典型套筒类零件加工工艺分析2.docx
《典型套筒类零件加工工艺分析2.docx》由会员分享,可在线阅读,更多相关《典型套筒类零件加工工艺分析2.docx(10页珍藏版)》请在冰豆网上搜索。
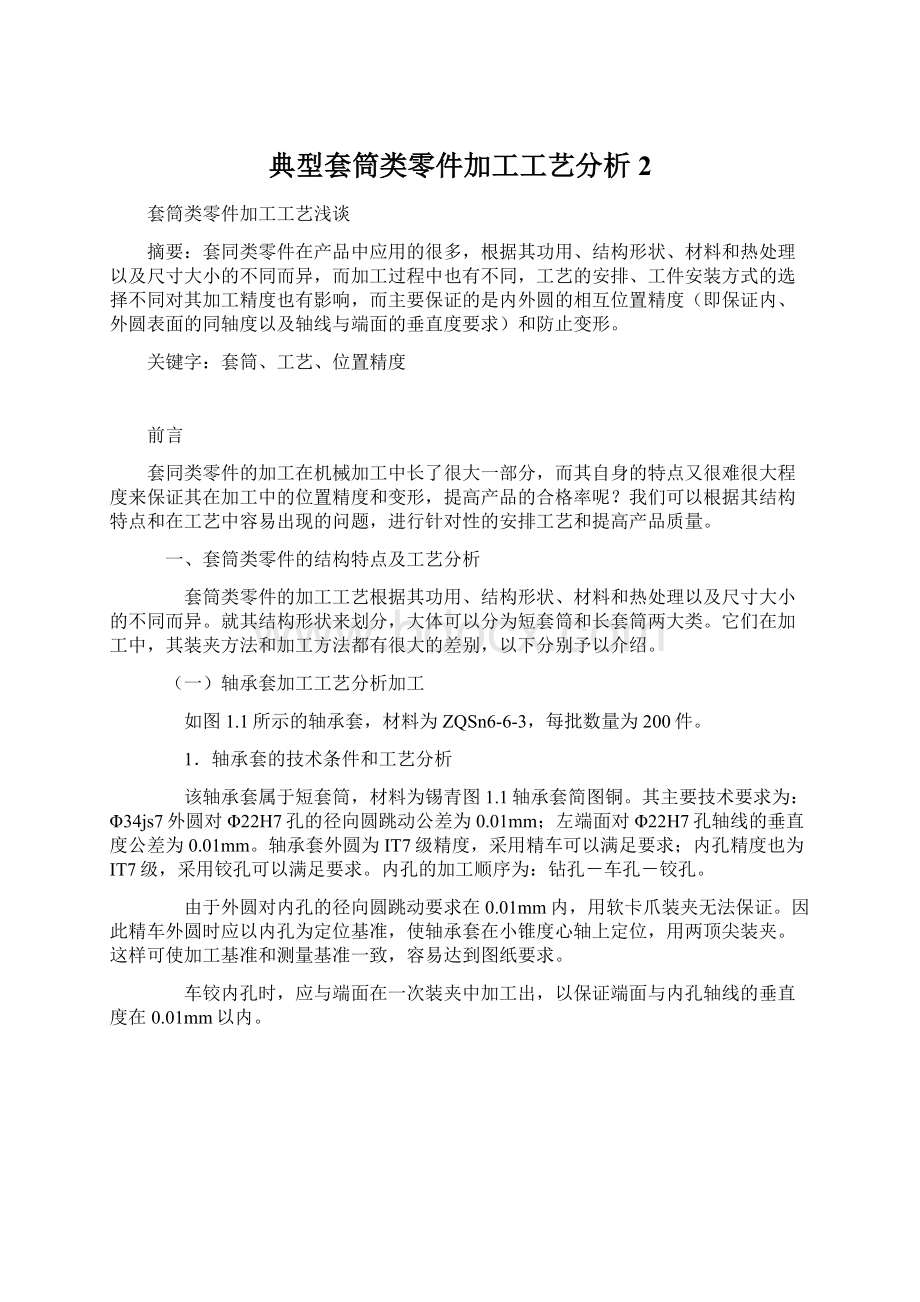
典型套筒类零件加工工艺分析2
套筒类零件加工工艺浅谈
摘要:
套同类零件在产品中应用的很多,根据其功用、结构形状、材料和热处理以及尺寸大小的不同而异,而加工过程中也有不同,工艺的安排、工件安装方式的选择不同对其加工精度也有影响,而主要保证的是内外圆的相互位置精度(即保证内、外圆表面的同轴度以及轴线与端面的垂直度要求)和防止变形。
关键字:
套筒、工艺、位置精度
前言
套同类零件的加工在机械加工中长了很大一部分,而其自身的特点又很难很大程度来保证其在加工中的位置精度和变形,提高产品的合格率呢?
我们可以根据其结构特点和在工艺中容易出现的问题,进行针对性的安排工艺和提高产品质量。
一、套筒类零件的结构特点及工艺分析
套筒类零件的加工工艺根据其功用、结构形状、材料和热处理以及尺寸大小的不同而异。
就其结构形状来划分,大体可以分为短套筒和长套筒两大类。
它们在加工中,其装夹方法和加工方法都有很大的差别,以下分别予以介绍。
(一)轴承套加工工艺分析加工
如图1.1所示的轴承套,材料为ZQSn6-6-3,每批数量为200件。
1.轴承套的技术条件和工艺分析
该轴承套属于短套筒,材料为锡青图1.1轴承套简图铜。
其主要技术要求为:
Φ34js7外圆对Φ22H7孔的径向圆跳动公差为0.01mm;左端面对Φ22H7孔轴线的垂直度公差为0.01mm。
轴承套外圆为IT7级精度,采用精车可以满足要求;内孔精度也为IT7级,采用铰孔可以满足要求。
内孔的加工顺序为:
钻孔-车孔-铰孔。
由于外圆对内孔的径向圆跳动要求在0.01mm内,用软卡爪装夹无法保证。
因此精车外圆时应以内孔为定位基准,使轴承套在小锥度心轴上定位,用两顶尖装夹。
这样可使加工基准和测量基准一致,容易达到图纸要求。
车铰内孔时,应与端面在一次装夹中加工出,以保证端面与内孔轴线的垂直度在0.01mm以内。
图1.1
2.轴承套的加工工艺
下面为轴承套的加工工艺过程。
粗车外圆时,可采取同时加工五件的方法来提高生产率。
轴承套加工工艺过程如下:
序号
工序名称
工序内容
定位与夹紧
(1)备料棒料,按5件合一加工下料
(2)钻中心孔
车端面,钻中心孔
调头车另一端面,钻中心孔
三爪夹外圆
(3)粗车
车外圆Ф42长度为6.5mm,车外圆Ф34Js7为Ф35mm,车空刀槽2×0.5mm,取总长40.5mm,车分割槽Ф20×3mm,两端倒角1.5×45°,5件同加工,尺寸均相同
中心孔
(4)钻
钻孔Ф22H7至Ф22mm成单件
软爪夹Ф42mm外圆
(5)车、铰
车端面,取总长40mm至尺寸
车内孔Ф22H7为Ф22
mm
车内槽Ф24×16mm至尺寸
铰孔Ф22H7至尺寸
孔两端倒角
软爪夹Ф42mm外圆
(6)精车
车Ф34Js7(±0.012)mm至尺寸
Ф22H7孔心轴
(7)钻
钻径向油孔Ф4mm
Ф34mm外圆及端面
(8)检查
(二)液压缸加工工艺分析
液压缸为典型的长套筒零件,与短套筒零件的加工方法和工件安装方式都有较大的差别。
1.液压缸的技术条件和工艺分析
液压缸的材料一般有铸铁和无缝钢管两种。
图1.2所示为用无缝钢管材料的液压缸。
为保证活塞在液压缸内移动顺利,对该液压缸内孔有圆柱度要求,对内孔轴线有直线度要求,内孔轴线与两端面间有垂直度要求,内孔轴线对两端支承外圆(Φ82h6)的轴线有同轴度要求。
除此之外还特别要求:
内孔必须光洁无纵向刻痕;若为铸铁材料时,则要求其组织紧密,不得有砂眼、针孔及疏松。
图1.2
2.液压缸的加工工艺
液压缸加工工艺过程如下:
序号
工序名称
工序内容
定位与夹紧
(1)配料
无缝钢管切断
(2)车
1.车Ф82mm外圆到Ф88mm及M88×1.5mm螺纹(工艺用)
三爪卡盘夹一端,大头顶尖顶另一端
2.车端面及倒角
三爪卡盘夹一端,搭中心架托Ф88mm处
3.调头车Ф82mm外圆到Ф84mm
三爪卡盘夹一端,大头顶尖顶另一端
4.车端面及倒角取总长1686mm(留加工余量1mm)
三爪卡盘夹一端,搭中心架托Ф88mm处
3
深孔推镗
1.半精推镗孔到Ф68mm
一端用M88×1.5mm螺纹固定在夹具中,另一端搭中心架
2.精推镗孔到Ф69.85mm
3.精铰(浮动镗刀镗孔)到Ф70±0.02mm,表面粗糙度值Ra为2.5μm
4.滚压孔
用滚压头滚压孔至Ф70
mm,表面粗糙度值Ra为0.32μm
一端用螺纹固定在夹具中,另一端搭中心架
5.车
1).车去工艺螺纹,车Ф82h6到尺寸,割R7槽
软爪夹一端,以孔定位顶另一端
2).镗内锥孔1°30′及车端面
软爪夹一端,中心架托另一端(百分表找正孔)
3).调头,车Ф82h6到尺寸,割R7槽
软爪夹一端,顶另一端
4).镗内锥孔1°30′及车端面
软爪夹一端,顶另一端
二、套筒类零件加工中的主要工艺问题
一般套筒类零件在机械加工中的主要工艺问题是保证内外圆的相互位置精度(即保证内、外圆表面的同轴度以及轴线与端面的垂直度要求)和防止变形。
1.保证相互位置精度
要保证内外圆表面间的同轴度以及轴线与端面的垂直度要求,通常可采用下列三种工艺方案:
(1)在一次安装中加工内外圆表面与端面。
这种工艺方案由于消除了安装误差对加工精度的影响,因而能保证较高的相互位置精度。
在这种情况下,影响零件内外圆表面间的同轴度和孔轴线与端面的垂直度的主要因素是机床精度。
该工艺方案一般用于零件结构允许在一次安装中,加工出全部有位置精度要求的表面的场合。
为了便于装夹工件,其毛坯往往采用多件组合的棒料,一般安排在自动车床或转塔车床等工序较集中的机床上加工。
图1.3所示的衬套零件就是采用这一方案的典型零件。
其加工工艺过程参见棒料毛坯的机械加工工艺过程和图1.4。
棒料毛坯的机械加工工艺过程如下:
序号
工序内容
定位基准
1
加工端面、粗加工外圆表面,粗加工孔,半精加工或精加工外圆、精加工孔、倒角、切断(见图7-70)
外圆表面、端面(定料用)
2.加工另一端面、倒角
外圆表面
3.钻润滑油孔
外圆表面
4.加工油槽
精加工外圆表面(如要求不高的衬套,该工序可由工序1中的精车代替)
外圆表面
图1.3
(2)全部加工分在几次安装中进行,先加工孔,然后以孔为定位基准加工外圆表面。
用这种方法加工套筒,由于孔精加工常采用拉孔、滚压孔等工艺方案,生产效率较高,同时可以解决镗孔和磨孔时因镗杆、砂轮杆刚性差而引起的加工误差。
当以孔为基准加工套筒的外圆时,常用刚度较好的小锥度心轴安装工件。
小锥度心轴结构简单,易于制造,心轴用两顶尖安装,其安装误差很小,因此可获得较高的位置精度。
图1.5所示的轴套即可采用这一方案加工,其加工工艺过程见下面单件毛坯轴套的机械加工工艺。
图1.4转塔车床加工衬套
图1.5
单件毛坯轴套的机械加工工艺过程如下:
序号
工序内容
定位基准
1
粗加工端面、钻孔、倒角
外圆
2
粗加工外圆及另一端、倒角
孔(用梅花顶尖和活络顶尖)
3
半精加工孔(扩孔或镗孔)、精加工端面
外圆
4
精加工孔(拉孔或压孔)
孔及端面
5
精加工外圆及端面
内孔
(3)全部加工分在几次安装中进行,先加工外圆,然后以外圆表面为定位基准加工内孔。
这种工艺方案,如用一般三爪自定心卡盘夹紧工件,则因卡盘的偏心误差较大会降低工件的同轴度。
故需采用定心精度较高的夹具,以保证工件获得较高的同轴度。
较长的套筒一般多采用这种加工方案。
2.防止变形的方法
薄壁套筒在加工过程中,往往由于夹紧力、切削力和切削热的影响而引起变形,致使加工精度降低。
需要热处理的薄壁套筒,如果热处理工序安排不当,也会造成不可校正的变形。
防止薄壁套筒的变形,可以采取以下措施:
(1)减小夹紧力对变形的影响
①夹紧力不宜集中于工件的某一部分,应使其分布在较大的面积上,以使工件单位面积上所受的压力较小,从而减少其变形。
例如工件外圆用卡盘夹紧时,可以采用软卡爪,用来增加卡爪的宽度和长度,如图1.6所示。
同时软卡爪应采取自镗的工艺措施,以减少安装误差,提高加工精度。
图1.7是用开缝套筒装夹薄壁工件,由于开缝套筒与工件接触面大,夹紧力均匀分布在工件外圆上,不易产生变形。
当薄壁套筒以孔为定位基准时,宜采用涨开式心轴。
②采用轴向夹紧工件的夹具。
如图1.8所示,由于工件靠螺母端面沿轴向夹紧,故其夹紧力产生的径向变形极小。
③在工件上做出加强刚性的辅助凸边,加工时采用特殊结构的卡爪夹紧,如图1.9所示。
当加工结束时,将凸边切去。
图1.6用软卡爪装夹工件
图1.7用开缝套筒装夹薄壁工件
(2)减少切削力对变形的影响
常用的方法有下列几种:
①减小径向力,通常可借助增大刀具的主偏角来达到。
②内外表面同时加工,使径向切削力相互抵消,见图1.9所示。
图1.8轴向加紧工件
图1.9辅助凸边的作用
③粗、精加工分开进行,使粗加工时产生的变形能在精加工中能得到纠正。
(3)减少热变形引起的误差
工件在加工过程中受切削热后要膨胀变形,从而影响工件的加工精度。
为了减少热变形对加工精度的影响,应在粗、精加工之间留有充分冷却的时间,并在加工时注入足够的切削液。
热处理对套筒变形的影响也很大,除了改进热处理方法外,在安排热处理工序时,应安排在精加工之前进行,以使热处理产生的变形在以后的工序中得到纠正。
总结
因此我们在加工套同类工件时,首先要了解其结构形状、材料和热处理以及尺寸大小,从而选择更加合理的工艺步骤和工件安装方式,以保证内外圆的相互位置精度和防止变形,提高加工质量和产品合格率。