课程设计说明书鼓形轴套注射模设计.docx
《课程设计说明书鼓形轴套注射模设计.docx》由会员分享,可在线阅读,更多相关《课程设计说明书鼓形轴套注射模设计.docx(18页珍藏版)》请在冰豆网上搜索。
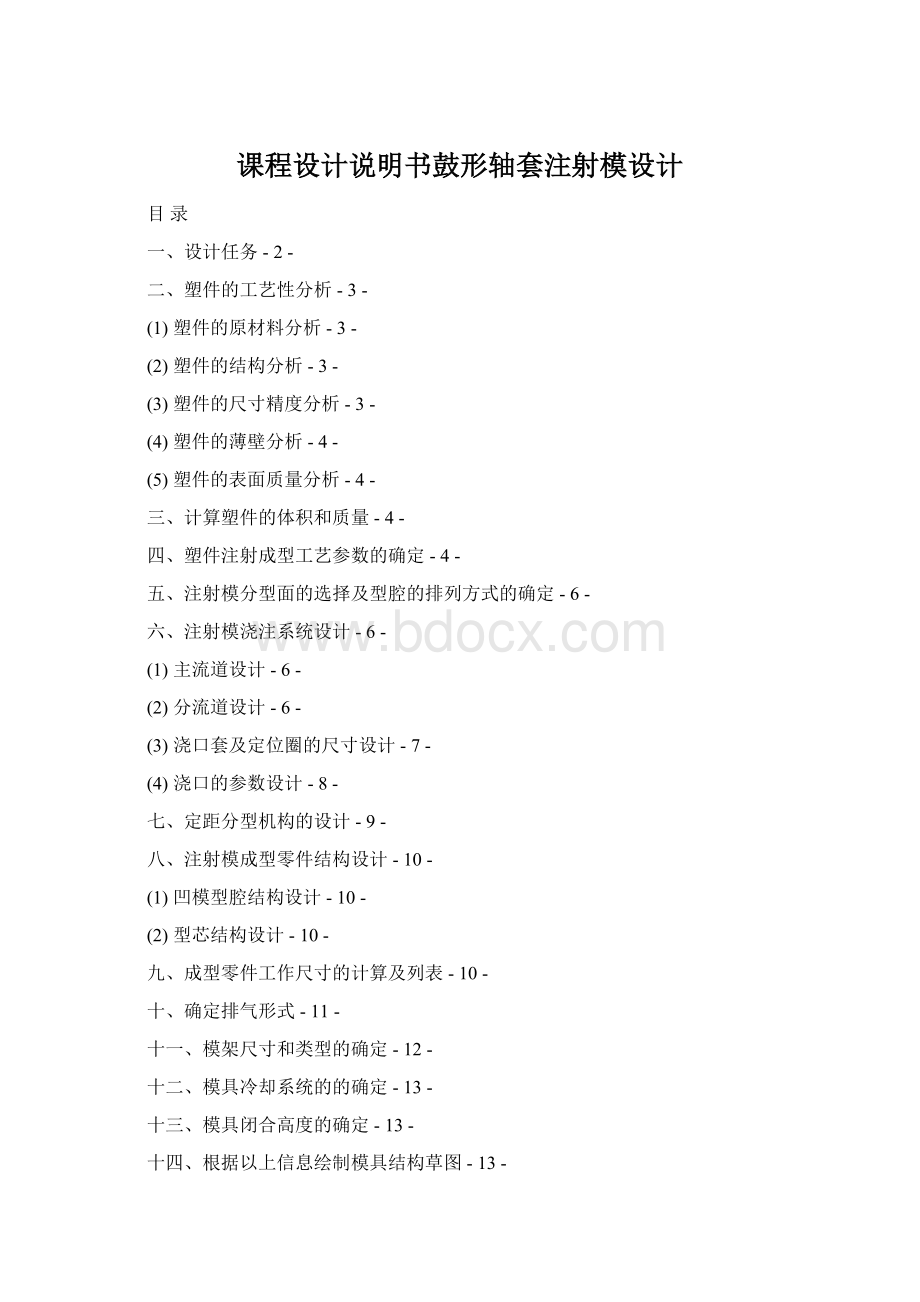
课程设计说明书鼓形轴套注射模设计
目录
一、设计任务-2-
二、塑件的工艺性分析-3-
(1)塑件的原材料分析-3-
(2)塑件的结构分析-3-
(3)塑件的尺寸精度分析-3-
(4)塑件的薄壁分析-4-
(5)塑件的表面质量分析-4-
三、计算塑件的体积和质量-4-
四、塑件注射成型工艺参数的确定-4-
五、注射模分型面的选择及型腔的排列方式的确定-6-
六、注射模浇注系统设计-6-
(1)主流道设计-6-
(2)分流道设计-6-
(3)浇口套及定位圈的尺寸设计-7-
(4)浇口的参数设计-8-
七、定距分型机构的设计-9-
八、注射模成型零件结构设计-10-
(1)凹模型腔结构设计-10-
(2)型芯结构设计-10-
九、成型零件工作尺寸的计算及列表-10-
十、确定排气形式-11-
十一、模架尺寸和类型的确定-12-
十二、模具冷却系统的的确定-13-
十三、模具闭合高度的确定-13-
十四、根据以上信息绘制模具结构草图-13-
十五、校核注射机的有关参数-14-
(1)锁模力校核-15-
(2)注射量校核-15-
(3)合模机构尺寸的校核-15-
十六、绘制出模具的总装配图和非标准零件工作图-17-
十七、注射模具设计小结-17-
一、设计任务
要求:
按下图要求设计一副注射模具
名称:
鼓形轴套材料:
聚甲醛(黑色)
技术要求:
未注尺寸公差按一般精度等级选用
注:
采用一模一件,三个点浇口
二、塑件的工艺性分析
(1)塑件的原材料分析
塑件材料采用工程材料黑色聚甲醛(POM),属于热塑性材料。
从使用性能上看,该塑料强度、刚度高,抗冲击,耐疲劳,蠕动性能较好,减磨耐磨性好;从成型性能上看,该塑料的流动性较好,成型容易,但收缩率大。
此外,该塑件容易产生表面缺陷、如毛班、折皱、熔接痕、凹痕等弊病,从而,必须严格控制成型条件,可适当提高模温,宜用高温高压注射,塑件可在较高温度脱模,还应缓慢冷却,可将塑件90℃左右的热水中或整形夹具冷却,以防止出现收缩变形,应力不匀等现象。
加工前,应对材料进行干燥和预热处理,对改善塑件表面光泽有较好效果。
(2)塑件的结构分析
从零件图上分析知,该零件由直径不等的圆柱或圆筒组成,总高37mm,最大直径为Ø76mm,最小直径为Ø8mm,且为了提高零件的表面质量,还在零件表面设有三个互成120°直径为Ø8mm深度为1mm的沉孔,以设置点浇口。
因此该模具应采用双分型面注射模。
为了容易在第一次分型时将浇口拉断,同时缩短分流道的长度,则应将直径为Ø76mm的塑件型腔设置在动模部分。
(3)塑件的尺寸精度分析
因技术要求中无特殊要求,则未注尺寸公差按一般精度等级选用。
查表得出如下结果
(4)塑件的薄壁分析
从零件图上可得出,最大壁厚为6mm,最小壁厚为4mm,壁厚差为2mm。
材料流动性好,采用高压注射有利于塑件的成型。
(5)塑件的表面质量分析
因技术要求中没有特殊说明,从而没有特殊的表面质量要求,故比较容易实现。
三、计算塑件的体积和质量
据图计算塑件的体积为
V=π×382×5+π×42×11+π×102×12-(
)×12×2-π×42×(17+11)+π×(302-262)×20mm3≈41cm3
查表得塑件的密度为ρ=1.41g/cm3,从而塑件的质量为
m=ρ·V=41×1.41g≈58g
根据题目要求,采用一模一件的的模具,且为点浇口,考虑到其外形尺寸、注射时所需的压力和浇注系统的凝料等情况,初步选用HTF90型注射机。
四、塑件注射成型工艺参数的确定
查附录H,工程塑料聚甲醛(共聚POM)的注射成型工艺参数可作如下选择:
注射机类型:
螺杆式
螺杆转速:
(20~40)r/min
料筒温度:
前段170~190℃,中段170~190℃,后段170~180℃
喷嘴形式:
直通式
喷嘴温度:
170~180℃
模具温度:
90~100℃
注射压力:
80~120MPa
保压压力:
30~50MPa
注射时间:
2~5s
保压时间:
20~90s
冷却时间:
20~60s
成型周期:
50~160s
上述工艺参数可在试模时作适当调整,详细信息见注射成型工艺卡。
塑料零件注射成型工艺卡片
产品型号
零件图号
第页
产品名称
电流线圈架
零件名称
电流线圈架
共页
材料名称
聚甲醛(黑)
材料牌号
材料颜色
黑色
每台件数
1
零件净重
58g
零件毛重
61g
消耗定额
设备
HTF90
注射成型工艺
料筒温度
第一段
170~190℃
注射时间
闭模
模具
编号
第二段
180~200℃
注射
2~5s
型腔数量
3
第三段
170~190℃
保压
20~90s
推出高
第四段
~℃
冷却
20~60s
总高
262mm
喷嘴
170~180℃
总时间
50~160s
附件
压力
注射
80~120MPa
模温
90~100℃
嵌件
图号
名称
数量
保压
30~50MPa
螺杆类型
螺杆式
螺杆转速
加料刻度
脱模剂
原料干燥处理
使用设备
电热干燥箱
零件成型后处理
工序号
工序内容
工艺装备
工时
描图
盛料高度
准终
单件
翻料时间
热处理
塑料烘干
描校
干燥温度
100℃
加热温度
注射成型
干燥时间
4h
加热时间
检验
底图
保温时间
包装
冷却方式
装订号
编制
审核
会签
标记
处数
更改号
签字
日期
标记
处数
更改号
签字
日期
五、注射模分型面的选择及型腔的排列方式的确定
因模具的浇口设为点浇口,则说明模具必须为双分型面,第一分型面用于取出凝料,第二分型面用于取出塑件。
因该模具为一模一件,故无需讨论其型腔的排列方式。
六、注射模浇注系统设计
(1)主流道设计
查附录G的HTF90型注射机喷嘴的有关尺寸为:
喷嘴孔径d1=3mm;
喷嘴前端圆弧半径r=10mm。
从而可得出主流道球面半径R=r+(1~2)mm;
浇口套小端直径D1=d1+(0.5~1)mm;
曲主流道球面半径R=11mm,浇口套小端直径D1=4mm。
为了在第一次分型能顺利进行,即将凝料从浇口套中拔出,则将主流道设置为锥形,锥度为2°~6°。
经计算可得出
主流道大端直径D2=6mm;
为了便于熔体顺利进入分流道,在主流道出料端设计半径为R1=2mm的圆弧过渡;
(2)分流道设计
工程塑料聚甲醛属于流动性较好的塑料,可采用热量损失和压力损失均不大的梯形截面分流道,其相关截面尺寸可以根据下面的经验公式确定
b=
h=
b
式中b为梯形大底边宽度(mm);
m为塑件的质量(g);
L为分流道的长度(mm);
h为梯形的高度(mm)。
梯形的侧面斜角常取5°~10°,此处取8°。
经计算b=
≈0.2654×7.6×2.1
≈4.2mm
h=
×4.2=2.8mm
(3)浇口套及定位圈的尺寸设计
因该模具为小型模具浇口套球面深度为h1=(3~5)mm,取h1=4mm;
选取常用定位圈,规格为φ35×φ100×15
浇口套凸台高度h2=(8~10)mm,取h2=10mm;
浇口套外径d2=(18~45)mm,取d2=20mm。
浇口套及定位圈相关尺寸见下图所示:
(4)浇口的参数设计
根据本题设计要求,点浇口直径d3=(0.5~1.5)mm,取d3=1.2mm;
点浇口长度L1=(1.0~2.5)mm,L2=(0.5~1.5)mm,取L1=2mm;
此处二级分流道锥度α=6°~35°,浇口末端锥度β=60°~120°;
冷料穴长度一般为1~1.5倍流道直径,即(1~1.5)b,取6mm。
浇口的相关尺寸见下图所示:
七、定距分型机构的设计
根据需要,该塑件可采用双分型面注射模典型结构中的“摆钩分型螺钉定距式双分型面注射模”,即利用摆钩和定距螺钉的配合,完成模具的两次分型,以便分别取下塑件和浇注系统的凝料。
该机构的示意图如下所示:
(见下一页)
其中挡块的斜度为1°~3°,可取为2°;
摆钩与挡块的接触长度为5~6mm左右,可取为5mm;
摆钩在压块的作用下使其绕转轴转动旋转一定角度而完成模具的第二次分型,其具体结构尺寸得根据模板厚度做进一步计算。
八、注射模成型零件结构设计
(1)凹模型腔结构设计
模具采用一模一件的结构形式,且塑件的形状不是很复杂,中间板上型腔采用整体式结构,动模板上型腔设在了主型芯内部,其结构形式见草图所示所示。
(2)型芯结构设计
由图形可以看出,该塑件设有一个主型芯两种次型芯(其中有三个形同的型芯固定在中间板上,为浇口设计三个沉孔;另外一个型芯套在主型芯中间用于制作塑件中心的通孔,固定于动模板上),其结构形式见草图所示。
九、成型零件工作尺寸的计算及列表
成型零件工作尺寸采用平均法计算。
查附录B得出工程塑料聚甲醛的收缩率Smin=1.5%,Smax=3.0%,从而其平均收缩率
=
=(1.5+3.0)/2×100%=2.25%
由技术要求知
计算型腔和型芯的径向尺寸时,不考虑模具成型零件的制造误差δZ和模具成型零件的磨损量δC;
计算型腔的深度和型芯的高度尺寸时,同样不考虑模具成型零件的制造误差δZ和模具成型零件的磨损量δC;
计算中心距尺寸时,由于中心距的公差都是双向等值公差,同时磨损的结果不会使中心距尺寸发生变化,在计算时不必考虑磨损量。
根据以上信息可列出下表(其中标注偏差时δZ取1/2Δ计算),见第二页所示
成型零件工作尺寸计算列表
类别
塑件尺寸
计算公式
型腔(芯)尺寸
型腔的计算
φ
φ
φ
φ
φ
φ
型芯计算尺寸
φ
φ
φ
φ
孔距尺寸
φ
φ
十、确定排气形式
因零件的拐角过多,故将动模板拆分为两块板,一块设置型腔,一块用于固定型芯,具体内容见草图所示。
十一、模架尺寸和类型的确定
根据塑件结构需要,理论上该模具采用推杆推出机构,动模部分有两块板,包含支承板,定模部分有两块板,故选用A2型标准模架。
因塑件结构不复杂,型腔采用整体式结构,而中间板中的型腔为圆形,最大基本尺寸为φ76mm,则查表得型腔壁厚至少为40mm,则可以初步得出中间板的边界尺寸为76+40+40=156mm,再考虑到定距螺钉和导柱导套的设置,则初选模架为160mm×160mm的A2型标准模架,并多设置一块座板(用以支撑导柱),两块模板(一块用于固定主型芯,一块用于支撑中间板部分型芯)。
对壁厚进行校核,画出下图。
由图易知导套孔与型腔孔间距为53.23mm,满足壁厚至少为(1/2~1/3)×40mm的要求。
复位杆与型腔的距离为,也满足壁厚至少为(1/2~1/3)×40mm的要求。
因此,该模架满足壁厚要求。
十二、模具冷却系统的的确定
因模具的冷却系统的设计较为复杂,且考虑到本模具的摸温(90℃~100℃)较高,故本模具不特意去设置冷却系统。
十三、模具闭合高度的确定
根据所选用的标准模架规格,查表知定模座板厚度h1=20mm,支撑板厚度h3=32mm动模座板厚度h4=20mm,推杆固定板厚度h5=12.5mm,推板厚度h6=16mm。
查壁厚,确定中间板厚度。
根据直径为Ø20mm,查得整体式型腔最小壁厚为20mm,又为了避免中间板中塑件在成型过程中产生飞边,应将小型芯伸出(3~5)mm,而小型芯直径为Ø8mm,对壁厚影响较小,从而可以确定中间板厚度调整为20+(17-5)+(3~5)mm,取35mm。
确定定模部分型芯支撑板厚度,因该模板起支承型芯的作用同时也是为了防止熔体渗入型芯与模板的间隙,其厚度要求不是很高,可取为10mm。
确定动模板的厚度。
根据直径为Ø76mm,查得整体式型腔最小壁厚为40mm,但考虑到排气的需要,可将动模板分成两块板,一块板用于制造型腔,深度为5+20=25mm,一块用于固定主型芯,厚度可选为20mm。
确定垫板的厚度。
根据经验公式垫板厚度C=h5+h6+型腔深度+(3~5)mm求得。
其中型腔深度即塑件高度37mm,则C=12.5+16+37+(3~5)mm=65.5+(3~5)mm,取C=70mm。
模具的闭合高度计算
H=2×20+10+35+25+20+32+70+20+(15-5)mm=262mm
其中(15-5)mm表示定位圈厚15mm,沉入定模座板5mm。
所以本模具的外形尺寸为160mm×160mm×262mm。
十四、根据以上信息绘制模具结构草图
见下一页所示。
十五、校核注射机的有关参数
本题初选HTF90型注射机,查附录G,其主要技术参数如下
最大注射容量为121cm3;
注射压力为249MPa;
锁模力为900KN;
拉杆内距为360mm×360mm;
最大模具厚度为380mm;
最小模具厚度为150mm;
模板开模行程为320mm;
喷嘴圆弧半径为SR10mm;
喷嘴孔直径为3mm;
中心顶杆直径为φ80mm,周围分布有4个φ28mm的顶杆。
根据上述所选注射机进行参数校核。
(1)锁模力校核
依据公式FP≥npA+pA1进行校核。
(其中n=1)
通常熔体对型腔的压力取注射机压力的80%。
根据工艺卡中的注射压力知:
p=100×80%MPa=80MPa。
计算塑件在分型面上的投影面积为A=π×(76/2)2mm2≈4534mm2;
计算凝料在分型面上的投影面积为A1≈(6+19)×4.2×3mm2=315mm2;
则有npA+pA1=(4534+315)×10-6×80×106N=387920N≈388KN
显然,锁模力FP=900KN≥388KN,说明注射剂锁模力足够,可以达到锁模的要求。
(2)注射量校核
由以上计算知塑件的体积为41cm3,浇注系统的凝料的体积约为V1=
×π×
×(3×46+32.2)+3×2.8×4.2×(19+6)≈2485mm3=2.5cm3,因此,浇注系统凝料和塑件的体积为2.5+41cm3≈43.5cm3。
(可得出零件毛重约为43.5×1.41g≈61g)
注射剂的最大注射量是121cm3,校核得121×80%cm3=96.8cm3≥43.5cm3,说明该注射机可以满足注射成型的要求。
(3)合模机构尺寸的校核
①模具厚度的校核
注射剂允许安装的模具最大厚度为380mm,允许安装的模具最大厚度为150mm。
而模具的实际闭合厚度为262mm,故模具的厚度满足要求。
②开模行程校核
因为该模具为双分型注射模,所以有两段行程,且必须满足注射机的最大开模行程S≥S1+S2+(5~10)mm
a.第一次分型的行程计算
第一次分型的行程S1主要受浇注系统凝料高度的影响,即约为40-5+10+35+1mm=81mm,取S1=90mm计算。
(可据此设计限位螺钉的长度)
b.第二次分型的行程计算
第二次分型的行程S2主要受塑件高度、型腔深度和推出机构的推出距离的影响,即20+17+43+20mm=100mm。
(其中43mm是根据所选标准模架而得来的)
综上可得S1+S2+(5~10)mm=182+(5~10)mm≤S
③推出机构的校核
本模具的推出机构主要主要靠推杆作用,而为了让推出过程更加平稳,同时不让塑件发生变形,故设置了六根φ6mm的推杆均匀分布在小型芯的四周。
依据公式F总=Ap(μcosα-sinα)计算。
其中,材料为聚甲醛时设置的脱模斜度α=1°;
塑料对钢的摩擦因数μ=0.1~0.3,取μ=0.2计算;
选择膜外冷却塑件,p=24~39MPa,取p=30MPa计算;
A为塑件包络型芯的面积。
A=π×8×(20+17)+π×52×20+π×16×11+π×(82-42)+π×(262-82)
≈6820mm2=6.82×10-3m2
那么F总=Ap(μcosα-sinα)
=6.82×10-3×30×106×(0.2×cos1°-sin1°)
≈36.8KN
从而每根推杆所需的推出力为36.8/6≈6.1KN。
而在选材时,推杆的材料为4Cr5MoSiV1,经热处理后,硬度为50~55HRC,其余要求合符GB/T4170-2006的规定,查相关手册知,显然该推杆合符要求。
十六、绘制出模具的总装配图和非标准零件工作图
见附图所示
十七、注射模具设计小结
塑料模课程设计总结
时间飞逝,短短一周半的塑料模课程设计就要结束了,自己设计的摆钩分型螺钉定距式双分型面注射模也算是草草收工了。
本次课程设计是基于为期五周的单元教学而设置的,其目的就是为了检验我们对塑模相关知识掌握程度的同时让我们也体会一下模具设计的基本成型工艺过程。
相比于单元教学之前的模具的拆装与测绘,这次的课程设计算是得到了一次质的飞跃,把之前拆装与测绘所不懂的知识全部弄清了,把平时在课堂上所学的知识很好地运用到实践中去了,真正意义上的体会到了“做中学,学中做”的理念。
根据课程设计的要求,我们要在一周半的时间里完成老师布置的任务,包括一份课程设计说明书、一张总装配图及应有的零件图,对于刚学设计的人来说,时间确实很紧,要想把设计中所遇到的所有不解的地方搞清楚就很困难。
主要体现在排气系统、冷却与加热系统、推出机构的设计。
虽说在模具拐角过多且较深的型腔部位最好设置排气槽,但对于具体的塑件所对应的型芯或型腔,对排气槽的设置就会让我们感觉很困难。
对于冷却系统的设计与相关的计算我们之前在学习课本的过程中接触的较少,而加热系统往往与冷却系统联系紧密,这对于我们来说设计起来就会很棘手。
而对于推出机构的设计,其变换就更加难以捉摸,首先,推出机构的选取得依据塑件的成型要求和外观而设定;其次,推出机构的设计往往就决定了标准模架的选取,并且还会遇到自己所设计的塑件形状怪异,仅靠一种推出机构无法达到设计要求或是在满足不影响塑件外观的条件下的这种推出机构又不适合塑件或模具的外形尺寸。
还有一些例如技术要求的填写,分流道的设计与本次课程设计没涉及到的侧向分型机构的设计都没有很好地掌握。
总之,经过这次的课程设计让我们感受到了一副塑料模具的设计确实不简单,正所谓冰山一角,我们最多也只算是菜鸟,要学的东西还很多,还有很多知识需要进一步学习,还需要在实践中去积累去摸索。