第二章 电火花加工的基本原理及设备2.docx
《第二章 电火花加工的基本原理及设备2.docx》由会员分享,可在线阅读,更多相关《第二章 电火花加工的基本原理及设备2.docx(16页珍藏版)》请在冰豆网上搜索。
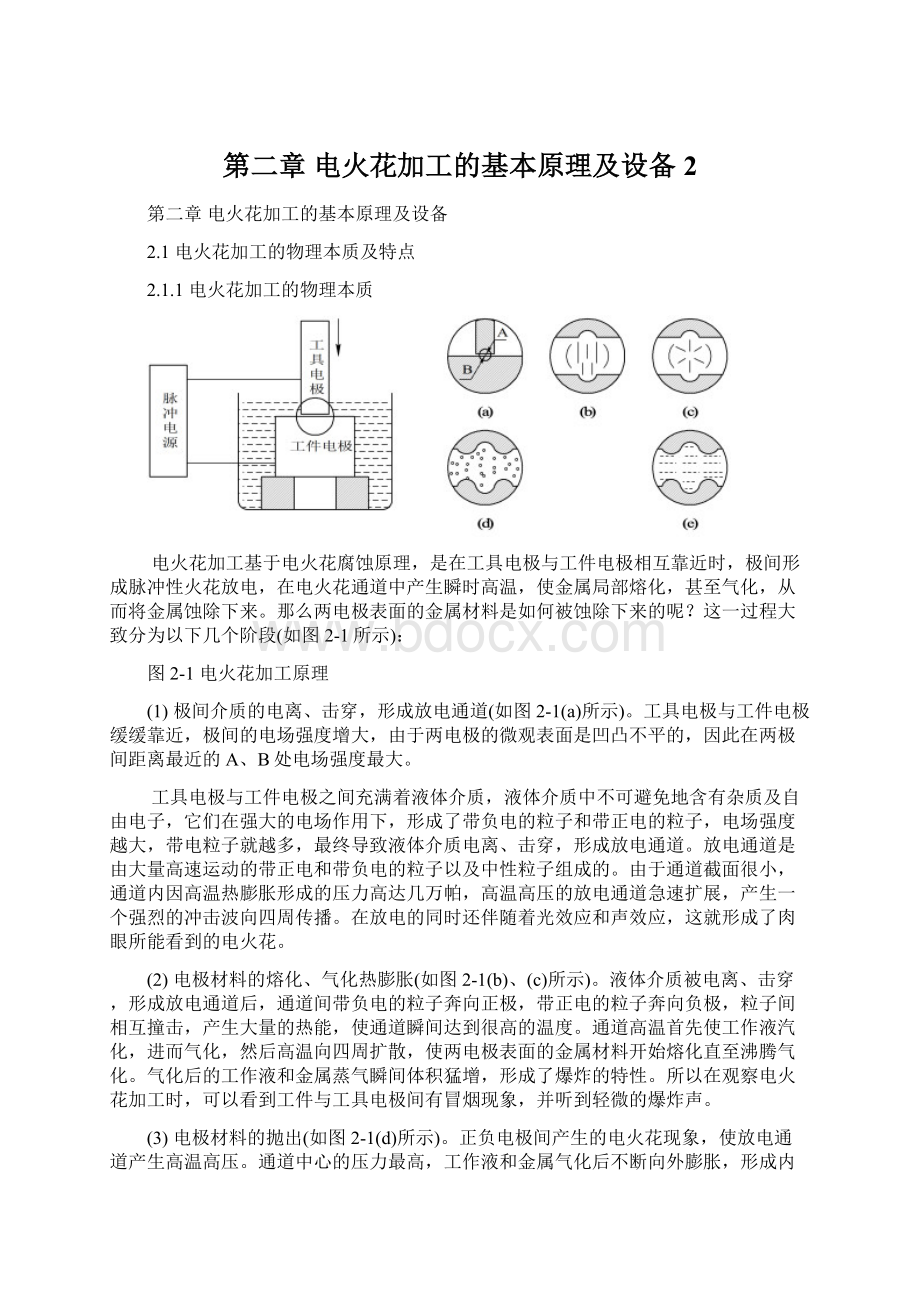
第二章电火花加工的基本原理及设备2
第二章电火花加工的基本原理及设备
2.1电火花加工的物理本质及特点
2.1.1电火花加工的物理本质
电火花加工基于电火花腐蚀原理,是在工具电极与工件电极相互靠近时,极间形成脉冲性火花放电,在电火花通道中产生瞬时高温,使金属局部熔化,甚至气化,从而将金属蚀除下来。
那么两电极表面的金属材料是如何被蚀除下来的呢?
这一过程大致分为以下几个阶段(如图2-1所示):
图2-1电火花加工原理
(1)极间介质的电离、击穿,形成放电通道(如图2-1(a)所示)。
工具电极与工件电极缓缓靠近,极间的电场强度增大,由于两电极的微观表面是凹凸不平的,因此在两极间距离最近的A、B处电场强度最大。
工具电极与工件电极之间充满着液体介质,液体介质中不可避免地含有杂质及自由电子,它们在强大的电场作用下,形成了带负电的粒子和带正电的粒子,电场强度越大,带电粒子就越多,最终导致液体介质电离、击穿,形成放电通道。
放电通道是由大量高速运动的带正电和带负电的粒子以及中性粒子组成的。
由于通道截面很小,通道内因高温热膨胀形成的压力高达几万帕,高温高压的放电通道急速扩展,产生一个强烈的冲击波向四周传播。
在放电的同时还伴随着光效应和声效应,这就形成了肉眼所能看到的电火花。
(2)电极材料的熔化、气化热膨胀(如图2-1(b)、(c)所示)。
液体介质被电离、击穿,形成放电通道后,通道间带负电的粒子奔向正极,带正电的粒子奔向负极,粒子间相互撞击,产生大量的热能,使通道瞬间达到很高的温度。
通道高温首先使工作液汽化,进而气化,然后高温向四周扩散,使两电极表面的金属材料开始熔化直至沸腾气化。
气化后的工作液和金属蒸气瞬间体积猛增,形成了爆炸的特性。
所以在观察电火花加工时,可以看到工件与工具电极间有冒烟现象,并听到轻微的爆炸声。
(3)电极材料的抛出(如图2-1(d)所示)。
正负电极间产生的电火花现象,使放电通道产生高温高压。
通道中心的压力最高,工作液和金属气化后不断向外膨胀,形成内外瞬间压力差,高压力处的熔融金属液体和蒸汽被排挤,抛出放电通道,大部分被抛入到工作液中。
仔细观察电火花加工,可以看到桔红色的火花四溅,这就是被抛出的高温金属熔滴和碎屑。
(4)极间介质的消电离(如图2-1(e)所示)。
加工液流入放电间隙,将电蚀产物及残余的热量带走,并恢复绝缘状态。
若电火花放电过程中产生的电蚀产物来不及排除和扩散,产生的热量将不能及时传出,使该处介质局部过热,局部过热的工作液高温分解、积炭,使加工无法继续进行,并烧坏电极。
因此,为了保证电火花加工过程的正常进行,在两次放电之间必须有足够的时间间隔让电蚀产物充分排出,恢复放电通道的绝缘性,使工作液介质消电离。
上述步骤
(1)~(4)在一秒内约数千次甚至数万次地往复式进行,即单个脉冲放电结束,经过一段时间间隔(即脉冲间隔)使工作液恢复绝缘后,第二个脉冲又作用到工具电极和工件上,又会在当时极间距离相对最近或绝缘强度最弱处击穿放电,蚀出另一个小凹坑。
这样以相当高的频率连续不断地放电,工件不断地被蚀除,故工件加工表面将由无数个相互重叠的小凹坑组成(如图2-2所示)。
所以电火花加工是大量的微小放电痕迹逐渐累积而成的去除金属的加工方式。
图2-2电火花表面局部放大图
2.1.2电火花加工、电火花线切割加工的特点
1.共同特点
(1)二者的加工原理相同,都是通过电火花放电产生的热来熔解去除金属的,所以二者加工材料的难易与材料的硬度无关,加工中不存在显著的机械切削力。
(2)二者的加工机理、生产率、表面粗糙度等工艺规律基本相似,可以加工硬质合金等一切导电材料。
(3)最小角部半径有限制。
电火花加工中最小角部半径为加工间隙,线切割加工中最小角部半径为电极丝的半径加上加工间隙。
2.不同特点
(1)从加工原理来看,电火花加工是将电极形状复制到工件上的一种工艺方法(如图2-3(a)所示)。
在实际中可以加工通孔(穿孔加工)和盲孔(成型加工)(如图2-3(b)、(c)所示);而线切割加工是利用移动的细金属导线(铜丝或钼丝)做电极,对工件进行脉冲火花放电,切割成型的一种工艺方法,如图2-4所示。
图2-3电火花加工
图2-4线切割加工
(2)从产品形状角度看,电火花加工必须先用数控加工等方法加工出与产品形状相似的电极;线切割加工中产品的形状是通过工作台按给定的控制程序移动而合成的,只对工件进行轮廓图形加工,余料仍可利用。
(3)从电极角度看,电火花加工必须制作成型用的电极(一般用铜、石墨等材料制作而成);线切割加工用移动的细金属导线(铜丝或钼丝)做电极。
(4)从电极损耗角度看,电火花加工中电极相对静止,易损耗,故通常采用多个电极加工;而线切割加工中由于电极丝连续移动,使新的电极丝不断地补充和替换在电蚀加工区受到损耗的电极丝,避免了电极损耗对加工精度的影响。
(5)从应用角度看,电火花加工可以加工通孔、盲孔,特别适宜加工形状复杂的塑料模具等零件的型腔以及刻文字、花纹等(如图2-5(a)所示);而线切割加工只能加工通孔,能方便地加工出小孔、形状复杂的窄缝及各种形状复杂的零件(如图2-5(b)所示)。
(a)电火花加工产品(b)线切割加工产品
图2-5加工产品实例
2.2电火花加工机床简介
2.2.1机床型号、规格、分类
我国国标规定,电火花成型机床均用D71加上机床工作台面宽度的1/10表示。
例如D7132中,D表示电加工成型机床(若该机床为数控电加工机床,则在D后加K,即DK);71表示电火花成型机床;32表示机床工作台的宽度为320mm。
在中国大陆外,电火花加工机床的型号没有采用统一标准,由各个生产企业自行确定,如日本沙迪克(Sodick)公司生产的A3R、A10R,瑞士夏米尔(Charmilles)技术公司的ROBOFORM20/30/35,台湾乔懋机电工业股份有限公司的JM322/430,北京阿奇工业电子有限公司的SF100等。
电火花加工机床按其大小可分为小型(D7125以下)、中型(D7125~D7163)和大型(D7163以上);按数控程度分为非数控、单轴数控和三轴数控。
随着科学技术的进步,国外已经大批生产三坐标数控电火花机床,以及带有工具电极库、能按程序自动更换电极的电火花加工中心,我国的大部分电加工机床厂现在也正开始研制生产三坐标数控电火花加工机床。
2.2.2电火花加工机床结构
电火花加工机床主要由机床本体、脉冲电源、自动进给调节系统、工作液过滤和循环系统、数控系统等部分组成。
1.机床本体
机床本体主要由床身、立柱、主轴头及附件、工作台等部分组成,是用以实现工件和工具电极的装夹固定和运动的机械系统。
床身、支柱、坐标工作台是电火花机床的骨架,起着支承、定位和便于操作的作用。
因为电火花加工宏观作用力极小,所以对机械系统的强度无严格要求,但为了避免变形和保证精度,要求具有必要的刚度。
主轴头下面装夹的电极是自动调节系统的执行机构,其质量的好坏将影响到进给系统的灵敏度及加工过程的稳定性,进而影响工件的加工精度。
机床主轴头和工作台常有一些附件,如可调节工具电极角度的夹头、平动头、油杯等。
本节主要介绍平动头。
电火花加工时粗加工的电火花放电间隙比中加工的放电间隙要大,而中加工的电火花放电间隙比精加工的放电间隙又要大一些。
当用一个电极进行粗加工时,将工件的大部分余量蚀除掉后,其底面和侧壁四周的表面粗糙度很差,为了将其修光,就得转换规准逐挡进行修整。
但由于中、精加工规准的放电间隙比粗加工规准的放电间隙小,若不采取措施则四周侧壁就无法修光了。
平动头就是为解决修光侧壁和提高其尺寸精度而设计的。
平动头是一个使装在其上的电极能产生向外机械补偿动作的工艺附件。
当用单电极加工型腔时,使用平动头可以补偿上一个加工规准和下一个加工规准之间的放电间隙差。
平动头的动作原理是:
利用偏心机构将伺服电机的旋转运动通过平动轨迹保持机构转化成电极上每一个质点都能围绕其原始位置在水平面内作平面小圆周运动,许多小圆的外包络线面积就形成加工横截面积,如图2-7所示,其中每个质点运动轨迹的半径就称为平动量,其大小可以由零逐渐调大,以补偿粗、中、精加工的电火花放电间隙δ之差,从而达到修光型腔的目的。
具体平动头的结构及原理可以参考其他书籍。
目前,机床上安装的平动头有机械式平动头和数控平动头,其外形如图2-8所示。
机械式平动头由于有平动轨迹半径的存在,它无法加工有清角要求的型腔;而数控平动头可以两轴联动,能加工出清棱、清角的型孔和型腔。
图2-7平动头扩大间隙原理图
(a)机械式平动头(b)数控平动头
图2-8平动头外形
与一般电火花加工工艺相比较,采用平动头电火花加工有如下特点:
(1)可以通过改变轨迹半径来调整电极的作用尺寸,因此尺寸加工不再受放电间隙的限制。
(2)用同一尺寸的工具电极,通过轨迹半径的改变,可以实现转换电规准的修整,即采用一个电极就能由粗至精直接加工出一副型腔。
(3)在加工过程中,工具电极的轴线与工件的轴线相偏移,除了电极处于放电区域的部分外,工具电极与工件的间隙都大于放电间隙,实际上减小了同时放电的面积,这有利于电蚀产物的排除,提高加工稳定性。
(4)工具电极移动方式的改变,可使加工的表面粗糙度大有改善,特别是底平面处。
2.脉冲电源
在电火花加工过程中,脉冲电源的作用是把工频正弦交流电流转变成频率较高的单向脉冲电流,向工件和工具电极间的加工间隙提供所需要的放电能量以蚀除金属。
脉冲电源的性能直接关系到电火花加工的加工速度、表面质量、加工精度、工具电极损耗等工艺指标。
脉冲电源输入为380V、50Hz的交流电,其输出应满足如下要求:
(1)要有一定的脉冲放电能量,否则不能使工件金属气化。
(2)火花放电必须是短时间的脉冲性放电,这样才能使放电产生的热量来不及扩散到其他部分,从而有效地蚀除金属,提高成型性和加工精度。
(3)脉冲波形是单向的,以便充分利用极性效应,提高加工速度和降低工具电极损耗。
(4)脉冲波形的主要参数(峰值电流、脉冲宽度、脉冲间歇等)有较宽的调节范围,以满足粗、中、精加工的要求。
(5)有适当的脉冲间隔时间,使放电介质有足够时间消除电离并冲去金属颗粒,以免引起电弧而烧伤工件。
电源的好坏直接关系到电火花加工机床的性能,所以电源往往是电火花机床制造厂商的核心机密之一。
从理论上讲,电源一般有如下几种。
1)弛张式脉冲电源
弛张式脉冲电源是最早使用的电源,它是利用电容器充电储存电能,然后瞬时放出,形成火花放电来蚀除金属的。
因为电容器时而充电,时而放电,一弛一张,故又称“弛张式”脉冲电源(如图2-9所示)。
由于这种电源是靠电极和工件间隙中的工作液的击穿作用来恢复绝缘和切断脉冲电流的,因此间隙大小、电蚀产物的排出情况等都影响脉冲参数,使脉冲参数不稳定,所以这种电源又称为非独立式电源。
弛张式脉冲电源结构简单,使用维修方便,加工精度较高,粗糙度值较小,但生产率低,电能利用率低,加工稳定性差,故目前这种电源的应用已逐渐减少。
图2-9RC线路脉冲电源
2)闸流管脉冲电源
闸流管是一种特殊的电子管,当对其栅极通入一脉冲信号时,便可控制管子的导通或截止,输出脉冲电流。
由于这种电源的电参数与加工间隙无关,故又称为独立式电源。
闸流管脉冲电源的生产率较高,加工稳定,但脉冲宽度较窄,电极损耗较大。
3)晶体管脉冲电源
晶体管脉冲电源是近年来发展起来的以晶体元件作为开关元件的用途广泛的电火花脉冲电源,其输出功率大,电规准调节范围广,电极损耗小,故适应于型孔、型腔、磨削等各种不同用途的加工。
晶体管脉冲电源已越来越广泛地应用在电火花加工机床上。
目前普及型(经济型)的电火花加工机床都采用高低压复合的晶体管脉冲电源,中、高档电火花加工机床都采用微机数字化控制的脉冲电源,而且内部存有电火花加工规准的数据库,可以通过微机设置和调用各挡粗、中、精加工规准参数。
例如汉川机床厂、日本沙迪克公司的电火花加工机床,这些加工规准用C代码(例如C320)表示和调用,三菱公司则用E代码表示。
4.工作液过滤和循环系统
电火花加工中的蚀除产物,一部分以气态形式抛出,其余大部分是以球状固体微粒分散地悬浮在工作液中,直径一般为几微米。
随着电火花加工的进行,蚀除产物越来越多,充斥在电极和工件之间,或粘连在电极和工件的表面上。
蚀除产物的聚集,会与电极或工件形成二次放电。
这就破坏了电火花加工的稳定性,降低了加工速度,影响了加工精度和表面粗糙度。
为了改善电火花加工的条件,一种办法是使电极振动,以加强排屑作用;另一种办法是对工作液进行强迫循环过滤,以改善间隙状态。
工作液强迫循环过滤是由工作液循环过滤器来完成的。
电火花加工用的工作液过滤系统包括工作液泵、容器、过滤器及管道等,使工作液强迫循环。
图2-11是工作液循环系统油路图,它既能实现冲油,又能实现抽油。
其工作过程是:
储油箱的工作液首先经过粗过滤器l,经单向阀2吸入油泵3,这时高压油经过不同形式的精过滤器7输向机床工作液槽,溢流安全阀5使控制系统的压力不超过400kPa,补油阀11为快速进油用。
待油注满油箱时,可及时调节冲油选择阀10,由阀8来控制工作液循环方式及压力。
当阀10在冲油位置时,补油冲油都不通,这时油杯中油的压力由阀8控制;当阀10在抽油位置时,补油和抽油两路都通,这时压力工作液穿过射流抽吸管9,利用流体速度产生负压,达到实现抽油的目的。
图2-11工作液循环系统油路图
5.数控系统
1)数控电火花机床的类型
数控系统规定除了直线移动的X、Y、Z三个坐标轴系统外,还有三个转动的坐标系统,即绕X轴转动的A轴,绕Y轴转动的B轴,绕Z轴转动的C轴。
若机床的Z轴可以连续转动但不是数控的,如电火花打孔机,则不能称为C轴,只能称为R轴。
根据机床的数控坐标轴的数目,目前常见的数控机床有三轴数控电火花机床、四轴三联动数控电火花机床、四轴联动或五轴联动甚至六轴联动电火花加工机床。
三轴数控电火花加工机床的主轴Z和工作台X、Y都是数控的。
从数控插补功能上讲,又将这类型机床细分为三轴两联动机床和三轴三联动机床。
三轴两联动是指X、Y、Z三轴中,只有两轴(如X、Y轴)能进行插补运算和联动,电极只能在平面内走斜线和圆弧轨迹(电极在Z轴方向只能作伺服进给运动,但不是插补运动)。
三轴三联动系统的电极可在空间作X、Y、Z方向的插补联动(例如可以走空间螺旋线)。
四轴三联动数控机床增加了C轴,即主轴可以数控回转和分度。
现在部分数控电火花机床还带有工具电极库,在加工中可以根据事先编制好的程序,自动更换电极。
2)数控电火花机床的数控系统工作原理
数控电火花机床能实现工具电极和工件之间的多种相对运动,可以用来加工多种较复杂的型腔。
目前,绝大部分电火花数控机床采用国际上通用的ISO代码进行编程、程序控制、数控摇动加工等,具体内容如下:
(ISO代码编程ISO代码是国际标准化机构制定的用于数控编码和程序控制的一种标准代码。
代码主要有G指令(即准备功能指令)和M指令(即辅助功能指令),具体见表2-1。
表2-1常用的电火花数控指令
6.电火花机床常见功能
电火花机床的常见功能如下:
(1)回原点操作功能。
数控电火花在加工前首先要回到机械坐标的零点,即X、Y、Z轴回到其轴的正极限处。
这样,机床的控制系统才能复位,后续操作机床运动不会出现紊乱。
(2)置零功能。
将当前点的坐标设置为零。
(3)接触感知功能。
让电极与工件接触,以便定位。
(4)其他常见功能(如图2-15所示)。
图2-15电火花机床常见功能
2.3电火花线切割加工机床简介
2.3.1机床分类、型号
1.分类
线切割加工机床可按多种方法进行分类,通常按电极丝的走丝速度分成快速走丝线切割机床(WEDM-HS)与慢速走丝线切割机床(WEDM-LS)。
1)快速走丝线切割机床
快速走丝线切割机床的电极丝作高速往复运动,一般走丝速度为8~10m/s,是我国独创的电火花线切割加工模式。
快速走丝线切割机床上运动的电极丝能够双向往返运行,重复使用,直至断丝为止。
线电极材料常用直径为0.10~0.30mm的钼丝(有时也用钨丝或钨钼丝)。
对小圆角或窄缝切割,也可采用直径为0.6mm的钼丝。
工作液通常采用乳化液。
快速走丝线切割机床结构简单、价格便宜、生产率高,但由于运行速度快,工作时机床震动较大。
钼丝和导轮的损耗快,加工精度和表面粗糙度就不如慢速走丝线切割机床,其加工精度一般为0.01~0.02mm,表面粗糙度Ra为1.25~2.5μm。
2)慢速走丝线切割机床
慢速走丝线切割机床走丝速度低于0.2m/s。
常用黄铜丝(有时也采用紫铜、钨、钼和各种合金的涂覆线)作为电极丝,铜丝直径通常为0.10~0.35mm。
电极丝仅从一个单方向通过加工间隙,不重复使用,避免了因电极丝的损耗而降低加工精度。
同时由于走丝速度慢,机床及电极丝的震动小,因此加工过程平稳,加工精度高,可达0.005mm,表面粗糙度Ra≤0.32μm。
慢速走丝线切割机床的工作液一般采用去离子水、煤油等,生产率较高。
慢走丝机床主要由日本、瑞士等国生产,目前国内有少数企业引进国外先进技术与外企合作生产慢走丝机床。
2.型号
国标规定的数控电火花线切割机床的型号,如DK7725的基本含义为:
D为机床的类别代号,表示是电加工机床;K为机床的特性代号,表示是数控机床;第一个7为组代号,表示是电火花加工机床,第二个7为系代号(快走丝线切割机床为7,慢走丝线切割机床为6,电火花成型机床为1);25为基本参数代号,表示工作台横向行程为250mm。
2.3.2快走丝线切割机床简介
由于科学技术的发展,目前在生产中使用的快走丝线切割机床几乎全部采用数字程序控制,这类机床主要由机床本体、脉冲电源、数控系统和工作液循环系统组成。
1.机床本体
机床本体主要由床身、工作台、运丝机构和丝架等组成,具体介绍如下:
1)床身
床身是支承和固定工作台、运丝机构等的基体。
因此,要求床身应有一定的刚度和强度,一般采用箱体式结构。
床身里面安装有机床电气系统、脉冲电源、工作液循环系统等元器件。
2)工作台
目前在电火花线切割机床上采用的坐标工作台,大多为X、Y方向线性运动。
不论是哪种控制方式,电火花线切割机床最终都是通过坐标工作台与丝架的相对运动来完成零件加工的,坐标工作台应具有很高的坐标精度和运动精度,而且要求运动灵敏、轻巧,一般都采用“十”字滑板、滚珠导轨,传动丝杠和螺母之间必须消除间隙,以保证滑板的运动精度和灵敏度。
3)运丝机构
在快走丝线切割加工时,电极丝需要不断地往复运动,这个运动是由运丝机构来完成的。
最常见的运丝机构是单滚筒式,电极丝绕在储丝筒上,并由丝筒作周期性的正反旋转使电极丝高速往返运动。
储丝筒轴向往复运动的换向及行程长短由无触点接近开关及其撞杆控制(如图2-16中的5、4),调整撞杆的位置即可调节行程的长短。
这种形式的运丝机构的优点是结构简单、维护方便,因而应用广泛。
其缺点是绕丝长度小,电动机正反转动频繁,电极丝张力不可调。
图2-16快走丝线切割机床结构图
4)丝架
运丝机构除上面所叙述的内容外,还包括丝架。
丝架的主要作用是在电极丝快速移动时,对电极丝起支撑作用,并使电极丝工作部分与工作台平面保持垂直。
为获得良好的工艺效果,上、下丝架之间的距离宜尽可能小。
为了实现锥度加工,最常见的方法是在上丝架的上导轮上加两个小步进电动机,使上丝架上的导轮作微量坐标移动(又称U、V轴移动),其运动轨迹由计算机控制。
2.脉冲电源
电火花线切割加工的脉冲电源与电火花成型加工作用的脉冲电源在原理上相同,不过受加工表面粗糙度和电极丝允许承载电流的限制,线切割加工脉冲电源的脉宽较窄(2~60μs),单个脉冲能量、平均电流(1~5A)一般较小,所以线切割总是采用正极性加工。
3.数控系统
数控系统在电火花线切割加工中起着重要作用,具体体现在两方面:
(1)轨迹控制作用。
它精确地控制电极丝相对于工件的运动轨迹,使零件获得所需的形状和尺寸。
(2)加工控制。
它能根据放电间隙大小与放电状态控制进给速度,使之与工件材料的蚀除速度相平衡,保持正常的稳定切割加工。
目前绝大部分机床采用数字程序控制,并且普遍采用绘图式编程技术,操作者首先在计算机屏幕上画出要加工的零件图形,线切割专用软件(如YH软件、北航海尔的CAXA线切割软件)会自动将图形转化为ISO代码或3B代码等线切割程序。
4.工作液循环系统
工作液循环与过滤装置是电火花线切割机床不可缺少的一部分,其主要包括工作液箱、工作液泵、流量控制阀、进液管、回液管和过滤网罩等。
工作液的作用是及时地从加工区域中排除电蚀产物,并连续充分供给清洁的工作液,以保证脉冲放电过程稳定而顺利地进行。
目前绝大部分快走丝机床的工作液是专用乳化液。
乳化液种类繁多,大家可根据相关资料来正确选用。
2.3.3慢走丝线切割机床简介
同快走丝线切割机床一样,慢走丝线切割机床也是由机床本体、脉冲电源、数控系统等部分组成的。
但慢走丝线切割机床的性能大大优于快走丝线切割机床,其结构具有以下特点:
1.主体结构
1)机头结构
机床和锥度切割装置(U,V轴部分)实现了一体化,并采用了桁架铸造结构,从而大幅度地强化了刚度。
2)主要部件
精密陶瓷材料大量用于工作臂、工作台固定板、工件固定架、导丝装置等主要部件,实现了高刚度和不易变形的结构。
3)工作液循环系统
慢走丝线切割机床大多数采用去离子水作为工作液,所以有的机床(如北京阿奇)带有去离子系统。
在较精密加工时,慢走丝线切割机床采用绝缘性能较好的煤油作为工作液。
2.走丝系统
慢走丝线切割机床的电极丝在加工中是单方向运动(即电极丝是一次性使用)的。
在走丝过程中,电极丝由储丝筒出丝,由电极丝输送轮收丝。
慢走丝系统一般由以下几部分组成:
储丝筒、导丝机构、导向器、张紧轮、压紧轮、圆柱滚轮、断丝检测器、电极丝输送轮、其他辅助件(如毛毡、毛刷)等。
图2-18为日本沙迪克公司某型号线切割机床的电极丝的送出部分结构图,其中某些部件的作用如下:
2—圆柱滚轮可使线电极从线轴平行地输出,且使张力维持稳定
3—导向孔模块可使电极丝在张紧轮上正确地进行导向
5—张紧轮在电极丝上施加必要的张力
6—压紧轮防止电极丝张力变动的辅助轮
7—毛毡去除附着在电极丝上的渣滓
8—断丝检测器检查电极丝送进是否正常,若不正常送进,则发出报警信号,提醒发生电极丝断丝等故障
9—毛刷防止电极丝断丝时从轮子上脱出
图2-18电极丝送丝装置
2.3.4线切割机床常见的功能
下面简单介绍线切割机床较常见的功能。
(1)模拟加工功能。
模拟显示加工时电极丝的运动轨迹及其坐标。
(2)短路回退功能。
加工过程中若进给速度太快而电腐蚀速度慢,在加工时出现短路现象,控制器会改变加工条件并沿原来的轨迹快速后退,消除短路,防止断丝。
(3)回原点功能。
遇到断丝或其他一些情况,需要回到起割点,可用此操作。
(4)单段加工功能。
加工完当前段程序后自动暂停,并有相关提示信息,如:
单段停止!
按OFF键停止加工,按RST键继续加工。
此功能主要用于检查程序每一段的执行情况。
(5)暂停功能。
暂时中止当前的功能(如加工、单段加工、模拟、回退等)。
(6)MDI功能。
手