冶炼烧结喷煤工艺.docx
《冶炼烧结喷煤工艺.docx》由会员分享,可在线阅读,更多相关《冶炼烧结喷煤工艺.docx(22页珍藏版)》请在冰豆网上搜索。
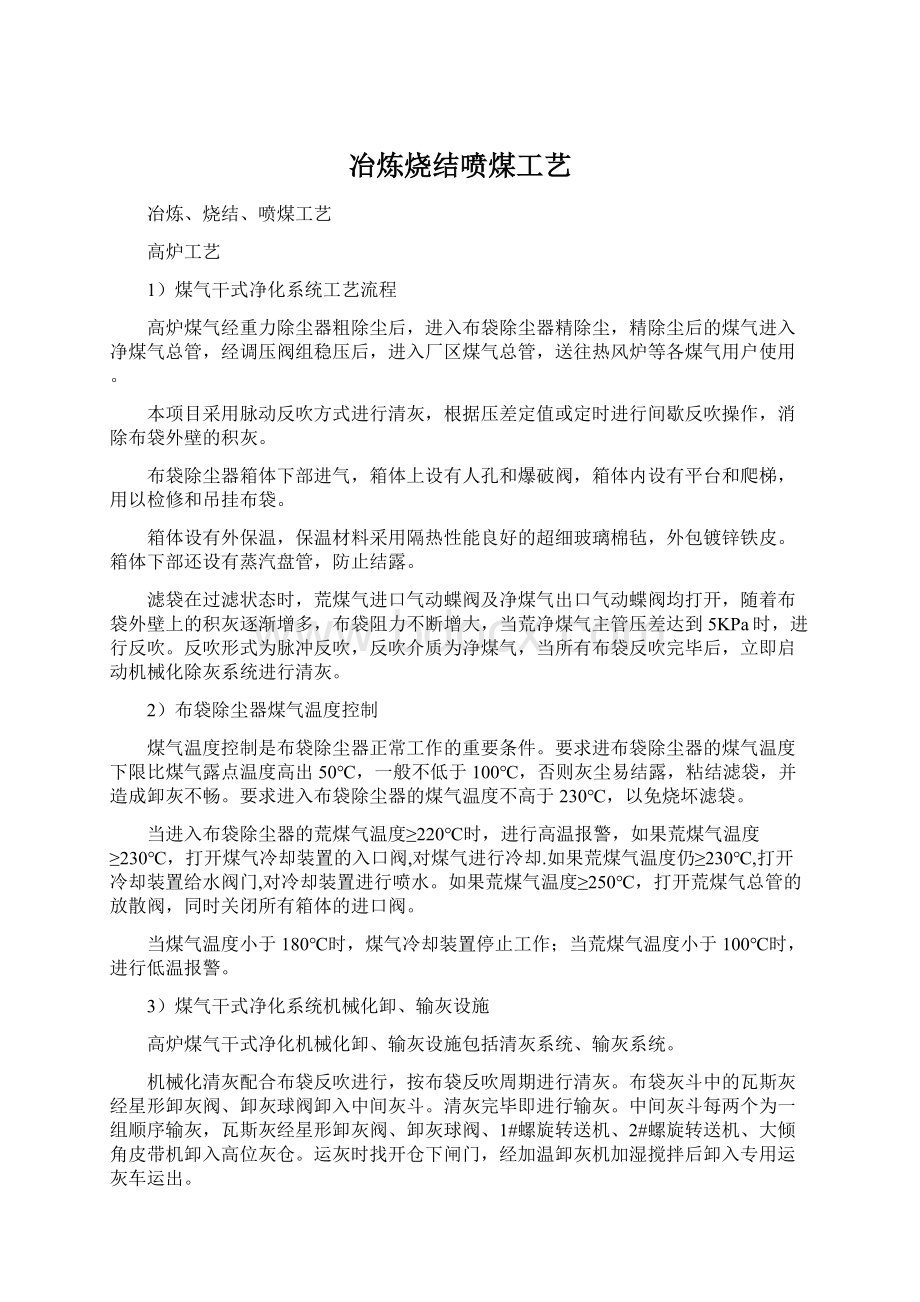
冶炼烧结喷煤工艺
冶炼、烧结、喷煤工艺
高炉工艺
1)煤气干式净化系统工艺流程
高炉煤气经重力除尘器粗除尘后,进入布袋除尘器精除尘,精除尘后的煤气进入净煤气总管,经调压阀组稳压后,进入厂区煤气总管,送往热风炉等各煤气用户使用。
本项目采用脉动反吹方式进行清灰,根据压差定值或定时进行间歇反吹操作,消除布袋外壁的积灰。
布袋除尘器箱体下部进气,箱体上设有人孔和爆破阀,箱体内设有平台和爬梯,用以检修和吊挂布袋。
箱体设有外保温,保温材料采用隔热性能良好的超细玻璃棉毡,外包镀锌铁皮。
箱体下部还设有蒸汽盘管,防止结露。
滤袋在过滤状态时,荒煤气进口气动蝶阀及净煤气出口气动蝶阀均打开,随着布袋外壁上的积灰逐渐增多,布袋阻力不断增大,当荒净煤气主管压差达到5KPa时,进行反吹。
反吹形式为脉冲反吹,反吹介质为净煤气,当所有布袋反吹完毕后,立即启动机械化除灰系统进行清灰。
2)布袋除尘器煤气温度控制
煤气温度控制是布袋除尘器正常工作的重要条件。
要求进布袋除尘器的煤气温度下限比煤气露点温度高出50℃,一般不低于100℃,否则灰尘易结露,粘结滤袋,并造成卸灰不畅。
要求进入布袋除尘器的煤气温度不高于230℃,以免烧坏滤袋。
当进入布袋除尘器的荒煤气温度≥220℃时,进行高温报警,如果荒煤气温度≥230℃,打开煤气冷却装置的入口阀,对煤气进行冷却.如果荒煤气温度仍≥230℃,打开冷却装置给水阀门,对冷却装置进行喷水。
如果荒煤气温度≥250℃,打开荒煤气总管的放散阀,同时关闭所有箱体的进口阀。
当煤气温度小于180℃时,煤气冷却装置停止工作;当荒煤气温度小于100℃时,进行低温报警。
3)煤气干式净化系统机械化卸、输灰设施
高炉煤气干式净化机械化卸、输灰设施包括清灰系统、输灰系统。
机械化清灰配合布袋反吹进行,按布袋反吹周期进行清灰。
布袋灰斗中的瓦斯灰经星形卸灰阀、卸灰球阀卸入中间灰斗。
清灰完毕即进行输灰。
中间灰斗每两个为一组顺序输灰,瓦斯灰经星形卸灰阀、卸灰球阀、1#螺旋转送机、2#螺旋转送机、大倾角皮带机卸入高位灰仓。
运灰时找开仓下闸门,经加温卸灰机加湿搅拌后卸入专用运灰车运出。
4)高炉煤气净化后送入电厂(不在本次评价范围之内)、热风炉和烧结使用。
高炉煤气的主要成份是一氧化碳(27~30%)、氢气(1.5~1.8%)、氮气(55~57%)、二氧化碳(8~12%),发热量为850~950kcal/Nm3,燃点700℃,主要性质是无色无味,有剧毒易燃易爆。
高炉煤气的使用和管道敷设情况见下表。
表2.4-1高炉煤气的使用和管道敷设情况表
序号
名称
所在位置
管径mm
敷设方式
压力MPa
使用量104m3/h
1
煤气管道
与高炉相连的管道
DN1600
架空
0.15
12
2
与布袋除尘器相连的管道
DN700
架空
0.015
12
3
送入电厂的管道
DN1400
架空
0.015
5.4
4
与热风炉相连的管道
DN1200
架空
0.015
4.8
5
送入烧结的管道
DN700
架空
0.015
1.8
2.4.1高炉喷煤设施
1)喷吹煤种
喷吹煤种为无烟煤。
2)高炉喷煤工艺
原煤由装载机经煤棚运入原煤仓,转运前要对原煤进行破碎、筛分、除铁等处理。
给煤机按照生产的要求均匀地将原煤喂入中速磨煤机,由热风烘干,磨细的煤粉随烟气一起至布袋收尘器内进行气粉分离,煤粉经筛分后落入煤粉仓,尾气由主排粉风机排入大气。
煤粉仓内煤粉经串联的煤粉切断阀和高压密封阀进入喷吹罐,喷吹罐内煤粉经流化装置流化后,沿喷吹管道送至高炉炉台,经炉前盘式分配器、喷枪喷入高炉各风口。
3)喷煤系统组成
高炉喷煤系统由四大部分组成,即原煤储运系统、制粉系统、喷吹系统、外网风、水、电、气系统。
主要设备:
烟气升温炉(自制)、中速磨、引风机、主排粉风机、喷吹罐、煤粉分配器、空压机等。
4)煤棚
喷煤车间南侧的煤棚为直接供煤场地。
外购的精煤运到煤棚或煤场,卸到煤场的精煤用轮式装载机集中堆高、倒堆或者再次装车运到煤棚,在此不进行配煤作业。
5)中速磨
1台33.5t的中速磨,配套的设施有风量为80500m3/h的主排粉风机,干燥煤粉所需要的高温引风机1套(90kW)、烟气炉1座及其配套设施。
6)喷吹系统
喷吹系统包括喷吹罐、供气(氮气和空气)、喷吹管线、分线器、煤枪以及喷煤计量、安全监测等。
高炉喷吹煤粉输送按浓相输送进行设计,在保证煤粉喷吹均匀、稳定喷吹的前提下,尽管各高炉的喷吹距离不同,总管的煤粉输送浓度达到20kg/kg以上。
(1)喷吹工艺流程
煤粉喷吹工艺见图2.3-3。
图2.3-3喷吹工艺流程图
喷吹系统由喷吹罐、煤粉给煤器、喷煤总管、过滤器、煤粉分配器、喷煤支管、煤枪、氮气及空气供气、喷煤调节控制和安全联锁系统等组成。
(2)喷吹罐
喷吹罐为并列罐布置。
并列罐的特点是喷吹工艺简单、总量计量准确、并且设备少,土建投资低。
并列罐喷吹工艺是两个喷吹罐轮换对一座高炉喷吹煤粉,一个喷吹罐喷吹煤粉时,另一个喷吹罐放散、装煤、充压,两个喷吹罐轮换喷吹。
煤粉仓下配设四个喷吹罐,两个喷吹罐一组对一个高炉实现连续喷煤,共计四个喷吹罐可以对两座高炉喷煤。
喷吹罐几何容积为16m3,满罐时大约可以装7吨煤粉,在喷煤比150/t·Fe时对高炉喷吹,40分钟左右换一次罐,不至于使喷煤过程的倒罐操作很频繁。
喷吹罐压力1.0MPa,工作压力为0.8MPa。
充压、补压、流化均使用氮气,煤粉喷吹用气使用压缩空气。
喷吹罐支撑在三个5吨的压力传感器上,使用电子秤进行喷吹罐的称重和喷煤量计量,为了计量准确,喷吹罐与煤粉仓以及所有与喷吹罐连接的管路均用金属软管或波纹管连接,喷吹罐并设置校秤装置。
喷吹罐泄压放散的气体排至布袋收粉器或直接排放。
喷吹罐喷吹形式为流化上出料、补气调节,
(3)喷煤管路
喷煤总管根据高炉距离的远近和现场条件铺设,管路的开始段直径DN65mm,在高炉附近管径扩大为DN80mm,通过输煤总管扩径减少喷煤输送过程的压力损失。
喷煤管路设计煤粉堵塞吹扫返吹管路,使清堵吹扫的煤粉被反吹回布袋收粉器,避免清堵时的煤粉外泄周围环境。
(4)分配器与煤枪
分配器
根据高炉热风压力在设定的喷吹压力下将煤粉从喷吹罐下部的给煤器连续地送入喷煤总管,通过设置在高炉相应平台上总管分配器分配给喷煤支管再经煤枪喷进高炉风口。
安装时尽量使分配器之后的喷煤支管当量长度相近,以保证煤粉的均匀分配。
煤枪
分配器之后的喷煤支管直径为φ20mm,煤粉通过煤枪均匀喷进高炉的各个风口。
煤枪在不喷煤的由压缩空气冷却,或手动拔出更换。
煤枪的入口设置逆止阀,防止拔枪时热风倒流喷出。
2.3.1烧结生产工艺
烧结机系统工艺流程是从原料进厂到成品输出,包括燃料接受、燃料破碎、锰矿接受、配料、混合、制粒、滚煤、烧结、冷却、筛分整粒、成品制样、物理检验及输出等全部工艺过程。
烧结工艺流程见图2.3-1:
锰矿生石灰熟白云石返矿燃料
破碎
配料
混合
燃料分加
空气煤气制粒
点火滚煤铺底料
烧结
烧损
除尘热破碎
散料
抽风冷却
烟囱一次筛分
>12mm<12mm
排入大气二次筛分三次筛分
>20mm5-12mm<5mm
12-20mm
成品
图2.3-1烧结厂工艺流程图
2.3.2高炉冶炼工艺
锰铁合金铁冶炼采用2×630m3高炉,高炉利用系数0.78t/m3·d,全年运行时间350天。
(1)工艺流程
其生产工艺流程为:
将烧结矿、块矿、白云石(熔剂)、焦炭(燃料、还原剂)经配料、称量后,由皮带机上料,经斜桥料车送至高炉炉顶后加入高炉炉体内,由热风炉向高炉炉膛鼓入热风助焦炭燃烧,焦炭燃烧生成高炉煤气,炽热的煤气在上升过程中把热量传递给炉料进行冶炼,原、辅料随着冶炼过程的进行而下降。
在炉料下降和煤气上升过程中,先后发生传热、还原、熔化、渗碳等过程使锰铁矿还原生成锰铁水;同时烧结矿等原料中的杂质与加入炉内的熔剂相结合生成了炉渣。
为了降低能耗,提高冶炼效率,冶炼过程配有喷煤工艺,将无烟煤粉磨合格后通过输送带送入煤仓,由压缩空气硫化后送到炉顶的给煤口中,经喷吹系统喷入炉内。
喷吹系统由空压机、氮气系统、助燃风机、喷煤枪组成。
上料系统采用双料车斜桥上料,斜桥角度50°46′17″。
(1)料车有效容积主要取决于焦炭批重及矿石批重,正常焦炭批重为5t,每批料由两车焦和两车矿组成,料车有效容积为5.5m3。
(2)卷扬机室除布置料车卷扬上,还布置2台炉顶探尺卷扬机。
卷扬机室设1台10t电动单轨吊,用于料车卷扬机的安装和检修。
(3)卷扬机有自动和手动两种操作方式,自动控制设施设在槽下电气室,卷扬机操作室设有手动操作台。
卷扬机与槽下供料系统及炉顶装料设备按程序自动保护装置以确保设备安全运行。
高炉冶炼是连续生产,生成的铁水和炉渣不断地积存在炉缸底部,到一定时间后打开高炉出铁口、出渣口,进行出铁出渣。
从出铁口出来的铁水通过高炉出铁场的铁沟、撇渣器、摆动流嘴等流入铁水罐,热装送往铸铁机。
高炉渣由出铁场的渣沟流出,采用炉前水冲渣法处理,形成的高炉水渣再进行综合利用。
高炉冶炼时产生的高炉煤气,经干法除尘净化后供热风炉、烧结、高线厂、特钢厂、发电厂等作燃料使用。
锰铁合金高炉冶炼工艺流程图如下:
见图2.3-2
块铁烧结矿熔剂焦炭
图2.3-2高炉冶炼工艺
(2)生产设施
生产主体工艺设施包括:
原燃料贮运系统、上料系统、炉顶系统、炉体系统、风口平台出铁场系统、热风炉系统、煤气除尘系统、煤粉喷吹系统、渣处理系统。
辅助工程设施主要包括:
燃气设施、热力设施、采暖、通风及除尘设施、给排水设施、供配电机传动、自动化仪表过程检测与控制、高炉基础自动化系统、电信设施、机修及检化验设施。
2.3.4主要生产设备设施
(1)烧结系统主要设施
主要包括燃料破碎室、配料室、混合室、制粒式、燃料外配室、滚煤室、烧结室、烧结矿筛分室、成品取样室、烧结成品槽、机头电除尘器、主抽风机室。
1)燃料破碎
破碎室设有φ610×400mm对辊破碎机碎和φ900×700mm四辊破碎机组成的两套破碎系统。
焦粉和无烟煤由汽车运输至燃料破碎室,由Q=5t桥式抓斗起重机给至矿槽中储存。
矿槽下采用皮带机排料,无烟煤给至对辊破碎机,经过辊破碎机破碎后的燃料粒度为≤20mm,由皮带机输送到细碎室,再经四辊破碎机将其破碎成≤3mm的合格粒度;焦粉则不经粗碎直接由皮带机给至细碎室,由单设的一台四辊破碎机破碎。
燃料经破碎后,由皮带机运至配料室。
2)配料室
烧结用锰矿料和燃料由皮带机输送至配料室。
生石灰和熟白云石用散装罐车运输,风力输送入仓。
采用自动重量配料法,原料和冷返矿采用φ2500mm园盘给料机给料,配料电子秤称量;燃料采用定量给料机称量给料;生石灰和熟白云石采用螺旋称称量给料,其中生石灰经消化螺旋消化后给至配料集料皮带。
为改善配料室操作条件,在矿槽处加隔墙隔开。
3)混合室
配好的各种原料经皮带机运来,混合室选用φ3000×12000mm圆筒混合机进行混匀,同时从混合机尾部加水润湿,混合时间2.22min,润湿混匀后的混合料由皮带机运至制粒室。
4)制粒室
混匀后的混合料由皮带机运至制粒室上部,并被分别卸入两个混合料矿槽,每个矿槽有效容积为55m3,贮料时间约20min,每个槽设有一套混合料仓蒸汽预热装置。
然后由园盘给料机给料,电子皮带称称量,经溜槽送入园筒制粒机。
制粒机选用两台φ3000×12000mm圆筒制粒机,每台制粒时间5.19min。
5)燃料外配室
成品燃料外购,由汽车倒运至燃料堆场,燃料堆场面积约1000m2,可贮成品煤2000余t,设有2个受料槽,由受料槽下的皮带机运至燃料外配室。
燃料外配室设有一个燃料矿槽,有效容积为125m3,贮存时间约11h,由拖式皮带秤称量,给料至制粒后的皮带机。
6)滚煤室
滚煤室设在烧结室上部,用一台φ2800×7000mm圆筒滚煤机,滚煤时间1.2min。
7)烧结
从烧结矿筛分室运来的12~20mm的铺底料,由皮带机运至烧结室上部,送入铺底料矿槽。
铺底料矿槽有效容积30m3,贮料时间约1.3h。
烧结机上铺底料由铺底料矿槽下的给料闸门及摆漏斗均匀布料,铺底料料层厚度为30mm。
铺底料槽设有料位信号,通过料位控制铺底料皮带机的起停,保持料位的设定值范围内。
经滚煤机排出的混合料,由B=1200,L=12000梭式布料机给入烧结机的混合料矿槽。
混合料矿槽有效容积40m3,贮料时间约8~10min,并设有一套混合料仓蒸汽预热装置。
经圆辊给料机和多辊布料器将混合料的均匀地布在烧结机上。
料矿槽设有料位信号,根据料位调节配料室自动重量配料系统的总给定值。
每台烧结机有效面积100m2,台车宽3m,栏板高620mm,料层厚600mm,有效烧结长度33.3m。
烧结混合料经点火后进行抽风烧结(烧结点火采用新型节能的点火炉,燃料主高炉煤气,发热值为3344kj/m3)(800kcal/m3),在点火保温后,有一段热风烧结,利用环冷机的废气无动力输送至此。
烧结饼经φ1.6×3.19m单辊破碎机破碎至≤150m。
破碎后的烧结矿给入140m2环冷机进行鼓风冷却,料层厚度1.4m,台车宽度3.2m,有效冷却时间60~80min。
环冷机配4台冷却风机,三开一备运行。
冷却后由板式给矿机给至皮带机上送入成品筛分到;环冷机下散料采用双层卸灰阀和手动散料小车处理至工艺上料皮带机上。
烧结机下的小格散料采用皮带机收集并作为成品,由皮带机运到冷烧结矿皮带机上。
机头电除尘器灰经加湿后、烧结室除尘管排灰与散料用皮带机输送至工艺皮带,进入混合室混合,与原料混合在一起重新参加烧结。
抽风系统,共设23个双侧抽风风箱,其中机头2个风箱、机尾1个风箱长度2m,中部20个风箱长度3m。
大烟道(集气管)采用单根两段式结构,前部直径φ5500mm,后部直径φ4500mm,管内烟气最大流速13.34m/s。
为防止烟气结露对风机转子、电除尘器造成危害,对风箱和大烟道采取保温措施;为防止烟气温度超过电除尘器所允许的工作温度,在大烟道尾部设冷风调节阀。
8)烧结矿筛分室
烧结矿筛分为双系列,一备一用。
经过鼓风机环式冷却机冷却后的烧结矿由皮带机转运至烧结矿筛分室,由筛孔分别为12mm、20mm和5mm的冷矿振动筛组成,筛出<5mm、12~20mm、>20mm和5~12mm四种产品,其中12~20mm为铺底料,由皮带机运至烧结室铺底料矿槽,多余部分转入成品皮带机;5~12mm和>20mm成品烧结矿由皮带机送入取制样室再转运至烧结矿成品矿槽;<5mm的返矿由皮带机输送至配料室返矿料仓参加配料。
9)成品取制样室
整粒筛分后的烧结矿经过成品取制样室。
室内设有成品取样机、转鼓、移动台秤等样和物理检验设施,在此进行取样和一些物理检验工作。
10)烧结成品矿槽
成品矿仓长51m,宽6m。
设有6个仓,每个仓有效430m3,成品矿总贮量约15h。
烧结矿通过移动可逆皮带机卸入成品仓内,由皮带机送入高炉转运站。
11)机头电除尘器
选用2台220m2双室三电场电除尘器,净化后废气排放到大气中,废气排放达到国家标准。
机头电除尘器收集的灰尘经双层卸阀排出后,用螺旋输送机给至烧结室下部的加湿机,加湿后由皮带机转运至工艺上料皮带机上,参加混合。
12)主抽风机室
主抽风机采用SJ19000烧结风机,升压15.5kpa,电机功率9000kw为防止主抽风机的噪声污染环境,风机出口设置了消音器。
经净化后的烧结废气由110m烟囱排入大气。
(2)高炉冶炼主要设施
主要有槽上给料系统、槽下、上料系统、高炉本体、高炉送风系统、热风炉系统、煤气系统、渣铁处理系统、铸铁机及除尘系统。
1)装料系统
锰铁合金高炉采用串罐中心卸料式无料钟炉顶装料设备。
高炉炉顶由炉顶装料设备、炉顶均排压、炉顶液压站及干油润滑站、炉顶传动齿轮箱水冷设施、探尺、炉顶金属结构及炉顶检修设施组成。
上料系统:
上料采用双料车斜桥上料,斜桥倾角为:
50°46′17″,料车容积5.5m3,由Ф2000mm滚筒卷扬机从斜桥上料,卷扬机除布置料车卷扬设备外,还布置两台炉顶探尺卷扬机,卷扬机室设1台10t电动单轨吊,用于料车卷扬机的安装和检修。
卷扬机有自动和手动两种操作方式,自动控制设施设在槽下电气室,卷扬机操作室设有手动操作台。
卷扬机与槽下供料系统及炉顶装料设备按程序自动控制并安全联锁,卷扬机室设有多种自动保护装置以确保设备安全运行。
2)高炉本体
2×630m3高炉炉体为自立式框架结构,高炉炉体支柱下部间距为16m×16m,上部间距为12m×12m。
炉体设有六层平台,平台间设两路走梯。
炉体采用工业水开路循环冷却方式。
3)高炉送风系统
选用静叶可调电动鼓风机,型号为AV50-13;风量2000m3/min,出口风压:
0.448~0.29MPa。
本鼓风站设3台鼓风机,2台AV50-13轴流鼓风机运行,1台D2650离心鼓风机备用,实现2运1备。
4)热风炉系统
配置4座落地式球式热风炉,全高25.7m。
热风炉拱顶采用了结构稳定、气流分布合理的球形拱顶,拱顶砌砖脱离大墙,直接由外壳支托,大墙可自由膨胀,防止了因不均匀膨胀造成的拱顶损坏。
热风炉风温≥1150℃。
废气温度250~300℃,全部采用高炉煤气燃烧,热值3344kJ/Nm3。
采用三段式球床,球床高度为7.5m。
上部球床高1.5m,装Ф80mm锆刚玉火球;中部球床高2m,装Ф60mm高强度高铝球;下部球床高4m,装Ф40mm高强度高铝球。
烟道采用高架式,热风主管、支管及烟道均设波纹补偿器,并在烟道总管、煤气总管、助燃风机管、助燃风机管上设分离式热媒换热器。
4座热风炉设1座助燃风机房,内设2台助燃风机,1台工作,1台备用。
5)炉顶装料系统
炉顶装料设备采用串罐无料钟炉顶,料罐有效容积为15m3。
炉顶设两台软探尺装置,直接反映料面高度。
串罐均压设一次均压,采用半净煤气,二次均压采用氮气,均压阀和均压放散阀的启闭采用液压控制。
炉顶上方设1台16t吊装梁,可将设备从地面吊装到炉顶平台安装位置。
无料钟装料设旋转溜槽,通过溜槽检修孔,可采用手动葫芦进行装卸。
6)风口平台及出铁场
风口平台及出铁场系统由风口平台和出铁场及其设备组成。
高炉采用单出铁场,高炉设有16个风口,1个铁口,1个渣口。
炉前采用50t铁水罐运送锰铁水。
7)高炉煤气粗除尘
高炉煤气粗除尘系统包括:
煤气导出管、上升管、下降管、重力除尘器本体、遮断阀、放散阀、卸灰阀和螺旋搅拌机等设备。
四根Ф1600mm的导出管,在上部汇成两根Ф2000mm的上升管,最后合成一根Ф2520mm的下降管进入重力除尘器。
荒煤气经重力除尘器粗除尘后,煤气含尘量达6~10g/m3。
重力除尘器中沉降的灰经下部的卸灰阀、螺旋搅拌机、清灰管定期排出。
为控制炉顶压力休风时迅速排放煤气,在煤气上升管顶部设有两台600mm放散阀。
为吸收高炉炉壳及导出管的热膨胀,上升管直段部分设有波纹补偿器。
为了在休风时迅速切断煤气和排放煤气,在除尘器的上部设有进入Ф2260mm遮断阀及Ф250mm放散阀各一台。
以上各阀均配有电动卷扬机驱动。
8)煤气净化系统
高炉煤气经重力除尘器粗除尘后,进入布袋除尘器精除尘,精除尘后的煤气进入净煤气总管。
采用净煤气加压反吹方式进行清灰,根据压差定值或定时进行间歇反吹操作,消除布袋内壁的积灰。
9)渣铁处理系统
高炉渣从冲渣沟沟头进入冲渣沟,与高压冲渣水汇合,通过冲渣沟注入过滤池过滤脱水,过滤后的清水经阀门组或热水泵抽入热水池贮存,热水或送至冷却架冷却处理后循环使用。
脱水后的水渣用抓斗吊车抓到堆渣场贮存或直接汽车外运。
采用四个过滤池,每个过滤池面积为168m2,过滤速度6t/m2..h。
每次出渣使用两个过滤池,每个过滤池连续过滤四次铁的渣后进行清渣作业。
过滤池在清渣之后重新使用之前,要进行反灌水和反冲洗作业,以防止滤层板结,保证过滤池的过滤效果。
两台反冲洗机,风量9300m3/h,风压0.09MPa,一用一备。
过滤池由过滤层、工字钢保护格栅、过滤出水管、反冲洗配气管等组成。
过滤层用不同粒度石子组成,全高在1~1.5m之间,粒度2~25mm,分四层放置。
石子过滤层顶面用工字钢格栅保护,避免桥式抓斗起重机抓渣时破坏过滤层。
过滤出水管、反冲洗配气管埋入过滤层底部。
过滤池旁设阀门室,内设管线及多台电动阀门,以满足过滤、反冲洗、反灌水、清渣等作业的操作要求。
在水渣操作室内对阀门及设备进行集中手动操作,在阀门室内各阀门设备旁也设有操作箱进行机旁手动操作。
为提高过滤水出水标高,设置了一组热水泵,这样可减少贮水池、循环泵房的地下混凝土工程量,节省土建工程投资。
露天栈桥跨距28.5m,长83m,装备Q=10t、V=4m3的桥式抓斗起重机1台。
露天栈桥内过滤池旁设堆渣场。
容量约1500m3,可贮存1.5天。
水渣外售粉磨站做水泥原料或送往公司水渣砖厂制砖原料。
2.4.6供配电
1)概述
630m3高炉供配电设施及电气传动控制系统范围包括原料及装料系统、高炉炉顶、炉体、出铁、出渣系统、热风炉系统、煤气净化系统、高炉循环水系统、通风除尘系统、铸铁机、鼓风机站等。
2)电力负荷及耗电量
高炉系统的负荷分别为I类、II类、III类,其中I类负荷占总负荷35%,II类负荷占总负荷的23%,其它为III类负荷。
高炉总装机容量约为15465KW(其中10KV装机容量为12763KW),工作容量为13936KW(其中10KV工作容量为12568KW)。
年耗电量为6756.75×104kWh
3)电源及电压等级
①电源
工程所需用电负荷,一路引自厂区110kv变电站(引自古交220kv变电站),另一路引自距厂区较近的柳泉110kv变电站。
②电压等级
主要电气室配电电源10kv
高压电动机配电电源10kv
低压动力电源交流380V交流220V
控制回路电源直流220V直流24V交流220V
电气照明电源交流220V/36v
4)供配电系统
①10KV开关站
630m3高炉区在高炉鼓风机站及循环水泵站设两个10KV开关站,由110KV电源分别引至两个10KV开关站,再由循环水泵站10KV开关站二段母线各引一路分别引至高炉系统三个主要电气室:
中央电气室、矿槽电气室、高炉循环水泵电气室。
高炉鼓风机电动机由鼓风机开关站供电,装机容量135000KW。
高炉区其他高压电机均由循环泵房10KV开关站供电。
主要包括:
矿槽除尘风机(800KW);出铁场除尘风机(1250KW);热风炉助燃风机(500KW×2);渣处理系统反吹风机(250KW×2);12台高压水泵电机。
以上10KV高压负荷合计装机容量8425KW,工作容量6550KW。
②中央电气室
中央电气室负责对高炉炉顶、炉体系统、风口平台出铁、出渣系统、热风炉系统进行供电及控制并给各系统液压站、煤气除尘系统、出铁场除尘系统、冲渣泵房、鼓风机站、化验楼等提供380交流电源。
本电气室设二台6/0.4KV,1250KVA动力变压器向上述低压负荷供电。
出铁场除尘电气室
控制出铁场的除尘设备,低压负荷电源引自中央控制室,其安装容量为69.6KW。
煤气除尘电气室
对煤气除尘系统各设备进行控制。
电源引自中央电气室,煤气除尘系统装机容量187.3KW。
冲渣泵房电气室
对冲渣泵房各设备进行控制。
电源引自中央电气室,其安装容量为881KW,工作容量为544KW。
鼓风机房电气室
对鼓风机房各设备进行控制。
电源引自中央电气室。
3矿槽电气室
主要对槽上供料系统、