体系稽核管理规定.docx
《体系稽核管理规定.docx》由会员分享,可在线阅读,更多相关《体系稽核管理规定.docx(25页珍藏版)》请在冰豆网上搜索。
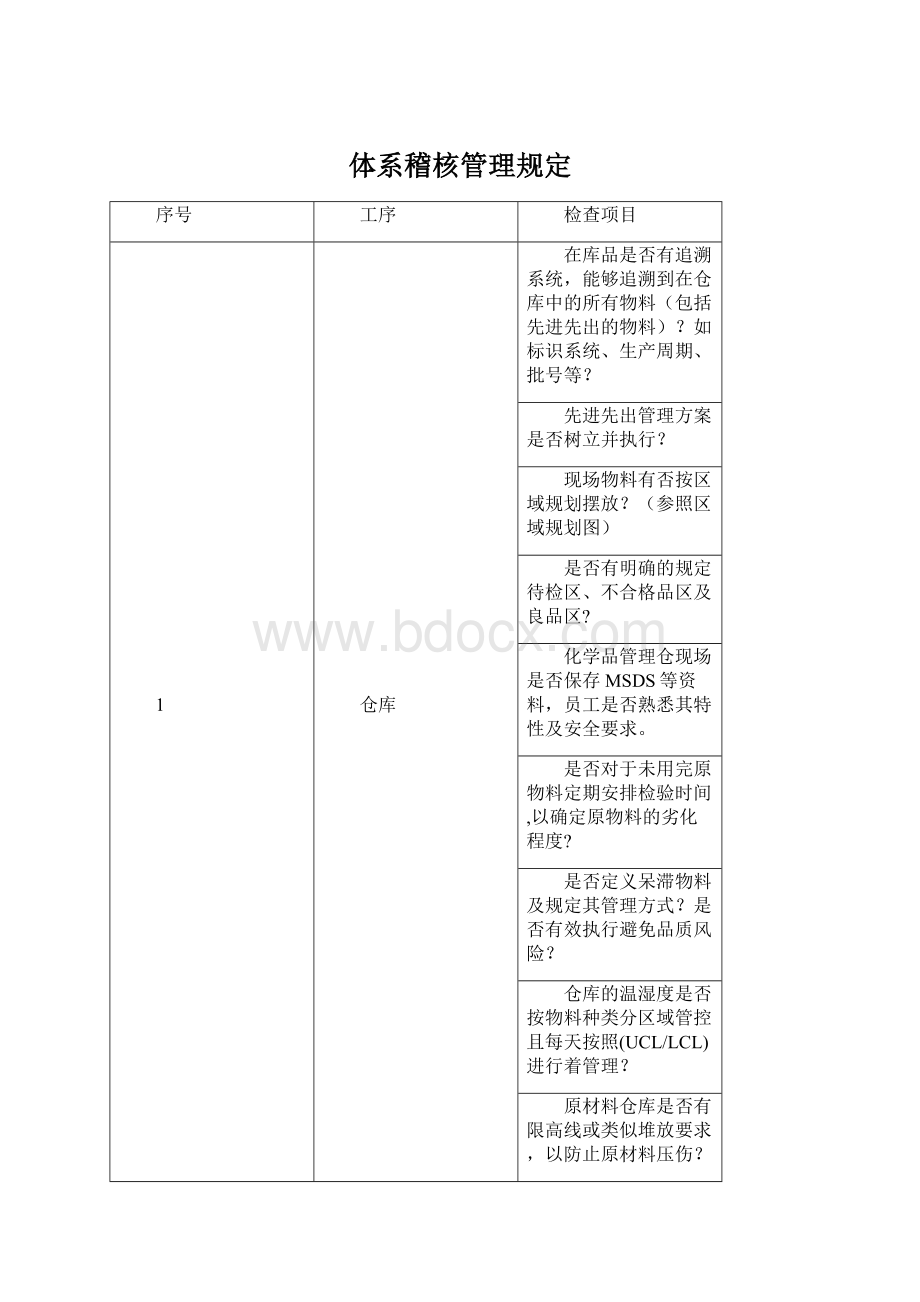
体系稽核管理规定
序号
工序
检查项目
1
仓库
在库品是否有追溯系统,能够追溯到在仓库中的所有物料(包括先进先出的物料)?
如标识系统、生产周期、批号等?
先进先出管理方案是否树立并执行?
现场物料有否按区域规划摆放?
(参照区域规划图)
是否有明确的规定待检区、不合格品区及良品区?
化学品管理仓现场是否保存MSDS等资料,员工是否熟悉其特性及安全要求。
是否对于未用完原物料定期安排检验时间,以确定原物料的劣化程度?
是否定义呆滞物料及规定其管理方式?
是否有效执行避免品质风险?
仓库的温湿度是否按物料种类分区域管控且每天按照(UCL/LCL)进行着管理?
原材料仓库是否有限高线或类似堆放要求,以防止原材料压伤?
是否有进行安全库存管理?
储存环境是否有避免日光直接照射?
化学品是否有专人负责?
是否有经过化学品危害性和消防培训?
化学品存放区域是否有特定标识做区分?
化学品使用添加区域是否有安全防护设备(如眼罩、橡胶手套等)?
仓库是否有消防设备和防爆设备(消防水栓,灭火器,消防沙箱,防爆门等)?
并定期保养?
叉车是否有定期点检或保养?
仓库是否有定期盘点?
2
IQC
检验人员保持上岗前资格认证培训记录?
是否持证上岗
对于考核不合格检查员是否进行相关培训等以使其能达到要求,并保留文件记录?
检验仪器是否具备?
各仪器是否定期校正?
待检/合格/不合格/开发用材料是否区分进行管理?
–是否有各原材料进料检验规范的标准文件、承认书、标准样板、限度板等?
并执行?
是否具备并遵守抽样检验标准?
(G-1,2,3/严格检查/AQL/首件3批次全部检查)
是否按SIP、作业指导书等要求作业,保持检验记录且正确?
样本保存是否适当(温湿度和环境)?
检验报告是否有效的进行管理
油墨入料检验是否有粘性测试?
网版入料检验是否有张力测试?
刮刀入料检验是否有硬度检验?
各物料是否有定期可靠性检测与监控?
不合格批是否均适当标示(品名,不良状况,不良项目)且并可追溯?
是否有对环境温湿度做日常监控记录?
是否有不合格批次处理流程?
–不合格品是否有做异常处理,是否有及时开立异常单通知厂商并记录SCAR;供应商回复的SCAR是否有做确认、追踪及保存?
检验工作建立品质履历管理?
(重大品质异常、后工序投诉、客诉、ECN、RoHS异常等)
是否按《内部RoHS送测计划》要求作业,并保持记录?
有害物质检测报告是否定期更新及管理?
是否保持MSDS,并有效管理?
物料的变更是否有效的进行管理
检验/检测设备是否按时进行校验,标示是否清晰
3
开料
关键岗位人员有定义且持证上岗?
人员熟练掌握本制程产品特性和要求(所有工站)
现场适当位置是否保持并悬挂SOP\POP、标准工艺参数、CTQ、等作业文件?
作业人员严格按SOP、标准参数、CTQ等要求作业?
(有自检/互检要求)
开料段,Scribing划线速度、压力(Air&ServerMotor)、下刀深度基准是否进行管理?
刀轮品名(尺寸、角度外)是否在作业指导书上体现,工作人员确认后记录于工作报表进行管理?
是否有刀轮的寿命标准,且累计记录管理?
工作台真空压力的规格是否设定、并记录管理(设置及实测检查)
机台设备有操作保养指导书?
机台设备有点检表,并按时点检?
是否具有工作台清扫方法的标准,洁净度是否良好?
4
CNC
在产线是否放置作业机种的作业指导书,作业相关事项是否记录管理?
是否有切削液的管理标准(比重,交替周期等)?
砂轮棒的磨损状态是否有定期检查确认以及记录交替历史?
产品插放前,是否使用可清除设备内和安插部位异物的气枪,清洁度是否良好?
插放部位的真空压力是否有设定规格标准,是否进行(设置和实际测试检查)的记录管理?
刀轮交换周期是否有设定和有刀轮交换履历,累计寿命距离是否可以确认?
刀轮转数在作业指导书中是否有明确说明,作业者确认后是否记录在报表管理?
检验人员严格按照SIP作业,保持首、中,末巡检&抽检记录,且准确?
是否有进行全尺寸测量?
是否有标识重点尺寸,标识是否合理,关键过尺寸是否在统计管制之下?
(如管制图、Cp/Cpk等)
是否有对产品崩边等不良率的管控并定义异常管控反馈、改善机制?
CNC风险批次是否能够进行有效隔离并提供处理方式?
现场合格&不合格、已产&待产物料等区域划分、标识是否清晰?
是否按区域摆放?
预防混入?
测量设备有无进行MSA分析计划?
并依计划实施,有检验报告?
5
一次清洗
是否都有具备各型号类别的作业指导书,并按照进行作业?
是否遵循清洁干燥条件,清洗后是否有痕迹和水汽遗留?
清洗剂是否依更换周期更换?
各槽的温度:
规格标准设定与否,记录管理(设置与实际测试检查)
超音波的强度:
规格标准设定与否,记录管理(设置与实际测试检查)
洗洁液稀释浓度:
规格标准设定与否,记录管理(设置与实际测试检查)
净水交替周期:
规格标准设定与否,记录管理(设置与实际测试检查)
热风干燥条件:
温度,时间规格标准设定与否,记录管理(设置与实际测试检查)
6
平磨
现场适当位置是否保持并悬挂SOP\POP、标准工艺参数(平磨的标准(转速/时间要求))、CTQ、等作业文件?
是否有各机种的返修SOP及记录?
是否区分钢化前平磨与钢化后平磨?
机台设备有操作保养指导书?
机台设备有点检表,并按时点检?
现场合格&不合格、已产&待产物料等区域划分、标识是否清晰?
是否按区域摆放?
预防混入?
磨粉的配置与更换是否有书面的管理要求
是否有对平磨使用的治具进行管理及更换周期?
平磨前后的厚度有无管控?
机械特性有无管控?
返工产品是否保持重检记录?
(加严一级)
7
白片检验
现场适当位置是否保持并悬挂作业标准、检验标准,标准文件?
检验是是否持证上岗?
是否定期测试其岗位能力?
是否对检验台进行点检管理并按时点检?
现场合格&不合格、待检、待返等产品区域划分、标识是否清晰?
是否按区域摆放?
预防混入?
是否建立限度样板清单并有效管理?
是否对检验用光源进行灯光照度监测校准?
现场定置定位,5S是否良好?
所有产品检验记录是否有效保管并可追溯?
8
强化
各机种作业指导书是否在产线上张贴,作业相关的各种事项是否都有记录(4PB、CS、DOL、CT值)?
使用的强化液的型号是否与作业指导书中记录的一致?
强化液是否定期更换,且是否按照标准更换(补充)强化液并记录
强化液是否设定na+离子的浓度,是否进行(设定及实测检查)记录管理?
强化工程后,是否用各机种的治具确认强化深度?
强化炉温度与强化时间是否有进行DOE验证区分管控并落实执行?
是否根据每各钢化炉位置的不同制定强度及平坦度检查标准,并记录实验结果进行管理
是否具有强化工程条件的DOE资料
强化温度、时间等参数是否设定CTQ和记录管理?
(预热、强化、冷却三阶段)
强化深度、表面应力、落球试验、延伸率设备是否遵循规格设定,量产时周期性试验及记录管理
重新强化产品有无各机种的SOP?
返工品加工完成后是否有层别和标识?
返强化后是否有对产品尺寸进行100%检验
检验人员严格按照SIP作业,保持首、中,末巡检&抽检记录,且准确?
(应力、落球、三点弯曲测试)
检验发现异常,有开出相应《质量异常单》,并跟进处理、效果验证,保持结案记录?
硝酸钾使用寿命是否进行管控,监测方法是什么,是否有添加更换记录?
钢化炉的温度是否进行点检,是否有检测标准,点检频率是多少,是否有记录?
客户的性能标准现场是否可快速清晰的获得?
是否按照客户标准进行判定,是否有测试记录,每批钢化产品是否可准确追溯其测试结果?
返工产品是否保持重检记录?
(加严一级)
9
二次清洗
是否具备各机种作业指导书,而且按照标准书进行工作?
清洗剂是否依更换周期更换?
是否遵守清洗干燥的条件,清洗后不留有水渍及污渍
-各槽温度:
规格设定与否、记录管理(设置及实测检查)
-超声波强度:
规格设定与否、记录管理(设置及实测检查)
-清洗剂稀释浓度:
规格设定与否、记录管理(设置及实测检查)
-净水更换周期:
规格设定与否、记录管理(设置及实测检查)
-热风干燥条件:
规格设定与否、记录管理(设置及实测检查)
清洗后产品是否有进行外观抽检与确认?
清洗台架等治具是否有定期确认可用性与洁净度?
10
网版管理
网版管理是否有相应作业指导书?
网板尺寸、厚度、张力、外观是否有依据规范检验并记录?
当网板量测异常时,是否立即采取有效改善措施或流程?
网版若回收是否有相关作业流程?
网版若回收是否有回收网版管理规范?
网板是否有报废流程并有记录可查?
网版印刷的菲林是否保留,并检查?
版次有无记录?
根据网版印刷的次数,以及根据外观不良(磨损和破裂)的交换周期是否明确登记在作业指导书上?
网版感光胶的涂布标准是否有规定?
网版烘干条件是否按照标准来进行?
(温度+时间)
网版是否有区域化的不同保管室,不造成损坏并且使其在管理上查找容易?
网版的使用次数是否有记录管理?
是否设定网版清洗周期并按周期清洗?
11
油墨管理
油墨调配是否由专人负责?
油墨调配是否有明确SOP?
油墨搅拌时间是否有明确规定与操作记录?
开罐油墨与未开罐油墨是否分别进行管理?
开罐油墨、未开罐油墨保存期、报废期有无明显标识并执行?
已开罐油墨针对油墨粒子数、油墨粘度是否由建立先关文件并进行定时监控?
油墨的调色或调和时是否有运用各颜色类别的限度样本?
油墨更替周期是否在作业指导书上详细登记,作业者确认后是否有记录登记管理?
为了油墨粘度管理,是否在作业指导书上明确登记固化剂、稀释剂混合比例,作业者确认后记录在日记上登记管理?
回收油墨是否有进行相关管理与区分?
12
印刷及烘干
关键岗位人员保持上岗前资格认证培训记录?
且持证上岗?
机台设备有操作保养指导书?
机台设备有点检表,并按时点检?
现场适当位置是否保持并悬挂SOP、POP、标准工艺参数、CTQ等作业文件?
作业人员严格按照SOP、标准参数、CTQ等要求作业?
(有自检/互检要求)
配备有各型号类别的印刷作业指导书,并且根据指导书进行作业?
为了管理静电,是否在周边机器都设置了接地设备?
网版的油墨投放量是否按照使用量进行投放?
刮刀角度,压力,速度、硬度的相应标准是否有进行DOE验证并详细登记在作业指导书上,作业者确认后记录在作业报表上管理?
是否订定印刷油墨的回收程序?
印刷区域洁净度是否定义洁净度要求并定期监控?
烘烤时间、烘烤温度是否有DOE验证并明确规定在文件中?
产品烘干是否按照设定的烘干标准来进行?
(制定确认清单)
烤箱升温曲线是否有明确SOP规范?
烤箱升温曲线是否有定期进行点检并记录
现场合格&不合格、已产&待产物料等区域划分、标识是否清晰?
是否按区域摆放?
预防混入?
丝印后产品尺寸是否有进行首检与过程抽检(印刷颜色、字体尺寸位置度)?
IR孔有无进行100%量测?
每道印刷厚度、总厚度有无管控?
检测量具&检具是否有效管理、点检、记录?
检验人员严格按照SIP作业,保持首、中,末巡检&抽检记录,且准确?
(外观、油墨导电性测试、IR透过率、油墨厚度、百格、硬度、表面能、酒精测试)?
检验发现异常,有开出相应《质量异常单》,并跟进处理、效果验证,保持结案记录?
丝印区域自检处灯光要求、检验方式是否符合客户要求?
13
真空镀膜
在产线是否都配备各型号的作业指导书,并且相关作业事项都有记录?
Sio2和AF覆膜液的产品名称是否详细记录在作业指导书上,是否作业者在确定后使用并在作业报表上进行记录管理?
Sio2和AF覆膜的厚度标准是否详细记录在作业指导书上,是否作业者在确定后使用并在作业报表上进行记录管理?
去除保护胶带后,是否用除电枪喷射去除表面的灰尘或静电?
是否有管理除电枪的操作状态和气压?
真空度作业条件是否有在CTQ工程里有指定,并且明确记录在作业指导书中,是否在开始作业之后并记录管理作业条件和变更情况。
电镀原材料的使用量和使用周期是否有进行管理?
电镀重要作业条件(power,燃气量,作业时间,转数,装载数量)是否有通过SPC来做趋势管理?
是否有电极管理方案(使用次数记录管理和交换增加)
Sio2和AF电镀时间是否有按每发设定标准,并且遵守?
AF电镀机的作业者是否理解作业条件并且是主要负责人负责?
AF电镀是否区分为电熔电镀机在产线操作
AF电镀前,是否对仓体进行清洁并对清洁度进行管理记录?
(清洁周期,冷冻机核对周期,油泵检查等)
检测量具&检具是否有效管理、点检、记录?
AF工程
检验人员严格按照SIP作业,保持首、中,末巡检&抽检记录,且准确?
(水滴角、耐磨测试、盐雾实验、水煮测试等)?
检验发现异常,有开出相应《质量异常单》,并跟进处理、效果验证,保持结案记录?
14
贴合
产线各站位是否有正确的SOP,员工操作是否按SOP执行
车间及贴膜机内是否定期测量空气洁净度,测量记录,空气洁净度不达标时是否有相应处理机制
贴膜首件是否有测量膜片拉拔力
贴膜是否按CTQ参数执行
除泡参数是否按CTQ参数执行
膜片来料贴膜前是否有100%检验
检验光源照度是否达到SOP要求,是否有定期进行测量
检验人员检出能力是否有定期考核,GRR测试记录
检验后不良品是否有进行单独区分放置
15
外观检测
-是否有各机种检验指导书与检验基准?
是否有检验员培训记录及GRR考核记录依据并持证上岗?
检验标准是否符合客户要求,是否有背面丝印颜色、方式、位置等的检验?
规格等变更后是否有相关培训或注意事项宣导?
作业工位洁净度是否达标?
是否有定期进行洁净度测量并改善?
检验人员的手法是否规范并是否一致?
手指套更换频率是否有进行DOE验证并明确定义在文件中且落实执行?
是否对检查环境(照度、温湿度)有规定?
检查工作台是否有离子风机?
检查环境是否与骏达保持一致?
外观检验是否有不良样本或图示?
是否进行良品、不良品及待复判品的区分摆放?
检验人员漏检率、误判率是否有定义标准?
检验人员漏检率、误判率是否有做统计与管控?
是否定期对漏检超标人员、进行培训?
漏检率超标人员是否培训合格后再上岗?
是否有进行样本管理,检验时是否有进行样品比对?
是否针对前五大不良进行改善?
外观检验不良率是否有明确定义停线标准并进行异常反馈与改善追踪?
OQC抽检频率是否满足客户要求?
OQC判退率是否有持续管控并持续改善?
是否有针对客诉不良明确宣导、培训与粘贴标示?
是否有文件推行IR透过率97%全检及实施记录?
16
包装
–包装是否各机种有规格书指导作业?
是否对包装环境(照度、温湿度)有规定?
包装区域未进行包装产品是否有相应放置落尘的保护措施?
改善品、变更品是否区分,并在外箱明显位置标识“××改善品、变更品”?
包装区域洁净度是否有环境洁净度是否达到1000级并管控?
相似物料是否有建立相关区分文件及标识于检验及包装台面?
-是否采取有效的预防措施以防混料及短装异常发生?
外包装标识是否符合客户要求?
外箱标示是否有产品的料号、生产日期、封箱人员信息等。
尾数箱包装是否有特殊标记
针对短装、多装、混料是否有实施管制。
托盘设计及包装设计时是否进行跌落和振动试验?
17
出货检查
确认是否有建立检验规范?
明确出货检验项目?
是否有出货管制计划(包括抽样计划)?
抽样计划是否考虑现存产品质量水平和目标?
对汽车产品是否执行C=0抽检方案
是否对照封样检查?
是否对主要的不良进行统计地监控?
是否推动改善行动来减少不良?
变更品发货前是否提前通知CQE,并由CQE通知骏达SQE?
检验不良率达到停线标准时是否立即发出改善通知单給厂內相关单位人員,要求即时提出改善对策
退货不良品是否做不良标示?
退货不良品是否有进行不良解析与持续改善?
-承认书、标准书与成绩书的检查项目是否一致?
-是否区分管理待检,合格,不合格区域?
是否有客诉异常履历清单记录管理?
18
样品管理
是否建立样品管理台帐?
样品阶段是否组织召开FMEA会议,并有记录?
FMEA会议是否推动相关的改善活动?
样品阶段是否有品质人员参与?
样品出货前是否由品质人员全检?
样品制作是否建立Checklist?
样品结果是否输出报告并留样?
样品报告是否提供给骏达?
是否跟踪此样品在骏达的生产情况?
是否跟踪此样品在骏达的客户生产情况?
19
可靠性测试
是否有制定可靠性测试管理文件?
(实验周期、实验方法、判定标准)
功能测试项目与测试频率是否符合客户要求?
测试设备与测试方法是否符合客户要求?
是否有保存可靠性测试记录及实验样品?
测试人员是否经过培训并考核合格后上岗作业
可靠性测试设备是否齐全?
是否满足骏达产品实验要求?
使用的测试设备有无定期校验?
有无校验标识?
测试NG时是否有相关异常处理机制、不良品处理机制?
测试NG是否有进行失效分析与改善?
20
重工
对于可返修产品是否有返修计划书?
返修后产品是否有经过重新测试或检查后方可出货?
返修后产品是否有做标记以便后续跟踪?
作业区是否有对环境温湿度做日常监控记录?
返修动线是否有规划(避免与正常品混料)?
返修后的产品是否与未返修的产品有区分开来?
返工治具(研磨机)与使用溶液(研磨液)是否有定期维修并规范化管理?
不通过区域研磨是否有不同参数定义?
IR孔返工品是否有进行透过率与外观确认?
21
仪器设备
是否有设备预防保养计划?
各工序使用机台是否有保养维修记录(维修日志)?
现场模具及治具是否有被管制(料号及版别)?
设备是否有定期校准?
使用治具及量測一起是否有列表控管?
22
共同管理
不良品是否被分析,分类及提出改善对策?
是否制定对于制程不良进行趋势管理并订立目标,并进行对前三项工程不良的改善活动?
是否确认清洁度管理状态,是否有管理标准(位置,粒子大小,粒子数量,测试周期)并进行越势管理?
-是否执行外观检验员的实名制度和等级制度?
.实名制:
制定检验员的固定编号。
标记追踪免得流出不良!
.等级制:
通过测试制定等级(A级检验员,B级检验员,C级检验员等等)
是否保持管理检验员的检出力评价标准?
→评价对象,评价周期,评价试料,评价方法,评价数量,评价时间,等级管理
→检验员培训履历,检查基准书,新员工及调岗位员工培训结果,检查员流失率管理,检查环境点检履历等
-是否保持管理变更点?
→变更点过程,培训履历,申请单,检讨结果,变更产品标识、变更产品检验记录标识,客户承认回复等
全制程3定5S是否管理?
是否符合?
备注:
本文件属于TB-CT-MC-DC-002《体系稽核管理规定》附件
(2)文件。
编制:
胡志辉2018.3.9审核:
朱立军2018.3.9批准:
刘让豪2018.3.9