毕业设计炼焦工艺流程的设计.docx
《毕业设计炼焦工艺流程的设计.docx》由会员分享,可在线阅读,更多相关《毕业设计炼焦工艺流程的设计.docx(25页珍藏版)》请在冰豆网上搜索。
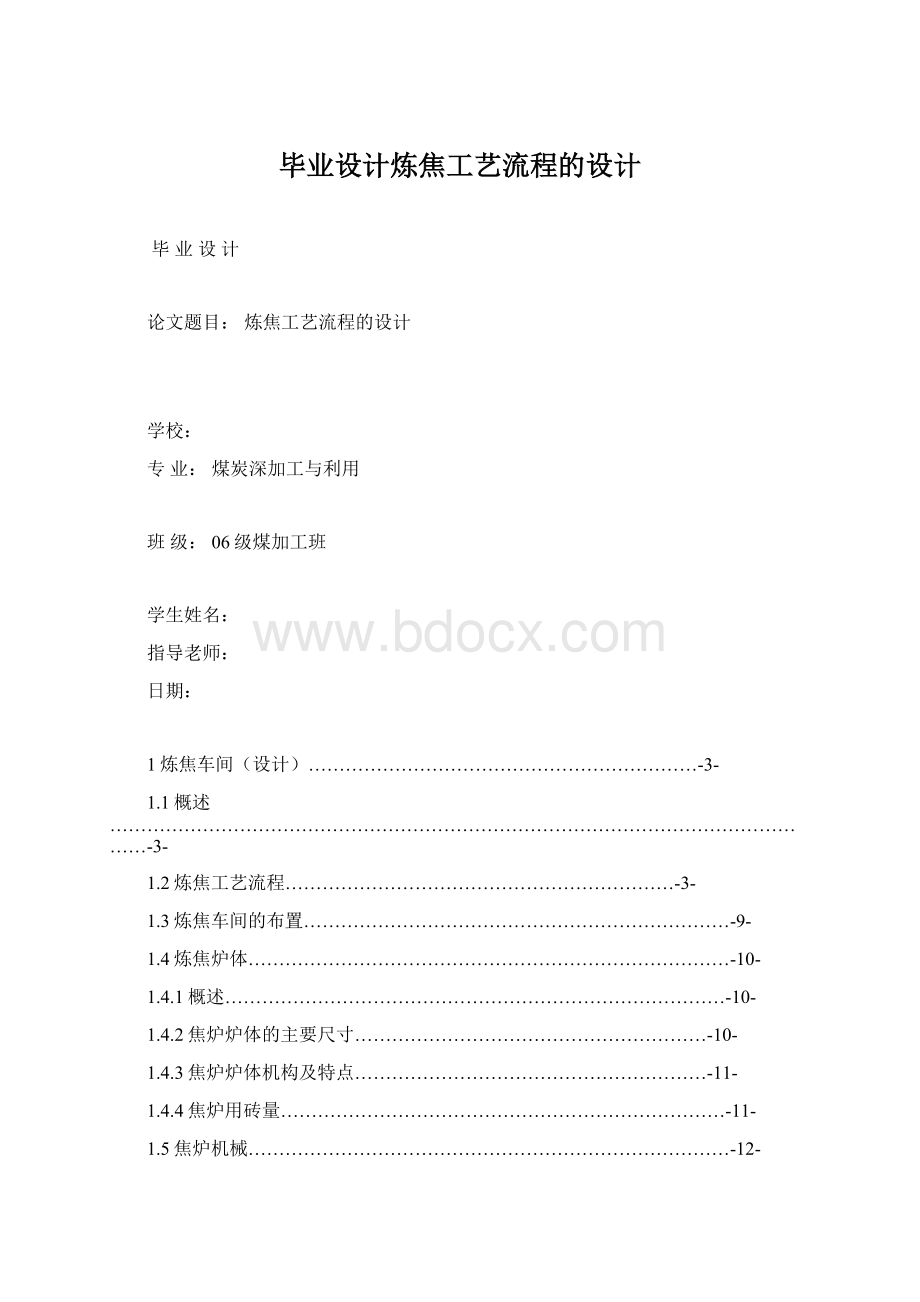
毕业设计炼焦工艺流程的设计
毕业设计
论文题目:
炼焦工艺流程的设计
学校:
专业:
煤炭深加工与利用
班级:
06级煤加工班
学生姓名:
指导老师:
日期:
1炼焦车间(设计)………………………………………………………-3-
1.1概述………………………………………………………………………………………………………-3-
1.2炼焦工艺流程………………………………………………………-3-
1.3炼焦车间的布置……………………………………………………………-9-
1.4炼焦炉体……………………………………………………………………-10-
1.4.1概述………………………………………………………………………-10-
1.4.2焦炉炉体的主要尺寸…………………………………………………-10-
1.4.3焦炉炉体机构及特点…………………………………………………-11-
1.4.4焦炉用砖量………………………………………………………………-11-
1.5焦炉机械……………………………………………………………………-12-
1.5.1焦炉机械配置……………………………………………………………-12-
1.5.2焦炉机械的主要性能及特点…………………………………………-12-
1.6工艺装备……………………………………………………………………-15-
1.6.1集气系统…………………………………………………………………-15-.
1.6.2护炉铁件…………………………………………………………………-15-
1.6.3加热交换系统……………………………………………………………-15-
1.6.4熄焦系统…………………………………………………………………-16-
1.7熄焦装置……………………………………………………………………-16-
1.7.1概述………………………………………………………………………-16-
1.7.2干熄焦装置主要工艺参数…………………………………………-16-
1.7.3干熄焦工艺流程………………………………………………………-17-
1.7.4干熄焦装置的布置……………………………………………………-18-
1.8焦炉除尘设施……………………………………………………………-18-
1.8.1阵发性排放烟尘治理………………………………………………-18-.
1.8.1.1装煤除尘……………………………………………………………-18-
1.8.1.2出焦除尘……………………………………………………………-20-
1.8.1.3熄焦除尘……………………………………………………………-21-
1.8.2连续性排放烟尘治理………………………………………………-22-
1.9辅助设施……………………………………………………………………-22-
2筛叫系统(设计)…………………………………………………………-22-
2.1概述…………………………………………………………………………-22-
2.2设施及主要设备…………………………………………………………-22-
2.2.1焦台………………………………………………………………………-22-
2.2.2筛、贮焦楼……………………………………………………………-22-
2.2.3焦场………………………………………………………………………-24-
2.3其它…………………………………………………………………………-24-
炼焦工艺流程的设计(可不要)
摘要:
(用黑体)根据实习具体内容设计一个炼焦车间为2×50孔JN60型焦炉,年产干全焦93.62万t,日产焦炉煤气109.44m3。
采用干法熄焦(预留干熄焦装置),焦炉的装煤及出焦除尘均采用除尘地面站方式。
现将工艺流程、焦炉炉体、干熄焦装置、焦炉除尘设施、焦炉机械做简单介绍。
关键词:
(用黑体)工艺流程、工艺流程图、工艺的装备/设备、焦炉的机械、炉体的简介、干熄焦的装置、焦炉除尘设施(选一些有实际意义和代表性的词,4~5个就够了,像炼焦炉、四大车等)
摘要和关键词独立用一页,完整的还需翻译成英文(你们不要求,就不用)。
任务分析与方案确定
(根据所给条件(已知条件)和要达到的任务,来确定需要哪些过程和步骤、流程等,后面再到具体车间的设计,这样的话就更连贯,而不觉得突兀。
也就是现在要采用假设的方法,要站在焦化厂还没建起前的情景下来做,即采用逆向的思维。
)
1炼焦车间
1.1概述
炼焦车间新建2×50孔JN60型焦炉,年产干全焦93.62万t,日产焦炉煤气109.44m3。
配套建设干熄焦及1×12000kw/h发电装置,当干熄焦装置检修或事故时,采用新型湿法熄焦作为备用。
焦炉的装煤及出焦除尘均采用除尘地面站方式。
炼焦基本工艺参数
炭化室孔数2×50孔
炭化室有效容积38.5m3/孔
每孔炭化室装煤量(干)28.5t
焦炉周转时间20h
焦炉年工作日数365d
焦炉紧张操作系数1.07
焦炉加热用煤气低发热值:
焦炉煤气17900kJ/m3
1.2炼焦工艺流程
由备煤车间送来的配合煤装入煤塔。
装煤车按作业计划从煤塔取煤,经计量后装入炭化室内,煤料在炭化室内经过一个结焦周期的高温干馏炼制成焦炭和荒煤气。
在装煤的同时,地面站集尘系统把从装煤孔逸出的烟气抽出,经集尘管导至地面站,除尘净化后排入大气。
(行距统一:
1.5倍)
预留干熄焦流程炭化室内的焦炭成熟后,用推焦机推出,经拦焦机导入焦罐内,并由电机车牵引至干熄站进行干法熄焦,所产生的蒸汽用于发电,熄焦后的焦炭送往筛贮焦工段,经筛分按级别贮存待运。
当干熄焦装置检修或事故时需利用备用的湿法熄焦时,炭化室内成熟的焦炭经拦焦机导入熄焦车内,并由电机车牵引至熄焦塔内进行喷水熄焦。
熄焦后的焦炭卸至晾焦台上,晾置一定时间后送往筛贮焦工段,经筛分按级别贮存待运。
焦炉出焦时产生的烟尘,由拦焦机集尘罩将其收集,并通过集尘管导至地面站,经除尘净化后排入大气。
煤在炭化室干馏过程中产生的荒煤气汇集到炭化室顶部空间,经过上升管,桥管进入集气管,约700℃左右的荒煤气在桥管内被氨水喷洒冷却至90℃左右。
荒煤气中的焦油等同时被冷凝下来。
煤气和冷凝下来的焦油同氨水一起经吸煤气管道送入煤气净化车间。
焦炉加热采用焦炉煤气,由外部管道架空引入。
经预热后送到焦炉地下室。
通过下喷管把煤气送入燃烧室立火道底部与废气交换开闭器进入的空气汇合燃烧。
燃烧后的废气通过立火道顶部跨越孔进入下降气流的立火道,再经过蓄热室,由格子砖把废气的部分显热回收后,经过小烟道、废气交换开闭器、分烟道、总烟道、烟囱,排入大气。
上升气流的煤气和空气与下降气流的废气由交换传动装置定时进行换向。
工艺流程见图1-1。
本项目炼焦采用干熄焦,拟布置为:
新建450孔JN60型焦炉布置在一条中心线上,组成一个大炉组,每250孔焦炉为一个独立炉组。
在每组焦炉的焦侧各布置一座高135m烟囱。
在每个炉组的炉端台外各设一套干熄焦装置及湿法熄焦系统。
在1号焦炉干熄焦装置外侧设2×12000KW/h发电装置
1-1炼焦工艺流程图
1-2炼焦生产工艺流程:
现代焦炭生产过程分为洗煤、配煤、炼焦和产品处理等工序。
工艺流程图如下
炼焦车间主要设备见表1-1。
炼焦车间主要设备
序
号
名 称
数量(台)
操作
备用
1
备煤中PFCK1618型可逆锤式粉碎机
2
1
2
JN60型焦炉
2
0
3
干熄炉
1
0
4
干熄焦锅炉2×1200MW
1
0
5
湿法熄焦熄焦塔
1
0
6
装煤车
2
1
7
推焦机
1
1
8
拦焦机
1
1
9
电机车(干湿两用)
2
1
10
液压交换机
2
0
11
焦罐车
4
2
12
熄焦车(定点接焦)
2
0
13
干熄焦地面除尘站
1
0
14
装煤除尘地面站
1
0
15
出焦除尘地面站
1
0
16
筛贮焦地面除尘站
1
0
1-3设备流程图〔1〕
炭化室内成焦过程如图所示。
1-4结焦过程示意图〔2〕
1.3炼焦车间布置
新建250孔JN60型焦炉布置在同一条中心线上,组成一个炉组。
中间设一座三跨双曲线斗槽的煤塔,煤塔与焦炉之间设炉间台,焦炉端部设炉端台,两侧设机焦侧操作台。
煤塔下部各层分别设有电子秤及其操作室、配电室、值班室、交换机室和仪表室。
炉间台主要布置单斗提升机和煤气管道。
炉端台顶层设工人休息室和10t电动葫芦;中层设炉门修理站和推焦杆、平煤杆更换站;下层设调火工室、热修瓦工室及灰浆搅拌机室。
在焦炉焦侧布置一座高135m烟囱。
在焦炉炉端台外设置1套干熄焦装置并设一套1×12000kw/h发电装置及备用新型湿法熄焦系统。
在机侧建筑物边界线外设高压氨水泵房及其配套设施。
1.4焦炉炉体
1.4.1概述
进入七十年代以后,焦炉炭化室加高加宽、提高单孔炭化室产焦量已成为世界炼焦技术的发展方向。
单以炭化室高度而言,至1975年国外6.0m以上焦炉已建成5000多孔,近10多年来,日本、德国、法国等国家先后建设7.0m以上大型焦炉40多座,炭化室高度最高已达到8.2m。
我国自八十年代中期从日本引进450孔6.0m“M”型焦炉在宝钢投产以后,由我国自行设计建造的第一座6.0m焦炉于1987年底在北京焦化厂建成投产;接着该厂又建成了第二座6.0m焦炉,随后宣钢、攀钢、首钢、石家庄、马钢、昆钢、天津、邯郸、山焦、涟钢等大型钢铁公司的新建焦炉或焦炉改造都选择了6.0m焦炉。
宝钢二、三期我国分别自行设计的450孔全下调6.0m焦炉先后建成投产。
至2005年底,我国已有6米大型焦炉90座。
JN60型焦炉在我国已有二十年的生产历史,生产操作和管理水平较高,代表我国焦炉的先进水平。
6.0焦炉与4.3m焦炉相比,有以下优点:
a)6.0m焦炉由于炉体加高,炭化室单孔容积增大,装炉煤堆比重增加,在相同炼焦配煤比的情况下,M40提高2~5%,M10下降~1%,焦炭质量有较大的改善。
b)经计算,6.0m焦炉蓄热室格子砖换热面积比4.3m焦炉大20%,废气出口的温度低,焦炉的热效率提高,可降低炼焦能耗约2%。
c)6.0m焦炉的设备机械化操作水平和控制水平比4.3m焦炉要高很多,因此,其劳动强度低。
d)在产量相同的情况下,由于日出炉次数6.0m焦炉比4.3m焦炉减少,同时6.0m焦炉比4.3m焦炉每天开启密封装置的总次数减少,另外,6.0m焦炉设备比4.3m焦炉的管理维护水平要高。
因此,在相同环保设施效果前提下,6.0m焦炉操作中烟尘排放量比4.3m焦炉少,更有利于环境保护。
因此本项目采用国内先进的JN60型焦炉。
1.4.2焦炉炉体的主要尺寸如表1-2
序号
名称
单位
数量
1
炭化室全长
mm
15980
2
炭化室有效长
mm
15140
3
炭化室全高
mm
6000
4
炭化室有效高
mm
5650
5
炭化室平均宽
mm
450
6
炭化室锥度
mm
60
7
炭化室中心距
mm
1350
8
炭化室有效容积
m
38.5
9
立火道中心距
mm
480
10
加热水平
mm
1005
1.4.3焦炉炉体结构及特点
a)JN60型焦炉的结构为双联火道、废气循环、焦炉煤气下喷式焦炉。
它是在总结国内6m焦炉多年生产经验的基础上,运用国内外的新技术、新材质、新经验设计的新型焦炉。
此焦炉具有结构严密、合理、加热均匀、热工效率高的特点。
b)蓄热室主墙是用带有三条沟舌的异型砖相互咬合砌筑的,而且蓄热室主墙砖煤气道管砖与蓄热室无直通缝,保证了砖煤气道的严密。
蓄热室单墙为单沟舌结构,用异型砖相互咬合砌筑,保证了墙的整体性和严密性。
c)蓄热室内装有薄壁大蓄热面格子砖,比厚壁格子砖增加1/3的蓄热面,可使废气离开蓄热室的温度降低30~40C。
d)改进了蓄热室封墙的设计,内封墙改用硅砖,取消了效果不佳的隔热罩,改用近年已在焦炉上广泛使用、隔热和密封效果都很好的新型保温材料抹面,再加一层20mm硅酸钙隔热板,因此减少了封墙漏气,改善了炉头加热,减少了热损失,改善了操作环境。
e)为保证炭化室高向加热均匀,设计采用了加大废气循环量和设置焦炉煤气高灯头(高灯头距炭化室底400mm)等措施。
此外,由于采用废气循环,可以降低废气中的氮氧化物含量,减少了对大气的污染。
f)炭化室墙采用“宝塔”砖结构,它消除了炭化室与燃烧室之间的直通缝,增强了炉体的严密性,使荒煤气不易窜漏,并便于炉墙剔茬维修。
g)为了适应配煤需要,确定加热水平高度为1005mm,可使焦饼上部与下部同时成熟,还可以避免炉顶空间长石墨过多。
h)炉顶装煤孔和上升管孔砌体用带有沟舌的异型砖砌筑,并在装煤孔及上升管孔座砖上加铁箍,保证了它的整体性,使炉顶更为严密,减少了荒煤气的窜漏,防止炉顶横拉条的烧损。
i)加大装煤孔和上升管孔底部砖砌体的倾斜角,使之尽量接近入炉煤的安息角,以达到装煤时煤气流通畅的目的。
本设计为机侧设单集气管的焦炉,所以特将机侧第一装煤孔至上升管之间的炉顶空间加大,并加大上升管孔底部面积,使流经此区域的荒煤气流速降低,有利于荒煤气中夹带的焦粉沉降,避免大量焦粉带进集气管。
j)炉顶面焦炉中心至机、焦侧正面,设有50mm的坡度,以利炉顶排水。
k)炉顶内层的红砖改为同强度的漂珠砖,增强了隔热效果。
1.4.4焦炉用砖量如表1-3
序号
名称
单位
数量
1
硅砖
t
9354.1
2
粘土砖
t
1943.7
3
粘土格子砖
t
1885
4
高铝砖
t
40.8
5
缸砖
t
163
6
红砖
t
36.3
7
高强隔热砖
t
207.6
8
漂珠砖
t
411
说明:
此表为150孔JN60型焦炉用砖量
1.5焦炉机械
1.5.1焦炉机械配置如表1-4
序
号
名 称
数量(台)
操作
备用
1
装煤车
1
1
2
推焦机
1
1
3
拦焦机
1
1
4
电机车(干湿两用)
1
1
5
液压交换机
2
0
6
焦罐车
2
1
7
熄焦车(定点接焦)
0
1
1.5.2焦炉机械的主要性能及特点
焦炉机械是在总结国内焦炉机械操作经验的基础上,吸取了国外焦炉机械的先进技术,以提高机械效率、降低劳动强度和改善操作环境为出发点,以先进、安全、实用为原则进行设计和制造的。
全套焦炉机械是按5-2推焦串序进行操作,采用单元程序控制,并带有手控装置。
推焦机和电机车之间设有事故联锁装置。
各司机室设有载波电话,提高设备运行的安全性和可靠性。
各机械的主要性能及特点如下:
1)装煤车
装煤车为除尘式装煤车。
采用一次定位、机械揭闭装煤孔盖以及机械清扫上升管。
设计采用螺旋给料、顺序装煤,并设有炉顶清扫装置。
煤塔漏咀的开闭和煤塔震煤的操作均在司机室内控制,方便可靠。
司机室密闭隔热,内设空调,改善了操作条件。
为了实现无烟装煤操作,装煤车上设与焦侧集尘干管对接的套筒,下煤导套等。
除尘装煤车主要技术性能如下:
煤斗数量4个
装煤方式螺旋给料
走行速度约90m/min
轨道中心距7780mm
电机总功率约280kW
设备自重约170t
2)推焦机
推焦机采用5-2串序一次对位操作,推焦电流自动显示和记录。
设有推焦、平煤、启闭炉门装置,炉门、炉框和小炉门的机械清扫机构和头尾焦处理、清扫上升管根部石墨装置。
司机室和电气室设空调。
各单元程序操作,均由PC机控制。
推焦机主要技术性能如下:
钢结构主体构架形式门型
走行速度约60m/min
轨道中心距12000mm
电机总功率约450kW
设备自重约414t
3)拦焦机
拦焦机采用一次定位型式,设有取闭炉门和导焦机构,机械清扫炉门、炉门框机构,头尾焦回收装置,烟尘收集和导出机构,炉台清扫装置等。
拦焦机主要技术性能如下:
走行速度约60m/min
轨道中心距2700mm
电机总功率约230kW
设备自重约220t
4)电机车
炭化室内的焦炭成熟后,用推焦机推出,经拦焦机导入焦罐内,并由电机车牵引至干熄站进行干法熄焦。
电机车运行在焦炉焦侧的熄焦车轨道上,用于牵引和操纵焦罐车或湿熄焦车,它两端都有牵引装置,既能满足干法熄焦的作业要求,又能满足湿法熄焦的作业要求。
具有运行速度快,调速性能好,对位准确且行车安全的特性。
电机车采用变频调速。
电机车的车体形式为两层固定双轴式台车,主要由车体﹑走行装置﹑制动装置﹑气路系统﹑空调系统及电气系统等组成。
车体由司机室﹑机械室﹑电气室﹑台车﹑平台及走梯等组成。
电机车还设有电源滑触线支架等。
当干熄焦装置检修或事故时需利用备用的湿法熄焦时,炭化室内成熟的焦炭经拦焦机导入熄焦车内,并由电机车牵引至熄焦塔内进行喷水熄焦。
电机车主要技术性能如下:
车体型式两层固定双轴台车式
轨距2108mm
轨型QU100
电源AC3P660V,50Hz
牵引重量约220t(满罐时)
走行距离90~300m/单程
电机车的周转时间≤10min
走行速度约180、60、10m/min
走行调速方式变频调速(VVVF)
干熄站对位精度±20mm
制动方式能耗制动﹑盘式制动和运载车的气闸制动
空压机螺杆式空压机
司机室及电气室用空调装置各1台
机械连接方式刚性插销连接
气路及电路连接快速接头
电机车自重约45t
电机车总功率约300kW
5)液压交换机
每台液压交换机设有液压站、电控屏、操作台、行程指示装置。
液压站采用双泵、双阀系统,互为备用,并有手动装置。
在煤气低压时,采用自动报警和切断煤气供应等安全措施,交换机的操作全部采用PC机控制。
液压交换机主要技术性能如下:
交换周期20min
自动交换一次时间46sec
手动交换一次时间约10min
电机总功率7.5kW
设备自重约6t
6)焦罐车
焦罐车由旋转焦罐及运载车组成,总重约98t。
焦罐主要由罐体﹑内衬板﹑可摆动的底闸门及带导向辊轮与底闸门联动的吊杆等组成。
●焦罐的主要技术规格为:
数量3个(2个操作1个备用)
焦罐型式对开底闸门与吊杆联动式
形状圆形
结构型钢与钢板焊接结构
焦罐有效容积约25t焦炭
焦罐重量约44t
●主要材质:
焦罐本体Q235-B
内衬板耐热球墨铸铁及耐热铸钢
隔热材料陶瓷纤维垫
底闸门不锈钢
运载车主要由台车框架﹑焦罐旋转装置及焦罐提升导向轨道等组成。
主要技术规格为:
数量3台(2台操作1台备用)
形式鞍型构架(带焦罐旋转装置)
结构型钢与钢板焊接结构
荷重约77t(满罐时)
旋转速度最大7rpm
旋转速度的控制方式VVVF
旋转用电机约30kW
运载车重约54t
移动方式由电机车牵引
轨距2108mm
轨型QU100
制动方式气闸制动
1.6工艺装备
1.6.1集气系统
集气系统包括上升管、桥管、阀体、水封盖、集气管、吸气弯管、高低压氨水管道以及相应的操作台等。
设计采用单集气管,设在机侧,采用双吸气管,吸气弯管上设手动和自动调节翻板。
自动调节集气管的压力,使集气管内的压力保持稳定,保证结焦末期炭化室的底部压力不低于5Pa。
集气管设自动放散点火装置以提高环保水平。
上升管内衬粘土砖和隔热材料并在外侧设隔热罩,降低上升管外表面温度,改善了炉顶的操作条件。
上升管下部采用铸铁座与炉体相接,上部用水封盖密封。
桥管与水封阀的连接采用水封结构,氨水可在内部形成水封,避免荒煤气的泄漏。
桥管上装有高低压氨水喷嘴,通过三通球阀切换用于喷洒低压氨水以降低荒煤气温度或喷射高压氨水来配合装煤车的顺序装煤,较顺利地将大部分的荒煤气导入集气管,而装煤时产生的部分烟气则经除尘装煤车抽吸导入集尘干管,送至除尘地面站,实现无烟装煤操作。
集气管设置高压氨水清扫装置,供定期分段清扫使用,这样减轻了工人的劳动强度。
1.6.2护炉铁件
护炉铁件包括炉柱、纵横拉条、弹簧、保护板、炉门及炉门框等。
炉门采用弹簧刀边、弹簧门栓、悬挂式空冷炉门,炉门对位时位置的重复性好,弹性刀边对炉门框能始终保持一定压力,防止炉门冒烟冒火。
保护板为工字型大保护板,有效保护了炉头免受破坏。
炉柱采用单H型钢,沿焦炉高向设置七线小弹簧。
在纵横拉条的端部设有弹簧组,能均匀地对炉体施加一定压力,保证了焦炉整体结构的完整和严密。
1.6.3加热交换系统
焦炉采用焦炉煤气加热。
加热煤气主管上设有温度、压力、流量的测量和调节装置。
各项操作参数的测量、显示、记录、调节和低压报警由自动控制仪表来完成。
焦炉煤气系统设有煤气预热器以保证入炉煤气温度的稳定。
焦炉煤气加热为下喷式,主管布置在地下室。
采用交换旋塞、调节旋塞及孔板盒来进行各横排管间的煤气交换和煤气流量的调节,焦炉煤气小支管流量由喷嘴调节。
在废气系统中,每座焦炉的分烟道设自动调节翻板,总烟道设手动调节翻板,使加热系统的吸力得到适当调节,以利于焦炉加热的稳定和降低炼焦能耗。
焦炉加热用的煤气、空气和燃烧后的废气在加热系统内的流向由液压交换机驱动交换传动装置来控制,每隔20~30分钟换向一次。
交换系统为自动控制系统(也可以手动控制),同时设有自动和手动事故控制系统。
1.6.4熄焦系统
设计以干法熄焦为主。
当干熄焦装置年修或出现故障时,利用新开发的湿法熄焦系统熄焦。
湿法熄焦采用一点定位式熄焦车和特殊设计的熄焦塔。
熄焦塔高度约为68m,熄焦塔内设有新型快速熄焦装置、水雾捕集装置以及二层折流板式除尘装置。
一点定位接焦式熄焦车到达熄焦塔固定位置后,熄焦系统开始对红热的焦炭进行熄焦,时间控制在70~90s。
熄焦后的焦炭水分可控制在~3%且水分稳定,同时使焦炭的粒度更加均匀,可大大改善高炉内的炉料透气性。
当熄焦系统开始工作时,水雾捕集系统也同时启动并在熄焦塔内形成一层水雾,熄焦时产生的大量熄焦逸散物在热浮力的作用下急剧上升,在经过水雾捕集系统形成的雾层时得到冷却,蒸汽中的粉尘颗粒一部分被洗涤掉,其余大部分形成了以粉尘颗粒为内核的冷凝液滴,随蒸汽继续上升。
在熄焦塔的顶部设有二层折流板式除尘装置。
折流板式除尘装置由木架、除尘板组成。
经过水雾捕集系统洗涤冷却的蒸汽在熄焦塔内继续上升,冷却后的气体速度有所下降,在通过第一道折流板捕尘格栅缝隙时,以粉尘颗粒为内核的冷凝液滴被静电吸收并通过机械碰撞而沉淀在格栅上。
通过第一道折流板后的其余蒸汽继续上升但气体流速进一步降低,蒸汽中的部分含尘冷凝液滴在重力的作用下而下落,当蒸汽通过第二道折流板时再次得到净化,最后被净化的汽体从熄焦塔出口排入大气。
除尘装置的除尘片上附着了焦粉颗粒,定期用水喷淋洗涤。
熄焦产生的含有大量污染物的蒸汽在经过水雾洗涤、冷却、重力沉降以及二次折流板捕集净化后,大大降低了含尘量,吨焦散发的焦粉量可控制在50g以下,符合国际上通行的污染物排放