UHT灭菌乳二次污染的主要原因及解决办法.docx
《UHT灭菌乳二次污染的主要原因及解决办法.docx》由会员分享,可在线阅读,更多相关《UHT灭菌乳二次污染的主要原因及解决办法.docx(15页珍藏版)》请在冰豆网上搜索。
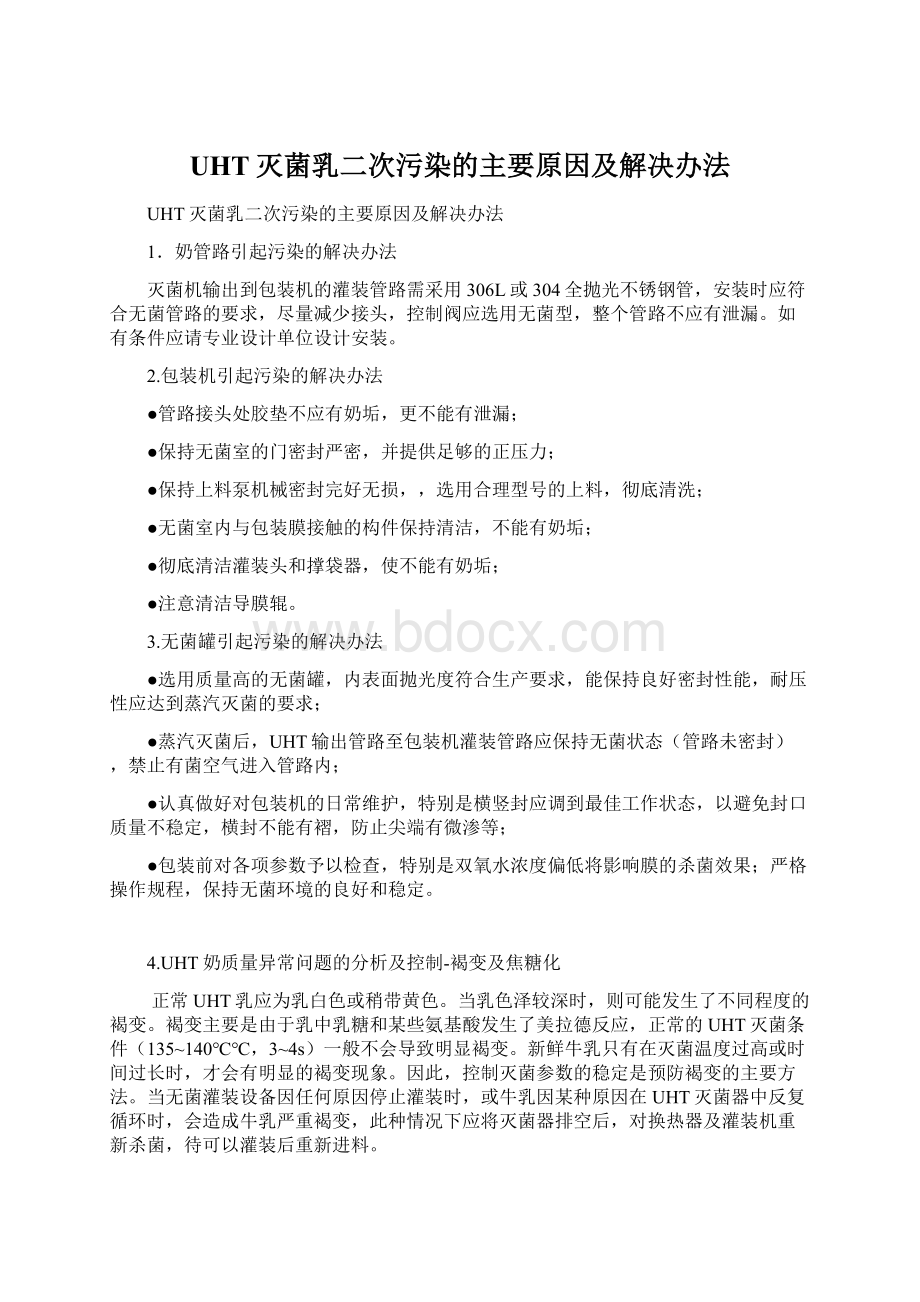
UHT灭菌乳二次污染的主要原因及解决办法
UHT灭菌乳二次污染的主要原因及解决办法
1.奶管路引起污染的解决办法
灭菌机输出到包装机的灌装管路需采用306L或304全抛光不锈钢管,安装时应符合无菌管路的要求,尽量减少接头,控制阀应选用无菌型,整个管路不应有泄漏。
如有条件应请专业设计单位设计安装。
2.包装机引起污染的解决办法
●管路接头处胶垫不应有奶垢,更不能有泄漏;
●保持无菌室的门密封严密,并提供足够的正压力;
●保持上料泵机械密封完好无损,,选用合理型号的上料,彻底清洗;
●无菌室内与包装膜接触的构件保持清洁,不能有奶垢;
●彻底清洁灌装头和撑袋器,使不能有奶垢;
●注意清洁导膜辊。
3.无菌罐引起污染的解决办法
●选用质量高的无菌罐,内表面抛光度符合生产要求,能保持良好密封性能,耐压性应达到蒸汽灭菌的要求;
●蒸汽灭菌后,UHT输出管路至包装机灌装管路应保持无菌状态(管路未密封),禁止有菌空气进入管路内;
●认真做好对包装机的日常维护,特别是横竖封应调到最佳工作状态,以避免封口质量不稳定,横封不能有褶,防止尖端有微渗等;
●包装前对各项参数予以检查,特别是双氧水浓度偏低将影响膜的杀菌效果;严格操作规程,保持无菌环境的良好和稳定。
4.UHT奶质量异常问题的分析及控制-褐变及焦糖化
正常UHT乳应为乳白色或稍带黄色。
当乳色泽较深时,则可能发生了不同程度的褐变。
褐变主要是由于乳中乳糖和某些氨基酸发生了美拉德反应,正常的UHT灭菌条件(135~140℃℃,3~4s)一般不会导致明显褐变。
新鲜牛乳只有在灭菌温度过高或时间过长时,才会有明显的褐变现象。
因此,控制灭菌参数的稳定是预防褐变的主要方法。
当无菌灌装设备因任何原因停止灌装时,或牛乳因某种原因在UHT灭菌器中反复循环时,会造成牛乳严重褐变,此种情况下应将灭菌器排空后,对换热器及灌装机重新杀菌,待可以灌装后重新进料。
控制生鲜牛乳的新鲜度在一定程度上也会提高牛乳的抗褐变能力。
原料乳质量不好或生产时间过长或是温度突然过高会使乳蛋白变性程度增大并产生糊管及焦糖化现象,因而会影响杀菌效与果。
另外,乳中加的稳定剂也会影响生产,如加热表面结焦;UHT温升过快,浪费生产实践;UHT管内壁的结焦还会影响清洗效果,造成恶性循环。
因此遇到UHT温升太快(平均1h超过1℃),或者清洗后刚开始使用就温升过快,就要第一分析配方组成,改变一下配方。
第二是跟踪清洗效果。
调整CIP清洗程序
5.UHT奶质量异常问题的分析及控制-原料乳酸度高、盐类不平衡
原料乳酸度过高、盐类不平衡则易形成软凝块和杀菌器内挂乳石等。
原料乳的好坏是影响乳制品质量的关键,只有优质原料乳才能保证优质的产品。
为了提高原料乳质量必须做到保证生产用水符合饮用水国家标准,保持牛舍环境的卫生,牛舍通风应良好。
建立自动化机械挤奶装置代替手工挤奶。
牛奶挤出后应冷却至4℃,或是向其通入二氧化碳,ClaraG等人通过实验证明CO2颗明显控制原料乳中微生物的生长。
建立CIP清洗系统。
对于收集到的奶必须通过75度酒精试验,对于不合格的原料乳应坚决予以拒收。
6.UHT奶质量异常问题的分析及控制-碱液残留问题
UHT生产过程中除了正常的CIP清洗外,还经常使用中间清洗(AIC)。
AIC是指生产过程中在保证完全无菌状态的情况下,对热交换器进行清洗,确保而后的灌装可在无菌的情况下正常进行的过程。
采用这种清洗是为了去除加热面上沉积的脂肪、蛋白质等垢层,降低系统内压力,对牛乳进行从份有效的杀菌,从而延长运转时间。
超高温乳生产加工中中间清洗(AIC),一般先使用水赶出乳,然后加入碱运行一段时间后,用水洗去残留的碱液,如果水洗时间不够就进料,会使乳中残留碱液,而是乳呈现碱味。
为了生产出优质的超高温乳,车间工作人员应该严格按照生产规范进行操作。
7.UHT奶质量异常问题的分析及控制-H2O2的残留
无菌包装机的灌注头一般使用H2O2杀菌,所以刚生产出的几袋奶是不能留用的,废弃的代数根据生产实践来定。
8.UHT奶质量异常问题的分析及控制-乳脂肪上浮
成品的脂肪上浮一般出现在生产后几天到几个月范围内,上浮的严重程度一般与储存及销售的温度有关,温度越高,上浮速度越快,严重时在包装的顶层可达几毫米厚。
原因分析:
1均质效果不好;2低温下均质;3过度机械处理;4前处理不当,混入过多空气;5原料乳中含过多脂肪酶,有研究表明,经140℃、5s的热处理,胞外脂肪酶残留量约为40%,残留的脂肪酶在储存期间分解脂肪球膜释放出自由脂肪酸而导致聚合、上浮;6饲料喂养不当导致脂肪与蛋白质比例不合适;7原料乳中含有过多自由脂肪酸。
控制措施:
1提高原料乳质量;2均质设备要在生产前进行检查;3人员要严格按照生产要求进行操作;4进行必要的质量人员监督。
9.UHT奶质量异常问题的分析及控制-乳风味的改变
除了微生物、酶及加工引起的风味的改变外,还有由于环境、包装膜等因素引起的乳风味的变化。
乳是一种非常容易吸味的物质。
如果包装容器隔味效果不好或其本身或环境有异味,乳一般呈现非正常的风味,如包装膜味、汽油味、菜味等,有效的措施就是采用隔味效果非常好的包装容器,并对储存环境进行良好的通风及定期的清理。
另外,UHT乳长时放在阳光下,会加速产生日晒味及脂肪氧化味,因此UHT乳不应该放在太阳直接照射的地方。
10.利乐包牛奶中出现的质量问题
利乐包出现的质量问题主要可分为两大类:
一类是由于微生物的原因引起的坏包,通常它对人体有害;另一类是由于理化的原因引起的牛奶内在状况发生了改变,通常它只会影响感官,一般不会对人体有害。
因此,对牛奶出现的质量问题要认真分析,查找原因,以利于解决问题。
(1)由微生物原因所造成的坏包
●平酸包:
症状为包型完整,打开包后牛奶喝时口味有酸味,组织状态有时会呈现出豆腐脑状,如清析出(分层现象),除此之外,有时还会出现臭味。
●胀包:
症状为包型鼓胀,打开包后牛奶喝时口味有酸味,组织状态会呈现出豆腐脑状,乳清析出(分层现象),除此之外,有时还会出现臭味。
苦包:
症状通常包型完整,打开包后牛奶喝时有苦味,有时还夹杂有酸味(通常为个例问题)。
(2)由理化原因所造成的质量问题
●脂肪上浮包:
打开包后,在牛奶叶面上漂浮有一些片状块状五(或油状物),在盒内壁上有白色或淡黄色的黏状物,严重时在包装内的顶层可达几毫米厚的脂肪层[1],喝时牛奶没有苦味或酸味,但有时有哈喇味。
●蛋白凝固包:
打开包后,在盒底部有些粒状块状物,喝时牛奶没有苦味或酸味。
苦包:
打开包后牛奶喝时有苦味,一般要生产加工一段时间(约2个月左右)后才会出现,并且此种状况的牛奶会随着贮藏时间延长而变得苦味加重(通常为批量问题)
理化指标偏低包(俗称“水包”):
打开包后牛奶喝时口味偏淡、颜色偏浅(通正常的产品比较),有水样的感觉。
●褐色包:
纯牛奶打开包后牛奶颜色发暗(有时呈红棕色),喝时有时有蒸煮味。
●沉淀包(特别是对乳饮料或高钙奶而言):
打开包后,盒的底部有较多的糊状的沉淀物,喝时牛奶没有苦味或酸味。
●分层包(特别是对酸性乳饮料而言):
打开包后出现明显的分层,上部颜色较底部颜色为淡。
11.微生物所造成的坏包的原因分析
牛奶被微生物污染后,会造成变质、变坏。
若污染的微生物在产品中会繁殖并产气,则产品外观鼓胀(即胀包);若污染的微生物在产品中会繁殖但不产气,则产品外观包型完整(即平酸包);若污染的微生物在产品中会分解蛋白质成一些发苦的肽类片断,则产品口味偏苦。
主要原因有:
(1)原料奶或辅料的影响。
若原料奶或辅料中含有较多的芽孢菌或耐热芽孢菌,则超高温灭菌后,相应的产品中芽孢菌或耐热芽孢菌也会残留的较多,从而使产品的坏包数增加。
(2)灭菌效率未达到要求。
灭菌效率取决于灭菌温度和灭菌时间的配合,也会受杀菌器(对间接加热而言)内表面(产品的一面)的结垢程度的影响。
●不同的产品,须采取不同的灭菌温度和灭菌时间,若灭菌效率未达到要求,则灭菌后的产品中残留的微生物(特别是芽孢菌或耐热芽孢菌)就较多,包装后的产品就会出现坏包。
●杀菌器内便面的结垢程度较后,则会影响热的传递,使产品的实际灭菌温度降低和灭菌时间缩短,从而影响灭菌效率
(3)灭菌后的输送管道、无菌罐清洗不到位。
超高温灭菌后的五菌产品的输送管道以及五菌罐要确保无菌,若清洗杀菌不到位,会引起产品被二次污染,从而使包装后的产品出现坏包。
(4)包材灭菌效果不佳。
包材的灭菌通常是由双氧水进行的,若双氧水浓度或温度达不到要求,就不能有效地杀死包材内表面的微生物,包装后的产品就会出现坏包。
(5)灌装机在生产时无菌环境被破坏。
●为了保证灌装时的无菌状态,则灌装前整个灌装机同产品有接触的表面都必须进行彻底的清洗和杀菌,若清洗杀菌不到位,则会使同不洁表面接触的产品含有较多的微生物,从而使包装后的产品出现许多坏包。
●在生产灌装时要通过热空气和蒸汽阀来保证灌装时的无菌状况,若热空气温度太低或蒸汽阀的保证作用未达要求,则易使产品出现坏包。
●产品在灌装时出现“爆管”现象(“爆管”是指灌注牛奶的纸管有泄漏点),即纸管成形灌注牛奶时,由于各种原因(如:
纸管被夹爪拉破、纸接头未达要求)造成缝合不好形成泄漏,则有可能会使微生物通过泄漏处进入纸管,破坏了纸管内的无菌环境,则易使产品出现坏包。
●对于封闭式无菌包装系统,若无菌室正压状态被破坏,则易使产品出现坏包。
(6)包型缝合不严:
若包型缝合不严,则易造成微生物的污染,出现坏包。
(7)运输、贮存不当:
利乐包产品为无菌包装,若运输、贮存不当,包被碰伤、挤压变形严重,就易使得包的无菌状况被破坏,出现坏包。
12.理化原因所造成的质量问题的原因分析
(1)脂肪上浮包产生的原因
●原料奶质量不佳:
含有由微生物(特别是嗜冷菌)产生的较多的脂肪酶,而这些脂肪酶较耐热,在超高温温度下,不能完全被钝化。
有研究表明,经140℃,5s的热处理,胞外脂肪酶的残留量约为40%。
残留的脂肪酶在产品贮存期间分解脂肪球膜,释放出自由脂肪酸,而导致脂肪易聚合上浮。
●原料奶贮存时间较长:
因原料奶需在低温下贮存,否则易造成原料奶的变质。
但在低温下贮存时间过长,则易造成嗜冷菌的繁殖,产生较多的脂肪酶,从而使加工完的牛奶易脂肪上浮(原因同上)。
●加工过程中牛奶均质效果不好:
若均质效果不好,牛奶中的脂肪球没有打碎到很小的粒度以及充分的分散,则加工后的牛奶中的这些脂肪球易重新聚集,形成大的脂肪球,从而加快脂肪上浮速度。
●加工后的牛奶存放时间过长或贮存温度较高:
牛奶加工后,由于牛奶的特性,都会存在着脂肪上浮,如果只是原料、加工控制的好,也仅能延缓脂肪聚集上浮速度而已,因此,加工后的牛奶随着存放时间的延长,则脂肪上浮的情况也会加重。
同时,在一定温度下,若贮存温度较高,也会造成脂肪分子的碰撞聚合的机会加快,从而使脂肪上浮速度加快
(2)蛋白质凝固包或苦包产生的主要原因
原料奶中由于微生物(特别是嗜冷菌)产生的蛋白分解酶较耐热,其耐热性远远高于耐热芽孢,曾有人计算过,一种蛋白分解酶的耐热性是嗜热脂肪芽孢杆菌耐热性的4000倍。
同样有研究表明,经140℃,5s的热处理,胞外蛋白酶的残留量约为29%。
残留的蛋白分解酶在加工后的贮存过程中分解蛋白质,根据蛋白分解程度的不同,可分为下列2种情况:
●凝块的出现:
凝块出现的快慢与产品中蛋白分解酶的残留量和销售条件有关,通常是牛奶先不稳定,有时看上去牛奶还没有出现凝块,但一加热就出现凝块,严重时在盒底部有明显的蛋白凝块,一般凝块出现在生产2个月以后。
●苦包的产生:
若蛋白分解酶分解蛋白质形成带有苦味的短肽链(苦味来源于由某些带苦味的氨基酸残基形成的),则产品就带有苦味,并且随着贮存时间的延长,苦味会加重。
(3)理化指标偏低包(俗称“水包”)产生的主要原因
●开始灌装时,以奶顶水,若控制不好,奶顶水时间太短,造成水没有顶干净就开始包装,使包装后的少量产品理化指标偏低。
●生产快结束时,以水顶奶,若控制不好,水顶奶时间太长,造成水混入奶中,使包装后的少量产品理化指标偏低。
(4)褐色包产生的主要原因
●灭菌温度较高或灭菌时间较长,则会加剧非酶褐变(即美拉的反应生成黑色素),从而使奶易褐变。
●无无菌罐的厂家,若超高温灭菌的奶回流量大,汇流次数多,则奶易褐变。
●有无菌罐的厂家,若超高温灭菌机调速,从高速调到低速至流量稳定的一段时间内,则会使奶的受热时间延长和加热温度升高,从而使这一段时间的奶褐变加剧(同正常加热的奶相比较)。
●若原料奶质量不佳或灭菌时间长,会使加热器内表面结垢,若垢层太厚掉落奶中,就会使这一段时间的奶褐变加剧,又是奶中还会有褐色块状物。
●若产品在高温下贮存时间较长,则会使奶褐变加剧,颜色较深。
(5)沉淀包(特别是乳饮料或高钙牛奶)产生的主要原因
●添加的稳定剂使用的品种或量不对,使产品的稳定性差,产品易沉淀。
●随着产品贮存时间的延长,产品中稳定剂的稳定效果会下降,则沉淀两会逐渐增加。
(6)分层包(特别是酸性乳饮料)产生的主要原因
●若加工工艺控制不当(如调酸过快活所加酸浓度较高),都会造成牛奶组织状态的不稳定,使产品易分层。
●添加的稳定剂使用的品种或量不对,使产品的稳定性差,产品易分层。
●酸性乳饮料灭菌的温度较高,造成产品的稳定性下降,产品易分层。
13.微生物原因产生的坏包应采取的措施
(1)严格控制原料奶的卫生质量,通常要求用于超高温的原料奶的细菌总数、嗜冷菌数、芽孢总数、耐热芽孢总数分别控制在小于105、103、102、10mL-1。
(2)不同的产品采取不同的灭菌温度,以确保既能充分杀灭各种微生物(特别是芽孢和耐热芽孢),又能尽量减少营养物质的损失和稳定性的破坏。
●对于酸性乳饮料,由于在酸性条件下,有可能生长的主要是一些不耐热的微生物(如酵母和霉菌)。
因此,杀菌的温度不需要过高,一般采用灭菌温度为115~120℃;时间为4s。
●当用含芽孢或耐热芽孢数较多的辅料(如可可粉、咖啡粉、奶粉等)生产花色奶或中性乳饮料时,应相应地提高灭菌温度,以尽量杀灭这些芽孢(如生产巧克力奶)。
一般采用为:
灭菌温度139~142℃;4s。
●当用含有芽孢或耐热芽孢的原料奶生产春牛奶或中性乳饮料时,一般采用灭菌温度为137~139℃;时间4s。
(3)管道、容器(特别是超高温灭菌后的管道、无菌罐)要进行认真的清洗、消毒。
●通常采用CIP碱或酸清洗(碱常用NaOH,酸常用HNO3),要注意控制好清洗时碱或酸的质量浓度、清洗时间、温度以及清洗时的流量和流速:
I.碱的质量分数为1.5%~2%;酸的质量分数为0.8%~1.2%。
II. 清洗时间>=20min;
III.碱液温度控制在80~85℃;酸液温度控制在60~65℃。
IV. 流速为>=20t/h。
●清洗干净后,生产前从UHT的灭菌段开始直至灌装机之前的管道用137℃左右的热水进行消毒;无菌罐用蒸气(大约140℃)进行消毒,消毒时间都控制在30min以上。
(4)利乐包材的灭菌通常是采用双氧水进行,因此应严格控制好双氧水的品质、浓度、温度、双氧水在包材上停留时间(或包材走过双氧水槽的时间)。
●采用经过改良的性能稳定的食品级双氧水。
●双氧水质量分数控制在30%~50%.具体要求为:
开机之前、每生产4h左右、停机前都必须测定质量浓度,一旦质量浓度偏低,应停机,之前的产品要特别管制。
●双氧水温度控制在70~80℃。
●包材走过双氧水槽的时间控制在6~7s。
●生产中每隔120h或每星期都要更换1次系统内的双氧水
(5)灌装机在灌装时保持无菌环境
●在灌装前,罐装机要进行彻底的清洗,通常清洗采用酸、碱,具体要求同3.1中的(3)。
然后用无菌热空气(280℃以上对可能灌装时同牛奶杰出的几内管道表面、无菌空气管路、无菌室、灌装机的充填管、AP阀等进行灭菌。
●灌装时,灌装机内同牛奶接触的地方,要用热空气(约125℃)保持无菌[2],又无菌室的要保持正压状态(通常压力要求大于666.6Pa,一般为2666.4~3999.66Pa);同时进出灌装机和无菌罐的连接处要用蒸气障保护,以免被外界微生物污染。
●若出现“爆管”现象,则灌装机应停机,进行清洗后再开机,同时“爆管”前后时间段的产品要特别管制。
(6)保持利乐包的封合状态
为了确保利乐包的完整封合,防止外界的污染,要特别注意横、纵封的封合,通常相隔一段时间,就必须进行检查(如:
纵封的注射试验、横封的剥皮试验);要控制好封合时的加热功率和压力(同包材的品种、厚度有关);纵、横条要光滑、平整。
(7)在手工接包材、接3P条时,手要清洗干净,并用酒精消毒。
(8)在搬运、运输、销售过程中,要防止包被碰伤、挤压变形,从而使宝内部损坏,造成微生物污染,产生坏包。
13.理化原因所产生的质量问题应采取的措施
(1)对脂肪上浮报应采取的措施
●加强对原料奶的控制。
搞好原料奶的卫生,减少微生物的污染,细菌总数应小于105mL-1;加快原料奶的生产,最好在挤奶后24h内加工完毕;原料奶进贮藏罐时,最好进行预巴氏杀菌,,以杀灭会产生耐热酶的嗜冷菌。
预巴氏杀菌温度为65~70℃;时间为4s左右。
●严格控制好均质压力、温度和均质头平整等状态:
均质温度为70~75℃;均质压力为采用二级均质(第一级均质压力为18~20MPa;第二级均质压力为5MPa);均质头要保持平整,否则会影响脂肪球的破碎效果;均质前最好先脱气。
●前处理时,严格控制搅拌速度和时间,减少奶中混入空气的量。
●生产的产品要避免高温贮藏,尽快销售。
(2)对蛋白凝固包和苦包应采取的措施同
(1)中的○1和○4
(3)对理化指标偏低报(俗称“水包”)应采取的措施
●严格按规定做好奶顶水、水顶奶的操作,防止产生理化指标偏低包;
●在开机进入生产线的首包、生产结束时的最后一包以及UHT断料顶水时间段的产品进行检测,发现理化指标偏低包,则要对有关产品进行管制,并重点进行检查,以挑出理化指标偏低包。
(4)对褐色包应采取的措施
●根据不同的产品特点,严格控制好灭菌温度和灭菌时间;
●不要在高温条件下贮藏;
●生产中若无无菌罐时,严格控制好回流量,一般控制在3%~5%;
●生产中若有无菌罐时,在生产时要减少UHT的流量变化,如从生产能力大调整到生产能力小时,则会使这一段时间奶受热强度比其它段强(因为受热温度增高,受热时间变长),从而使颜色加深;
●UHT加工的时间长短,同原料奶的品质有关(原因为原料奶品质好,则奶加热时稳定性就好,加热器的内表面就不易结垢,内外温度变化小),一般内外温差变化要求小于10℃,否则要停机清洗;
●对于UHT连续灭菌而言,即使原料奶品质好,内外温差变化小于10℃,UHT连续生产也最好不要超过12h,以免加热器的内表面上的奶垢掉到奶中,使奶中有褐色块。
(5)对沉淀包(特别是对乳饮料或高钙牛奶而言)应采取的措施
●改进所用稳定剂的品种或添加量,以减缓沉淀速度;
●由于乳饮料(或高钙乃)加有较多的辅料(有些是不易溶解的物质,如钙粉等),从而造成了产品的不稳定,即使加有稳定剂,也只是延缓沉淀的速度。
因此产品要在低温下贮藏,并尽快销售,以减少沉淀量;
●对于乳饮料而言,采用适当的方法(石英砂过滤、渗透膜过滤等)改进所用水的质量。
使用硬度小(一般德国度不超过4度)和电导率低的水(一般电导率<50us/cm)。
(6)对分层包(特别是对酸性乳饮料而言)应采取的措施
●对于酸性乳饮料,若灭菌温度太高,会影响其中的稳定剂的稳定性,造成牛奶分层,因此灭菌温度不能太高,时间不能太长,一般采用115~120℃,4s左右;
●改进所用稳定剂的品种或添加量,以确保稳定效果;
●严格按工艺规程操作(如调酸浓度和调酸速度要严格控制)以确保产品不分层。
14.搅拌型酸奶常见的质量问题及控制措施-胀包
酸奶在贮存及销售过程中,特别是在常温下销售及贮存很容易出现胀包,酸奶由于产气菌主要是酵母菌与其它产气杂菌作用而产生气体,使酸奶变质的同时也使酸奶的包装气胀。
原因分析
污染酸奶而使酸奶产气的产气菌主要是酵母菌和大肠杆菌,其污染途径主要在以下几方面:
(1)、菌种被产气菌污染(主要是酵母菌污染);
(2)、生产过程中酸奶被酵母菌和大肠杆菌污染;
(3)、酸奶包装材料被酵母菌和大肠杆菌污染。
(4)、包材本身不合格使外界微生物侵入而造成的污染。
(5)杀菌不彻底有产气菌未杀死的污染。
(6)、生产工艺中杀菌机杀菌参数设定不正确而残留产气菌的污染。
(7)在灌装时破坏无菌环境使外界微生物侵入而造成的污染。
控制措施
(1)、继代菌种在传代过程中要严格控制环境卫生,确保无菌操作,可用一次性直接干粉菌种来解决继代菌种存在的一些避病;
(2)、严格控制生产过程中可能存在的污染点和一些清洗不到的死角。
如设备杀菌、发酵罐、酸奶缓冲罐、进出料管、灌装设备、配料设备等一定要清洗彻底,以后再进行杀菌,杀菌温度一般为90℃以上(设备出口温度)并且保证20—40分钟,杀菌效果的验证可采取涂抹试验来检验杀菌效果,生产环境用空降来检测空气中酵母菌是否超标,若超标可采取二氧化氯喷雾,乳酸薰蒸、空气过滤等措施来解决空气污染,采取空气降落法来检验空气中酵母、霉菌数,一般生产环境空气中酵母、霉菌数为≤50个/平板,另外严格控制人体卫生,进车间前一定要严格消毒,生产过程中经常对工作服、鞋及人手进行涂抹试验,确保人体卫生合格,加强车间环境、设备等方面的消毒、杀菌工作,确保大肠杆菌无论是在工序还是成品中的检验都是未检出的状态;
(3)、包材在使用前涂抹方法检测微生物的数量,在生产时可用紫外线杀菌或双氧水灭菌等方法来控制,并且要严格控制好包材贮存的环境质量;
(4)、也可采取在酸奶中添加一定量的抑制酶(抑制酵母和霉菌)来解决此问题;
(5)、杀菌要彻底,酸奶中不能有颗粒物质存在,若有会影响杀菌的彻底性。
(6)、杀菌机参数设定要达到在保质期内不发生任何变质,酸奶属于高酸性产品,杀菌温度一般不用太高。
(7)、严格按无菌操作要求规程操作。
15.搅拌型酸奶常见的质量问题及控制措施-产品发霉
酸奶在销售、贮运过程中有霉菌生长,长出霉斑,从而使酸奶发生变质。
原因分析
(1)、菌种污染霉菌、接种过程中有霉菌污染;
(2)、生产过程中有霉菌污染;
(3)、包材被霉菌污染。
控制措施
(1)、如果使用传代菌种,菌种在传代过程中要严格控制污染,确保无菌操作,保证免受霉菌污染。
(2)、生产环境要严格进行消毒、杀菌,确保生产地理环境中霉菌数合格,一般生产环境空气中酵母、霉菌数为≤50/平板;
(3)、包材在进厂之前一定要严格检验,确保合格,存放于无菌环境中,使用时有紫外线杀菌,
(4)、可采取加入抑制酶(抑制酶和霉菌)来解决。
搅拌型酸奶常见的质量问题及控制措施-乳清析出
酸奶在生产、销售、,贮存时有时出现乳清析出的现象,酸奶的国家标准规定酸奶允许有少量的乳清析出,但大量的乳清析出是属于不合格产品。
原因分析
(1)、乳中干物质、蛋白质含量过低;
(2)、脂肪含量低;
(3)、均质效果不好;
(4)、接种温度过高;
(5)、发酵过程中凝胶组织遭受破坏;
(6)、乳中氧气含量过多;
(7)、菌种产黏度低;(8)、灌装温度过低;
(9)、酸奶在冷却、灌装过程中充入了气体;
(10)、酸奶配方中没加稳定剂或用量过少。
控制措施
(1)、调整配方中各组成成分的比例,增加乳中干物质、蛋白质的含量;
(2)、增加乳中的脂肪含量;
(3)、均质温度设定在65-70℃,均质压力为15-20MPa之间,经常检验奶的均质效果,定期检查均质机部件,如有损坏及时更换;
(4)、将接种