汽车内外饰塑料件产品结构设计准则_.doc
《汽车内外饰塑料件产品结构设计准则_.doc》由会员分享,可在线阅读,更多相关《汽车内外饰塑料件产品结构设计准则_.doc(11页珍藏版)》请在冰豆网上搜索。
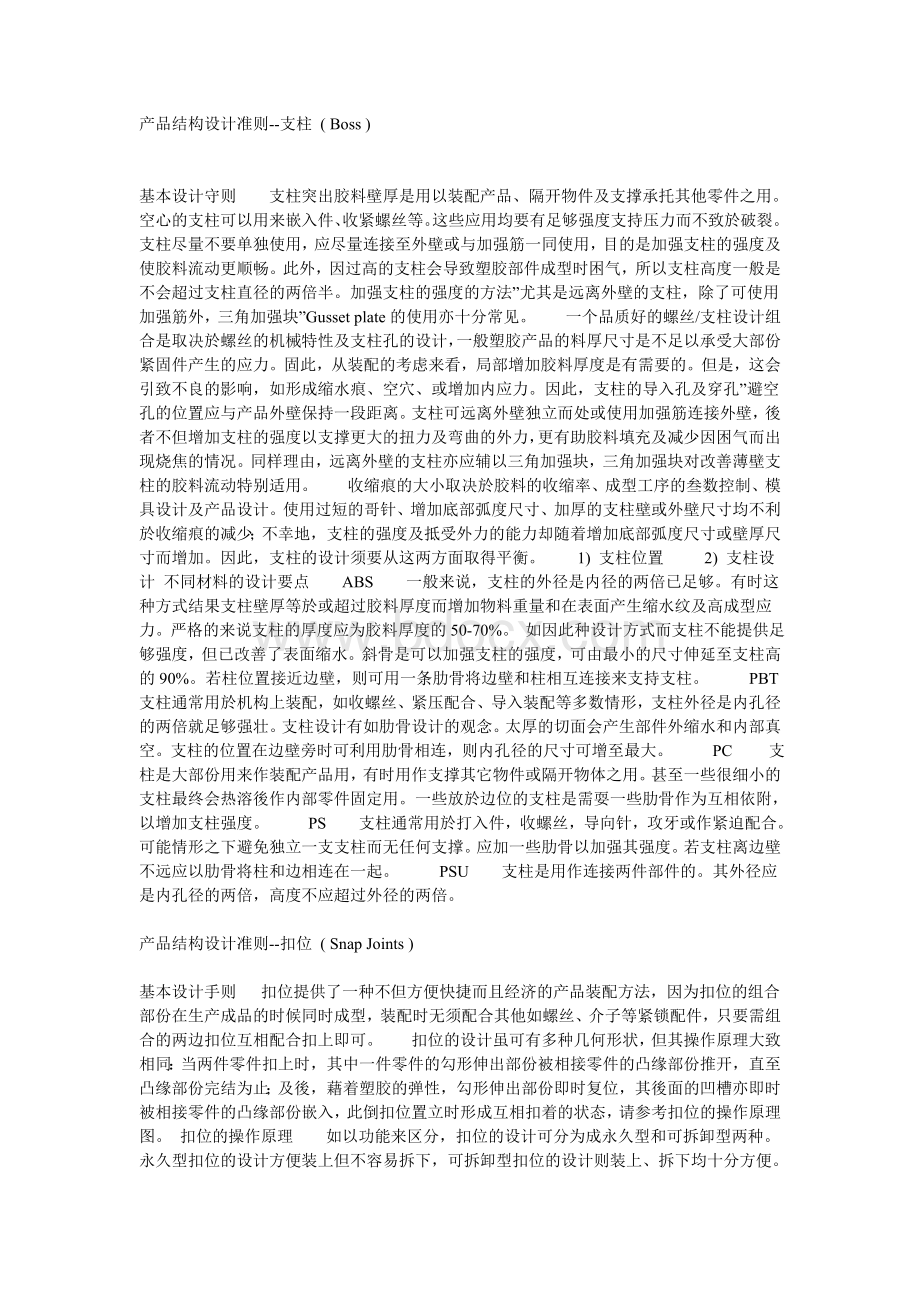
产品结构设计准则--支柱(Boss)
3^"D#~;j3`6k
-v*d/{+X'C6O7h'O5]+M6A-i0Z"O"C:
R
基本设计守则 支柱突出胶料壁厚是用以装配产品、隔开物件及支撑承托其他零件之用。
空心的支柱可以用来嵌入件、收紧螺丝等。
这些应用均要有足够强度支持压力而不致於破裂。
支柱尽量不要单独使用,应尽量连接至外壁或与加强筋一同使用,目的是加强支柱的强度及使胶料流动更顺畅。
此外,因过高的支柱会导致塑胶部件成型时困气,所以支柱高度一般是不会超过支柱直径的两倍半。
加强支柱的强度的方法”尤其是远离外壁的支柱,除了可使用加强筋外,三角加强块”Gussetplate的使用亦十分常见。
一个品质好的螺丝/支柱设计组合是取决於螺丝的机械特性及支柱孔的设计,一般塑胶产品的料厚尺寸是不足以承受大部份紧固件产生的应力。
固此,从装配的考虑来看,局部增加胶料厚度是有需要的。
但是,这会引致不良的影响,如形成缩水痕、空穴、或增加内应力。
因此,支柱的导入孔及穿孔”避空孔的位置应与产品外壁保持一段距离。
支柱可远离外壁独立而处或使用加强筋连接外壁,後者不但增加支柱的强度以支撑更大的扭力及弯曲的外力,更有助胶料填充及减少因困气而出现烧焦的情况。
同样理由,远离外壁的支柱亦应辅以三角加强块,三角加强块对改善薄壁支柱的胶料流动特别适用。
收缩痕的大小取决於胶料的收缩率、成型工序的叁数控制、模具设计及产品设计。
使用过短的哥针、增加底部弧度尺寸、加厚的支柱壁或外壁尺寸均不利於收缩痕的减少;不幸地,支柱的强度及抵受外力的能力却随着增加底部弧度尺寸或壁厚尺寸而增加。
因此,支柱的设计须要从这两方面取得平衡。
1) 支柱位置 2) 支柱设计 不同材料的设计要点 ABS 一般来说,支柱的外径是内径的两倍已足够。
有时这种方式结果支柱壁厚等於或超过胶料厚度而增加物料重量和在表面产生缩水纹及高成型应力。
严格的来说支柱的厚度应为胶料厚度的50-70%。
如因此种设计方式而支柱不能提供足够强度,但已改善了表面缩水。
斜骨是可以加强支柱的强度,可由最小的尺寸伸延至支柱高的90%。
若柱位置接近边壁,则可用一条肋骨将边壁和柱相互连接来支持支柱。
PBT 支柱通常用於机构上装配,如收螺丝、紧压配合、导入装配等多数情形,支柱外径是内孔径的两倍就足够强壮。
支柱设计有如肋骨设计的观念。
太厚的切面会产生部件外缩水和内部真空。
支柱的位置在边壁旁时可利用肋骨相连,则内孔径的尺寸可增至最大。
PC 支柱是大部份用来作装配产品用,有时用作支撑其它物件或隔开物体之用。
甚至一些很细小的支柱最终会热溶後作内部零件固定用。
一些放於边位的支柱是需耍一些肋骨作为互相依附,以增加支柱强度。
PS 支柱通常用於打入件,收螺丝,导向针,攻牙或作紧迫配合。
可能情形之下避免独立一支支柱而无任何支撑。
应加一些肋骨以加强其强度。
若支柱离边壁不远应以肋骨将柱和边相连在一起。
PSU 支柱是用作连接两件部件的。
其外径应是内孔径的两倍,高度不应超过外径的两倍。
:
Z"d%G1B.G6H!
R0\1}*L*t;o)@
产品结构设计准则--扣位(SnapJoints)
!
o;[+G4E U)c
&A+l!
J,R1o t基本设计手则 扣位提供了一种不但方便快捷而且经济的产品装配方法,因为扣位的组合部份在生产成品的时候同时成型,装配时无须配合其他如螺丝、介子等紧锁配件,只要需组合的两边扣位互相配合扣上即可。
扣位的设计虽可有多种几何形状,但其操作原理大致相同:
当两件零件扣上时,其中一件零件的勾形伸出部份被相接零件的凸缘部份推开,直至凸缘部份完结为止;及後,藉着塑胶的弹性,勾形伸出部份即时复位,其後面的凹槽亦即时被相接零件的凸缘部份嵌入,此倒扣位置立时形成互相扣着的状态,请参考扣位的操作原理图。
扣位的操作原理 如以功能来区分,扣位的设计可分为成永久型和可拆卸型两种。
永久型扣位的设计方便装上但不容易拆下,可拆卸型扣位的设计则装上、拆下均十分方便。
其原理是可拆卸型扣位的勾形伸出部份附有适当的导入角及导出角方便扣上及分离的动作,导入角及导出角的大小直接影响扣上及分离时所需的力度,永久型的扣位则只有导入角而没有导出角的设计,所以一经扣上,相接部份即形成自我锁上的状态,不容易拆下。
请叁考永久式及可拆卸式扣位的原理图。
永久式及可拆卸式扣位的原理 若以扣位的形状来区分,则大致上可分为环型扣、单边扣、球形扣等等,其设计可参阅下图。
球型扣(可拆卸式) 扣位的设计一般是离不开悬梁式的方法,悬梁式的延伸就是环型扣或球型扣。
所谓悬梁式,其实是利用塑胶本身的挠曲变形的特性,经过弹性回复返回原来的形状。
扣位的设计是需要计算出来,如装配时之受力,和装配後应力集中的渐变行为,是要从塑料特性中考虑。
常用的悬梁扣位是恒等切面的,若要悬梁变形大些可采用渐变切面,单边厚度可渐减至原来的一半。
其变形量可比恒等切面的多百分之六十以上。
不同切面形式的悬梁扣位及其变形量之比较 扣位装置的弱点是扣位的两个组合部份:
勾形伸出部份及凸缘部份经多次重覆使用後容易产生变形,甚至出现断裂的现象,断裂後的扣位很难修补,这情况较常出现於脆性或掺入纤维的塑胶材料上。
因为扣位与产品同时成型,所以扣位的损坏亦即产品的损坏。
补救的办法是将扣位装置设计成多个扣位同时共用,使整体的装置不会因为个别扣位的损坏而不能运作,从而增加其使用寿命。
扣位装置的另一弱点是扣位相关尺寸的公差要求十分严谨,倒扣位置过多容易形成扣位损坏;相反,倒扣位置过少则装配位置难於控制或组合部份出现过松的现象。
不同材料的设计要点 PA 免时,特别的造模零件是可以达致以上效果。
另一种可得到倒扣效果的设计是考虑塑胶物料的特性。
利用塑胶柔软的变型,将倒扣的地方强顶出模具,但通常要注意不会把倒扣的地方括伤。
以下是扣位的计算方式。
尼龙的百份比在5%左右。
脱模角大一点和倒扣的地方离底部高时是可有10%。
PBT 扣位有分内扣和外扣,外扣的可利用分模面做成,内扣的可用变形方式或对碰方式出模。
内扣的可利用算式计算扣位百份率,一般在6%左右,玻璃充填的约在1%左右。
PBT外扣位设计方式PBT用对碰方式的内扣方式 PBT内扣位设计的算法 POM 扣位必须为弧形或转角弧度要大,方便塑胶成品容易滑过模具表面。
并且减少脱落时应力集中的现象。
内置扣位通常比外置扣位难脱模,因塑胶收缩时将模蕊抓紧,外置式的就刚好相反而易於脱模。
较高的模具温度使成品较热,易於弯曲变形而易於顶出模具,POM的扣位百份率可以比较大,可有5%。
POM扣位的计算方式 PS 基本上扣位的设计是不鼓励,但由於设计上的需要,则模具上使用凸轮、模蕊推出或其它装置以达成设计要求。
塑料件结构设计
1.胶厚(胶位):
塑胶产品的胶厚(整体外壳)通常在0.80-3.00左右,太厚容易缩水和
产生汽泡,太薄难走满胶,大型的产品胶厚取厚一点,小的产品取薄一点,一般产品取
1.0-2.0为多。
而且胶位要尽可能的均匀,在不得已的情况下,局部地方可适当的厚一点或
薄一点,但需渐变不可突变,要以不缩水和能走满胶为原则,一般塑料胶厚小于0.3时就很
难走胶,但软胶类和橡胶在0.2-0.3的胶厚时也能走满胶。
2.加强筋(骨位):
塑胶产品大部分都有加强筋,因加强筋在不增加产品整体胶厚的情况
下可以大大增加其整体强度,对大型和受力的产品尤其有用,同时还能防止产品变形。
加
强筋的厚度通常取整体胶厚的0.5-0.7倍,如大于0.7倍则容易缩水。
加强筋的高度较大时
则要做0.5-1的斜度(因其出模阻力大),高度较矮时可不做斜度。
3.脱模斜度:
塑料产品都要做脱模斜度,但高度较浅的(如一块平板)和有特殊要求的除
外(但当侧壁较大而又没出模斜度时需做行位)。
出模斜度通常为1-5度,常取2度左右,
具体要根据产品大小、高度、形状而定,以能顺利脱模和不影响使用功能为原则。
产品的
前模斜度通常要比后模的斜度大0.5度为宜,以便产品开模事时能留在后模。
通常枕位、插
穿、碰穿等地方均需做斜度,其上下断差(即大端尺寸与小端尺寸之差)单边要大于0.1以
上。
4.圆角(R角):
塑胶产品除特殊要求指定要锐边的地方外,在棱边处通常都要做圆角,
以便减小应力集中、利于塑胶的流动和容易脱模。
最小R通常大于0.3,因太小的R模具上很
难做到。
5.孔:
从利于模具加工方面的角度考虑,孔最好做成形状规则简单的圆孔,尽可能不要做
成复杂的异型孔,孔径不宜太小,孔深与孔径比不宜太大,因细而长的模具型心容易断、
变形。
孔与产品外边缘的距离最好要大于1.5倍孔径,孔与孔之间的距离最好要大于2倍的
孔径,以便产品有必要的强度。
与模具开模方向平行的孔在模具上通常上是用型心(可镶
、可延伸留)或碰穿、插穿成型,与模具开模方向不平行的孔通常要做行位或斜顶,在不
影响产品使用和装配的前提下,产品侧壁的孔在可能的情况下也应尽量做成能用碰穿、插
穿成型的孔。
6.凸台(BOSS):
凸台通常用于两个塑胶产品的轴-孔形式的配合,或自攻螺丝的装配。
当BOSS不是很高而在模具上又是用司筒顶出时,其可不用做斜度。
当BOSS很高时,通常在
其外侧加做十字肋(筋),该十字肋通常要做1-2度的斜度,BOSS看情况也要做斜度。
当
BOSS和柱子(或另一BOSS)配合时,其配合间隙通常取单边0.05-0.10的装配间隙,以便适
合各BOSS加工时产生的位置误差。
当BOSS用于自攻螺丝的装配时,其内孔要比自攻螺丝的
螺径单边小0.1-0.2,以便螺钉能锁紧。
如用M3.0的自攻螺丝装配时,BOSS的内孔通常做
Ф2.60-2.80。
7.嵌件:
把已经存在的金属件或塑胶件放在模具内再次成型时,该已经存在的部件叫嵌件
。
当塑胶产品设计有嵌件时,要考虑嵌件在模具内必须能完全、准确、可靠的定位,还要
考虑嵌件必须与成型部分连接牢固,当包胶太薄时则不容易牢固。
还要考虑不能漏胶。
8.产品表面纹面:
塑料产品的表面可以是光滑面(模具表面省光)、火花纹(模具型腔用
铜工放电加工形成)、各种图案的蚀纹面(晒纹面)和雕刻面。
当纹面的深度深、数量多
时,其出模阻力大,要相应的加大脱模斜度。
9.文字:
塑料产品表面的文字可以是凸字也可以是凹字,凸字在模具上做相应的凹腔容易
做到,凹字在模具上要做凸型心较困难。
10.螺纹:
塑胶件上的螺纹通常精度都不很高,还需做专门的脱螺纹机构,对于精度要求
不高的可把其结构简化成可强行脱模的结构。
11.支撑面:
塑胶产品通常不用整个面做支撑面,而是单独做凸台、凸点、筋做支撑。
因
塑胶产品很难做到整个较大的绝对平面,其容易变形翘曲。
12.塑胶产品的装配形式:
1.超声线接合装配法,其特点是模具上容易做到,但装配工序中需专门的超声机器,成本
增大,且不能拆卸。
超声线的横截面通常做成0.30宽0.3高的三角形,在长度方向以5-
10MM的长度间断2MM;
2.自攻螺丝装配法,其特点是模具上容易做到,但增加装配工序,成本增大,拆卸麻烦;
3.卡钩-扣位装配法,其特点是模具加工较复杂,但装配方便,且可反复拆卸,多次使用
。
卡钩的形式有多种,要避免卡钩处局部胶位太厚,还要考虑卡钩处模具做模方便。
卡钩
要做到配合松紧合适,装拆方便,其配合面为贴合,其他面适当留间隙。
4.BOSS轴-孔形
式的装配法,其特点是模具加工方便,装配容易,拆卸方便,但其缺点是装配不是很牢固
。
13.齿