,后期脱水速度较快,蒙脱石脱水温度600~~750℃;伊利石脱水温度为400~~600℃后两者脱水速度较和缓;滑石在600℃以上脱水后,晶格部重排,形成偏硅酸盐和活性SiO2我国滑石在900℃附近有明显吸热和失重效应。
高岭土脱除结构水的反映式为
Al2O3*2SiO2*2H2O→Al2O3*2SiO3+2H2O↑(400~~~600℃)
升温速度对脱除结构水有直接影响,快速升温时,结构水的温度移向高温,而且比较集中。
1.碳酸盐的分解
瓷坯体中含有碳酸盐类物质,其分解温度一般在1050℃以下,其主要反应为:
MgCO3→MgO+CO2↑(500~~~850℃)
CaCO3→CaO+CO2↑(850~~~1050℃)
4FeCO3→2Fe2O3+4CO2↑(800~~~1000℃)
MgCO3*CaCO3(白云石)→CaO+MgO+2CO2↑(730~~950℃)
2.硫酸盐的分解
瓷坯体中的硫酸盐,分解温度一般在650℃左右,其主要反应为:
Fe(SO3)3→MgO+CO2↑(560~~750℃)
MgSO4→MgO+SO3(900℃以上,氧化焰)
(一)、石英的多晶转化和少量液相的生成
石英在配方中一般用量较多,在本阶段将发生多晶转化。
在573℃,β-石英转化为a-石英伴随体积膨胀0.82%;在867℃,a—石英缓慢转变为a-磷石英,体积膨胀14.7%在900℃附近,长石与石英。
长石与分解后的粘土颗粒,在接触位置处有共熔体的液滴生成。
伴随以上化学变化,本阶段发生以上物理变化:
随着结构水和分解气体的排除,坯体质量急速减少,密度减少,气孔增加。
根据配方中粘土、石英含量多少发生不同程度的体积变化。
后期由于少量熔体的胶结作用,使坯体强度相应提高。
为保证氧化分解反应在液相大量出现以前进行彻底,本阶段应注意加强通风,保持良好的氧化气氛;控制升温速度,保证有足够的氧化分解反应时间,必要时可进行保温,同时减小窑上下温差。
三.冷却阶段
冷却阶段也可细分为急冷/缓冷和最终冷却三个阶段.
从最高烧成温度(高火保温结束)到850℃为急冷阶段。
此时坯体液相还处于塑性状态,故可进行快冷而不开裂。
快冷不仅可以缩短烧成周期,加快整个烧成过程,而且可以有效防止液相吸晶和晶粒长大以及低价铁的再度氧化。
从而可以提高坯体的机械强度/白度和釉面光泽度。
冷却速度可控制在150~300℃/h。
从850℃到400℃为缓冷阶段。
850℃以下液相