纺织工艺课程设计一指导书101DOC.docx
《纺织工艺课程设计一指导书101DOC.docx》由会员分享,可在线阅读,更多相关《纺织工艺课程设计一指导书101DOC.docx(23页珍藏版)》请在冰豆网上搜索。
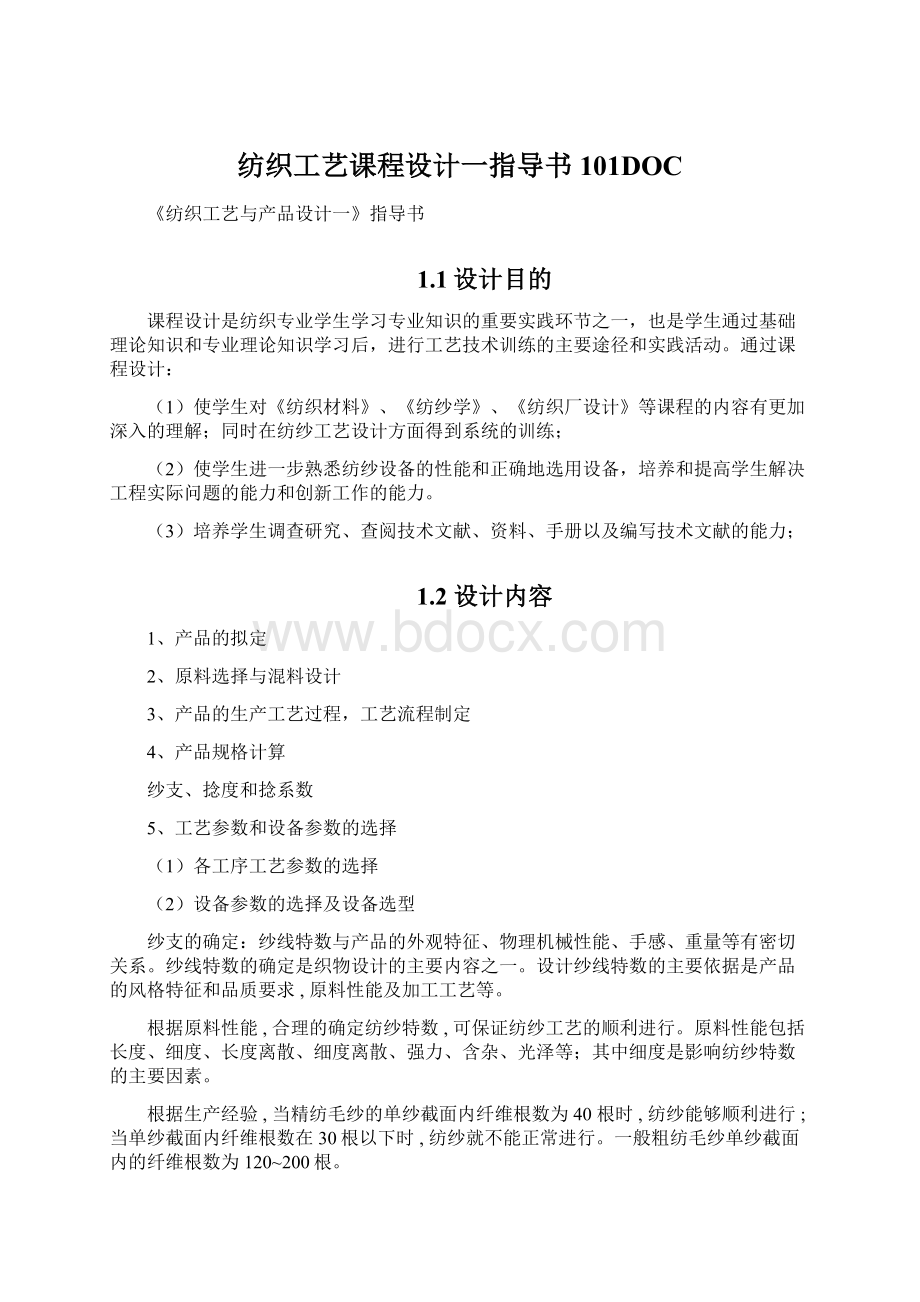
纺织工艺课程设计一指导书101DOC
《纺织工艺与产品设计一》指导书
1.1设计目的
课程设计是纺织专业学生学习专业知识的重要实践环节之一,也是学生通过基础理论知识和专业理论知识学习后,进行工艺技术训练的主要途径和实践活动。
通过课程设计:
(1)使学生对《纺织材料》、《纺纱学》、《纺织厂设计》等课程的内容有更加深入的理解;同时在纺纱工艺设计方面得到系统的训练;
(2)使学生进一步熟悉纺纱设备的性能和正确地选用设备,培养和提高学生解决工程实际问题的能力和创新工作的能力。
(3)培养学生调查研究、查阅技术文献、资料、手册以及编写技术文献的能力;
1.2设计内容
1、产品的拟定
2、原料选择与混料设计
3、产品的生产工艺过程,工艺流程制定
4、产品规格计算
纱支、捻度和捻系数
5、工艺参数和设备参数的选择
(1)各工序工艺参数的选择
(2)设备参数的选择及设备选型
纱支的确定:
纱线特数与产品的外观特征、物理机械性能、手感、重量等有密切关系。
纱线特数的确定是织物设计的主要内容之一。
设计纱线特数的主要依据是产品的风格特征和品质要求,原料性能及加工工艺等。
根据原料性能,合理的确定纺纱特数,可保证纺纱工艺的顺利进行。
原料性能包括长度、细度、长度离散、细度离散、强力、含杂、光泽等;其中细度是影响纺纱特数的主要因素。
根据生产经验,当精纺毛纱的单纱截面内纤维根数为40根时,纺纱能够顺利进行;当单纱截面内纤维根数在30根以下时,纺纱就不能正常进行。
一般粗纺毛纱单纱截面内的纤维根数为120~200根。
设单纱截面内纤维根数为mf时,则
式中:
Ntf一一纤维特克斯数;
Nt——纱线特克斯数。
而纤维特克斯数与纤维直径之间的关系为:
式中:
d一一纤维直径(μm);
β一一纤维比重(mg/mm3);
Ntf一一纤维特克斯数。
对羊毛纤维,纱线特数与纤维直径的关系可通过下式表示
羊毛品质支数与纺纱支数
品质支数(支)
平均直径(μm)
可纺支数
tex
公支
70
18.1~20.0
15.63以下
64以上
66
20.1~21.5
16.67
60
64
21.6~23.0
20~17.86
50~56
60
23.1~25.0~
20.83~20
48~50
58
25.1~27.0
23.81~20.83
42~48
56
27.1~29.5
31.25~23.81
32~42
改良毛64支以上
-
50~55.5
18~20
60(相当于一级毛)
-
62.5
16
二级毛(相当于52~58支)
-
100
10
三级毛(相当于46~48支)
-
125
8
四级毛(相当于36支)
-
200
5
捻系数的确定
(1)细纱捻系数
细纱捻系数的确定,主要决定于纱的用途、产品的特征及所用原料的品质。
①细纱用途不同,则选用的捻系数也不同。
经纱要求强力高,捻系数也应较高;纬纱在织造过程中所受张力较小,要求比较柔软,则捻系数可较低;针织用纱的捻系数还应偏低一些。
②细纱细度不同及所用原料不同,则选用不同的捻系数。
纱支越高、纤维长度越短,捻系数越大。
纯毛纱的捻系数大于混纺的捻系数。
而j昆纺纱的捻系数又大于纯化纤纱的捻系数。
原料品质高的,捻系数可适当降低一些。
③产品特征不同,捻系数也不同。
重缩绒的织物捻系数宜小;轻缩绒织物捻系数较大;不缩绒织物经纬纱可选用相同的捻系数。
缩绒织物纬纱捻系数可较低;薄爽织物捻系数应大;树脂整理的化纤织物捻系数可小些。
华达呢、单面花呢类产品,捻系数应大些。
(2)股线捻系数
股线捻度的大小将直接影响织物的外观和手感。
股线捻系数的选择,主要考虑以下几点。
①根据细纱捻系数,选用不同的股线捻系数,以使股线强力达到最大值;
②股线和细纱捻向相同时,股线捻系数可小些,否则手感硬、光泽差;股线和细纱的捻向相反时,股线捻系数可大些,便可得到较好的光择和手感。
粗纺纱常用捻系数
纱线类别
经纱
纬纱
毛混纺纱
再生纤维纱
备注
捻系数
线密度制
379.4~505.9
347.8~379.4
211.3~347.8
474.3~600.8
毛染色纱较本色纱捻系数高5%
公制
120~160
110~120
70~110
150~190
精纺纱常用捻系数(公制)
品种
单纱捻系数
股线捻系数
风格特征
全毛哔叽
80~85
110~130
柔软,光洁整理
全毛啥味呢
75~80
100~110
柔软,缩绒整理
全毛华达呢
85~90
140~160
结实,挺括
1.3设计方法及步骤
1.3.1工艺流程的制订
1、要与产品的特征和规格相适应
每一种产品,都有其特定的外观和技术要求,所用原料、纺纱制度、织物组织、染色方法、整理特点和光泽、手感等方面,都有一定的差异。
为此,应对计划生产的品种进行实事求是的分析,了解其独特的性质,以便制订相应的工艺流程。
2、使产品的特殊需要与可能得到的技术条件相适应
例如,近年来,混纺和混色产品日益增多,对于产品的外观,也提出了很多的要求。
诸如此类,在确定工艺流程时,既要充分考虑产品的特殊需要,又要注意实际条件的可能。
不加分析地一味追求某些高精尖的设备,在实际生产中往往只能取得相反的结果。
一个工厂不可能满足每一种产品的每一个特殊要求,否则,就会有相当数量的特殊加工设备经常处于停机状态,不能充分发挥作用。
粗梳毛织物的生产工艺流程:
可分为原料初步加工、纺织工艺和染整工艺三部分。
精梳毛织物生产的工艺流程:
毛条制造、条染复精梳、前纺、后纺、织造、染整工艺流程
1.3.2工艺参数和设备参数的选择
(1)根据精、粗纺产品工艺流程完成各工序工艺参数的选择;
(2)设备参数的选择及设备选型。
2.加工系统
2.1粗梳毛纺系统
洗毛初加工→和毛加油→梳毛→细纱→(蒸纱)→络筒
2.2精梳毛纺系统
(1)条染产品流程
原毛初加工→毛条制造→条染复精梳→前纺→后纺→准织→染整→成品
典型的条染产品纺纱工艺流程:
选毛配毛→开洗烘→和毛加油→梳毛→毛条头道针→毛条二针→毛条三针→精梳→毛条四针→毛条末针(毛条制造)松球→装筒→条染→脱水→复洗→混条针梳→前纺头针→毛条三针→复精梳→毛条四针→混条→毛条末针(条染复精梳)混条→前纺头针→前纺二针→前纺三针→前纺四针→粗纱(前纺)细纱→并线→捻线→(蒸纱)→络筒(后纺)(自动络筒→电子并线→倍捻)
(2)匹染产品流程
原毛初加工→毛条制造→前纺→后纺→准织→染整→成品
典型匹染产品纺纱工艺流程:
选毛配毛→开洗烘→和毛加油→梳毛→毛条头道针梳→毛条二针→毛条三针→精梳→毛条四针→毛条末针→混条→混条→前纺头针→前纺二针→前纺三针→前纺四针→粗纱→细纱→并线→捻线→(蒸纱)→络
筒→(自动络筒→电子并线→倍捻)
2.3半精纺系统
原毛→初加工→洗净毛→和毛→梳毛→针梳2-3道→粗纱→细纱→毛纱→并、捻、络(含蒸纱)→毛股线
3.精梳毛纺工艺设计
3.1原料
羊毛,特种动物毛、化纤等
3.2毛条工艺设计
毛条制造工艺设计的内容包括原料选用、工艺流程的确定、加油量和油水比的确定、主要设备的工艺计算和主要工艺参数的确定。
3.2.1配毛
原料的选用应考虑生产毛条的品种和采用的加工系统,如纯毛条、化纤条或羊毛与化纤混梳条,采用法式加工系统还是英式加工系统。
(1)配毛方式
精梳毛纺配毛分两个阶段,第一阶段在毛条制造,采用梳条配毛(散毛选配),第二阶段在前纺毛条搭配。
(2)梳条配毛原则
①长度选择。
一般选毛丛长度较短的一种毛为主体毛。
主体毛应占总配毛成份的70%以上,当以毛丛较长的毛为配合毛,可掺少量较短毛。
配合毛的毛丛长度不得超过主体毛毛丛长度20mm。
长度在95mm以上的细支毛不宜作主体毛。
对质量差异不大,毛丛长度相差10mm以内的羊毛,可以进行列主体配毛。
②细度选择。
一般配合毛与主体毛平均细度差异控制在2μm以内。
注意:
加工会使条中羊毛变粗
③粗腔和弱节毛的含量。
粗腔含量加工后会减少。
注意:
控制弱节毛节含量。
④草刺。
根据条件适当掌握。
⑤色泽和手感。
原料色泽和手感应以较接近的互相并合。
3.2.2和毛加油设计
(1)和毛
和毛机B261:
将原料开松、均匀混合
工艺参数:
相关机件间的速比、隔距原则同梳理机原理。
为使原料开松混合均匀,一般原料要经过多次和毛。
(2)加油
目的:
增加纤维间的润滑,减少纤维在开松梳理过程中的损伤;减少生产中静电;增加纤维的柔软性、抱合性。
油剂一般由油和抗静电剂等组成。
油一般为矿物油或植物油,油须乳化,加油大多是在和毛机出口处输送时喷洒。
一般洗净毛:
残脂率在0.6%以下时加油率为0.7%;残脂率在0.6%以上时加纯油率为0.5%;油水比一般为1:
4~1:
5。
化纤:
加纯油率为0.5~0.8%,油水比为1:
2~1:
3
混料梳毛的上机回潮率应不同:
弹性针布(19~24%)比金属针布(16~20%)多加水。
羊毛比化纤多加水(合纤应加抗静电剂)
3.2.3加油计算举例
投料1000kg羊毛,实际回潮率为15%,含油为0.6%,要求和毛后羊毛回潮率达到25%,含油率达到2%。
求需加油水量(和毛油,油水比1:
4)
①回潮15%时羊毛的含水率=(1×实回)/(1+实回)=15%/115%=13%
②1吨毛中含水量=1000×13%=130kg
③毛干重=1000-130=870kg
④回潮为25%时羊毛应含水=干重×回潮=870×25%=217.5kg
⑤羊毛尚需加水=217.5-130=87.5kg
⑥羊毛尚需加油=1000×(2%-0.6%)=14kg
⑦加和毛油量=14×(1+4)=70kg
⑧和毛油中有水=14×4=56kg
⑨和毛油中还需加水量=87.5-56=31.5kg
3.2.4梳毛工艺设计
(1)隔距设计
①选择隔距的原则。
首先考虑原料种类和性质,如细而卷曲的羊毛,梳理较困难,采用小隔距,加强梳理;其次,根据两滚筒之间作用性质而定,分梳作用是基本作用,应作为校对隔距的重点;考虑隔距时,还应该按照羊毛在梳毛机内前进方向逐渐变小,以保证逐步加强梳理作用。
②分梳作用区隔距选择。
在分梳作用区内的锡林与工作辊间隔距,应与混料的松解程度相适应(渐小),一般为靠后几个相差较大,越向前差距逐渐减小;锡林与道夫间隔距,应小于与其最近的工作辊隔距;喂入罗拉与胸锡林之间隔距应为全机最大处。
③剥取作用区隔距的选择。
剥取作用区的隔距:
在剥毛辊与工作辊之间的隔距可适当大些,以能顺利剥取为度;由后向前各剥毛辊的隔距可以由大变小,在同一锡林上也可以采用同一隔距。
最大、最小隔距可参考相关设备参数。
(2)梳毛机速度比的设计
梳毛机速比的确定:
大锡林的速度是梳毛机的基本速度,其他机件的速度都随其而变化。
锡林速度的大小直接关系到梳毛机的分梳效能,影响分梳效能的因素除了隔距外,还有工作辊速比,又称凝聚倍数,可通过调整变换齿轮齿数来改变。
一般可参考以下规则:
①梳理细羊毛时,应采用较小的道夫和工作辊变换齿轮以加大速比,加强梳理;梳理粗羊毛时则采用较大的道夫和工作辊变换齿轮,即采用小速比。
②当梳理化纤等较长纤维时,可用较大的道夫和工作辊变换齿轮,以减小速比保护纤维长度。
③当要求提高梳毛机产量以满足后工序需要时,可适当加大道夫和工作辊变换齿轮,以减小速比,减少毛层厚度。
④在毛条中的毛粒数量不超过规定时,应尽量减小速比以保护纤维。
⑤对于抱合力较差的纤维,可采用较小的道夫和工作辊变换齿轮以加大速比,避免工作辊上有毛网剥落的现象。
(3)梳毛机出机条重量设计
不同类型的梳毛机其出条重量不同,一般控制在10~20克/米,实际生产可遵循以下原则:
①细羊毛的条重可轻些,粗羊毛可重些。
②化纤条易梳的可重些,难梳的则轻些。
③使用金属针布时可重些,使用弹性针布时可轻些。
④梳毛机的出条重量视毛网的质量而定,使毛网中的毛粒保持最小,降低喂入重量和出条重量,可使纤维获得充分梳理,减小毛粒。
如果毛粒含量能保持在允许范围内,适当提高出条重量可以增加产量。
(4)梳毛条质量设计
①毛网要清晰,纤维分布均匀,无破洞和云斑,要尽量减少纤维在长度上的损伤。
②对毛网中的毛粒有一定限制:
64s~70s毛条<30只/克,60s毛条<20只/克。
③梳毛机的条重差异,集体成球时不大于±1克;单独成球时不大于±0.5克。
④出机毛条疵点有一定要求,梳毛的疵点主要为毛粒、草屑和毛片。
⑤出机毛条回潮应有一定要求。
3.2.5针梳工艺设计
加工细羊毛时,采用的针梳机道数比较多;加工粗羊毛或化纤时,采用针梳机的道数可少些。
(1)加工流程确定
①加工细羊毛条时采用正常工艺,工艺流程如下:
梳毛→头针→二针→三针→精梳→四针→末针。
②加工粗羊毛或化纤条时,可缩短,采用上述工艺流程而跳过二针;加工供染色的毛条时,只到四针即可。
(2)牵伸倍数、出条重和并合根数确定
①牵伸倍数。
针梳机的牵伸倍数,由头针到三针逐步加大,因梳毛机刚下机的毛条结构松散、强力低,纤维排列紊乱,平行伸直度差,故头针采用较小的牵伸倍数(6倍以下),否则会造成条干不匀;二针是在头针对纤维梳理顺直的基础上进行工作的,这时毛条结构和纤维状态已得到改善,故可提高其牵伸倍数(一般为6~7倍);三针下机毛条是供应精梳机的,要求纤维有较好的平行顺直程度,故牵伸倍数可大些(一般都在8倍左右),但要注意条干均匀;四针的牵伸倍数应比三针的小(一般在7倍左右),末针的牵伸倍数可逐步提高(一般在8倍左右);
②出条重量。
针梳机的出条重量主要是控制三针和末针的出条重量。
三针的出条重量有限制,一般在7~12克/米之间,最大不超过12克/米(否则喂入精梳机毛条过厚,易产生拉毛现象);末针的下机毛条是成品毛条,其重量应符合标准规定。
③并合根数。
增多针梳机的并合根数,有助于改善毛条条干及结构的均匀度。
但并合根数受针箱喂入负荷与机器最大并合根数的限制,而且过多的并合根数又会增加牵伸负担,牵伸倍数过大又会影响毛条条干。
在确定牵伸倍数出条重量、并合根数时还应考虑前后机台平衡。
在确定牵伸倍数、并合根数和出条重量时,还应该通过计算考虑前后机台供应平衡的问题,如供应不平衡,除适当改变出条速度外,还可对喂入负荷和出条重量作适当调整。
(3)隔距、速比、罗拉加压和针板规格
①隔距。
针梳机的隔距分总隔距和前隔距两种,总隔距应大于最长纤维的长度,一般是不可变动的;前隔距是指前罗拉中心线到第一块针板钢针之间的距离。
在这里的隔距主要是指前隔距,其一般按原料长度来设定。
加工较长纤维时可大些,加工短纤维时可小些。
前三针出条重量较轻,前隔距可小些,有利改善纤维的伸直度。
后一针毛条状态较好,前隔距可适当放大以减少损伤,范围一般在35~55mm之间。
②后速比与前张力牵伸。
针梳机的后速比,是指后罗拉到针板之间的牵伸,而前张力牵伸是指出条罗拉与前罗拉之间的牵伸。
前张力牵伸主要影响条干,后速比不仅影响条干,而且关系到针板负荷。
针梳机后速比一般都小于1,大约在0.85~1之间。
③罗拉加压。
压力大小与原料种类各牵伸倍数有关。
④针板规格。
针板号数应随原料品种和加工流程而变化
(4)针梳机毛条质量要求
①条干均匀无明显粗细节。
②出条重量符合要求。
理条毛条重量公差为±1克/米,整条±0.5克/米。
③重不匀。
支数毛条<3%,级数毛条<4%
④毛条表面光洁。
⑤毛粒毛片草屑要少。
(5)针梳毛条着疵点产生的原因
①条干不匀和粗细节。
主要是牵伸倍数过大,前隔距过大,接头不良,罗拉绕毛或运转不灵。
②重不匀。
主要是并合根数少,喂入毛球重不匀大。
③毛粒增加。
头二针牵伸倍数过大,针板状态不良。
清洁工作差,退绕毛球剥皮,通道不光滑。
④毛条表面发毛。
毛条回潮低产生静电,抱合力差,机体件封毛。
⑤条子牵不开出硬头。
主要是毛条进入梳箱时后张力太大,某些化纤长度长,磨擦系数大,牵伸力大握持力不足,喂入负荷大,毛条集中重叠。
3.2.6精梳工艺设计
纺高支纱时可采用正常的精梳制条工艺,纺低支纱时可采用半精梳制条工艺。
精梳工艺参数主要包括喂入根数、喂入长度、拔取隔距、出条重量和针号、针密等。
(1)喂入根数和总喂入量
当喂入根数一定时,在梳针强度允许和不影响梳理质量的情况下,增加喂入毛条的重量可以提高精梳机的产量。
各型号精梳机均有自身的最大喂入根数及总喂入量限制。
通常,增加喂入根数有利于毛片并合均匀。
应在全面权衡梳理质量、产量、工作能力等方面,确定喂入根数和总喂入量。
如B311型喂入20根,总喂入量不超过200克/米,喂入条重一般7克/米。
(2)喂入长度
对梳理质量和产量均有影响,喂入长度大,产量可提高,但梳理负担加重,易产生拉毛现象,主要考虑随纤维原料的不同而异。
粗长毛喂入长度大一些(10),细短毛小一些(6.4)。
(3)拔取隔距R
对除去的短纤维长度和精梳落毛率有直接关系。
加工长纤维时,拔取隔距要大。
加工细短纤维时,反之。
其大小取决于原料长短,同时结合毛网质量和制成率进行。
常用26.28.30mm三种
(4)出条重量
精梳机出条重量随原料不同而变化,一般在17~20克/米。
加工细毛时轻一些。
(5)针号及针密
为保证梳理质量,一般随原料状态不同(原料种类和纤维细度)选用相应的针号和针密,包括圆梳梳针和顶梳梳针的选用。
圆梳梳针选用1~9排不变,10~18排随原料而变。
顶梳根据原料的种类,纤维细度而变化。
(6)精梳毛条的质量
①毛网正面毛粒多。
喂入负荷太大或喂入毛条重不匀,毛片厚薄不匀造成圆梳梳理不良,钳板与圆梳梳针间距离过大,部分须丛梳理不充分,圆梳针梳起始梳理位置不当,造成对须丛控制不良影响,梳理小毛刷位置不对,使纤维浮于针面。
梳针残缺,针密不够,梳针不清洁,充塞纤维杂质。
拔取隔距过小喂入长度过大,梳理次数不足。
②毛网反面毛粒多。
顶梳位置太高,往往同时发生拉毛。
顶梳抬高太早顶梳不洁,缺针或针密不够。
③圆梳拉毛。
钳板啮合不严,对须丛握持不牢。
顶梳插入太深,喂入长度太大,小毛刷位置太低。
喂入毛条接头不良,有捻度。
圆梳缺梳、歪针、针尖毛刺、皮板过紧,拔取罗拉加压不足或弯曲。
④粗细节严重。
喂入不正常,毛条搭接不良,拔取皮板厚薄不匀等毛条制造中梳毛、针梳、精梳工艺参数为重点。
毛条工艺设计举例
根据原料、工艺流程、设备性能确定其工艺参数。
然后以毛条(成品)重从末道推算到和毛油(前后道平衡)
①原料:
66s毛,长度56.8,细度21.55,含油0.89%,数量6645kg,比例100%。
②和毛:
加油量0.6%,加水量13%,梳毛机上机回潮23%
③梳毛:
出条重38g/m
A272A隔距:
工作辊与锡林:
2.67,1.7,1.22,0.79,0.69,0.61,0.53,0.48,0.38
剥毛辊与锡林:
1.7,1.09,0.84,0.69,0.61,0.53,0.48,0.43,0.38
打草辊:
1.22,0.69,0.48
上道出条单重=本道喂入单重,
本道喂入条单重×并合根数/牵伸倍数=本道出条单重×出条数
表1针梳和精梳各环节工艺参数
机型
单重(g/m)*并合根数
牵伸
前隔距
出条重g/m
梳针号数
B302
13*10
5.6
35
23
5
B303
23*6
6.2
35
22
5
B304
22*6
7.3
35
17/2
7
B311C
17/2*9*2
9.5
拔取26
17
顶梳27
B305
17*8
6.8
40
20
10
B306
20*7
7
40
20
13
3.3前纺工艺设计
3.3.1条染复精梳工艺设计
工艺流程选择
(1)多色号品种的混合次数大于单色号品种
(2)多混纺成分品种的混合次数大于大衣成分品种或化纤混纺品种
(3)原料成分或颜色成分差异较大混纺产品的混合次数大于差异较小品种
(1)松球
退捻,定量,密度下降。
质量:
松紧适中,成形良好,重量均等
(2)毛条染色工艺
①染料选择——纤维性质、用途,色泽成本货源,染色性能
②拼用染料——染色性接近、染料个数少
③随时对色光
(3)复洗工艺
复洗工序应根据加工原料和产品要求而定,一般都用在支数毛条和染色毛条的加工流程中,对级数毛条可不采用。
在流程上有两种方案,对通常原料,采用精梳后复洗;另一种则采用精梳前复洗。
毛条经复洗后纤维较平顺,有利于精梳加工,可减少纤维损伤,落毛量也较少。
生产实践证明精梳前复洗的制成率可提高1%~2%,纤维长度约增加1~2毫米,故较适宜于细短羊毛的加工,但不适宜草刺含量多的羊毛,对含草刺多的毛条,先经精梳可提高毛条的洁净度,而且有利于复洗工作。
表2复洗工艺
原料
羊毛
涤、腈、锦
处方及工艺条件
用料(g/L)
温度(℃)
用料(g/L)
温度(℃)
第一槽
209
2~5
45~55
209
1~3
45~55
第二槽
活水
40~55
活水
40~50
第三槽
水化白油
平平加
各10~15
45~55
水化白油
平平加
各5~10
45~55
色条复洗要求
浮色羊毛:
4级涤:
3.5级
回潮18±2%<2%
含油1±2%0.3±0.1
手感滑松爽
(4)复精梳工艺——再次精梳
目的:
纤维色泽混合、去毛粒、短毛、草屑,前后三针工艺内容和制条相同
(5)条染复精梳产品质量要求
质量要求:
毛粒3-4个/克,毛片重不匀3.5%,浮色洗净程度
质量控制:
①条染工序
a染羊毛—酸性媒介
注意点:
化料—仔细,PH—高则色不正,低则色花,温度—上染曲线,助剂用量—少则色不正、牢度差;多则糙,1:
1~0.25:
11。
放水时间长;国产毛染料比进口用量要少
b染涤条用分散染料
注意:
松球,PH5.5:
化料好,后处理:
缸内冲洗
c锦纶大多用中性染料
注意:
松球,PH6~7:
化料好,沸煮法,80℃以上升温要慢,75℃以上染快
②复洗工序
控制好含油及回潮,除洗剂还需加助剂、平平加、RN。
助剂用量视条染后浮色定
c复精梳工序
减少化纤结并、发涩,
精梳—轻定量,少20~30%,低车速。
针梳—少喂入、大隔距、小加压、小针密
牵伸6~8倍,纯毛>混纺,细羊毛>粗羊毛
3.2.2前纺工艺设计
针梳与毛条制造差不多,是纺出细纱品质优劣的关键,应根据品种和性能,产品的规格和质量要求,结合纺纱支数、设备能力选用合理道数和工艺参数。
(1)混条
混纺成份比例要均匀、稳定,混色均匀,一般在前纺第一道或条染复精梳进行。
在出口处加喷嘴补加油。
①加油量计算例
设毛涤50/50混纺条1000kg。
纺60s纱。
羊毛原含油为0.8%,涤条原含油0.1%,要求毛涤在前纺中含油达0.7%。
混条机出条速度60m/min。
出条单重20