铝合金熔铸工42铸造操作.docx
《铝合金熔铸工42铸造操作.docx》由会员分享,可在线阅读,更多相关《铝合金熔铸工42铸造操作.docx(8页珍藏版)》请在冰豆网上搜索。
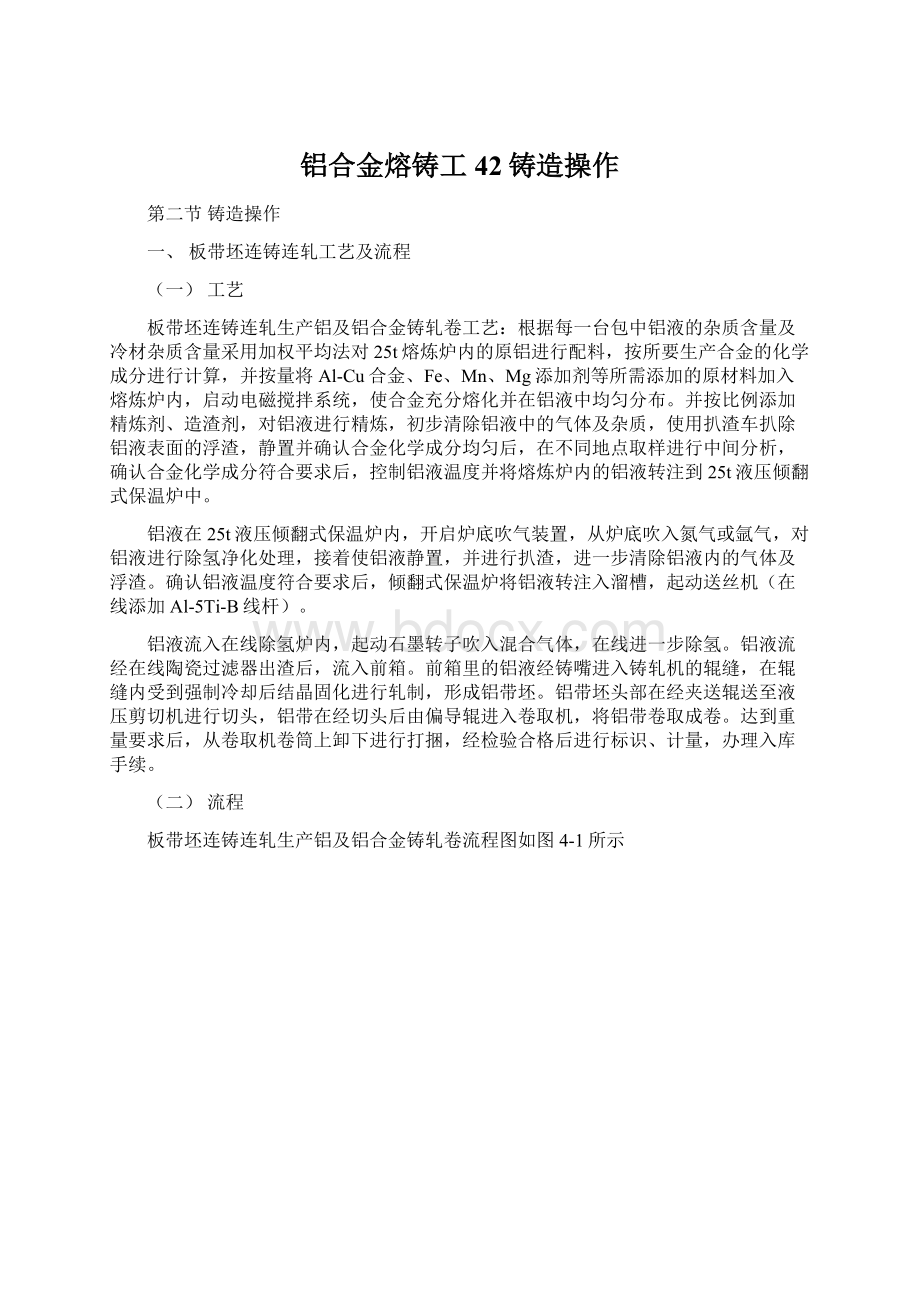
铝合金熔铸工42铸造操作
第二节铸造操作
一、板带坯连铸连轧工艺及流程
(一)工艺
板带坯连铸连轧生产铝及铝合金铸轧卷工艺:
根据每一台包中铝液的杂质含量及冷材杂质含量采用加权平均法对25t熔炼炉内的原铝进行配料,按所要生产合金的化学成分进行计算,并按量将Al-Cu合金、Fe、Mn、Mg添加剂等所需添加的原材料加入熔炼炉内,启动电磁搅拌系统,使合金充分熔化并在铝液中均匀分布。
并按比例添加精炼剂、造渣剂,对铝液进行精炼,初步清除铝液中的气体及杂质,使用扒渣车扒除铝液表面的浮渣,静置并确认合金化学成分均匀后,在不同地点取样进行中间分析,确认合金化学成分符合要求后,控制铝液温度并将熔炼炉内的铝液转注到25t液压倾翻式保温炉中。
铝液在25t液压倾翻式保温炉内,开启炉底吹气装置,从炉底吹入氮气或氩气,对铝液进行除氢净化处理,接着使铝液静置,并进行扒渣,进一步清除铝液内的气体及浮渣。
确认铝液温度符合要求后,倾翻式保温炉将铝液转注入溜槽,起动送丝机(在线添加Al-5Ti-B线杆)。
铝液流入在线除氢炉内,起动石墨转子吹入混合气体,在线进一步除氢。
铝液流经在线陶瓷过滤器出渣后,流入前箱。
前箱里的铝液经铸嘴进入铸轧机的辊缝,在辊缝内受到强制冷却后结晶固化进行轧制,形成铝带坯。
铝带坯头部在经夹送辊送至液压剪切机进行切头,铝带在经切头后由偏导辊进入卷取机,将铝带卷取成卷。
达到重量要求后,从卷取机卷筒上卸下进行打捆,经检验合格后进行标识、计量,办理入库手续。
(二)流程
板带坯连铸连轧生产铝及铝合金铸轧卷流程图如图4-1所示
二、 板带坯连铸连轧生产
(一)25t熔炼炉工艺操作
1.进铝
1)使用叉车将废料或冷材加入熔炼炉内。
2)检查虹吸管、高压风管、喷射器是否有堵塞现象。
3)折弯高压风管,打开气阀,检查空气压力是否达到0.4—0.5MPa。
4)引导抬包车到达熔炼炉前,用取样勺顶开抬包包盖。
5)引导抬包车到虹吸管下,对准包口,使虹吸管下降到包底,待到达包底后,再使虹吸管上升5~10cm。
6)缓慢打开气阀,观察前炉情况,待铝液抽出后,逐渐增大压力,并观察前炉及溜槽的铝液流量。
当压力表下降时,降低虹吸管,抽空包内剩余铝液。
7)当压力表指针下降时,迅速关闭气阀升起虹吸管,使其离开抬包口,通知司机,驶离虹吸区域。
8)按上述步骤进行出铝操作,直至进满熔炼炉为止。
2.配料、搅拌、扒渣
1)调整铝液温度(750±10)℃。
2)根据合金化学成分要求进行配料,用叉车加入中间合金和其他金属添加剂,待合金熔化后,再加入易烧损金属,并做好相关记录。
3)每吨铝添加打渣剂和精炼剂个1kg,并做好相关记录。
4)起动电磁搅拌,设定搅拌方式,搅拌铝液20--30min。
5)电磁搅拌结束后,取样进行中间分析。
若化学成分不符合要求,必须重新调整化学成分。
6)确认化学成分符合要求后,使用扒渣车进行扒渣处理,并将炉台及炉前渣子清理干净。
7)扒渣结束后,静置10—15min,调整铝液温度(740±20)℃。
3.转注前工作
打开出铝口堵头,清理干净出铝口,换上新的堵套,将铝液转注到25t保温炉内。
4.转注后工作
转注结束后,清理干净出铝口,堵上堵头,并将溜槽清理干净,刷上滑石粉。
5.注意事项
1)加入熔炼炉内的冷材、中间合金及添加剂必须干净、干燥。
2)进铝时,禁止人员从虹吸管下穿过。
3)熔炼炉炉台上的铝汝必须清除干净。
(二)25t倾翻保温炉工艺操作
1)待高温铝液全部进入保温炉后,用石棉绒将铝液入口堵住。
2)起动炉底吹气装置10--20min,控制每块透气砖流速为1.27m3/h。
3)检查N2或Ar的供气装置,发现压力过小及时更换。
4)停止吹气后,保持透气砖有一微小气体流速,流量为0.85m3/h,防止透气砖堵塞。
6.防止透气砖堵塞。
5)对铝液进行扒渣处理,并将炉台及地面铝渣清理干净。
6)静置铝液10--15min,并调整铝液温度在(740±20)℃范围内。
7)待工艺条件合格后,起动液压系统,保温炉开始倾翻。
在铸造过程中,由溜槽液位激光传感器自动控制保温炉倾翻。
8)铸造结束后,控制保温炉复位。
9)注意事项:
透气砖每小时连续通气5min;保温炉台上的铝渣必须清除干净。
(三)燃油系统工艺操作
1)通过操作台输入主要技术参数。
2)熔炼炉炉膛报警温度:
1060℃;保温炉炉膛报警温度:
900℃;铝液温度控制范围:
(740±20)℃。
3)炉压控制范围:
1--30Pa。
4)一旦超过参数控制范围,燃烧器将关闭并闭锁。
5)通过PLC自动控制系统,确保炉内熔体温度及烟气的排放。
6)点火控制:
PLC检测有关参数,如炉顶温度是否超温、炉压是否超限助燃风压和燃油压力是否符合范围等;满足条件起动点火控制器,开始点火;若点火失败,点火程序控制器发出指令,自动关闭安全电磁阀,并报警;查明原因,按下复位按钮,重新执行点火程序。
7)将炉温控制数据进行记录。
8)停炉时,供油燃烧系统控制。
9)尽可能将炉内残存铝液放干。
10)完全关闭轻油阀门,并对燃烧器进行清理。
11)停止风机运转,关闭空气蝶阀及烟道。
12)注意事项:
确认参数输入的正确性;随时观察炉内燃烧情况,如有异常及时处理;炉内没有铝液时,关闭燃烧器;保证轻油及压缩空气压力符合要求。
(四)除气、过滤工艺操作
1.在线除氢操作
1)当溜槽内铝液到达除气炉时,打开除气炉入口处及出口出的石棉绒。
2)调整N2或Ar压力至0.3--0.7MPa,转子流量为5m3/h,增大转子转速至正常转速。
3)打开Cl2控制阀门,调整压力至0.3MPa,流量为0.1m3/h,使Cl2平稳地流入主气流中。
4)在除气过程中,确认除气炉内铝液温度,及时调整。
5)铸轧结束后,用石棉绒堵死除气炉出口、入口,同时清理干净溜槽内铝液。
6)关闭Cl2阀门,降低转子转速,同时保持一个微量的Ar通过石墨转子。
7)确认除气炉在不浇注时,加热器工作正常。
8)如遇到紧急事故或停电时,需放掉炉内铝液,进行清渣操作:
首先,关闭气体阀门、石墨转子及加热器,启动液压系统,升起石墨转子和加热器,清理干净上面的铝渣;其次,打开放流口,放掉炉内铝液,通过移动式炉门清理干净炉内铝渣;最后,将石墨转子和加热器复位,堵上放流口。
2.在线过滤装置操作
1)在生产前30min,启动加热系统对陶瓷过滤板进行预热。
2)在铸造过程中,确认过滤箱内铝液温度,并及时调整。
3)铸轧结束,关闭加热系统,起动液压系统,升起加热盖。
4)打开放流口,取出陶瓷过滤板,并清理干净箱体内铝渣。
5)堵死放流口,生产前放入陶瓷过滤板,放下加热盖。
6)清理干净溜槽,整理好工器具。
3.注意事项
1)在保温期间,确保除气炉加热器工作正常。
2)巡视Cl2流量和压力,如有异常及时处理。
3)生产前对过滤箱及工器具进行预热。
(五)Φ960mm×1850mm超型铸轧机铸造工艺操作
1.立板准备
(1)熔体准备将保温炉内铝液温度升至760℃以上,炉内铝液量不应小于12t,以确保立板过程中铝液连续供给。
(2)设备及工具准备设备及工具的准备包括以下方面:
1)检查铸轧机列各部分能否正常运行,起动液压系统,根据产品的合金牌号及规格设定好预载力,调整好辊缝(新辊测量辊缝是,应在距离轧辊边部测量,测量时铝杆应放直)及上、下辊石墨喷枪(或火焰喷涂系统)限位。
2)对新辊先用汽油清洗其表面油污,表面油污必须清洗干净,并认真检查轧辊表面是否有缺陷,然后用干净的布将表面擦干净。
用液化气喷枪对辊面进行往复烘烤,烘烤完毕擦去辊面炭黑,然后起动石墨喷涂系统或火焰喷涂系统,往辊面上均匀喷上一层石墨液或碳粉。
对于已生产过的旧辊,先用240目砂布砂平辊上印痕,再均匀喷上一层石墨液或碳粉。
旧辊石墨可少喷一些,然后关闭石墨喷枪或火焰喷涂系统,用压缩空气吹扫辊面,使辊面水分尽量挥发干净。
3)起动主水泵,按工艺需求调整上、下辊进、出水流量大小,冷却水入口温度根据不同辊径设定在25—60℃之间。
起动冷却风机及循环水泵。
4)吊放好渣箱及渣斗位置。
5)从烘干箱内移出铸嘴组件,吊放在专用平台上,按生产要求调整好嘴子开口,锁紧耳子两侧紧固顶丝,检查铸嘴唇口,然后吊到铸轧机平台上紧固好。
6)调整稳流器锥头位置,使其与前箱流眼配合良好,稳流器要备用一套。
7)在前箱内侧表面(靠流眼)标定液面高度线。
8)调整铸嘴水平位置,比正常工作位置后退20mm左右。
9)打开铸嘴平台液压手动阀,将嘴子缓慢移向辊缝。
移动时,轧机前要有人注意观察嘴子垂直位置,发现太高或太低应立即停止铸嘴移动,待垂直僮置调整至合适后,再移动铸嘴,直到铸嘴平台到位。
10)同步调整嘴子水平和垂直位置到预定的铸轧区长度范
围内,嘴子与上、下辊面的间隙控制在恰当位置。
11)装上尾部溜槽,并清理干净,用硅酸铝毡塞紧溜槽接缝,确保连接处紧密、无缝隙。
12)堵紧前箱底座放流口,接上放溜槽,准备好立板用工
具及运行中使用的材料。
13)用液化气喷枪对溜槽系统进行充分预热。
14)填写好立板工艺检查表,详细记录立板参数。
2.立板过程
1)当立板准备工作完成后,操作人员必须穿戴好劳保用品,按分工进入各自岗位。
2)根据合金、规格等设定好轧辊跑渣线速度。
3)打开静置炉流眼,及时处理溜槽系统中半凝固状态的铝液,让铝液顺利通过溜槽系统,经前箱上不放流口通过放溜槽进入渣箱,用铝液温度充分预热溜槽系统,并将除气炉转入正常运转状态。
4)将热电偶放入前箱测量铝液温度。
当前箱铝液温度达到720--730℃时,(特殊情况下可以控制为730℃以上),将控流杆放入流口中,控流装置调整至工作状态,稳定流口箱所需液面高度,接着拔出前箱塞杆堵头,在一定静压力作用下,让铝液完全充满嘴腔,随轧辊旋转带出。
5)当辊面上板凝固状态组织达一定长度,操作人员将其控离,铲入渣斗内,用棉布擦净辊面上铝屑。
防止铝屑进入轧辊与铸嘴之间的部位。
根据辊面及板面情况确定跑渣时间。
跑渣结束,将渣斗吊开。
6)观察铝液在辊缝中结晶情况,调整液面高度、铸嘴位置和辊速,直至形成完整的固体板,通过导出辊、导入板、夹送辊至剪切机切掉板头不规则部分,至卷取机卷取。
7)测量板宽,调整前箱液面高度,使宽度公差符合生产计划要求,安放好液面报警浮标。
8)若辊面局部出现热,应用孔径为0.063mm(240目)砂布沿辊圆周方向砂去印痕,然后用布擦去污物。
9)观察铸轧板半板面情况,起动石墨喷枪行程按钮或火焰喷涂系统,打开压缩空气,、石墨液阀门,开启石墨喷涂泵,调整所需喷涂量,观察喷枪行程限位是否恰当,使其喷涂范围稍大于板宽80--100mm。
10)逐步降低前箱温度至工艺要求范围,调整嘴子位置,同时逐步提高带速至工艺范围要求。
11)起动细化线杆加料机,钛丝添加速度按工艺要求设定。
12)测量带材两边厚差,其差值应≤0.03mm。
待板面状况良好后,剪切两块样板,取一块用水冲冷,测量两边厚差及中凸度;另一块用酸洗,检查晶料度及条纹缺陷,确认合格后,开始卷成品。
3.正常铸轧过程
1)控制并记录各工艺参数,使工艺参数稳定在规定的范围内。
2)及时处理板面存在的缺陷。
3)当卷径达到额定值时,应先调整卸卷小车顶上铸轧卷,注意不要过紧或过松,合上夹送辊后剪切取样。
当铸轧板端头接近卸卷小车托辊时停止卷取,收缩卷轴,将卷推出,推出后卷轴重新定位,升上出口台板,待板前端进入钳口后卷轴胀起,开始另一卷的卷取。
4)移出卸卷小车并降下,用钢带捆紧,(一般捆两道),在卷上标明合金牌号、卷号、生产班组、机号和规格等标志。
5)吊开铸轧卷,将铸轧卷放在铸轧卷架上冷却至室温。
吊卷时应注意,不允许碰伤铸轧卷。
4.停机处理
1)当生产任务完成,或铸轧机列故障以及无法保证带材质量时应停机。
2)停机前应升起导入版并伸出,升起卸卷小车托紧轧卷。
当铸轧板尾部与轧辊脱离后,应及时关闭石墨喷涂系统。
然后使轧辊停止转动,避免损伤轧辊。
3)堵上保温炉流眼,退出铝钛硼杆,将除气炉石墨转子调至闲置状态。
每次换辊停机时除气炉应进行热清炉。
4)打开前箱底座流口,前箱处渣箱尽量先装满,然后打开流口箱流眼及过滤箱流眼,让铝液流入中间渣箱。
5)清理溜槽系统、前箱及底座,并拆卸活动溜槽部分,用硅酸铝毡盖密溜槽及过滤箱体,除气炉进出口应用挡板密封。
6)待渣箱内铝液凝固后,吊走渣箱。
移出铸嘴并吊放在专用平台上,按生产计划重新组装嘴子,放入烘干箱烘烤。
7)用孔径为0.063mm(240目)砂布砂去轧辊上印痕并清理干净。
8)吊走铸轧卷,搞好卫生,保管好所使用的工具,准备下一次立板。
5.注意事项
1)铸嘴的制作要符合要求,并且进行充分预热。
2)溜槽、前箱、工器具等必须进行预热。
3)铸嘴的调整必须准确到位。
4)保证轧辊表面无损伤、干净。