金属切削原理与刀具.docx
《金属切削原理与刀具.docx》由会员分享,可在线阅读,更多相关《金属切削原理与刀具.docx(49页珍藏版)》请在冰豆网上搜索。
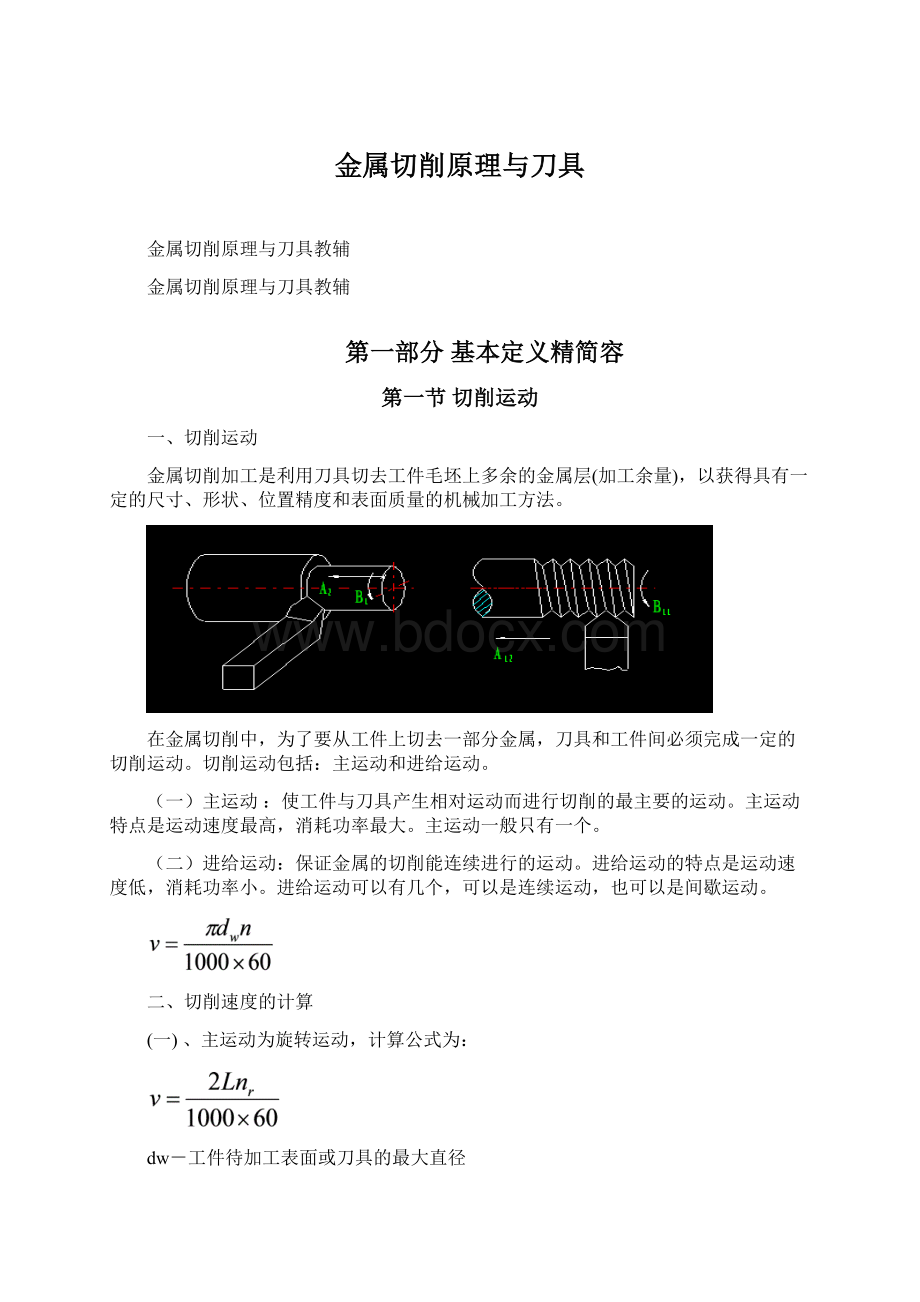
金属切削原理与刀具
金属切削原理与刀具教辅
金属切削原理与刀具教辅
第一部分基本定义精简容
第一节切削运动
一、切削运动
金属切削加工是利用刀具切去工件毛坯上多余的金属层(加工余量),以获得具有一定的尺寸、形状、位置精度和表面质量的机械加工方法。
在金属切削中,为了要从工件上切去一部分金属,刀具和工件间必须完成一定的切削运动。
切削运动包括:
主运动和进给运动。
(一)主运动:
使工件与刀具产生相对运动而进行切削的最主要的运动。
主运动特点是运动速度最高,消耗功率最大。
主运动一般只有一个。
(二)进给运动:
保证金属的切削能连续进行的运动。
进给运动的特点是运动速度低,消耗功率小。
进给运动可以有几个,可以是连续运动,也可以是间歇运动。
二、切削速度的计算
(一)、主运动为旋转运动,计算公式为:
dw-工件待加工表面或刀具的最大直径
n-工件或刀具每分钟转数
(二)、主运动为往复直线运动,计算公式为:
L-往复直线运动的行程长度
nr-主运动每分钟的往复次数
三.工件上的表面
在切削加工过程中工件上有三个不断变化着的表面。
⑴待加工表面工件上有待切除的表面。
⑵已加工表面工件上经刀具切削后产生的新表面。
⑶过渡表面切削刃正在切削的表面。
该表面的位置始终在待加工表面与已加工表面之间不断变化。
四.切削用量
切削速度、进给量、背吃刀量
(1)切削速度VC
(2)进给量fVf=f·n(mm/s)
f—车刀每转进给量(mm/r)
n—工件转速(r/s)
五.主运动和进给运动的合成
和成切削运动:
是由主运动和进给运动合成的运动。
刀具切削刃上选定点相对工件的瞬时合成运动方向称合成切削运动方向,其速度称合成切削速度.
第二节刀具切削部分组成要素
一.车刀由刀柄和刀头组成,切削部分包括以下几个部分:
(一)前 面Ar(face) :
前面是刀具上切屑流过的表面。
(二)主后面Aa(flank) :
刀上同前面相交形成主切削刃的后面,即与工件上过渡表面相对的表面。
(三)副后面Aa:
与已加工表面相对的表面,刀具上同前面相交形成副刃的后面
二.刀具组成
•切削刃:
刀具上两个面相交形成切削刃
•主切削刃S:
前刀面与主后刀面相交形成的切削刃,它担任主切削工作。
•副切削刃Sˊ:
前刀面和副后刀面相交形成的切削刃。
•刀尖:
刀尖是指主切削刃与副切削刃的交点。
三.刀具结构
其它各类刀具,如刨刀、钻头、铣刀等,都可看作是车刀的演变和组合。
第三节刀具角度
一.刀具角度
(一)刀具的切削角度,是刀具和工件在切削运动的状态下确定的角度。
所以刀具的切削角度的坐标应该用合成切削速度向量Ve来说明。
(二)由于实际生产多数加工表面都是空间曲面,不便于直接用来做为坐标平面,因此需通过切削刃上某一选定点,做工件加工表面的切削平面和法平面。
(三)刀具静止参考系(标注参考系):
不考虑进给运动,并在特定的安装条件下的参考系。
(四)刀具工作参考系(动态参考系):
是确定刀具在切削运动中有效工作角度的基准。
考虑了进给运动及安装情况的影响。
二、刀具切削角度的坐标平面
三、刀具标注角度的坐标
为了便于刀具设计者在设计刀具时的标注,有一些理想状态的假定:
1)装刀时,刀尖恰在工件的中心线上;
2)刀杆中心线垂直工件轴线;
3)没有进给运动;
4)工件已加工表面的形状是圆柱表面。
(外圆刀具标注角度)
第四讲切削层要素
一、切削层
工件上正被切削刃切削的一层金属,亦即相邻两个加工表面之间的一层金属。
二、切削层参数
切削层参数共有三个,它们通常都在垂直于切削速度v的平面度量。
(一)切削宽度:
沿主切削刃方向度量的切削层尺寸。
车削外圆时切削宽度:
(二)切削厚度:
两相邻加工表面间的垂直距离。
车外圆时,切削厚度:
(三)切削深度:
在基面上垂直于进给运动方向测量的切削层尺寸。
车削加工时的切削深度:
dw,dm分别为待加工表面和已加工表面的直径。
(四)切削面积:
切削层垂直与切削速度截面的面积。
车外圆时:
三.自由切削和非自由切削,残留面积及其高度
(一).自由切削是指只有一个直线切削刃的切削。
(二).非自由切削是指切削刃为折线形,即有主切削刃和副切削刃;或曲线形的切削。
由于切削运动和刀具的几何形状的关系,使加工后仍有一部分金属未被切除,而残留在已加工表面上,构成已加工表面的横向不平度(粗糙度),既所谓残留面积。
(三).当刀尖没有圆弧半径残留面积有直线构成其高为:
实际上r必不可少,当f较小,残留面积纯粹由两段圆弧构成,即不含有副切削刃的直线部分时残留面积高度为:
小项可略去不记,上式简化为:
第二部分刀具材料精简容
第一节刀具材料应具备的性能
一.刀具材料应具备的性能
刀具材料的切削性能直接影响着生产效率、工件的加工精度、已加工表面质量和加工成本等,所以正确选择刀具材料是设计和选用刀具的重要容之一。
金属切削时,刀具切削部分直接和工件及切屑相接触,承受着很大的切削压力和冲击,并受到工件及切屑的剧烈摩擦,产生很高的切削温度。
即刀具切削部分是在高温、高压及剧烈摩擦的恶劣条件下工作的。
因此,刀具切削部分材料应具备以下基本性能:
(1)硬度高
刀具材料的硬度必须高于被加工材料的硬度。
一般要求刀具材料的常温硬度必须HRC62以上。
(2)足够的强度和韧性
刀具切削部分的材料在切削时承受着很大的切削力和冲击力,因此刀具材
料必须要有足够的强度和韧性。
(3)耐磨性和耐热性好
刀具在切削时承受着剧烈的摩擦,因此刀具材料应具有较强的耐磨性。
刀
具材料的耐磨性和耐热性有着密切的关系,其耐热性通常用它在高温下保持较高硬度的能力来衡量(热硬性)。
耐热性越好,允许的切削速度越高。
(4)导热性好
刀具的材料热导率大,表示导热性好,切削时产生的热量就容易传散出去,
从而降低切削部分的温度,减轻刀具磨损。
(5)具有良好的工艺性和经济性
既要求刀具材料本身的可切削性能、耐磨性能、热处理性能、焊接性能等要好,且又要资源丰富,价格低廉。
二.常用刀具材料
刀具材料可分为工具钢、高速钢、硬质合金、陶瓷和超硬材料等五大类。
常用刀具材料的主要性能及用途见表:
第二节高速钢
一.高速钢
高速钢是一种含钨(WW)、钼(MMOO)、铬(Cr)、钒(VV)
等合金元素较多的高合金工具钢。
由于合金元素与碳原子的结合力很强,使钢在550~600℃时仍能保持高硬度,从而使切削速度比碳素工具钢和合金工具钢成倍提高,故得名“高速钢”,又名“风钢”或“锋钢”。
高速钢刀具制造工艺简单,容易磨出锋利的刃口,广泛用于制造切削速度较高、形状复杂的刀具,如钻头、丝锥、成形刀具、拉刀及齿轮刀具等。
高速钢按化学成分可分为钨系、钼系(含MO2%以上);按切削性能可分为普通高速钢和高性能高速钢。
①普通高速钢
普通高速钢指用来加工一般工程材料的高速钢,常用的牌号有:
a)W18Cr4V(简称W18)属钨系高速钢,具有较好的切削性能,是我国最常用的一种高速钢。
b)W6Mo5Cr4V2(简称M2)属钼系高速钢,碳化物分布均匀性、韧性和高温塑性均超过W18Cr4V,但其磨削性能较差,我国目前主要用于热轧刀具,如麻花钻等。
c)W9Mo3Cr4V(简称W9)是一种含钨量较多,含钼量较少的钨钼系高速钢。
其碳化物不均匀性介于W18和M2之间,但抗弯强度和冲击韧度高于M2。
具有较好的硬度和韧性,其热塑性也很好,可用于制造各种刀具(如锯条、钻头、拉刀、铣刀、齿轮刀具等)。
②高性能高速钢
高性能高速钢是在普通高速钢的基础上,用调整其基本化学成分和添加一些其它合金元素(如钒、钴、铅、硅、铌等)的办法,着重提高其耐热性和耐磨性而衍生出来的。
它主要用来加工不锈钢、耐热钢、高温合金和超高强度钢等难加工材料。
主要有以下几种:
a)钴高速钢钴高速钢是在高速钢中加入钴,常用牌号是W2Mo9Cr4Co8(简称M42),具有良好的综合性能,允许的切削速度较高,有一定的韧性,可磨削性好,可用于切削高温合金、不锈钢等难加工材料。
b)铝高速钢是我国独创的钢种,加入了少量的铝不但提高了钢的耐热性和耐磨性,而且还能防止含碳量高引起的强度、韧性下降。
但由于含钒量较多,其磨削加工性较差,过热敏感性强,氧化脱碳倾向较大,使用时要严格掌握热处理工艺。
常用牌号有W6Mo5Cr4V2Al(简称501)和W10Mo4Cr4V3Al(简称5F6)
第三节硬质合金
硬质合金是用高硬度、高熔点的金属碳化物(WC、TiC、NbC、TaC等)作硬质相,用钴、钼或镍等作粘结相,研制成粉末,按一定比例混合,压制成型,在高温高压下烧结而成。
硬质合金的常温硬度很高(89~93HRA,相当于78~82HRC)。
耐熔性好,热硬性可达800~1000℃以上,允许的切削速度比高速钢提高4~7倍,刀具寿命高5~8倍,是目前切削加工中用量仅次于高速钢的主要刀具材料。
但它的抗弯强度和韧性均较低,性脆,怕冲击和振动,工艺性也不如高速钢。
因此,硬质合金常制成各种形状的刀片焊接或夹固在车刀、刨刀、端铣刀等的刀体上使用。
我国目前常用的硬质合金主要有以下三类:
①钨钴类硬质合金(YG类)KK类---红色
由WC和Co组成,代号为YG。
常温硬度为89~91HRA,耐热性达800~900℃,适用于加工切屑呈崩碎状的脆性材料。
如铸铁。
常用牌号有YG3、YG6和YG8等,其中数字表示含Co的百分比,其余为含WC的百分比。
钴在硬质合金中起粘结作用,含Co愈多的硬质合金韧性愈好,所以YG8适于粗加工和断续切削,YG6适于半精加工,YG3适于精加工和连续切削。
②钨钛钴类硬质合金(YT类)PP类---蓝色
由WC、TiC和Co组成,代号为YT。
此类硬质合金的硬度、耐磨性和耐热性(900~1000℃)均比YG类合金高,但抗弯强度和冲击韧度降低。
主要适于加工切屑呈带状的钢料等韧性材料,如钢类。
常用牌号有YT30、YT15和YT5等,数字表示含TiC的百分比。
故YT30适于对钢料的精加工和连续切削,YT15适于半精加工,YT5适于粗加工和断续切削。
③钨钛钽(铌)钴类硬质合金(YW类)KK类---黄色
又称通用合金,由WC、TiC、TaC(NbC)TCo组成,代号为YW。
其抗弯强度、疲劳强度、冲击韧性、耐热性、高温硬度和抗氧化能力都有很大提高。
常用牌号有YW1和YW2,这两种硬质合金都具有YG类硬质合金的韧性,比YT类硬质合金的抗刃口剥落能力强。
由于YW类硬质合金的综合性能较好,除可加工铸铁、有色金属和钢料外,主要用于加工耐热钢、高锰钢、不锈钢等难加工材料。
第四节其它刀具材料
一.陶瓷材料
陶瓷刀具材料的主要成分是硬度和熔点都很高的Al2O3、Si3N4等氧化物、氮化物,再加入少量的金属碳化物、氧化物或纯金属等添加剂。
也是采用粉末冶金工艺方法经制粉,压制烧结而成。
陶瓷刀具有很高的硬度(91~95HRA)和耐磨性,刀具耐用度高;有很好的高温性能,化学稳定性好,与金属亲和力小,抗粘结和抗扩散能力好;具有较低的摩擦系数,在高速精车和精密铣削时,被加工工件可获得镜面效果。
陶瓷刀具的最大缺点是脆性大,抗弯强度和冲击韧度低,承受冲击负荷的能力差。
主要用于对钢料、铸铁、高硬材料(如淬火钢等)连续切削的半精加工或精加工。
二.人造金刚石
人造金刚石是在高温高压和金属触媒作用的条件下,由石墨转化而成。
金刚石刀具的性能特点是:
有极高的硬度和耐磨性,切削刃非常锋利,有很高的导热性。
但耐热性较差,且强度很低。
主要用于高速条件下精细车削及镗削有色金属及其合金和非金属材料。
但由于金刚石中的碳原子和铁有很强的化学亲合力,故金刚石刀具不适合加工铁族材料。
三.立方氮化硼(简称CBN)
是用六方氮化硼(俗称白石墨)为原料,利用超高温高压技术,继人造金刚石之后人工合成的又一种新型无机超硬材料。
其主要性能特点是:
硬度高(高达8000~9000HV),耐磨性好,能在较高切削速度下保持加工精。
热稳定性好,化学稳定性好,且有较高的热导率和较小的摩擦系数,但其强度和韧性较差。
主要用于对高温合金、淬硬钢、冷硬铸铁等材料进行半精加工和精加工。
第三部分切削过程及切屑种类精简容
第一节金属切屑过程
金属切削过程:
是指通过切削运动,使刀具从工件上切下多余的金属层,形成切屑和已加工表面的过程。
在这一过程中产生了一系列的现象,如切削变形、切削力、切削热与切削温度、刀具磨损等。
研究诸现象的成因、作用和变化规律并掌握这些规律,对于合理使用与设计刀具、夹具和机床,保证切削加工质量,减少能量消耗,提高生产率和促进生产技术发展等方面起着重要的作用。
一.切削变形
金属切削过程与金属受压缩(拉伸)过程比较:
如下图(a)所示,塑性金属受压缩时,随着外力的增加,金属先后产生弹性变形、塑性变形,并使金属晶格产生滑移,而后断裂;
如下图(b)所示,以直角自由切削为例,如果忽略了摩擦,温度和应变速度的影响,金属切削过程如同压缩过程,切削层受刀具挤压后也产生塑性变形。
切削过程中产生的诸现象均与金属层变形密切相关。
为了进一步分析研究切削层变形的特殊规律,通常把切削刃作用部位的金属层划分为三个变形区:
第Ⅰ变形区也称为基本变形区,近切削刃处切削层产生的塑性变形区;金属的剪切滑移变形,基本变形区的变形最大;
第Ⅱ变形区也称为摩擦变形区,与前刀面接触的切屑层产生的塑性变形区;金属的挤压摩擦变形;
第Ⅲ变形区也称为加工表面变形区,近切削刃处已加工表层产生的变形区;金属的挤压摩擦变形。
如图c,三个变形区汇集在切削刃附近,此处的应力集中而且复杂,金属的背切削层在此与工件基体发生分离,大部分变成切屑。
二.切屑的形成及变形特点
(一)第一变形区金属的剪切滑移变形
切削层受刀具的作用,经过第一变形区的塑性变形后形成了切屑。
下面以直角自由切削为例,分析较典型的连续切屑的形成过程。
切削层受到刀具前刀面与切削刃的挤压作用下,使近切削刃处的金属先产生弹性变形,继而塑性变形,在这同时金属晶格产生滑移。
如图:
切削层金属在始滑移面OA以左发生弹性变形,越靠近OA面,弹性变形越大。
在在OA面上,应力达到材料的屈服点σs,则发生塑性变形,产生滑移现象。
在滑移面OM上上,应力和变形达到最大值。
越过OM面面,切削层金属将脱离工件基体,沿着前面流出切屑,完成切离过程。
经过塑性变形的金属,其晶粒沿大致相同的方向生长。
金属切削过程实际上是一种挤压过程。
取金属部质点P来分析滑移过程:
P点移到1位置时,产生了塑性变形。
即在该处剪应力达到材料的屈服极限,在1处继续移动到1′处的过程中,P点沿最大剪应力方向的剪切面上滑移至2处,之后同理继续滑移至3、4处,离开4处后,就沿着前刀面方向流出而成为切屑上一个质点。
在切削层上其余各点,移动至AC线均开始滑移、离开AE线终止滑移,在沿切削宽度围,称AC是始滑移面,AE是终滑移面。
AC、AE之间为第Ⅰ变形区。
由于切屑形成时应变速度很快、时间极短,故AC、AE面相距很近,一般约为0.02~0.2mm,所以常用AB滑移面来表示第一变形区,AB面亦称为剪切面。
第Ⅰ变形区就是形成切屑的变形区,其变
形特点是切削层产生剪切滑移变形
经过塑性变形的金属,其晶粒
沿大致相同的方向生长。
金属
切削过程实际上是一种挤压过程。
二.第二变形区金属的挤压摩擦变形
经过第一变形区后,形成的切屑要沿前刀面方向排出,还必须克服刀具前刀面对切屑挤压而产生的摩擦力。
切屑在受前刀面挤压摩擦过程中进一步发生变形(第二变形区的变形)这个变形主要集中在与前刀面摩擦的切屑底面一薄层金属里,,表现为该处晶粒纤维化的方向和前刀面平行。
这种作用离前刀面愈远影响愈小。
三.第三变形区金属的挤压摩擦变形
已加工表面受到切削刃钝圆部分和后刀面的挤压摩擦,造成纤维化与加工硬化。
第二节切屑的类型
一.切屑的分类
由于工件材料不同,切削条件不同,切削过程的变形也不同,所形成的切屑多种多样。
通常将切屑分为四类:
带状切屑;挤裂切屑;单元切屑;崩碎切屑
(1)带状切屑
它是经过上述塑性变形过程形成的切屑,外形呈带状。
加工塑性金属材料例如碳素钢、合金钢、铜和铝合金,当切削厚度较小,切削速度较高、刀具前角较大时,常得到这类切屑。
其切削过程平稳,切削力波动小,已加工表面的表面粗糙度值较小。
(2)挤裂切屑
在形成切屑的过程中,剪切面上局部位置处的剪应力τ达到材料的强度极限,使切屑上与前刀面接触的一面较光洁,其背面局部开裂成节状。
切削黄铜或用低速切削钢,当切削厚度较大,切削速度较低、刀具前角较小时,常得到这类切屑较易得到这类切屑。
(3)单元切屑
当剪切面上的剪应力超过材料的强度极限时产生了剪切破坏,使切屑沿厚度断裂成均匀的颗粒状。
切削铅或用很低的速度切削钢时可得到这类切屑。
(4)崩碎切屑
在切削脆性金属时,,例如铸铁、黄铜等材料,,切削层几乎不经过塑性变形就产生脆性崩裂,得到的切屑呈不规则的细粒状。
切屑的类型是由材料的应力--应变特性和塑性变形程度决定的。
如加工条件相同,塑性高的材料不易断裂,易形成带状切屑;改变加工条件(如减小前角,或加大切削厚度),材料产生的塑性变形程度随之变化,切屑的类型便会相互转化,当塑性变形尚未达到断裂点就被切离时出现了带状切屑,变形后达到断裂就形成挤裂切屑或单元切屑。
因此,在生产中常利用切屑转化条件,使之得到较为有利的屑型。
切屑控制:
在切削加工中采取适当的措施来控制切屑的卷曲、流出和折断,使之形成“可接受”的良好切屑。
研究表明,工件脆性越大、切屑厚度越大、切屑卷曲半径越大,切屑就越容易折断。
二.切屑控制的方法切屑控制的方法
(1)采用断屑槽
通过设置断屑槽对流动的金属施加一定的约束力,可使切屑应变增大,切屑蜷曲半径减小。
断屑槽的形状有折线形、直线圆弧形、全圆弧形。
(2)改变刀具角度
增大主偏角,切削厚度变大,有利于断屑;减小前角,可使切屑变形加大,切屑易于折断。
刃倾角可改变切屑的流向。
(3)调整切削用量
提高进给量可使切削厚度增大,有利于断屑,但增大进给量会使表面粗糙度增大;适当降低切削速度可使切削变形增大,有利于断屑,但会降低切除效率。
三.积屑瘤现象
(一).在切削速度不高而又能形成连
续切屑的情况下,加工一般钢料或
其它塑性材料时,常常在前刀面处
粘着一块剖面有时呈三角状的硬块。
它的硬度很高,通常是工件材料的
2-3倍,在处于比较稳定的状态时,
能够代替切削刃进行切削。
这块冷
焊在前刀面上的金属称为积屑瘤或
刀瘤。
积屑瘤对切削过程的影响:
1.代替刀具切削,保护刀具
2.增大前角,减小变形和力
3.产生过切及犁沟,↓精度
4.增大已加工表面粗糙度
积屑瘤对精加工是不利的,应避免它产生:
降低工材塑性;合理选切削速度;增大前角;减小进给量;采用润滑液等.
如图所示,积屑瘤是堆积在前刀面上近切削刃处的一个楔块,经测定它的硬度为金属母体的2~3倍,积屑瘤高出
前刀面0.369mm、凸出后刀面
0.057mm、宽1.138mm,在切削
时形成了实际前角32°27′(有
的可达40°)。
当积屑瘤的顶部具有大的刃口圆弧半径时
(图中R0.134mm),会产生较
大的挤压作用。
此外,由于积
屑瘤顶部凹凸不平和脱落后粘
附在已加工表面上,促使加工表面粗糙度增加。
所以在精加工时应尽量避免或抑制积屑瘤的产生。
(二).积屑瘤的形成有许多解释:
通常认为是由于切屑在前刀面上粘结造成的。
当在一定的加工条件下,随着切屑与前刀面间温度和压力的增加,摩擦力也增大,使近前刀面处切屑中塑性变形层流速减慢,产生“滞流”现象。
越贴近前刀面处的金属层,流速越低。
当温度和压力增加到一定程度,滞流层中底层与前刀面产生了粘结。
当切屑底层中剪应力超过金属的剪切屈服极限时,底层金属流速为零而被剪断,并粘结在前刀面上。
该粘结层经过剧烈的塑性变形使硬度提高,在继续切削时,硬的粘结层又剪断软的金属层。
这样层层堆积,高度逐渐增加,形成了积屑瘤。
长高了的积屑瘤,受外力或振动的作用可能发生局部断裂或脱落。
有些资料表明积屑瘤的产生、成长和脱落是在瞬间进行的,它们的频率很高,是个周期性的动态过程。
(三).形成积屑瘤的条件:
主要决定于切削温度.在切削温度很低时,,切屑与前刀面间呈点接触,摩擦系数μ较小,故不易形成粘结;在温度很高时,接触面间切屑底层金属呈微熔状态,起润滑作用,摩擦系数也较小,积屑瘤同样不易形成。
在中温区,例如切削中碳钢的温度在300~380℃时,切屑底层材料软化,粘结严重,摩擦系数μ最大,产生的积屑瘤高度达到很大值。
此外,接触面间压力、粗糙程度、粘结强度等因素都与形成积屑瘤的条件有关。
合理控制切削条件,调节切削参数,尽量不形成中温区域,就能较有效地抑制或避免积屑瘤的产生。
以切削中碳钢为例,从图示的曲线可知,低速(vc≤3m/min左右)切削时,产生的切削温度很低;较高速(vc>60m/min)切削时,产生的切削温度较高,这两种情况的摩擦系数均小,故不易形成积屑瘤。
在中速(vvcc≈20m/min),积屑瘤的高度达到最大值。
所以许多中速加工工序,如攻丝、拉孔、钻孔、铰孔等经常由于积屑瘤作用而影响加工表面粗糙度。
如同其它精加工工序,为了提高加工表面质量,应尽量不采用中速加工,否则应配合其它改善措施。
在切削硬度和强度高的材料时,由于剪切屈服强度τS高,不易切除切屑,即使采用较低的切削速度,也易达到产生积屑瘤的温区域,为了抑制积屑瘤,通常选用中等以上切削速度加工。
切削塑性高的材料,需选用高的切削速度才能消除积屑瘤。
第四部分切削力精简容
第一节切削力的来源、切削合力及其分解、切削功率
一、切削力的来源
切削时作用在刀具上的力,由下列两个方面组成:
①变形区产生的弹性变形抗力和塑性变形抗力
②切屑、工件与刀具间的摩擦力。
二、切削合力及其分解
为了便于分析切削力的作用和测量、计算切削力的大小,通常将合力Fr在按主运动速度方向、切深方向、进给方向作的空间直角坐标轴z、y、x上分解成三个分力,它们是:
切削力的分解:
由图可知,合力与各分力间关系为:
其中,Fy=Fx.ycoskr;
Fx=Fx.ysinkr
式中Fxy-合力在Fr基面上的分力
三、切削功率
(1)单位切削力
单位切削力p是指切除单位切削层面积所产生的主切削力,可用下式表示:
表明,单位切削力p与进给量f有关,它随着进给量f增加而减小。
单位切削力p不受背吃刀量asp的影响,这是因为背吃刀量改变后,切削力Fz与切削层面积AD以相同的比例随着变化。
而进给量f增大,切削层面积AD随之增大,而切削力Fz增大不多。
利用单位切削力p来计算主切削力Fz较为简易直观。
(2)切削功率
切削功率Pm是指车削时在切削区域消耗的功率,通常计算的是主运动所消耗的功率。