机械系统设计论文资料.docx
《机械系统设计论文资料.docx》由会员分享,可在线阅读,更多相关《机械系统设计论文资料.docx(14页珍藏版)》请在冰豆网上搜索。
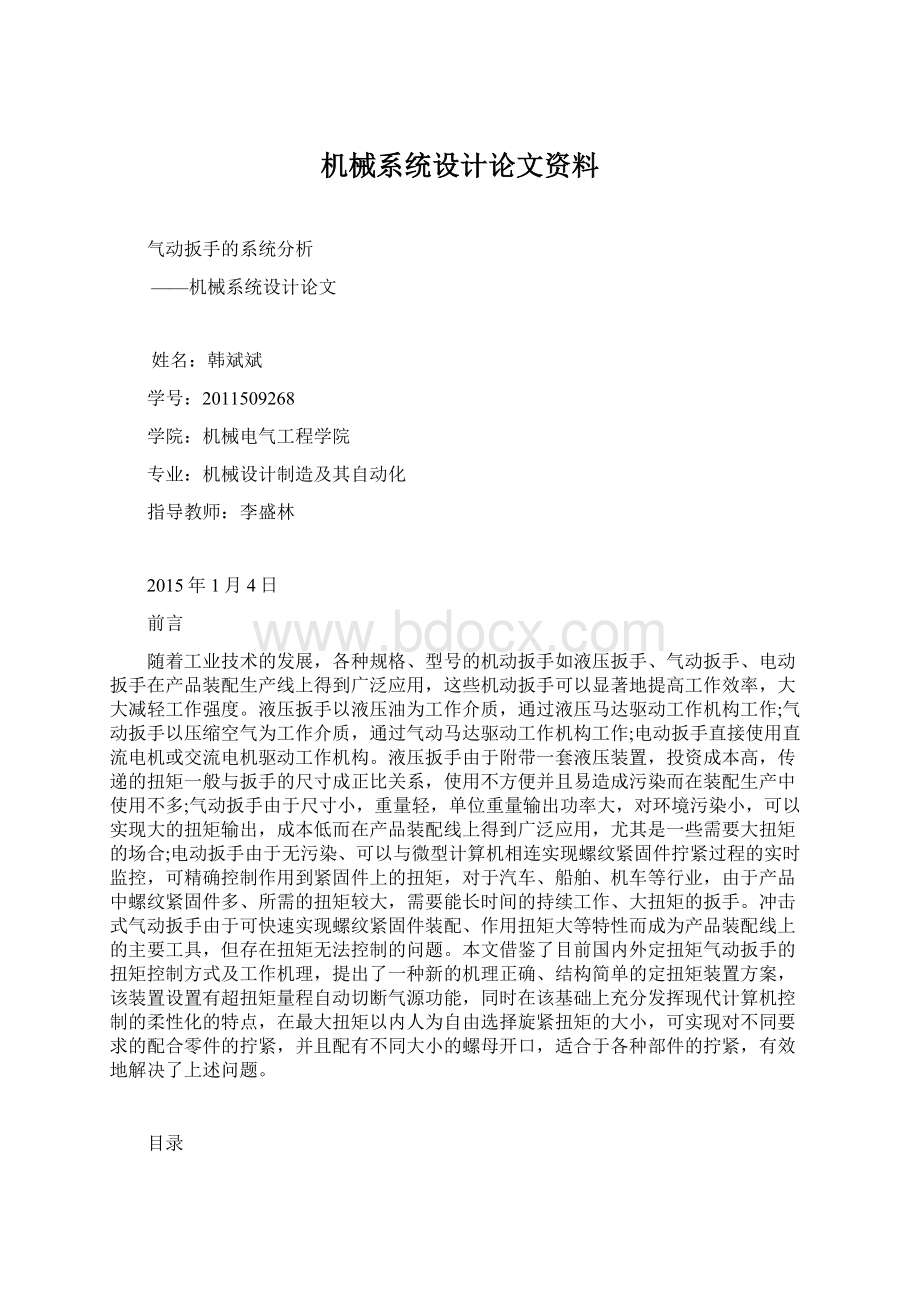
机械系统设计论文资料
气动扳手的系统分析
——机械系统设计论文
姓名:
韩斌斌
学号:
2011509268
学院:
机械电气工程学院
专业:
机械设计制造及其自动化
指导教师:
李盛林
2015年1月4日
前言
随着工业技术的发展,各种规格、型号的机动扳手如液压扳手、气动扳手、电动扳手在产品装配生产线上得到广泛应用,这些机动扳手可以显著地提高工作效率,大大减轻工作强度。
液压扳手以液压油为工作介质,通过液压马达驱动工作机构工作;气动扳手以压缩空气为工作介质,通过气动马达驱动工作机构工作;电动扳手直接使用直流电机或交流电机驱动工作机构。
液压扳手由于附带一套液压装置,投资成本高,传递的扭矩一般与扳手的尺寸成正比关系,使用不方便并且易造成污染而在装配生产中使用不多;气动扳手由于尺寸小,重量轻,单位重量输出功率大,对环境污染小,可以实现大的扭矩输出,成本低而在产品装配线上得到广泛应用,尤其是一些需要大扭矩的场合;电动扳手由于无污染、可以与微型计算机相连实现螺纹紧固件拧紧过程的实时监控,可精确控制作用到紧固件上的扭矩,对于汽车、船舶、机车等行业,由于产品中螺纹紧固件多、所需的扭矩较大,需要能长时间的持续工作、大扭矩的扳手。
冲击式气动扳手由于可快速实现螺纹紧固件装配、作用扭矩大等特性而成为产品装配线上的主要工具,但存在扭矩无法控制的问题。
本文借鉴了目前国内外定扭矩气动扳手的扭矩控制方式及工作机理,提出了一种新的机理正确、结构简单的定扭矩装置方案,该装置设置有超扭矩量程自动切断气源功能,同时在该基础上充分发挥现代计算机控制的柔性化的特点,在最大扭矩以内人为自由选择旋紧扭矩的大小,可实现对不同要求的配合零件的拧紧,并且配有不同大小的螺母开口,适合于各种部件的拧紧,有效地解决了上述问题。
目录
第一章绪论
1.1课题研究的目的和意义
1.2自动扳手主要技术指标
1.3气动扳手的发展现状和问题
第二章基本原理和总体设计
2.1扭矩测量及拧紧系统的基本原理及总体方案
2.2各组成系统的设计·
第三章机械结构的设计
3.1气动发动机的设计计算
3.2机械式定扭矩装置设计
3.3气源自动切断装置
第四章信号检测与数据处理及程序举例
4.1自动检测控制装置
4.2电路组成
心得体会
参考文献
附录A主要部分电路连接图
附录B新型自检测气动扳手结构图
第1章绪论
1.1课题研究的目的和意义
机电一体化系统设计是多学科的交叉和综合,设计的学科和技术非常广泛,且其应用领域众多。
要全面精通它,不但需要强化训练学科融合的思维能力、加强相应的实践环节,还要及时学习新概念、新技术、将来才能成为机电一体化复合型人才。
本课程设计的目的是研究怎样利用系统设计原理和综合集成技巧,将控制电动机、传感器、机械系统、微机控制系统、接口及控制软件等机电一体化要素组成各种性能优良、可靠的机电一体化产品或系统。
本课程的具体要求是:
掌握机电一体化系统设计的基本概念、基本原理和基本知识;熟悉机电一体化系统设计中的常用机械量检测传感器、控制电动机的原理、结构、性能和应用;初步掌握机电一体化系统设计的原理和综合集成技巧,进行总体方案的分析和设计。
1.2课题主要技术指标要求
本课程设计要求能实现扭矩的微机自动检测,扳手开口直径大小可调,要求传感器具有较高的检测精度。
1.3气动扳手的发展现状和问题[1]
目前,冲击式气动扳手在产品装配流水线上作为主要的低值易耗工具被广泛应用,这种扳手具有输出扭矩大、成本低、无污染等优点,但其噪音大,而且作用到螺纹紧固件上的扭矩大小难以控制。
因此,目前大部分冲击式气动扳手都不具有定扭矩的功能。
但随着社会生产的发展,对产品的装配提出了很高的要求,要求提高螺纹紧固件的装配质量、可靠性和装配效率。
例如对于汽车、飞机等产品中的一些重要的螺纹联接,要求装配时作用到螺纹紧固件上的扭矩非常精确,这样才能确保联接的可靠性,保证产品的质量。
同时,随着人们环保意识的增强,绿色产品悄然兴起,相应的产品绿色设计成为一种新的设计方法。
对产品进行绿色设计要求改进产品结构,多使用一些可拆性、可回收性的结构如螺纹联接、键联接。
这时,为保证产品性能,要求这些联接可靠,螺纹紧固件所受的扭矩也需控制在一定值内。
为此需要气动扳手拧紧螺纹紧固件时作用在螺纹紧固件上的扭矩控制在预定的扭矩范围内。
扭矩值变动范围不能偏大,否则将使螺纹紧固件在工作时因强度不足发生突然折断而失效或者在工作时易产生松动导致产品性能不能满足要求。
因此,在使用气动扳手进行产品装配时,需要气动扳手能够精确控制其输出扭矩。
具有精确扭矩控制的气动扳手成为当前气动扳手的发展趋势。
纵观现有的定扭扭矩气动扳手存在下列问题:
l)实现扭矩控制的装置结构复杂,加工制造成本较高;
2)扳手的体积较大,重量重,有的还需要附带一套控制装置,使用不方便;
3)扭矩控制精度不高,不能满足生产需要,并且扭矩调节困难;
第2章系统的基本原理和总体设计
目前,国内外风动工具生产企业生产的各种定扭矩气动扳手所采用的扭矩控制方式是不同的,相应的定扭矩控制装置也不同。
下面对于冲击式定扭矩气动扳手的扭矩控制应采用的方式,提出了结构简单、原理可行的扭矩控制方案,从理论上分析了该方案的可行性。
2.1扭矩测量及拧紧系统的基本原理
这里采用扭矩测量传感器,利用应变片检测扭矩的大小,经放大器放大后,将其送入单片机,进行数据的处理与判断,系统工作的情况下,电磁阀的状态是开启的,如果该测量值大于单片机程序中的预设值,那么单片机输出控制信号将电磁阀关闭,从而切断气源输出,实现自动检测,自动切断的功能,单片机中扭矩预设值为用户自己选择,为控制系统的最大扭矩输出,在这里设计了片簧转子机构,当预设值大于或等于该扳手的最大输出时,检测控制系统将失去作用,因此,该预设值必须在最大值下设定。
系统的控制原理图如下:
扳手检测装置有标准扭矩传感器、扭矩测量仪表和气源控制器三部分构成,硬件构架主要包括89S52的单片机、I/O模块、驱动模块等部分组成,具体的工作原理如下图所示:
扳手连接完成后,单片机将控制信号通过I/O模块发送给驱动模块,驱动模块控制气源给气,内部旋转轴开始动作,同时扭矩测量仪实时测量扭矩,扭矩值通过数据采集系统传输给单片机,并由单片机输出显示信息,将测量的扭矩值显示在LCD显示盘上,单片机判定是否达到预设的扭矩值,比较判断后继续发出控制信号,进而完成系统闭环控制
2.2各分系统的设计
2.2.1气动扳手的结构[4]
气动扳手按其工作机理不同可分为冲击式气动扳手和脉冲扳手,其中冲击式气动扳手在我国使用最为广泛。
冲击式气动扳手结构主要由气动发动机和冲击机构组成,包含气动发动机、冲击头、凸轮轴、扳轴、柄体等零部件。
气动发动机是气动扳手的动力来源,它将压缩空气的压力能转换为气动发动机的动能,同时输出扭矩。
冲击机构由冲击头、凸轮轴、钢球、扳轴、花键联接套等组成,是气动扳手的工作机构,输出气动发动机产生的扭矩和能量。
冲击头和花键联接套之间通过花键相连,冲击头内端面有一不封闭的凹槽,凸轮轴左端面有一凹槽且凹槽为凸轮轮廓;在冲击头和凸轮轴凹槽之间夹着一钢球,扳轴与凸轮轴之间通过花键相连。
扳轴端部为四方头,可配接各种螺帽套。
工作时,扳轴与螺纹紧固件相连,气动发动机的扭矩通过花键联接套、冲击头、扳轴等传递作用到螺纹紧固件上。
气动扳手工作时,螺纹紧固件与扳轴、凸轮轴相连,并与之一同转动;冲击头通过花键联接套与气动发动机相连,随气动发动机一同转动;冲击弹簧压紧冲击头,使冲击头和凸轮轴与钢球相互接触。
当打开气阀开关后,压缩空气驱动气动发动机转动,输出扭矩。
若扳轴所受的螺纹紧固件阻力矩小于凸轮轴与钢球、冲击头与钢球之间的摩擦力矩时,冲击头带动凸轮轴转动,凸轮轴带动扳轴、螺帽一同转动。
此时,螺帽一般没有与被联接件接触。
若扳轴所受的螺纹紧固件阻力矩大于凸轮轴与钢球、冲击头与钢球之间的摩擦力矩时,钢球的摩擦力矩不能带动凸轮轴转动,钢球在冲击头带动下将沿凸轮轴端面内凹槽凸轮轮廓爬升,冲击头与凸轮轴之间有相对运动,冲击头在转动的同时沿轴向向左运动。
在冲击头的左端有一对牙嵌。
当钢球爬升到凸轮轴端面上时,冲击头的牙嵌与扳轴发生碰撞,推动扳轴转动,螺纹紧固件也随之一同转动。
同时,钢球又滑回到凸轮轴端面内凹槽中,冲击头轴向右移,与扳轴脱开结束碰撞。
通常冲击头每转一圈,冲击头与扳轴碰撞一次。
扳轴每碰撞一次就将扭矩传递给螺纹紧固件。
随着碰撞次数增加,螺纹紧固件上积累的扭矩增多。
当螺纹紧固件上积累扭矩大于气动发动机所能产生的最大扭矩时,冲击头与扳轴碰撞时产生反弹,气动发动机不再对扳轴作功。
此时操作工需关闭气阀,切断气动发动机的进气。
2.2.2定扭矩装置结构设计
设计定扭矩气动扳手的扭矩控制的装置的基本思路是当输出扭矩达到最大值时,冲击部分能与气动发动机安全脱开,不再拧紧螺纹紧固件,使气动发动机的扭矩不传递给螺纹紧固件。
出于对气动扳手的尺寸较小,输出扭矩大,成本低等要求的考虑,本课题设计的定扭装置采用结构简单、工作可靠、使用方便的机械式离合器。
这样可以保证定扭装置在输出较大扭矩情况下保持较小的尺寸,并且成本低廉,满足气动扳手的定扭矩精度要求。
2.2.3片簧一转子结构
根据上面基本思想设想提出了一种可以控制扭矩的离合器结构一一片簧一转子结构,其结构示意图如图2.2(图(a)为整体结构示意图,(b)为单个片簧一转子的结构放大图)。
考虑到具有扭矩控制的气动扳手的输出扭矩应可以调节,这样可使该定扭矩气动扳手的使用范围更广,图2.2所示的转子一片簧结构的定扭矩装置具有扭矩可调的功能。
在转子一片簧结构中,片簧固结在内圈上,内圈和外圈之间可以相对转动。
当调节好内圈与外圈之间的相对位置后,将内圈和外圈固定在一起,它们的位置在转子一片簧结构工作时保持不变。
为了减小转子与片簧之间的摩擦和磨损,在转子末端装有滚柱。
若将该结构嵌入到气动扳手中,转子可与气动扳手中的气动发动机的输出轴相连,片簧、内圈、外圈可与气动扳手冲击部分相连。
工作时,如果转子一片簧结构中内圈受到阻力矩,固定不动,转子在驱动力矩作用下产生转动,对片簧产生作用力,使片簧产生弯曲变形。
若内圈所受的阻力矩小于片簧所承受的最大力矩时,片簧、内圈、外圈和冲击部分随转子一同转动,使该结构输出扭矩;若内圈所受的阻力矩大于片簧所承受的最大力矩时,转子打滑,片簧、内圈和外圈不再随转子转动,没有扭矩输出。
这样可使片簧一转子结构的扭矩输出值控制在规定的范围内。
该装置除可以控制扭矩外,还可以实现扭矩的调节,调节范围士20%。
当调节扭矩时,可以调节内、外圈之间的相对位置。
研究表明,该结构输出的最大扭矩与片簧和内圈中心线之间的夹角a值有很大关系。
设计片簧一转子结构时,需要确定计算出片簧、内圈等的基本参数。
片簧一转子结构设计计算过程如图2.4。
转子的半径厂由所传递的扭矩按与转子相配合的轴的强度来计算确定滚柱半径,按与滚柱配合的轴的剪切强度确定。
内圈的半径R的确定需要考虑片簧的变形,应使片簧的变形较小并且片簧在工作时不应与内圈发生干涉,这里取(r+rT)=0.8R。
对于片簧一转子结构来说,其输出扭矩的主要影响因素是片簧的截面尺寸,故片簧的设计成为该结构设计的主要内容。
由于片簧的截面尺寸结构决定于片簧的惯性矩I,设计时确定片簧惯性矩就可以确定片簧尺寸。
由式(2.3)可知,若片簧各处截面相等,在其它参数一定条件下输出扭矩M与片簧惯性矩I成正比,并且片簧惯性矩I值变化对结构的最大输出扭矩值所对应的βm值没有影响。
设计时,初选片簧的惯性矩I0,计算出此时该结构的最大输出扭矩Mmax。
比较最大输出扭矩Mmax和所允许的最大扭矩[M]值,可以确定片簧的惯性矩I。
若片簧的截面为矩形,当给定片簧截面的宽度或高度尺寸后,就可以确定片簧的高度或宽度尺寸。
考虑片簧要有弹性,片簧的材料选用弹簧钢。
若所允许的最大扭矩[M]=26N·m,现设计片簧一转子结构模型。
按照上述片簧一转子结构设计过程,取α=45,片簧的材料选择弹簧钢55Si2Mn,其弹性模量E=206GPa,片簧的截面为矩形。
根据所传递的最大扭矩,按照强度要求计算得r=23mm,:
rT=5mm,则R=35mm。
初定片簧的惯性矩为I=7.8mm4。
由式(2.3)可得到最大输出扭矩Mmax对应的βm值,此时βm=5.7。
。
由于最大输出扭矩Mmax与片簧惯性矩I成正比,由所允许的[M]值可确定片簧的惯性矩为I=4mm4。
根据设计计算的片簧惯性矩I,当给定片簧截面的宽度或高度尺寸时,就可确定高度或宽度尺寸。
若片簧的宽度为6mm,则高度为2mm。
第3章其他机械结构的设计
气动扳手使用压缩空气作为工作介质,采用冲击碰撞的机理进行工作。
气动扳手涉及到热工学、碰撞理论等方面的知识,设计时需要综合应用这些知识。
定扭矩气动扳手主要由气动发动机、冲击机构和定扭矩部分组成,故定扭矩气动扳手的设计还包括气动发动机设计、冲击机构设计、定扭矩装置设计以及气动扳手中气路设计、气阀设计等辅助控制装置设计。
3.1气动发动机的设计计算[5]
气动发动机也称为气马达,按结构形式分有活塞式气马达、叶片式气马达、齿轮式气马达、涡轮式气马达。
叶片式气马达由于结构简单、外形尺寸小、单位重量输出功率大、维护性好等特点,在气动工具中被广泛用作动力源件。
气动扳手常采用正反转性能相同的叶片式气马达。
3.1.1气动发动机工作原理
正反转性能相同的叶片式气马达的工作原理图如图3.1。
当气马达正转时,压缩空气自左边口1进气,压缩空气对叶片5作功,驱动转子旋转。
直到气马达转子内气腔的气体与排气口3接通,则进行排气;尚有部分未从排气口3排完的气体则从右边口2(反转时的进气口)排到大气中。
当气马达反转时,压缩空气自右边口2进气,压缩空气对叶片5作功,驱动转子反转,转到一定位置,转子内气腔的气体与排气口3接通,则进行排气;尚有部分未从排气口3排完的气体则从左边口l(正转时的进气口)排到大气中。
排气口3相对于左边口1(正转时的进气口)和右边口2(反转时的进气口)的位置是对称的,故气马达正转和反转时性能相同。
3.2机械式定扭矩装置设计
第二章中介绍了定扭矩气动扳手所采用的片簧一转子结构定扭矩装置的结构设计。
由理论分析可知,该结构的定扭矩装置输出扭矩有个最大值,可以用来控制扭矩。
当把定扭矩装置放置到气动扳手中,可将定扭矩装置放在气动发动机和冲击部分之间,其结构示意图如图3.6。
转子与气动发动机相连,片簧、内圈与气动扳手冲击部分相连。
通过控制冲击部分的输入扭矩来控制气动扳手作用到螺纹紧固件上的扭矩。
由于气动扳手是装配生产中使用的机动扳手,通常要求其尺寸小,重量轻,适合单人操作。
故对于具有扭矩控制的气动扳手不仅要求能够控制输出扭矩,而且要求气动扳手的尺寸不能很大。
同时,要求定扭矩气动扳手在输出扭矩达到预定值后能自动切断气源以便降低气动扳手的耗气量,节约产品的装配成本,并且希望定扭矩气动扳手能够给操作工发出扭矩达到规定值的信号,也就是要求定扭矩气动扳手在扭矩达到预定值时具有自动切断气阀、自动报警功能。
考虑到这些因素和功能要求,当把定扭矩装置集成到气动扳手中时,需要对定扭矩装置和气动扳手的结构进行改进。
需要考虑定扭矩装置如何与气动扳手中各部件连接,如何在保持定扭矩装置一定输出扭矩时缩小定扭矩装置的尺寸以及如何实现扭矩达到时自动切断气阀、自动报警等功能。
本课题中定扭矩气动扳手是以BQG16型气动扳手为基础,根据BQG16型气动扳手应用范围,要求气动扳手的输出扭矩控制在10ON.m,则定扭矩装置中片簧一转子结构所允许的最大扭矩[M]=100N.m。
由BQG16型气动扳手的气动发动机输出轴的直径和联接平键的强度要求可确定转子半径r=15mm,滚柱半径rT=5mm,片簧与内圈中心线的夹角α=450。
,并由此可确定内圈半径R=25mm。
由前面介绍的片簧一转子结构的设计步骤可知:
当确定转子半径r、滚柱半径rT、角α和内圈半径R后,可以设计片簧的结构。
设计计算时,可先假设片簧的惯性矩I=4mm4,利用式(2.1)(2.2)(2.3)得到片簧一转子结构最大输出扭矩时对应的角βm值,βm=6.527。
。
由于最大输出扭矩Mmax与片簧的惯性矩I成正比,故对于等截面的片簧,由要求的最大输出扭矩值[M]可确定片簧的惯性矩I=13.5mm4。
若片簧的截面为矩形并且知道片簧的宽度b=6mm,则由矩形截面惯性矩计算公式
3.3气源自动切断装置
定扭矩气动扳手自动切断气阀装置应在气动扳手输出扭矩达到最大值后,能自动切断气动发动机的进气,并且能在气动扳手关闭后恢复到工作前状态,为气动扳手的下一步正常工作做好准备。
根据现有的定扭矩装置和气动扳手的特点,利用气压差特性设计了一套自动切断气动发动机进气的装置,其装置的结构如图3.8。
图中(a)为定扭矩部分控制结构图,(b)为自动切断气源部分的视图,(C)为气动发动机进气控制阀的侧视图。
花键联接套上装有花键销,内圈端面上有凸台,用来控制花键销沿径向的伸缩运动,花键销可以与外圈上内花键啮合。
控制杆和控制阀杆靠近末端处各有一半圆形槽。
由于气动扳手使用压缩空气作为工作介质,气动发动机的进气控制阀的内外存在压力差。
当定扭矩气动扳手正常工作、气动扳手的输出扭矩没有达到预定值时,花键联接套上的花键销没有与外圈上的内花键啮合,外圈不随花键联接套转动。
由于控制杆末端圆柱体插入控制阀杆的半圆形槽中,勾住控制阀杆,使得控制阀套内外的压力差不能使控制阀杆关闭控制阀套,压缩空气可以通过控制阀套进入气动发动机。
当扭矩快达到预定值时,内圈上的凸台开始推动花键销往外运动,与外圈的内花键啮合,从而使花键联接套带动外圈转动。
当外圈转动时,外圈上的凸台使控制杆向下运动。
这时控制阀杆与控制杆的半圆形槽相对,控制杆无法勾住控制阀杆。
控制阀套内外压力差克服控制阀弹簧的弹力,压缩控制阀弹簧使控制阀杆右移,关闭控制阀。
这样,压缩空气无法进入气动发动机中,气动发动机不能做功。
同时控制阀杆在右移关闭控制阀时,其末端圆柱体插入到控制杆半圆形槽中,挡住控制杆的回退运动,使控制杆不能复位。
当操作工关闭气阀后,控制阀套的内外压力差相等,控制阀弹簧的弹力使得控制阀杆离开控制阀套,恢复到工作前的位置。
此时,控制阀打开,控制阀杆上的半圆形槽与控制杆相对,控制杆在控制杆弹簧作用下复位,控制杆末端圆柱体插入到控制阀杆的半圆形槽中,控制杆重新勾住控制阀杆。
第四章信号检测与数据处理方法及程序举例
4.1自动检测控制装置
原理:
工作时,单片机通过I/O模块和驱动模块驱动气源加载,实施采集扭矩扳手测量仪的数据,检测判定达到峰值后,记录数据,并驱动关闭气源。
4.2电路组成
控制程序主要功能包括采集数据,发出控制信号,数据处理与维护等,单片机与检测仪器实时通讯,单片机的P0口的八位接I/O模块,用来接收扭矩传感器的信号,中间的电路部分见附录A,其中8255A为方式0,A口输入,B口输出,8255的片选信号CS及地址线A0,A1,分别由单片机的P0.7和P0.0,P0.1经地址锁存器提供,因此8255A的A,B,C口及控制口地址分别是FF7CH,FF7DH,FF7EH,FF7FH.下面是利用汇编语言编制的信号采集程序片段:
MOVAL,98H
OUTFF7FH,AL
MOVAL,00H
OUTFF7DH,AL
ADDAL,10H
OUTFF7DH,AL
SUBAL,10H
LOOP:
INAL,FF7EH
TESTAL,FF70H
JZLOOP
INAL,FF8OH
INAL,FF7CH
HLT
单片机的P1.0接电磁换向阀,采用双向可控硅电路,
假设预设值存入寄存器R0中,采样值存入寄存器R1中,则逻辑判断程序如下
ORG 0000H
START:
MOVAL,PO
CMPAL,@RO
JCLP1
MOVAL,00H
OUTP1.0,AL
LP1:
MOVAL,01H
OUTP1.0,AL
HLT
下面是采用LCD显示的程序片段:
心得体会:
通过本课程设计的整个设计制作过程,初步了解了利用系统设计原理和综合集成技巧,以及如何将控制电动机、传感器、机械系统、微机控制系统、接口及控制软件等机电一体化要素进行优化配置,合理选型,从而组成各种性能优良、可靠的机电一体化产品或系统。
初步掌握了机电一体化系统设计的基本概念、基本原理和基本知识;基本熟悉了机电一体化系统设计中的常用机械量检测传感器、控制电动机的原理、结构、性能和应用;初步掌握了机电一体化系统设计的原理和综合集成技巧,从而为今后的毕业设计及工作奠定良好的基础。
参考文献:
1甘作霖,王鹤.液压脉冲气扳机.1991(3):
15一20
2刘志峰.绿色产品设计与可持续发展.机械设计.1997
(1):
l一3
3黎永泉.80年代国外凿岩机械气动工具的发展.1990
(2):
28一37
4黎永泉.国外装配用气动工具现状.1993(l):
35一38
5刘见恒译.冲击式气扳机的紧固扭矩自动控制装置.1982
(2):
52一53
6《机械设计手册》联合编写组.机械设计手册.北京:
化学工业出版社.1987.12
7李富成.叶片式气动马达气缸上进、排气口位置及大小的确定.凿岩机械与风动工具.1986
(2):
17一26