东风8B型内燃机车段修规程.docx
《东风8B型内燃机车段修规程.docx》由会员分享,可在线阅读,更多相关《东风8B型内燃机车段修规程.docx(81页珍藏版)》请在冰豆网上搜索。
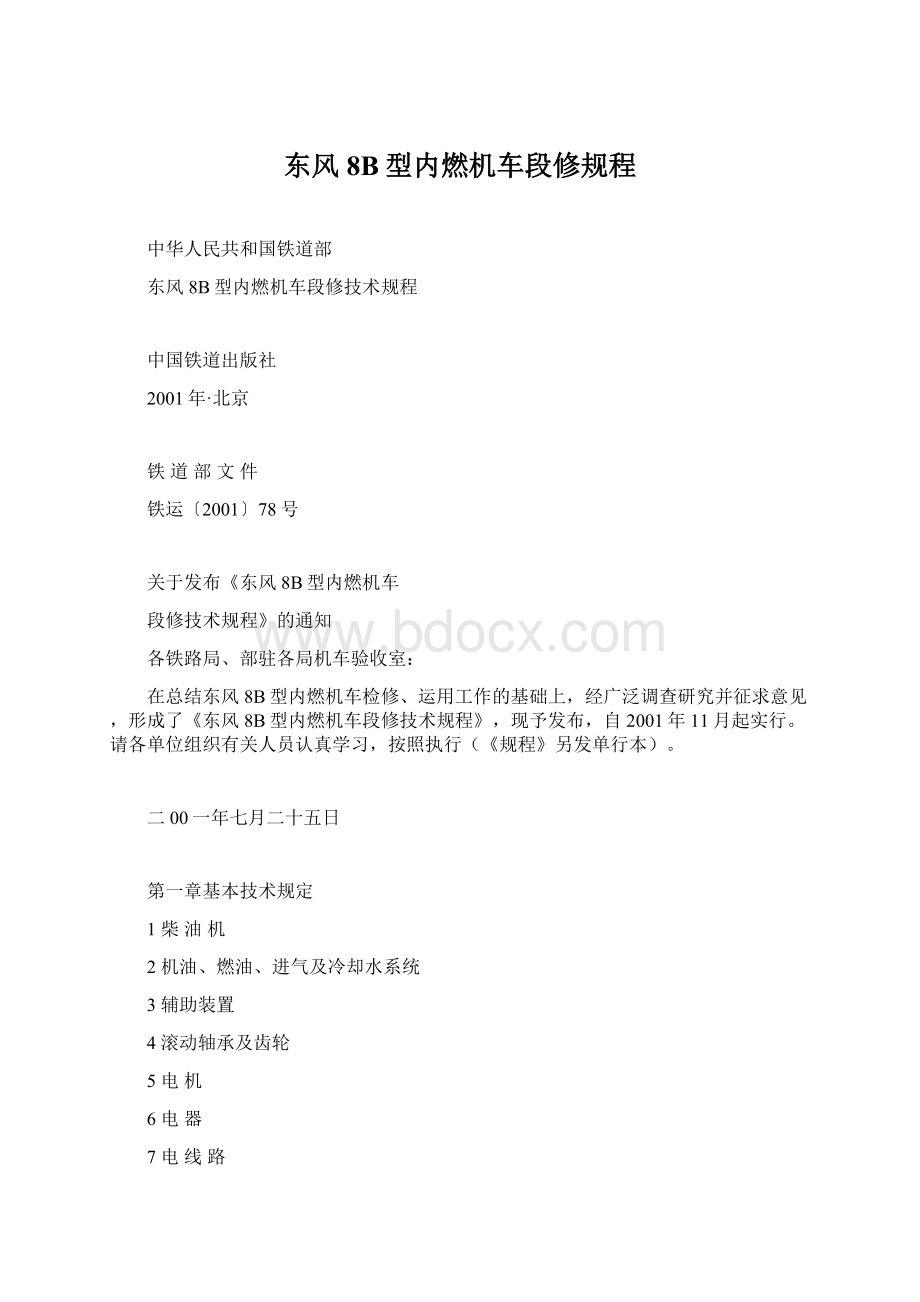
东风8B型内燃机车段修规程
中华人民共和国铁道部
东风8B型内燃机车段修技术规程
中国铁道出版社
2001年·北京
铁道部文件
铁运〔2001〕78号
关于发布《东风8B型内燃机车
段修技术规程》的通知
各铁路局、部驻各局机车验收室:
在总结东风8B型内燃机车检修、运用工作的基础上,经广泛调查研究并征求意见,形成了《东风8B型内燃机车段修技术规程》,现予发布,自2001年11月起实行。
请各单位组织有关人员认真学习,按照执行(《规程》另发单行本)。
二00一年七月二十五日
第一章基本技术规定
1柴油机
2机油、燃油、进气及冷却水系统
3辅助装置
4滚动轴承及齿轮
5电机
6电器
7电线路
8电阻制动装置
9蓄电池
10空调机组电器检修
11仪表
12运行监控记录装置
13车体及走行部
14空气压缩机及空气制动装置
15机车总装、负载试验及试运
16其他
第二章段修限度
1限度表使用说明
2段修限度表
第三章段修零件探伤范围
第一章基本技术规定
1柴油机
1.1机体及油底壳检修要求
1.1.1清洗、检查机体及油底壳状态。
1.1.2机体及主轴承盖的所有安装平面须平整,不许碰伤。
1.1.3水平螺栓、主轴承盖、主轴承座咬口面R圆角部分不许裂损,主轴承螺栓与螺母、气缸盖螺栓与螺母不许断扣、毛刺及碰伤,当有上述缺陷时,须拆下探伤、修复或报废。
1.1.4用980N·m紧固力矩检查栽入机体的主轴承螺栓及气缸盖螺栓,不许松缓。
1.1.5当水平螺栓未拧紧前,机体与轴承盖配合侧面用0.05mm塞尺检查,不许塞入;用0.03mm塞尺检查,不许全部贯通。
1.1.6机体主轴承止推面对主轴承轴线的垂直度允差为0.05mm。
1.1.7凸轮轴孔铜套不许拉伤。
1.1.8主轴承螺栓伸长量为0.65~0.75mm;水平螺栓紧固力矩为500N·m。
1.1.9主机油道须冲洗干净,焊修后须进行1.0MPa水压试验,保持10min无泄漏。
1.1.10油底壳不许裂损,焊修后须进行渗水试验,保持20min不许泄漏。
1.1.11油底壳与机体须配对组装,自由端须平齐,输出端须低于机体端面,但不超过0.1mm。
1.1.12清洗油底壳安全阀,进行调压试验:
当机油温度为70~80℃、压力为0.8
MPa时须动作。
1.2连接箱检修要求
1.2.1清洁无油垢,各部不许裂损(裂纹允许清除修复)。
1.2.2连接箱与机体须配对使用,与机体及同步主发电机的结合面须良好,整修碰伤、毛刺等缺陷。
1.2.3连接箱与机体的结合面紧固后须密贴,用0.05mm塞尺检查不许塞入,但允许长度不超过两个螺栓间距的局部间隙存在。
1.2.4焊修后或更换连接箱时须检查:
1.2.4.1连接箱直径Φ1544mm定位孔对主轴承孔的同轴度允差为Φ0.20mm。
1.2.4.2连接箱安装同步主发电机的平面,对机体主轴承孔公共轴线的端面跳动允差为0.4mm,且不许用偏垫调整。
1.3曲轴及其附件检修要求
1.3.1曲轴不许裂损,允许消除局部发纹。
各轴颈及其过渡圆角表面、止推面不许烧伤和碰伤。
1.3.2清洗油道,重新组装油堵、螺堵须进行0.7MPa油压试验,保持5min不许泄漏。
1.3.3目视检查平衡块螺钉不许松弛。
1.3.4卷簧减振器不许泄漏,簧片不许裂损。
更换簧片时,弹簧组须整组更换,且弹力差不许大于98N。
减振器与曲轴装配时,压装行程为10~13mm,压装后与齿轮端面的间隙须小于0.03mm,弹簧组座孔及限制块不许擦伤。
1.3.5分解、清洗大圆薄板联轴节,各部件不许裂损和碰伤。
M30、M20螺栓的紧固力矩分别为1570N·m、315N·m。
1.4轴瓦检修要求
1.4.1轴瓦须有胀量。
不许剥离、龟裂、脱壳、烧损、严重腐蚀和拉伤。
1.4.2须使用相应等级轴颈的等级轴瓦。
1.4.3轴瓦选配
1.4.3.1新轴瓦高出度(按TB/T2958-1999的规定,在检验胎具内用检验高出度用的比较轴瓦作换算,下略)须符合表1-1的规定。
表1-1主轴瓦、连杆瓦施加压力及高出度
名称
轴瓦厚度(mm)
施加压力(N)
高出度(mm)
双边加载(aB1+aB2)
单边加载(aA)
主轴瓦
7.357.39
44130
0.170.21
0.180.22
连杆瓦
4.874.90
27460
0.130.17
0.140.18
1.4.3.2旧轴瓦高出度允许较表1-1下限减少0.02mm。
1.4.3.3轴瓦的合口面须平行,在瓦口全长内平行度为0.03mm。
1.4.3.4同一瓦孔内两片轴瓦厚度差不大于0.030mm;受力主轴瓦厚度的计算阶梯度相邻不大于0.035mm,全长不大于0.080mm。
1.4.4轴瓦组装
1.4.4.1瓦背与瓦座孔须密贴,轴瓦定位舌背不许顶住主轴承座和连杆大端孔的定位舌槽。
1.4.4.2止推挡圈与曲轴止推面须紧密贴靠,允许不大于0.05mm的局部间隙,但沿圆周方向累计长度不许大于1/4圆周,止推挡圈合口总间隙须为0.50~0.80mm。
1.4.4.3主轴瓦端面与主轴承盖、座的不平齐度小于0.5mm,连杆瓦端面与连杆体、盖的不平齐度小于0.3mm。
1.4.4.4使用旧瓦时须与原轴颈、原机体和原连杆配对组装。
1.5活塞检修要求
1.5.1活塞头与裙不许烧损,打磨消除轻微碰伤的棱角。
1.5.2分解活塞头与裙,清除油垢、积炭,更新橡胶密封圈及螺母弹性卡销。
1.5.3探伤检查活塞头、裙及连接螺柱、螺母、弹性套,不许裂损。
1.5.4用专用螺纹通、止环规检查连接螺柱外螺纹精度,用专用螺纹通、止塞规检查活塞头内螺纹精度,均须符合要求。
1.5.5检查活塞头、裙支承面高度须符合表1-2要求。
表1-2活塞头、裙支承面高度单位:
mm
活塞头支承面高度
活塞裙支承面高度
1.5.6更新活塞环。
1.5.7活塞环槽侧面拉伤或磨损超限,允许将环槽宽度增加一个修理等级(0.5mm),并配以相应等级的活塞环。
当活塞头更新时,活塞头连接螺柱须同时更新。
1.5.8活塞销不许裂损,活塞销堵不许裂损及松动,活塞销油腔须进行0.4MPa的油压试验,保持5min不许泄漏。
1.5.9活塞连接螺柱涂上二硫化钼并以39N.m力矩紧固,螺母以39N.m及58~78N.m力矩分两次对角均匀紧固。
1.5.10组装后,活塞头与裙在外径结合面处的组装间隙须为0.03~0.15mm。
1.5.11同台柴油机各活塞组质量差不许大于0.25kg。
1.6连杆检修要求
1.6.1连杆体及盖不许裂损,小端衬套不许松动,更换衬套时过盈量须为0.06~0.13mm。
1.6.2在距连杆中心线两侧各200mm处测量连杆大、小端孔(小端带铜套)轴线的弯曲度为0.15mm,扭曲度为0.20mm。
超限时,在保证衬套尺寸及配合限度的前提下,允许刮修衬套。
1.6.3连杆螺钉不许裂损,其螺纹不许锈蚀、损坏或严重磨损。
1.6.4校核连杆螺钉紧固伸长量
1.6.4.1以49N·m扭矩拧紧螺钉,以此作为0°。
1.6.4.2用转角法拧紧连杆螺钉,长螺钉转角为128°~130°,短螺钉转角为105°~107°。
1.6.4.3重新做好刻线记号。
1.6.5同台柴油机须使用同种连杆,各连杆组质量差不许超过0.40kg。
其中连杆大头部分允差为0.25kg,小头部分允差为0.15kg。
1.7活塞连杆组装要求
1.7.1同台柴油机活塞连杆组质量差不许大于0.40kg。
1.7.2各零部件组装正确,油路畅通,连杆能绕轴自由摆动。
1.7.3连杆盖及连杆螺钉的支承面不许拉伤,其结合面用0.03mm塞尺不许塞入。
1.7.4活塞环在最后总装前装到活塞上,活塞环在环槽内转动须灵活。
各活塞环开口位置互相错开120°,并不许对准销孔两端。
1.8气缸盖检修要求
1.8.1清洗积炭、水垢,保持油路、水路畅通。
1.8.2更新喷油器套管密封圈、垫,套管锁紧母紧固扭矩为588~637N.m。
1.8.3气缸盖底部缸垫密封面须平整,允许切修,但此面与气缸盖底面的距离不大于10.5mm。
1.8.4气缸盖、气门座不许裂损,气门座、气门导管、横臂导杆、摇臂球头、横臂压头、横臂压块、工艺堵不许松缓,气门座口密封环带宽度不大于5.6mm,更换气门座与气门导管时,装配过盈量分别为0.108~0.150mm和0.010~0.025mm。
1.8.5气门不许裂损、腐蚀、碰伤,气门杆不许烧伤、拉伤,气门阀口面对杆身轴线的斜向圆跳动为0.05mm,杆身直线度为0.05mm,气门阀盘圆柱部厚度:
进气门不小于7mm,排气门不小于4mm。
1.8.6气缸盖须进行0.5MPa压力试验,保持5min不许泄漏。
1.8.7气门摇臂、横臂、摇臂轴座、摇臂轴、调整螺钉、摇臂球头、摇臂压头、横臂压块、气门弹簧不许裂损,油路须畅通。
气门内外弹簧及横臂弹簧不许变形、裂损,气门锁夹须无严重磨损,并须配对使用。
1.8.8气缸盖组装时,气门与气门座须配研,用煤油进行密封性试验,保持1min不许泄漏。
横臂须水平,其调整螺钉、压销与气门杆的端部接触须良好。
组装后配气机构动作须灵活。
1.8.9更新全部密封圈。
1.9气缸套检修要求
1.9.1清洗,去除积炭和水垢。
1.9.2不许裂损,内表面不许严重拉伤,外表面穴蚀深度不大于6mm。
1.9.3更新水封圈。
1.10凸轮轴及推杆、挺柱检修要求
1.10.1凸轮轴不许弯曲、裂损,凸轮及轴颈工作表面允许有少量分散麻点,但不许剥离、偏磨、凹坑及烧伤,轴颈不许严重拉伤。
1.10.2凸轮型面磨损大于0.15mm时,允许成型磨修,磨修后的表面硬度不低于HRC57,升程曲线须符合原设计要求,但配气凸轮基圆半径不小于51.5mm,供油凸轮基圆半径不小于47.5mm。
1.10.3更换凸轮轴单节时,凸轮轴各位轴颈对1、5、9位轴颈的公共轴线圆跳动为0.09mm。
各凸轮相对于第一位同名凸轮(或第9位同名凸轮)的分度允差为35ˊ。
1.10.4凸轮轴与齿轮的定位销孔允许扩大,最大孔径为Φ12mm;各节凸轮轴之间的定位销孔允许扩大,最大孔径为Φ14mm。
1.10.5挺柱头不许松缓,挺柱头和滚轮不许严重压痕和麻点,挺柱、滚轮轴、滚轮及衬套不许严重拉伤和烧伤。
推杆头不许松缓,推杆不许弯曲(但允许冷校直)、裂损,球窝不许拉伤和凹坑。
1.10.6更新密封圈。
1.11进、排气系统检修要求
1.11.1清除积炭、油垢,各零部件不许裂损和变形,排气管裂纹焊修后须进行0.5MPa的水压试验,保持5min不许泄漏。
1.11.2排气管路隔热保护层须完好。
1.11.3更新各垫片及橡胶圈。
1.12增压器检修要求
1.12.1VTC254-13、VTC254-13G增压器
1.12.1.1解体,清除积炭、油污。
1.12.1.2压气机的导风轮、叶轮、扩压器叶片不许裂损、严重击伤和卷边。
导风轮叶片允许有沿直径方向长度不大于5mm、顺叶片方向深度不大于1mm的撞痕与卷边;扩压器叶片允许有深度不大于1mm的撞痕。
1.12.1.3涡轮叶片不许裂损,叶片进气边允许有2处深度小于1mm、长度小于5mm的撞痕和卷边。
1.12.1.4喷嘴环内、外圈不许裂损;喷嘴环叶片允许有深度不大于1mm的撞痕、轻微的卷边与变形,叶片变形不许校正,喷嘴环叶片不许裂损,喷嘴环的出口面积与环上实测标定值允差为1%。
1.12.1.5修整圆滑上述各项允许的撞痕、卷边与变形。
1.12.1.6主轴不许裂损,各轴颈表面不许拉伤、偏磨、烧损与变形,各轴颈的径向跳动不大于0.02mm。
1.12.1.7压气机端轴承总成、涡轮端轴承总成及环形止推轴承状态须良好。
1.12.1.8喷嘴环镶套不许裂损。
1.12.1.9燃气排气壳水腔须进行0.5MPa的水压试验,保持5min不许泄漏。
1.12.1.10涡轮叶片与涡轮盘装配时严禁用铁锤锤铆,锁紧片只准弯曲一次;装配后,叶片顶部沿圆周方向晃动量为0.25~2.50mm,涡轮叶根的轴向窜动量不大于0.10mm。
1.12.1.11更新活塞环、O型密封圈、垫片及垫圈。
1.12.1.12转子组更换零件后须进行动平衡试验:
压气机叶轮组(压气机叶轮、导风轮、衬套)不平衡量不大于2.5g.cm;叶片轴(涡轮、主轴)不平衡量不大于1.5g.cm(允许压导轮组装到位后进行转子总成动平衡试验,不平衡量不大于4.0g.cm,转子组重新组装时,须恢复原组装定位刻线)。
1.12.1.13增压器组装后,各部间隙须符合限度规定,用手轻轻拨动转子,转子转动须灵活、无碰擦与异声,检查导风轮轮廓外径的径向跳动量须不大于0.04mm。
当柴油机在油、水温度不低于55℃时,以最低稳定转速运转5min以上停机后(喷油泵齿条回停油位起),转子惰转时间不少于30s。
1.12.1.14同台柴油机须配套使用同型号的增压器。
1.12.1.15机车小辅修时须检查转子转动应灵活。
1.12.2ZN310-A4、ZN310-LSA4增压器
1.12.2.1解体,清除积炭、油污。
1.12.2.2压气机的导风轮、叶轮、扩压器叶片不许裂损、严重击伤和卷边。
导风轮叶片允许有沿直径方向长度不大于2mm、顺叶片方向深度不大于1mm的撞痕与卷边;扩压器叶片允许有深度不大于1mm的撞痕。
1.12.2.3涡轮叶片不许裂损,叶片进气边允许有2处深度小于1mm、长度小于2mm、间距大于3mm的撞痕和卷边。
1.12.2.4喷嘴环内、外圈不许裂损;喷嘴环叶片允许有深度不大于1mm的撞痕、轻微的卷边与变形,叶片变形不许校正,喷嘴环叶片不许裂损,喷嘴环的出口面积与环上实测标定值允差为1%。
1.12.2.5修整圆滑上述各项允许的撞痕、卷边与变形。
1.12.2.6主轴不许裂损,各轴颈表面不许拉伤、偏磨、烧损与变形,各轴颈的径向跳动不大于0.015mm。
1.12.2.7压气机端轴承总成、涡轮端轴承总成及环形止推轴承状态须良好。
1.12.2.8喷嘴环镶套不许裂损。
1.12.2.9燃气排气壳水腔须进行0.5MPa的水压试验,保持5min不许泄漏。
1.12.2.10涡轮叶片与涡轮盘装配时严禁用铁锤锤铆,锁紧片只准弯曲一次;装配后,叶片顶部沿圆周方向晃动量为0.04~0.50mm,涡轮叶根的轴向窜动量:
A4型不大于0.20mm;LSA4型不大于0.10mm。
1.12.2.11更新铸铁环、石墨环、O型橡胶密封圈、垫片及垫圈。
检查铸铁环不许翘曲,其开口间隙须为7.2~8.6mm,闭口间隙须为0.20~0.30mm。
1.12.2.12更换涡轮叶片时,叶片质量差不大于3g,配组叶片质量差不大于0.1g。
1.12.2.13转子组更换零件后,须将压导轮组装到位进行转子总成动平衡试验,总不平衡量≤3g.cm(压气机端不平衡量≤1.5g.cm;涡轮端不平衡量≤1.5g.cm),转子组重新组装时,须恢复原组装定位刻线。
1.12.2.14增压器组装后,各部间隙须符合限度规定,用手轻轻拨动转子,转子转动须灵活、无碰擦与异声,检查导风轮轮廓外径的径向跳动量须不大于0.04mm。
当柴油机在油、水温度不低于55℃时,以最低稳定转速运转5min以上停机后(喷油泵齿条回停油位起),转子惰转时间不少于30s。
1.12.2.15同台柴油机须配套使用同型号的增压器。
1.12.2.16机车小辅修时须检查转子转动应灵活。
1.13喷油泵及下体检修要求
1.13.1解体、清洗,严禁碰撞。
各零件不许裂损,柱塞偶件不许拉伤、剥离,齿杆不许弯曲和拉伤,导套压痕深度不大于0.13mm。
1.13.2出油阀行程须为5.4~5.7mm,出油阀Φ14mm和Φ18mm处的总间隙须为0.008~0.015mm和0.08~0.12mm,弹簧自由高度见表1-3。
表1-3弹簧自由高度单位:
mm
弹簧名称
出油阀弹簧
柱塞弹簧
喷油器调压弹簧
自由高度
43.61.0
104.01.5
47.01
1.13.3出油阀偶件须进行0.4~0.5MPa的风压试验,保持15s不许泄漏(至少检查2个不同的相对位置)。
1.13.4更新密封橡胶圈。
1.13.5柱塞偶件密封性试验:
试验台须用标准柱塞偶件定期校核,试验油为柴油和机油的混合油,其20℃时的运动粘度为(1.02~1.07)10-5m2/s,试验油温为18~22℃,试验时柱塞与柱塞套的相对位置须使柱塞的有效行程为7.2mm,将试验油以(22.00.3)MPa压力充入柱塞顶部,偶件密封时间为8~30s(试验次数不许少于2次)。
1.13.6喷油泵组装后,拉动调节齿杆须灵活,并按表1-4进行油量调整试验(更换偶件时须先做30min以上的磨合试验)。
试验中,齿杆处燃油滴漏不超过2滴/5min。
表1-4喷油泵供油量试验要求
试验工况
齿条位置刻线
凸轮轴转速(r/min)
供油次数
供油量(mL)
备注
大油量
13
500±5
200
4205
小油量
4
200±5
200
110~135
同台柴油机各泵油量差不大于8mL
停油位
0
200±5
200
0
注:
试验台供油量须用标准喷油泵及标准喷油器定期校核。
1.13.7喷油泵组装后须重测B尺寸,并刻写在喷油泵体方法兰的外侧面上。
1.13.8喷油泵下体各零件不许裂损及拉伤,滚轮不许腐蚀及剥离。
1.14喷油器检修要求
1.14.1解体、清洗,严禁碰撞,各零件不许裂损,针阀偶件不许拉伤、剥离及偏磨。
1.14.2调压弹簧须符合要求,其自由高度见表1-3。
1.14.3阀座磨修深度不大于0.1mm。
1.14.4针阀行程为(0.6±0.03)mm。
1.14.5喷油器组装后须作性能试验
1.14.5.1针阀偶件颈部密封性试验:
试验台须用标准针阀偶件定期校核,试验油为柴油和机油的混合油,其20℃时运动粘度为(1.02~1.07)10-5m2/s,试验油温为18~22℃,喷射压力调整到34.3MPa后,油压从32.4MPa降到27.4MPa所需时间为20~50s。
针阀体密封端面和喷孔处不许滴油(连续试验3次)。
1.14.5.2雾化试验:
喷油压力为25.5
MPa,以每分钟50~60次速度喷射,雾化须良好,声音短促、清脆,喷孔口不许漏油和滴油。
1.14.5.3偶件座面密封性试验:
当喷油器喷油压力调整为25.5
MPa,以30次/min的速度连续喷射30次后,喷油器头部不许滴漏。
1.14.6更新密封圈。
1.14.7喷油器在运行中须有回油量,但不许超过35滴/min。
1.15调速器检修要求
1.15.1D型联合调节器
1.15.1.1解体,清洗,更换过限和破损零件及垫片、橡胶件、油封。
1.15.1.2配对更换飞铁时,飞铁质量允差为0.1g,其内外摆动的幅度须保证柱塞全行程为(6.2±0.1)mm。
1.15.1.3滑阀在中间位置时,滑阀活塞与套座第5排孔的上边缘须有(1.6±0.1)mm的重叠,滑阀上、下行程均为(3.2±0.1)mm。
1.15.1.4伺服马达杆的行程为(25.0±0.5)mm。
1.15.1.5各连接杠杆动作须灵活、无卡滞。
1.15.1.6联合调节器组装后须进行磨合试验和性能试验:
(a)体的各结合面及油封无泄漏。
(b)油温为55~60℃,储油室工作油压在所有工况下均不低于0.65MPa。
(c)最低转速(400r/min)和标定转速(1000r/min)时转速允差为10r/min。
(d)功率伺服器在300°转角范围内转动灵活,从最大励磁位到最小励磁位的电阻变化为0~493Ω。
变阻器电刷接触须良好,各电阻不许烧损及断路或短路。
(e)步进电动机转动须灵活,扭矩不小于0.5N.m。
1.15.2302D-Z型调速器
1.15.2.1解体、清洗、更换过限和破损零部件及垫片、橡胶件、油封。
1.15.2.2各滑动、转动表面无拉伤、卡滞,柱塞在倾斜45°位置时须能自由滑下,各连接杠杆、销钉连接处作用灵活可靠,无卡滞。
1.15.2.3各弹簧的弹力须符合设计要求。
1.15.2.4飞铁块质量允差为3g,配对更换飞铁时,飞铁质量允差须为1.5g。
1.15.2.5电器元件须良好。
1.15.2.6输出轴最大转角须为46°。
1.15.2.7在垂直位时,两飞铁脚高度差不能大于0.10mm。
其内外摆动的幅度须保证柱塞全行程为6.2±0.1mm。
1.15.2.8当飞铁全开(柱塞在上面位置)及飞铁合拢(柱塞在下面位置)时,柱塞5mm的控制台与滑阀装配Φ5孔的开启度须相等(可用螺母调整)。
1.15.2.9调速器组装后须进行磨合试验和性能试验
(a)调速器须能顺利起、停机。
(b)最低转速(400r/min)和标定转速(1000r/min)时转速允差为10r/min。
工况变换时,伺服马达杆波动不能超过三次,稳定时间不能超过10s。
(c)在稳定工况下,调速器转速波动不许超过6r/min。
在标定转速时,伺服马达杆抖动量不许超过0.1mm,在最低转速时,伺服马达杆拉动量不许超过0.2mm。
功率伺服器在300°转角内转动须灵活,从最大励磁位到最小励磁位电阻变化值为0~487Ω。
当油温不低于50℃时,恒压室工作油压在所有工况下不低于0.88MPa。
(d)步进电动机转动须灵活,扭矩不小于0.5N.m。
(e)停车电磁阀在不低于30V直流电压时须能吸合,吸力不许低于50N,在70±5V直流电压时,须能在120℃正常工作,吸力不得低于100N。
(f)在试验过程中,各部分不许渗油。
1.15.3调速器装机后的试验要求
1.15.3.1油温达到正常时,复查柴油机转速,在最低转速(400r/min)和标定转速(1000r/min)时,允差为10r/min。
1.15.3.2变换控制手柄位置时,转速波动不超过3次,稳定时间不大于10s。
1.15.3.3手柄由最低转速升至标定转速时,升速时间为16~18s。
由标定转速突降至最低转速时,降速时间为18~20s。
1.16柴油机控制装置检修要求
1.16.1控制装置各拉杆不许弯曲,安装正确,动作灵活。
左右拉杆轴向总间隙不大于0.5mm,与喷油泵齿条连接后在弹性拉杆处检查整个拉杆系统须灵活,总阻力须小于118N。
1.16.2左右转臂与拉杆垂直时,各泵齿条刻线均须在额定供油量的中间位(即第7刻线),各喷油泵齿条刻线差须小于0.7刻线。
1.16.3当喷油泵齿条刻线在-2格以内,调速器动力活塞处在下极限位置时,安装输出臂和弹性拉杆,扳动输出臂至最大转角时,须使喷油泵齿条行程大于14刻线。
1.16.4根据柴油机最大运用功率封定供油止档。
1.16.5当柴油机转速达到1120~1150r/min时,超速停车装置须动作,喷油泵齿条须回到停油位。
1.16.6超速停车装置各零件不许裂损,组装后飞锤行程为6.0~6.5mm,摇臂滚轮与飞锤座间隙为0.7~1.0mm,摇臂偏心尺寸为0.