《烟草工业企业卷接包装工序.docx
《《烟草工业企业卷接包装工序.docx》由会员分享,可在线阅读,更多相关《《烟草工业企业卷接包装工序.docx(25页珍藏版)》请在冰豆网上搜索。
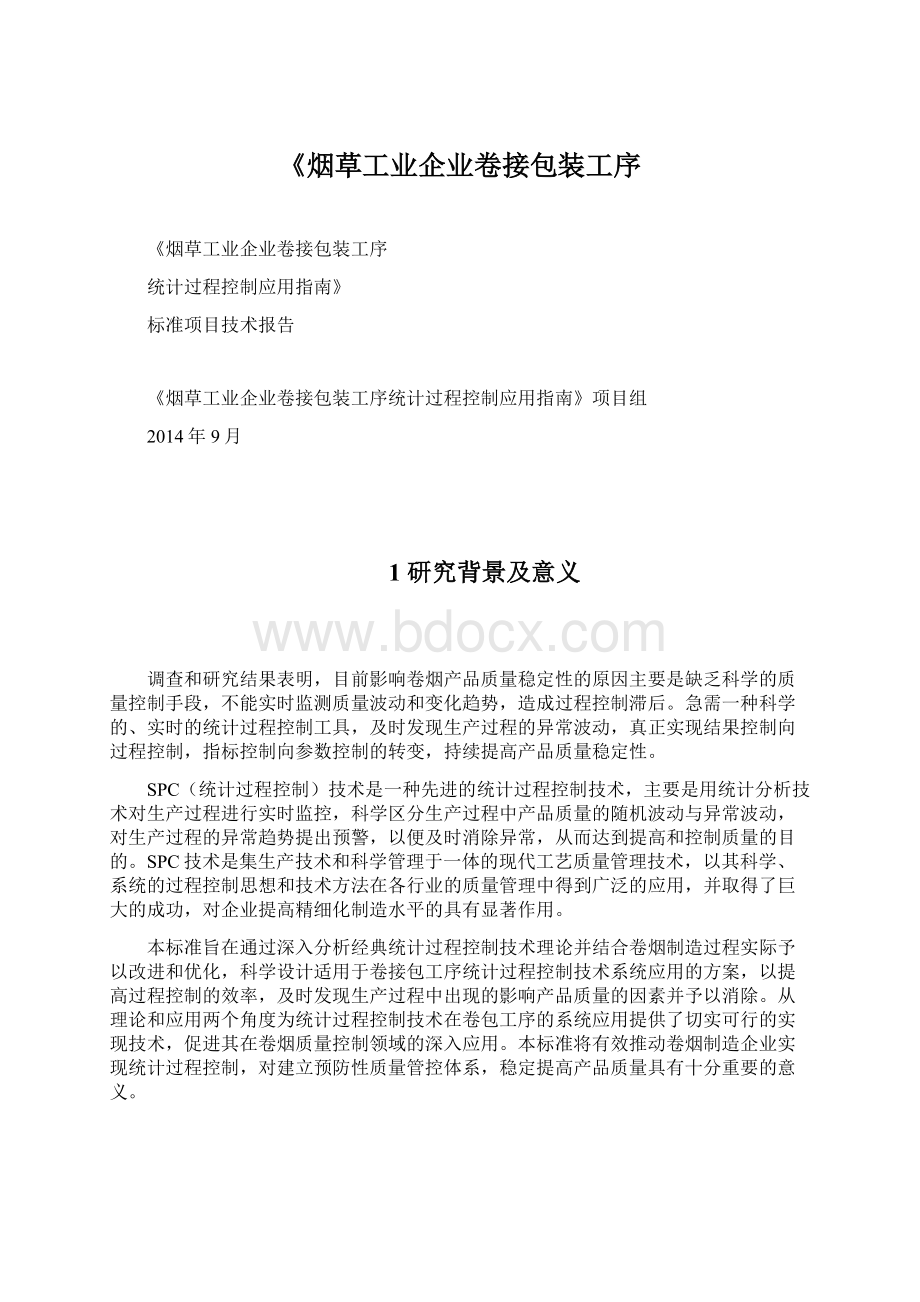
《烟草工业企业卷接包装工序
《烟草工业企业卷接包装工序
统计过程控制应用指南》
标准项目技术报告
《烟草工业企业卷接包装工序统计过程控制应用指南》项目组
2014年9月
1研究背景及意义
调查和研究结果表明,目前影响卷烟产品质量稳定性的原因主要是缺乏科学的质量控制手段,不能实时监测质量波动和变化趋势,造成过程控制滞后。
急需一种科学的、实时的统计过程控制工具,及时发现生产过程的异常波动,真正实现结果控制向过程控制,指标控制向参数控制的转变,持续提高产品质量稳定性。
SPC(统计过程控制)技术是一种先进的统计过程控制技术,主要是用统计分析技术对生产过程进行实时监控,科学区分生产过程中产品质量的随机波动与异常波动,对生产过程的异常趋势提出预警,以便及时消除异常,从而达到提高和控制质量的目的。
SPC技术是集生产技术和科学管理于一体的现代工艺质量管理技术,以其科学、系统的过程控制思想和技术方法在各行业的质量管理中得到广泛的应用,并取得了巨大的成功,对企业提高精细化制造水平的具有显著作用。
本标准旨在通过深入分析经典统计过程控制技术理论并结合卷烟制造过程实际予以改进和优化,科学设计适用于卷接包工序统计过程控制技术系统应用的方案,以提高过程控制的效率,及时发现生产过程中出现的影响产品质量的因素并予以消除。
从理论和应用两个角度为统计过程控制技术在卷包工序的系统应用提供了切实可行的实现技术,促进其在卷烟质量控制领域的深入应用。
本标准将有效推动卷烟制造企业实现统计过程控制,对建立预防性质量管控体系,稳定提高产品质量具有十分重要的意义。
2主要研究内容及技术思路
利用流程分析(IPO)、矩阵分析(C&E)、测量系统分析(MSA)等工具和方法,全面系统梳理卷接包的工艺流程,筛选影响质量指标的关键因素,识别在线监测仪器的可靠性,确定生产过程重点监控对象,在收集、分析、整理大量数据和信息的基础上,建立使用卷包工序应用的统计过程控制规则,实现卷包关键指标的实时监控、即时报警、系统分析,解决质量控制手段落后,控制层次不够深入,控制体系不够系统等制约质量控制水平提升的瓶颈问题,有效提升产品质量的预测、控制、分析、改进能力。
3主要技术方案
4
标准项目研究的技术路线见图1。
图1标准项目研究的技术路线
5结果与分析
6
4.1确定控制对象
4.1.1卷接包装工序流程调研
利用IPO流程分析、因果矩阵分析、FMEA等工具和技术,对卷接包装生产工艺流程进行了系统、深入的梳理,制作了详细的卷烟、接装、包装工艺质量控制流程图,确定了卷接、包装工序关键的质量输入与输出变量,为找出关键质量指标影响因素,科学确定控制对象,查找异常波动原因奠定了基础。
4.1.2确定控制对象
在流程梳理过程中,经过大量数据分析发现,重量、圆周、吸阻对卷烟质量影响显著,且卷包生产现场有综合测试台可以满足重量、圆周、吸阻的实施检测,确定将重量、圆周和吸阻作为计量型SPC控制对象。
考虑外观缺陷种类较多、需手工统计且抽样数量较少等因素,鉴于空头和小盒外观均有在线监测仪可以利用,确定将烟支空头、小盒外观以及总不良率作为计数型SPC控制对象。
6.2测量系统分析
6.3
测量系统可分为“计数型”及“计量型”测量系统两类。
测量后能够给出具体的测量数值的为计量型测量系统;只能定性地给出测量结果的为计数型测量系统。
“计量型”测量系统分析通常包括偏倚(Bias)、稳定性(Stability)、线性(Linearity)、以及重复性和再现性(Repeatability&Reproducibility,简称R&R)。
在测量系统分析的实际运作中可同时进行,亦可选项进行,首先根据具体使用情况,确定主要通过分析R&R来确定测量系统能力,即主要分析测量系统的宽度变差。
测量系统的位置变差的分析和修正可以通过工序已有的定期校验工作来完成。
“计数型”测量系统分析可以利用假设检验分析法来进行判定。
计量型测量系统主要采用“重复性与再现性”和“双样本t”假设检验方法判定方法进行分析。
计量型测量系统主要采用“配对t”假设检验方法和“Kappa”方法进行测量系统分析。
6.4统计过程方案设计
6.5
4.3.1控制图类型选取
在SPC质量控制中常用的数据有计量值和计数值之分,因此基本上也可以将控制图分为两大类:
计量值控制图和计数值控制图。
4.3.1.1计量型控制图
在卷接过程中,物测指标(圆周、重量、吸阻)为计量值数据,数据批量大,故排除中位数-极差和单值-移动极差控制图,卷包工序现场大多有计算机辅助计算,均值-标准差图比均值-极差控制图更准确,因此对于物测指标(圆周、重量、吸阻)均采用均值-标准差控制图。
常规控制图只能发现较大的过程异常波动,对较小的波动不灵敏,由于卷接设备生产速度很快,越早发现异常,越能避免质量损失,因此考虑在使用均值-标准差控制图的同时,联合使用专门用来监控较小波动的EWMA(指数加权移动平均)控制图。
EWMA控制图的设计思想就是对数据的信息加以积累,将过程的小偏移累加起来,达到放大的效果,提高控制图对小波动的监控灵敏度。
4.3.1.2计数型控制图
烟支空头(数据来源为卷烟机在线检测仪器显示剔除空头数)可以用单位时间内生产过程中剔除的空头数量与生产总量的比值作不良率控制图,该统计量为计数型,同样时间内的生产总量不相等,即样本不一样大,因此排除NP图,选择P图。
盒内烟支外观、小盒外观、盒装缺陷、条装缺陷、箱装缺陷,采用C图控制图。
4.3.2抽样频率的确定
在设计控制图时,抽样频率是非常重要的一个因素,尤其是对于大批量生产的过程或者有许多异常因素发生的场合,更需要加大抽样频率,以便于及时发现过程中的质量问题。
4.3.2.1计量型抽样频率的确定
为了验证抽样频率对监控效率的影响,首先进行了不同抽样频率下监控效果的对比试验,以10pcs/10min以及10pcs/30min分别作为抽样频率对物测指标(圆周、重量、吸阻)作控制图进行试验,试验结果见图2.1、图2.2、图2.3。
图2.1不同抽样频率下圆周的X-bar控制图对比分析
图2.2不同抽样频率下重量的X-bar控制图对比分析
图2.3不同抽样频率下吸阻的X-bar控制图对比分析
从图2.1、图2.2、图2.3可以发现,10pcs/30min的控制图灵敏程度要远差于10pcs/10min,甚至有些过程异常都难以发现。
测试结果表明,抽样频率的提高对及时发现过程变化,提高监控效率有明显作用,由于目前考虑到大多数卷烟企业设备条件所限,抽样频率仍采用30min抽样一次,在条件允许后尽可能提高抽样频率,进而提高监控效率。
4.3.2.2计数型抽样频率的确定
对不同抽样频率下计量型控制图的监控效果进行了对比试验,分别以每班和每小时为抽样频率计算空头不良率并建立P图,如图3、图4所示。
图3按班统计空头不良率P图分析
图4按小时统计空头不良率P图分析
按班和按小时进行统计采样的空头不良率P控制图都能够诊断发现机台空头剔除量过多的情况,及时报警避免过多剔除损耗和设备异常带来的空头数量的增加。
在空头剔除不稳定的情况下,按小时记录的空头不良率控制图比按班记录的空头不良率控制图效率高,但按小时记录工作量比较大,计算过程相对较为复杂。
烟支外观缺陷、小盒外观、盒装缺陷、条装缺陷、箱装缺陷,均为每小时抽样一次。
4.3.3样本容量的确定
4.3.3.1计量型控制图样本容量的确定
样本容量的确定对于控制图的监控效果有着显著的影响。
一般来说,计量型的控制图的样本容量都在3到5个左右,但对于卷接包的物测指标来说,由于生产批量大,对于监控效率的需求较高,因此需要采用更大的样本容量,而样本容量过大则会受到测量系统能力的约束,影响过程监测的及时性。
为了选择比较合理的样本容量,通过试验验证了不同样本容量情况下监控效率的区别,在一定范围内,选择样本大小分别为5,10和15,抽样频率为30分钟,在试验机台进行试验,分别采用常规控制图和EWMA图对圆周,重量和吸阻三个指标的数据进行分析,确定样本大小对监控效率的影响。
如图5所示,抽样数据的各分布参数特性(主要是均值和方差)来看,采用样本大小为5时,各参数的值与样本大小为10和15时的各参数值差别比较显著;而样本大小为10和15之间,各参数值的差别较小,可以认为样本大小为10和15时用样本估计总体的分布是一致的。
而样本大小为5时估计的总体的分布与样本为10和15时不一致。
图5不同样本容量下圆周、重量、吸阻的统计分析
进一步比较不同样本下同一特性的控制图,如图6.1、6.2、6.3所示,同样可以发现,样本为10和15的控制图没有明显的差别,而样本为5的控制图与其余二者差别较大。
结合抽样数据分布的数字特征,可以得到以下结论:
分别采用样本大小为10和15之间没有显著差异,样本大小的增加不能提高控制图的监控效率,从节约成本和提高检测效率的角度出发,建议不考虑采用样本大小为15的抽样方案,而样本大小为5和10之间如何选择还需下面作进一步分析。
图6.1样本容量(15)的圆周控制图
图6.2样本容量(10)的圆周控制图
图6.3样本容量(5)的圆周控制图
图7和图8分别为样本大小为5和10时圆周的X-bar控制图和EWMA控制图的比较分析。
图7不同样本大小圆周均值控制图比较
A:
样本为10的控制图对该异常反应比样本为5的控制图明显
B:
样本为10的控制图发现异常,样本为5的控制图未发现
C:
样本为10的控制图比样本为5的控制图早发现异常
D:
样本为10的控制图比样本为5的控制图早发现异常
E:
样本为10的控制图比样本为5的控制图早发现异常
F:
样本为10的控制图比样本为5的控制图早发现异常
由此可见,样本为10的圆周X-bar控制图监控效率高于样本为5的圆周X-bar控制图监控效率。
图8不同样本大小圆周均值EWMA控制图比较
A:
样本为10的控制图比样本为5的控制图早发现异常
B:
样本为10的控制图发现异常,样本为5的控制图未发现
C:
样本为10的控制图比样本为5的控制图早发现异常
D:
样本为10的控制图比样本为5的控制图早发现异常
由此可见,样本为10的圆周EWMA控制图监控效率高于样本为5的圆周EWMA控制图监控效率。
同样,对于重量数据,样本大小为5和10时的X-bar控制图的比较分析见图9。
重量的监控过程比较稳定,样本大小的改变对其影响不大,但仍有个别异常波动在样本为10的控制图中发现而样本为5的控制图未发现,见上图中A、B。
重量的EWMA监控情况,以及吸阻的监控情况与上述分析类似,都能够体现出样本容量为10的控制图监控效率高于样本容量为5的控制图监控效率。
图9不同样本大小重量均值控制图比较
从理论分析的角度来说,根据现有的生产速度及产量,抽样间隔应取较小值,样本大小取较大值,但考虑到硬件环境,目前取样定在每半小时取10支较为合理,根据SPC控制图平均值1.5σ的漂移理论,有95%的概率落在要求范围内,见图10。
图10样本容量与发现过程异常的概率之间的关系
综上所述,样本容量为10是目前最合理的选择,在以后的控制过程中,如果过程稳定性进一步提高了,想进一步强化控制时,在要求允许的情况下,可适当的提高抽样频率和样本大小。
4.3.3.2计数型控制图样本容量的确定
空头控制图的数据来源是在线全检的数据,样本容量即为每次抽样间隔内生产的所有数据。
卷烟包装外观抽检数据控制图的样本容量为每次抽样间隔内抽检的数据。
4.3.4控制界限的确定
在控制图上有三条线:
中心线和上、下控制界限。
当控制界限间隔变宽离中心线更远时,第一类错误(即点因纯属偶然原因出界,而过程实际上仍处于控制状态并无异常因素发生的虚发报警的错误)的概率α减小;但同时第二类错误(过程实际上已失控而点仍落在控制界限内的漏发报警的错误)的概率β增加。
反之,当控制界限变窄时,则第一类错误的概率α增加,第二类错误的概率β减小。
无论虚发报警还是漏发报警的错误都会造成质量损失,在选择控制界限时,应使两类错误所造成的总损失最小。
经验证明,3σ控制界限所造成的总损失是比较小的,同样选择3σ控制界限。
4.3.4.1计量型控制图控制限的制订
在分析用控制图阶段,判断生产过程是否处于稳定状态,然后采用稳定状态下的数据进行统计分析,确定控制界限,物测指标(圆周、重量、吸阻)的控制界限的确立步骤如下:
第一步:
综合同一机台的近期的物测历史数据(可为前一个月)计算均值和方差,并以此建立分析用控制图;
第二步:
观察该分析用控制图,选取一段较为平稳的过程数据,数据以30-60个子组为宜;较为平稳的过程表现为该段过程数据无连续的较大过程偏移(也就是说没有连续多个点都位于界外较远的位置),且点分布较为均匀(中心线上下点的数量基本一致,没有明显的向某一侧偏移的趋势,也就是说保持近似服从正态分布)。
其基本判断条件有以下两条:
(1)所有的点基本上都落在控制界限内。
这一条意味着:
①连续25个点中,没有一个点超出控制界限。
因为用少量数据作控制图容易产生错误的判断,所以至少要有25个点才能作出相对正确的判断。
②连续35个点中,最多有一个点超出控制界限。
从概率理论可知,连续35个点中,至少有一点落在界外的概率为0.0041,是个小概率事件。
③连续50个点中,最多有两个点超出控制界限。
在连续的50个点中,最多有两个点超出控制界限的概率为0.006,也不超过1%,也是个小概率事件。
由概率论可知,小概率事件可以认为不会发生。
(2)在控制界限内的点随机排列。
随机排列意味着满足以下三个条件:
①样本点分布均匀,位于中心线两侧的样本点各占50%;②靠近中心线的样本点约占2/3;③靠近控制界线的样本点极少。
第三步:
用这些数据重新制定分析用控制图,若无点出界,则将这时的控制界限定为本月该机台的控制界限,均值和方差控制图的控制界限计算公式分别为:
第四步:
若有个别点在控制线外,则剔除对应点的数据,重新建立分析用控制图,直至无点出界为止,将这时的控制界限定为本月该机台的控制界限;
第五步:
若有较多点出界(超过10个),则认为这一段的数据不稳定,返回第二步重新选取数据进行分析。
4.3.4.2计数型控制图控制限的制订
对于外观控制图,控制界限的确定方法与计量型控制图类似。
空头不良率P图的控制线计算公式为:
为使控制图的控制界限反映实际生产过程质量状况,应该定期修订控制界限,采用的控制图修订的周期以月为单位,在每个月的月初根据上月的数据制订当月的控制界限。
除了定期修订外,当遇到下列情况时,还需要进行不定期的修订:
(1)通过积累的数据分析,表明过程质量发生了显著的变化;
(2)过程条件如烟用材料、工艺方法、设备和环境条件发生了显著的变化;
(3)取样方法已改变。
4.3.5控制图判异准则的优化
在控制图控制界限确定之后,就可以从分析用控制图阶段转为控制用控制图结点,用来进行日常监控。
4.3.5.1计量型控制判异准则的优化
常规的八项判异准则最初来源于机械制造行业,不能充分满足烟草行业的要求,需要结合卷烟制造过程质量控制的实际对判异准则进行优化。
以试验机台某段时间测量数据,对圆周和重量的控制图判异准则进行分析。
图11圆周控制图判异准则分析
图11是对圆周数据采用均值-标准差控制图进行监控,用八项判异准则进行判异的控制用控制图。
从图中可以看到,准则3、4、7在实际使用时基本无效。
首先,准则3主要是用于监测过程平均值的偏移,但由于抽样频率较低,使均值的这种偏移在满足准则3报警条件之前已经出界或满足其它判异准则报警条件了;准则4主要用于检测过程数据是否存在分层不当的现象,圆周数据来自同一机台,准则4的报警条件也不可能满足;准则7主要用于检测数据的真实性,也可以不予考虑。
准则1、2、5、6、8对异常波动的监测效率有所差别,该批数据中共有15个大小各异的波动,见表1中A-O。
对于这些波动的监测效率,可以通过表1进行进一步比较分析。
表1圆周控制图不同判异准则效率比较
波动
A
B
C
D
E
F
G
H
J
K
L
M
N
O
准则1
1,6
9
20
29,30,
35
45
52
65,67
94,95
97,99
101,
102
116
139,
144
148,
150
准则2
43-48
76
119
准则5
2,6
20,22,24
27-34
46
66,68
95
97,99
101,102
116,118,120
139-
144
149
准则6
16-24
29-34
41
54
69-74
99
115,116,118
141-
144
准则8
101,
102
144
在表1中的数字代表每一个波动被不同判异准则报警的点的序号,如波动A在第1和第6点报警,都是违背了判异准则1;在第2和第6点报警,都是违背了判异准则5。
从表中可以看出,准则2和准则8的监测效率较差,异常波动的检出能力不高,需要对这两个判异准则进行修改,以提高检出能力。
八项判异准则的第一类错误(虚发报警)的概率分别为:
;
可以看出,准则2、8的检出能力弱的主要原因就是其虚发报警的概率都比较小,可以适当增加虚发报警的概率,以提高检出力。
对于准则2,将连续9点在中心线同一侧改为连续8、7、6点在中心线同一侧并比较虚发报警的概率的变化:
连续9点在中心线同一侧的虚发报警概率为
;
连续8点在中心线同一侧的虚发报警概率为
;
连续7点在中心线同一侧的虚发报警概率为
;
连续6点在中心线同一侧的虚发报警概率为
;
当该准则从连续9点变为7点时,虚发报警的概率都比较小,而当变为6点时,虚发报警的概率过大,因此可认为将该准则修改为连续7点在中心线同侧比较适宜。
对于准则8,将连续8点距离中心线超过1个标准差(中心线的上方和下方)改为连续7、6、5、4点距离中心线超过1个标准差(中心线的上方和下方)并比较虚发报警的概率的变化:
连续8点距离中心线超过1个标准差(中心线的上方和下方)的虚发报警概率为
;
连续7点距离中心线超过1个标准差(中心线的上方和下方)的虚发报警概率为
;
连续6点距离中心线超过1个标准差(中心线的上方和下方)的虚发报警概率为
;
连续5点距离中心线超过1个标准差(中心线的上方和下方)的虚发报警概率为
;
连续4点距离中心线超过1个标准差(中心线的上方和下方)的虚发报警概率为
;
虽然连续4点时检测能力可以满足要求,但是虚发报警概率太高,因此准则8也不予考虑。
表2圆周控制图判异准则改进后效率比较
波动
A
B
C
D
E
F
G
H
J
K
L
M
N
O
准则1
1,6
9
20
29,30,
35
45
52
65,67
94,95
97,99
101,
102
116
139,144
148,
150
准则2
43-48
76
119
改进准则2
27
41-48
74-76
101-103
117-120
144
准则5
2,6
20,22,24
27-34
46
66,68
95
97,99
101,102
116,118,120
139-144
149
准则6
16-24
29-34
41
54
69-74
99
115,116,118
141-144
从表2可以看出,当该准则从连续8点变为5点时,虚发报警的概率都比较小,而当变为4点时,虚发报警的概率过大,因此可认为将该准则修改为连续5点距离中心线超过1个标准差(中心线的上方和下方)比较适宜。
由此,圆周的均值-标准差控制图确定采用准则1为主、准则2、5、6为辅,对过程质量进行监控。
图12重量控制图判异准则分析
图12是对重量数据采用均值-标准差控制图进行监控,用八项判异准则进行判异的控制用控制图。
从图中可以看到,准则2、3、4、7、8在实际使用时基本无效,可以不予考虑。
准则1、5、6对异常波动的监测效率有所差别,该批数据中共有7个大小各异的波动,见表3中A-G。
对于这些波动的监测效率,可以通过表3进行进一步比较分析。
表3重量控制图不同判异准则效率比较
波动
A
B
C
D
E
F
G
准则1
46,
55,
64,
98,
118
准则5
47,48
55,60
64,65
98
准则6
86
疑为误判
106,107
121-123
由此,重量的均值-标准差控制图可采用准则1为主,准则5、6为辅,对过程质量进行监控。
4.3.5.2计数型控制判异准则的优化
外观控制图的判异准则主要采用准则1(距离中心线超过3个标准差)进行过程质量监控。
4.3.5.3控制图判异准则确定
以将控制图的“两种错误”控制在较低的概率为原则,根据卷接包装工序实际情况,对常规控制图的八项判异准则进行了选择、修订和优化,确定了控制图判异准则如表4所示:
表4控制图判异准则
准则序号
判异准则内容
适用的控制图
准则一
1个点,距离中心线超过3个标准差
烟支圆周、重量、吸阻、总通风率均值控制图和标准差控制图;烟支空头、烟支外观缺陷、小盒外观、盒装缺陷、条装缺陷、箱装缺陷的计数型控制图
准则二
连续7点在中心线同一侧
烟支圆周均值控制图
准则五
3点中有2点,距离中心线超过2个标准差(在中心线的同一侧)
烟支圆周均值控制图、烟支重量均值控制图
准则六
5点中有4点,距离中心线超过1个标准差(在中心线的同一侧)
烟支圆周均值控制图、烟支重量均值控制图
4.3.6控制图应用流程
图13统计过程控制应用流程
6.6统计过程判稳分析
6.7
观察均值控制图所有的点是否基本上都落在控制界限内并且在控制界限内的点是否随机排列,依据A类和B类判稳准则(如表5所示)判定过程是否处于稳定状态,如过程处于稳定状态,则将分析用控制图的控制限确定为控制用控制图的控制限;如过程处于非稳定状态,应剔除异常点,重新计算并修正控制限直至过程处于稳定状态,同时采取适当的补救措施以消除可查明原因并防止其再次出现。
如异常点的数量超过子组数量的20%应重新收集数据。
表5控制图判稳准则
类别
判稳准则类别
判稳准则
适用的控制图
A类
所有的点基本上都落在控制界限内
1