丙烯制环氧丙烷HPPO项目建议书.docx
《丙烯制环氧丙烷HPPO项目建议书.docx》由会员分享,可在线阅读,更多相关《丙烯制环氧丙烷HPPO项目建议书.docx(19页珍藏版)》请在冰豆网上搜索。
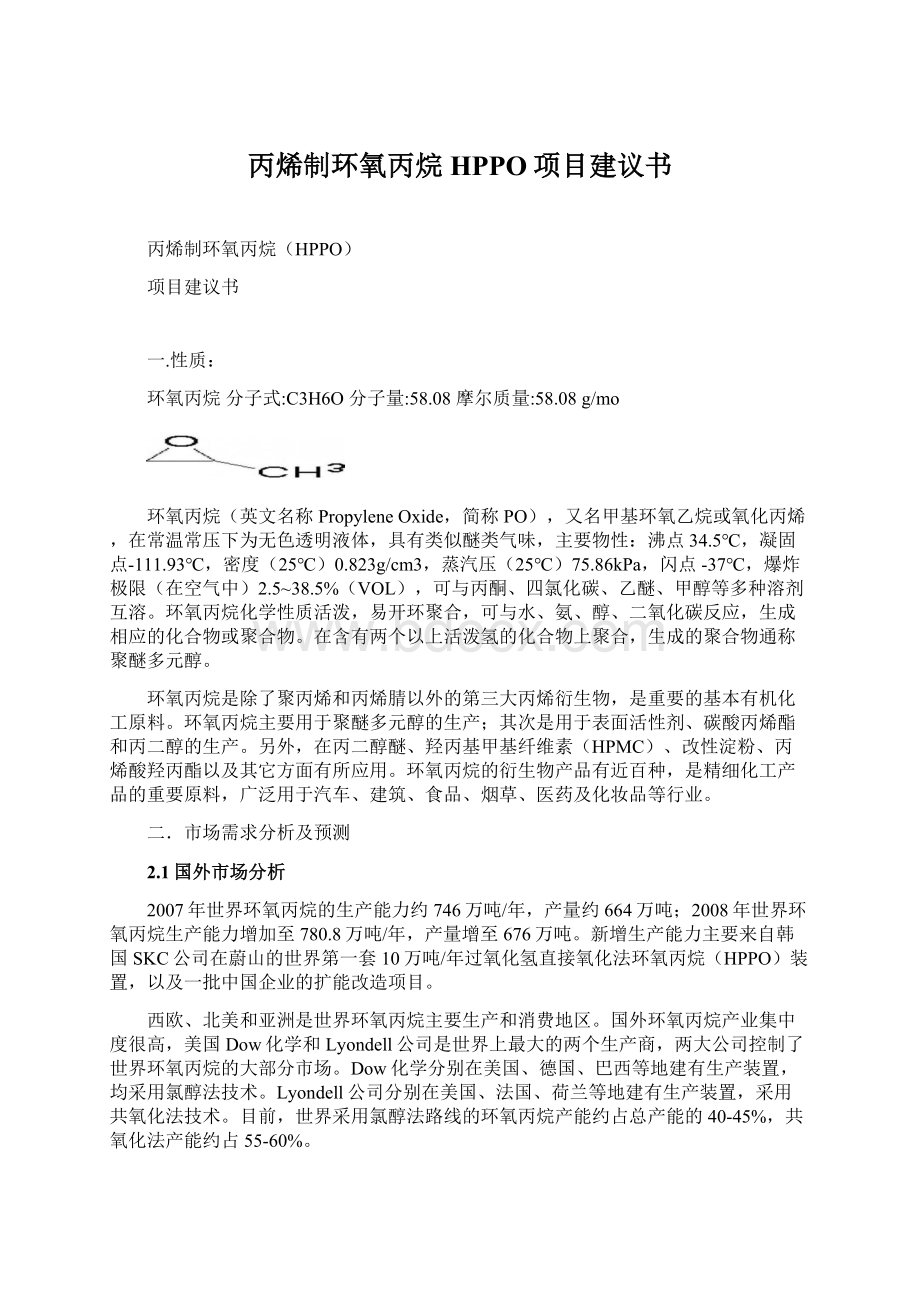
丙烯制环氧丙烷HPPO项目建议书
丙烯制环氧丙烷(HPPO)
项目建议书
一.性质:
环氧丙烷分子式:
C3H6O分子量:
58.08摩尔质量:
58.08g/mo
环氧丙烷(英文名称PropyleneOxide,简称PO),又名甲基环氧乙烷或氧化丙烯,在常温常压下为无色透明液体,具有类似醚类气味,主要物性:
沸点34.5℃,凝固点-111.93℃,密度(25℃)0.823g/cm3,蒸汽压(25℃)75.86kPa,闪点-37℃,爆炸极限(在空气中)2.5~38.5%(VOL),可与丙酮、四氯化碳、乙醚、甲醇等多种溶剂互溶。
环氧丙烷化学性质活泼,易开环聚合,可与水、氨、醇、二氧化碳反应,生成相应的化合物或聚合物。
在含有两个以上活泼氢的化合物上聚合,生成的聚合物通称聚醚多元醇。
环氧丙烷是除了聚丙烯和丙烯腈以外的第三大丙烯衍生物,是重要的基本有机化工原料。
环氧丙烷主要用于聚醚多元醇的生产;其次是用于表面活性剂、碳酸丙烯酯和丙二醇的生产。
另外,在丙二醇醚、羟丙基甲基纤维素(HPMC)、改性淀粉、丙烯酸羟丙酯以及其它方面有所应用。
环氧丙烷的衍生物产品有近百种,是精细化工产品的重要原料,广泛用于汽车、建筑、食品、烟草、医药及化妆品等行业。
二.市场需求分析及预测
2.1国外市场分析
2007年世界环氧丙烷的生产能力约746万吨/年,产量约664万吨;2008年世界环氧丙烷生产能力增加至780.8万吨/年,产量增至676万吨。
新增生产能力主要来自韩国SKC公司在蔚山的世界第一套10万吨/年过氧化氢直接氧化法环氧丙烷(HPPO)装置,以及一批中国企业的扩能改造项目。
西欧、北美和亚洲是世界环氧丙烷主要生产和消费地区。
国外环氧丙烷产业集中度很高,美国Dow化学和Lyondell公司是世界上最大的两个生产商,两大公司控制了世界环氧丙烷的大部分市场。
Dow化学分别在美国、德国、巴西等地建有生产装置,均采用氯醇法技术。
Lyondell公司分别在美国、法国、荷兰等地建有生产装置,采用共氧化法技术。
目前,世界采用氯醇法路线的环氧丙烷产能约占总产能的40-45%,共氧化法产能约占55-60%。
未来几年,随着新装置的投产,预计2015年世界环氧丙烷生产能力将达到1050万吨/年左右,较2008年新增400万吨/年。
由于除日本之外的亚洲地区环氧丙烷下游产品年消费增长率一直保持近两位数增长,因此许多企业计划在亚洲新建或扩建环氧丙烷生产装置,大部分新增产能将集中在这一地区,预计除日本之外的亚洲其他地区新增产能将占新增总产能的70%以上。
世界环氧丙烷主要用于聚醚多元醇、丙二醇和丙二醇醚等的生产,其中用于聚醚多元醇的环氧丙烷约占总消费量的65.8%,用于丙二醇生产的约占18.1%,用于丙二醇醚的环氧丙烷约占6.1%。
2008年世界主要地区环氧丙烷消费构成如下:
世界主要地区环氧丙烷消费构成(万吨)
消费领域
美国
日本
世界
聚醚多元醇
98.0
30.9
436.7
丙二醇
45.5
5.9
120.3
丙二醇醚
11.1
4.0
40.7
其它
29.2
2.0
66.3
合计
183.8
42.8
664.0
由于亚洲需求急剧增加,近几年世界环氧丙烷需求呈现强劲增长,2003-2008年需求年均增长率达到3.7%,2008年需求量估计达到约676万吨。
预计2008-2015年期间世界环氧丙烷年均需求增速约为5.3%,2015年世界环氧丙烷需求量将达到970万吨左右。
其中以中国和印度为代表的亚洲地区需求增长将最为迅速,亚洲地区环氧丙烷市场增长率将达到年均11.6%,同期北美、欧洲则将分别以每年3.3%和3.7%的速度增长。
世界环氧丙烷需求增长的主要动力将来自于聚氨酯行业对聚醚多元醇的需求增长。
2.2国内市场分析
2.2.1供应状况分析及预测
我国环氧丙烷生产始于20世纪60年代,当时国内环氧丙烷装置能力小,单套装置年生产能力均在几千吨左右,生产装置均采用自有技术,工艺技术落后,原材料及公用工程消耗较高,“三废”污染严重。
20世纪80年代,我国先后引进了日本旭硝子公司、三井东压公司、昭和电工公司和美国陶氏公司技术,同时国内自行开发的环氧丙烷生产工艺技术水平也有较大幅度地提高。
某化工、某、某石化、某化工、某、某氯碱等企业已成为国内环氧丙烷生产的主力。
2006年3月随着中海壳牌年产25万吨环氧丙烷装置投产,国内环氧丙烷市场格局发生重大变化。
中海壳牌项目是目前国内最大的一套环氧丙烷装置,也是国内唯一采用环氧丙烷/苯乙烯共氧化联产法工艺的环氧丙烷装置。
截至2010年末我国环氧丙烷产能已增长至154.7万吨/年。
除中海壳牌的环氧丙烷装置采用联产苯乙烯的共氧化法外,其他环氧丙烷装置均采用氯醇法。
2010年底我国主要环氧丙烷生产厂情况如下表。
2010年底我国主要环氧丙烷生产厂情况(万吨/年)
生产企业
产能
工艺技术
备注
某化学有限公司
28.5
乙苯共氧化
中海壳牌石油化工有限公司
25
乙苯共氧化
某集团有限公司
17
氯醇
某化工有限责任公司
15
氯醇
2006年9月完成由8万吨扩到15万吨
某化工集团氯碱股份有限公司
13
氯醇
某集团有限公司
10
氯醇
某化工有限公司
6.0
氯醇
江苏金浦集团和韩国锦湖石化各持50%股份,2008年投产
某石化公司
8
氯醇
某化学工业有限公司
6
氯醇
某控股集团有限公司
5
氯醇
某化工有限公司
4
氯醇
某化工有限公司
4
氯醇
某氯碱工业有限公司
4
氯醇
某化工股份有限公司
4
氯醇
中国石油大学(华东)的校办企业
某化学有限公司
2
氯醇
某化工厂
2
氯醇
某石油化工有限公司
0.7
氯醇
154.7
近几年国内环氧丙烷大量扩建、新建,今后一段时期仍将是国内环氧丙烷产能新增高峰,山东、江苏、浙江是今后国内产能增长的主要地区。
2011年前后,金浦锦湖公司、镇海乙烯Lyondell等大型环氧丙烷项目将逐步投产。
某公司计划在南京化学工业园区扩建环氧丙烷一体化装置,新增10万吨/年环氧丙烷产能;Lyondell与中石化合资在宁波镇海建设28.0万吨/年共氧化法环氧丙烷生产装置,2010年投产。
此外,一些扩建、新建项目也在计划中。
预计2015年国内环氧丙烷生产能力有望达到229万吨/年左右。
国内环氧丙烷装置规模在向大型化发展,20世纪80年代引进技术建设的装置规模多为2万吨/年,某建设的最大装置规模为8万吨/年,近年国内新建单套规模均在4万吨/年以上,大型氯醇法装置规模在10万吨/年、共氧化法装置规模在20万吨/年以上。
随着装置规模的扩大,规模经济性明显,竞争力增强,对原有小型氯醇法生产装置将形成较大冲击。
2.2.2需求状况分析及预测
国内环氧丙烷行业自20世纪90年代初期开始,消费量保持高速增长,从1990-2005年期间,环氧丙烷消费量年均增长率高达22.6%。
2005年以来,随着我国聚氨酯工业进入新一轮发展期,上游原料环氧丙烷需求增长进一步加快。
我国近年环氧丙烷供需平衡如下表:
我国环氧丙烷供需平衡(万吨/年,万吨)
年份
生产能力
产量
进口量
出口量
消费量
1995年
18.5
9.8
0.01
0
9.81
2000年
35.4
25.2
2.88
0.03
28.05
2001年
47.6
33
3.64
0.02
36.62
2002年
52
36.5
5.29
0.04
41.75
2003年
52
41.4
11.56
0.06
52.9
2004年
56
43
19.06
0.06
62
2005年
70
51.3
15.13
1.05
65.4
2006年
96
68
12.0
1.52
78.5
2007年
110
90
14.7
0.44
104
2008年
113.5
95
15.3
0.04
110.3
2009年
126.2
105.0
25.5
0.005
130.5
2010
125.0
125.0
36.2
0.0
161.2
国内环氧丙烷最大的用途是在碱金属氧化物和起始剂作用下开环聚合生成聚醚多元醇。
由于所用起始剂的不同,聚醚可分为软泡聚醚、硬泡聚醚和弹性体聚醚。
软泡聚醚用于生产聚氨酯软泡,以制造衬垫、包装用品等;硬泡聚醚用于生产聚氨酯硬泡,用作保温材料等;弹性体聚醚用于生产聚氨酯弹性体,用作跑道、涂料、粘合剂、密封剂等。
2009年国内环氧丙烷表观消费量约130.5万吨,其中用于聚醚多元醇的消费量约102万吨,占总消费量的78%,这一比例远高于世界65%的平均水平;其次是在表面活性剂和碳酸丙烯酯、丙二醇方面的消费量,合计为18.9万吨,占总消费量的14.4%。
另外,国内环氧丙烷在丙二醇醚、甲基纤维素(HPMC)、改性淀粉、丙烯酸羟丙酯以及其它方面也有一些应用,环氧丙烷消费量约9.8万吨,占7.5%。
2010年国内环氧丙烷消费结构见下表:
2010年国内环氧丙烷消费结构
消费领域
消费量(万吨)
比例(%)
聚醚多元醇
125.7
78.0
碳酸丙烯酯和丙二醇
3.2
2.0
其他
32.2
20.0
合计
161.2
100.0
其他应用领域包括丙二醇醚、丙二醇醚醋酸酯、改性淀粉、丙烯酸羟丙酯和HPMC等。
从消费区域分布来看,由于聚醚是环氧丙烷最大的消费领域,所以国内聚醚厂家集中的地区也就是环氧丙烷最大的消费地区。
目前,国内环氧丙烷的消费主要集中在华东地区,约占国内总消费量的50%左右,山东、江苏、浙江和上海等地的聚醚厂家众多,而这些聚醚厂家本身要么不生产环氧丙烷,需要全部外购,要么自身的环氧丙烷装置产能较小,不足以满足聚醚生产需要,也需大量采购环氧丙烷来进行聚醚生产。
华南、东北和华北也是国内环氧丙烷消费量较大的地区,其消费量分别占总消费量的23.1%、11.7%和9.3%;而西南和西北地区消费量较少,分别占总消费量的3.0%和2.6%。
总体来看,目前国内华北地区主要环氧丙烷供应商是某、某氯碱、某、某和某等;华南地区主要供应商是中海壳牌及少量进口货源;华东地区主要供应商为高桥石化、钟山化工、中海壳牌、某、某及部分进口货源。
聚氨酯是一种有机高分子材料,因其卓越的性能而被广泛应用于国民经济众多领域。
在人类面临的长期能源紧张和能源成本趋高的情况下,聚氨酯在家具、汽车以及隔热领域广阔应用,将会给聚氨酯行业带来源源不断的发展动力。
目前我国聚氨酯人均消费水平还远远落后,国内市场聚氨酯材料还有巨大的发展空间。
随着世界聚氨酯行业中心向中国大陆的转移,将大大促进了我国聚氨酯行业的发展,同时,随着我国建筑保温节能一系列政策的推进、汽车和家具行业的持续发展,将会进一步加速聚氨酯行业的发展,从而拉动环氧丙烷需求的增长。
预计未来一段时期国内市场对聚氨酯主要原料聚醚多元醇产品的需求仍将保持8%左右的增长速度,聚醚多元醇仍将是环氧丙烷最大的消费领域和主要需求增长领域。
此外,国外大量消耗环氧丙烷的丙二醇,目前我国产量还比较少,相应消费的环氧丙烷也较少。
今后,随着国内一批丙二醇装置的投产,消耗在丙二醇方面的环氧丙烷量会有较快增长,将是环氧丙烷需求增长最快的领域。
预计到2015年国内环氧丙烷需求量将达到175万吨左右,2020年需求量将增加至230万吨左右。
国内的环氧丙烷市场正在从供不应求局面逐步走向自给自足的平衡态势。
由于环氧丙烷化学性质活泼,不适于远距离运输,而且其下游产品附加值较高,因此国内外多数环氧丙烷生产企业采用一体化经营模式,配套建设聚醚多元醇和丙二醇等下游产品装置。
2.2.3国内进出口分析
我国环氧丙烷进口量一直不大,其进口量主要体现在下游产品聚醚和聚氨酯上,但从2003年随着需求的增长进口量开始猛增,2003年进口量由2002年的5.3万吨,增加到11.6万吨,2004年又猛增至19.1万吨,2005年至2008年,随着国内新增产能的大量投产,国内环氧丙烷进口量逐步回落,维持在12-15万吨。
2009年,受世界金融危机影响,国外企业加大了对中国市场销售力度,我国环氧丙烷进口量增加至25.5万吨。
近年来我国环氧丙烷对外贸易进出口情况见下表:
中国环氧丙烷进出口情况
年份
进口量(万吨)
出口量(万吨)
2000年
2.88
0.03
2001年
3.64
0.02
2002年
5.29
0.04
2003年
11.56
0.06
2004年
19.06
0.06
2005年
15.13
1.05
2006年
12.0
1.52
2007年
14.7
0.44
2008年
15.3
0.04
2009年
25.5
0.005
2010年
36.2
0.0
我国环氧丙烷进口主要来自日本、新加坡和美国,进口主要地区为江苏、浙江、上海和山东等。
我国环氧丙烷出口量较少,中海壳牌石化、某氯碱、某化工和某有少量出口。
2.2.4国内外产品价格分析
价格分析:
环氧丙烷的价格短期来看主要受上游产品丙烯和下游产品聚醚多元醇的价格影响,长期来看主要受环氧丙烷供需平衡影响。
丙烯是生产环氧丙烷的主要原料,单耗在0.8~0.9之间,丙烯的价格主要受油价的影响。
原料丙烯从两方面影响环氧丙烷的价格:
一方面是丙烯的供应影响环氧丙烷的产量,国内丙烯主要由乙烯裂解装置副产,只有一小部分用于生产环氧丙烷,限制了环氧丙烷的产量,进而抬高其价格;另一方面,丙烯的价格与环氧丙烷的价格具有联动性,一般环氧丙烷的价格变动滞后于丙烯价格变动。
聚醚多元醇是环氧丙烷最主要的下游产品,软泡聚醚多元醇单耗在0.8~0.9,硬泡聚醚多元醇单耗在0.7左右。
聚醚多元醇与环氧丙烷的价格具有
很强的联动性。
通常情况下,聚醚多元醇价格与环氧丙烷价差较大时,受下游聚醚多元醇利好的拉动,环氧丙烷需求旺盛,价格上涨;当两者价差过小,聚醚多元醇企业盈利空间关闭,需求通道萎缩,导致氧丙烷价格下行。
从较长周期看,环氧丙烷价格主要受到其产能与需求平衡的影响。
综合供需情况分析,我国近10年环氧丙烷的自给率呈逐渐下降的趋势,导致国内环氧丙烷供应紧张、价格高企。
2002—2010年,环氧丙烷价格从6600元/t一路上涨,一直维持在高位
从历年国内环氧丙烷的价格变化走势来看,2001年的最高售价为8600元/吨。
2002年上升至9600元/吨以上,2003年环氧丙烷市场平均价格在9900元/吨,2004-2007年又达到10000元/吨以上的高位,2008年中期甚至达到19000元/吨的历史高位,后随着世界金融危机的爆发和石油价格的大幅下降,降至8000元/吨左右。
2009年,随着国内外经济形势的逐步好转和油价的回升,国内环氧丙烷价格也稳步回升至14000元/吨左右。
国内环氧丙烷价格变化情况见下表:
国内环氧丙烷价格变化情况(元/吨)
年份
市场价格
年份
市场价格
2001年
7600~8600
2006年
13500~15500
2002年
9000~10200
2007年
11400~14300
2003年
9600~10200
2008年
8000~19000
2004年
9800~16000
2009年
14000~21000
2005年
13000~17500
2010年
11000~15000
由于环氧丙烷的价格与原油价格直接相关,预计未来几年油价会逐步回归较为理性的价位,在60-90美元/桶之间波动,环氧丙烷价位在12000-17000元/吨之间,厂家的利润也将恢复到合理的水平。
三.工艺技术方案
3.1生产工艺技术及比较
目前,世界上环氧丙烷工业化生产方法主要是氯醇法、共氧化法、双氧水氧化法。
氯醇法环氧丙烷的规模正在下降,以间接氧化法生产环氧丙烷规模在不断扩大。
直接氧化法中的双氧水氧化法生产环氧丙烷工艺(即HP-PO工艺)正在开始工业化,直接氧化法中的氧气直接氧化法仍处于概念性试验阶段。
●氯醇法
反应总过程:
氯气+水 →次氯酸
丙烯+次氯酸→氯丙醇
氯丙醇+熟石灰→环氧丙烷
氯醇法生产环氧丙烷主要由氯醇化、皂化以及精馏3个步骤组成[3],采用氯气和水以丙烯反应,无需催化剂,水既是溶剂也参与反应,来源容易,且对环境和人员没有影响,反应压力比较温和,一般在大气压或略低于大气压下即可,反应温度为常温,其关键是保证氯气溶解在水中,从而提高氯气的反应选择性。
存在的问题是氯气和水产生的次氯酸对设备蚀严重,而且在皂化过程中利用了大量的碱液同样具有腐蚀性。
2.2共氧化法(PO/SM、PO/MTBE、CHP法)。
●氧化法
反应总过程:
乙苯+丙烯→环氧丙烷+苯乙烯
共氧化法生产环氧丙烷是由乙苯与丙烯进行共氧化反应生成环氧丙烷和苯乙烯。
反应在温度100~200℃、压力0.3~3.0兆帕条件下进行;环氧化反应在温度120~150℃、压力高于丙烯气化压力下进行。
共氧化法克服了氯醇法的腐蚀、污水多等缺点,而且可联产苯乙烯,但工艺流程长,所需的原料种类多,对丙烯纯度要求较高,设备造价高,装置投资大,只有在装置规模大型化时,才显示其优势。
丙烯和乙苯共氧化法的工艺专利商有Lyondell(Arco)、Shell、NKNC,丙烯和异丁烷共氧化联产环氧丙烷和叔丁醇(或MTBE)的专利商有Lyondell(Arco)和Texaco。
●双氧水氧化法(HP-PO)工艺
催化
反应总过程:
丙烯+过氧化氢(双氧水)——→环氧丙烷
过氧化氢真接氧化法是由过氧化氢(双氧水)催化环氧化丙烯制环氧丙烷的新工艺,HPPO法采用TS-1钛硅分子筛催化剂,在甲醇做溶剂的条件下,丙烯和双氧水在温度50~150℃、压力0.5~1.5兆帕的条件下反应。
反应过程需要有溶剂的大量循环。
含羟基的溶剂(如甲醇)会使PO开环,从而降低收率。
在反应后序处理过程中,对于残余过氧化氢的分解产生氧气的风险,需要采取足够安全设施,以保生产过程中只生成环氧丙烷和水,工艺流程简单,产品收率高,没有其他联产品,基本无污染,属于环境友好的清洁生产系统。
目前过氧化氢真接氧化法工艺分别由赢创工业集团(原德固萨,Degussa)与伍德(Uhde)公司、陶氏化学和巴斯夫(BASF)公司联合开发和工业化推广。
2001年,赢创工业集团和伍德公司在德国法兰克福建设了1套过氧化氢法试验性装置,测试最佳催化剂和测定临界参数,并开始对技术进行工业化设计。
2003年,赢创推出该技术的商业化工艺包。
通过上述分析可以得出结论:
氯醇法由于产生大量皂化废液,目前产能正在下滑;共氧化法虽克服了氯醇法腐蚀、污水多等缺点,但工艺流程长,对丙烯纯度要求较高,设备造价高,技术转让费和装置投资大;双氧水法克服了氯醇法设备腐蚀严重,废液、废渣多的缺点,并且工艺流程短,设备投资较少,是未来环氧丙烷生产工艺的主流方向之一,但目前尚处于发展起步阶段,工业化经验较少。
因此,在本规划推荐采用双氧水氧化法生产环氧丙烷。
工艺类别
原料成本
亿/万tPO
废水
吨/tPO
副产物
/tPO
缺点
氯醇法
2.10
43吨
CaCl2
二氯丙烷
1、废水量大
2、副产物廉价
3、设备腐蚀严重
共氧化法
2.77/4.69
约1吨
叔丁醇
苯乙烯
1、工艺路线长。
2、投资大。
HPPO
1.1
约1吨
无
1、H2O2需配套
三种技术的优缺点比较
生产方法
优点
缺点
氯醇法
工艺成熟,流程短,操作弹性大
选择性好,收率高
生产比较安全
对原料丙烯要求不严格
建设投资小
设备易腐蚀
废水量大
氯气消耗多
副产二氯丙烷
废渣量大
共氧化法
废水量小
无腐蚀
副产品经济价值高
废水处理困难
工艺流程长
原料品种多
对原料丙烯要求严格
生产大量联产品
投资大
HPPO法
三废量小
投资小
占地面积小
无联产品
工艺流程短
工业化时间短
工艺待完善
3.2.2催化剂
环氧化催化剂采用钛硅酸盐(TS),其组成为(TiO2)x·(SiO2)1-x(x=0.001~0.05),优选TS-1(MFI结构)和TS-2(MEL)结构。
它的制备方法有普通水解法和火焰水解法2种。
3.2.3环氧化工艺
丙烯和H2O2在甲醇溶剂中的环氧化反应可间歇或连续,反应器优选催化剂固定床的连续流反应器,特别是带冷却水夹套的管式反应器。
反应混合物表观流速优选5~30m/h,液体空速(LHSV)优选1.3~15h-1。
由于未反应的H2O2不能被回收,因此通常采用过量的丙烯以使H2O2尽可能完全转化。
n(丙烯):
n(H2O2)=(1.1~30):
1,m(甲醇):
m(H2O2水溶液)=0.5~20,催化剂用量应满足使H2O2转化率>95%,反应时间优选1min~5h。
反应温度优选在40~60℃,压力优选2.1~3.0MPa,丙烯分压优选>2.5MPa,可用N2作载气,以维持系统压力恒定,还可用于除去H2O2分解产生的O2。
HPPO是一个高度放热的反应,而且具有1个较高的激活温度,只有在该激活温度以上时才能获得合理的H2O2转化率,但高温下会导致副反应增加而影响PO选择性,因此必须有效去除反应热。
对于固定床多相反应器而言,采用向下流动模式进行操作,此时反应器保持滴流床状态。
维持反应体系温度分布在窄范围内,对于提高H2O2转化率和PO选择性是极其重要的,这可通过维持夹套中冷却水温度≥40℃,控制夹套入口和出口冷却水温差≤2℃,催化剂床内最高温度tmax≤60℃来完成。
催化剂床内温度用多个Pt-100热电偶来测量,它们沿管式反应器的轴向以适当间距布置。
传统的带夹套管式反应器不能有效控制催化剂填充层内部的温度。
他们采用一种特制的具有一系列平行排列的热交换板的管式反应器,催化剂固定床设置在热交换板之间,然后使多相混合物以向下流动模式连续流过催化剂层,同时通过冷却水除去反应热。
板间距优选10~30mm,冷却水优选以并流方式通过热交换板。
优选将催化剂涂敷在热交换板的外表面上,这有利于减少板间距,在反应器尺寸固定的前提下,可增加总换热面积。
该反应器中温度分布更加均匀,且不易发生堵塞和结垢现象,因而可降低设备成本。
3.2.4催化剂再生
随着环氧化反应的进行,催化剂活性逐渐下降,优选当H2O2转化率<95%或反应器内与冷却水夹套中温差变为初始值的50%时进行再生。
他们使用采用溶剂甲醇在≥100℃条件下洗涤催化剂的再生方法。
该方法无需将催化剂从反应器中取出,使甲醇在环氧化温度下通过催化剂层,同时升温至100~200℃,再生时间优选4~10h。
再生后降温至环氧化温度,重新开始环氧化反应,保持体系压力恒定,同时以≤0.025K/h的速度升温以补偿催化剂的失活,此举可使H2O2保持恒定的转化率(变化在±2%)。
再生开始时,使通过催化剂层的甲醇循环使用,可减少甲醇用量。
再生后的甲醇被送入后加工阶段,蒸馏分离出甲醇后循环使用。
该方法的再生周期优选1500~2500h,2个再生步骤之间的环氧化反应时间与再生催化剂时间之比优选在(100~300):
1。
用上述方法进行再生时,需要使反应中断;而采用切换反应器的方式时,需要较多的反应器,这会增加设备成本。
3.