工艺管道专业工程质量检查与验收标准.docx
《工艺管道专业工程质量检查与验收标准.docx》由会员分享,可在线阅读,更多相关《工艺管道专业工程质量检查与验收标准.docx(24页珍藏版)》请在冰豆网上搜索。
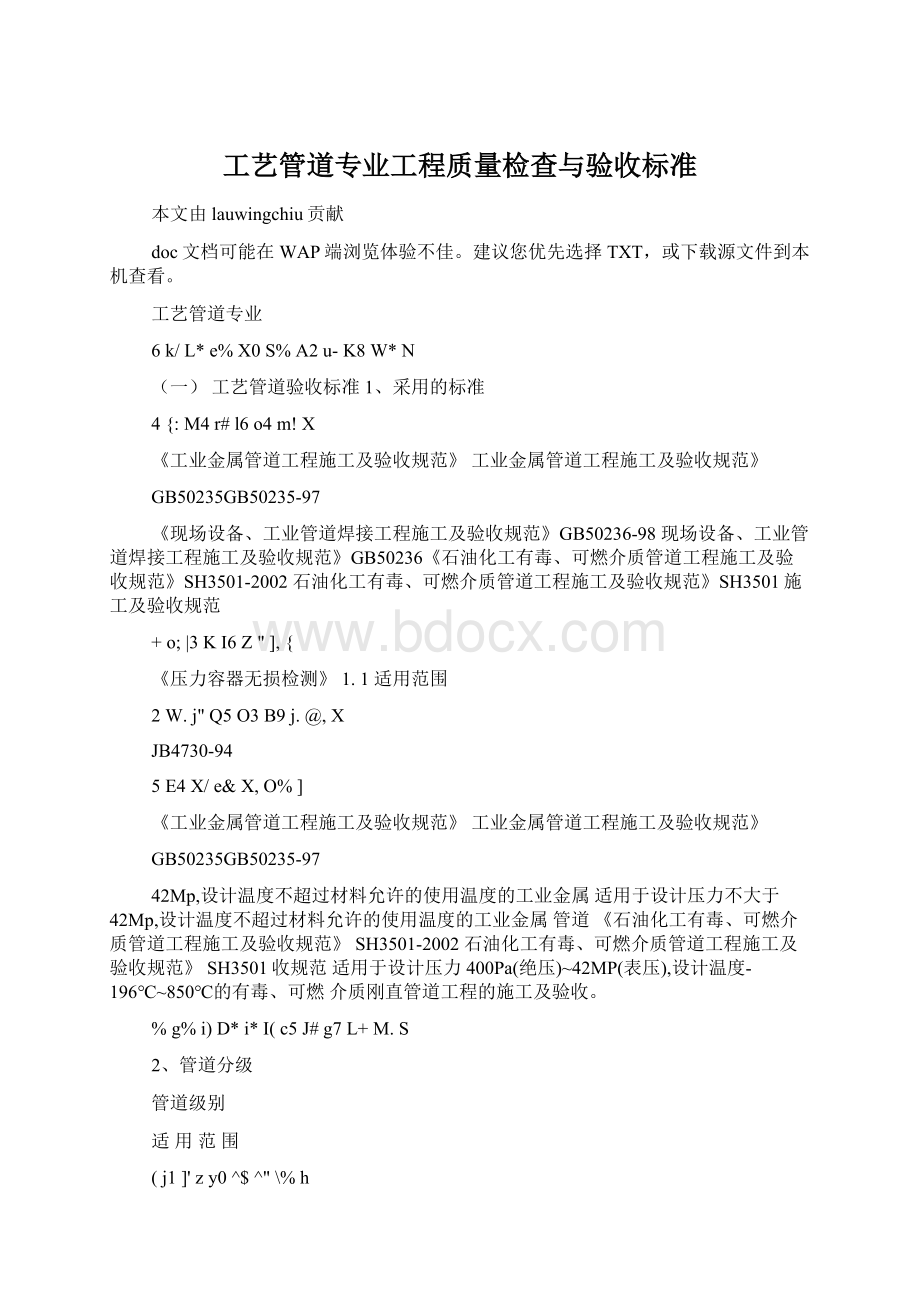
工艺管道专业工程质量检查与验收标准
本文由lauwingchiu贡献
doc文档可能在WAP端浏览体验不佳。
建议您优先选择TXT,或下载源文件到本机查看。
工艺管道专业
6k/L*e%X0S%A2u-K8W*N
(一)工艺管道验收标准1、采用的标准
4{:
M4r#l6o4m!
X
《工业金属管道工程施工及验收规范》工业金属管道工程施工及验收规范》
GB50235GB50235-97
《现场设备、工业管道焊接工程施工及验收规范》GB50236-98现场设备、工业管道焊接工程施工及验收规范》GB50236《石油化工有毒、可燃介质管道工程施工及验收规范》SH3501-2002石油化工有毒、可燃介质管道工程施工及验收规范》SH3501施工及验收规范
+o;|3KI6Z"],{
《压力容器无损检测》1.1适用范围
2W.j"Q5O3B9j.@,X
JB4730-94
5E4X/e&X,O%]
《工业金属管道工程施工及验收规范》工业金属管道工程施工及验收规范》
GB50235GB50235-97
42Mp,设计温度不超过材料允许的使用温度的工业金属适用于设计压力不大于42Mp,设计温度不超过材料允许的使用温度的工业金属管道《石油化工有毒、可燃介质管道工程施工及验收规范》SH3501-2002石油化工有毒、可燃介质管道工程施工及验收规范》SH3501收规范适用于设计压力400Pa(绝压)~42MP(表压),设计温度-196℃~850℃的有毒、可燃介质刚直管道工程的施工及验收。
%g%i)D*i*I(c5J#g7L+M.S
2、管道分级
管道级别
适用范围
(j1]'zy0^$^"\%h
1、毒性程度为极度危害介质管道(苯管道除外)2、毒性程度为高度危害介质的丙稀腈、光气、二硫化碳和氟化氢SHA介质管道
;_0H2r5R1q!
g*s
3、设计压力不大或等于10.0Mp输送设计压力不大或等于输送有毒、可燃介质管道SHB1、毒性程度为极度危害介质的苯管道2、毒性程度为高度危害介质管道(丙稀腈、光气、二硫化碳和氟
化氢管道除外)体介质管道
;N:
r'd2Q#T
3、甲类、乙类可燃气体和甲A类液化烃、甲B类、乙A类可燃液
&d'E@8@/z#N0C
1、毒性程度为中度、轻度危害介质管道SHC2、乙B类、丙类可燃液体介质管道SHD
/|&F7g9I0d'P
设计温度低于-29℃的低温管道
"F+v9R)P#x*S2p1B6]
3、管道组成件的检验
*s9c7c5d"G/[)N
3.1管材、管件、阀门必须具有制造厂的质量证明书。
3.2管材、管件使用前应进行外观检查,表面应符合下列要求。
--无裂纹、缩孔、夹渣、折叠、重皮等缺陷。
--有材质标记。
%Y5?
"?
4O'Y-T5\"z(]!
a
--无超过壁厚负偏差的锈蚀、凹陷及机械损伤。
3f&].C;v4N4U(P*]!
{
)Q-?
$lj(F0s+{
3.3材料使用前应认真按设计要求进行核对管线的材质、规格。
3.4管道组成件及管道支撑件在施工过程中应妥善保管,不得混淆或损坏,其色标或标记应明显清晰。
3.5暂时不能安装的管子,应封闭管口。
3.6阀门检验3.6.1用于本工程的阀门产品,应符合设计文件中“阀门规格书”的要求。
%C-K7fk4y-E*R-D%@
3.6.2阀门的质量证明书应有下列内容:
1、制造厂名称2、阀门名称、型号、规格、公称压力3、适用介质,温度
$~"z+{+\`(~4_
4、出厂日期
3J#r/K9W8M6A6f2],p"}&b
5、产品标准代号、质量检查结论
2C"^,K%^3\0t4X(T)G7i#u
6、制造厂检验单位及检验人员的印章
$C"`8X3p!
a+G&L
3.6.3阀门的外观质量应符合下列要求:
9n,K,M1@6H#?
/Z8A"k!
Q
1、阀门上应有制造厂的铭牌,铭牌上应标明:
阀门名称、型号、公称压力、公称直径、工作温度、制造厂名;2、阀门的壳体上应注有公称压力、公称直径、介质流向等标识;3、阀体不得有损坏、锈蚀、缺件、脏污、铭牌脱落、色标不符等;4、阀门的手柄或手轮应操作灵活轻便,无卡涩现象;5、阀门两端的临时端盖应完好,封闭严实,阀体内无杂物;
用。
*c5A'V,]5g;@1i.e
3.6.4下列管道的阀门,逐个进行壳体压力试验和密封试验。
不合格者,不得使
1)输送有毒流体、可燃流体管道的阀门;2)输送设计压力大于等于1MP、或设计压力小于等于1MPa且设计温度大于186℃的非可燃流体、无毒流体管道的阀门3)输送设计压力设计压力小于等于1MPa且设计温度为-29~186℃非可燃流体、无毒流体管道的阀门应从每批中抽查10%,且不得少于1个进行壳体压力试验和密封试验。
当不合格时,应加倍抽查,仍不合格时,该批阀门不得使用。
B.VQ+{8?
)s"f6x4G.]7y9v
3.6.5阀门的壳体实验压力不得小于公称压力的1.5倍,试验时间不得小于5min。
以壳体填料无渗漏为合格;密封试验以公称压力进行,以阀瓣密封面不漏为合格。
3.6.6试验合格的阀门,及时排净内部积水,吹干。
除需要脱脂的阀门外,密封面上应涂防锈油,关闭阀门,封闭出入口,做出明显标记。
4、管道预制加工
4.1管道预制按预制加工图进行预制并满足下列要求:
7h4M$Za;b,a3@
4.1.1管道预制加工按现场审查确认的管段预制图进行。
预制加工图应标注现场组焊位置和调节裕量;4.1.2现场组焊的焊缝应便于施焊与检验。
4.2管道预制过程中每一道工序都要核对其标记,并做好标记移植。
管道切割、4.3管道切割、坡口加工4.4弯曲度超过允许偏差的钢管,在加工前进行调直。
碳素钢管可冷调或热调,不锈钢管应冷调。
5T&F-Z'n7Q;u
4.5钢管冷调在常温下进行,公称直径不大于50mm的管子,在管子调直机调直,其压模应与钢管外径相符。
+`h%l#f(k)o;A
4.6碳素钢管热调时应将钢管的弯曲部分加热到800~1000℃,然后平放到平台上反复滚动,使其目然调直,也可采用火焰调直法。
9f8N0N&f8J3R,l
4.7钢管下料时应按预制加工图的尺寸号料。
切割时应符合下列规定:
3H/O4I(V4~
4.7.1、不锈钢管应用机械或等离子方法切割:
%P$`&k8b0~6\2|1m
4.7.2、碳素钢管可用火焰切割,并必须除去影响焊接质量的表面层。
$I3E%|2l)y:
Z)M
4.8钢管的焊接坡口加工应符合下列要求:
%E8o6M1T$_!
K:
R%Z+\,T
4.8.1、碳素钢管,宜用机械方法加工,亦可采用火焰加工:
;P&x4b*~!
e
4.8.2、不锈钢管应采用机械方法加工。
不锈钢管若用砂轮切割或修磨时,必须用专用砂轮片。
-x-t/I7x2c
4.8.3、若用火焰或等离子加工钢管后,必须除去影响焊接质量的表面层。
4.9焊接坡口两侧的壁厚差大于下列数值时,应按要求削薄进行加工。
#X3B*R7\*C*x
4.9.1SHA级管道的内壁差0.5mm或外壁差2mm;4.9.2.SHB、SHC级管道内壁差1mm或外壁差2㎜;4.9.3.其余管道外壁差3mm。
4.10坡口的质量应下列要求:
3|:
`5\5O2P!
Y%H'l;h7l9~'`'{7Q+@+]+d0g8r4B
4.10.1、表面平整,不得有裂纹、重皮、毛刺、凸凹缩口;4.10.2、切割表面的熔渣、氧化铁、铁屑等应予以清除;
7L4x+`9k$r;B'V(_6v+g
4.10.3、端面倾斜偏差为管子外径的1%,但不得超过2㎜;4.10.4、坡口尺寸和角度应符合要求。
管道组对、4.11管道组对、预组装
+G+s-p/L#y
8r8I;E.T9j'`
m6b!
i:
A#h
4.12管段组对时,座垫置牢固,定位可靠,防止在焊接过程中产生变形。
4.13管段对口时应检查组对的平直度,允许偏差为1㎜/m,但全长的最大累计偏差不得超过10mm。
4.14管道组成件组对时,使用内径对口器。
0D.g)K)z/B!
f7\3R
4.14.1、管段组对时,不得采用强力对口或加热管子的方法来消除接口端面的过量间隙、错边与不同心等缺陷。
当发现这些缺陷时,应检查相邻或相关管段的尺寸,然后对产生缺陷的部位应进行校正和返工。
4.15管道上仪表取源部件应按规定位置先钻孔后焊接。
温度计取源部件的开孔,不得向里倒角。
2e!
Q,k$i-V;]7r
4.16管道预组装前,应对管道组成件进行检查与清理,具备下列条件方可组装:
9P.h)Q'b)Q"B"?
(v
4.16.1、管道组成件的材质、规格、型号应符合设计要求;
8D6U1z9A*u3?
0j5q!
h6K
4.16.2、管道组成件内外表面的泥土、油垢及其他杂物等已清理干净:
0o1z+g3N4F:
z/{
4.16.3、标识齐全。
4.17管道预组装时,应检查总体尺寸与各部尺寸及调节裕量,它们的偏差应符合下列要求:
4j5\+d6f"j3r
4.17.1每个方向总长L允许偏差为±5㎜;4.17.2间距N,允许偏差为±1.5㎜;
!
A;t,R:
M*S
4.17.3支管与主管的横向偏差c,允许值为±1.5mm;
#k-W,V5\3l
4.17.4法兰面相邻的螺栓孔应跨中安装,f的允许偏差为±lmm;4.17.5法兰端面应垂直,e的允许偏差为:
a.公称直径小子或等于300mm时不大于lmm;b.公称直径大于300mm时不大于2mm。
4q5G,J(K%v+H
0v+\%_+v+q(w3O6F,^
4.18壁厚相同的管道组对时,内壁平齐,其错边量不超过下列规定SHA级管道为壁厚的10%,且不大于0.5mm;SHB、SHC级管道内壁差1.0mm或外壁差2mm;
2c;i/W5J!
Q+U(E
+r6}0H!
L)e(g0e7w
4.19管道预制应方便运输和安装,组合件应有足够的刚度与强度,否则应有临时加固措施,必要时应标出吊装索具捆绑点的位置。
4.20管段预制完成后,应做好编号及防护保管工作。
4.21管道支吊架制作、安装道支吊架制作、
S,U)d4\&J&`)V)m"v0I$}#u']!
f#]2o9Q(M#G.f
4.21.1管道支、吊架应在管道安装前根据设计零件图及需用量集中加工,提前预制。
管道支、吊架的型式,加工尺寸、材质应符合设计要求。
钢板、型钢用机械切断,切断后应清除毛刺。
机械剪切切口质量应符合下列要求:
"?
-S6}(^0Y2X"V
(1)、剪切线与号料线偏差不大于2㎜;
(2)、切口处表面无裂纹;(3)、型钢端面剪切斜度不大于2㎜。
*K;H
(c8J+k;a/O;I
N)m-K)_'~(A.B
4.21.2采用热切割时,应清除熔渣和飞溅物,其切割质量应符合下列要求:
7q#w;];e-@._;q;y+TP
⑴、手工切割的切割线与号料线的偏差不大于2㎜;
6\%a)k4H+i9@#l&p7iL
⑵、切口端面垂直度偏差应小于工件厚度的10%,且不大干2mm。
*^,B7z6@;g
4.21.3管道支、吊架的螺栓孔,用机械方法加工。
.P;z#^0A)f(|4?
/i
4.21.4管道支、吊架的卡环或“U”型卡用扁钢弯制而成,圆弧部分应光滑,尺寸应与管子外径相符。
4.21.5支架底板及弹簧支、吊架弹簧盒的工作面平整光洁。
滑动或滚动支架的滑道加工后,采取保护措施,防止划伤或碰损。
4.21.6管道支、吊架制作组装后,外形尺寸偏差不得大于3mm,并作编号和标识。
4.21.7管道安装时,及时调整和固定支、吊架位置准确,安装平整牢固,与管子接触紧密。
4.21.8安装完毕后,按设计图纸规定逐个核对支、吊架的形式和位置。
8h)\5O6m!
p.{5{
4.21.9无热位移的管道,其吊杆垂直安装。
有热位移的管道,吊点设在位移的反方向,按位移值的1/2偏位安装。
5、管道安装
9v'I4M#y:
L*t'H
5.1敷设管道的管廊、管道支柱、低管架的混凝土支墩、预埋件、预留孔等已按设计文件施工完。
坐标位置、标高、坡度符合要求,且混凝土强度达到75%以上;
.a4_-F&c0@
5.2与管道连接的设备已找正合格、固定完毕,二次灌浆后检强度达到要求;
*i3_:
D$a0?
.S'}-v8y#v:
O
5.3设备上为安装、焊接管道支、吊架用的护板,位置及数量应能满足管道安装的要求;
1c3a#X"r*a8u
5.4管道安装应具备下列条件:
5.4.1管道组成件应具有所需的质量证明文件,并经检验合格;5.4.2管道组成件已按设计要求进行核对,其材质、规格、型号正确;管道预制已按图样完成,并符合要求:
5.4.3管道安装前应完成的有关工序,如无损检测、外部防腐等已进行完毕,并符合要求;
1M!
R%?
*Z/i'n"~)T
5.5管道安装按下列顺序进行:
5.5.1、先大管道后小管道;
B)O1Z$h7A:
{'G3U;P
5.5.2、先高压管道后低压管道;
*O2Z.C9b/@4z1|&D
5.5.3、先合金钢管道后碳素钢管道;5.6预制的管道应按管道系统号和预制顺序号安装。
z/@6?
:
?
.F0j4h6m%C$X
5.7管道安装时,检查法兰密封面及垫片,不得有划痕、斑点等缺陷。
#o)e3I7T-c4O0M-g'A0{
5.8法兰连接应与管道同心,并保证螺栓自由穿入。
法兰螺栓跨中安
装。
法兰间保持平行,其偏差不大于法兰外径的1.5‰,且不大于2mm,不得强紧螺栓来消除歪斜。
5.9拧紧螺栓时,不得将密封材料挤入管内。
5.10法兰连接使用同一规格螺栓,安装方向一致。
螺栓紧固后与法兰紧贴,不得有楔缝。
5.11管道连接时,不得用强力对口或加多层垫来消除接口端面间隙。
/|0X%d'@1R1a2?
8Z1g#u
5.12与转动机器连接管道,从机器侧开始安装,先安装管支架,其水平度或垂直度偏差小于1mm/m。
5.13与机器连接管道,其支、吊架先安装,不得将管道及其阀门重量或力矩附加在设备上。
待安装完毕卸下接管上法兰螺栓,在自由状态所有螺栓能在其孔中顺利通过。
7c*w8h$i$dH2x
5.14有静电接地要求管道,各段管道间应导电良好。
用做静电接地材料或零件安装前不得刷油。
5.15与机泵连接的管道,安装前先将泵进出口封住,防止异物掉入泵体内。
连接机泵的管道,其固定焊口应远离机器。
管道安装合格后,不得承受设计以外的附加载荷。
5.16管道安装时,不宜使用临时支吊架。
当使用临时支吊架时,不得将其焊在管道上。
在管道安装完毕后,应及时更换成正式支吊架。
;N:
@0H+X7d'y4b7^
5.17管道安装有间断时,及时封闭敞口管口。
5.18管道安装合格后,不得承受设计外载荷。
0e-g0W6B2u
K&^
5.19管道组成件内部及焊接接头附近已清理干净,没有油污或杂物:
5.20管道安装的坡向、坡度应符合设计规定,若设计无规定时,符合下列要求:
⑴、重力流管道、易冷凝的气体管道,易液化的气体管道,在安装时应有坡度.使排液畅通:
⑵、每段管道应有连续一致的坡度,不得有倒坡现象。
&}-t4F/h6{*h+n*H:
c'C2`
5.21管道的坡度,用支座下的金属垫板或吊杆螺栓调整。
垫板应加在主管道支座底板与基础顶板之间,且应与预埋件或钢结构进行焊接。
5.22法兰、活接头及其他连接件和焊缝的位置应便于检修,不得紧靠墙壁、楼饭、沟壁、平台、梯子或管道支、吊架。
%?
;@$[.D%B3r(a7Y
5.23安装管道时不宜焊接临时支撑物,若需焊接时,应符合焊接工艺的有关规定。
5.24管道安装工作若有中断,应及时封闭敞开的管口。
安装相连的管道时,应对前期安装的管道内部进行检查,确认管内无异物后,再进行安装。
5.25管道安装前应进行内部清理,清理作业可根据设计对管道内部清洁程度的要求及管径的大小,采用不同的清理方法:
4m%f$Y&G;p
⑴、公称直径200~550mm的管道,可用弧形板拖扫或将管子直立,同时以木锤敲打管壁,使管内的铁锈及污物彻底倾出;⑵、公称直径80~200mm的管道。
可用拖布、毛刷、钢丝刷在管内反复拖拉,直至干净;⑶、公称直径等于或小于80mm的管道,用压缩空气吹净:
5.26法兰装配前应对相应的尺寸进行测量,直径应相符,管子圆度若
有超差必须予以矫正。
对焊法兰内径与管子内径的偏差不应超过营于壁厚的10%,且不大于0.5mm。
5.27法兰装配时,应使密封面与管子中心线垂直,以法兰密封面为基准进行测量,垂直度偏差不应超过法兰外径的0.25%,且不大于2mrn。
5.28法兰装配时,可先在上方进行定位焊接,然后用法兰角尺沿上下方向找正,合格后在下方进行定位焊,再找正左右两则并进行定位焊。
1e&\1H;Q:
G&r
5.29同一管段的两端有焊接法兰时,应将管段找平、找正,先焊好一端法兰,然后以此法兰为基准,用线坠或水平尺找正后,再装配另一端的法兰。
5.30伴热管安装
)C.}%^3Q;`+K
⑴伴热管在安装时必须熟悉哪些部件应有伴管及如何敷设,细致地进行伴管走向布置,保证冷凝液顺利排防,并作到排列美观,操作方便。
⑵伴管安装的位置:
对水平管道安装在下方,垂直管道的伴管均匀分布在主管周围。
不得将伴热管直接点焊在主管上,采用钢带或镀锌铁丝等固定在主管上:
弯头部位的伴热管绑扎带不得少于三道。
这种间距应适当缩短。
9x'I.r8_-u!
\6?
.p/r9q4u
⑶伴热管绑扎点以1m间距固定,在伴热管与被伴管不能紧密接触的弯头处,
管道的静电接地5.31管道的静电接地
⑴有静电接地要求管道,各段管道间应导电良好。
用做静电接地材料或零件安装前不得刷油。
⑵静电接地安装完毕后,必须进行测试,电阻值超过规定时,进行检查。
合格后及时填写管道静电接地测试记录。
与不锈钢管直接连接。
与不锈钢管直接连接。
^4A.n9i-p*T$k
⑶有静电接地要求的不锈钢管道,导线跨接或接地线采用不锈钢板过渡,不得有静电接地要求的不锈钢管道,导线跨接或接地线采用不锈钢板过渡,
4a7y8X,y4c8Z,t
⑷管道系统静电接地线,采用焊接形式。
对地电阻值及接线位置符合设计要求。
管道系统静电接地线,采用焊接形式。
对地电阻值及接线位置符合设计要求。
置符合设计要求
(R*t7b'e$\
-b,l9a,B3Q
6、焊接工艺要求及焊接质量检验6.1一般工艺要求1)
4W,\4_*T+J3M5Y*v*y.i$y
DN≤60或壁厚δ≤4的焊缝采用全氩弧焊,其余焊缝采用氩弧
焊打底、手工电弧焊填充及盖面的工艺或手工电弧双面焊工艺。
2)4)接5)所有伴热线可采用氩弧焊工艺。
3)承插焊缝至少焊接两遍。
多层焊时各层、道之间的接头相互错开。
6.2奥氏体不锈钢的焊所有焊缝均采用氩弧焊打底的焊接方法,氩气纯度不低于
99.9%,DN≥400的焊缝由于口径大,内部充氩保护较难达到效果,安装焊缝采用不需充氩的药芯焊丝进行施焊(不包括压缩机润滑油管线)作为钨极氩弧焊的补充。
6)手工电弧焊填充及盖面时,在坡
口两侧各不小于100mm范围内的母材上涂以白垩粉,以防焊接飞溅损伤母材。
7)采用小线能量施焊。
8)层间用角向磨光机进行彻层间及表面采用不锈钢钢丝
底清理,打磨使用白刚玉砂轮片。
9)
刷清理,且不得与碳素钢混用。
10)管材及配件用胶皮或石棉布垫放,且不得与碳钢混放。
11)焊接并检验完毕后应及时对焊缝外表面进行酸洗。
现场安装时若存在交叉作业,应对管道对可能的污染部位覆盖石棉布。
0^.tf(z/Bw
6.3低温钢焊接12)所有焊缝均采用全焊透工艺。
13)焊件组对前,应将坡口表面的氧化物、油污、挂渣及其它有害杂质清除干净。
消除范围为坡口及其两侧母材不少于20mm区域。
14)不得采用锤击等
强制手段进行组装,不得在母材表面刻划或敲打材料标记和焊工钢印
等,以防形成产生缺口效应的划痕。
15)至15℃以上方可施焊。
16)
环境温度低于0℃时预热
焊接过程必须严格控制焊接线能量不
超过30KJ,尽量选用较小的焊接线能量,采用多层多道法施焊。
17)焊件表面严禁有电弧擦伤。
焊接时,不得在焊件表面引弧、焊接收弧时应将弧坑填满,并用砂轮磨去临时
收弧和试验电流。
18)
弧坑缺陷。
多层焊时各层间的接头应错开30~50mm。
19)
点固到管道上的卡具采用砂轮机拆除、修磨,并进行着色检查,不得采用敲打的方法强行拆除。
6.4异种钢焊接异种钢由于物理和化学性能差
别较大,异种金属的焊接问题比同种金属复杂,施焊中的主要问题是如何防止裂纹、脱碳和组织不均匀性。
1)焊接工艺必须以工艺评定为基础。
2)焊工资格确认必须严格,优先安排优秀焊工进行施焊。
3