英文翻译.docx
《英文翻译.docx》由会员分享,可在线阅读,更多相关《英文翻译.docx(12页珍藏版)》请在冰豆网上搜索。
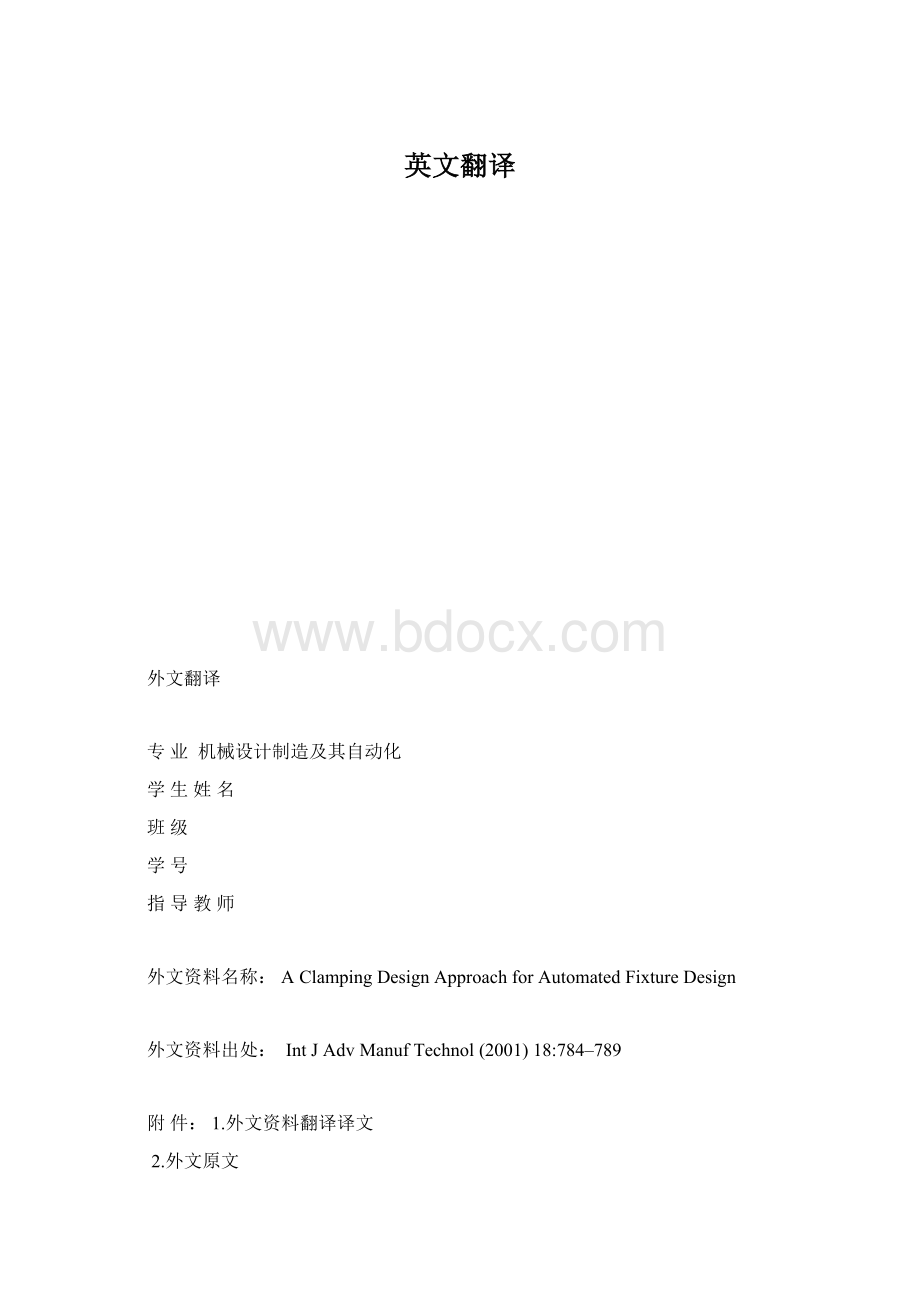
英文翻译
外文翻译
专业机械设计制造及其自动化
学生姓名
班级
学号
指导教师
外文资料名称:
AClampingDesignApproachforAutomatedFixtureDesign
外文资料出处:
IntJAdvManufTechnol(2001)18:
784–789
附件:
1.外文资料翻译译文
2.外文原文
指导教师评语:
签名:
年月日
自动化夹具设计的一种夹紧设计方法
J.Cecil
王凌译
摘要:
这篇文章中指出了一种具有创新的夹具设计方案,夹具设计在计算机辅助的下,其中的夹紧设计涉及到一个给定的工件的夹紧面和夹紧点的确定。
这种设计方案与定位设计方案相关,定位设计方案的主要目的是:
支承工件在加工时并在不妨碍刀具的情况下,使工件定位。
夹具自动化设计方案将给出详细的步骤。
还有,运用几何法就可以算出可行的夹紧面和位置。
所需要的只是成品工件CAD模型的参数和特征,还有定位点和定位件。
关键词:
夹紧;夹具设计
一.前言
夹具设计是主要部分,它联系着设计和制造两个模块,三者是一体化的。
实现下一代制造系统的关键是研究开发自动化夹具设计以及计算机辅助夹具设计(CAFD)。
本文讨论的夹紧设计方案对综合夹具设计方法论会是一个很大的促进。
夹紧设计方案集中了几个研究工作。
Chou[1]着重于工件稳定性和要完全克制的条件。
随着夹具设计中专家系统的广泛应用,人工智能的实现也会越来越临近[2,3]。
从CAD模型的部分几何信息也驱动了夹具设计。
Bidanda[4]描述了能够确定回转体零件的定位点和夹紧面的规则型专家系统。
夹具装置用来执行定位和夹紧两功效。
有些研究者(例如[5,6])分析切削力和建立钻孔机械模型及其他金属切削过程。
Kang等[2]定义组合夹具的装配约束。
几个研究者运用模块化装夹原理设计夹具[2,7-11]。
还有夹具设计的研究在[1,3,9,12-23]说明。
还有些夹具设计的论述可以在[21,24]找到。
第2部分概述了自动化夹紧设计方案的各个概述。
第3部分测定在工件
时加工的夹具尺寸。
第4部分中讲述有关工件夹紧面自动确定的有关内容。
第5部分讨论工件夹紧点的确定。
二.夹具的总体设计
这一部分描述夹具总体设计方法。
一般来说,夹具放在特定位置上,并能够抵消切削力的影响。
夹具设计中,夹紧与定位之间有很大的联系性。
很多时候,夹紧与定位在同一个装置就能完成。
错误地认为它们是分开的,可能会导致夹具设计的不能可靠的工作。
设计者通常先解决定位问题,这需要设计一个定位装置;然而,总体定位和支持的设计方案已经超出了设计计划的范围。
CAD模型的零件设计(夹具的组件),公差大小,工艺程序,定位点等设计,这些因素都应纳入到夹具设计方案中。
夹紧的目的是靠定位和支承件保持工件位置不变。
导向元件是在加工过程中确保不受切割或动力。
夹具定位应在加工时切削力有利于保持工件静止的方向上。
由于切削力对着定位装置,零件(或工件)被固定在定位点上,所以零件不能够远离定位装置。
这里的夹紧设计方法放在夹具总体设计中讨论。
事先设计的定位和夹紧装置,初期的特征的分析与识别,相关公差要求及其他必要的说明都应该初步评价和决定,以便进行定位和夹紧件的设计,本文描述的夹紧设计方案是基于一个假设,即定位机构的设计属性已经确定较早(这包括确定适当的工件上的定位和支撑面,以及定位和支撑装夹元件如V型块,底板,定位针等)。
2.1进入夹具设计
进入这些包括产品设计的实体模型,公差要求,特征,加工工艺和每一个零件设计中相关特征的加工方向,定位面和定位机构,加工时实现相应特征的切削力。
2.2夹具设计的过程
图1概述了夹具自动化设计的主要步骤,具体如下:
第1步:
参照SUi结构的配置清单,找到相关的[工艺特征]结构。
第2步:
确定夹紧的方向和类型。
这就需要加工方向向量mdv1,mdv2,……mdvn,并确定了支撑面nvs的法向矢量。
如果加工方向是向下的(对应方向向量[0,0,-1]),那么支撑面的法向向量应平行于加工方向,夹紧力的方向是平行于向下的加工方向[0,0,-1]。
如果需要一个侧向夹紧,没有可行的地方放置向下夹紧的夹具,侧向夹紧的方向应如下,假设sv和tv是第二支撑面和第三支撑面的法向矢量。
侧向夹紧机构的夹紧方向应该像这样,例如V型块应平行于sv和tv等。
具体的说就是,V型块的两个V型面的法向应各自平行于sv和tv。
第3步:
确定切削力(每个特征的)MFi(i=1,…,n)中的最高切削力。
在设计SUi结构的夹具时,这些有效力FE必须达到力平衡。
第4步:
计算出的最高切削力FE并确定支撑工件的夹具的各个尺寸大小(例如,皮带夹可被用来作为夹紧机构),第三部分对这种方法详细说明。
图1夹具设计流程图
第5步:
确定给定工件的夹紧面。
这一步会如第四部分描述的那样自动化进行。
第6步:
夹紧面上夹具的实际位置以一种自动的方式确定,就如第五部分说的那样。
考虑下一个SU(i+1)的结构设计并进行第1步。
三.确定夹具尺寸
在这项工作中,使用的夹具被称为皮带扣夹具。
皮带扣夹具根据杠杆原理(见图2)设计的。
本部分描述了皮带扣夹具的自动化设计。
螺丝的大小或支承夹具的螺纹装置与要求的夹紧力有关。
夹紧力应与切削力平衡以便支承工件。
假定夹紧力为W,螺栓直径为d。
下面的方法能够确定满足要求夹紧力所需的螺丝的直径大小。
最初,夹具材料的极限抗拉强度(悉尼科技大学)可查看手册。
可来自同一个数据图书馆,不同的材料有不同抗拉强度。
选用何种夹具材料也可以直接采用启发式规则。
举例来说,如零件材料是低碳钢,夹具材料可以是低碳钢或机件钢。
为了确定设计应力,极限抗拉强度可以用安全系数(如4或5)。
螺栓的根部面积A1(如螺旋夹紧机构)等于夹紧力/设计应力DS。
随后,螺栓横截面积FA等于
图2带扣的夹具
A1/(65%)(因为螺栓的根部面积大概是螺栓横截面积65%时剪切才会发生)螺栓直径d可由FA/(3.14*d2/4)得到。
另一个方程中包括与螺栓直径d有关的夹具宽度b,高度H和跨度L(B,H和L能够算出d的大小):
d2=4/3BH2/L
四.确定夹紧面
确定夹紧位置必需包括:
产品的CAD模型,提取特征信息,特征的尺寸、面和孔,定位孔和定位面的确定。
假设一个潜在的夹紧面PCF如图3。
夹紧面不应该重叠或相交在结合面上,如图4所示。
接触工件表面(或者PCF)的夹紧面是一个由二维剖面构成的曲线如图(6)。
用线段相交测试,可以确定是否有潜在的夹紧域,它与给定的PCF有重叠现象。
夹紧面的确定可自动如下:
第1步:
确定这样的面,它平行于第二定位面和第三定位面(lf1和lf2),并且远离lf1和tcj。
演示如下:
(一)确定面tci、tcj,tci平行于lf1,tcj平行于lf2。
(二)插入清单TCF中的候选面tci。
(三)通过检查所有列在TCF中的面tci,确定分别离lf1和lf2最远的面tci和tcj,删除列于TCF中的其他面。
第2步:
确定平行于定位面但不能与另外定位面邻近的面。
最好选择一个不在定位件垂直面上的夹紧面。
这一步骤可自动进行如下所示:
(一)考虑TCF中的每个面tci,并取得相应的面fci,它们邻近并垂直于面tci。
然后,插入FCF中的每个面fci。
图3潜在夹紧面与特征剖面
图4潜在夹紧面与夹具盒面
(二)检测每个面fci,履行下列环节:
如果fci是邻近的,且垂直于lf1或lf2,然后把检测到的fci从TCF中提取出来,插入到库NTCF中。
第3步:
确定夹紧面,它立足于潜在的夹紧面,分述如下:
情况
(一):
如果在库NTCF中没有通过,则使用库TCF中的面,并进行第4步。
如果检测到垂直于第二定位面lf1和第三定位面lf2的面,它们是夹紧面的最优选择。
在这种情况下,剩下的唯一选择是重新审视库NTCF中的面。
情况
(二):
若库NTCF中通过的面只有一个,那可行夹紧面就是fci。
相应的邻近的垂直面tci的法向就是夹具的中心。
情况(三):
如果在库NTCF中通过的面数大于1,确定面tci,并进行第4步。
第4步:
根据夹紧方向是不是[(+或-)1,0,0]或[(+或-)0,1,0],夹具可以顺着面tci的中心区放置。
用零件的几何与拓扑信息可以确定夹具的候选几何位置,会
在下一节描述。
图5夹具轮廓尺寸的确定
五.确定夹紧面上的夹紧点
夹紧面确定以后,它面上的夹紧位置也必需被确定。
插入的包括夹具轮廓尺寸,夹具的坐标系[X,Y,Z],及潜在夹紧面CF。
使用几何学CF可获得夹具轮廓尺寸(如案例(g),如下所述:
首先就是要确定一个盒子的大小,测试它是否能够包含一切特征。
简介相交测试,也可以用该方法描述。
如果相交测试给予一个错误的结果,那么就没有特征和夹具盒轮廓相交,如图4所示。
如果相交测试给予一个肯定的结果,那么就执行以下的步骤:
(1)把夹具盒剖面分割成尺寸为(1×w)的小型矩形条(图5和6)。
(2)演示发生在给定零件CF面上特征的相交测试和特征概况。
(3)没有发生特征相交时,矩形条区域是可行夹紧区域。
如果有一个以上的矩形,向着沿着夹具轴线的CF面的中点的矩形轮廓就是夹具轮廓(和夹紧点)。
如果没有和特征轮廓不相交的轮廓Pi,夹具宽度可以减少一半以及在那个面上的夹具数量可以增加到两个。
利用这些已经修正过的夹具尺寸,实施先前的特征相交测试。
如果测试也失败的话,那么邻近PCF的侧面可以作为夹紧面来完成辅助夹紧。
这个侧面成为PCF,再进行特征相交测试。
5.1相交剖面测试
必要的投入包括二维剖面P1,另一个二维剖面P2。
使用以下的方法,所有的剖
图6特征与夹具区域的轮廓相交测试
面能够自动地确定。
分别输入由一个封闭的回路线段Lij构成的剖面Pi。
剖面测试的步骤如下:
(T1)假设P1上的线段L(i,1)和另一个P2上的线段L(2,j)。
(T2)对于输入L(i,1)和L(2,j),我们利用边的相交性。
如果边的相交测试给予了肯定,那么特征剖面估计会与潜在的夹具剖面相交。
如果它给予了否定,那么进行第3步。
(T3)重复步骤(T1),为了P1上的同一边(Li,1),并且保持P2上的线段[(L2,j+1)直到j=n+1]
(T4)重复步骤(T1)和(T2)保持边或线段在剖面P1上的L12,L13,…,L1n。
如果特征剖面与夹具剖面有重叠,线相交测试将确定其发生。
边测试可自动侦测到两条边是否彼此相交。
这个测试需要的是线段L12{连接(x1,y1)和(x2,y2)}和线段L34{连接(x3,y3)和(x4,y4)}。
假设L12的方程式为:
F(x,y)=0
(1)
和L34的方程式为:
H(x,y)=0
(2)
第1步:
利用方程式
(1),把x3代入x,y3代入y得出r3=F(x3,y3),把x4代入x,y4代入y,得出r4=F(x4,y4)。
第2步:
如果r3不等于0,r4也不等于0,并且r3等于r4,(这表明r1和r2在同一侧),边L12和L34就不相交。
如果不满足这些条件,进行步骤3。
第3步:
利用方程式
(2),得出r1=H(x1,y1)。
接着得出r2=G(x2,y2)并进行步骤4。
第4步:
如果r1不等于零,r2不等于零,并且r1等于r2,那么r1和r2在同一侧,输入的线段不会相交。
否则,如果这个条件不满足,进行步骤5。
图7用于说明夹具设计方案的零件图
第5步:
给定的线段不相交,完成测试。
考虑如图7所示的零件。
它的特征是一个台阶和一个孔。
定位件的设计已经完成。
支承件(或主要的定位件)是一个底板(它靠着f4面),第二定位件和第三定位件靠着面f6和面f5(它们分别对应着在第四节中讨论的定位面lf1和lf2)。
也可以使用辅助定位件——V形块(它靠着辅助面f3和f5),如图8所示。
因为在早些时候讨
图8为图7中零件的夹具图
论的夹具设计方案概述的步骤,辅助面(它们是平行的并且最远离lf1和lf2)是面f3和f5。
事实上没有面平行于定位面,也不邻近它们.在这个实例中使用优先原则(第4节的第3步中讨论过这样的情况),保留的辅助面是面f2。
夹具方向是向下的;V形块和其他一些定位件能够提供夹具上需要的定位,以便用来支承靠着基板向下的工件。
按照第5部分中描述的步骤来确定夹具的定位位置。
如在面f2上没有特征,那就没有必要进行特征相交测试来确定无碰撞的夹紧。
夹具的位置应该远离V形块(V形块靠着辅助定位面),这是由于夹紧面邻近于辅助定位面(这就确保了更好的快速夹紧的机会)。
最终的定位和夹紧设计如图8所示。
与其他文献中的夹具设计方案相比,本文中的夹具设计方案毫不逊色。
本方法中独到之处在于通过零件的几何拓扑结构进行夹紧面的系统识别,加工件的特征描述。
其他方法没有充分地描述定位件的位置,所提议的方法指出了在加工时使用定位件限制工件的自由度。
这个方法的另一个优点是使用剖面相交测试来确定夹具上的可行的辅助定位位置(早期描述),它能够快速地,有效地识别在工件的夹紧和加工过程中发生的某些问题。
六.结论
在这本文中讨论了关于夹具的夹紧设计方面。
定位的设计,零部件的设计,以及其他一些关于确定夹紧面和夹紧的方向。
这一办法也在本文中讨论了实现自动化的各个步骤。
参考文献
1.Y.C.Chou,V.ChandruandB.Barash,“Amathematicalapproachtoautomaticconfigurationofmachiningfixtures:
analysisandsynthesis”,TransactionsASME,JournalofEngineeringforIndustry,111(4),pp.299–306,1989.
2.Y.Kang,Y.RongandM.Sun,“Constraintbasedmodularfixtureassemblymodellingandautomateddesign”,ProceedingsoftheASMEManufacturingScienceandEngineeringDivision,8,pp.901–908,1998.
3.M.ManiandW.R.D.Wilson,“Automateddesignofworkholdingfixturesusing
kinematicconstraintsynthesis”,16thNAMRC,pp.437–444,1988.4.B.BidandaandP.H.Cohen,“Developmentofacomputeraidedfixtureselectionsystemforconcentricrotationalparts,”AdvancesinIntegratedDesignandManufacturing,Proceedings1990ASMEWinterAnnualMeeting,SanFrancisco,CA,vol.23–1,pp.151–162,1990.
5.R.E.DeVor,V.ChandrasekharanandS.G.Kapoor,“Mechanisticmodeltopredictthecuttingforcesystemforarbitrarydrillpointgeometry”,TransactionsASMEJournalofManufacturingScienceandEngineering,120,pp.563–570,1998.
6.R.E.DeVor,S.G.KapoorandW.J.Endres,“Adualbasedapproachtothepredictionofmachiningforcesformetalcuttingprocesses:
PartII,Modelvalidationandinterpretation”,TransactionsJournalofEngineeringforASMEIndustry,117,pp.534–541,1995.
7.M.V.GandhiandB.S.Thompson,“Automateddesignofmodularfixturesforflexiblemanufacturingsystems”,JournalofManufacturingSystems,5(4),pp.243–252,1987.
8.T.S.Kow,A.SenthilKumarandJ.Y.H.Fuh,“Anintegratedcomputeraidedmodular
fixturedesignsystemforinterferencefreedesign”,ProceedingsoftheASMEManufacturingScienceandEngineeringDivision,8,pp.909–916,1998.
9.Y.RongandS.Wu,“Automatedverificationofclampingstabilityincomputeraided
fixturedesign”,ComputersinEngineering,ProceedingsoftheInternationalConference,
ASMENY,pp.421–426,1994.
10.Y.RongandY.Bai,“Machiningaccuracyanalysisforcomputeraidedfixturedesign”,JournalofManufacturingScienceandEngineering,118,pp.289–300,1996.
11.Y.Wu,Y.RongandW.Ma,“Automatedmodularfixtureplanning:
geometricanalysis”,RoboticsandComputerIntegratedManufacturing,14,pp.1–15,1998.
12.J.R.BoermaandH.J.J.Kals.“FixturedesignwithFIXES”,AnnalsCIRP,38,pp.
399–402,1988.
13.W.Cai,S.J.HuandJ.X.Yuan,“Avariationalmethodofrobustfixtureconfiguration
designfor3Dworkpieces”,JournalofManufacturingScienceandEngineering,119,pp.593–602,1997.
14.J.A.Cecil,“FixturedesigninaCIMenvironment,PhDdissertation,TexasA&MUniversity,DepartmentofIndustrialEngineering,CollegeStation,1995.
15.J.Dai,A.Y.C.NeeandJ.Y.H.Fuh,“Anapproachtoautomatingmodularfixturedesignandassembly”,ProceedingsoftheInstitutionofMechanicalEngineers,PartB,JournalofEngineeringManufacture,211,pp.509–521,1997.
16.A.R.DarvishiandK.F.Gill,“Knowledgerepresentationdatabaseforthedevelopmentofafixturedesignexpertsystem”,ProceedingsofIMechE,202,pp.37–49,1988.
17.W.Ma,J.LiandY.Rong,“Developmentofautomatedfixtureplanningsystems”,InternationalJournalofAdvancedManufacturingTechnology,15(3)pp.171–181,1999.
18.A.Y.C.Nee,K.WhybrewandA.SenthilKumar,AdvancedFixtureDesignforFMS,Springer-Verlag,1995.
19.Y.Rong,Y.Wu,W.MaandS.LeClair,“Automatedmodularfixturedesign:
accuracyanalysisandclampingdesign”,RoboticsandComputerIntegratedManufacturing,14,pp.1–15,1997.
20.ShahandM.Mantyla,ParametricandFeatureBasedCAD-CAM:
Conceptsand
Technology,JohnWiley,NewYork,1995.
21.B.S.ThompsonandM.V.Gandhi,“Aliteraturesurveyoffixturedesignautomation”,InternationalJournalofAdvancedManufacturingTechnology,pp.240–255,1985.
22.A.J.C.TrappeyandC.R.Liu,“Automatedfixtureconfigurationusingprojectivegeometryapproach”,InternationalJournalofAdvancedManufacturingTechnology,Vol.8,pp.297–304,1993.
23.K.WrightandC.C.Hayes,“Automatedplanninginthemachiningdomain,knowledgebasedexpertsystemsformanufacturing”,ASME,PED-24,pp.221–232,1986.
24.J.A.Cecil,“Initiativesincomputeraidedfixturedesign”,VEELLaboratoryReport,UtahStateUn