基于Proe的平面分流组合模有限元分析.docx
《基于Proe的平面分流组合模有限元分析.docx》由会员分享,可在线阅读,更多相关《基于Proe的平面分流组合模有限元分析.docx(24页珍藏版)》请在冰豆网上搜索。
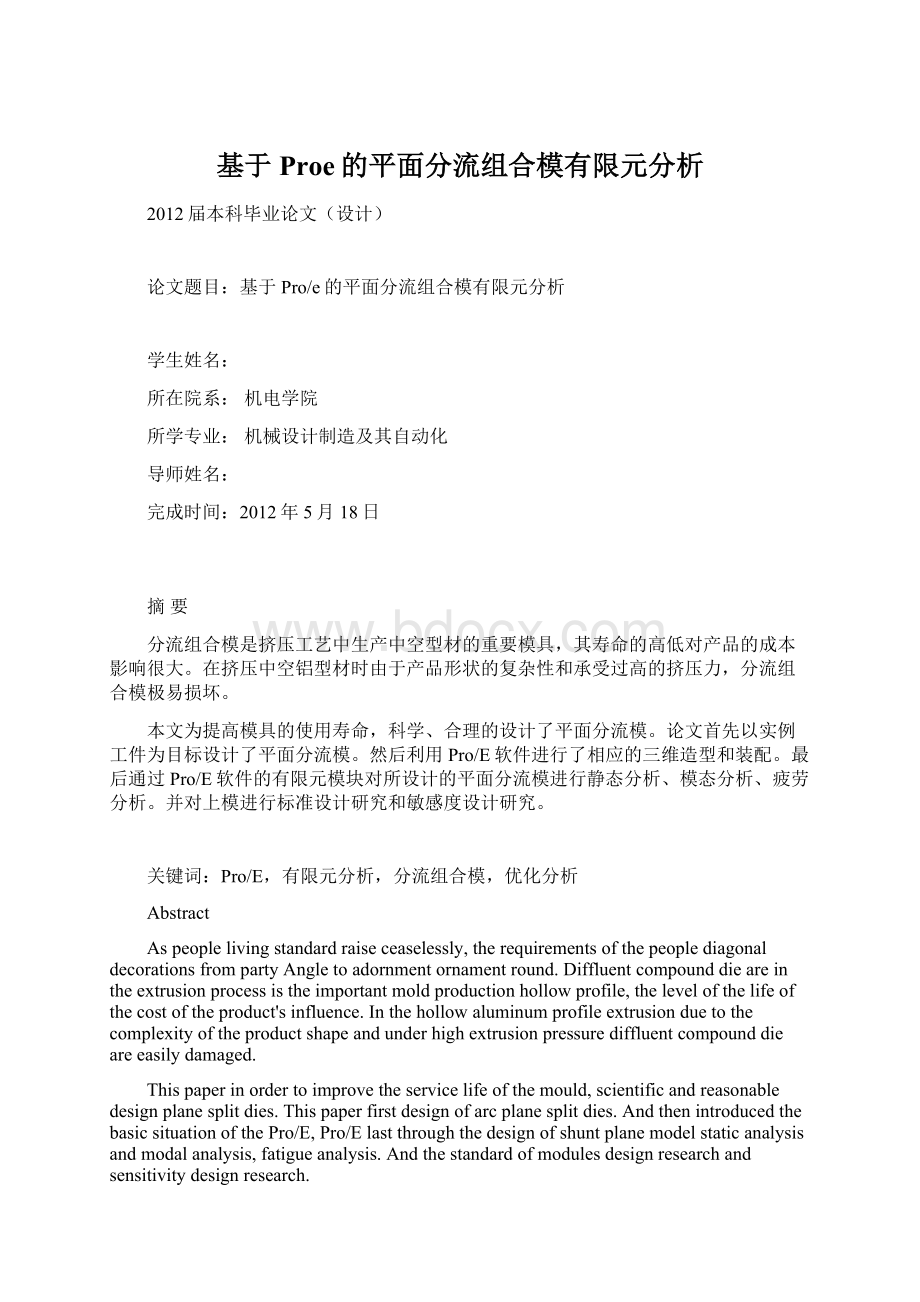
基于Proe的平面分流组合模有限元分析
2012届本科毕业论文(设计)
论文题目:
基于Pro/e的平面分流组合模有限元分析
学生姓名:
所在院系:
机电学院
所学专业:
机械设计制造及其自动化
导师姓名:
完成时间:
2012年5月18日
摘要
分流组合模是挤压工艺中生产中空型材的重要模具,其寿命的高低对产品的成本影响很大。
在挤压中空铝型材时由于产品形状的复杂性和承受过高的挤压力,分流组合模极易损坏。
本文为提高模具的使用寿命,科学、合理的设计了平面分流模。
论文首先以实例工件为目标设计了平面分流模。
然后利用Pro/E软件进行了相应的三维造型和装配。
最后通过Pro/E软件的有限元模块对所设计的平面分流模进行静态分析、模态分析、疲劳分析。
并对上模进行标准设计研究和敏感度设计研究。
关键词:
Pro/E,有限元分析,分流组合模,优化分析
Abstract
Aspeoplelivingstandardraiseceaselessly,therequirementsofthepeoplediagonaldecorationsfrompartyAngletoadornmentornamentround.Diffluentcompounddieareintheextrusionprocessistheimportantmoldproductionhollowprofile,thelevelofthelifeofthecostoftheproduct'sinfluence.Inthehollowaluminumprofileextrusionduetothecomplexityoftheproductshapeandunderhighextrusionpressurediffluentcompounddieareeasilydamaged.
Thispaperinordertoimprovetheservicelifeofthemould,scientificandreasonabledesignplanesplitdies.Thispaperfirstdesignofarcplanesplitdies.AndthenintroducedthebasicsituationofthePro/E,Pro/Elastthroughthedesignofshuntplanemodelstaticanalysisandmodalanalysis,fatigueanalysis.Andthestandardofmodulesdesignresearchandsensitivitydesignresearch.
Keywords:
Pro/E,Analysis,Diffluentcompounddieare
目录
1绪论3
2平面分流组合模的设计3
2.1挤压机、模具材料的选择3
2.2挤压比的计算3
2.3分流比的选择3
2.4分流孔的形状、断面尺寸、数目及分布3
2.5分流桥的设计3
2.6模芯(或舌头)的设计3
2.7焊合室设计3
2.8模孔尺寸的设计3
2.9模孔工作带长度的确定3
2.10模孔空刀结构设计3
2.11设计立体图。
3
3Pro/E软件简介3
3.1Pro/E简介3
3.2Pro/E的工作模式与模块:
3
4关于模具的分析与优化3
4.1上模的模型分析3
4.1.1分配材料3
4.1.2定义约束3
4.1.3创建载荷3
4.1.4上模的分析/研究3
4.2下模的模型分析3
4.2.1分配材料3
4.2.2定义约束3
4.2.3创建载荷3
4.2.4下模的分析/研究3
4.3优化分析3
4.3.1对上模的标准设计研究3
4.3.2敏感度设计研究3
5结束语3
致谢3
参考文献3
1绪论
现如今,铝合金型材广泛用于日常生活、建筑、航空、汽车街等领域。
铝型材也越来越复杂,种类也越来越多,对模具的设计也提也了更高的要求,日益激烈的市场竞争已使模具产品的设计与生产厂家越来越清楚地意识到:
能比别人更快地推出优秀的新产品,就能占领更多的市场。
用挤压的方法生产铝型材,既节约金属又具有很高的生产效率。
因此该方法在生产和研究领域都日益受到重视,众多的科研工作者为挤压工艺的改进和模具的优化做了大量的研究工作。
在铝型材挤压工艺生产中,经常凭借经验和反复试模来进行模具设计,这样就会造成人力与物力的耗费问题;再者,铝型材挤压时,由于挤压模具内部是封闭的型腔,因此材料的流动、应力与应变场的分布以及模具载荷情况都很难监测与掌握到。
现如今,人们的生活水平不断提高,人们对生活水平提出了更高的要求。
对于角边的装饰不再用以前那种方角装饰,改用圆角装饰,这样不仅美观,而且密封性好。
分流组合模是挤压工艺中生产中空型材的重要模具,其寿命的高低对产品的成本影响很大。
在挤压中空铝型材时由于产品形状的复杂性和承受过高的挤压力,分流组合模极易损坏。
为提高模具的使用寿命,必须合理、科学地设计模具。
当今有限元分析软件的一个发展趋势是与通用CAD软件的集成使用,即在用CAD软件完成部件和零件的造型设计后,能直接将模型传送到CAE软件中进行有限元网格划分并进行分析计算,如果分析的结果不满足设计要求则重新进行设计和分析,直到满意为止,从而极大地提高了设计水平和效率。
为了满足工程师快捷地解决复杂工程问题的要求,许多商业化有限元分析软件都开发了和著名的CAD软件(例如Pro/E、Unigraphics、SolidEdge、SolidWorks、IDEAS、Bentley和AutoCAD等)的接口。
有些CAE软件为了实现和CAD软件的无缝集成而采用了CAD的建模技术,如ADINA软件由于采用了基于Parasolid内核的实体建模技术,能和以Parasolid为核心的CAD软件(如Unigraphics、SolidEdge、SolidWorks)实现真正无缝的双向数据交换
Pro/E软件具有强大的建模能力,虽然其分析能力不如一些专业的有限元分析软件如ANSYS等,但对于一些简单的模型分析和设计研究完全可以胜任。
本文列出了应用PROE进行简单模型有限元分析的一般流程,问题和解决方案对实际工程也有参考意义。
如果对于更为复杂的模型分析,本人设想可以采用多种软件综合分析,如用PROE建立模型和预处理,通过ANSYS进行求解,发挥各自的优势,更有效率更加准确的得出结果。
2平面分流组合模的设计
现如今,人们的生活水平不断提高,人们对生活水平提出了更高的要求。
对于角边的装饰不再用以前那种方角装饰,改用圆角装饰,这样不仅美观,而且具有良好的密封性能。
圆角型材如图1所示:
图1铝行材断面图
2.1挤压机、模具材料的选择
由于该图形的外接圆直径为76mm,所以选择吨位为580美吨(1美吨=0.907185吨),挤压筒直径为90mm的挤压机。
由于模具的工作于高温、高冲击、高摩擦高压的环境中,所以选择模具材料为3Cr2W8V。
2.2挤压比的计算
为使挤压型材具有一定的变形量,同时又不致于难挤压,选择合理的挤压比是很重要的,现所采用的挤压机的挤压筒直径为Φ90mm,根据挤压比计算公式:
(1)
计算结果在允许范围之内,所以满足要求。
将挤压比调整为60。
2.3分流比的选择
分流比的大小直接影响到挤压阻力的大小、制品的成形和焊合质量,其值愈小时则挤压时变形阻力愈大,对模具的使用和挤压生产是不利的,在保证模强度的前提下,选择大的分流比是有利的,一般情况下,在生产空心型材时,取分流比K为10~30;再加上,分流比越大,越有利于金属流动与焊合,减少挤压力,所以在设计该模具时选K=20。
2.4分流孔的形状、断面尺寸、数目及分布
分流孔的数目根据空心型材的断面形状状、复杂程度和模孔排列位置具体确定,对于外形尺寸小、断面形状较对称的型材,可采用两孔或三孔。
对外型较大、断面复杂的型材,取四孔或多孔。
一般情况下,分流孔数目应尽量少,以减少模桥造成的焊缝。
少取分流孔可增大分流孔的面积,从而降低了挤压力为了保证金属的合理流动及模具寿命,分流也不宜过于靠近模子中心。
由于挤压筒的直径为
90mm,所以选择分流孔数为3个,分布于R40mm的圆上。
如图2所示:
图2模具分流孔布局图图3分流孔布局三维图
2.5分流桥的设计
分流桥结构直接影响挤压力大小、金属流动快慢、焊合质量和模具强度。
从加大分流比,降低挤压力来考虑,分流桥宽度B可选择小些;但从改善金属流动均匀性和模具强度来考虑,模孔最好受到分流桥的遮敝,因而B选择得大一点较合适。
分流桥的高度H直接影响挤压力的大小和模具强度。
一般在保证模具强度的前提下,桥越矮越好,这样可以降低挤压力。
为了改善金属的流动与焊合,而且便于模具加工,选择水滴形分流桥。
桥底圆角选用R5mm,分流桥的高度选为50mm。
如图4所示:
图4分流桥断面图图5分流桥三位图
2.6模芯(或舌头)的设计
在模芯宽度b<10mm时,多采用锥式。
这种结构形式的模芯强度和刚度都较高,但不易加工;模芯宽度在10mm
这种结构的强度和刚度较锥式的稍低,但加工容易些;当模芯b>20mm时,多采用凸台式,虽然这种结构的模芯强度和刚度不及前两种,但加工容易,同时也便于修模。
为了增加模芯刚度,在保证有充足金属流入模孔的前提下,模芯应尽量做得短一点,这样,在挤压时模芯很少失去稳定性而发生偏壁。
但模芯又不能做得太短,因为太短会影响焊合质量,而且容易产生流速不均,使正对分流孔的部分流速加快。
一般模芯要伸出下模工作带3~5mm。
由于该模芯宽度为25mm,所以采用凸台式模芯,且伸出工作带3mm。
2.7焊合室设计
当分流孔形状、数目、大小及分布状态确定之后,焊合室断面形状和大小也基本上确定了。
在分流模的设计时,主要考虑三个参数,模子的入口角、槽底圆角和焊合室的高度。
模子的入口角是模子工作端面与定径带形成的端面角。
它可防止低塑性合金在挤压时产生表面裂纹和减少金属在流入定径带时的非接触变形,同时也减少在高温下挤压时模子棱角的压塌变形。
但是,圆角增大了接触摩擦面积,可能引起挤压力增高。
一般取15°左右。
槽底圆角值的选取主要考虑能否在焊合室边缘与模孔平面之间的接合处产生死区。
挤压铝及其合金时,在平面分流组合模的入口处做成r=0.5~5mm的圆角。
焊合室高度h太高会影响模芯的稳定性,易出现型材壁厚不均,而且挤压力也大;高度太矮时,由于压力不足,会使焊合质量不佳。
焊合室高度在很大程度上取决于挤压筒的直径。
该模具的焊合室位于下模上,为了提高焊缝质量,焊合室的深度选为15mm;为了避免出现死区现现象,采用蝶形焊合室,并在焊合室的入口处做成15°的圆角,槽底圆角选用R5。
如图6所示:
图6模具焊合室结构图图7模具焊合室锥角图
2.8模孔尺寸的设计
设计模孔的基本原则是:
在保证挤压制品在冷却状态下不超出图纸规定的制品公差的条件下,尽量延长模具的使用寿命。
影响制品尺寸的因素很多,如温度,模具材料,被挤压金属材料,制品形状和尺寸,拉伸矫直量以及模具变形情况等,在确定模模孔尺寸时,一般应根据具体情况着重考虑其中的一个或几个影响因素。
在模孔设计时,主要考虑制品冷却后的收缩量和拉矫后的缩减量。
制品外形的模孔尺寸A可由式
确定。
如图8所示;制品壁厚尺寸可由式
确定。
即
为1+0.1=1.1mm。
图8模具出口尺寸图
2.9模孔工作带长度的确定
定径带长度h过短,制品尺寸难于稳定,易产生波纹、椭圆、压痕、压伤等现象,同时,模子易磨损,会大大降低模具的使用寿命;h定过长,会增大与金属的摩擦,增加挤压力,易粘结金属,使制品表面出现划伤、毛刺、麻面、搓衣板型波浪等缺陷。
对于空部位的工作带来说为制品壁厚的2倍,即为2mm。
但为了确保型材的尺寸和形状,将其调整为3mm;与空心部位相邻的实心部位为(3~4)t。
选为3mm。
2.10模孔空刀结构设计
模子出口直径d出过小,则易划伤制品表面,甚至会引起堵模。
但d出过大,会大大削弱定径带的强度,引起定径带过早地变形、压蹋,明显地降低模具的使用寿命。
因此,在一般情况下,出口带尺寸应比定径带尺寸大3~6mm,对于薄壁管或变外径管材的模子,其值可适当增大。
为了增大模子的强度和延长模具的使用寿命,出口带可做成喇叭锥。
出口喇叭锥角(从挤压型材离开定径带开始)可取1.5°~10°(此值受锥刀角度的限制)。
特别是对于壁厚小于2mm而外形十分复杂的型材模子,为了保证模具的强度,必须做成喇叭出口。
有时为了便于加工,也可设计成阶梯形的多级喇叭锥。
为了增大定径带的抗剪强度,定径带与出口带之间可以20°~45°的斜面或以圆角半径为1.5~3.0mm的圆弧连接。
由于图纸要求型材的厚度为1mm,所以模孔空刀结构选择图1图所示的结构,定径带与出口处采用R3的圆弧过渡,如图9所示。
图9凹模断面图
2.11设计立体图。
图10上模立体图图11下模立体图
图12装配立体图
3Pro/E软件简介
3.1Pro/E简介
Pro/E是美国PTC开发的有限元软件。
该软件可以实现和Pro/E的完全无缝集成。
绝大部分有限元分析软件的几何建模功能比较弱,这些有限元软件通常通过IGES格式或者STEP格式进行数据交换,而这样做最大的弊端在于容易造成数据的丢失,因此常常需要花费大量的时间与精力进行几何模型的修补工作。
使用Pro/E恰好可以克服这一点,该软件可以直接利用Pro/E的几何模型进行有限元分析。
P-method能够比较精确地拟合几何形状,能够消除表面上的微小凹面。
这种单元的应力变形方程为多项式方程,最高阶次能够达到九阶。
这意味着这种单元可以非常精确地拟合大应力梯度。
Pro/E中四面体单元的计算结果比其他传统有限元程序中四面体的计算结果要好得多。
首先单元以较低的阶次进行初步计算,然后在应力梯度比较大的地方和计算精度要求比较高的地方自动地提高单元应力方程的阶次,从而保证计算的精确度和效率。
3.2Pro/E的工作模式与模块:
Pro/E工作模式:
(1)FEM模式:
FEM模式没有求解器,只能完成对模型的网格划分、边界约束、载荷、理性化等前处理工作、然后借助第三方软件完成计算分析。
(2)集成模式:
用户可以在Pro/E中建立几何模型,然后进入Pro/E模块中,定义载荷及边界条件,进行分析研究。
应用较多的还是集成模式。
Pro/E的三个模块:
(1)Pro/ESTRUCTURE:
结构分析软件包,可以进行零件模型和装配模型的结构分析和优化分析。
具有的分析类型有:
静态分析、模态分析、屈曲分析、接触分析、预紧分析及振动分析等。
(2)Pro/ETHERMAL:
温度分析模块,可以进行零件和装配模型的稳态和瞬态温度分析,也可以根据温度问题进行灵敏度分析和优化设计。
(3)Pro/EMOTIQN:
运动分析软件包,进行机构分析和机构运动优化设计,可以进行三维静态分析、运动学分析、动力学分析、逆向动力学分析及干涉检验分析。
4关于模具的分析与优化
4.1上模的模型分析
4.1.1分配材料
打开shangmo.prt文件,选中“steel.mtl”材料选项,使其高亮显示,选择菜单栏中的【编辑】¦【属性】命令,系统弹出“材料定义”对话框,如图13所示。
选择【失效准则】下拉表框中的“最大剪切应力”选项,【疲劳】下拉表框中的“统一材料法则”选项,【材料类型】下拉列表框中的“低合金钢”选项,【表面光洁度】下拉列表框中的“精加工”选项,在【失效强度衰减因子】文本框中输入2,在【抗张屈服应力】文本框中输入100,在【抗张极限强度】文本框中输入1000。
图13分流模材料设置图
4.1.2定义约束
(1)单击“E对象”工具栏上的【位移约束】工具按钮,系统弹出“约束”对话框,如图14所示。
(2)单击【参照】列表框中的空白,在3D模型中选择左侧面,如图15所示。
模型的六个自由度全部固定,单击【确定】按钮完成这一侧面的约束创建,用同样方法固定另一侧面的自由度。
完成约束创建。
图14位移约束选择图
图15上模位移约束图
4.1.3创建载荷
(1)单击“E对象”工具栏上的【压力载荷】工具按钮,系统弹出“压力载荷”对话框,如图16所示。
图16载荷设置图
(2)在3D模型中选择处得一个曲面,在【压力】选项组中【Vaule】文本框中输入30000,单位为MPa。
(3)利用一种方法创建与该曲面相对的另一侧面的压力载荷。
(4)利用上述方法为下模曲面创建压力载荷,值为30000。
如图17所示。
图17上模受力图
4.1.4上模的分析/研究
(1)对上模静态分析如图18。
图18上模静态分析图
局部视图如图19。
图19静态分析局部图
图中红色和黄色区域受力较大,容易变形需要改进。
(2)对上模模态分析如图20。
图20上模的模态分析
由于红色区域的尺寸变化较大,在下模突出部位两侧容易产生应力集中。
易发生疲劳破坏,其他部分的应力分布较为均匀。
(3)对上模的疲劳分析有以下内容:
疲劳寿命:
发生在疲劳破坏时的应力循环次数,或者从开始受重复载荷作用到断裂所经历的时间,成为疲劳寿命。
疲劳破坏:
就是在交变载荷作用下引起的零件失效或破坏。
疲劳破坏不是在一次大载荷作用下的破坏,而是反复载荷作用下产生的破坏,疲劳破坏通常没有明显的塑性变形迹象。
安全系数:
就是输入载荷的许用安全系数。
当计算处得疲劳寿命比设计寿命长时,疲劳分析能够反过来计算输入载荷的许用安全系数。
疲劳寿命可信度:
就是计算出的疲劳和设计寿命的比值。
由于疲劳具有统计特征,因此,疲劳寿命可信度越大越好。
图21疲劳寿命可信度条纹图
红色区域表示模具的寿命较长,绿色和黄色区域表示模具寿命较短。
在加工过程中受力较大。
图22下模的安全系数条纹图
红色区域为安全区,蓝色区域加工时应注意。
4.2下模的模型分析
4.2.1分配材料
打开shangmo.prt文件,选中“steel.mtl”材料选项,使其高亮显示,选择菜单栏中的【编辑】¦【属性】命令,系统弹出“材料定义”对话框,如图10所示。
选择【失效准则】下拉表框中的“最大剪切应力”选项,【疲劳】下拉表框中的“统一材料法则”选项,【材料类型】下拉列表框中的“低合金钢”选项,【表面光洁度】下拉列表框中的“精加工”选项,在【失效强度衰减因子】文本框中输入2,在【抗张屈服应力】文本框中输入100,在【抗张极限强度】文本框中输入1000。
4.2.2定义约束
(1)单击“E对象”工具栏上的【位移约束】工具按钮,系统弹出“约束”对话框,如图11所示。
(2)单击【参照】列表框中的空白,在3D模型中选择左侧面,如图23所示。
模型的六个自由度全部固定,单击【确定】按钮完成这一侧面的约束创建,用同样方法固定另一侧面的自由度。
完成约束创建。
图23下模位移约束图
4.2.3创建载荷
(1)单击“E对象”工具栏上的【压力载荷】工具按钮,系统弹出“压力载荷”对话框,如图13所示。
(2)在3D模型中选择处得一个曲面,在【压力】选项组中【Vaule】文本框中输入30000,单位为MPa。
(3)利用一种方法创建与该曲面相对的另一侧面的压力载荷。
(4)利用上述方法为下模曲面创建压力载荷,值为30000。
如图24。
图24下模受力图
4.2.4下模的分析/研究
(1)下模的静态分析如图25。
图25下模静态分析图
有图可知受力基本均匀。
(2)下模模态分析如图26。
图26下模模态分析图
由于红色区域的尺寸变化较大,在下模突出部位两侧容易产生应力集中。
易发生疲劳破坏,其他部分的应力分布较为均匀。
(4)下模的疲劳分析。
图27疲劳寿命可信度条纹图
红色区域表示模具的寿命较长,可以看出下模的设计很合理。
4.3优化分析
4.3.1对上模的标准设计研究
(1)在“分析和设计研究”对话框中,选择菜单栏中的【文件】¦【新建标准设计研究】命令,系统弹出“标准研究定义”对话框。
(2)选中【分析】列表框中的所有分析,单击【变量】列表框右侧的【从模型中选取参数】按钮,返回“标准研究定义”对话框。
(3)在工作区中选中3D模型,然后选中分流桥倒角5,单击“选取”对话框中的【确定】按钮,返回“标准研究定义”对话框。
(4)在【变量】列表框中设置文本框中输入6,单击【确定】按钮,系统返回“分析和设计研究”对话框,完成标准设计研究的建立。
(5)选中列表框中刚才创建的标准设计研究,选择菜单栏中的【运行】¦【开始】命令,单击【是】按钮,系统就开始计算,大约几分钟后,系统就弹出“诊断”对话框,对话框中显示标准设计研究分析过程以及分析出现的问题。
(6)关闭“诊断”对话框,系统返回“分析和设计研究”对话框,选中列表框中刚才创建的标准设计研究,单击工具栏上的【查看设计研究或有限元分析结果】工具,系统弹出“结果窗口定义”对话框。
(7)选择【显示类型】下拉列表框中的“Fringe”选项。
(8)其他选择为系统默认值,单击【确定并显示】按钮,结果窗口中显示倒角变化后的应力条纹图,如图28所示。
图28倒角变化后的应力条纹图
4.3.2敏感度设计研究
(1)选择菜单栏中的【文件】¦【新建敏感度设计研究】命令,系统弹出“敏感度研究定义”对话框。
(2)选中【分析】列表框中的静态分析、模态分析、疲劳分析,使其高亮显示。
(3)单击【变量】右侧的【从模型中选取尺寸】按钮,系统弹出“选取”对话框,在3D模型中选中上模,使其尺寸全部显示,双击倒角尺寸5,系统自动返回。
(4)单击右下角的【选项】按钮,系统弹出“设计研究选项”对话框,选取【重复P还收敛】和【每次形状更新后进行网格重画】复选框,单击【关闭】按钮,返回“敏感度设计研究定义”对话框。
(5)单击【确定】按钮,系统返回“分析和设计研究”对话框,完成敏感度研究的创建。
(6)选中列表框中刚才创建的敏感度设计研究,选择菜单栏中的【运行】¦【开始】命令,系统弹出提示询问对话框,单击【是】按钮,系统就开始计算,几十分钟之后,系统弹出“诊断”对话框,对话框中显示敏感度设计研究分析过程以及分析出现的问题。
(7)关闭“诊断”对话框,系统返回“分析和设计研究”对话框,选中列表框中刚才创建的敏感度设计研究,单击工具栏上的【查看设计研究或有限元分析结果】工具,系统弹出“结果窗口定义”对话框。
(8)选中【显示类型】下拉列表框中的“Graph”选项。
(9)单击【量】选项卡,选中下拉表框中的“Measure”选项,单击【测量】按钮,系统弹出测量对话框,选中【预定义】列表框中的“max_stress_vm”选项,单击【确定】按钮,返回“结果窗口定义”对话框。
(10)其他选项为系统默认值,单击【确定并显示】按钮,结果窗口中显示最大应力随下模突出倒角变化曲线,如图26所示。
(