注塑机计算方法及一些应用方法.docx
《注塑机计算方法及一些应用方法.docx》由会员分享,可在线阅读,更多相关《注塑机计算方法及一些应用方法.docx(53页珍藏版)》请在冰豆网上搜索。
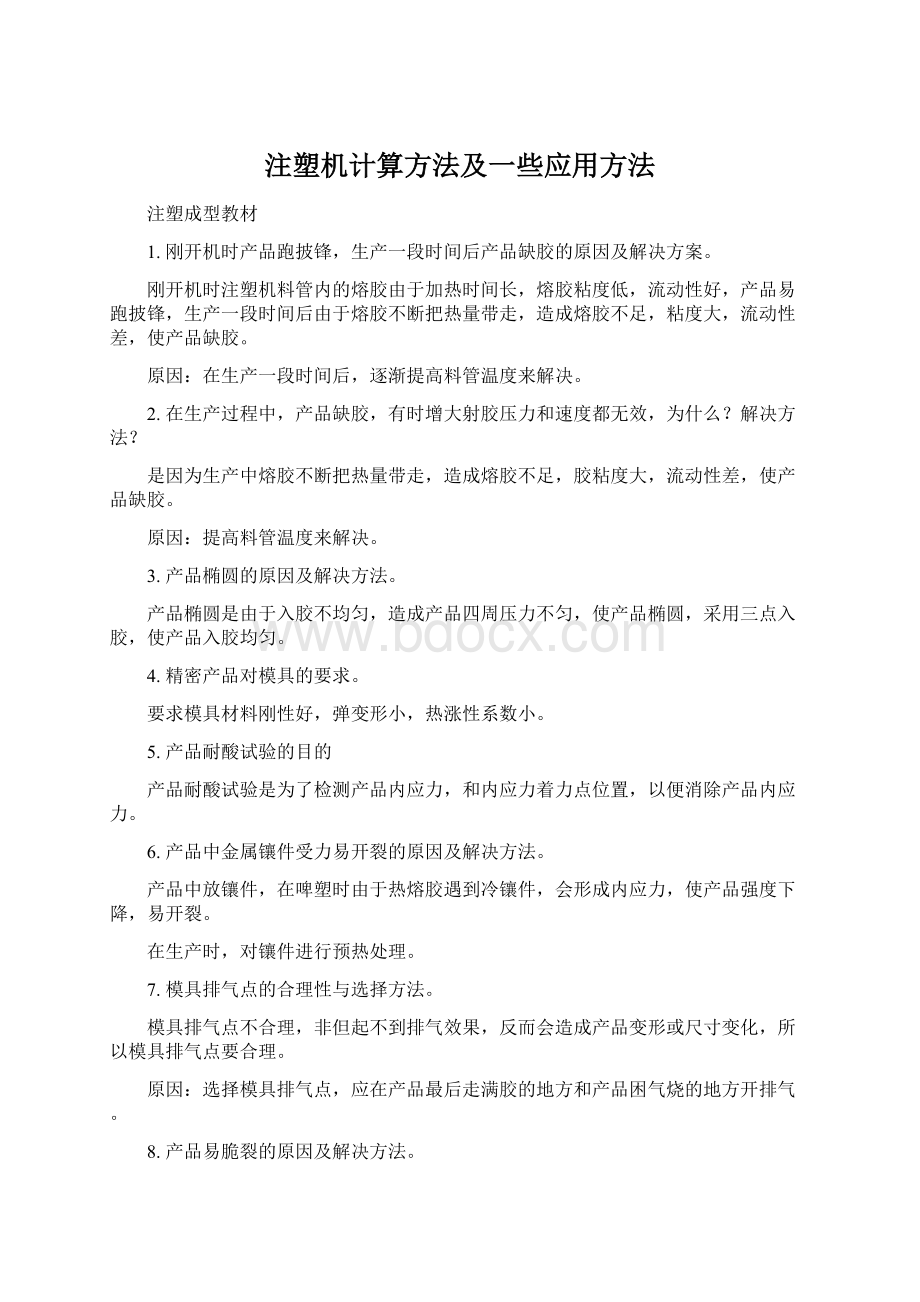
注塑机计算方法及一些应用方法
注塑成型教材
1.刚开机时产品跑披锋,生产一段时间后产品缺胶的原因及解决方案。
刚开机时注塑机料管内的熔胶由于加热时间长,熔胶粘度低,流动性好,产品易跑披锋,生产一段时间后由于熔胶不断把热量带走,造成熔胶不足,粘度大,流动性差,使产品缺胶。
原因:
在生产一段时间后,逐渐提高料管温度来解决。
2.在生产过程中,产品缺胶,有时增大射胶压力和速度都无效,为什么?
解决方法?
是因为生产中熔胶不断把热量带走,造成熔胶不足,胶粘度大,流动性差,使产品缺胶。
原因:
提高料管温度来解决。
3.产品椭圆的原因及解决方法。
产品椭圆是由于入胶不均匀,造成产品四周压力不匀,使产品椭圆,采用三点入胶,使产品入胶均匀。
4.精密产品对模具的要求。
要求模具材料刚性好,弹变形小,热涨性系数小。
5.产品耐酸试验的目的
产品耐酸试验是为了检测产品内应力,和内应力着力点位置,以便消除产品内应力。
6.产品中金属镶件受力易开裂的原因及解决方法。
产品中放镶件,在啤塑时由于热熔胶遇到冷镶件,会形成内应力,使产品强度下降,易开裂。
在生产时,对镶件进行预热处理。
7.模具排气点的合理性与选择方法。
模具排气点不合理,非但起不到排气效果,反而会造成产品变形或尺寸变化,所以模具排气点要合理。
原因:
选择模具排气点,应在产品最后走满胶的地方和产品困气烧的地方开排气。
8.产品易脆裂的原因及解决方法。
产品易脆裂是产品使用水口料和次料太多造成产品易脆裂,或是料在料管内停留时间过长,造成胶料老化,使产品易脆裂。
原因:
增加新料的比例,减少水口料回收使用次数,一般不能超过三次,避免胶料在料管内长时间停留。
9.加玻纤产品易出现泛纤的原因及解决方法
是由于熔胶温度低或模具温度低,射胶压力不足,造成玻纤在胶内不能与塑胶很好的结合,使纤泛出。
原因:
加高熔胶温度,模具温度,增大射胶压力。
10.进料口温度对产品的影响。
进料口温度的过高或过低,都会造成机器回料不稳定,使加料量不稳定,而影响产品的尺寸和外观。
11.透明产品有白点的原因及解决方法。
透明产品有白点是因为产品内进入冷胶造成,或料内有灰尘造成的。
原因:
提高射嘴温度,加冷料井,原料注意保存,防止灰尘进入。
12.什么是注塑机的射出能力?
射出能力PK=射出压力(kg/cm2)×射出容积(cm3)/1000
13.什么是注塑机的射出马力?
射出马力PW(KW)=射出压力(kg/cm2)×射出率(cm3/sec)×9.8×100%
14.什么是注塑机的射出率?
射出率V(cc/sec)=/4×d2×
d2:
:
料管直径:
料的密度
15.什么是注塑机的射胶推力?
射胶推力F(kgf)=/4(D12-D22)×P×2
D1:
油缸内径D2:
活塞杆外径P:
系统压力
16.什么是注塑机的射胶压力?
射胶压力P(kg/cm2)=[/4×(D12-D22)×P×2]/(/4×d2)
17.什么是注塑机的塑化能力?
塑化能力W(g/sec)=2.5×(d/2.54)2×(h/2.54)×N×S×1000/3600/2
h=螺杆前端牙深(cm)S=原料密度
18.什么是系统压力?
与注塑压力有什么区别?
系统压力(kg/cm2)=油压回路中设定最高的工作压力,注塑压力是指注塑时的实际压力,两者不相等。
19.注塑机液压用油的要求:
(1)适当的粘度和良好的粘温性能
(2)良好的润滑性和防锈性;
(3)良好的化学稳定性,不易气化成胶质;
(4)搞泡沫性好;
(5)对机件及密封装置的腐蚀性要小;
(6)燃点(闪点)要求,凝固点要低。
20.液压油粘度对注塑机的影响?
当系统工作环境温度较高时,应采用较高粘度的油,反之,应采用较低粘度的油,系统工作压力较高时,应采用粘度较高的,因为在高压,密封较困难,泄漏是主要问题,反之,系统工作压力较低,宜采用粘度较小的油,当液压系统的工作部件运转速度高时,油液的流速也高,这时压力损失也将增加,而泄漏量相对减小,宜采用粘度较低的油,反之,工作部件运动速度低时,宜采用粘度较高的油。
21.松退的设定。
松退正确位置=过胶圈移动位置+螺杆越位距离
22.松退位置设定的重要性
松退位置设定过大,会造成回料吸氧,使胶料氧化和产生气泡。
位置设定过小,使料筒内压力大,剪切力过高使胶料分解,射嘴流涎。
位置误差不能超过0.4mm.
23.熔胶位置的设定
熔胶位置=产品的重量/(最大行程/最大熔胶量)
24.气辅注塑的主要优点(GAM)
能抽空厚型材料芯部,制成空心管件,可节省材料,缩短周期时间。
在注塑中采用气体可使压力均匀分布,当塑料冷却和固化时,气体可通过膨胀对塑料的体积收缩进行补偿。
降低模塑制品内应力,从而提高外形稳定性,消除变形和翘曲现象。
25.活塞杆外径中间小,两头大问题?
由于中孔针过热产品收缩不均衡,造成活塞杆外径中间小,两头大.中孔针可采用散热快的磷铜材料来做,模具在产品中间部分排气.
26.球面丝印后开裂问题.
由于产品表面存在应力,造成丝印后开裂.增加模具温度,减小应力;可用退火的方法消除应力.
27.眼镜架,水口边易断问题.
射胶压力和保压压力大,水口边残存内应力,造成产品易断.尽量减小射胶压力和保压压力,适当提高模具温度来解决.
28.电器外壳,四个装配柱子,打螺丝时爆裂问题.
由于柱子存在夹水线,造成产品装配柱子易暴裂.模具增加排气,适当提高模温,加快射胶速度来减小夹水线.
29.产品变形问题.
产品变形主要是热收缩时不平衡造成产品变形,或由于产品本身内应力作用下使产品变形.
30.透明PC外壳气泡问题。
原料干燥不够;产品存在胶厚薄不均现象,模具排气不良,原料易分解都可能造成产品气泡.
原因:
充分干燥原料,增大模具排气,尽量减少胶厚薄不均现象.
31.复印机,磁性材料的啤塑问题。
应采用高模温,快速射胶方法.
32.产品包胶,水口边缩水问题。
模具排气不良,射胶速度慢,保压压力和时间不够,都能造成水口缩水.
原因:
增大模具排气,适当提高射胶速度,增加保压压力和时间.
33.产品内应力,造成产品放置一段时间后爆裂问题。
由于产品内残存应力,产品放置一段时间后由于应力的作用,使产品爆裂.
原因:
提高啤塑时的模具温度,降低射胶压力,来消除产品应力,产品可用退火的方法消除应力.
34.ABS料在用黑色色母时,造成产品易断裂脱皮问题。
是色母的颜料中用了碳粉过多原因,造成产品脱皮.更换色母颜料.
35.一台180吨14安士机,产品一出四CD盒共120克,外观良好,无批峰,但其中一只重2克,为什么?
原因:
模具产品一出四,由于模具进胶不平衡造成其中一只产品啤塑饱满,密度大,出现重2克现象.
36.一台100吨液压曲肘机使用了三年,模具锁紧后,经常打不开。
原因:
是由于机器曲肘磨损,造成开模不平衡,所以模具锁紧后,会经常打不开.
37.一台7安士机使用了二年,出现射胶不稳定,一啤批峰一啤缺胶,换过油封和分胶头,系统压力也稳定,就不行。
原因:
由于螺杆磨损或损坏,造成回料不匀,所以会出现射胶不稳定.
38.一台150吨新机啤PP水口料半年,原来熔胶最快3秒,而现在要6秒。
原因:
由于螺杆磨损,造成回料慢.
39.一啤塑师父在调试一产品,出现缺胶,速度或压力升一点,产品没反应,再升一点就出批峰?
原因:
机器锁模机构磨损,造成锁模有间隙,所以会出现披锋.
40.一台机用了二年,啤货时炮筒中间温度偏高,关了电源也没用。
原因:
由于螺杆磨损变得粗糙,啤塑回料时磨擦产生热,使炮筒中间温度偏高.
41.某厂有新旧机十几台,油封经常漏油,换了一段时间又漏?
原因:
油温过高使油封易老化损坏,漏油;油缸芯子磨损,造成刮坏油封漏油.
42.油泵电机起动电路的讲解。
油泵电机起动是采用星三角起动
43.省电泵原理讲解。
省电泵即为变流量泵,当机器有动作时,压力油通过油阀油缸推动机械动作,再回到油箱,当机器没有动作时,压力油直接回到油箱。
44.电子线路板输入与输出的讲解。
由各个动作感应开关和电子尺等信号输入电子版,电脑通过运算后再输出给油阀,执行动作。
45.略
46.油封顽固性漏油的原因及预防。
油缸芯子磨损刮坏油封,造成顽固性漏油,保持油缸芯子干净,避免磨损预防刮坏油封造成漏油。
47.压力与流量线性对注塑工艺的影响。
压力与流量线性成比例,对注塑工艺的参数准确和稳定有着重要意义。
48.生产周期变慢的原因及改善措施。
生产周期变慢的原因主要是冷却时间延长,和螺杆因磨损使回料时间加长。
改善模具冷却效果,缩短冷却时间,更换磨损的螺杆,使回料时间缩短,加快生产周期。
49.熔胶时发出尖叫声的原因与处理方案。
熔胶时发出尖叫声是由于螺杆与料磨擦发出的或螺杆与炮筒磨擦发出的。
对螺杆抛光处理或电镀,使表面光滑减小磨擦;调整螺杆的中心度使它不与炮筒发生磨擦。
50.锁模平行度的检测与调整方法。
用四个百分表测定机器锁模时哥林柱的拉伸长度,看是否在允许公差内,来检测哥林柱锁模平等度。
然后调整哥林柱大螺母来调整锁模平行度。
(看另一本书《注塑机原理》)
51.哥林柱折断的原因与预防措施。
原因:
哥林柱折断的原因是由于锁模不平等造成的。
调整锁模平行度来预防哥林柱折断。
52.曲肘磨损的原因分析。
原因:
曲肘磨损的原因是,曲肘润滑不良造成的。
53.螺杆及分胶头折断的原因与预防。
原因:
螺杆及分胶头折断的原因,是由于塑胶还没达到熔化温度或料筒内有铁块卡死螺杆,在回料时,压力大造成扭断螺杆及分胶头。
54.冷却器容易漏水的分析。
原因:
由于冷却水的酸性或咸性过大,腐蚀冷却器的管道,造成冷却器易漏水。
55.氮气射胶的安装与应用。
原因:
氮气射胶是安装在射胶油路中的一个附加装置,在射胶时,氮气迅速澎胀挤压液压油,使液压油流速增快来达到快速射胶。
56.气体辅助设备的应用。
原因:
气体辅助是啤塑产品时,在产品中充气,使产品里面空的,可减少塑胶材料。
57.开环与闭环油路的比较。
原因:
开环与闭环油路的比较就是闭环油路在射嘴处多加了一个压力传感器,当设定参数与实际数据偏差时,压力传感器就会反馈信号给电脑,电脑就会修正偏差值,使设定值与实际值相等。
58.水平度对注塑机台的影响。
原因:
注塑机水平度对机器的开锁模平衡有重要意义,对机器的运行平稳起到保证作用。
59.模板(头板、二板、尾板)破裂的原因与预防措施。
原因:
模板破裂的原因主要是模板内存有内应力,在应力的作用下,模板破裂,模板在加工时,应及时消除应力,可以防止模板破裂。
60.使用工程塑料时,熔胶扭力不足和射胶压力不足的解决方案。
原因:
使用工程塑料时,熔胶扭力不足可能增大一级熔胶马达来解决,射胶压力不足可以采用减小螺杆直径来解决。
61.料管中段温度偏高的原因与解决方案。
原因:
料管中段温度偏高,主要是螺杆表面光滑度不够,螺杆与料相磨擦造成的。
应对螺杆表面抛光处理或电镀。
减少回料背压等措施。
62.液压曲肘式注塑机在生产中,锁模力下降及模具变松的原因及处理方案。
原因:
主要是曲肘磨损,锁模油缸油封老化造成的.更换曲肘铜套,更换锁模油缸油封。
63.使用润滑油和润滑脂(黄油)的比较。
原因:
润滑油和润滑脂都是润滑机器的机械活动,润滑油比润滑脂更容易渗透到机械活动部位。
而润滑脂可长时间附着在机械活部位。
64.电子尺与解码器的比较。
原因:
电子尺与解码器都是机器运动标尺,电子尺精度比解码器差,但比解码器稳定,不会变原点。
解码器比电子尺精度高,但没有电子尺稳定,易变原点。
65.油泵噪音变大的分析。
原因:
主要是油泵磨损,或油泵轴承磨损造成油泵噪音变大。
66.在生产正常的情况下,发热圈频烧的原因分析。
原因:
主要是发热圈接触不好,造成线头烧断,或发热圈电热丝不耐高温易氧化造成烧坏。
67.顶针油缸固定螺丝经常折断的原因与处理方案。
原因:
主要是固定螺丝强度不够,或固定螺丝易振松造成的。
更换强度高的固定螺丝,安装时要在固定螺丝上加止滑圈防止螺丝振松。
68.加装节能变频器对机器的影响分析。
原因:
加装节能变频器对机器的稳定有影响,使机器起压迟缓。
69.液压油变白变质的分析。
原因:
液压油变白是由于液压油内混有水造成变白变质。
70.熔胶传动轴易折断,轴承易损坏的原因。
原因:
主要是传动轴固定螺母松动造成的。
71.产品重量偏差过大的原因与处理方案。
原因:
产品重量变大是由于机器锁模没有锁紧,或锁模机构磨损造成的,射胶压力过大或背压过大都可以造成产品重量变大。
检查机器锁模机构是否磨损,调模是否到位。
减小射胶压力或背压。
72.模具经常打不开的原因与预防措施。
原因:
模具经常打不开,检查油路是否有卡死堵塞现象,检查锁模机构是否磨损,不平衡现象。
模具锁得太死,时间过长都会造成模具打不开。
73.射胶终点不稳定的原因分析。
原因:
主要是过胶头止流环磨损造成射胶终点不稳定。
74.产品在模腔内的推力计算。
原因:
产品的投影面积×单位面积的射胶压力=模腔内的推力
75.射胶压力计算与螺杆的选择。
原因:
射胶压力F=[/4×(D12-D22)×P×2]×[/4×d2]
(kgf)D1油缸内径(CM)D2活塞杆外径(CM)P系统压力
76.热塑性与热固性塑料最大特性是什么?
原因:
热塑性是受热达到材料的软化温度时,材料变成熔胶,冷却后固化成型,可反复逆转.
热固性是受热后固化成型,冷却后不变,不可逆转.
77.为什么塑料中要混有添加剂。
原因:
塑料中混有添加剂,是因为产品性能的需要,添加剂可以改善塑料中的许多性能和功用.
78.如何设定锁模力。
原因:
设定锁模力是根据产品的投影面积乘以塑胶材料的压力系数
参考(注塑机原理)
79.如何正确设定保压切换点。
原因:
正确保压切换点是产品射满到98%时转保压.
80.螺杆若以高速转动或较低速转动对螺杆内塑料引起何种变化。
原因:
螺杆高速转动,可以提高熔胶的塑化程度,由于高速转动大熔胶剪切力,使熔胶粘度下降,有利于成型.但磨擦热增大易使熔胶分解,温度失控.低速转动使熔胶塑化程度下降,但摩擦热减小,对塑胶性能有利.
81.正确与不正确背压使用对塑料引起何种变化?
原因:
螺杆在旋转,后退之阻力为背压,设此阻力之目的为使原料在被螺杆输送,压缩过程中更能紧密排除原料中之空气,原料密度会较高,射出之成品会更加稳定,原料因在料管内经过较多次的搅拌,所以融解热会增加对于成品混色不良,需要快速转换颜色或塑料及成品有气纹,使用背压效果良好。
因此背压太低成品易产生内部的气泡或表面的银纹,背压过高,原料易过热,料斗下料处结块,螺杆不退、周期延长、射嘴溢科。
背压控制有利用节流阀或调压阀控制两种。
82.注塑件形成毛边的原因和解决办法。
熔胶量太大
保压时间太长
射出转换保压动作太迟
流动性太好保压压力太
料管温度太高
模具密著性不
好;产生段差锁模力不足
模具钢性不良成品投影面积过大
模具合模线配合不良Flush
模具间有异物
原料中有水分等原料熔融不均一,部分过热
挥发性气体
润滑剂中含有挥缓衡量不足
发性成分
射出速度太射嘴温度太低
混入异种原料快或太慢
原料过热分解
排气不良
脱模剂太多射嘴太小
模具表面有水
或油附者Surfacehaze
浇口或浇到太小
模具温太高或太低
84.如何调较注塑工艺参数(温度、压力、速度、位置)?
温度
温度的测量和控制在注塑中是十分重要的。
虽然进行这些测量是相对地简单,但多数注塑机都没有足够的温度采点或线路。
在多数注塑机上,温度是由热电偶感应的。
一个热电偶基本上由两条不同的电线尾部相接而组成的。
如果一端比另一端热,将产生一个微小的电讯;越是加热,讯号越强。
温度的控制
热电偶也广泛应用作温度控制系统的感应器。
在控制仪器上,设定需要的温度,而感应器的显示将与设定点上产生的温度相比较。
在这最简单的系统中,当温度到达设定点时,就会关闭,温度下降后电源又重新开启。
这种系统称为开闭控制,因为它不是开就是关。
熔胶温度
熔胶温度是很重要的,所用的射料缸温度只是指导性。
熔胶温度可在射嘴处量度或使用空气喷射法来量度。
射料缸的温度设定取决于熔胶温度、螺杆转速、背压、射料量和注塑周期。
您如果没有加工某一特定级别塑料的经验,请从最低的设定开始。
为了便于控制,射料缸分了区,但不是所有都设定为相同温度。
如果运作时间长或在高温下操作,请将第一区的温度设定为较低的数值,这将防止塑料过早熔化和分流。
注塑开始前,确保液压油、料斗封闭器、模具和射料缸都处于正确温度下。
注塑压力
这是引起塑料流动的压力,可以用在射嘴或液压线上的传感器来测量。
它没有固定的数值,而模具填充越困难,注塑压力也增大,注塑线压力和注塑压力是有直接关系。
第一阶段压力和第二阶段压力
在注塑周期的填充阶段中,可能需要采用高射压,以维持注塑速度于要求水平。
模具经填充后便不再需要高压力。
不过在注塑一些半结晶性热塑性塑料(如PA及POM)时,由于压力骤变,会使结构恶化,所以有时无须使用次阶段压力。
锁模压力
为了对抗注射压力,必须使用锁模压力,不要自动地选择可供使用的最大数值,而要考虑投影面积,计算一个适合的数值。
注塑件的投影面积,是从锁模力的应用方向看到的最大面积。
对大多数注塑情况来说,它约为每平方英寸2吨,或每平方米31兆牛顿。
然而这只是个低数值,而且应当作为一个很粗略的经验值,因为,一旦注塑件有任何的深度,那么侧壁便必须考虑。
背压
这是螺杆后退前所须要产生及超越的压力,采用高背压虽有利于色料散布均匀及塑料熔化,但却同时延长了中螺杆回位时间,减低填充塑料所含纤维的长度,并增加了注塑机的应力;故背压越低越好,在任何情况下都不能超过注塑机注塑压力(最高定额)的20%。
射嘴压力
射嘴压力是射嘴里面的压力。
它大约就是引起塑料流动的压力。
它没有固定的数值,而是随模具填充的难度加大而增高。
射嘴压力、线压力和注射压力之间有直接的关系。
在螺旋式注塑机上,射嘴压力大约比注射压力少大约百分之十左右。
而在活塞式注塑机时压力损失可达到百分之十左右。
而在活塞式注塑机时压力损失可达到百分之五十。
注塑速度
这是指螺杆作为冲头时,模具的填充速度。
注塑薄壁制品时,必须采用高射速,以便于熔胶未凝固时完全填充模具,生产较为光滑的表面。
填充时使用一系列程序化的射速,避免产生喷射或困气等缺陷。
注射可在开环式或闭环式控制系统下进行。
无论采用那种注射速度,都必须将速度值连同注射时间记录于记录表上,注射时间指模具达到预定的首阶段射压所须的时间,乃螺杆推进时间的一部分。
模具排气
由于快速填充模具的缘故,模具必须让气体排出,多数情况下这气体只是模腔中的空气。
如果空气不能排出,它会被熔融压缩,使温度上升将引起塑料燃烧。
排气位须设于夹水纹及最终注塑部份附近。
一般排气位为6至13毫米宽,0.01至0.03毫米深的槽,通常设于其中一个半模的分模面处。
保压
在注塑周期的填充阶段中,可能需要采用高射压,以维持注塑速度于要求的水平。
模具填充后,就进入保持阶段,这时螺杆(起冲压器作用)推进额外的塑料以补偿塑料收缩。
这可在较低或同样高的压力下完成。
通常若首阶段采用高压,次阶段便采用较低压力。
不过,在注塑一些半结晶性热塑性塑料(如PA及POM时),由于压力骤变,会使结晶体结构恶化,所以有时无需使用次阶段压力。
再生塑料的使用
许多注塑机使用新塑料和回用再生塑料(即通常所说的水口料)的混合物。
令人惊奇的是,使用再生塑料可以改善注塑机的表现,即它的使用产生了更一致的注塑件,但值得注意的是,再生料在使用前最好要先除去粉尘,以免引起塑料进料量的差异而导致注塑件颜色分布偏差。
再生塑料的确切使用比例要根据实验的数来确定,这个数据必须是在不影响注塑件的物理性质的前提下得来的,一般的经验数值是在15%至25%之间。
品质控制
注塑件最终的特点(重量和大小)与生产条件:
如垫料大小、注塑压力和流量之间在紧密发联系。
这表示在许多情况下,有可能在没有真正对注塑件进行任何测量之前就可以检查到注塑件是否令人满意。
在每次注塑中,对选择的参数进行量并比较设定或储的数值。
只要测量值在预先选择的范围内,控制系统就判定该注塑件可以接受。
如果测量超出设定的限制,该注塑件将会被废弃,或者,如果只是超出了一点,就要停下来等有资格人士第二次检测。
现在的注塑机配备了录影机、电脑系统,这样在注塑时,每一个注塑件都与储存的要求映像相比较。
每一个注塑件都要和标准注塑件的尺寸和视觉上的缺陷相比较。
记录注塑条件
永远不可忘记注塑的目的是在特定时间内按指定的成本生产符合品质要求的注塑件。
要做到这点,基本是做准确的记录。
在许多注塑机上按钮就可以做到这点。
若没有按钮,应该完成适当的记录单并保留注塑件样本,作为将来的参考。
停机
最重要的是采取一个合理的停机过程,这样便可节省大量时间和金钱。
如果您要停机,正例如燃烧塑料,那么便没有需要泻出塑料,您可能会节省完全关闭和清洁注塑机的费用。
暂时的停顿
若注塑机暂停运作,更须多次将余胶喷清或让别的塑料来通过注塑机清洗射料缸的剩余塑料。
遇上塑料退色,喷清的次数就要增加。
进行办轻微修理时,射料缸的加热器须调校至最低值,以尽量减低热分解的可能。
在更现代化的注塑机上,该过程可能会自动启动。
整晚的停顿
注塑热塑性塑料(如PS)前,如已预先停机一晚,就只须关闭底部的滑板及射料缸加热器,将射料缸喷射干净。
射嘴完全清洁后,尽量把射料缸高度冷却,等注塑机冷却后关闭所有装备,注塑机便可充分准备好再次加热。
热敏感性塑料
若塑料在注塑机内分解可燃烧,最终会变色,使注塑件变成废件。
遇此情形,便须完全关闭注塑机,喷清干净。
预防方法是用一种热稳定性较高的塑料喷清遇热敏感的塑料,这样便能抵常驻随时后再加热。
为了应付塑料氧化的问题,操作者可以在射料缸中充满塑料,如PE。
塑胶制品成型时变形重要原因:
(1)成品肉厚不同,且差距过大,收缩率大小不同而产生。
(2)射压传达不均匀,因密度高低而产生(浇口位置及型式)
(3)模温分布不均匀,冷却系统近浇口处要较冷,反之。
(4)分子配向差距过大。
(5)后结晶(结晶性塑胶)。
(6)内应力过高。
锁模压力:
锁模压力必须大于塑料射入模内之总压力,若过低塑料即可能由分模面处溢出。
压力过高又会损耗机器,模具及浪费电力。
故适当的锁模力是以成品射入模内分模面不出毛边为原则。
螺杆功能:
螺杆对原料有输送、混练、排气、除湿、熔解及计量等功能,塑胶原料熔融时所需之热量有百分之七十是来自螺杆旋转时发生之磨擦热,有百分之三十是来自电热片补充之热量。
低黏度、小螺杆、熔胶转速要加快。
高黏度、大螺杆熔胶转速要放慢。
复合材料需放慢转速。
射出速度:
射出速度之快慢,主要决定原料在模具之浇道中及模穴内流动之状况。
速度太快会产生毛头过饱、烧
焦及黏模,太慢易造成短射缩水,结合线明显,须依实际需要分段调整。
射出压力:
射出压力于射出速度有部分共同之影响,都是决定在模具内原料如何能均匀的,彻底的适量的流满各
角落,压力太低会产生短射缩水,压力太高会产生毛边、黏模、内应力残留日后变形、破裂、易损坏模具,机台等。
原料温度:
成型时使原料恰当熔融所需之热量及温