第10章植物油脂生产技术.docx
《第10章植物油脂生产技术.docx》由会员分享,可在线阅读,更多相关《第10章植物油脂生产技术.docx(30页珍藏版)》请在冰豆网上搜索。
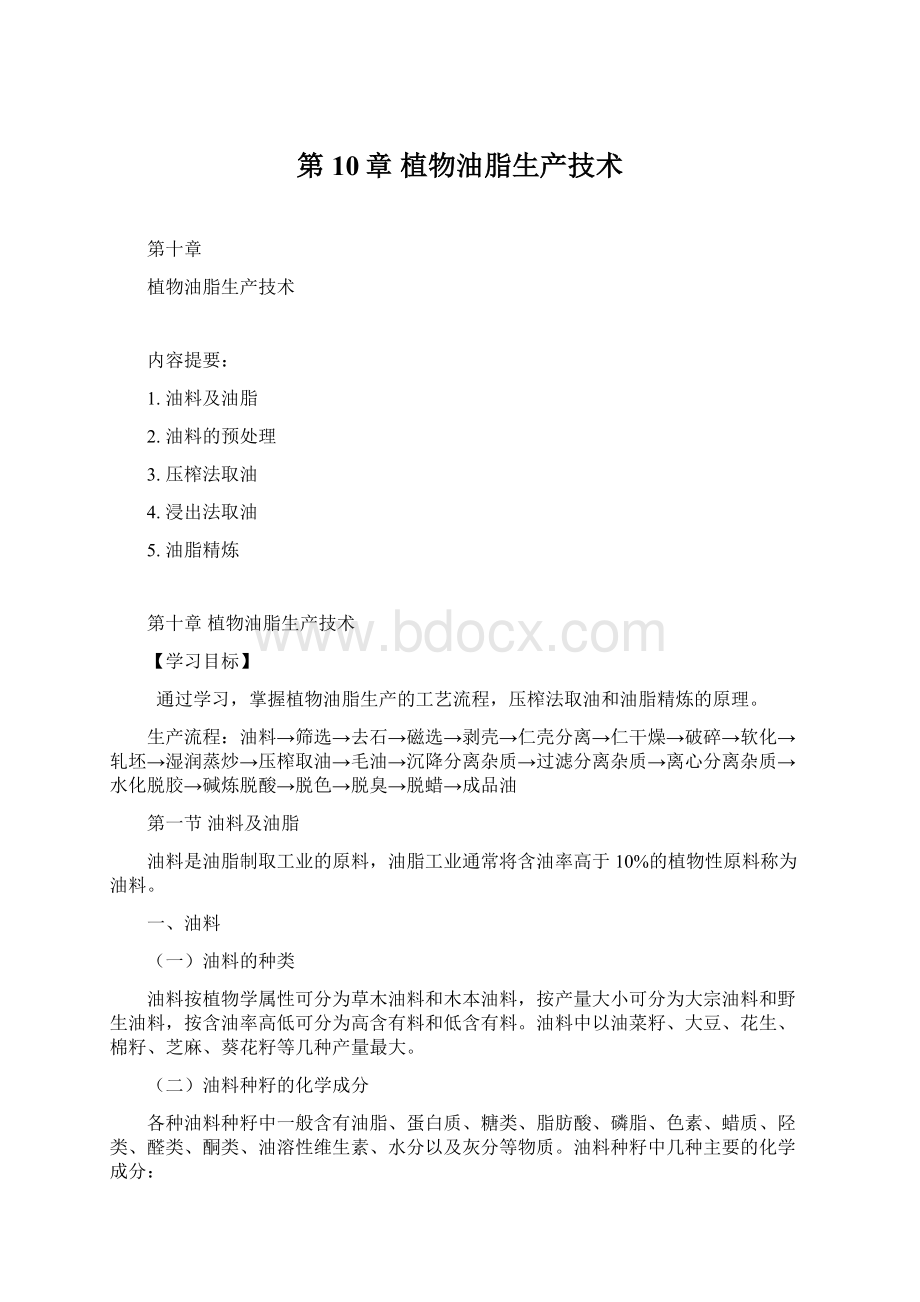
第10章植物油脂生产技术
第十章
植物油脂生产技术
内容提要:
1.油料及油脂
2.油料的预处理
3.压榨法取油
4.浸出法取油
5.油脂精炼
第十章植物油脂生产技术
【学习目标】
通过学习,掌握植物油脂生产的工艺流程,压榨法取油和油脂精炼的原理。
生产流程:
油料→筛选→去石→磁选→剥壳→仁壳分离→仁干燥→破碎→软化→轧坯→湿润蒸炒→压榨取油→毛油→沉降分离杂质→过滤分离杂质→离心分离杂质→水化脱胶→碱炼脱酸→脱色→脱臭→脱蜡→成品油
第一节油料及油脂
油料是油脂制取工业的原料,油脂工业通常将含油率高于10%的植物性原料称为油料。
一、油料
(一)油料的种类
油料按植物学属性可分为草木油料和木本油料,按产量大小可分为大宗油料和野生油料,按含油率高低可分为高含有料和低含有料。
油料中以油菜籽、大豆、花生、棉籽、芝麻、葵花籽等几种产量最大。
(二)油料种籽的化学成分
各种油料种籽中一般含有油脂、蛋白质、糖类、脂肪酸、磷脂、色素、蜡质、陉类、醛类、酮类、油溶性维生素、水分以及灰分等物质。
油料种籽中几种主要的化学成分:
1、蛋白质
化学成分及它们的性质。
在油料种籽中,蛋白质主要存在于籽仁的凝胶部分。
因此,蛋白质的性质对油料的加工影响很大。
油料中蛋白质的相对密度大致接近于1.25—1.30;蛋白质除醇溶朊(蛋白质)外都不溶于有机溶剂;蛋白质在加热、干燥、压力以及有机溶剂等作用下会发生变性;蛋白质可以和糖类发生作用,生成颜色很深的不溶于水的化合物。
2、磷脂
磷脂即磷酸甘油脂,简称磷脂。
磷脂咸胆碱俗称卵磷脂,磷脂咸乙醇氨俗称脑磷脂,它们是两种最主要的磷脂。
油料中的磷脂是一种营养价值很高的物质。
磷脂不溶于水,可溶于油脂和一些有机溶剂中;磷脂有很强的吸水性,吸水膨胀形成胶体物质。
3、脂肪酸
脂肪酸在油料种籽中主要是以结合状态存在于油脂中,油料种籽成熟度较差或油料种籽在储存过程中发热霉变,油料种籽中的游离脂肪酸含量就会升高。
软脂酸和硬脂酸是已知分布最广的两种饱和脂肪酸,存在于所有的动植物油脂中,在猪脂、牛脂、棕榈油、可可脂中的含量最高。
在一烯酸中,以含有18个碳原子数的油酸分布最广,几乎存在于所有的动植物油脂中。
油酸的系统命名为顺-9-十八碳一烯酸,它表示碳原子数有18个,以羧基上的碳原子作为1,然后依次排至碳连末端,在9位上有一个顺式双键。
天然油脂中最常见的二烯酸是亚油酸,即顺-9、顺-12-十八碳二烯酸。
亚油酸具有特殊的生理和生物活性,是人体必须的脂肪酸。
亚油酸普遍存在于液体植物油中,如红花油、葵花油中含亚油酸70%——85%。
棉籽油、大豆油、玉米油、芝麻油中含亚油酸40%—50%。
4、色素
纯净的甘油三酸是无色的液体。
油料种籽的色素一般有叶绿素、类胡萝卜素、黄铜色素及花色素等。
油脂中的色素能够被活性白土或活性碳吸附除去,也可以在碱炼过程中被皂角吸附除去。
5、蜡
蜡是高分子的一元脂肪酸和一元醇结合而成的酯,主要存在于油料种籽的皮壳内,且含量很少。
常温下蜡是一种固态粘稠的物质,蜡能溶于油脂中,溶解度随温度的升高而增大,在低温冷却时溶解度大大降低并从油脂中析出。
在高档油脂产品中,蜡的存在会影响其外观,所以需用脱蜡工艺将其脱除。
二、油脂、
(一)油脂的分类
1、按物理状态分:
脂肪(常温下为固态)和油(常温下为液态);
2、按化学结构分:
简单脂:
酰基脂,蜡;复合脂:
鞘脂类(鞘氨酸、脂肪酸、磷酸盐、胆碱组成),脑苷脂类(鞘氨酸、脂肪酸、糖类组成),神经节苷脂类(鞘氨酸、脂肪酸、复合的碳水化合物);衍生脂:
类胡箩卜素、类固醇、脂溶性纤维素等。
3、来源分:
乳脂类、植物脂、动物脂、海产品动物油、微生物油脂。
4、按不饱和程度分:
干性油:
碘值大于130,如桐油、亚麻籽油、红花油等;半干性油:
碘值介于100-130,如棉籽油、大豆油等;不干性油:
碘值小于100,如花生油、菜子油、蓖麻油等。
5、按构成的脂肪酸分:
单纯酰基油,混合酰基油。
(二)油脂的功能
1、生命功能:
构成机体,调节生命过程;
2、营养功能:
提供必需脂肪酸和热能,运输脂溶性维生素;
3、风味功能。
(三)油脂的物理性质
1、油脂的物理性质
(1)、溶解度油脂不溶于水,可溶于大多数的有机溶剂
(2)、黏度油脂的黏度随温度的增高而很快的降低。
在制油的过程中,对油胚进行加热蒸炒,以降低油脂的黏度,增加油脂的流动性,提高出油率。
(四)油脂的化学性质
1、油脂的水解
油脂在较高的温度、压力和催化剂作用下,可以水解而生成甘油和游离脂肪酸。
2、油脂的氧化
空气氧化使油脂酸值升高。
油脂空气氧化的分解产物对油脂的营养和应用十分不利,分解产生的低分子醛、酮、酸、烃等物质绝大多数具有特殊的刺激性气味,俗称哈喇味或酸败味,影响油脂的风味;这些分解产物在人体中很难代谢,对肝脏造成的损坏。
油脂氧化产生聚合物为致癌物质,对人体健康更为有害。
100克油脂在一定条件下所能游离出KI中的碘的克数(I2/100)称为该油脂的过氧化值(PVO)。
过氧化值反映油脂中氢过氧化合物的量,也即表示油脂受空气氧化的程度。
防止油脂酸败的措施主要是防止油脂氧化及水解,一般要将油避光、避热,降低水分含量,减少金属离子的含量,去除叶绿素等光敏物质,加入抗氧化剂和增效药剂以提高油脂的稳定性等。
在植物油脂中普遍存在的生育酚及个别油脂中存在的阿魏酸、棉酚、芝麻酚以及角鲨烯等成分也具有抗氧化效能,常称为天然抗氧化剂。
为提高油脂的稳定性。
在抗氧化剂添加限量的基础上,可在油脂中添加增效剂。
常用的增效方法有两种,一种是把两种或两种以上的抗氧化剂混用,另一种是加入具有降低过渡金属离子活力的物质即增效药剂,常用增效药剂有磷酸、柠檬酸、酒石酸、抗坏血酸(维生素C)、脑磷脂及生育酚等。
第二节油料的预处理
油料的预处理即是在油料取油之前对油料进行清选除杂,并将其制成具有一定结构性能的物料,以符合不同取油工艺的要求。
一、油料的清理
(一)清理的目的和方法
油料清理就是利用各种设备分离油料中所含杂质的工艺过程。
1、清理的目的:
减少油分损失,提高出油率,提高油脂、饼粕和副产物的质量,提高设备的处理量,减轻对设备的磨损,延长设备的使用寿命,避免生产事故,保证生产的安全,减少和消除车间的尘土飞扬,改善操作环境等。
2、清理的方法:
常采用筛选、磁选、风选、相对密度去石等方法和设备,将油料与杂质分离,以达到除杂的目的。
3、清理的要求:
净料中含杂质最高限额:
花生仁为0.1%,大豆、棉籽、油菜籽、芝麻为0.5%。
杂质(下脚料)中含油料最高的限额:
大豆、棉籽、花生仁为0.5%,油菜籽、芝麻为1.5%。
二、油料的剥壳及仁壳分离
剥壳是带壳油料在取油之前的一道重要工序,对花生、棉籽、葵花籽等一些带壳油料必须经过剥壳才能用于制油。
(一)剥壳的目的、要求和方法
1、剥壳的目的:
剥壳的目的为提高出油率,提高毛油和饼粕的质量,减轻对设备的磨损,增加设备的有效生产量,利于轧坯等后续工序的进行及皮壳的综合利用等。
2、剥壳的要求:
剥壳的要求是剥壳率高,漏籽少,粉末度小,利于剥壳后的仁、壳分离。
3、常用的剥壳方法:
(1)借粗糙面的碾搓作用使油料皮壳破碎,如用圆盘剥壳机对棉籽、花生、油桐籽、油茶籽进行剥壳。
(2)借与壁面或打板的撞击作用使皮壳破碎,如用离心式剥壳机对葵花籽进行剥壳。
(3)借锐利面的剪切作用使油料皮壳破碎,如用刀板剥壳机、齿辊剥壳机对棉籽进行剥壳。
(4)借轧辊的挤压作用使油料皮壳破碎,如用轧辊剥壳机对蓖麻籽进行剥壳。
(二)剥壳设备
1、圆盘剥壳机
圆盘剥壳机通常用于棉籽的剥壳,也用于花生果、油桐籽、油茶籽的剥壳。
(1)、特点:
机构比较简单,调整使用方便,一次剥壳率高,但仁壳混合物的粉碎读度较大,不易分离。
(2)、结构:
它主要由喂料器、固定磨盘、活动磨盘、磨片、底座机壳和调节器等组成。
棉籽进入喂料器后,在喂料翼1的作用下均匀落下,调节板2的作用是控制进料量。
棉籽通过进料通道3进入固定磨盘4和活动磨盘5中间,受到磨盘的搓碾作用而被剥壳或破碎,剥壳后的棉籽从下面的出口排出。
活动磨盘和固定磨盘上都装有6块扇形磨片6和7,组成环形工作面。
磨片有斜条槽纹两种,调节器主要用于调节磨盘间距。
图10——1圆盘剥壳机
2、齿辊剥壳机
齿辊剥壳机是一种新型的棉籽剥壳设备,也可以用于大豆、花生等大颗粒油料的破碎。
齿辊剥壳机主要是通过两个有速差的齿辊对油料的剪切和挤压作用,实现剥壳过程。
齿辊之间的间隙可根据油料大小通过调节装置进行调节。
1、特点:
该机剥壳率高,剥壳后壳仁混合物的粉末度小,整仁率高,仁壳易分离。
2、结构:
用于棉籽剥壳和仁壳分离的齿辊剥壳机组,它由齿辊剥壳机、六联打筛、振动平筛及风选系统组成。
经齿辊剥壳机剥壳后,仁壳混合物直接落到下面的一组六联打筛和振动平筛进行筛选分离,然后再通过风选分离,将仁壳较完全地分开。
图10——2齿辊剥壳机
1-齿辊剥壳机2-分配螺旋输送机
3-六连打筛4-分离平筛5-吸风道
3、离心剥壳机
离心剥壳机有卧式和立式两种,主要用于葵花籽的剥壳,也能用于油桐子、油茶籽及核桃等油料的剥壳。
立式离心剥壳机用于葵花籽的剥壳。
图10——3立式离心剥壳机
1-料斗2-调节手轮3-可调料门4-打板
5-挡板6-转盘7-转动轴8-卸料漏斗
9-机架10-传动皮带轮
图10——4锤击式剥壳机
4、锤击式剥壳机
它是利用带有锤击头的转动辊在半圆形箅栅内旋转,将进入箅栅的花生果锤击、挤压使之破碎,然后通过筛选和风选将仁、壳分离。
花生果从存料斗1中通过调节器2、6和拔料辊4控制流量,形成较薄的料层均匀下落。
在花生果下落的过程中,从风道13吹出的气流把轻杂吹走,经导风板3送往集壳管9.重杂质落入溜管14排出。
花生果在气流作用下偏向左边流入箅栅8,箅栅中间为剥壳辊7,辊上装有锤击头。
剥壳辊以100r/min的转速旋转,花生果在锤击头的打击和挤压作用下破碎,并通过下部的半圆形箅栅缝隙下落。
从箅栅缝隙下落的剥出物,遇到风机吹来的另一路气流,将花生壳屑、花生衣吹向集壳管,从中间出口吹出机外。
下落的花生仁及少量的小粒花生果,则进入振动筛10进行分离。
振动筛共有三层,上层分离花生果及花生仁,筛上物花生果需返回重剥;中层筛面分离大花生仁和一般的小花生仁;下层筛面中间有一段筛孔较小的筛板,以除去部分细小杂质,其余部分为淌板。
图19——4为集壳管出口,11为调节活门,12为风机。
该剥壳及仁壳分离机组的结构简单,使用方便,剥壳及仁壳分离效率高。
(三)对仁壳分离方法及设备
1、对仁、壳分离的要求
(1)、仁中含壳率(10目筛检验):
棉籽仁不超过10%,花生仁不超过1%,葵花籽仁10%—15%。
(2)、壳中含仁率:
棉籽壳不超过5%,花生壳不超过0.5%,葵花籽壳不超过1%。
2、仁、壳分离的方法
(1)、筛选法:
筛选法按仁壳混合物各组成成分体积大小进行分离。
常用的筛选设备有振动筛、旋转筛、螺旋筛。
旋转筛的筛孔自大而小(6㎜、5㎜、4㎜),因为经过打棒的不断拍打翻动,物料逐渐松散粉碎,适当缩小筛孔可以减少通过筛孔混入仁中的壳屑。
螺旋筛是一种新型的仁壳分离筛,其结构如图2——5所示,螺旋筛是一种变形的的螺旋输送机,其壳体用筛板制成,在螺旋叶片装有角钢制成的刮料板,其他部件均与螺旋输送机相似。
螺旋输送机送出,经三层筛分离后的棉壳从最下层筛的末端出壳口排出。
图10——5螺旋筛
1-进料口2-螺旋轴3-螺旋叶4-支撑5-刮料版6-链轮
7-筛网8-盖板9-外壳10-仁出口11-壳出口
2、风选法:
当油料剥壳后的混合物在外形和大小上无明显区别,难以用筛选的方法进行有效分离时,可利用这些物料悬浮速度的不同,采用风力分选的方法将其分离。
三、油料的干燥
(一)干燥的要求
不同工序对油料干燥的要求不同,要求干燥后的油料含水达到最适宜的水分,干燥后油料无焦糊和夹生现象。
干燥过程中的温度不能影响油料品质,干燥料坯时不能粉碎。
按照热能传给湿物料的方式,干燥可分为对流干燥、传导干燥、辐射干燥、介电加热干燥,在油厂普遍应用的是对流干燥和传导干燥。
(二)干燥设备
1、回转式干燥机制油厂又称滚筒式干燥机滚筒的内壁对称分布几组加热排管,内通蒸汽对物料进行加热。
图10——6回转式干燥机
1-外壳2-进料口3-导轮4-齿圈5-加热排管6-分汽盘7-送汽管
8-托轮9-伞齿轮传动机构10-填料盘根11-出料口12-翻扬板
2、平板干燥机如图2——7所示,由加热板、刮板链条、链轮、无级调速电机,减速器及机架组成。
在干燥室内,装有多层加热板和回转的刮板链条输送器。
当料坯落在上层加热板上后,料坯在刮板链条拖动下向前移动,移动到末端时,落到下一层平板上,继续被刮板链条带着运动,直至最下层。
料坯在各层加热板上移动的过程中加热干。
图10——7平板干燥机
1-出料口2-主动轮3-机壳4——从动轮5-分配器
6-刮板链条7-热空气出口8-平板夹层
四、油料生坯的制备
在提取油脂前,油料必须先被制造成适合于取油的料坯。
料坯的制备通常包括油料的破碎、软化和轧坯等工序。
(一)油料的破碎
1、破碎的目的
破碎的目的首先是使油料具有一定的粒度以符合轧坯条件;其次是油料破碎后表面积增大,利于软化时温度和水分的传递,软化效果好。
另外,对于颗粒较大的压榨饼块,也必须将其破碎成为较小的饼块,才更利于浸出取油。
2、破碎的要求
要求破碎后的油料粒度均匀,不出油,不成团,少成粉
3、油料破碎方法和设备
目前,油厂常用的破碎设备是齿辊破碎机,其次还有锤式破碎机、园盘剥壳机等。
(二)油料的软化
软化是通过对水分和温度的调节,使油料塑性增加的工序,主要应用于含油量低和含水分低的油料。
1、软化的目的
通过对温度和水分的调节,使油料具有适宜的弹塑性,减少轧坯时的粉末度和粘辊现象。
软化还可以减少轧坯时由于轧辊磨损造成的机器的振动,以利于轧坯操作的正确进行。
2、软化的工艺要求
当油料含水量高时,软化温度要低一些;反之软化温度可高一些,还要求软化后的料粒有适宜的弹塑性及均匀透彻。
3、软化设备
常用的软化设备有层式软化锅和滚筒软化锅。
层式软化锅的结构如层式蒸炒锅。
滚筒软化锅的结构相似于滚筒干燥器。
(三)油料的轧坯
轧坯就是利用机械的作用,将油料由粒状轧成片状的过程。
1、轧坯的目的
轧坯的主要目的是破坏油料的细胞组织,以提高浸出或压榨时的出油速度和出油率。
另外,通过轧坯可使油料由粒状变成片状,表面积增加,以保证料坯蒸炒的效果。
2、轧坯的要求
料坯薄而均匀,粉末度小,不露油。
料坯的厚度为大豆0.3mm以下,棉仁0.4mm以下,菜籽0.35mm以下,花生仁0.5mm以下。
粉末度要求控制在孔径20目筛下物不超过3%。
3、轧坯设备
目前油厂应用较多的是平列式的双对辊弹簧紧辊轧坯机和液压紧辊轧坯机.图2——8为弹簧紧辊式的对辊扎坯机,它主要由进料斗、轧辊、刮刀、辊距调节装置及机架组成。
图10——8单对辊轧机
1-料斗2-下料活口3-喂料辊4-链条5-皮带轮6-后辊(主动辊)7-重锤柄8-重锤9-刮刀10-机座11-轴承12-轴承座13-机架14-调节螺杆15-弹簧16-锁紧螺母17-前辊18-调节手柄19-凸轮轴20-凸轮
五、油料熟坯的制备
(一)蒸炒的目的和方法
1、蒸炒的目的
蒸炒的目的在于使料坯在微观生态、化学组成以及物理状态等方面发生变化,以提高压榨出油率及改善油脂和饼粕的质量。
蒸炒使油料细胞受到彻底破化,使蛋白质变性,油脂聚集,油脂黏度和表面张力降低,料坯的弹性和塑性得到调整。
2、蒸炒的方法
蒸炒方法随油料品种和用途的不同而有所不同,可分为干蒸炒和湿润蒸炒两种。
干蒸炒只对料坯或油籽进行加热和干燥,不进行湿润。
湿润蒸炒指在蒸炒开始时利用添加水分或喷入直接蒸汽的方法使生坯达到最优的蒸炒开始水分,再将湿润过的料坯进行蒸炒,使料坯中水分、温度及结构性能最适宜压榨取油的要求。
这是油厂普遍采用的一种蒸炒方法。
(二)湿润蒸炒工艺
湿润蒸炒设备称为蒸炒锅,有立式和卧式两种型式。
国内油厂常用立式的层式蒸炒锅。
1、湿润
湿润的方法有加热水法、喷蒸汽法、加水和喷蒸汽混合法。
湿润水分一般为13%——15%,对棉籽生坯应采用高水分蒸坯,其湿润水分含量最高可达18%——22%。
为使料坯有充分的时间与水分接触,保证料坯湿润均匀,蒸锅湿润层的装料要满。
一般装料量控制在80%——90%。
保持蒸炒锅密闭,关闭排气孔,以防水分散失。
2、蒸坯
为保证蒸坯的效果,料坯要蒸透蒸匀。
因此,操作时要做到蒸坯层的装料要满,一般装料量应控制为锅层高度的80%,以延长蒸坯时间。
蒸锅应密闭,以增加蒸锅空间湿度,经过蒸坯,料坯温度应提高至95——100℃,湿润与蒸坯时间约需50——60min.
3、炒坯
炒坯的主要作用是加热去水,使料坯达到最适宜压榨的低水分含量。
锅中的存料量要少,一般装料量控制在40%左右。
经过炒坯,出料温度应达到105——110℃,水分含量在5%——8%之间。
图10——9立式蒸炒锅
1-蒸汽边夹层2-蒸汽底夹层3-搅拌轴4-搅拌翅5-排气管6-变速箱7-落料孔
8-自动料门9-联轴器10-出料孔
第三节压榨法取油
借助机械外力作用,将油脂从油料中挤压出来的取油方法称为压榨法取油。
压榨法取油的特点:
工艺简单,配套设备少,对油料品种适应性强,生产灵活,油品质量好,色泽浅,风味纯正。
但压榨后的饼残油量高,出油效率低,动力消耗大,零件易损耗。
一、压榨法取油的基本原理
(一)压榨过程
压榨时,受榨料坯的粒子受到强大的压力作用,致使其中的液体部分和凝胶部分分别发生两个不同的变化,即油脂从油料空隙中被挤压出来和榨料粒子经弹性变形形成坚硬的油饼。
二、动力螺旋榨油机取油
(一)螺旋榨油机的工作原理
动力螺旋榨油机的工作原理概括地说,是由于旋转着的螺旋轴在榨膛内的推进作用,使榨料连续地向前推进。
同时,由于榨螺螺旋导程的缩短和根圆直径的逐渐增大,使榨膛空间体积不断缩小对榨料产生压榨作用。
榨料压缩后,油脂从榨笼缝隙中挤压流出,同时榨料被压成饼状块从榨膛末端排出。
(二)螺旋榨油机取油的基本过程
在螺旋榨油机中,压榨过程一般分为三个阶段,即进料(预压)段、主压榨段(出油段)和成饼段(重压沥压段)。
1、进料段
在进料段,榨料在向前推进的同时,开始受到挤紧作用,因而排出空气与少量水分,形成松饼。
2、主压榨段
此阶段是形成高压大量排油的阶段。
这时由于榨膛空间迅速有规律地减小,使个别粒子开始结合,榨料在榨膛内成为连续的多孔物而不再松散。
3、成饼段
榨料已形成瓦块饼,成为完整的可塑体,几乎呈整体式推进,因而,也产生了较大的压缩阻力(主要指轴向力)。
图10——10ZX型螺旋榨油机结构示意图
1-喂料螺旋2-榨条段3-螺旋轴4-榨圈段5-上、下榨笼骨架6-榨螺
7-压紧螺母8-调节螺丝
三、毛油中悬浮物的处理
螺旋榨油机压榨所得的毛油中,含有许多粗的或细的油渣操作规程要求排渣量为10%以下,这些机械杂质的存在将使毛油输送和油脂精炼发生困难,因此必须在油脂精炼之前去除这些机械杂质。
对压榨毛油中饼渣的分离多采用沉降和过滤的方法,设备有板框压滤机、澄油箱、螺旋卸料沉降式离心机等。
第四节、浸出法取油
一、浸出法取油概念
浸出法取油是应用固液萃取的原理,选用某种能够溶解油脂的有机溶剂,经过对油料的喷淋和浸泡作用,使油料中的油脂被萃取出来的一种取油方法。
二、浸出法的过程
过程是把油料料坯、预榨饼颗粒浸于选定的溶剂中,使油脂溶解在溶剂中形成混合液即混合油,然后将混合油与浸出后的固体粕分离。
利用溶剂与油脂的沸点不同对混合油进行蒸发、汽提,可使溶剂气化与油脂分离,从而获得浸出毛油。
浸出后的固体粕含有一定量的溶剂,经脱溶烘干处理后得到成品粕。
从湿粕蒸脱、混合油蒸发及其他设备排出的溶剂蒸汽和混合蒸汽经过冷凝、冷却以及溶剂与水的分离,分离出的溶剂循环使用。
三、浸出法取油的特点
粕残油量低,出油效率高,粕的质量好。
可以得到蛋白质变性程度很小的粕,以用于油料蛋白的提取和利用。
但油脂浸出所用溶剂大多易燃易爆,具有一定的毒性,生产的安全性较差。
第五节油脂精炼
一、概述
(一)毛油的组分
经压榨或浸出法得到的未经精炼的植物油脂一般称为粗油(毛油)。
精炼油的主要成分是混合脂肪酸甘油三脂,俗称中性油,此外,还含有数量不等的各类非甘油三酯成分,统称为油脂的杂质。
油脂的杂质一般可归纳为以下五类。
1、机械杂质
这类杂质是指在制油或储存过程中混入油中的泥沙、料坯粉末、饼渣、纤维、草屑及其他固态杂质。
这类杂质不溶于油脂,故可以采用过滤、沉降的方法从油中除去。
2、水分
粗油中水分的存在,影响油脂的透明度,促使油脂酸败,不利于优质的安全储存。
用加热的方法从油中除去。
3、胶溶性杂质
这类杂质以极小的微粒状态分散在油中,与油一起形成胶体溶液。
这类杂质主要包括磷脂、蛋白质、糖类、树脂和粘液物等,其中最主要的是磷脂。
磷脂混入油中会使油色变得深暗、浑浊。
磷脂遇热280℃会焦化发苦,吸收水分促使油脂酸败,影响油品的质量和利用。
4、脂溶性杂质
这类杂质完全溶解于油中,与油形成真溶液状态。
这类杂质主要包括游离脂肪酸、醇、维生素、蜡、色素等。
油脂中游离脂肪酸的存在,会影响油品的风味和食用价值,促使油脂酸败。
游离脂肪酸能与碱发生皂化反应,凝聚成皂粒与油脂分离;也能在高温、高真空下从油脂中蒸馏逸出。
故生产上常采用碱炼、蒸馏的方法将其从油脂中除去。
色素能使油脂带较深的颜色,影响油脂的外观,可采用吸附脱色的方法将其从油中除去。
(二)油脂精炼的目的和方法
1、油脂精炼的目的
毛油中的某些杂质会严重影响油脂加工的顺利进行,影响油脂的安全储藏,降低油脂的品质和使用价值。
为了保证食用油的品质,必须除去油中的有害杂质。
2、油脂精炼的方法
(1)机械方法:
包括沉降、过滤、离心分离,主要用以分离悬浮在油脂中的机械杂质及部分胶溶性杂质。
(2)化学方法:
包括酸炼、碱炼,还有氧化、脂化等。
酸炼即用酸处理,用来除去色素、胶溶性杂质等;碱炼即用碱处理,除去游离脂肪酸等杂质;氧化则用于脱色。
(3)物理化学方法:
物理化学方法主要包括水化、吸附、水蒸气蒸馏及液-液萃取法。
水化主要用于除去磷脂,吸附用来除去色素,液-液萃取法用于脱色、脱除游离脂肪酸等。
二、悬浮杂质的脱除
以悬浮状态存在于油脂中的杂质称为悬浮杂质。
目前,工业上常用的分离法油自然沉降、过滤、离心分离、分子膜分离法等,其中过滤法使用得较为普遍。
(一)沉降分离法
沉降法又可分为自然沉降、流动床沉降和超声波沉降等,自然沉降应用得最为普遍。
自然沉降法是利用悬浮颗粒与油脂的相对密度不同,在自然静止状态下,使悬浮杂质从油中沉降下来而与油脂分离的过程。
自然沉降法分离的设备结构简单、操作简便、耗能源少,在油脂厂被广泛采用。
这种设备有降池、履带式捞渣机等。
(二)过滤分离法
过滤分离法是借助于压滤机、输油泵、过滤介质,在重力或机械动力作用下使液体穿过滤布,杂质被截留成滤饼,从而达到清除悬浮杂质目的的方法。
常用的过滤设备有厢式压滤机,板框式压滤机。
图10——11板框式压滤机图10——12板框式压滤机工作原理图
1-尾板2-滤框3-滤板4-主梁1-滤板2-滤框3-滤布4-悬浮液入口
5-头板6-