旋手柄注射模设计.docx
《旋手柄注射模设计.docx》由会员分享,可在线阅读,更多相关《旋手柄注射模设计.docx(28页珍藏版)》请在冰豆网上搜索。
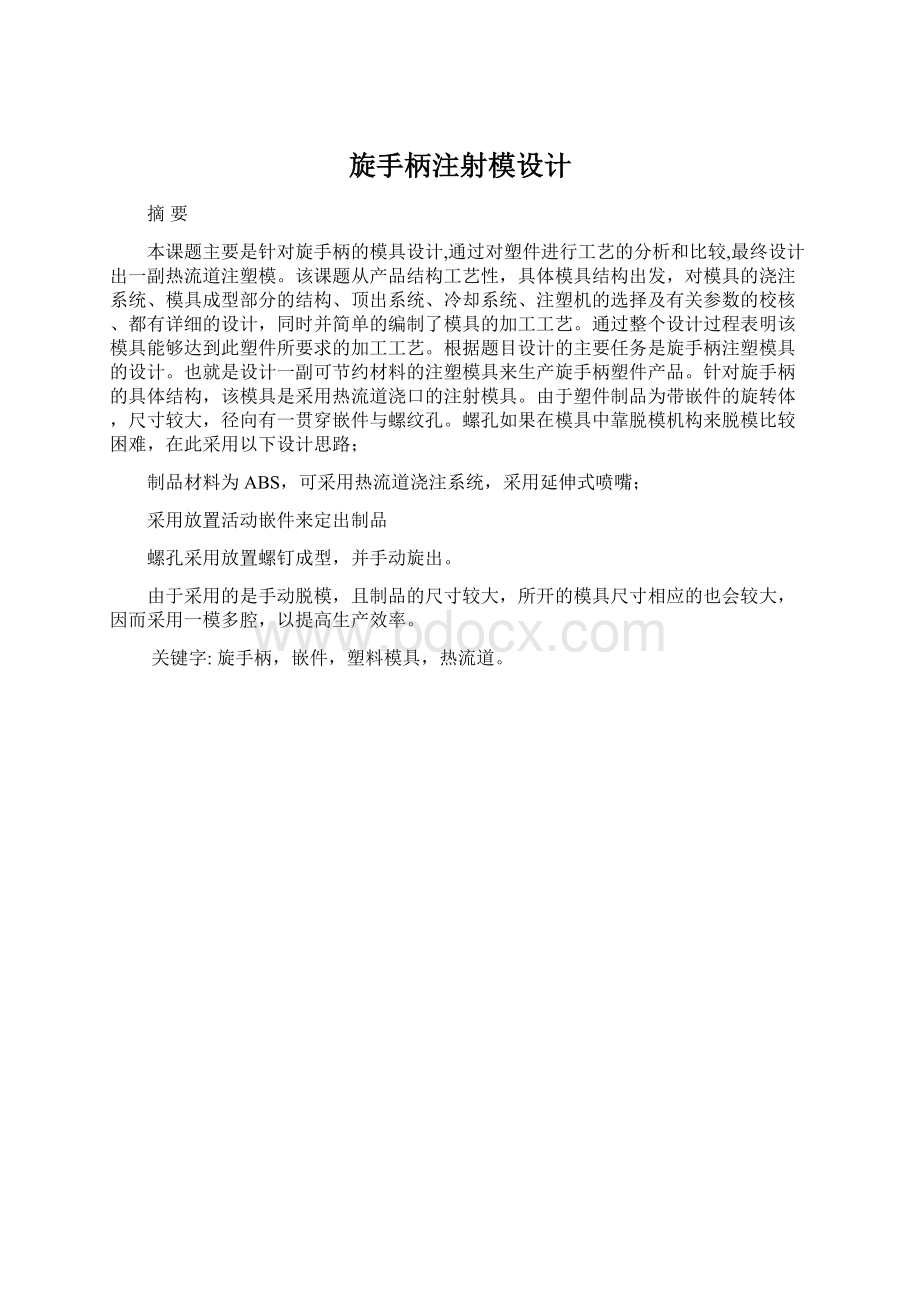
旋手柄注射模设计
摘要
本课题主要是针对旋手柄的模具设计,通过对塑件进行工艺的分析和比较,最终设计出一副热流道注塑模。
该课题从产品结构工艺性,具体模具结构出发,对模具的浇注系统、模具成型部分的结构、顶出系统、冷却系统、注塑机的选择及有关参数的校核、都有详细的设计,同时并简单的编制了模具的加工工艺。
通过整个设计过程表明该模具能够达到此塑件所要求的加工工艺。
根据题目设计的主要任务是旋手柄注塑模具的设计。
也就是设计一副可节约材料的注塑模具来生产旋手柄塑件产品。
针对旋手柄的具体结构,该模具是采用热流道浇口的注射模具。
由于塑件制品为带嵌件的旋转体,尺寸较大,径向有一贯穿嵌件与螺纹孔。
螺孔如果在模具中靠脱模机构来脱模比较困难,在此采用以下设计思路;
制品材料为ABS,可采用热流道浇注系统,采用延伸式喷嘴;
采用放置活动嵌件来定出制品
螺孔采用放置螺钉成型,并手动旋出。
由于采用的是手动脱模,且制品的尺寸较大,所开的模具尺寸相应的也会较大,因而采用一模多腔,以提高生产效率。
关键字:
旋手柄,嵌件,塑料模具,热流道。
前言
现在,模具生产技术水平的高低,已成为衡量一个国家产品制造水平高低的重要标志之一,因为模具在很大程度上决定着产品的质量、效益和新产品的开发能力。
当今世界正进行着新一轮的产业调整.一些模具制造逐渐向发展中国家转移,中国正成为世界模具大国。
近年来,外资对我国模具行业投入量增大,工业发达国家将模具向我国转移的趋势进一步明朗化。
我国模具行业结构调整和体制改革步伐加大,主要表现在,大型、精密、复杂、长寿命、中高档模具及模具标准件发展速度高于一般模具产品;塑料模和压铸模比例增大;专业模具厂数量及其生产能力增加;“三资”及私营企业发展迅速;股份制改造步伐加快等。
从地区分布来看,以珠江三角洲和长江三角洲为中心的东南沿海地区发展快于中西部地区,南方的发展快于北方。
目前发展最快、模具生产最为集中的省份是广东和浙江,江苏、上海、安徽和山东等地近几年也有较大发展。
近期,据资料统计在国外50%的模具采用热流道技术,甚至有些国家达到了80%。
但在我们国家,由于生产力和科技水平的发展等因素,在国内最多仅有30%的模具采用热流道,与国外相比相差甚远。
但是,随着聚合物工业的发展,热流道技术将不断完善并广泛使用。
尽管使用热流道会增加大约15%~20%的模具造价成本,但就长期利益来讲,使用热流道所得的益处要远大于成本增加带来的影响,其潜在的应用市场非常广大。
本次设计的主要要求有:
热流道成型,塑件与嵌件的回转体中心同轴度要求较高。
本次设计的主要难点有:
1)熔体充模时活动镶件与动模镶件配合要求不能跑胶。
2)热流道及热流道喷嘴的设计。
3)制品为带有嵌件的旋转体,且径向有一螺纹孔,在模具中靠机构来脱模比较困难,在此采用放置活动镶件。
脱模是用顶杆将整个活动镶件顶出,模外旋出螺钉,脱出制品。
具体过程,详见以后说明书内容分析和计算。
本说明书为塑料注射模具设计说明书,是根据大量手册上的设计过程及相关工艺编写的。
编写本说明书时,力求符合设计步骤,详细说明了塑料注射模具设计方法,以及各种参数的具体计算方法。
本说明书在编写过程中,得到老师和同学的大力支持和热情帮助,在此谨表谢意。
由于本人设计水平有限,在设计过程中难免有错误之处,敬请各位老师批评指正。
第一章热流道塑料模具概述
1.1原理:
在注射模具内装上热嘴及热流道板,利用加热的原理,使塑料能从注塑机炮筒出来后一直保持熔融状态,制品的入水位跟直接接触到注塑机的射嘴一样,那么成品在脱模时便不会拖着一条或几条料头
1.2热流道模具的特点:
热流道模具在当今世界各工业发达国家和地区均得到极为广泛的应用。
这主要因为热流道模具拥有如下显著特点:
(1)缩短制件成型周期
因没有浇道系统冷却时间的限制,制件成型固化后便可及时顶出。
许多用热流道模具生产的薄壁零件成型周期可在5秒钟以下。
(2)节省塑料原料
在纯热流道模具中因没有冷浇道,所以无生产费料。
这对于塑料价格贵的应用项目意义尤其重大。
事实上,国际上主要的热流道生产厂商均在世界上石油及塑料原料价格昂贵的年代得到了迅猛的发展。
因为热流道技术是减少费料降低材料费的有效途径。
(3)减少费品,提高产品质量
在热流道模具成型过程中,塑料溶体温度在流道系统里得到准确地控制。
塑料可以更为均匀一致的状态流入各模腔,其结果是品质一致的零件。
热流道成型的零件浇口质量好,脱模后残余应力低,零件变形小。
所以市场上很多高质量的产品均由热流道模具生产。
如人们熟悉的MOTOROLA手机,HP打印机,DELL笔记本电脑里的许多塑料零件均用热流道模具制作。
(4)消除后续工序,有利于生产自动化。
制件经热流道模具成型后即为成品,无需修剪浇口及回收加工冷浇道等工序。
有利于生产自动化。
国外很多产品生产厂家均将热流道与自动化结合起来以大幅度地提高生产效率。
(5)扩大注塑成型工艺应用笵围
许多先进的塑料成型工艺是在热流道技术基础上发展起来的。
如PET预成型制作,在模具中多色共注,多种材料共注工艺,STACKMOLD等。
与此同时,热流道也存在以下不足:
(1)模具成本上升
热流道元件价格比较贵,热流道模具成本可能会大幅度增高。
如果零件产量小,模具工具成本比例高,经济上不花算。
对许多发展中国家的模具用户,热流道系统价格贵是影响热流道模具广泛使用的主要问题之一。
2.热流道模具制作工艺设备要求高
热流道模具需要精密加工机械作保证。
热流道系统与模具的集成与配合要求极为严格,否则模具在生产过程中会出现很多严重问题。
如塑料密封不好导致塑料溢出损坏热流道元件中断生产,喷嘴镶件与浇口相对位置不好导致制品质量严重下降等。
3.操作维修复杂
与冷流道模具相比,热流道模具操作维修复杂。
如使用操作不当极易损坏热流道零件,使生产无法进行,造成巨大经济损失。
第二章塑料制件的工艺性分析
2.1产品图
材料:
ABS
图2.1
2.2材料工艺性能
2.2.1ABS的基本特性
ABS是由丙烯腈、丁二烯、苯乙烯共聚而成的。
这三种组分的各自特性,使ABS具有良好的综合性能。
丙烯腈使ABS有良好的耐化学腐蚀性及表面硬度,丁二烯使ABS坚韧,苯乙烯使它有良好的加工和染色性能。
ABS无毒、无味,呈微黄色,密度1.02g/cm3~1.20g/cm3,成型的塑料件有较好的光泽。
有极好的冲击强度,且在低温温下也不迅速下降。
水、无机盐、碱、酸类对ABS几乎无影响,在酮、醛、酯、氯代烃中会溶解或形成乳浊液,不溶于大部分醇类及烃类溶剂,但与烃长期接触会软化溶胀。
ABS表面受冰醋酸、植物油等化学药品的侵蚀会引起应力开裂。
ABS有一定的硬度和尺寸稳定性,易于成型加工。
经过调色可配成任何颜色。
其缺点是耐热性不高.
性能:
综合性能较好,冲击韧度、力学性能较高,尺寸稳定而化学性、电气性能良好;易于成形和机械加工,与此相反372有机玻璃的熔接性良好,可作双色成形塑件,且表面可镀铬。
用途:
适于制作一般机械零件、减摩耐摩零件、传动零件以及化工、电器、仪表等零件。
2.2.2成形特性
1.无定形塑料,其品种很多,各品种的机电性能及成型特性也有差异,应按品种确定成形方法及成形条件。
2.吸湿性强,含水量应小于0.3%,必须充分干燥,要求表面光泽的塑件应要求长时间预热干燥。
3.流动性中等,溢边料0.04mm左右(流动性比聚苯乙烯、AS差,但比聚碳酸脂,聚氯乙烯好)。
4.比聚苯乙烯加工困难,宜取高料温、模温(对耐热、高抗冲击和中抗冲击型树脂,料温更宜取高)。
料温对物性影响较大,料温过高易分解(分解温度为250℃左右,比聚苯乙烯易分解),对要求精度较高塑件,模温宜取50℃~60℃,要求光泽及耐热型料宜取60℃~80℃。
注射压力应比聚苯乙烯高,一般用柱塞式注射机时料温为180℃~230℃,注射压力为100~140MPa,螺杆式注射机则取160℃~230℃,70~100MPa为宜。
5.模具设计时要注意浇注系统,选择好进料口位置、形式。
推出力过大或机械加工时塑料件表面呈现“白色”痕迹(但热水中预热可消失)。
脱模斜度宜为2°以上。
2.3塑件的工艺要求
制品为带嵌件的旋转体,尺寸较大,径向有一贯穿嵌件与螺纹孔。
螺孔如果在模具中靠脱模机构来脱模比较困难
2.3.1塑件的壁厚
制品的壁厚对其质量有很大的影响,壁厚过小难以满足使用强度和刚度的要求,
2.3.2塑件的圆角
塑件制品设计圆角,能使其成型时的流动性能好,成型顺利进行。
因为当制品带有尖角时,往往会在尖角处产生应力集中,在受力或受冲击振动时发生破裂。
本设计的制品均采用圆角半径为0.2㎜。
2.3.3制品的表面质量
制品的表面质量包括表面粗糙度和外观质量等,制品的外观要求越高,表面粗糙度值应越低。
这除了在成型时从工艺上尽可能避免冷疤、云纹等缺陷来保证外,主要取决于模具型腔表面的粗糙度。
一般模具表面的粗糙度要比制品的要求低1~2级。
查表-常用材料模塑件公差等级和选用(GB/T14486)、表-模塑件尺寸公差表(GB/T14486)得:
以上三个尺寸均按MT3级塑料精度,属于一般等精度等级,在模具设计和制造过程中要严格保证这些尺寸的精度要求,其余尺寸均无精度要求为自由尺寸,可按MT5级精度查取公差值。
2.3.4收缩率
本设计中取ABS的平均收缩率为0.006。
第三章塑件成型方案的确定
3.1.确定型腔数量及排列方式
表3-1单型腔、多型腔的优缺点及适用范围
类型
优点
缺点
适用范围
单型腔模具
塑件的精度高;工艺参数易于控制;模具结构简单;模具制造成本低,周期短。
塑料成形的生产率低,塑件的成本高。
塑件较大,精度要求较高或者小批量及试生产。
多型腔模具
塑料成形的生产率高,塑件的成本低。
塑件的精度低;工艺参数难以控制;模具结构复杂;模具制造成本高,周期长。
大批量、长期生产的小型塑件。
型腔数目确定的方法有多种,如根据锁模力,根据最大注射量,根据制品的精度要求,根据经济性等等。
由于在这次设计中注射机还未确定,本次设计与实际在工厂中的设计有所不同。
工厂中的注塑机是已有固定的,模具设计人员通常都是根据车间内的注塑机来确定最大的之间产量,即是说厂中的注塑机选择是有限的。
而在本次设计中,我们选择注塑即的原则则是按我们想象中的产品产量和实际的塑件形状来选择任何一款注塑机,最后校核能满足使用要求即可。
,
本设计采用了Pro/E软件画出塑件的实体图,然后通过分析可得到
塑件的体积V=2.4979113e+05毫米^3
塑件的质量m=2.4979113e+05g
流道凝料的质量4m还是个未知数,可按塑件质量的0.6倍来计算,从上述分析中确定为一模4腔,由于此制件的尺寸较大,其质量属性如下体积=2.4979113e+05毫米^3
曲面面积=8.8136938e+04毫米^2
平均密度=1.0000000e+00g/毫米^3
质量=2.4979113e+05g
由于采用手动脱螺纹方式,生产效率会大大降低,故从型腔数量来提高生产效率,采用一模四腔。
因此模具采用的是热流道浇注系统,故型腔的排列方式须考虑热流道的方式。
以下是热流道浇注系统的几种形式,如图3.1
图3.1热流道浇注系统系列
综合以上情况型腔的排列方式可以确定为以下;如图3.2
图3.2型腔排列形式
3.2分型面位置的确定
如何确定分型面,需要考虑的因素比较复杂。
由于分型面受到塑件在模具中的成型位置、浇注系统设计、塑件的结构工艺性及精度、嵌件位置形状以及推出方法、模具的制造、排气、操作工艺等多种因素的影响,因此在选择分型面时应综合分析比较,从几种方案中优选出较为合理的方案。
选择分型面时一般应遵循以下几项原则:
1)分型面应选在塑件外形最大轮廓处。
2)便于塑件顺利脱模,尽量使塑件开模时留在动模一边。
3)保证塑件的精度要求。
4)满足塑件的外观质量要求。
5)便于模具加工制造。
6)对成型面积的影响。
7)对排气效果的影响。
8)对侧向抽芯的影响。
其中最重要的是第5)和第2)、点。
为了便于模具加工制造,应尽是选择平直分型面工易于加工的分型面。
本产品不需采用侧向抽芯故采用如下图A-A这样一个平直的分型面,大简化了动定模的加工。
A-A分型面也是整个模具的主分模面。
这样的分型面有利于动模活动镶件的加工。
脱模时由于采用的是热流道浇口,浇口的热力闭合或机械闭合使得产品脱模时不会有一条很长的料头,且有型芯的包紧力的作用,塑件会留在动模一侧,开模后由顶杆将活动镶件携制品顶出,,顶出的制品由人工将螺钉卸下取出制品。
分型卖弄如图3.3
图3.3分型面
3.3浇注系统形式和浇口的设计
3.3.1浇注系统概述
浇注系统可分为普通浇注系统和热流道浇注系统两大类。
浇注系统控制着塑件成型过程中充模和补料两个重要阶段,对塑件质量关系极大。
浇注系统是指从注塑机喷嘴进入模具开始,到型腔入口为止的那一段流道。
普通模具的浇注系统由主流道、分流道、浇口、冷料井几部分组成。
浇注系统设计是模具设计中最重要的问题之一。
浇注系统的合理性对制品质量和生产效率有着决定性的影响。
本设计采用的是热流道浇注系统,具体原因如下:
热流道注射模具用于生产塑料制品,需要昂贵的费用和高难度的技术。
模具生产企业在启动设计制造前,必须进行可行性研究。
在给定的生产经营和技术环境条件下,对某个塑料制品是否采用热流道技术的分析判断,不仅需要测算经济成本,权衡生产管理水平,还要考虑制品生产的质量,考虑模具和注射机等技术条件。
但是本次设计作为毕业设计仅作为结构和可行性的设计练习,目的在于能够在以后工作上得到帮助。
因此以上诸多因素可以不必考虑,只要考虑制件的材料是否适宜用热流道浇注系统。
表3-2各种塑料对绝热流道和热流道的适用性
该制件的材料ABS可用于热流道浇注系统。
热流道系统是注射机喷嘴的衍伸,同时又是模具的流道系统。
与冷流道系统相比,它扩展了加工注射量,降低了压力损失,使浇口热力闭合或者机械闭合。
为此它加入了外部的加热源,模具结构变得复杂了。
但是能够提高生产效率和节约材料。
3.3.2主流道设计
此模具的浇注系统由主流道、分流道、导料套、浇口及热喷嘴组成。
主流道是连接注射机的喷嘴与分流道的一段通道,通常和注射机的喷嘴在同一轴线上,断面为圆形,常有一定的锥度,本设计考虑到主流道要高温的塑料熔体反复接触和碰撞,因此将主流道部分设计成可拆卸的主流道衬套,见下图3.3,以便
选用优质的钢材单独加工可热处理。
图3.4主流道交口套
3.3.3分流道设计
分流道是主流道与浇口之间的通道上,一般开设在分型面上,起分流和转向的作用,多型腔的模具一定设置分流道,单型腔成型大型塑件,若使用多浇口进料也需设置分流道。
而本设计采用的是热流道模具成型塑件,所以分流道主要是布置在热流道板中。
(1)分流道长度
分流道的长度取决于模具型腔的总体布置方案和浇口位置,从输送熔体时的减少压力损失和热量损失以及减少浇道凝料的要求出发,应力求缩短。
(2)分流道断面形状及尺寸
要减少流道内的压力损失,希望流道的截面积大,表面积小,以减少传热损失,因此可用流道的截面积与周长的比值来表示流道的效率,综合效率与加成难易程度,本设计的分流道断
面形状采用圆形。
如图3.5
图3.5分流道形状
3.3.4导料套的设计
导料套也可以说是流道的过渡组合件,设计导料套目的是为了能使流道在流入热喷嘴时比较流畅,而且可以防止在转角处跑胶,如果发生跑胶则热流道板的接触面就不能很好的配合,就会影响到热流道的加热管的加热。
导料套形状尺寸如图3.6
图3.6导料套
3.3.5浇口的设计
浇口种类的选择、浇口形状和尺寸的确定是选用标准系列喷嘴的前提。
功能良好的浇口,使塑料熔体在合适的剪切速率下充模具注射;又给予保压补缩的注塑件以恰当的补偿,从而保证了制品的质量。
进一步确定浇口的形状和尺寸好,需要考虑的因素有:
浇口的流动性、制品的大小和壁厚、塑料流动特性、浇口痕迹的审美要求等。
塑料从从喷嘴流道流道注入窄小浇口通道,具有了很高的剪切速率,因此,有很大的压力损失。
生产中使用小浇口时常被迫提高喷嘴的加热温度,提高熔体流动性;又要强化浇口区的冷却,否则就要提高注射压力,但会增加模塑件中的内应力。
浇口的最大直径决定着热力闭合的实现。
如果浇口过大,并且过长,注塑件已经冷却,但浇口中物料不能闭合,就必须延长冷却时间。
本设计为了能实现浇口的合理化,采用了在塑件顶部中心处的直接浇口进胶的设计。
塑料熔体从热喷嘴出口直接环绕型芯注入型腔。
此设计可以避免由于浇口过小而须提高喷嘴加热温度。
由于塑件的环形孔尺寸不会过大,跟一般的热喷嘴的口径差不多,因此直接浇口进胶也可解决热力闭合的问题。
浇口形似及尺寸如下图3.7
图3.7浇口
3.3.6热喷嘴的设计
热流道喷嘴是热流道系统的终端,它包括加热器,热电偶和浇口。
它将熔体输送到模具的型腔。
热流道喷嘴是热流道系统的购置部件。
喷嘴是热流道系统中的复杂部件,其种类繁多,常用的有开式喷嘴,顶针式喷嘴,开关式喷嘴和边缘式喷嘴。
开放式和顶针式喷嘴是热力闭合;开关式喷嘴是机械闭合。
喷嘴流道的直径
在热流道喷嘴设计和订购热流道喷嘴时,不但要确定喷嘴类型和浇口直径,还需要确定喷嘴中流道的直径。
此直径被标准系列化,常用的系列是,
根据本制品的成型尺寸,按系列取直径Φ4mm的喷嘴。
制造喷嘴的材料
要求制造喷嘴的材料,有较高的力学强度和较好的导热率。
在一些应用场合,如无机矿物填料,玻纤增强或有阻燃剂的塑料注射时,喷嘴应有抗腐蚀和化学阻抗的性能。
使用最多的是耐热工具钢,有德国的DIN1.2343,X38CrMoV5-1,属淬透刚类。
硬度接近44HRC,热导率约为25W/(m.K),用于制作喷嘴的壳体和切削零件。
图3.8热流道喷嘴
图3.9喷嘴线圈式加热器图3.10热喷嘴产品图
3.3.7热流道板的设计
热流道的流道板是热流道系统的中心部件。
流道板将主流道传输来的塑料熔体经流道分送到折射点的喷嘴。
对注射模上的热流道板的选择或设计有些基本要求必须满足。
对大型型腔或多行腔的熔体充模要有合理的分配。
;熔体有适当的流动剪切速率,并使流道中压力损失较小;能防止过热和热损伤;熔体在流道中没有滞留的死点;流道板加热升温快,温度控制有效;流道板与模具的绝热良好,且与喷嘴间无熔体泄露,清洗容易,加热器的替换和维修方便。
图3.11热流道板剖面图
图3.12热流道板
热流道板做成两半,比较好加工流道和加热管沟槽,也有利于电热管的装拆。
流道板悬架在模架中,上有定模固定板,下有定模板。
流道板是被加热电器加热的高温部件,四周是由冷切系统维持的低温模板。
以空气间隙作为绝热介质,流道板的上下平面和四周与模板间都有间隙。
喷嘴的大部分表面与定模板之间也都有间隙。
为了避免流道板将热量传递给定模板和固定板,四个承压圈用绝热材料制造。
又因承压圈承受喷嘴轴线上流道板和喷嘴的热膨胀应力支撑垫承受注射机喷嘴的压力。
所以隔热垫应该用耐压而且绝热的高强度材料。
承压圈的接触面积太大不利于绝热;而面积太小,强大的压力会压溃定模固定板和定模板。
因此在此选用具有高强度和绝热的钛合金。
热流道板在加工时,加热管配合面须用磨床加工到表面粗糙度达到1.6。
热流道板的沟槽与金属加热管应紧密配合,沟槽的直径应比加热管的直径小10~20丝。
装配时用紧固螺钉将上下两块板锁紧。
若出现较大的间隙会使热流道板的热传递变坏,使加热管的工作温度升高而发生过热损伤。
加热管设计在下面详细介绍。
模具中央轴线上,流道板与定位板之间配有中心定位销,加上流道板边缘的止转定位销,从而保证了流道板的定位精度,使定模板周边间隙均匀,也保证了流道板与喷嘴流道的对准。
如图3.13所示
图3.13止转定位销
3.3.8温度控制系统设计
1加热管
热流道系统处于热平衡状态,理想状态的系统保持着给定的温度。
加热器均匀加热,且补偿着热量的损失。
由灵敏的热电偶和温度调节器,对热流道系统的流道板和各喷嘴进行有效准确的温度控制。
常用的流道板都采用外加热的方法。
热源在流道熔体外壁的流道板中。
以前流道板使用筒棒式加热器,现今它只能最为简单的加热器,已逐渐被淘汰掉了,。
流道板上大都已使用可弯曲的管状加热器。
管状加热器原理是在金属管内放入镍铬电阻丝线圈。
空隙部分紧密地填充了导热绝缘的氧化镁。
电阻丝在电加热管的两端通过导线与电源相连,它可被完成各种形状,镶嵌在流道板的沟槽中。
模板介质的最高加热温度为350C。
金属管状电热管的最高耐压克达到600V,功率密度是13W/cm2。
金属大部分采用不锈钢,最高工作温度可达600C。
但不能用铜管或铝管。
金属管状结构见图3.14
图3.14金属加热管
金属管状加热管的弯曲半径与他的管径有关,最小的弯曲半径为5~6mm
第四章成型零件的设计及尺寸计算
4.1成型零件设计
所谓工作尺寸是指成型零件上直接用以成型塑件部位的尺寸。
工作尺寸的计算受塑件尺寸精度的制约,影响塑件尺寸精度的因素甚多,且十分复杂,因此塑件尺寸难以达到高精度。
型腔是模具上直接成型塑料制件的部位。
直接构成模具型腔的所有零件的所有零件都称为成型零件,通常包括:
凹模、凸模、成型杆、成型环、各种型腔镶件等。
按结构主型芯可分为整体式和组合式两种。
采用组合式型芯,可简化结构复杂的型芯的加工工艺,减少热处理变形,便宜模具的维修,节省贵重的模具钢。
为了保证组合后的型芯尺寸的精度和装配的牢固,要求镶件的尺寸、形位公差等级较高,组合机构必须牢固,镶块的机械加工工艺性要好。
因此,选择合理的组合式结构是非常重要的。
塑件成形的总误差δ=δs+δz+δe+δi[5]应小于塑件的公差值,即δ≤△
式中δs——塑件的收缩率波动;
δz——模具成形零件的制造误差;
δe——模具成形零件的磨损;
δi——模具安装配合的误差
4.2成型零件尺寸计算
为计算简便起见,规定凡是孔类尺寸均以其最小尺寸作为公称尺寸,即公差为正;凡是轴类尺寸均以其最大尺寸作为公称尺寸,公差为负。
本设计采用平均收缩率法计算模腔各工作尺寸
在前面第一章有介绍了ABS的特性,其收缩率为0.003~0.008,本设计取其收缩率0.006
型腔径向尺寸:
(Lm)+δzm0=[(1+s)Ls-XΔ]+δz0[5]
型腔深度尺寸:
(Hm)+δz-0=[(1+s)Hs-XΔ]+δz0[5]
型芯径向尺寸:
(lm)0-δz=[(1+s)Ls+XΔ]0-δz[5]
型芯高度尺寸:
(Hm)0-δz=[(1+s)hs+XΔ]0-δz[5]
式中
Ls-塑件外型径向基本尺寸的最大尺寸(mm)
ls- 塑件内型径向基本尺寸的最小尺寸(mm)
Hs-塑件外型高度基本尺寸的最大尺寸(mm)
hs- 塑件内型深度基本尺寸的最小尺寸(mm)
X- 修正系数 取0.5~0.75
△- 塑件公差
δz- 模具制造公差 一般取(1/3~1/4)△
根据GB/T14486《工程塑料模塑塑料件尺寸公差标准》,塑件取MT3级精度,塑件的最大外形尺寸为100mm.查的塑件公差为0.58,12公差为0.18,Ф80的公差为0.52
H6.76公差为0.16,H5.24的公差为0.1422.76的公差为0.28
4.2.1型腔径