现场管理炼焦车间工艺流程.docx
《现场管理炼焦车间工艺流程.docx》由会员分享,可在线阅读,更多相关《现场管理炼焦车间工艺流程.docx(19页珍藏版)》请在冰豆网上搜索。
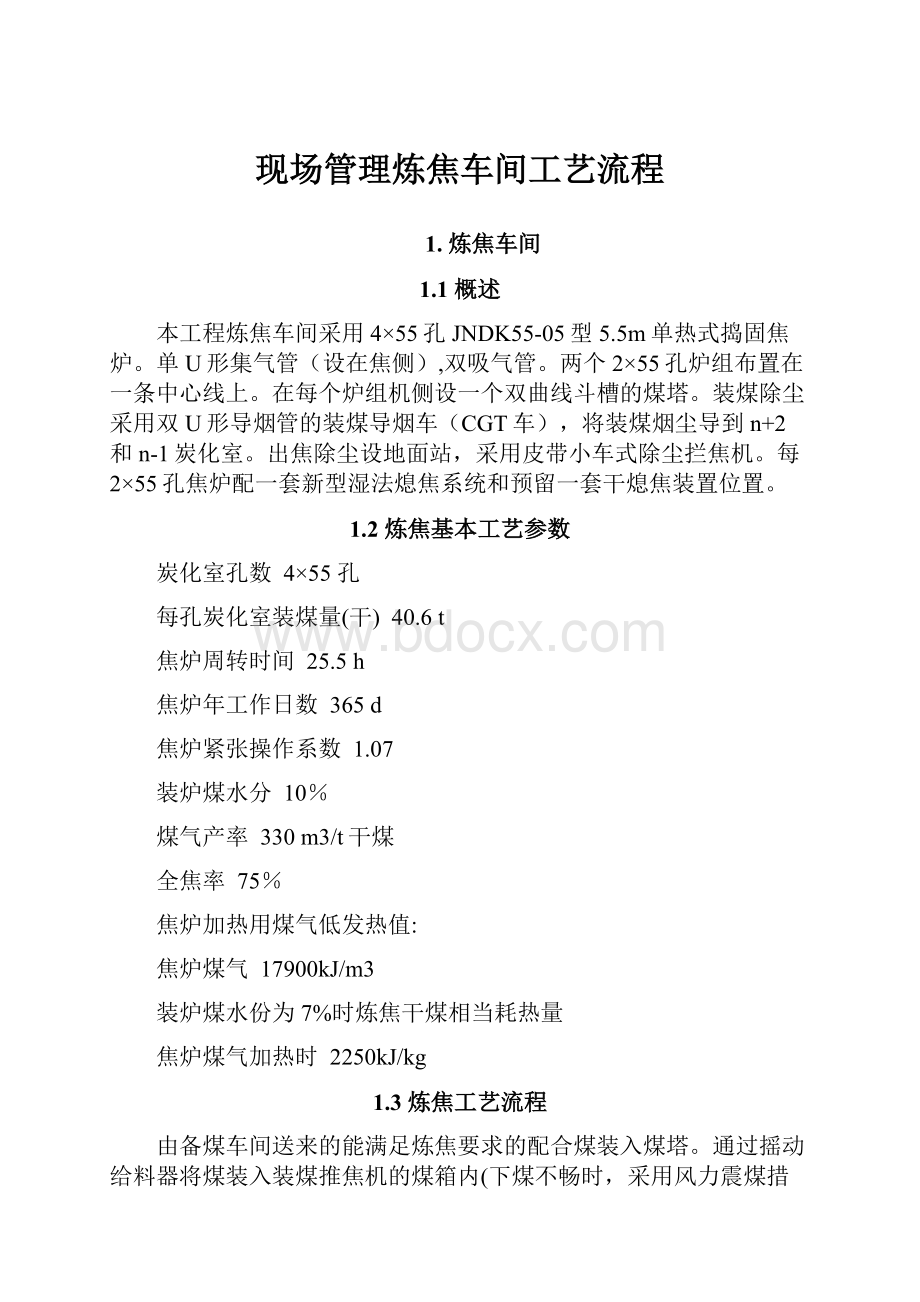
现场管理炼焦车间工艺流程
1.炼焦车间
1.1概述
本工程炼焦车间采用4×55孔JNDK55-05型5.5m单热式捣固焦炉。
单U形集气管(设在焦侧),双吸气管。
两个2×55孔炉组布置在一条中心线上。
在每个炉组机侧设一个双曲线斗槽的煤塔。
装煤除尘采用双U形导烟管的装煤导烟车(CGT车),将装煤烟尘导到n+2和n-1炭化室。
出焦除尘设地面站,采用皮带小车式除尘拦焦机。
每2×55孔焦炉配一套新型湿法熄焦系统和预留一套干熄焦装置位置。
1.2炼焦基本工艺参数
炭化室孔数4×55孔
每孔炭化室装煤量(干)40.6t
焦炉周转时间25.5h
焦炉年工作日数365d
焦炉紧张操作系数1.07
装炉煤水分10%
煤气产率330m3/t干煤
全焦率75%
焦炉加热用煤气低发热值:
焦炉煤气17900kJ/m3
装炉煤水份为7%时炼焦干煤相当耗热量
焦炉煤气加热时2250kJ/kg
1.3炼焦工艺流程
由备煤车间送来的能满足炼焦要求的配合煤装入煤塔。
通过摇动给料器将煤装入装煤推焦机的煤箱内(下煤不畅时,采用风力震煤措施),并将煤捣固成煤饼,装煤推焦机按作业计划从机侧炉门送入炭化室内。
煤饼在炭化室内经过一个结焦周期的高温干馏炼制成焦炭和荒煤气。
炭化室内的焦炭成熟后,用装煤推焦机推出,经拦焦机导入熄焦车内,由电机车牵引熄焦车至熄焦塔内进行喷水熄焦。
熄焦后的焦炭卸至凉焦台上,冷却一定时间后送往筛贮焦工段进行筛分。
煤在炭化室干馏过程中产生的荒煤气汇集到炭化室顶部空间,经过上升管,桥管进入集气管,约800℃左右的荒煤气在桥管内被氨水喷洒冷却至85℃左右。
荒煤气中的焦油等同时被冷凝下来。
煤气和冷凝下来的焦油同氨水一起经吸煤气管道送入煤气净化车间。
焦炉加热用的焦炉煤气,由外部管道架空引入。
分别进入每座焦炉的焦炉煤气经预热器预热至45℃左右送入地下室,通过下喷管把煤气送入燃烧室立火道与从废气开闭器进入的空气汇合燃烧。
燃烧后的废气通过立火道顶部跨越孔进入下降气流的立火道,再经过蓄热室,由格子砖把废气的部分显热回收后经过小烟道、废气交换开闭器、分烟道、总烟道、烟囱,排入大气。
上升气流的煤气和空气与下降气流的废气由交换传动装置定时进行换向。
1.4炼焦车间布置
新建两组2×55孔JNDK55-05型大型捣固焦炉组成两个炉组(即由1,2号和3,4号分别组成)布置在一条中心线上。
在每个炉组机侧设一个双曲线斗槽的煤塔。
煤塔端部设捣固机检修站。
在1,2号焦炉和3,4号焦炉之间分别设炉间台并在2,3号焦炉之间设大间台。
焦炉端部设炉端台,两侧设机焦侧操作台。
煤塔间台主要布置煤气管道、休息室、办公室、配电室、交换机室和集控室等。
炉端台顶层设炉顶工人休息室和5t旋转起重机,中间层设推焦杆托煤板更换站和炉门修理站,底层设工具间。
每两座焦炉共用一个高度120m的烟囱,布置在焦炉的焦侧,在1号、4号炉端台外分别设一套新型湿法熄焦系统,,在大间台焦侧区域预留2×140t/h干熄焦装置。
在1、4号炉端台外预留迁车台位置。
1.5焦炉炉体
2.5.1焦炉炉体的主要尺寸
见附表1
2.5.2焦炉炉体结构及特点
a)JNDK55-05F型捣固焦炉为双联火道,废气循环,宽炭化室,焦炉煤气下喷的复热式焦炉,是在总结焦炉多年生产经验的基础上新设计的炉型,此焦炉具有使用原料范围宽,多配入高挥发分弱粘结性煤,生产优质高炉用焦的优点.它在结构上作了许多改进,使焦炉炉体坚固严密,加热均匀,焦炉的操作环境和劳动条件得到了较大改善。
b)炉顶导烟孔和上升管孔砌体,用带有沟舌的大块异型砖砌筑,保证了砌体的整体性,炉顶更加严密,减少了荒煤气的窜漏,防止横拉条的烧损。
c)在炉顶区采用强度大,隔热效率高的漂珠砖和高强隔热砖,替换原焦炉采用的红砖和硅藻土隔热砖,确保炉顶表面层平整、严密,降低了炉顶面温度,改善了操作环境。
d)加热水平为800mm,可使焦饼上下同时成熟,并减少炉顶空间长石墨。
e)该焦炉炭化室的平均宽度为554mm,属于宽炭化室。
宽炭化室焦炉具有很大的优越性,不仅推焦容易、改善焦炭质量、延长焦炉寿命,而且还减少了机械磨损、减少了推焦次数,减少了污染。
f)炭化室墙采用了较为先进的“宝塔”形砖,它不仅清除了炭化室与燃烧室之间的直通缝,使炉体严密,荒煤气不易窜漏;并便于炉墙剔茬维修。
g)燃烧室盖顶大砖采取在一对火道内设拱顶的结构,使上面负荷归集在立火道隔墙上,加强了炉体结构强度。
h)燃烧室采用废气循环和加高焦炉煤气灯头结构,保证了沿炭化室高向加热均匀性。
此外,因为有废气循环,可以降低废气中氮氧化合物含量,减弱了对大气的污染。
由于焦炉煤气采用了高灯头,因此当焦炉延长结焦时间操作时,也不会短路。
i)结合生产实践,对立火道底部的斜道口断面积进行了理论研究和计算,新设计的调节砖及其排列,使燃烧室各火道的空气量和煤气量分配更加合理,焦炉投产后几乎不需要调整即可使燃烧室的横墙温度分布均匀,大大地减轻了热工人员更换调节砖的劳动强度。
j)异向气流蓄热室主墙厚290mm,是用带有三条沟舌的异型砖相互咬合砌筑的,而且,蓄热室主墙上砖煤气道与外层墙面间无直通缝,保证了砖煤气道的严密性;同向气流蓄热室单墙厚230mm,是用带单沟舌的异型砖相互咬合砌筑的,保证了墙的整体性和严密性。
k)为增加蓄热室封墙的严密性,取消了效果不佳的隔热罩装置,外抹隔热效果好且又不龟裂的新型保温材料GSY(HCS-23)。
l)小烟道采用扩散型箅子砖,利用扩散型的特性使大小孔径正反方向所造成的不同阻力来克服小烟道内变量气体所产生的内外压力差,这种箅子砖和方孔箅子砖相比,提高了格子砖的冲刷系数,可使废气温度降低200C左右。
m)为了保证炭化室具有的宽度,又要保证该焦炉具有足够的强度,我们采用了加大炭化室中心距的措施,炭化室中心距设计为1350mm。
2.5.3焦炉用砖量
见附表2
焦炉主要尺寸及技术指标表附表1
序号
名称
单位
数量
1
炭化室全长
mm
15980
2
炭化室有效长
mm
15220
3
炭化室全高
mm
5550
4
炭化室有效高
mm
5300
5
炭化室平均宽
mm
554
6
炭化室锥度
mm
20
7
炭化室中心距
mm
1350
8
炭化室有效容积
m
44.7
9
燃烧室立火道中心距
mm
480
10
燃烧室立火道个数
个
32
11
加热水平
mm
806
焦炉砖量表附表2
序号
耐火材料名称
需用量(t)
1
硅砖
8700
2
粘土砖
2306
3
粘土格子砖
2036
4
高铝砖
156
5
缸砖
145
6
漂珠砖
419
7
高强隔热砖
262
8
炉门衬堇青石砖
187
9
烟道衬粘土砖
1833
10
膨胀珍珠岩砖
55
注:
此为1×55孔JNDK55-05F型焦炉耐火材料用量
1.6焦炉机械
1.6.1焦炉机械配置
4×55孔焦炉机械配置如下表:
序
号
名称
数量(台)
操作
备用
1
装煤推焦机(左、右型各两台)
4
0
2
拦焦机
2
2
3
装煤导烟车
2
2
4
引进捣固机
4(套)
0
5
电机车
2
2
6
熄焦车
2
2
7
液压交换机
4
0
1.6.2焦炉机械的主要性能及特点
a)装煤推焦机
装煤推焦机分为左、右型。
装煤推焦机设置走行、机械化送煤、余煤回收、炉头烟密封装置、推焦装置、启闭炉门装置以及炉门清扫装置、炉框清扫装置、头尾焦回收处理装置等装置。
且左右型装煤推可以同时在煤塔下工作。
装煤推焦机走行至煤塔下,其煤槽中心与捣固锤杆中心能达到定位要求,并与捣固机设置了联锁。
定位后方可开启捣固机;当捣固机工作完后,捣固锤完全提出煤槽且安全钩锁闭后,装煤推焦机方可走行。
在装煤推焦机上设有煤饼顶部表面压实装置,该装置通过一个双槽钢梁,由齿条传动装置,沿着煤饼长向移动,在震动煤饼的同时刮平震动器前的浮煤,使煤饼顶面压平压实。
装煤推焦机的主要技术规格如下:
轨距12000mm
轨型QU120(U71Mn)
走行速度5~75m/min
走行对位精度±10mm
走行驱动方式六台变频调速电机驱动
装煤速度1.6~16m/min
装煤底版行程17615mm
装煤底版驱动方式变频电机、链条驱动
停电煤槽底板退出柴油发电机组或柴油机驱动
煤槽双活动臂行程2×40mm
电源3Ph,660V,50Hz
供电方式滑触线导入
外形尺寸(长×宽×高)~31600mm×21350mm×13000mm
整车重量~740t
b)拦焦机
拦焦机采用一次对位,设有走行、除尘罩,有取、装炉门和导焦机构,机械清扫炉门、炉门框机构,头尾焦回收装置,拦焦车耐热底板采用耐热耐磨的稀土合金底板。
除尘罩使用0.5mm不锈钢板,材质为0Cr18Ni9Ti。
所有上述单元即可手动操作又可采用单元程序控制(PC)。
拦焦机的主要技术规格如下:
第一轨距焦炉中心线12295mm
轨型QU100
第一轨距第二轨9010mm
走行速度3~60m/min
走行驱动方式4台变频调速电机驱动
外形尺寸(长×宽×高)20000mm×17500mm×8720mm
电源3Ph,380V,50Hz
供电方式滑触线导入
整车重量340t
c)固定式捣固机
固定式捣固机由安全挡装置、导向辊装置、提锤传动装置、停锤装置、捣固锤、机架、集中润滑系统、电控系统等组成。
捣固机捣固锤的数量为30个。
捣固设备由5组6锤捣固机组成。
5组捣固机之间用水平销轴连接,各自位置具有互换性。
采用固定式捣固机,无走行机构,减少维修和故障点。
捣固机的主要技术规格如下:
轨距2000mm
轨型50kg/m
捣固一个煤饼时间≯7min,装煤煤饼密度1.0t/m3(干)以上,捣固煤饼密度均匀,煤饼的稳定性好。
整车重量~60t
d)装煤导烟车(CGT车)
装煤导烟车由车体、启闭导烟孔盖装置、双U形管系统、上升管清扫装置、高低压氨水切换及上升管水封盖关闭装置组成,在装煤导烟车的车体上布置了位于车体机侧的U型导烟管和位于车体中部的U型导烟管,构成双U形管系统,集气管设在焦侧。
U型管系统能最大限度减少炭化室机侧的冒烟冒火现象,并能将导烟后残留的微量有害气体放散掉,非常安全可靠。
车体机侧的U型导烟管连通正装煤的第n孔炭化室和第n+2孔炭化室。
车体中部的U型导烟管,连通正装煤的第n孔炭化室和第n-1孔炭化室,启闭导烟孔盖装置位于车体机侧的U型导烟管和车体中部的U型导烟管的内上部,采用机械控制,实现导烟孔盖的自动启闭,操作过程中没有烟气外冒现象。
通过第n+2孔桥管处高压氨水喷射产生的抽吸力,正装煤的第n孔炭化室装煤产生的大量烟气首先通过布置在车体机侧的U型导烟管导到第n+2孔炭化室,进入集气管,吸力可调,避免炭化室机侧吸入大量空气,也避免炭化室机侧有大量烟气逸出。
随煤饼的装入,开启第n-1孔桥管处高压氨水,通过第n-1孔桥管处高压氨水喷射产生的抽吸力,第n孔炭化室内产生的大量烟气通过布置在车体中部的U型导烟管导入第n-1孔炭化室,进入集气管,随煤饼的继续装入,开启第n孔桥管处高压氨水,通过第n孔桥管处高压氨水喷射产生的抽吸力,直接导入集气管,全部操作均为程序控制。
导烟车的主要技术规格如下:
轨距7000mm
轨型50kg/m
走行驱动方式两台变频调速电机驱动
走行速度0~60m/min
吸尘口数量为2个
外形尺寸(长×宽×高)~14000×9600×8800mm
电源3Ph,380V,50Hz
供电方式滑触线导入
整车重量~60t
e)熄焦车(湿法熄焦固定底板式)
熄焦车为定点熄焦、底板固定,侧开车门,主要由转向架、车底板、车箱及开门机构组成。
熄焦车与电机车、拦焦机配合设计。
熄焦车的主要技术规格如下:
轨距2800mm,
轨型QU100
车箱有效容量33t(焦)
车箱有效长度8000mm
车箱底板固定,底板面与水平面夹角28°
车箱门打开最大宽度 650±20mm。
开门机构和制动装置为气动,工作压力600kPa,气源设在电机车上,由电机车司机操作,车门在关闭位置时能自锁。
熄焦车车箱内壁及底板均镶有耐热铸铁板,车门采用耐热合金铸钢,以适应骤冷骤热的工作环境。
熄焦车两端部设有缓冲器及车钩,并与电机车配合设计,使电机车可位于熄焦车的两端。
外型尺寸(长×宽×高)12250×6650×6450mm
整车重量~105t
开门机构:
开门气缸1个,为单向作用套筒式,由电机车司机操作。
车门的开闭动作由限位开关通过电气控制,保证其动作准确。
f)电机车(干湿两用)
电机车运行在焦炉焦侧的熄焦车轨道上,用于牵引和操纵焦罐车或湿熄焦车。
该电机车既能满足干法熄焦的作业要求,又能满足湿法熄焦的作业要求。
具有运行速度快,调速性能好,对位准确且行车安全的特性。
在电机车上可通过走台梯子直接登上焦炉焦侧炉台,司机室置于车体偏外侧,视线广阔,空压机采用螺杆式空压机,空压机电气柜置于机器室内,机器室封闭隔热,内设有冷气机,电控装置置于其内。
冷风机用压缩机置于司机室外,在靠炉侧设有风包及电源滑线支架,电机车两端设有缓冲器及牵引挂钩。
为检修方便,走行驱动装置采用外置式结构。
本电机车主要由车体、走行装置、制动系统、气路系统、牵引缓冲装置及电气系统组成。
电机车的主要技术规格如下:
数量2台(1开1备)
车体型式两层固定双轴台车式
轨距2800mm
轨型QU100
电源AC3P380V,50Hz
牵引重量240t(干熄满罐时)
电机车的操作周期≤9min
走行速度190~10m/min
走行调速方式变频调速(VVVF)
干熄站对位精度±100mm
制动方式能耗制动﹑盘式制动和运载车的气闸制动
走行电动机(2台)75kW
空压机(1台)22kW
司机室及电气室用空调装置各1台
机械连接方式板钩插销式
气路及电路连接快速接头
电机车自重约55t
电机车总功率(含圆形焦罐用电机)约200kW
g)液压交换机
液压交换机设有液压站、电控屏、操作台、行程指示装置。
液压站采用双泵、双阀系统,互为备用,配置2个油缸,具有自动、半自动、手动三种操作功能。
在煤气低压时,采用自动报警和切断煤气供应等安全措施,交换机的操作全部采用PC机控制,并设有氮气蓄能充压和直流蓄电池操作电磁阀的装置,以备停电时使用。
交换机的主要技术规格如下:
焦炉煤气系统油缸(针对1×55孔)
数量1个
额定拉力70kN
拉条行程420mm
设计行程460mm
直径Φ160mm
废气系统油缸(针对1×65孔)
数量1个
额定拉力90kN
拉条行程610mm
设计行程700mm
直径Φ200mm
交换周期20min
交换时间46sec
电源3Ph、380V、50Hz
1.7工艺装备
1.7.1集气系统
集气系统包括上升管、桥管及阀体、集气管、吸气弯管、高低压氨水喷洒装置、上升管水封盖和水封阀开闭装置、焦油盒和辅助水管、蒸汽管以及相应的操作台等。
①设计采用单集气管,双吸气管,有利于荒煤气的顺利导出,稳定集气管压力。
集气管设在焦侧,并采用高压氨水喷射,使上升管内形成负压,将装煤时的烟尘吸入集气管。
吸气弯管上设手动和自动调节翻板,调节集气管内煤气压力,使其保持规定的压力,不使炭化室出现负压操作现象。
②设计考虑适当加大炉顶空间和上升管直径,使煤气快速导入集气管内,减少装煤时炉门处的烟尘外逸。
③上升管内衬粘土砖和隔热材料,降低上升管外表面温度,改善炉顶操作条件。
下部用铸铁座与炉体连接,防止烧坏上升管下部结构。
④桥管顶部设有水封盖,防止荒煤气外逸,桥管与阀体的连接,采用水封承插结构,氨水可在内部形成水封,可避免荒煤气的泄露。
桥管上装有低压氨水喷洒装置用来冷却荒煤气。
使荒煤气温度于800℃左右冷至85℃左右。
⑤集气管内设高压氨水分段清扫装置,免去了人工清扫集气管的劳动。
1.7.2护炉铁件
护炉铁件包括炉柱、纵横拉条、弹簧、保护板、炉门及炉门框等。
①设计采用加大H型钢的炉柱,为了保证炉墙稳定性和强度,沿焦炉高向设置十二线小弹簧。
在纵横拉条的端部设有弹簧组,能均匀地对炉体施加一定保护压力,保证了焦炉整体结构的完整和严密。
②大保护板能有效地保护好炉头使之不受损坏。
③采用箱型断面的加厚炉门框,它与“L”形断面的炉门框相比,炉门框内外表面温差小。
所以箱形断面炉门框抵抗机械应力和热应力性能好,不易断裂。
④炉门采用弹性刀边,弹簧门栓、悬挂式空冷炉门,炉门对位时,位置的重复性好,弹性刀边能使终保持一定压力,防止炉门冒烟冒火。
⑤炉门、炉框、保护板主要材质选用蠕墨铸铁(RuT340),它具有耐急冷急热性能好,抗拉、抗弯强度高,铸件寿命长的优点。
1.7.3加热交换系统
焦炉采用焦炉煤气加热的单热系统。
主管由外部管道架空引进到焦炉地下室,煤气主管道上设有温度、压力和流量的测量和调节装置。
各项参数的测量、显示、记录、调节和低压报警都由自动控制仪表来完成。
在焦炉煤气主管道上设有煤气预热器,以保证入炉煤气温度的稳定。
在废气系统中,焦炉的分烟道设自动调节翻板,总烟道设手动调节翻板,使加热系统的吸力得到适当调节和稳定,保证焦炉在正确的温度压力下工作。
焦炉加热系统采用自动加热控制。
焦炉加热用的煤气、空气和燃烧后的废气在加热系统内的流向由液压交换机驱动交换传动装置来控制,每隔20~30分钟换向一次。
1.7.4湿熄焦系统
设计采用新型降污快速湿法熄焦技术,其优点在于⑴熄焦时间短,熄焦时间可控制在70-80s;⑵熄焦后的焦炭水分可控制在2-4%而且水分稳定;⑶熄焦塔上设有水雾捕集装置并设双层折流式木结构的捕集装置,除尘效果好,每吨焦散发的焦粉量可控制在50g以下。
湿法熄焦系统包括熄焦泵房、熄焦塔、熄焦喷洒管、水雾捕集装置、二层折流板式除尘装置、粉焦沉淀池、清水池、粉焦脱水台和双梁抓斗起重机、一点定位熄焦车、高位槽及自动控制系统等。
湿法熄焦工艺,在整个熄焦过程中下水量是分段进行的。
熄焦过程初期,先用小水量熄灭熄焦车厢顶层红焦及稳定了焦炭表面,持续一段时间后,再喷射大水量,水与炽热焦炭接触后产生的蒸气“由下至上”地熄灭熄焦车内底部、中部及中上部的焦炭。
这种熄焦方式用大水流喷射代替了喷洒,改善了熄焦车厢内沿焦炭深度方向上的水份分布,达到了缩短熄焦时间、降低焦炭水份的目的。
1)工艺管道及设备
a)熄焦水泵:
设置三台熄焦水泵(2开1备),每台都可向高位槽供水,其能力可以满足熄焦操作要求。
b)高位槽:
使用高位槽可在每次熄焦操作中以恒定压力提供可靠的供水。
c)工艺管道:
管道设计可满足在熄焦开始时迅速供水。
2)一点定位熄焦车
一点定位熄焦车可在不移车的情况下接受从炭化室推出的焦炭,使焦炭表面的轮廓及其在熄焦车厢内的分布对每炉焦炭均一样,这样就可以允许熄焦塔内水流可以调节,以提供合适的熄焦水量,可获得含水量更低的焦炭。
3)控制系统
熄焦系统的控制方式为自动调节阀(可调)开度控制,其控制过程通过PLC程序控制完成。
4)水雾捕集水泵与高位槽的快速开闭阀同开同关。
5)熄焦塔高68米,熄焦塔的下部设有熄焦水喷洒管、中部设有水雾捕集装置、顶部设有二层折流式木结构的捕集装置,可捕集熄焦时产生的大量焦粉和水滴,其除尘效率可达约85%以上,其除尘效果达到每吨焦散发的焦粉量在50g以下。
6)粉焦沉淀池的长度、宽度和深度使含焦粉的循环水有充分的沉淀时间和沉淀速度,可保证熄焦水循环使用。
7)为了定时清理粉焦沉淀池内粉焦,设计选用了容积1.5m3的电动葫芦双梁抓斗起重机,定时将沉淀池底的粉焦抓到粉焦脱水台上,经脱水后外运。
1.7.5焦炉除尘设施
本工程对焦炉生产过程中阵发性排放烟尘和连续性排放烟尘治理采取以下措施:
考虑捣固焦炉装煤除尘的特殊性,将5.5米捣固焦炉的煤顶上的空间通道高度增加到250mm,使荒煤气的逸出压力减小,以达到减少荒煤气外冒的目的。
1.7.5.1阵发性排放烟尘治理
a)装煤除尘:
在装煤推焦机上安装有活动的炉门密封框,在装煤过程中,依靠这些可变形的密封设备,保证将煤饼和炉门框之间充分密封。
炭化室产生的荒煤气及烟尘通过双U形导烟管式导烟车,配合高压氨水喷射产生的负压,将装煤烟尘导到n+2和n-1炭化室,减少装煤时荒煤气和烟尘的外逸。
b)熄焦除尘:
在熄焦塔中部设有水雾捕集装置和二层折流式木结构的捕集装置,捕集熄焦时产生的大量焦粉和水滴。
c)推焦除尘:
在拦焦机上带有大型集尘罩,该集尘罩与地面站除尘设备之间用一条固定于焦侧的水平干管连接,通过干管将抽吸的烟气送到除尘设备处理净化后排放。
并在推焦机、拦焦机上分别设有机、焦侧炉头挡烟装置,更有利于出焦时的烟尘治理。
d)集气管放散点火装置:
在集气管上设自动放散装置,点火方式采用常明火,可将集气管放散的荒煤气焚烧掉。
1.7.5.2连续性排放烟尘治理
a)炉顶用于导烟的吸尘孔盖采用水封结构,另一个采用球状结构。
b)炉门采用弹性刀边,炉门刀边密封靠弹簧顶压,使刀边受力均匀,密封效果好。
c)炉顶上升管盖及桥管与阀体承插均采用水封结构,可以杜绝上升管盖和桥管承插处的冒烟现象。
d)上升管根部采用铸铁座,杜绝了上升管根部的冒烟冒火现象。
1.7.6辅助设施
在炉端台的中层设有炉门修理站,推焦杆和托煤板更换站,在炉端台外侧设有5t旋转起重机,在焦炉两端台设拦焦车导焦栅检修装置,这些设施既方便了生产操作,又减轻了工人的劳动强度。
在煤塔端部设有捣固机检修站。
1.7.7焦炉主要生产操作指标
焦炉周转时间为25.5小时,焦炉正常操作的主要生产指标如下:
序号
项目
单位
指标
用焦炉煤气加热时
1