丙烯腈反应系统设计.docx
《丙烯腈反应系统设计.docx》由会员分享,可在线阅读,更多相关《丙烯腈反应系统设计.docx(25页珍藏版)》请在冰豆网上搜索。
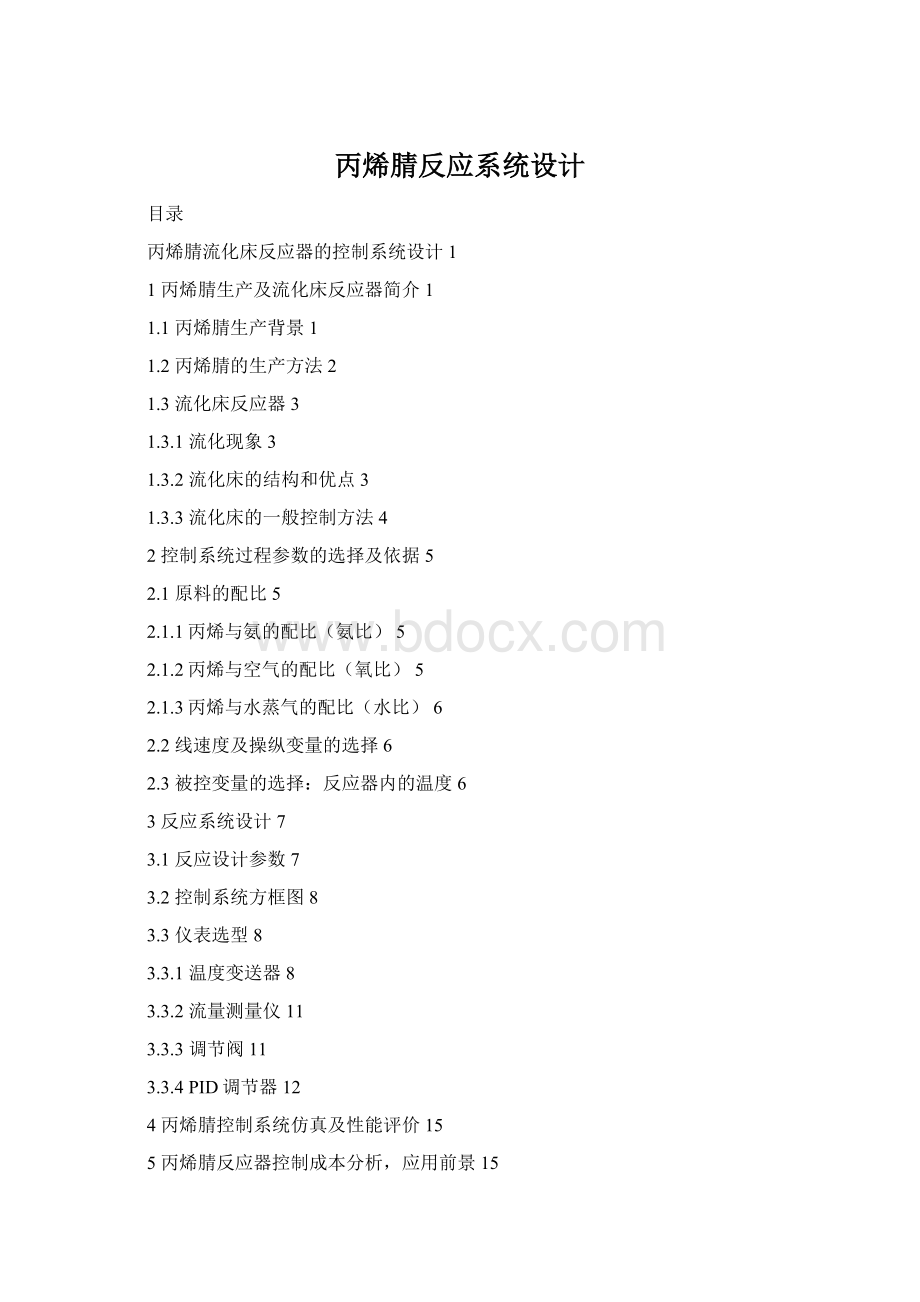
丙烯腈反应系统设计
目录
丙烯腈流化床反应器的控制系统设计1
1丙烯腈生产及流化床反应器简介1
1.1丙烯腈生产背景1
1.2丙烯腈的生产方法2
1.3流化床反应器3
1.3.1流化现象3
1.3.2流化床的结构和优点3
1.3.3流化床的一般控制方法4
2控制系统过程参数的选择及依据5
2.1原料的配比5
2.1.1丙烯与氨的配比(氨比)5
2.1.2丙烯与空气的配比(氧比)5
2.1.3丙烯与水蒸气的配比(水比)6
2.2线速度及操纵变量的选择6
2.3被控变量的选择:
反应器内的温度6
3反应系统设计7
3.1反应设计参数7
3.2控制系统方框图8
3.3仪表选型8
3.3.1温度变送器8
3.3.2流量测量仪11
3.3.3调节阀11
3.3.4PID调节器12
4丙烯腈控制系统仿真及性能评价15
5丙烯腈反应器控制成本分析,应用前景15
6设计历程及总结15
参考文献15
PPT制作思路:
17
遗留问题17
丙烯腈流化床反应器的控制系统设计
1丙烯腈生产及流化床反应器简介
1.1丙烯腈生产背景
丙烯腈是一种重要的有机化工原料,源自石油、煤、天然气的重要基础有机化工原料,全球丙烯的产能已超1亿吨/年。
主要应用于合成树脂、合成纤维及合成橡胶的生产。
目前,国内十多家丙烯腈生产商基本采用丙烯氨氧化法来生产丙烯腈。
近年,国内丙烯腈的产能和产量稳步增加。
丙烯腈以其在ABS合成树脂方面等的应用及我国未来一段时间ABS的迅猛需求将有较好的市场前景。
1.2丙烯腈的生产方法
当前生产丙烯腈的主要方法是丙烯氨氧化法,它是以丙烯、氨、空气和水为原料,按其一定量配比进入沸腾床或固定床反应器,在以硅胶作载体的磷钼铋系或锑铁系催化剂作用下,在400-500℃温度和常压下,生成丙烯腈。
然后经中和塔用稀硫酸除去未反应的氨,再经吸收塔用水吸收丙烯腈等气体,形成水溶液,使该水溶液经萃取塔分离乙腈,在脱氢氰酸塔除去氢氰酸,经脱水、精馏而得丙烯腈产品,其单程收率可达75%,副产品有乙腈、氢氰酸和硫酸铵。
此法是最有工业生产价值的生产方法。
该法具有原料价廉易得、工艺流程简单、设备投资少、产品质量高、生产成本低等许多优点。
丙烯氨氧化法:
主反应:
CH=CH-CH3+NH3+O2→CH2=CH-CN+3H2O
副反应:
CH2=CHCH3+3NH3+3O2→3HCN+6H2O
氢氰酸的生成量约占丙烯腈质量的1/6
CH2=CHCH3+NH3+O2→CH3CN+3H2O
乙腈的生成量约占丙烯腈质量的1/7
CH2=CHCH3+O2→CH2=CHCHO+H2O
丙烯醛的生成量约占丙烯腈质量的1/100
CH2=CHCH3+O2→3CO2+3H2O
二氧化碳的生成量约占丙烯腈质量的1/4,它是产量最大的副产物。
上述副反应都是强放热反应,尤其是深度氧化反应。
在反应过程中,副产物的生成,必然降低目的产物的收率。
这不仅浪费了原料,而且使产物组成复杂化,给分离和精制带来困难,并影响产品质量。
为了减少副反应,提高目的产物收率,除考虑工艺流程合理和设备强化外,关键在于控制影响反应的各个因素,尤其是温度。
1.3流化床反应器
由于丙烯腈氧化反应是强放热,所以工业生产中多采用流化床反应器。
流化床反应器是气相反应常用的一种反应器。
当反应气体通过反应器时,催化剂颗粒受到气流的作用悬浮起来,在反应器内作剧烈的翻滚、流动,整个系统与流动的或沸腾的液体很相像,所以称流化床或沸腾床。
1.3.1流化现象
对于固定床反应器,因为催化剂是固定的。
流体实际上只能在催化剂颗粒间的孔隙内穿流,不但催化剂的表面反应受到限制,降低了催化剂利用率。
而且,床层的温度分布不均匀,不能保证各部分都在最适宜的温度条件下进行化学反应。
如果减少颗粒大小,增加气流温度,且让气流由下自上通过,当气流速度达到某一值以后,催化剂在床内处于气流的湍动状态,大大增加了催化剂和气流的接触面积,既增加了催化剂的利用率,又改善了温度分布,这种固体在气流作用下产生像流体一样流动状态称流化态。
1.3.2流化床的结构和优点
为了保证流化和一定反应温度以及回收催化剂等原因,使流化床结构不同于固定床。
为适应流化状态、传热和催化剂回收等作用,流化床结构一般都由壳体、气体分布装置、内部构件、换热装置、气固分离装置和固体颗粒加卸载装置等组成。
常用流化床反应器有两种,一种是有固体物料连续进料和出料的装置,用于固相加工过程或催化剂迅速失活的流体相加工过程。
例如催化裂化过程,催化剂在几分钟内即显著失活,需用装置不断将其分离后进行再生。
另一种是无固体物料连续进料或出料装置,用于固体(催化剂)在长时间不发生明显变化的反应过程。
流化床反应器是气-固相催化反应常用的一种反应器。
图1:
丙烯腈流化床反应器示意图
丙烯腈反应所采用的流化床就属于后一种,催化剂长期不发生明显变化,且进料都是气体。
液态的丙烯与液氨经过气化后,在管路中汇合后经反应器底部的丙烯、氨分布器进入反应器,压缩空气经反应器底部的空气分布器进入反应器,一定的流动速度使催化剂颗粒呈悬浮状态,三种物料在处于流化状态下的催化剂的作用下,生成丙烯腈。
与固定床反应器相比,丙烯腈流化床反应器具有以下优点:
1可以实现物料的连续输入和输出;
2流体和颗粒运动使床层具有良好的传热性能,床层内部温度均匀,可在最佳温度点操作,而且易于控制,特别适用于强放热反应,此外,由于颗粒的高热容和返混,能防止局部过热或过冷,操作比较稳定;
3颗粒比较细小,有效系数高,可减少催化剂的用量;
4压降恒定,不易受异物堵塞;
1.3.3流化床的一般控制方法
对单器流化床的基本控制方法是流化床浓相区温度为被调参数,调节手段为下列管换热器进水量和稳定反应物料流量。
在冷水流量变化较大情况下,应该用反应温度与冷却水流量串级调节,因为,对流化床下部列管换热器来说,冷却剂流量、温度等变化,对反应影响极大。
对中、上部列管换热器,由于对反应影响小,冷却剂有些扰动影响不大。
图2:
一般流化床反应器的温度控制
(此处还剩张恩邦的一小部分,和柳旭聪的有点重合)
2控制系统过程参数的选择及依据
2.1原料的配比
合理的原料配比,是保证丙烯腈合成反应稳定、副反应少、消耗定额低,以及操作安全的重要因素。
2.1.1丙烯与氨的配比(氨比)
在实际投料中发现,当氨比小于理论值1:
1时,有较多的副产物丙烯醛生成,氨的用量至少等于理论比。
但用量过多也不经济,既增加了氨的消耗量,又增加了硫酸的消耗量,因为过量的氨要用硫酸去中和,所以又加重了氨中和塔的负担。
因此,丙烯与氨的摩尔比,应控制在理论值或略大于理论值,即丙烯:
氨=1:
1~1.2左右。
2.1.2丙烯与空气的配比(氧比)
丙烯氨氧化所需的氧气是由空气带入的。
目前,工业上实际采用的丙烯与氧的摩尔比约为l:
2~3(大于理论值1:
1.5),采用大于理论值的氧比,主要是为了保护催化剂,不致因催化剂缺氧而引起失活。
反应时若在短时间内因缺氧造成催化剂活性下降,可在540℃温度下通空气使其再生,恢复活性。
但若催化剂长期在缺氧条件下操作,虽经再生,活性也不可能全部恢复。
2.1.3丙烯与水蒸气的配比(水比)
丙烯氨氧化的主反应并不需要水蒸气参加。
但根据该反应的特点,在原料中加入一定量水蒸气有多种好处,如可促使产物从催化剂表面解吸出来,从而避免丙烯腈的深度氧化;若不加入水蒸气,原料混合气中丙烯与空气的比例正好处于爆炸范围内,加入水蒸气对保证生产安全有利;水蒸气的热容较大,又是一种很好的稀释剂,加入水蒸气可以带走大量的反应生成热,使反应温度易于控制;加入水蒸气对催化剂表面的积炭有清除作用。
另一方面,水蒸气的加入,势必降低设备的生产能力,增加动力消耗。
当催化剂活性较高时,也可不加水蒸气,从目前工业生产情况来看,当丙烯与加入水蒸气的摩尔比为1:
3时,综合效果较好。
2.2线速度及操纵变量的选择
对于固定床反应器,因为催化剂是固定的。
流体实际上只能在催化剂颗粒间的孔隙内穿流,不但催化剂的表面反应受到限制,降低了催化剂利用率。
而且,床层的温度分布不均匀,不能保证各部分都在最适宜的温度条件下进行化学反应。
如果减少颗粒大小,增加气流温度,且让气流由下自上通过,当气流速度达到某一值以后,催化剂在床内处于气流的湍动状态,大大增加了催化剂和气流的接触面积,既增加了催化剂的利用率,又改善了温度分布,这种固体在气流作用下产生像流体一样流动状态称流化态。
因此,在反应器尺寸结构一定的情况下,物料流量要保持一定,以保证物料流动的速度使物料达到湍动状态,保证催化剂的利用率。
2.3被控变量的选择:
反应器内的温度
温度是影响丙烯氨氧化的一个重要因素。
当温度低于350℃时,几乎不生成丙烯腈。
温度的变化对丙烯的转化率、丙烯腈的收率、副产物氢氰酸和乙腈的收率以及催化剂的空时收率都有影响。
要获得丙烯腈的高收率,必须控制较高的反应温度。
丙烯氨氧化法生产丙烯腈时,除生成丙烯腈外,尚有多种副产物生成。
在反应过程中,副产物的生成,必然降低目的产物的收率。
这不仅浪费了原料,而且使产物组成复杂化,给分离和精制带来困难,并影响产品质量。
为了减少副反应,提高目的产物收率,除考虑工艺流程合理和设备强化外,关键在于控制影响反应的各个因素,尤其是温度。
图3:
丙烯氨氧化法生产丙烯腈反应温度-产物曲线
如图所示,反应温度高,丙烯腈单程收率高、副产少。
但当反应温度过高时,合成物易深度氧化,生成较多的CO2,温度难以控制;另外,若持续长时间的高温,还会缩短催化剂的寿命。
生产中,实际温度控制在460℃左右,丙烯腈收率取得最大值
同时,流化床工作的好坏,可以明显地从反应温度上表现出来,当反应状况良好时,反应温度易于控制。
所以,选择温度作为反应器的被控变量。
3反应系统设计
3.1反应设计参数
丙烯流量:
质量浓度99.5%以上,年工作日:
330天,回收率98%,年产1万吨,则丙烯腈原料液的流量应该为1294.8kg/h,丙烯腈物质的量流量为24kmol/h,则可以取丙烯的流量为25kmol/h
氨烯比:
1.15:
1
空烯比:
10.5:
1
3.2控制系统方框图
3.3仪表选型
3.3.1温度变送器
SK-SBW系列一体化温度变送器是温度传感器与变送器的完美结合,以十分简捷的方式把-200~+1600℃范围内的温度信号转换为二线制4~20mADC的电信号传输给显示仪、调节器、记录仪、DCS等,实现对温度的精确测量和控制。
一体化温度变送器是现代工业现场、科研院所温度测控的更新换代产品,是集散系统、数字总线系统的必备产品。
特点:
超小型(模块φ44×18)一体化,通用性强
二线制4~20mADC输出。
传输距离远,抗干扰能力强。
冷端、温漂、非线形自动补偿。
测量精度高,长期稳定性好。
温度模块内部采用环氧树脂浇注工艺,适应于各种恶劣和危险场所使用。
一体化设计,结构简单合理,可直接替换普通装配式热电偶、热电阻。
机械保护IP65。
采用热电偶温变,可免用补偿导线,降低成本
液晶、数码管、指针等多种指示功能方便现场适时监控。
现场环境温度>70℃时,变送器和现场显示仪表可采用分离(隔离)式安装
防爆等级:
EXdIIBT4、EXdIIBT6、EXdIICT6。
防护等级:
IP54
其技术指标如下:
类别
SK-SBW模块式温变
SK-SBW一体化温变
准确度
0.2%F.S0.5%F.S
输入
热电偶:
B、S、T、K、J
热电阻:
Pt100、Pt10、Cu100、Cu50
输出
二线制4-20mADC
使用温度
-25-85℃(一体化LCD表头时0-60℃)
温度影响
≤0.05%/℃
湿度
5-95%RH
现场显示
无
3 1/2LED31/2LCD0-100%等分刻度
显示精度
无
数字式:
0.5级指针式:
2.0级
负载能力
<600Ω(额定负载250Ω)
外形尺寸
44×18
70×100(中继器)
选型要求:
测温范围:
420℃——450℃
仪表使用要求:
精度高,抗干扰,防震防潮防爆,方便温度测量和变送
测量环境:
反应器内部:
易燃易爆,有剧毒(要密封),强氧化,55KPa;
反应器外部:
常温常压
热电偶的选择:
根据图中热电偶的测量范围和线性度,选择镍铬-铜镍型热电偶。
热电偶的时间常数为60s(1min)。
具体型号选择:
型号
类别
感温元件
材料
现场显示
安装固定
方式
接线盒
形式
保护管直径
隔爆标志
内芯结构
保护管特征
说明
SK-SBW
温度变送器
R
热电偶
Z
热电阻
M
镍铬硅-镍铬{N}
N
镍铬-镍硅{K}
E
镍铬-铜镍{E}
F
铁-铜镍{J}
C
铜-铜镍{T}
P
铂{Pt100}
C
铜{Cu50}
Y
现场液晶显示
1
无固定装置
2
固定螺纹
3
活动法兰
4
固定法兰
5
活络管接头式
6
固定螺纹锥形式
7
直形管接头式
8
固定螺纹管接头式
9
活动螺纹管接头式
2
防喷式
3
防水式
4
防爆式
0
Ф16
1
Ф12
2
Ф16高铝质管
3
Ф20高铝质管
B
隔爆
无
普通元件
K
铠装元件
F
防腐型
N
耐磨型
SK-SBW
R
E
Y
2
4
0
B
K
F
型号选型
型号选定为SK-SBWREY240BKF
成本
商家报价约为1000元/个
3.3.2流量测量仪
4类别
工作原理
仪表名称
可测流体种类
适用管径mm
测量精度%
安装要求、特点
体积流量计
差流
压量式计
流体流过通管道中的阻力件时产生的压力差与流量之间有确定关系,通过测量差压值求得流量
节流式
孔板
液、气、蒸汽
50~1000
±1~2
需直管段,压损大
喷嘴
50~500
需直管段,压损中等
文丘里管
100~1200
需直管段,压损小
均速管
液、气、蒸汽
25~9000
±1
需直管段,压损小
转子流量计
液、气
4~150
±2
垂直安装
靶式流量计
液、气、蒸汽
15~200
±1~4
需直管段,
弯管流量计
液、气
±0.5~5
需直管段,无压损
容流积量式计
直接对仪表排出的定量流体计数确定流量
椭园齿轮流量计
液
10~400
±0.2~0.5
无直管段要求,需装过滤器,压损中等
腰轮流量计
液、气
刮板流量计
液
±0.2
无直管段要求,压损小
速流
度量
式计
通过测量管道截面上流体平均流速来测量流量
涡轮流量计
液、气
4~600
±0.1~0.5
需直管段,装过滤器
涡街流量计
液、气
150~1000
±0.5~1
需直管段
电磁流量计
导电液体
6~2000
±0.5~1.5
直管段要求不高,无压损
超声波流量计
液、气
>10
±1
需直管段,无压损
直
接
式
直接检测与质量流量成比例的量来质量流量
热式质量流量计
气
±1
冲量式质量流量计
固体粉料
±0.2~2
科氏质量流量计
液、气
±0.15
间
接
式
同时测体积流量和流体密度来计算质量流量
体积流量经密度补偿
液、气
±0.5
温度、压力补偿
流量计的比较如上图所示,可选择均速管、转子流量计、靶式流量计、涡轮流量计、超声波流量计等。
综合考虑测量精度、成本控制等因素,选择气体涡轮流量计,如图:
其部分参数如下,
公称口径:
管道式:
DN4~DN200
插入式:
DN100~DN2000
精度等级:
管道式:
±0.5级,±1.0级
插入式:
±1.5级、±2.5级,高精度的可达0.2级
环境温度:
-20℃~50℃
介质温度:
测量液体:
-20℃~120℃
测量气体:
-20℃~80℃
大气压力:
86KPa~106KPa
公称压力:
1.6Mpa、2.5Mpa、6.4Mpa、25Mpa
使用时根据管道公称直径等因素进行口径选择,单个成本在100-1000元。
4.3.1调节阀
由于初设的流量较大,阀前后压差较大,选择高精度电动单座调节阀,该调节阀压降损失小,输出力稳定,响应迅速,流量系数大,流量特性精度高,调节范围广。
以上海某公司生产的系列产品为例:
为使调节过程平稳缓和,选用等百分比流量特性。
介质为气体时,
,
且由于Cv=1.17Kv,粗取P1=25bar,P2=10bar,可得丙烯和氨气的流量系数为2.23和3.14,空气流量系数为37.07。
所以,对于丙烯和氨,选调节阀口径为DN25,配用执行机构为381LS/XA-20,正常工作时阀门开度为27.9%和39.3%;
对于空气,选调节阀口径为DN65,配用执行机构为381LS/XA-50,正常工作时阀门开度为74.1%。
4.3.2PID调节器
因为我们要控制的都是流量调节阀,因此我们选择了由江苏苏科仪表有限公司生产的SK-808/900系列中的智能调节器,它是控制流化床反应器时常用的一种调节器。
SK-808/900系列智能PID调节仪与各类传感器、变送器配合使用,实现对温度、压力、液位、容量、力等物理量的测量显示、智能PID调节仪并配合各种执行器对电加热设备和电磁、电动、气动阀门进行PID调节和控制、报警控制、数据采集、记录。
该调节器有以下特点:
(1)万能输入功能
(2)自动校准和人工校准功能
(3)手动/自动无扰动切换功能
(4)可选择适应加热或制冷的正/反作用
(5)控制输出信号限幅
(6)智能PID调节仪采用模糊控制理论和传统PID控制相结合的方式,使控制
(7)过程具有响应快、超调小、稳态精度高的优点,对常规PID难以控制的大纯滞后对象有明显的控制效果
(8)智能PID调节仪增加了30段程序控制功能
主要技术指标:
基本误差:
0.5%FS或0.2%FS±1个字
分辨力:
1/20000、14位A/D转换器
显示方式:
双排四位LED数码管显示
采样周期:
0.5S
报警输出:
二限报警,报警方式为测量值上限、下限及偏差报警,继电器输出触点容量AC220V/3A
控制输出:
⑴继电器触点输出
⑵固态继电器脉冲电压输出(DC12V/30mA)
⑶单相/三相可控硅过零触发
⑷单相/三相可控硅移相触发
⑸模拟量4~20mA、0~10mA、1~5V、0~5V控制输出
通讯输出:
接口方式--隔离串行双向通讯接口RS485/RS422/RS232/Modem
波特率--300~9600bps内部自由设定
馈电输出:
DC24V/30mA
电源:
开关电源85~265VAC功耗4W以下
选型表:
代码
说明
SK-808/900
智能PID调节仪
外型尺寸
A
横式160×80×125mm
A/S
竖式80×160×125mm
B
方式96×96×110mm
C
横式96×48×110mm
C/S
竖式48×96×110mm
D
方式72×72×110mm
报警输出
B□
B1-1个报警点,B2-2个报警点
控制输出
N
无控制输出
L
继电器控制输出
G
固态继电器输出
K1
单相可控硅过零触发
K2
三相可控硅过零触发
K3
单相可控硅移相触发
K4
三相可控硅移相触发
X1
4-20mA输出
X2
0-10mA输出
X3
1-5V输出
X4
0-5V输出
通讯输出
P
微型打印机
R
串行通讯RS232
S
串行通讯RS485
变送器配电电源
无馈电输出
V12
带DC12V馈电输出
V24
带DC24V馈电输出
供电电源
220VAC供电
W
DC24V供电
输入信号
Sn
见"输入信号类型表"
输入类型表
参数提示符
输入信号内容
参数提示符
输入信号内容
tc-K
K型
rtd
0-400Ω
tc-S
S型
1000
Pt1000
tc-E
E型
bA1
BA1
tc-b
B型
bA2
BA2
tc-t
T型
0-50
0-50mA
tc-n
N型
0-5V
0-5V
tc-j
J型
1-5V
1-5V
P100
Pt100
0-20
0-20mA
C100
Cu100
0-10
0-10mA
Cu50
Cu50
4-20
4-20mA
根据以上表,结合变送器的输出方式及执行器的输入方式,我们选择C/B1/X1/R/V24/W/Cu50代码组合的调节器
5丙烯腈控制系统仿真及性能评价
6丙烯腈反应器控制成本分析,应用前景
6设计历程及总结
反应系统设计的任务经历了10周左右的时间,为我们设计真正的反应器打下了基础,做了一个良好的铺垫。
初期设计遇到了很多困难:
我们选择设计反应器的控制系统,并定下了基本的原则——选择一个具体的化工生产中的化学反应并在对现代工厂的控制方案以及各类化学反应不甚了解的情况下选择了生产尿素的反应器的控制,搜索到一些资料之后,发现大部分都是及其复杂的控制系统,作为过程装备控制系统设计的初学者,衡量过自己已有的知识储备。
中期设计,我们遭遇更多的是不确定性:
分析出反应器温度和不同物料流量的比值是反应的决定性因素后,又通过查阅文献,设计出一个串级+比值的控制系统,经过定性分析,我们认为这样的组合能达到较好的控制,但却也不知这样的控制是否能达到良好的控制效果。
同时我们进行了各种控制仪表的选型,发现,可适用一个环境和条件的仪表有很多,如何选择最佳的仪表,更