最佳凸轮设计中考虑动态特性的凸轮阀门系统.docx
《最佳凸轮设计中考虑动态特性的凸轮阀门系统.docx》由会员分享,可在线阅读,更多相关《最佳凸轮设计中考虑动态特性的凸轮阀门系统.docx(12页珍藏版)》请在冰豆网上搜索。
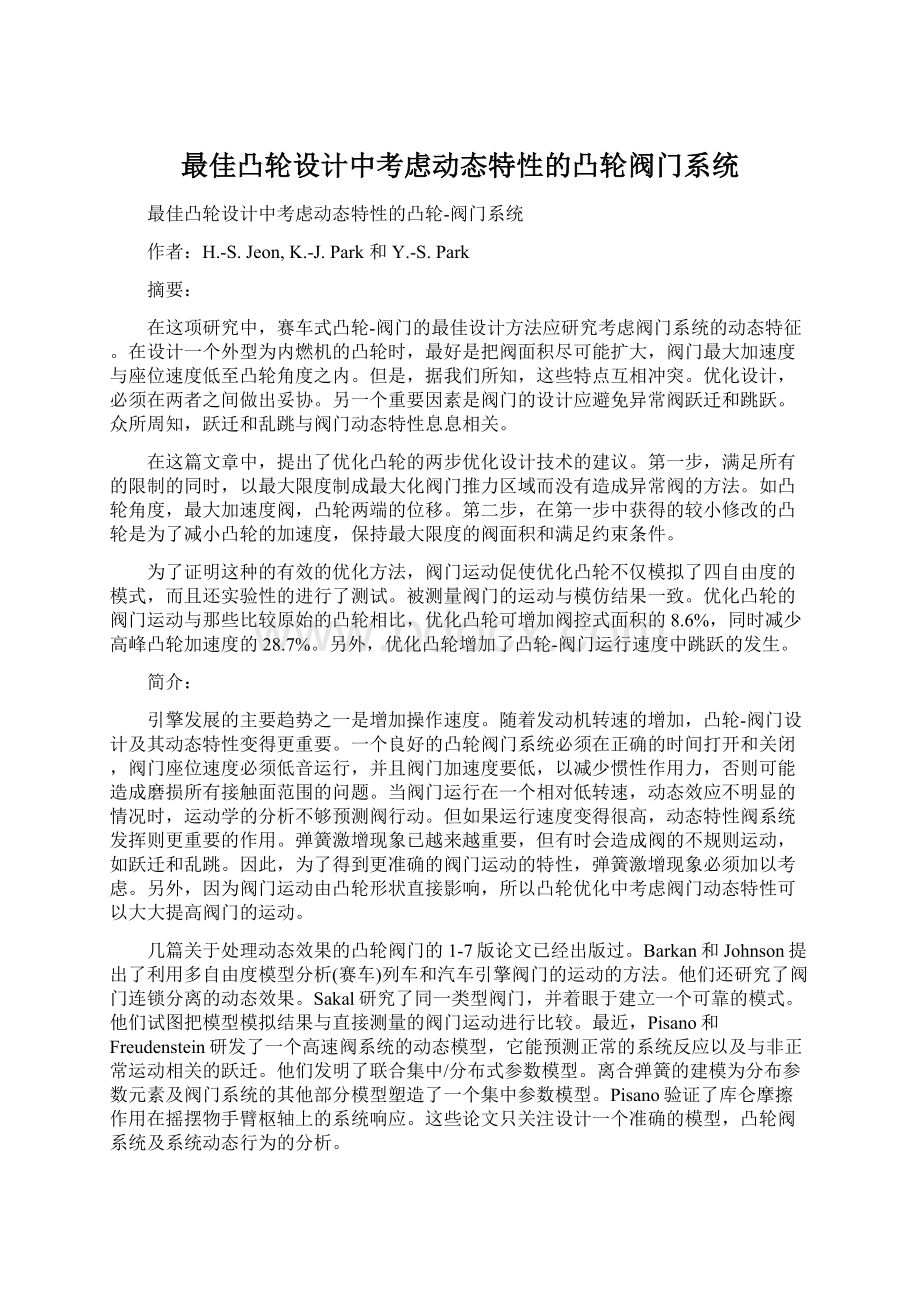
最佳凸轮设计中考虑动态特性的凸轮阀门系统
最佳凸轮设计中考虑动态特性的凸轮-阀门系统
作者:
H.-S.Jeon,K.-J.Park和Y.-S.Park
摘要:
在这项研究中,赛车式凸轮-阀门的最佳设计方法应研究考虑阀门系统的动态特征。
在设计一个外型为内燃机的凸轮时,最好是把阀面积尽可能扩大,阀门最大加速度与座位速度低至凸轮角度之内。
但是,据我们所知,这些特点互相冲突。
优化设计,必须在两者之间做出妥协。
另一个重要因素是阀门的设计应避免异常阀跃迁和跳跃。
众所周知,跃迁和乱跳与阀门动态特性息息相关。
在这篇文章中,提出了优化凸轮的两步优化设计技术的建议。
第一步,满足所有的限制的同时,以最大限度制成最大化阀门推力区域而没有造成异常阀的方法。
如凸轮角度,最大加速度阀,凸轮两端的位移。
第二步,在第一步中获得的较小修改的凸轮是为了减小凸轮的加速度,保持最大限度的阀面积和满足约束条件。
为了证明这种的有效的优化方法,阀门运动促使优化凸轮不仅模拟了四自由度的模式,而且还实验性的进行了测试。
被测量阀门的运动与模仿结果一致。
优化凸轮的阀门运动与那些比较原始的凸轮相比,优化凸轮可增加阀控式面积的8.6%,同时减少高峰凸轮加速度的28.7%。
另外,优化凸轮增加了凸轮-阀门运行速度中跳跃的发生。
简介:
引擎发展的主要趋势之一是增加操作速度。
随着发动机转速的增加,凸轮-阀门设计及其动态特性变得更重要。
一个良好的凸轮阀门系统必须在正确的时间打开和关闭,阀门座位速度必须低音运行,并且阀门加速度要低,以减少惯性作用力,否则可能造成磨损所有接触面范围的问题。
当阀门运行在一个相对低转速,动态效应不明显的情况时,运动学的分析不够预测阀行动。
但如果运行速度变得很高,动态特性阀系统发挥则更重要的作用。
弹簧激增现象已越来越重要,但有时会造成阀的不规则运动,如跃迁和乱跳。
因此,为了得到更准确的阀门运动的特性,弹簧激增现象必须加以考虑。
另外,因为阀门运动由凸轮形状直接影响,所以凸轮优化中考虑阀门动态特性可以大大提高阀门的运动。
几篇关于处理动态效果的凸轮阀门的1-7版论文已经出版过。
Barkan和Johnson提出了利用多自由度模型分析(赛车)列车和汽车引擎阀门的运动的方法。
他们还研究了阀门连锁分离的动态效果。
Sakal研究了同一类型阀门,并着眼于建立一个可靠的模式。
他们试图把模型模拟结果与直接测量的阀门运动进行比较。
最近,Pisano和Freudenstein研发了一个高速阀系统的动态模型,它能预测正常的系统反应以及与非正常运动相关的跃迁。
他们发明了联合集中/分布式参数模型。
离合弹簧的建模为分布参数元素及阀门系统的其他部分模型塑造了一个集中参数模型。
Pisano验证了库仑摩擦作用在摇摆物手臂枢轴上的系统响应。
这些论文只关注设计一个准确的模型,凸轮阀系统及系统动态行为的分析。
不少人认为,在设计凸轮外形时应考虑凸轮的动态效果,最小的输出振动,加速度,接触应力等,从而选择一个合适的标准凸轮优化方法。
他们解决该优化问题时用最优控制理论解决非线性接触应力准则的方法。
但他们也用了一个很简单的模型(一个自由度凸轮-从动模式)。
在这篇文章中,赛车式凸轮-阀门系统模型被作为了一个四自由度集参数模型。
为了提高模型的可靠性,可根据调谐的对比模型分析被测阀的运动。
凸轮优化技术提出了改善凸轮阀运动的方法以获得优化凸轮的加工精度,这也体现了优化技术的实际应用。
塑造凸轮-阀门系统
一个典型的赛车式凸轮-阀门系统体现在图1中。
如图2阀门的弹簧是由两个刚性物体(M1和M2)和弹簧三个要素(k1,k2和K3)组成。
每个阀门元件在假设条件下的对称性(Ks1=Ks3)与实际测量是等效的。
阀门弹簧的强度,阀弹簧刚度模型和阀弹簧模型(m1与M2)质量要素的选择等,计算它们固有频率的方法是测量阀门弹簧的自然频率。
每个阻尼系数决定后,粘性阻尼假设的条件应考虑的总阻尼对总的减震系统,闭环的估测面积,阀的推杆力的影响.所有的阻尼系数在阀门弹簧(c1,c2和C3)和阀门(C1,和C2)上进行了调整.合理分配实测总阻尼,也包括阀座刚度和阻尼在内,因为他们的跳跃是息息相关的。
估计阀门的质量(M)加上摇臂等于实际阀门质量。
根据同样的程序,获得旋转摇臂一半的推杆力。
根据推断,摇臂只作旋转运动.这种计算方法相当于分别计算摇臂的等效质量。
表1列出所有参数的值用于这项研究。
若忽略阀门,则可轻易取得运动模型方程:
[m],[c],[k]是质量,阻尼,和刚度,矩阵式凸轮-阀门模型和{x}={xe,xv,x1,x2}是物体(Me)和阀门质量(M)的位移矢量。
X1和x2的位移等于弹簧位移(m1和M2)。
公式
(1)中函数(f)可通过对称凸轮的形状计算傅立叶级数,凸轮xc可表达为公式
(2)。
其中Re表示实际部分,且CP为复杂的傅立叶系数(cp=cp1+jcp2)。
那么外界函数(f)变成:
初步确定,压缩力与当量刚度阀门的关系及摇臂比例。
从
(1),
(2),(3)阀的剧烈反应可以很容易地计算出凸轮参数cp(p=o,1....m)的公式。
图1--绘制的一个赛车型凸轮-阀门
图2--集中质量模型的凸轮-阀门
为了检验所建立模型的可靠性,对阀门的模拟运动进行了比较试验。
阀位移和推杆的作用力试验测定。
如图3瓣膜置换是采用一个光学位移测量装置(非接触型)和应变计电路推杆力记录。
而置于一端的凸轮轴控制和数据编码采集器,用来采集凸轮-阀门使用驱动马达的时间。
数字4,5和6显示的是用不同的方法测量仿真阀的同步运行速度。
由数字显示可知,模拟结果表明模拟方法是正确的。
波动推杆力的角度可以解释为阀门弹簧的激增和连锁的灵活性。
其余推杆力则显示出了凸轮活动角区域的情况。
5和6可以解释为阀的残余振动。
残余振动蔓延发展迅速,但不影响以后的瓣膜运动的凸轮角。
当发动机转速为2400rpm(图5)时,振动可以认定为零推杆力而不出现反弹,无论是在测量或模拟中都不能清楚地观察到。
不过,如果发动机转速提高至3000rpm(图6),无论从测量还是从模拟中跳跃和弹跳现象都可以清楚地观察到.比较模拟与实验结果,可以断定,四个自由度模型的模拟凸轮-阀门系统效果很好,所以四由度模型被用于凸轮形状的优化程序。
优化凸轮阀门的模拟在实验中,模拟计算参数如下。
表1--阀列车组件和模型参数
图3--实验仪器
凸轮剖面优化
这些规定是为了达到:
(1)最大阀门面积尽可能有效地摄入尾气流量;
(2)低阀加速提升最高运行速度;(3)使阀门的速度在匝道区域安静运行和减轻磨损。
阀的运动完全是由凸轮的形状和阀门动态特性决定,所以调整凸轮轮廓的傅立叶系数来修改凸轮。
在这项研究中,一、二两步优化技术提出了改善阀门的方案,同时也满足设计要求。
第一步优化
在这一步中,以原来的凸轮形状对凸轮轮廓作了修改,以最大限度使阀面积尽可能大,同时也满足限制.由凸轮的运动来看,最大加速度阀,凸轮位移两端的角度,总流量区域内的凸轮运动的角度以最大限度地被界定为公式(4):
其中0是凸轮运动角度,并指定凸轮在一个任意角度的运动。
实际上是由几何形状的阀座和阀决定的。
在这里,我们假定这些参数无法被确定。
因此,只有通过最大限度的改变凸轮轮廓的傅立叶系数来实现目标函数。
因此目标函数是可以用梯度表示:
p=0,l,...m。
用轮廓投影法来优化目标函数。
表2--傅立叶系数的原件和优化凸轮
图4--测量仿真瓣膜置换和推杆力的波动(发动机rpm=1200)
图5--测量仿真瓣膜置换和推杆力波动(发动机rpm=2400)
第二步优化
第一步优化是为了最大限度地在阀的运动区域内提高阀门加速度,其中最重要的因素是阀门设计,从原来的凸轮形状看,仅限于阀产生的最高加速度。
如果阀门最大加速度被取代,而又不改变阀区凸轮轮廓是最好的。
在优化的第二步中小型凸轮轮廓的修改是为了削减在第一步凸轮优化中产生的最高凸轮加速度。
在任意一个阀系统的凸轮运行速度,性能指标被定义为:
阀门的位移,速度和加速度在任意角度的凸轮系统中根据公式
(1)可计算出,而瓣膜置换和一个任意角度的凸轮的速度在首步优化中取得。
我们选择任意点的瓣膜置换和在阀门内凸轮运动角度的任意两点,进行量化的修改作为第二次优化过程中的一步。
首先公式(6)表示阀门的位移变化,可以解释凸轮的形状约束。
上一步的总阀门加速度在某一凸轮运动中的角度,也可以额外的阀门加速度。
其他因素可以根据设计者的主观选择判断。
采取较大的C值变化来获得较小的凸轮形状变化。
在这项研究中,我们采取nd=19和nv=5。
假设阀系统运行的行程为P:
在第二次优化步骤中将利用凸轮轮廓的傅立叶系数来减少总性能指标。
如果我们使cpl,cp2的和等于C,那么在最低点:
p=0,1......m.
运用公式(8)(6)和(7),并重新选择凸轮轮廓的傅立叶系数。
我们得到以下公式:
,
[X]和{T}是(2m+1)×(2m+1)系数矩阵,(2m+1)×1是向量系数。
这里我们研究用m=23。
公式(9)中应特别注意凸轮和阀门的延时运动。
由于阀门和阀门弹簧初压缩时出现了一个阀门静止的时间,这一区域被称为匝道时间。
在阀门系统设计中,阀匝道速度应当在一定范围内。
在匝道时期内制约方程可从公式
(2)得:
其中k=1,2.....m,点e和E为匝道时间内对凸轮位移和速度的规定。
凸轮位移
和速度
指定了凸轮角度应给定的约束方程。
在这项研究中,我们指明在匝道时间内凸轮速度和位移三点(s=3)。
可以选择方程(10)及(11)确定凸轮轮廓的傅立叶系数。
凸轮角
图7--比较原凸轮和优化凸轮
[L]和{U}为2e×(2m+1)系数矩阵和2ex1系数向量。
从(9)和(12)知,优化凸轮轮廓的傅立叶系数,应采用线性最小二乘的理论。
从而使最低误差可以计算如下:
其中{cp}是无偏最小二乘(代入[X][L]和[U]中),由公式(9)到公式(12)再到公式(13)所得,我们可以计算出一个满足约束的最优凸轮公式(12)。
比较原凸轮和优化凸轮
如前文所述,从原来的凸轮形状考虑,优化凸轮来源于两步优化技术。
图7显示了原凸轮和优化的凸轮的位移,速度和加速度。
从表2的列举,我们可以看到傅立叶系数的原始数据和优化解的差异。
从图7可以看出,优化的凸轮面积扩大了8.6%,而最大加速度则减少高达28.7%(从71.7mm/rad减小为51.08mm/rad)。
同时也显示了最优化的凸轮保持着和原凸轮几乎相同的速度水平。
从这些结果我们可以预计,优化的凸轮不但增加了火车阀门效率,而且还降低了火车阀门惯性力。
此外,降低了惯性力使我们能够提高阀控式列车平稳的运行速度。
图8--优化凸轮的加工误差
图9--优化凸轮仿真瓣膜置换和推杆力的测量(发动机rpm=1200)
核查优化凸轮
实验为了证明最了优化凸轮的效果,优化凸轮是经过数控凸轮铣床精心加工的。
为了了解加工误差,用三维剖面测量设备来准确地测量要加工的凸轮.图8显示了实测凸轮轮廓加工误差。
误差在正负50微米左右,在20微米的地方是阀门打开和关闭地方。
瓣膜置换和推杆力不仅模拟四个自由度的模式,而且是直接测得的试验设施,如图3中,数字9,10和11显示测量仿真瓣膜置换和推杆力不同行的驶速度。
可以说,模型计算的结果非常接近对原有凸轮分析的实际测量值。
推杆原件和优化凸轮处于不同速度时,中可以看出优化凸轮使最大推杆力大大下降。
举例来说,当引擎转速为2400rpm时,实测原来凸轮最大推杆力是255kgf(图5),但是它只识别182kgf为优化凸轮(图10)。
当转速为3000rpm时,峰值为350kgf(图6),则优化凸轮是260kgf(图11)。
所以减小推杆力将有助于减少磨损。
其他最优化凸轮的方法是提高列车阀的运行速度且无异常运动,在原始的凸轮中跳跃现象发生在3000rpm。
(图6)显示为零推杆力情况。
但在另一方面,优化凸轮在同样的速度下并未出现跳跃(图11)。
图10--优化凸轮测量仿真瓣膜置换和推杆力(发动机rpm=2400)
图11--优化凸轮的测量仿真瓣膜置换和推杆力(发动机rpm=3000)
从这个研究可以得出结论:
(1)有四个自由度的集中质量模型,足以代表赛车型火车阀门系统;
(2)凸轮可进行两步优化技术。
实验表明,优化的凸轮在减少凸轮加速度和最大推杆力的同时可以增加阀面积。
参考资料
1.Sakai,H.和Kosaki,H.《对阀门及阀弹簧激增运动的分析》,1976年东京大学出版.
2.Barkan,P.《高速阀门运动的演算与灵活顶部的联系》,1953年出版.
3.Johnson,G.I.《阀门动力学与电子计算机的研究》《阀门齿轮设计中计算机的应用》,1963年出版.
4.Akiba,K.,Shimizu,A.和Sakai,H.《全面高速阀门机构的模仿》,文件编号:
810865,1983年出版.
5.Pisano,A.P.和Freudenstein,F.《实验和调查分析动态响应高速凸轮从动系统的第一部分和第二部分》,1983年出版.
6.Pisano,A.P.《库仑摩擦高速凸轮系统》,1984年出版.
7.Pisano,A.P.和Chen,H.T.《库仑摩擦和优化摇臂的高速凸轮系统》,1986年出版.
8.Kwakernaak,H.和Stair,J.《最低振动凸轮》,1968年出版.
9.Kanzaki,K.和Itao,K.《型头定位的凸轮机制》,1972年出版.
10.Wiederrich,J.L.和Roth.B《用有限项三角级数合成动态照片》,1975年出版.
11.Chew,M.,FreudensteinF.和Longman,R.W《应用最优控制理论合成高速凸轮系统的第1部分和第2部分》,1983年出版.
12.Graham,C.G.和Robert,L.P《动态系统辨识》,Acaflemic出版社,1977年出版.