发动机连杆设计.docx
《发动机连杆设计.docx》由会员分享,可在线阅读,更多相关《发动机连杆设计.docx(27页珍藏版)》请在冰豆网上搜索。
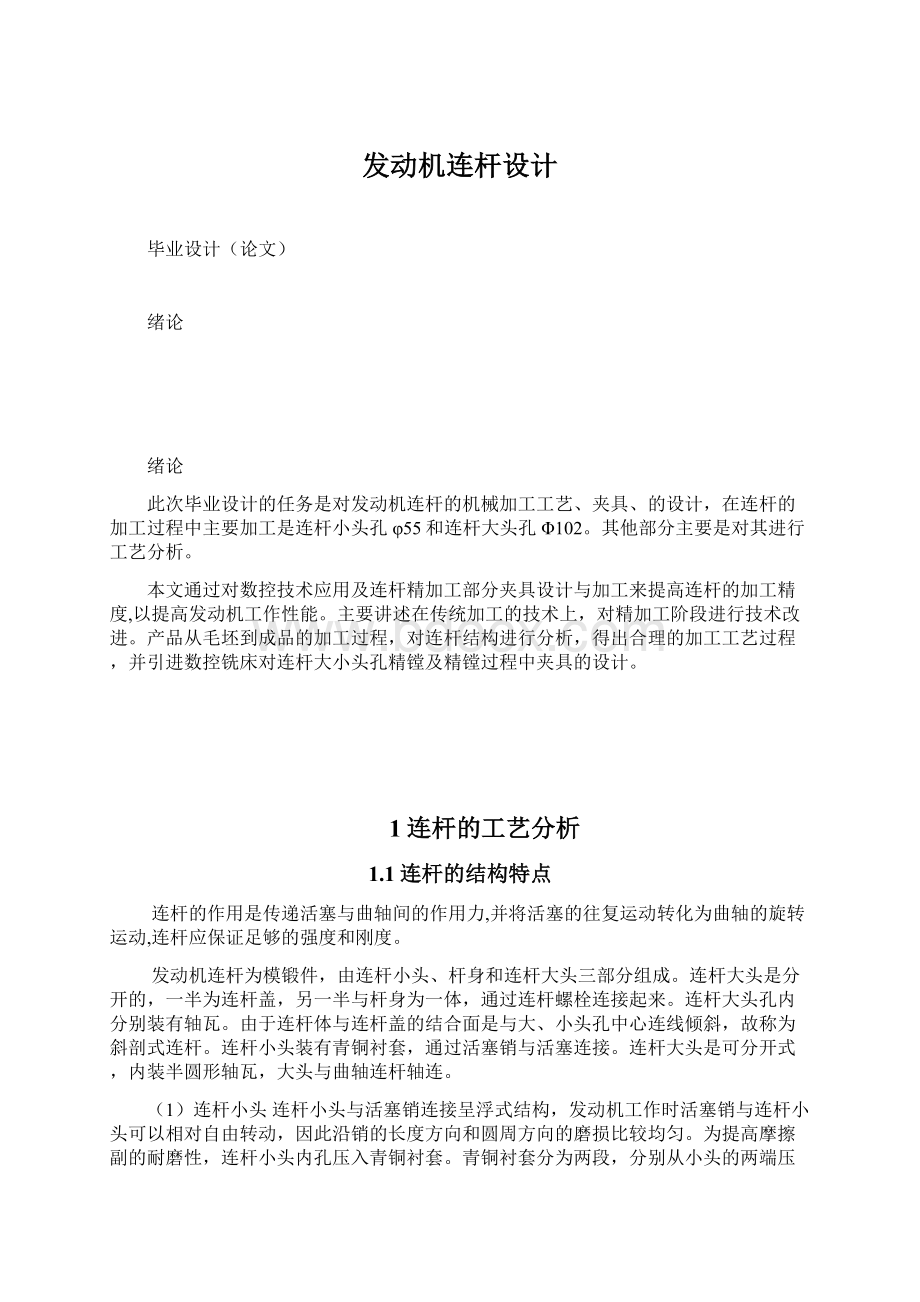
发动机连杆设计
毕业设计(论文)
绪论
绪论
此次毕业设计的任务是对发动机连杆的机械加工工艺、夹具、的设计,在连杆的加工过程中主要加工是连杆小头孔φ55和连杆大头孔Φ102。
其他部分主要是对其进行工艺分析。
本文通过对数控技术应用及连杆精加工部分夹具设计与加工来提高连杆的加工精度,以提高发动机工作性能。
主要讲述在传统加工的技术上,对精加工阶段进行技术改进。
产品从毛坯到成品的加工过程,对连杆结构进行分析,得出合理的加工工艺过程,并引进数控铣床对连杆大小头孔精镗及精镗过程中夹具的设计。
1连杆的工艺分析
1.1连杆的结构特点
连杆的作用是传递活塞与曲轴间的作用力,并将活塞的往复运动转化为曲轴的旋转运动,连杆应保证足够的强度和刚度。
发动机连杆为模锻件,由连杆小头、杆身和连杆大头三部分组成。
连杆大头是分开的,一半为连杆盖,另一半与杆身为一体,通过连杆螺栓连接起来。
连杆大头孔内分别装有轴瓦。
由于连杆体与连杆盖的结合面是与大、小头孔中心连线倾斜,故称为斜剖式连杆。
连杆小头装有青铜衬套,通过活塞销与活塞连接。
连杆大头是可分开式,内装半圆形轴瓦,大头与曲轴连杆轴连。
(1)连杆小头连杆小头与活塞销连接呈浮式结构,发动机工作时活塞销与连杆小头可以相对自由转动,因此沿销的长度方向和圆周方向的磨损比较均匀。
为提高摩擦副的耐磨性,连杆小头内孔压入青铜衬套。
青铜衬套分为两段,分别从小头的两端压入。
小头的顶上有一个集油孔,当曲轴旋转时,激溅起来的机油甩到活塞内腔的顶部,冷却活塞后,落下一部分通过集油孔聚集并流入连杆的小头内孔润滑活塞销。
(2)杆身发动机为了在最小质量时最大的强度和刚度,连杆杆身断面加工成“工”字形。
(3)连杆大头连杆通过大头与曲轴上的连杆轴颈相连,连杆大头为分开式,采用简单的平口结构形式。
连杆大头轴承盖固定螺母为自锁型螺母,其拧紧力为100~120N.m
1.2连杆的主要技术要求
小头孔φ55mm(未装铜套)是与活塞销配合的表面,加工尺寸精度为IT6,圆柱度公差为0.004~0.006mm、表面粗糙R0.8。
小头孔与活塞销的配合精度要求较高,如果配合间隙过小,会影响连杆与活塞间的传动力效果,如果配合间隙过大,就会产生晃动,使发动机在运行中发出敲击声,考虑到工作后的摩损量0.01,因此,安装时必须保证连杆小孔与活塞销之间的配合间隙。
要在加工中直接满足这一要求显然是困难的,因此在装配时,把连杆小头孔分成四组,每2.5um的尺寸间隔为一组,分组进行装配,才能有效控制配合间隙。
1.2.1大、小头孔的尺寸精度要求、形状精度
大头孔φ102mm(未装轴瓦)
大头孔上要装轴瓦,通过轴瓦与曲轴配合,为了保证良好的配合精度减小冲击的影响,大头孔的加工精度为IT6,圆柱度为0.004~0.006mm,表面粗糙度R为0.8um。
1.2.2大小头孔两端面
大头孔两端面与曲轴轴承座端面配合,其精度影响到安装和磨损,,端面跳动(100:
0.1)/mm,小头厚度52mm大头厚度为65mm。
1.2.3大小头孔中心距及孔的中心线的平行度和扭曲
大小头孔的中心距影响到发动机的压缩比,即发动机的工作效率,所以规定了较高的要求,中心距为280mm;大小头孔的中心线的平行度误差会使活塞在气缸中倾斜,造成气缸壁磨损不均匀,同时使曲轴的连杆轴颈产生边缘磨损,缩短发动机的使用寿命,所以规定平行度公差为0.02~0.04/100mm;大小头孔中心线的扭曲对不均匀磨损的影响较小,一般规定扭曲度不大于0.04~0.06/100mm。
这两项技术要求,对于结构刚性较差的连杆来说,加工可能有些困难,但是为了保证发动机的使用寿命,必须达到这些要求,加工中应特别注意。
1.2.4连杆连接螺栓孔的技术要求
连杆在工作过程中,受到急剧的动载荷的作用,这一作用又传递到连杆体和盖的两个连接螺母上。
因此,除了对螺栓及螺母提出较高的技术要求外,对螺栓孔及两螺栓孔端面也有一定的要求,两螺栓孔在互相垂直的两个方向的平行度公差为0.02~0.04:
100mm,两螺栓孔φ18.5mm与接合面的垂直度为0.1~0.2:
100mm,两螺栓孔的尺寸公差为0.021mm。
此外,连杆的毛坯都要求通过锻造来改善金相组织。
对于连杆体和盖分开锻造的毛坯,锻造工艺较整体锻造简单,金属纤维呈连续型式,使大头具有较高的强度,不易产生变形,但分开锻造使材料消耗增加,机械加工虽然省去了切开工序,但结合面加工余量较大,两侧平面加工余量较大,两侧平面加工需要分开进行,故机械加工工艺较整体锻造复杂。
整体锻造在切开体与盖的工序之后,金属纤维呈断裂状,强度减弱,加工后变形较大,但比整体锻造节省材料,提高了金属的利用率,生产效率高,便于组织生产,特别适于大批量生产。
考虑到整体锻造毛坯在切开体,盖后金属纤维呈断裂状的缺点,所以在连杆的大头增加了带“耳朵”形的肋。
连杆螺母的自锁,是利用连杆螺栓螺母上所开六个槽,拧紧螺母后,由于螺母的弹性变形保持有100~120N.m的扭矩。
由于该扭矩的作用,使螺母的底面受一向上顶的力,螺母产生的弹性变形卡住螺栓,保证螺母在工作时不会松动。
1.2.5有关结合面的技术要求
结合面主要应考虑其垂直度、粗糙度。
结合面与螺栓孔的垂直度为100︰0.15,表面粗糙度为Ra=0.8µm
1.3连杆的材料和毛坯
连杆材料一般采用45钢或40cr、45Mn2等优质钢或合金钢,近年来也有采用球墨铸铁的(粉末冶金),本连杆采用40MnB。
钢制连杆都用模锻制造毛坯。
连杆毛坯的锻造工艺有两种方案:
将连杆体和盖分开锻造;连杆体和盖整体锻造。
整体锻造或分开锻造的选择决定于锻造设备的能力,显然整体锻造需要有大的锻造设备。
从锻造后材料的组织来看,分开锻造的连杆盖金属纤维是连续的,因此具有较高的强度;而整体锻造的连杆,铣切后,连杆盖金属纤维是断裂的,因而消弱了强度。
整体锻造要增加切开连杆的工序,但整体锻造可以提高材料的利用率,减少结合面的加工余量,加工时装夹也较方便。
整体锻造只需一套锻模,一次便可锻成,也有利于组织和管理生产。
故一般只要不受连杆盖形状和锻造设备限制,均尽可能采用连杆的整体锻造工艺。
毛坯锻模后应正火并校直。
毛坯要经过调质热处理(加工量大时最好在粗加工后进行调质处理)。
其规范为:
(1)升温,880℃,保温90分。
(2)淬火,在浓度为1/1000的聚乙烯醇水溶液中进行,淬火硬度HRC50。
(3)回火升温580℃,保温120分,在空气中冷却。
(4)检查检查机械性能及变性量。
变形量在3~5毫米时允许整形以保证图纸要求,但整形后必须经消除内应力的热处理。
酸洗后要对毛坯进行喷丸处理。
表面喷丸是利用机械敲击产生表面残余压应力来强化机件,可以显著地提高零件的疲劳强度。
合金结构钢经表面喷丸强化后其疲劳极限能提高40~50%。
喷丸还可以提高表面硬度和耐磨性,降低应力集中敏感性,消除毛坯表面轻微脱碳的不利影想。
因此,喷丸处理是一项十分有效的工艺措施。
本连杆毛坯采用整体精密模锻工艺,连杆小头孔不予锻出,其目的为了减小在钻削小头孔时刀头偏离现象带来的加工难度。
连杆大头孔结构为椭圆状,如图1-1所示,其目的是为杆盖切离后,连杆大头孔因铣削缩短了杆盖之前的实际距离,使其接近圆以减小工作强度。
1.4连杆的机械加工工艺过程
铣连杆大、小平面粗磨大、小头平面、加工小头孔、铣大头两则面、扩大头孔、铣开连杆体和盖、加工连杆体、铣、磨连杆盖结合面、铣、钻、镗连杆总成体、粗镗大头孔、大头孔两端倒角、精磨大小头两平面、半精镗大头孔及精镗小头孔、精镗大头孔、镗小头孔衬套、珩磨大头孔、连杆的检验。
1.5连杆的机械加工工艺过程分析
1.5.1工艺过程的安排
加工阶段的划分和加工顺序的安排
连杆本身的刚度比较低,在外力作用下容易变形;连杆是模锻件,孔的加工余量较大,切削加工时易产生残余应力。
有残余应力存在,就会有变形的倾向。
因此,在安排工艺过程时,应把各主要表面的粗、精加工工序分开。
这样,粗加工产生的变形就可以在半精加工中得到修正;半精加工中产生的变形可以在精加工中得到修正,最后达到零件的技术要求。
如大头孔先进性粗镗,连杆合件加工后半精镗大头孔,精镗大头孔。
在工序安排上先加工定位基准,如端面加工的铣、磨工序放在加工过程的前面。
连杆工艺过程可分为以下三个阶段:
粗加工阶段
粗加工阶段也是连杆体和盖合并前的加工阶段:
基准面的加工,包括辅助基准面的加工;准备连杆体及盖合并所进行的加工,如两者对口面的铣、磨等。
半精加工阶段
半精加工阶段也是连杆体和盖合并后的加工,如精磨两平面,半精镗大头孔及孔口倒角等。
总之,是为精加工作准备阶段。
精加工阶段
精加工阶段主要是最终保证连杆主要表面—大、小头孔全部达到图纸要求的阶段,如珩磨大头孔、精镗小头孔轴承孔等。
定位基准的选择
连杆加工工艺过程的大部分工序都采用统一的定位基准:
一个端面、小头孔及凸台。
这样有利于保证连杆的加工精度,而且端面的面积大,定位也比较稳定。
由于连杆的外形不规则,为了定位需要,在连杆大头处作出工艺凸台,作为辅助基准面。
连杆大、小头端面对称分布在杆身的两端,由于大、小头孔厚度不等,所以大头端面与同侧小头端面不在一个平面上。
用这样的不等高面作为定位基准,必然会产生定位误差。
制定工艺时,可先把大、小头作成一样的厚度,这样不但避免了上述缺点,而且由于定位面积加大,使得定位更加可靠,直到加工最后阶段铣出这个阶梯面。
确定合理的夹紧方法
连杆是一个刚性较差的工作,应十分注意夹紧力的大小,作用力的方向及着力点位置的选择。
以免因受夹紧力作用而产生变形,使得加工精度下降。
实际生产中,设计的粗铣两端面的夹具中,夹紧力的方向与端面平行,在加紧力作用的方向上,大头端部与小头端部的刚性大,即使有一点变形,也产生在平行于端面的方向上,对端面平行度影响较小。
夹紧力通过工件直接作用在定位元件上,可避免工件产生弯曲或扭转变形。
主要表面的加工方法
两端面的加工
连杆的两端面是连杆加工过程中最主要的定位基准面,而且在许多工序中使用。
所以应先加工它,且随着工艺过程的进行要逐渐精化其基准,以提高其定位精度。
大批量生产多采用拉削和磨削加工;成批量生产多采用铣削和磨削。
铣两端面时,为保证两端面对称于杆身轴线,应以杆身定位。
铣削时多采用下面两种铣削方法:
一种是在专用铣床上装两把硬质合金端铣刀盘,工件装夹在回转工作台上低速回转进给运动,粗铣同时进行,只是切深不同,加工完一个面,转过180°再加工另一端面;另一种铣削方法是在专用的四轴龙门铣床上,用四把端铣刀从两端面方向同时铣削大、小两端面。
两端面的磨削加工,一般在立轴平面磨床上用磨轮端面进行磨削,生产率较高。
在大量生产中,可采用双端面磨床进行磨削,以保证两端面的平行度和高的生产率。
大、小头孔的加工
连杆大、小头孔的加工时连杆加工中关键工序,尤其大头孔的加工是连杆各部分加工中要求最高的部位,直接影响连杆的质量。
一般先加工小头孔,后加工大头孔,合装后再同时精加工大、小头孔。
小头孔小,锻坯上不锻出预孔,所以小头孔首道工序为钻削加工。
加工方案多为钻-扩(拉)-镗(铰)。
无论采用整体锻还是分开锻,大头孔都会锻出预孔,所以小头孔首道工序都是粗镗(或扩)。
大头孔的加工方案多为:
(扩)粗镗-半精镗-精镗。
在大、小头孔的加工中,镗孔是保证精度的主要方法。
因为镗孔能够修正毛坯和上道工序造成的孔的倾斜,易于保证孔与其它孔或平面的相互定位精度。
虽然镗杆尺寸受孔径大小的限制,但连杆的孔径一般不会太小,且孔深与孔径比皆在1左右,这个范围镗孔工艺性最好,镗杆悬伸短,刚性也好。
大、小头孔的精镗一般都在专用的双轴镗床同时进行,由条件的厂采用双面、双轴金刚镗床,对提高加工精度和生产率效果更好。
大、小头孔的光整加工是保证孔的尺寸、形状精度和表面粗糙度不可缺少的加工工序。
一般采用以下三种方案:
1)珩磨。
2)金刚镗。
3)脉冲式滚压。
1.5.2定位基准选择
在制定连杆机械加工工艺规程时,定位基准的选择与否,对能否保证连杆的尺寸精度和相互位置精度要求及对连杆各表面的加工顺序安排都有很大影响。
采用夹具装夹工件时,定位基准的选择还会影响到夹具的结构。
定位基准的选择,是设计连杆加工工艺改过程的首要问题。
在许多情况下,连杆的技术条件能否获得保证,首先决定于基准的选择正确与否。
因此定位基准的选择是一个很重要的工艺问题。
基准是连干上用以确定其他点、线、面位置所依据的那些点、线、面。
本零件主要考虑工艺基准中的定位基准。
定位基准可分为精基准和粗基准。
选择定位基准时,是从保证工件加工精度要求出发的,因此,定位基准的选择应先选择精基准,再选择粗基准。
选择精基准主要是从经济可靠地保证连杆各加工表面间的相互位置精度出发。
一般应考虑如下问题:
图1—2
精基准的选择
选择精基准时主要应考虑保证加工精度和工件安装方便可靠,如图1—2所示。
(1)因为连杆的大小端孔、大小端两端面、分开面、结合面以及螺栓孔等各加工表面间的相互位置精度都很高,既不能一次加工而成,又不能在一次安装中把这些有相互位置精度要求的各加工面都同时加工出来,而是经过多次安装,反复加工后逐步达到图纸要求的,所以,为了保证各加工表面的相互位置精度,要避免过多地转换定位基准,应尽量选择一个使大部分工序都可用它来作为定位基准的表面作为精基准。
这就是“基准统一”原则。
(2)由于连杆刚性较差,容易产生杆身弯曲变形,而直接影响各加工表面之间的相互位置精度,所以,要选择支撑面积大、精度高、定位准确、又能防止夹紧变形的表面作为精基准。
(3)尽量选择零件图上的设计基准作为精基准,即“基准重合”的原则。
这样,图纸上的设计尺寸是直接保证的,可以避免因定位基准与设计基准不重合而引起的基准不重合误差对该设计尺寸的影响。
为了满足以上要求,以连杆的大小端面及工艺面作为定位基准,并且在机械加工的开头就把这组定位基准面加工出来,且达到一定精度。
这种基准面在夹具中定位时,大小端端面面积大、精度高、定位准确、夹紧可靠,可作为极限工件沿Z轴移动、绕X轴和Y轴转动的三个自由度的主要基准面;工艺面间距离较大,可作为极限工件一个移动自由度和一个转动自由度的导向基准面,以使导向正确;工艺面面积狭窄,可作为限制工件一个移动自由度的止推基准面.
图1—3落差平面的定位方法
对于这组基准面的定位方法如图所示。
由于大小端端面不在同一个平面上,两者之间有落差。
为了减少落差而引起的定位误差,可将支承小端端面的夹具定位元件作成能随落差值变化而自动定位的浮动支承,这样才不会破坏固定支承对主要基准面大端端面的定位。
这种定位方法可以使得连杆在整个机械加工过程中,精基准得到统一。
其优点是:
(1)不仅避免了基准转换过多到来的积累误差,还为在一次安装中同时加工出有相互位置精度要求的表面提供了有利条件,从而使连杆大小端孔轴心线之间的平行度和扭曲度以及大小端孔轴心线分别对大小端面的垂直度等都达到了图纸的要求。
(2)由于小端孔的位置是靠大小头端端面决定的,大端孔的位置是根据小端孔中心线和小端端面决定的,所以,工艺面大小端端面是小端孔的设计基准,而小端孔中心线和小头端端面是大头孔的设计基准。
如用上述方式定位大小头端面孔,则定位基准和设计基准重合,基准不重合的误差等于零。
(3)简化了工艺过程设计,并使各工序的夹具结构基本相同或相似。
从而减少了设计和制造夹具所需的时间和费用,加速生产准备工作,降低生产成本。
图1—4连杆精基准的定位方法
为了提高主要基准面大端端面的定位精度,采用其中一个无工艺凸台的大端端面为精基准,并且该端面的加工应以已加工的有工艺凸台的大端端面定位,如图1—4所示。
对定位基准的定位方法如图所示。
大端端面用支承板定位,其作用相当于三个定位点,消除了工件一个移动(OZ方向)两个转动(OX和OY方向)的自由度;小端孔用短销定位,相当于两个定位点,又消除了工件两个移动(OX和OY方向)的自由度;大端工艺侧面用小支承板定位,由于其长度和宽度都比工件相差很大,所以只能相当于一个定位点,即只能消除工件以一个转动(OZ方向)的自由度。
这样,就完全限制了工件的六个自由度。
在加工小端孔夹具中,小端孔是用可伸缩的短销定位,在定位和夹紧后,再将定位销从小端孔中抽出。
1.5.3确定合理的夹紧方法
连杆是一个刚性较差的工件,在外力作用下容易产生变形,如果在夹紧状态下检查精度时,达到了规定的精度,但在松开后,由于工件的弹性变形的恢复而使连杆精度受到损失,因此,在选择连杆定位基准的同时,必须正确确定夹紧力的方向和着力点,注意防止连杆的夹紧变形。
夹紧力的方向对夹紧力作用方向的确定,就必须考虑下列问题:
(1)夹紧力的作用方向应朝向工件的主要基准面,把工件压向夹具定位面,以保证工件定位的准确性。
(2)夹紧力的作用方向应使工件变形最小。
夹紧力的着力点
夹紧力着力点的问题是指在夹紧方向的情况下,确定夹紧力着力点的位置和数目。
着力点的选择原则首先是不应破坏工件在定位时已经确定的位置。
如果着力点选择不当,会使工件产生翻转力矩。
为了防止工件切削时的振动,夹紧力的着力点应尽可能地靠近加工面,以使切削力对夹紧力作用点的力矩最小。
这是由于工件在承受平行于接触表面的切削力时最容易产生转动现象,而转动的中心往往正是夹紧力的着力点。
由于连杆刚性较差,很容易产生夹紧变形,所以夹紧力的着力点必须作用于工件的刚性最大的部位上,一定要避免在连杆杆身上进行夹紧。
否则就会造成连杆弯曲变形,而影响各加工表面间的相互位置精度。
应十分注意夹紧力的大小,作用力的方向及着力点位置的选择,以免因受夹紧力作用而产生变表面形,使得加工精度降低。
在生产中,设计的粗铣两端面的夹具中,夹紧力的方向与端面平行,在夹紧力作用的方向上,大头端部与小头端面的刚性大,即使有一点变形,也产生在平行于端面的方向上,对端面平行度影响较小。
夹紧力通过工件直接作用在定位元件上,可避免工件产生弯曲或扭转变形。
1.5.4连杆两端面的加工
连杆两端面的加工主要为后续工序的加工作好定位基准,其加工精度直接影响连杆大小头孔的同轴度,在加工过程中应选择适合的夹紧力,以免因夹紧变形造成材料变形,从而影响定位基准。
1.5.5连杆大、小头孔的加工
连杆大小头孔的加工是连杆加工的关键,确定基准是关键。
在加工连杆孔时以前序工序中两端面和工艺凸台为定位基准。
在镗削过程中,应选择合理的切削用量及夹具,在本工序中,采用了手动夹紧和液压夹紧来达到加工要求,这在后面会得以讲述。
1.5.6连杆螺栓孔的加工
连杆体和盖是用螺栓连接的,螺孔内部由螺纹、销部构成,其精度要求较高。
连杆大头与曲轴连接,当螺孔内与螺栓,销部接触位过盈配合,当接触不良时,在交变载荷的作用下,螺栓发生变性甚至断裂,将造成严重的后果,故在加工螺孔时,应充分考虑,钻孔、铰孔时排削问题以使螺孔达到设计要求。
螺纹底孔本身的螺纹精度主要取决于丝锥的精度,而螺纹中心线的不垂直度及其对其它表面的不平行度、不垂直度等形位精度则主要取决于螺纹底孔的形位精度。
所以对连杆螺栓孔的底孔采用以枪钻为基型的高压强制排屑的高速精钻工艺。
1.5.7连杆体和盖的铣开工序
连杆体和盖的铣开工序应注意切削时定位的可靠性及满足加工要求。
连杆大头肩部加载两个垂直向下的压力,为避免在铣削过程中连杆盖的夹紧刚度,应连杆盖中心垂直位置的垂线上预紧一定的力,并使压板与销对称,压紧力不易太大,以免连杆盖变形。
1.5.8大、小头侧面的加工
大头侧面的加工包括,大头工艺凸台的铣削,钻孔处工艺凸台的铣削是保证后序工序钻销螺孔的精度及钻削时刀具不发生倾斜而造成的偏差,故需精铣大头工艺凸台。
大头侧面的加工包括大头孔下端工艺凸台的铣削,钻孔处工艺凸台的铣削。
大头下端凸台的加工是为加工大头孔作定位基准。
通过小头孔的定位保证大头下端凸台与大小头孔中心线垂直度。
钻孔处凸台位于偏离中心处是为钻孔及连杆体盖切削作准备,尤其是大头孔下端凸台对连杆大头的垂直度影响较大
1.5.9加工小头孔
小头孔分粗加工,半精加工,精加工三个阶段。
主要为了消除在加工过程中因金属切削产生材料内部变形所引起的应力。
由于粗加工中要切除大量的金属材料,在不受力或受力减少时,材料内部组织会释放出因变形产生的力,这在金属加工中应慎重予以考虑。
1.5.10精镗大头孔
大头孔的镗削安排在数控卧式铣床上进行,这不仅可以保证连杆孔的加工精度,也可降低劳动工人的劳动强度,这将在后面予以介绍。
1.5.11小头孔压入衬套
本工序由钳工工人使用专有工具,将衬套压入连杆小头孔中,为后续的精镗做好准备,在压入时,应保证衬套在小头孔中的牢靠性。
1.5.12镗小头衬套孔
采用金刚镗床,连杆大头工艺凸台和小头的定位插销,小头的连杆体来进行定位,从而保证其定位精度,进而保证连杆的加工精度。
1.5.13珩磨大头孔
珩磨是磨削加工的特殊形式,又是一种高效率的加工方法,并且加工精度高,表面质量好。
连杆大头孔同轴度较高,在磨削大头孔时,其同轴度达到5µm以下,另一方面珩磨加工面具有交叉网纹,有利于润滑油的储存及油膜的保持,并具有较高的表面支承率(孔与轴的实际接承受较大的载荷,耐磨损,从而延长了使用寿命。
加之珩磨时速度低(只是普通磨削速度的几十分之一),且油石与孔是面接触,因此每一粒磨粒的平均磨削压力很小,这样工件的发热量很小,连杆产生的变形量也小。
由于在珩磨是将安装在珩磨头周围的若干条油石张开机构将油石沿径向张开,使其压向连杆孔壁以便产生一定的接触,同时使磨头作旋转和往复运动。
珩磨石采用金刚石或立方氮化硼等耐磨材料。
连杆孔的精度在一定程度上取决于珩磨头的原始精度。
本工序选用卧式珩磨机,见图表1-1。
表1-1
项目
合成切削速度Vem/min
交叉角φ
圆周速度V:
m/min
往复速度Vfm/min
精加工
30
40︒
28
10
精加工余量为0.03mm,切削液选用70%煤油加25%锭子油。
1.6连杆加工工艺设计应考虑的问题
连杆本身的刚度比较低,在外力作用下易变形,合理的加工工序将直接影响连杆的最终加工质量,在这里主要考虑连杆加工工序安排、定位基准选择、夹具使用问题。
1.6.1工序安排
连杆的工序安排见表1-2
工艺过程卡片
产品
名称
柴油机
毛坯
种类
胎模锻
零
件
名称
连杆
重量
图号
A1
尺寸
材料
40MnB
序号
工序名称及内容
设备
定位基准
1
模锻、退火
2
喷丸处理
3
探伤检查
4
划线身中心线及大小端两端面加工线
划线平台
考虑加工面余量均匀分配及其与不加工面相对位置尺寸
5
粗铣大小端一端面及工艺凸台
立式铣床
划线找正
6
粗铣大小端另一端面
立式铣床
大端一端面及工艺凸台
7
划大小端孔中心线及大小端外形线
划线平台
兼顾大小端的余量及壁厚均匀
8
钻小端孔
Z3080
大端一端面及工艺凸台小端孔中心线
9
插分开面及大端孔
插床
大小端另一端面及划线找正
10
检验
11
调质处理
12
喷丸处理
13
探伤检查
14
涂油漆
15
半精铣大小端一端面及工艺凸台
立式铣床
大小端另一端面
16
半精铣大小端另一端面
立式铣床
大端一端面及工艺凸台
17
划小端孔及外形线