第一章固体表面分析.docx
《第一章固体表面分析.docx》由会员分享,可在线阅读,更多相关《第一章固体表面分析.docx(19页珍藏版)》请在冰豆网上搜索。
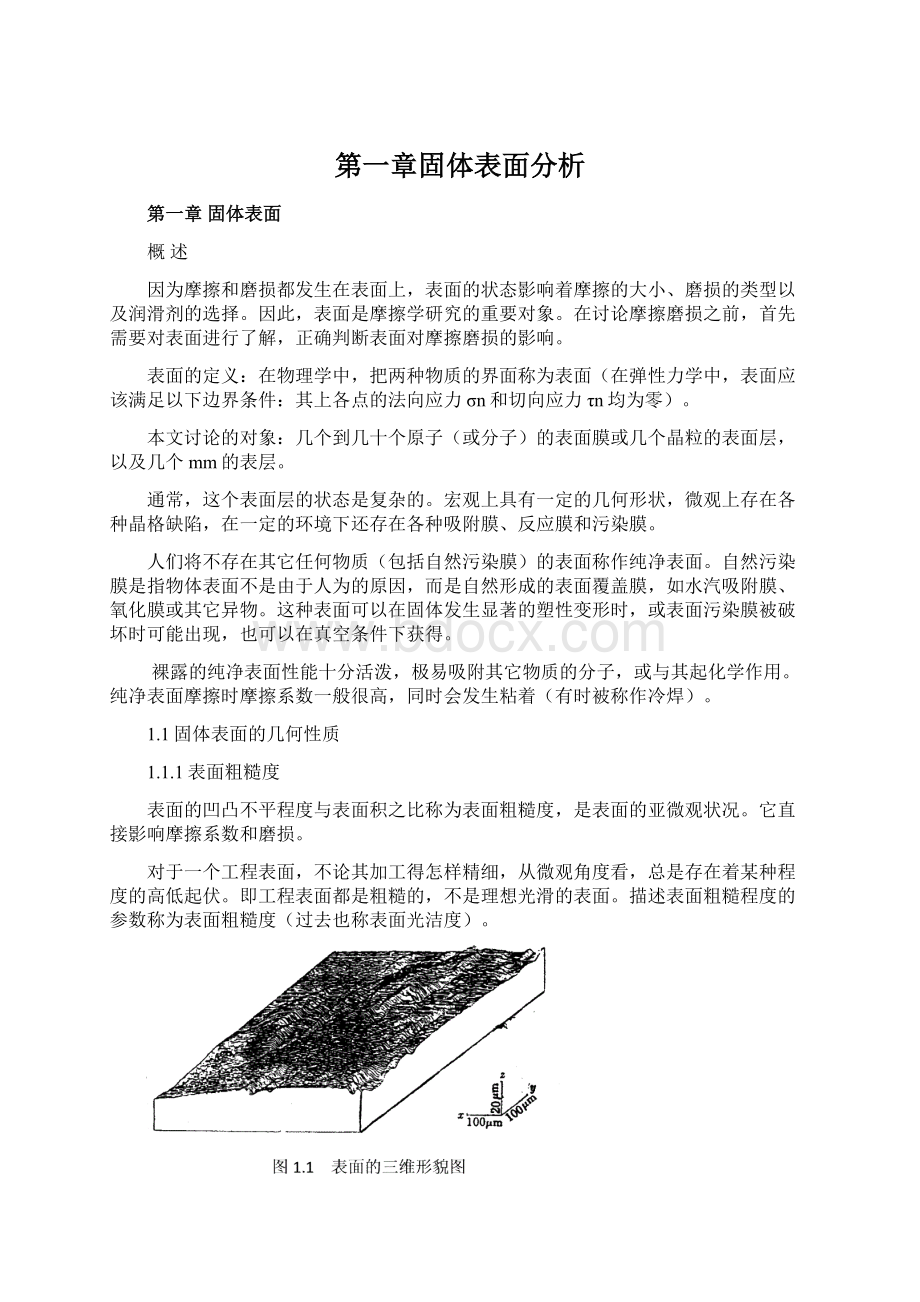
第一章固体表面分析
第一章固体表面
概述
因为摩擦和磨损都发生在表面上,表面的状态影响着摩擦的大小、磨损的类型以及润滑剂的选择。
因此,表面是摩擦学研究的重要对象。
在讨论摩擦磨损之前,首先需要对表面进行了解,正确判断表面对摩擦磨损的影响。
表面的定义:
在物理学中,把两种物质的界面称为表面(在弹性力学中,表面应该满足以下边界条件:
其上各点的法向应力σn和切向应力τn均为零)。
本文讨论的对象:
几个到几十个原子(或分子)的表面膜或几个晶粒的表面层,以及几个mm的表层。
通常,这个表面层的状态是复杂的。
宏观上具有一定的几何形状,微观上存在各种晶格缺陷,在一定的环境下还存在各种吸附膜、反应膜和污染膜。
人们将不存在其它任何物质(包括自然污染膜)的表面称作纯净表面。
自然污染膜是指物体表面不是由于人为的原因,而是自然形成的表面覆盖膜,如水汽吸附膜、氧化膜或其它异物。
这种表面可以在固体发生显著的塑性变形时,或表面污染膜被破坏时可能出现,也可以在真空条件下获得。
裸露的纯净表面性能十分活泼,极易吸附其它物质的分子,或与其起化学作用。
纯净表面摩擦时摩擦系数一般很高,同时会发生粘着(有时被称作冷焊)。
1.1固体表面的几何性质
1.1.1表面粗糙度
表面的凹凸不平程度与表面积之比称为表面粗糙度,是表面的亚微观状况。
它直接影响摩擦系数和磨损。
对于一个工程表面,不论其加工得怎样精细,从微观角度看,总是存在着某种程度的高低起伏。
即工程表面都是粗糙的,不是理想光滑的表面。
描述表面粗糙程度的参数称为表面粗糙度(过去也称表面光洁度)。
用显微镜观察表面,如地球表面的地形。
要用三维图像才能精确描述其表面形貌。
如图1.1所示。
如果表面加工方法有一定规律(如车、铣、刨),人们通常用二维图形来表示。
(如图1.2所示)。
由于加工方法造成的宏观粗糙度呈一定方向和波长的波形(称波度)。
微观粗糙度的波长很短,且具有不同的幅度和间距。
表面上的微小凸起部分称微凸体。
如经过抛光研磨等加工,这种波度明显消失,粗糙度显示出各向同性。
x轴
描述表面粗糙度,不是用其最大的波峰波谷之差。
国标(GB1031-83)规定了两种表面粗糙度的表示方法:
中线平均值(CLA)和平均平方根值(均方根)(RMS)。
图1.3为粗糙表面轮廓的二维示意图。
先取一中线(x轴),把二维轮廓分成上下两半,并满足:
中线上方的轮廓与中线所围的面积等于中线下方轮廓的面积。
令从中线到轮廓的高度为Zi。
①中线平均值(CLA)
表示表面轮廓上各点相对于中线的算术平均偏差。
②平均平方根值(均方根)(RMS)
表示表面轮廓上各点相对于中线的偏差值之平方的平均值的开方。
通常使用RMS比较好,因为,同样的CLA值其表面形貌是可以很不相同的,对摩擦磨损的影响也是不同的。
如图1.4。
而用RMS,图中各不相同的形貌具有不同的表面粗糙度。
1.1.2表面微凸体
用触针式表面轮廓仪可直接测得表面的起伏不平。
不过因其高度方向的放大比例远大于平面方向的。
故所得图形并不能反映峰谷起伏的实际形状。
而用电子显微镜观测到的表面,因其各向放大比例相等而比较真实。
由电子显微镜观测到的图形可以看到,表面上的峰与谷实际上是比较平缓的,因此人们通常取微凸体为近似的半球状、锥状或柱状来进行几何因素的分析。
表面微凸体的高度各点不同,如用统计学的方法进行研究,可以画出表面轮廓上各点的高度(Zi)是个随机的变量,将其不同高度出现的频率(概率)记录下来画成光滑的曲线(图1.5),称为高度分布曲线。
凡经过一般机械加工的表面,其微凸体高度的分布通常接近于正态分布(高斯分布)。
正态分布曲线理论上应延伸到处。
而实际上在的范围内已包括了99.5%的高度(σ为分布的标准差)。
1.2固体表面的原子排列和结构缺陷
经过不同加工过程形成的表面,因机械作用,往往导致材料的晶格扭歪、晶界开裂;由于温升导致金属发生相变而再结晶,使晶粒长大;或因为表层材料变形导致表层密度和体积发生变化,从而在表层的塑性变形层中产生残余应力,甚至产生微裂纹。
金属表层内种种微观性状的改变,均对其摩擦磨损有密切的关系。
因此需对其进行仔细的观察。
金属表面的原子排列具有一定的形状,对于没有缺陷的纯单晶体,表面上的原子排列应是整体材料内部原子排列的延伸。
不同的金属具有不同的晶体结构。
图1.6所示为金属的几种典型结构。
在各种晶体结构中,不同晶面上的原子密度不等。
当承受载荷发生滑动时,原子密度高(原子数多)表面能低的面上,容易发生滑移。
图1.7为立方晶系中几个可能滑移的晶面:
(100)面、(110)面和(111)面。
面心立方的(111)面和体心立方的(110)面,以及密排六方的(001)面都是原子密度高的晶面,沿这类晶面滑移的阻力最小。
但是表面的原子排列,往往不是整体材料内部原子排列的延伸,原子排列得不像理想的那样整齐。
如多晶体表面有镶嵌块结构;多晶体的晶界交错,原子排列常没有规律,而且还有缺陷。
如多晶体表面有镶嵌块结构。
单晶体的表层也会出现各种结构缺陷(如图1.8所示)。
如刀刃位错,形成通向内部的线缺陷;螺型位错,表示该处形成断层,由表面伸向内部,于是在表面上产生台阶;解理断裂形成了曲折和台阶;表面上的原子可能逸出而出现晶格空位,外来的原子可能形成填隙原子;如外来原子局域表面可形成“增附原子”;加上外部的杂质原子,使大多数金属晶体出现很多位错。
这些位错在滑移时会形成台阶。
见图1.5。
晶体材料接触滑动而引起变形的过程中会产生位错台阶(称为表面滑移带或滑移线),滑移带的移动可能与杂质相交,生成更多的位错。
位错堆积的地方会形成早期的微观裂纹。
在有结构缺陷(位错、台阶或空位)的地方会发生晶粒长大、溶解、吸附或化学反应(如腐蚀)等现象。
这些对摩擦磨损都有一定的影响。
这类结构缺陷不仅金属会有,一些非金属晶体(如层状晶体、金刚石、氯化钠和有机润滑剂等)也存在这类结构上的缺陷。
这些缺陷都比较小,需依靠现代的仪器设备才能看到。
如场离子显微镜(FIM),低能电子衍射(LEED),场发射显微镜(FEM)等。
1.3表面张力和表面能
液体受到拉向内部力的作用,使其表面肌收缩和凝聚,这种力叫表面张力。
表面能是指将液体内部分子拉到表面上所需作的功。
当液滴落在固体表面上时(见图1.9),由于液体具有各自的表面张力,它同时受到固体与空气的界面张力(γs)、液体与空气的界面张力(γl)和液体与固体的界面张力(γsl)的作用。
当时,液滴在表面上达到平衡,且具有一固定的形态。
式中:
θ为固液表面间的接触角
不同的液体在同种固体表面上,得到不同的接触角。
接触角小的液体表面张力小。
接触角的大小衡量着固体表面与液体之间的润湿性。
图1.9(a)中的接触角小,表示固液间的润湿性好。
而图1.9(b)中的接触角大,表示固液间的润湿性差。
固体也有表面能和表面张力。
固体的表面能是指将固体拉开而形成新表面时需作的功。
如果固体表面十分洁净(未被污染,也无吸附膜等),则表面处于高能状态。
如其它固体表面与这种表面接触,将显示出高的粘着能力,摩擦明显增大。
表面能高的固体与液体接触时,具有较小的接触角,能很好地与液体润湿,使液体润滑剂能很好地与之亲和,得到低摩擦。
同种液体在不同的固体表面上,也得到不同的接触角。
接触角小的表示固体的表面能高。
是亲水性表面。
接触角大的,说明固体的表面能低,是疏水性表面。
不易与液体亲和也不易与其它固体表面粘着。
对于结晶固体来说,表面能是沿晶面解理而形成新表面所需的解理能。
由于晶体各面的原子数不同,原子数高的表面易于解理,即这些表面的表面能低,易于发生滑移。
1.4表面膜
在一般条件下,固体表面总是被周围介质所包围。
而这些介质(包括气态或液态介质)常常与固体表面发生物理与化学作用,使固体表面的结构变得更复杂。
通常摩擦副由金属制成,金属表面在大气环境中总有一层薄薄的氧化膜覆盖着,氧化膜的外层还有污染膜和吸附膜等,构成了复杂的表面层。
1.4.1吸附膜
表面的洁净程度较高时,极易将周围介质的分子吸附到表面上形成吸附膜。
如果是靠范德华力键合在表面上的称物理吸附膜。
吸附的量是吸附物的分压(当吸附分子为气体时)或吸附物浓度(当吸附物为液体)和绝对温度的函数。
ns=f(p,T)
ns=f(c,T)
式中:
ns为吸附量;p为吸附气体分压;c为吸附液体浓度;T为绝对温度。
吸附膜的牢固程度(吸附力的大小),可以用吸附热来衡量。
吸附热是变量。
开始吸附时的吸附热高,当固体表面布满吸附分子后开始第二层吸附时,固体表面与吸附分子的作用随层数增多而减弱,吸附热就逐渐降低。
直到吸附热降低到没有能力再吸附时,吸附达到饱和。
要除去这种吸附膜,除了机械作用外,用加热可使其脱附。
故物理吸附膜是可逆的吸附膜。
吸附分子与固体表面发生电子交换时(即改变了吸附层分子的电子分布),吸附分子与固体表面的作用是化学键结合,称化学吸附膜。
其作用力比物理吸附膜强。
化学吸附的吸附热值比较高,所以脱附时需要比脱附物理吸附膜更高的温度(更高的能量)。
化学吸附常常是单分子层。
而物理吸附则可能是多分子层。
化学吸附需要一定的活化能,且与吸附剂的表面有关。
所以化学吸附有一定的选择性。
而物理吸附可以在任何表面上发生。
在固体表面上吸附的还有污染膜。
润滑剂分子可在固体表面上形成吸附膜(单分子层或多分子层)。
例如,脂肪酸类的润滑剂,具有很长的分子链,这种细长的分子链被密集地吸附在固体表面上,形成具有一定刚性的边界膜,把承受载荷的接触面分开。
同时,细长的分子有一定的柔性,当承载表面相对运动时,其剪切阻力很低,有明显的减摩效果。
润滑剂分子中如果电子分布不均匀(不对称),则分子链的形状不对称。
缺少(或多余)电荷的分子称偶极子,其一端带正电荷,另一端带负电荷,故也称为极性分子。
极性分子与固体表面的亲和力很强,能牢固地附着在表面上。
常用润滑剂都是长链的碳氢化合物,一端带有氨基(-NH2)、氰基(-CN)、羟基(-OH)、羧基(-COOH)等极性基。
这类极性分子的吸附效果很好。
如果使用的润滑剂无极性分子,可以加入少量具有极性的分子(称为油性剂),使吸附速度加快。
但如果第一层已吸附饱和,则再加入极性分子已不发挥作用,有时反而有副作用。
摩擦面上吸附膜的存在是一种动态过程。
在摩擦过程中,可能因为微凸体使吸附膜受到机械损伤,也可能因为局部摩擦热而被解吸。
同时,吸附又会在新生的表面上再次发生,所以是个动态过程。
如摩擦条件更有利于解吸,则此类吸附膜的减摩作用也将大大降低。
1.4.2表面氧化膜和反应膜
固体表面材料与周围介质起反应,形成的表面覆盖膜称为反应膜。
化学反应总是在物质的相与相的界面上发生。
化学反应必须有原子交换,即需提供一定能量,以得到反应物。
如反应所需的热量越高,表示起反应的温度也越高。
摩擦表面的温升如不能及时散逸,则会加快反应膜的生成速度。
反应速度除与温度有关外,还与压力、浓度和是否使用催化剂有关。
金属表面的氧化膜是典型的反应膜。
金属固体表面在有氧环境中很容易氧化生成氧化物。
氧化物多数以分层形式出现。
如铁的氧化首先是氧在铁表面上的化学吸附,然后氧化层增厚。
增厚过程中,往往出现孔隙和裂纹,有助于氧分子与新鲜表面的金属元素相接触而生成新的氧化物。
由于氧的浓度和反应温度的不确定,故而出现不同化学成分的氧化膜。
图1.10为570℃以上的氧化铁层。
润滑剂吸附膜的极性端与活性的金属表面分子及其氧化物反应生成金属皂膜。
这种皂膜的结构类似于晶态固体,其解吸温度比化学吸附膜还高。
在润滑剂中加入极压添加剂(EP剂),可促使其与金属形成反应膜。
常用的添加剂为含硫、磷、氯等的极性有机化合物。
当这些化合物在高温下与金属表面起化学反应,在金属表面上形成一层抗剪强度低的硫化物、磷化物或氯化物这类无机覆盖物。
这类膜可将摩擦表面隔开,而且承载能力比吸附膜高。
在摩擦过程中如因机械作用被破坏,还能再生。
但是对金属磨损作用,却有复杂的效果。
因为硫、磷、氯等成分对金属有腐蚀作用。
为了防止这类腐蚀作用,可以采用复合添加剂,如加入含锌、铅、钡、釹等元素的有机盐,而生成另一类反应膜,以改善其热稳定性和化学安定性。
以上所述的表面膜(吸附膜和反应膜)通常都覆盖在表面上,使摩擦的固体表面被隔开,有效地防止了固体与固体间的直接接触。
这些表面膜具有一定的承载能力,而其机械强度一般都低于固体自身的整体强度,这种表面膜都对摩擦磨损有明显的影响。
1.5固体表面的接触
1.5.1分子(或原子)间的接触
分子(或原子)间存在着吸力和斥力,当吸力和斥力相平衡时,分子(或原子)间有一个正常的距离d。
当施加外力使分子(或原子)间的距离大于d时,其间存在着吸力;反之,如使其间距离小于d时,则存在着斥力。
当施加的拉力较大,使分子(或原子)间的距离拉开到一定程度时就会发生材料分子的断裂。
原子沿解理面滑移比较容易,晶体往往沿解理面开裂。
要拉开晶格中相互键联的原子(或分子)就必须作功。
要拉开非解理面的原子需要的能量就比沿解理面移动原子的能量大。
在洁净的表面(或由于开裂而形成的初生面)上与介质分子间键联的力通常为范德华力。
而晶格中有的原子间的键力比范德华力高,就难以将这些原子分开。
单晶体不同方位解理而裂开时所需的功是不一样的,所以是各向异性的。
而金属(多晶体)因晶体排列错乱,故为各向同性。
对于金属晶体来说,施加外力可使晶格变形。
当外力卸除后能恢复到原有形状的称为弹性变形;如外力卸除后不能(或不能完全)恢复到原有形状时,残留下来的永久变形称塑性变形。
外力产生弹性变形作的功是可逆的,而产生塑性变形作的功是不可逆的。
1.5.2两表面间的接触
①接触面积
固体表面不论如何精加工都是凹凸不平的。
当在法向力N的作用下,使两固体表面相互压紧时,通常只在很小的面积上发生接触。
接触表面的面积可分为:
a.名义接触面积:
即表面宏观面积——An
b.真实接触面积:
在表观接触面积中,实际传递力的微小面积的总和称真实接触面积Ar。
如图1.11所示。
一般材料在塑性变形范围内的真实接触面积与载荷成正比,与表面的大小和形状无关。
假设接触材料的压缩屈服极限(塑性流动极限)为σb,在法向载荷N作用下相互压紧时,真实接触面积可表示为:
Ar=N/σb
②赫兹(Hertz)接触
经过精细加工的表面,常假定其微凸体为半球状、柱状、锥状等。
对于工程上单个微凸体而言,也并非几何学中的球、柱、锥形。
赫兹接触是在弹性接触范围内分析理想光滑的球(柱、锥)在无润滑条件下的接触。
而实际上也并非全是弹性变形,在接触点处有塑性变形。
从图1.12所示的“光滑”半球体赫兹接触下真实情况的照片,证实了赫兹压力中心处的接触斑点比较密集,而在赫兹压力边远处接触分布比较稀疏。
说明固体表面接触只在传力的微凸体顶端发生塑性变形,离开这小小的塑性变形区变形在弹性范围中。
因此,可以根据弹性理论来计算微凸体(球、柱或锥)接触时的压力分布。
a.椭球与椭球接触:
在法向压力N的作用下相互压紧(见图1.13),在接触部分产生弹性变形。
形成的接触面积,假定为以a和b为半径的椭圆形。
椭园形表面上赫兹压力的分布曲线为:
式中:
σ为坐标在x,y处的压力
σ0为最大赫兹压力,在x=y=0处;
a为接触区面积的x方向半径,
b为接触区面积的y方向半径
在应力椭圆上积分,求σ的总和得接触面上的正压力为:
由正压力N可求得:
b.球与球接触:
则接触面积呈圆形,即a=b。
其压力分布曲线为:
同样经积分可求得
最大压力:
平均压力:
即
接触区的半径:
式中:
R为接触两球的综合曲率半径,与两接触球半径的关系如下:
E为两球的综合弹性模量,与两接触材料性能的关系如下:
式中:
R1,R2分别为两接触球的半径;E1和E2以及ν1,和ν2分别为两球材料的弹性模量和泊松比。
则最大赫兹压力σH(x=y=0处):
c.球与平面的接触:
可对两球接触的公式中取:
R2=∝ R1=R,
则
d.圆柱与圆柱的接触:
接触面积为矩形。
长度为L,宽度为b。
则
总压力为
最大压力
接触半宽
经代入简化,得
式中:
R综合曲率半径;E综合弹性模量。
e.圆柱对平面的接触:
将R2=∞,R1=R代入圆柱对圆柱接触公式
则
f.赫兹接触的变形和接触面积
赫兹压力分布曲线表明,最大压应力在接触区的中心。
最大剪切应力在距压力中心处深度约0.5a的表层下,τmax≈0.3σ0。
最大拉应力作用在接触面边界处,σ≈0.133σ0。
接触承载时,表层下的某一深度处(0.5a)剪应力最大,材料在该处首先屈服。
但此屈服区很小,而且处于三个方向受压的状态。
而这小范围的塑变区,被四周弹性状态的材料包围着(见图1.14)。
通常材料在接触承载时,表面的最大压力:
σ0=3.1τs(τs为材料的剪切屈服极限)时,表层下剪应力的最大值τmax达到τs,就开始屈服。
但图中的塑性区很小,且处于三向受压状态。
所以当σ0=3.1τs时,表面材料仍未屈服。
直到表面平均压力σm≈6τs时,塑性区才扩展到表面,材料才开始屈服,表面上才留下压痕。
这时的平均压应力σm≈6τs≈σb(σb相当于压痕硬度H)。
剪切屈服极限与抗拉屈服极限的关系为:
τs≈0.5σs(σs材料拉伸时的屈服极限)。
即在接触承载时,材料发生塑性变形时的压应力相当于3倍的拉伸屈服极限。
对于大多数金属而言,都有以下关系:
H≈6τs≈3σs
因此材料发生塑性变形时的真实接
触面积:
此值大约只有表观接触面积的1/1000。
由此可见,真实接触面积的大小只取决于载荷和材料的流动压力,而与表面粗糙度的关系不大,与宏观表面积也无关。
③赫兹接触的法向接近
当一个球与平面在法向载荷N的作用下弹性接触时,球将发生变形,使球的中心下移,此下移量称为法向接近量δ。
如图1.15所示。
如只在球上发生弹性变形(图中a),根据几何图形可知R2=(R-z)2-r2,即
因为z<<2R,所以
式中r=a(接触面积的半径)
如球与平面都发生弹性变形,
将球对平面的赫兹接触中的代入上式
则得或
式中:
E为综合弹性模量;R球的半径;δ法向接近量。
变形后的接触面积A=πα2
式中α为接触面积的半径。
α2=Rδ
即在弹性范围内,变形后的接触区面积A=πα2=πRδ。
1.5.3理想的粗糙表面接触
假设微凸体都是理想光滑的半球,而且具有等高度、等半径的。
当一个理想光滑的刚性平面在法向力N的作用下与之接触时的情况如图1.16所示。
当处于弹性变形范围内,每个微凸
体承受的法向载荷
为:
式中:
ρ为微凸体的顶端半径;
δ为法向接近(图1.16中δ=Z-d);
N=n·Ni
每个微凸体的接触面积Ai=πρδ
经代入前面导出的公式,并简化后得到接触总面积:
式中:
这说明,弹性变形范围内,具有等高度、等半径的微凸体表面,在承载时,其接触面积Ar与载荷N成指数关系,为与N的2/3次幂成正比。
如法向载荷N增大,使微凸体顶端压力达到流动极限H时,微凸体发生塑性变形。
此
时的接触面积为与法向载荷N呈线性关系。
1.5.4实际粗糙表面的接触
实际工程表面微凸体的高度为正态分布。
假设与理想平面接触,法相接近量为δ=Z-d。
那么只有高度Z>d的微凸体才能与之接触(见1.17)。
根据赫兹接触公式及假设微凸体高度为指数分布,并设h=d/ε。
可
推导出:
比较上面两式,可见
式中:
N为法向载荷;A为总支承面积;c为常数项;ε=d/h表面粗糙度RMS;
h微凸体高度指数分布的指数。
这说明,高度为指数分布的微凸体发生弹性变形时,实际接触面积与法向载荷之间为简单的线性关系。
当微凸体顶端为塑性变形时:
A=N/H。
这一结果与高度分布无关。
实际上工程表面上微凸体的高度是按正态分布的。
由于高斯曲线顶端一段(约占25%的一部分),与指数函数十分接近,所以可以把它看作指数分布。
由此得到的结论是:
两个实际工程表面接触时,不论微凸体的顶端在弹性变形范围,还是在塑性变形范围,变形后所形成的真实接触面积A都与法向载荷N之间呈简单的线性关系。
1.5.5接触变形性质的判据
在实际工程表面间的接触,往往是高的微凸体可能产生塑性变形,低的则为弹性变形。
说明实际情况是弹、塑性混有的状态。
载荷越大,法向接近越大,塑性接触点越多。
所以法向接近量δ的大小,在N确定的情况下,反映了表面微凸体接触后发生塑性变形的程度。
当微凸体处于弹性接触时,平均压力σm<3σs。
将和A=πRδ=πρδ
代入,得和
而当最大压应力σ0=3.1τs或σm≈σs=1/3H时(H=3σs),开始转变为塑性变形。
此时
当σm≈6τs=3σs=H时为完全塑性变形,进一步扩大到
式中:
σm平均压应力;σs拉伸屈服极限;τs剪切屈服极限;δ法向接近量;
ρ微凸体顶端半径;H硬度(压缩屈服极限);E综合弹性模量。
在的等式前后除以得
将定义为塑性指数(ε为表面粗糙度RMS)。
用ψ来表示,则:
认为:
ψ>1为塑性接触;ψ<0.6为弹性接触。
这里可见,接触变形的性质不完全取决于载荷,而是与材料性质、表面粗糙度ε、微凸体顶端的平均曲率半径ρ有关。
ψ反映了接触表面的某些物理与几何性质的影响。
如一些零件经过磨合,由于表面粗糙度在磨合前后发生明显变化,而使ψ迅速降低。
1.5.6表面间有表面膜存在时的接触(见图1.18)
表面膜的存在,对于真实接触面积的计算没有什么影响。
因为表面的粗糙不平为10~100nm,远大于表面污染膜的厚度几nm,表面氧化膜的10~30nm,两表面接触时只有少数高点接触,大部分面积上的表面膜与对摩面上的表面膜相隔甚远,所以多数原子(或分子)间并不发生作用。
而且接触部分的面积比膜厚大得多,只要表面膜不破裂,微凸体的变形情况和表面上实际承载面积的大小,仍然取决于表层材料的物理性能和表面的几何性质。
因此,膜的存在对计算真实接触面积的影响不大。
但是,表面膜的存在对于表面的粘着是很有影响的。
洁净表面的真实接触面积上金属分子的相互作用很强,很容易粘着。
而接触面间有表面膜存在时对摩擦磨损的影响都是很明显的。
1.6摩擦状态下的表面
前面讨论的都是静态下表面的特征和表面接触状态。
摩擦一开始表面就是动态状况了。
一旦开始运动,由于载荷下接触时表面会发生变形,有弹性变形,也有塑性变形。
使表面与未接触时的原始状态发生了明显的变化。
在摩擦过程中,由于摩擦功变成热能使表面温度升高,引起表面的物理化学性能发生某些变化,从而又影响其接触状态。
摩擦过程中的发热效应,还会使表面发生晶体结构或机械性能的变化。
直接影响以后的摩擦情况。
摩擦过程中,由于接触而发生材料间的粘着。
对于不同的摩擦对偶表面和不同的摩擦条件下,粘着发生的部位及损伤程度各有不同。
这样,使摩擦表面在摩擦过程中不断被损伤或磨损,也即不断地发生着变化。
摩擦过程中润滑剂也将引入摩擦面。
不同的润滑剂将以不同形式和方法导入,不同成分的润滑剂会与表面产生不同的效果或发生不同的反应,又会改变表面的状况。
因此,摩擦状态下的表面以及摩擦的整个过程,是一个非常复杂的系统。
参考资料
1.陈耕、汪一麟,《摩擦与磨损》,同济大学出版社,1989,上海
2.郑林庆,《摩擦学原理》,高等教育出版社,1994,北京