奥迪汽车标志注塑模设计与制造毕业论文.docx
《奥迪汽车标志注塑模设计与制造毕业论文.docx》由会员分享,可在线阅读,更多相关《奥迪汽车标志注塑模设计与制造毕业论文.docx(17页珍藏版)》请在冰豆网上搜索。
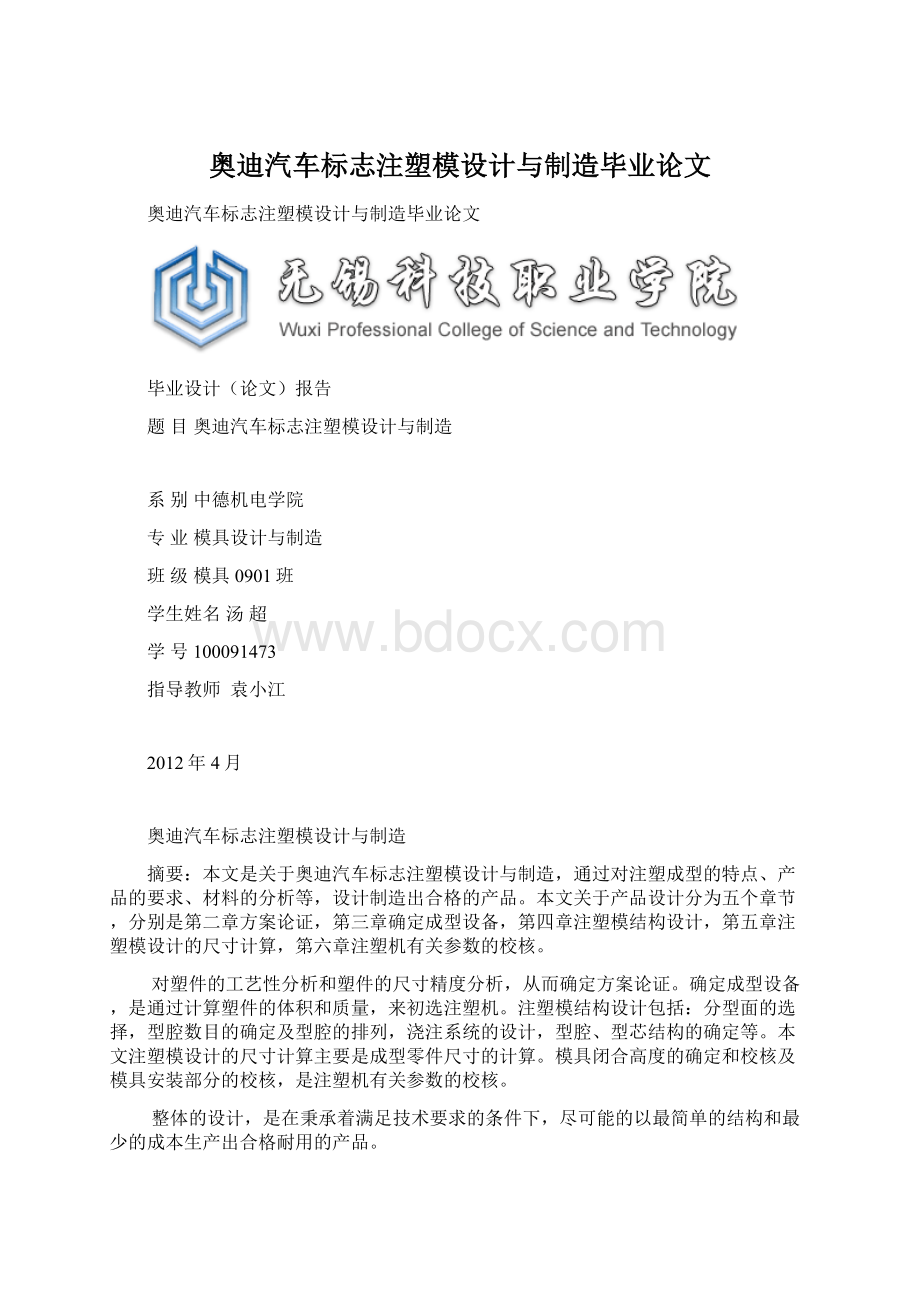
奥迪汽车标志注塑模设计与制造毕业论文
奥迪汽车标志注塑模设计与制造毕业论文
毕业设计(论文)报告
题目奥迪汽车标志注塑模设计与制造
系别中德机电学院
专业模具设计与制造
班级模具0901班
学生姓名汤超
学号100091473
指导教师袁小江
2012年4月
奥迪汽车标志注塑模设计与制造
摘要:
本文是关于奥迪汽车标志注塑模设计与制造,通过对注塑成型的特点、产品的要求、材料的分析等,设计制造出合格的产品。
本文关于产品设计分为五个章节,分别是第二章方案论证,第三章确定成型设备,第四章注塑模结构设计,第五章注塑模设计的尺寸计算,第六章注塑机有关参数的校核。
对塑件的工艺性分析和塑件的尺寸精度分析,从而确定方案论证。
确定成型设备,是通过计算塑件的体积和质量,来初选注塑机。
注塑模结构设计包括:
分型面的选择,型腔数目的确定及型腔的排列,浇注系统的设计,型腔、型芯结构的确定等。
本文注塑模设计的尺寸计算主要是成型零件尺寸的计算。
模具闭合高度的确定和校核及模具安装部分的校核,是注塑机有关参数的校核。
整体的设计,是在秉承着满足技术要求的条件下,尽可能的以最简单的结构和最少的成本生产出合格耐用的产品。
关键词:
注塑模;注塑模设计;塑件
Audicarmarkinjectionmolddesignandmanufacturing
ABSTRACT:
ThepaperisabouttheAudilogodesignandmanufactureofinjectionmold.It’saboutthedesignandmanufacturequalifiedproductsbyanalysisthecharacteristicsofinjectionmolding,productrequirements,materialandsoon.Thispaperisdividedintofivechaptersonproductdesign.Theyarethedemonstrationoftheprogramonchaptertwo,determinethemoldingequipmentonchapterthree,thestructuraldesignoftheinjectionmoldonchapterfour,thecalculatingofthediameteroftheinjectionmoldonchapterfive,andChecktheparametersofinjectionmoldingmachineonchaptersix.
Determinetheprogramdemonstrationbyanalysistheprocessandthesizeoftheplasticparts.Demonstrationoftheprogramistheselectionoftheinjectionmoldingmachinebycalculatingthevolumeandtheweightoftheplasticparts.Thestructuraldesignoftheinjectionmoldcontainsthechoiceofparting,thenumberofthecavitytodetermine,thearrangementofthecavity,gatingsystemdesign,determiningthestructureofthecavityandthecore,etc.Thepaperiscommittedonthecalculationofthemoldedpartdimensions.Determinationandcheckingofthemoldshutheight,andcheckingtheinstallationsectionofthemoldisabouttheinjectionmoldingmachine.
Theoveralldesignshouldbeasdurableproductionofqualifiedproductseconomicallyandsimply,andtheconditionshouldmeetthetechnicalrequirements.
Keywords:
Injectionmold;Injectionmolddesign;Plasticparts
前言
模具,是以特定的结构形式通过一定方式使材料成型的一种工业产品,同时也是能成批生产出具有一定形状和尺寸要求的工业产品零部件的一种生产工具。
模具加工具有如下特点:
尺寸精确、表面光洁;结构合理、生产效率高、易于自动化;制造容易、寿命高、成本低。
模具在很大程度上决定着产品的质量、效益和新产品开发能力。
所以模具又有“工业之母”的荣誉称号。
因此模具加工在加工工业中得到了广泛的应用。
模具是指工业生产上用以注塑、吹塑、挤出、压铸或锻压成型、冶炼、冲压、拉伸等方法得到所需产品的各种模子和工具。
而按所成型的材料的不同,模具可分为金属模具和非金属模具。
金属模具又分为:
铸造模具(有色金属压铸,钢铁铸造)、和锻造模具等;非金属模具也分为:
塑料模具和无机非金属模具。
而按照模具本身材料的不同,模具可分为:
砂型模具,金属模具,真空模具,石蜡模具等等。
其中,随着高分子塑料的快速发展,塑料模具与人们的生活密切相关。
塑料模具一般可分为:
注射成型模具,挤塑成型模具,气辅成型模具等等。
本文将就注射成型模具进行研究。
注射成型是先把塑料加入到注射机的加热料筒内,塑料受热熔融,在注射机螺杆或柱塞的推动下,经喷嘴和模具浇注系统进入模具型腔,由于物理及化学作用而硬化定型成为注塑制品。
注射成型由具有注射、保压(冷却)和塑件脱模过程所构成循环周期,因而注射成型具有周期性的特点。
热塑性塑料注射成型的成型周期短、生产效率高,熔料对模具的磨损小,能大批量地成型形状复杂、表面图案与标记清晰、尺寸精度高的塑件;但是对于壁厚变化大的塑件,难以避免成型缺陷。
塑件各向异性也是质量问题之一,应采用一切可能措施,尽量减小。
注塑模设计一般包括产品模型的分析和绘制,确定型腔数目与排列方式,合理选择分型面,确定侧向分型与抽芯机构,选用模架与标准件,设计浇注、排气、冷却和顶出系统,绘制各个零部件工程图,加工零部件,装配与调试,批量生产等步骤。
注塑模的三大系统包括浇注系统、冷却系统和顶出系统。
在注塑模设计中首先要确定型腔的数目,可以根据产品的结构和尺寸来确定是使用一模一腔还是使用一模多腔,若尺寸较大或者较复杂就选用一模一腔,否则,应使用一模多腔,但是根据经验,在模具中每增加一个型腔,塑件的尺寸精度就要降低4%,因此应综合考虑产品的精度和制造成本来确定型腔的数目。
接着是进行成型零部件的计算,主要是指成型部分与塑件接触部分尺寸的计算。
然后就是浇注系统的设计,浇注系统包括主流道和浇口。
主流道通常位于模具中心塑料熔体入口处,它将注塑机喷嘴注出的塑料熔体导入分流道或是型腔。
由于主流道要与高温塑料熔体及注塑机喷嘴反复接触,所以在注塑模中主流道部分常设计成可以拆卸更换的主流道衬套。
在卧式或立式注塑机上使用的注塑模中,主流道垂直干模具分型面。
为了使塑料熔体按顺序的向前流动,开模时塑料凝料能从主流道中顺利的拔出,需将主流道设计成圆锥形,具有2°~4°的锥角。
浇口套与注塑机喷嘴接触频繁,为防止撞伤,应采取淬火处理使其具有较高的硬度。
浇口是连接流道与型腔之间的一段细短通道,它是浇注系统的关键组成部分。
浇口的形状、位置和尺寸对制品的质量影响很大。
模具的温度直接影响着塑件的质量、熔体的温度以及生产效率。
因此通过调节温度,保持适当的模具温度,可以减小制品的变形,增强制品的力学性能,改善制品的外观质量,提高制品的尺寸精度;同时缩短占整个注射循环周期约80%时间的冷却时间,这将有利于提高注塑成型的生产率。
因此,注塑成型模具的冷却系统设计在一定程度上有利于成本的降低和塑件质量的提高。
在塑料注射成型模具的设计过程中,为了保证制品在脱模过程中不变形,须正确分析脱模力的集中部位和大小,选择合适的脱模方式和顶推位置,设计出准确可靠、运动灵活、结构简单的顶出机构。
顶出方式必须适合成型形状以防止损坏。
通常,部件在模芯上会出现收缩,影响脱模。
建议成型制品上应有较大的顶出面积,以防产品变形。
有几种顶出系统:
起模杆或注塑模顶套;注塑模顶片;气阀;脱模板。
总之,在模具设计过程中,要考虑各方面因素,任何细节都会影响产品的质量,生产的成本和效率。
总而言之,在设计中要综合考虑各种影响产品质量以及生产效率和生产成本的因素,尽量做到以最低的成本和最高的生产效率生产出质量最好的产品。
第一章方案论证
1.1结构分析
1.1.1产品设计图,如图1-1所示:
材料:
ABS
技术要求:
1.未注尺寸公差按GB/T14486-93MT±分布。
2.未注圆角R0.5。
3.外表面Ra=0.8。
4.要求零件外表面光洁,无毛刺、缺陷。
5.零件最终要进行表面电镀处理。
图1-1奥迪汽车标志注塑模设计与制造产品图
1.1.2产品结构工艺性分析
从图纸上分析,该塑件的外形为筒形件,壁厚较小且均匀,符合最小壁厚要求。
塑件大小不一,且较多,但无侧抽装置。
1.2成型工艺分析
1.2.1塑件的原材料分析
(1)基本特性ABS是由丙烯腈、丁二烯、苯乙烯共聚而成的。
这三种组分各自的特性,使ABS具有良好的综合力学性能。
丙烯腈使ABS有良好的耐化学腐蚀及表面硬度,丁二烯使ABS坚韧,苯乙烯使它有良好的加工性和染色性能。
ABS无毒、无味、呈微黄色,成型的塑件有较好的光泽。
密度为1.02g/cm3~1.05g/cm3。
ABS有很好的抗冲击强度,且在低温下也不迅速下降。
ABS有良好的机械强度和一定的耐磨性、耐寒性、耐油性、耐水性、化学稳定性和电气性能。
水、无机盐、碱和酸类对ABS几乎无影响,但在酮、醛、酯、氯代烃中会溶解或形成乳浊液。
ABS不容于大部分醇类及烃类溶剂,但与烃长期接触会软化溶胀。
ABS塑料表面受冰醋酸、植物油等化学药品的侵蚀会引起应力开裂。
ABS有一定的硬度和尺寸稳定性,易于成型加工,经过调色可配成任何颜色。
ABS的缺点是耐热性不高,连续工作温度为70℃左右,热变形温度为90℃左右,且耐气候差,紫外线作用下易变硬发脆。
根据ABS中三种组分之间的比例不同,其性能也略有差异,从而适应各种不同的应用要求。
根据应用要求不同,ABS可分为超高冲击型、高冲击型、中冲击性、低冲击性和耐热型等。
(2)主要用途ABS在机械行业上用来制造齿轮、泵叶轮、轴承、把手、管道、电机外壳、仪表壳、仪表盘、水箱外壳、蓄电池糟、冷藏库和冰箱衬里等。
在汽车工业领域,用ABS制造汽车挡泥板、扶手、热空气调节导管、加热器等,还可用ABS夹层板制小轿车车身。
ABS还可用来制作水表壳、纺织器材、电器零件、文教体育用品、玩具、电子琴及收录机壳体、食品包装容器、农药喷雾器及家具等。
(3)成性特点ABS在升温时粘度增高,所以成型压力高,故塑件上的脱模斜度宜稍大;ABS易吸水,成型加工前应进行干燥处理;ABS易产生溶接痕,模具设计时注意尽量减少浇注系统对料流的阻力;在正常的成型条件下,壁厚、熔料温度对收缩率影响极小。
在要求塑件精度高时,模具温度可控制在50~60℃,而在再强调塑件光泽和耐热时,模具温度应控制在60~80℃。
1.2.2塑件的尺寸精度分析
该塑件全部尺寸精度均按GB/T14486-93MT4±分布,其主要公差标注如下(单位均为mm)
塑件外形尺寸:
塑件外形尺寸:
孔心距尺寸:
1.2.3塑件表面质量分析
该零件要求外表面光洁,无毛刺、缺陷,粗糙度可取Ra0.8um,零件最终进行表面光度处理,塑件内部没有较高的粗糙度要求。
1.3生产规模
该产品要求大规模生产。
第二章确定成型设备
2.1计算塑件的体积
V=3.72cm3
2.2计算塑件的质量
计算塑件的质量是为了选择注射机及确定模具型腔数。
塑件的质量为m=pv=1.05×3.72=3.9g
2.3初选注射机
一模四腔,浇注系统投影面积A=245×5=1225㎜2,浇注系统凝料体积V1=3.14×(5/2)2×245/2+3.14×(8/2)2+50/2=3660㎜3,故浇注系统质量m1=pV1=1.05×3.66=3.84g
注射量m≥(nm+m1)/k=(4×3.83+3.84)/0.8=23.95g
注射压力查表3.1P注=(70~90)MPa
锁模力Fp>p(nA+A1)=30×(4×1017.36+1225)=15.9KN
式中n—型腔个数P—型腔压力查表4.1为30MPa
查表4.2初选注射机为XS-Z-125
2.4塑件模塑成型工艺参数的确定
试模时,可根据实际情况做适当的调整。
注射机类型螺杆式模具温度/℃50~70
螺杆转速/(r.min-1)30~60注射压力MPa70~90
喷嘴形式直通式保压压力MPa50~70
喷嘴温度/℃180~190注射时间/s3~5
前段200~210保压时间/s15~30
料筒温度/℃中段210~230冷却时间/s15~30
后段180~200成型周期/s40~70
第三章奥迪汽车标志注射模结构设计
注射模的设计主要包括:
分型面的选择、模具型腔数目的确定及型腔的排列、浇注系统设计、型芯、型腔结构的确定、推件方式、模具结构零件设计、冷却水道的放置等内容。
3.1分型面的选择
该塑件为奥迪汽车标志,零件外形要求外表偶面光洁,无毛刺、缺陷。
在选择分型面时,根据分型面的选择原则,塑件外形最大轮廓处,考虑不影响塑件的外观质量以及成型后能顺利取出塑件,此塑件无侧抽芯部分,模具结构简单,故选择大端底平面作为分型面,如图3-1所示:
图3-1分型面的确定
3.2型腔数目的确定及型腔的排列
此塑件大批量生产,塑件整体尺寸不大,又考虑塑件型腔中的平衡问题,所以采用一模四腔,型腔布置在模具的中间对称布置,如图3-2所示:
图3-2型腔数目及型腔排列图
3.3浇注系统的设计
浇注系统是指模具中由注射机喷嘴到型腔之间的进料通道。
普通浇注系统一般由主流道、分流道、浇口和冷料穴等四部分组成。
安装在卧式或立式注射机上生产的注射模具所用的浇注系统称为直浇口式浇注系统,其主流道垂直于模具分型面;安装在角式注射机上的模具所用的浇注系统称为横浇口式浇注系统。
浇注系统的设计是模具设计的一个重要环节,设计合理与否对塑件的性能、尺寸、内外部质量及模具结构、塑料的利用率等有较大影响。
(1)主流道设计
a.主流道是指浇注系统中从注射机喷嘴与模具接触处于开始到分流道为止的塑料熔体的流动通道,是熔体最先流经模具的部分,它的形状与尺寸对塑料熔体的流动速度和充模时间有较大影响。
在卧式或立式注射机上使用的模具,主流道垂直于分型面。
主流道通常设计在模具的浇口套中,为了让主流道凝料能顺利从浇口套中拔出,主流道设计成圆锥形,其锥角a为2°-6°,小端直径d比注射机喷嘴直径大0.5-1㎜,由于小端的前面是球面,其深度为3-5㎜,注射机喷嘴的球面在该位置与模具接触并且贴合,因此要求主流道球面半径比喷嘴球面半径大1-2㎜,。
流道的表面粗糙度Ra<=0.8um,浇口套一般采用碳素工具钢(如T8A、T10A等材料)制造,热处理淬火硬度53-57HRC。
b.根据手册查得XS-Z-30型注射机喷嘴的有关尺寸。
喷嘴球半径:
Ro=12mm
喷嘴孔直径:
do=φ4mm
根据模具主流道与喷嘴的关系:
R=Ro+(1~2)mm,d=do+0.5mm
取主流道球面半径:
R=14mm
取主流道的小端直径d=φ4.5mm
为了便于将凝料从主流道拔出,将主流道设计成圆锥形,其斜度为10~30。
经换算得主流道大端直径D=12mm。
同时为了使熔料顺利进入分流道,在主流道出料端设计的r=5mm圆弧过渡。
(2)分流道的设计
分流道是指主流道末端与浇口之间的一段塑料熔体的流动通道。
分流道的作用是改变熔体的流向,使其以平稳的流态均衡地分配到各个型腔。
设计时应注意尽量减少流动过程中的热量损失与压力损失。
分流到的形状及尺寸与塑件的体积、壁厚、形状的复杂程度、注射速率等因素有关。
该塑件的体积比较小,形状较简单,且壁厚均匀,考虑制件充满问题,采用对称中间进浇。
分流到截面形状为半圆形,查有关手册得R=5mm,分流道其他尺寸如图4.2。
(3)浇口设计
浇口亦称进料口,是连续分流道与型腔的熔体通道。
浇口设计与位置的选择恰当与否直接关系到塑件能否完好、高质量地注射成型。
浇口可分为限制性浇口和非限制性浇口两大类,其中限制性浇口分为中心浇口(进料口环形的面积大于主流道小端面积)、侧浇口等,非限制性浇口分为中心浇口、直接交口等。
浇口种类有:
直接浇口、中心浇口、侧浇口、环形浇口、轮辐式浇口、爪形浇口、点浇口、潜伏式浇口。
因为该塑件表面质量要求较高,故采用潜伏式浇口形式,避免了产生浇口痕迹而影响塑件的表面质量与美观效果,并且因为零件在后道工序中要进行电镀加工,故潜伏式浇口开设在推杆的上部而进料口在推杆上端的形式。
其截面为圆形,锥角B=10°~20°,取B=20°。
倾斜角a为45°~60°,取a=45°。
推杆上进料口宽度为0.8~2㎜。
浇口直径根据经验值取d=1㎜。
如图3-3所示:
图3-3开设在推杆上的潜伏式浇口示图
3.4型芯、型腔结构的确定
型芯、型腔可采用整体式或组合式结构。
整体式型腔是直接在型腔板上加工,有较高的强度和刚度。
但零件尺寸较大时加工和热处理较困难。
整体式型芯结构牢固,成型塑件质量好,但尺寸较大,消耗贵重模具钢多,不便加热和热
处理。
整体式结构适用于形状简单的中小型塑件。
组合式型腔是由许多拼块镶制而成的,机械加工和热处理比较容易,能满足大型塑件的成型需要。
组合式型芯可节省贵重模具钢,便于机加工和热处理,修理更换方便。
同时也有利于型芯冷却和排气的实施。
由于该塑件尺寸较小,形状简单,且型芯较多,型芯分布秘密。
故可采用整体式结构,有较高的强度和刚度。
型芯也采用整体式。
3.5推件方式的选择
浇口形式为潜伏式浇口,其浇口分布在推杆上,推出方式也即选择推杆推出,采用直通式推杆,此塑件型腔较浅,包紧力较小,因为推杆较细,为加强强度,故采用梯级式推杆。
推杆端面为圆形固定形式,推杆直径为∮2.5㎜及6㎜,如图6。
在推杆固定板上的孔应为7㎜,推杆抬肩部分的直径为11㎜,推杆固定板上的台阶孔为12㎜。
如图3-4所示:
如图3-4推杆示图
3.6标准模架选择
根据其结构形式及型腔尺寸,选择A2模架,模架尺寸为250×315,如总装图。
3.7冷却系统的设计
由于制件的平均壁厚为3mm.制品尺寸又较小,确定水孔直径为8mm。
由于冷却水道的位置,结构形式,孔径,表面状态,水的流速。
模具材料等很多因素都会影响模具的热量向冷却水道传递,精确计算比较困难。
实际生产中,通常都是根据模具的结构确定冷却水路,通过调节水温,水速来满足要求。
因此塑件壁厚均匀,冷却水道到型腔表面最好距离相当,一般水道孔边至型腔表面距离为10~15㎜,选择12㎜。
冷却水道布置如图3-5所示:
图3-5冷却水道布置示图
3.8排气系统的设计
当塑料熔体充填模具型腔时,必须将浇注系统和型腔中的空气以及塑料在成型过程中产生的低分子挥发气体顺利地排出模外,如果型腔内因各种原因产生的气体不能被排除干净,塑件上就会形成气泡、产生熔接不牢、表面轮廓不清及充填不满等成型缺陷,另外气体的存在还会产生反压力而降低充模速度,故排气系统很重要。
注射模排气方式有:
利用配合间隙排气、在分型面上开设排气槽及利用排气塞排气。
此产品为简单型腔的小型模具,利用推杆的配合间隙排气即可。
这种类型的排气形式,其配合间隙不能超过0.05㎜,一般为0.03㎜~0.05㎜。
3.9模具结构草图(如图3-6所示)
图3-6模具结构草图
3.10注射模动作过程分析
合模时,在导柱16和导套17的导向定位下,动模和定模闭合。
型腔由定模板4上的凹模与固定在动模板5上的凸模组成,并由注射机合模系统提供的锁模力锁紧。
然后注射机开始注射,塑料熔体经定模上的浇注系统进入型腔,待熔体充满型腔并经过保压、补缩和冷却定型后开模。
开模时,注射机合模系统带动动模后退,模具从动模和定模分型面分开,塑件包在凸模18上随动模一起后退,同时拉料杆15将浇注系统的主流道凝料从浇口套中拉出。
当动模移动一定距离后,注射机的顶杆接触推板11推出机构开始动作,使推杆14和拉料杆15分别将塑件及浇注系统凝料从凸模18和冷料穴中推出,塑件与浇注系统凝料一起从模具中落下,至此完成一次注射过程。
合模时,推出机构靠复位杆复位并准备下一次注射。
第四章塑模设计的尺寸计算
4.1成型零件尺寸计算
该塑件的成型零件尺寸按平均法计算。
查有关手册得ABS收缩率为S=0.4﹪~0.8%,故平均收缩率
=(0.4﹪~0.8%)/2=0.6﹪。
根据塑件尺寸公差要求,模具的制造公差取
=0.006
(1)型腔径向尺寸计算分别有
、
校核(Smax-Smin)Ls+δz+δc<Δ
(2)型芯径向尺寸计算
9434
校核(Smax-Smin)Ls+δz+δc<Δ
(3)型腔高度尺寸
校核(Smax-Smin)Ls+δz+δc<Δ(尺寸与拔模方向垂直时δc=0)
(4)中心距尺寸
(5)中心距尺寸18
=(1+0.005)×18
0.054
=18.09
0.054
校核(0.8%-0.3%)×18<0.43所以等式成立
(6)中心距尺寸27
=(1+0.0055)×27
0.065
=27.15
0.065
校核(0.8%-0.3%)×27<0.52所以等式成立
(7)中心距尺寸87
=(1+0.0055)×87
0.11
=87.48
0.11
校核(0.8%-0.3%)×87<0.87所以等式成立
(8)型芯高度尺寸25
式中Ls-塑件外型径向基本尺寸的最大尺寸(mm)
ls-塑件内型径向基本尺寸的最大尺寸
Hs-塑件外高度基本尺寸的最大尺寸
hs-塑件内型深度基本尺寸的平均尺寸
Cs-塑件中心距基本尺寸的平均尺寸
X-修正系数,取0.5~0.75
=塑件公差
=模具制造公差,取(1/3~1/4)
δc=模具成型零件的磨损,取1/6
(与脱模方向垂直的表面不考虑磨损,与脱模方向平行的表面应考虑磨损)
第五章注塑机有关参数的校核
5.1模具闭合高度的确定和校核
5.1.1模具闭合高度的确定。
根据标准模架各模板尺寸及模具设计的其他零件尺寸:
定模座板H定=25
5.1.2定模板