毕业设计论文.docx
《毕业设计论文.docx》由会员分享,可在线阅读,更多相关《毕业设计论文.docx(24页珍藏版)》请在冰豆网上搜索。
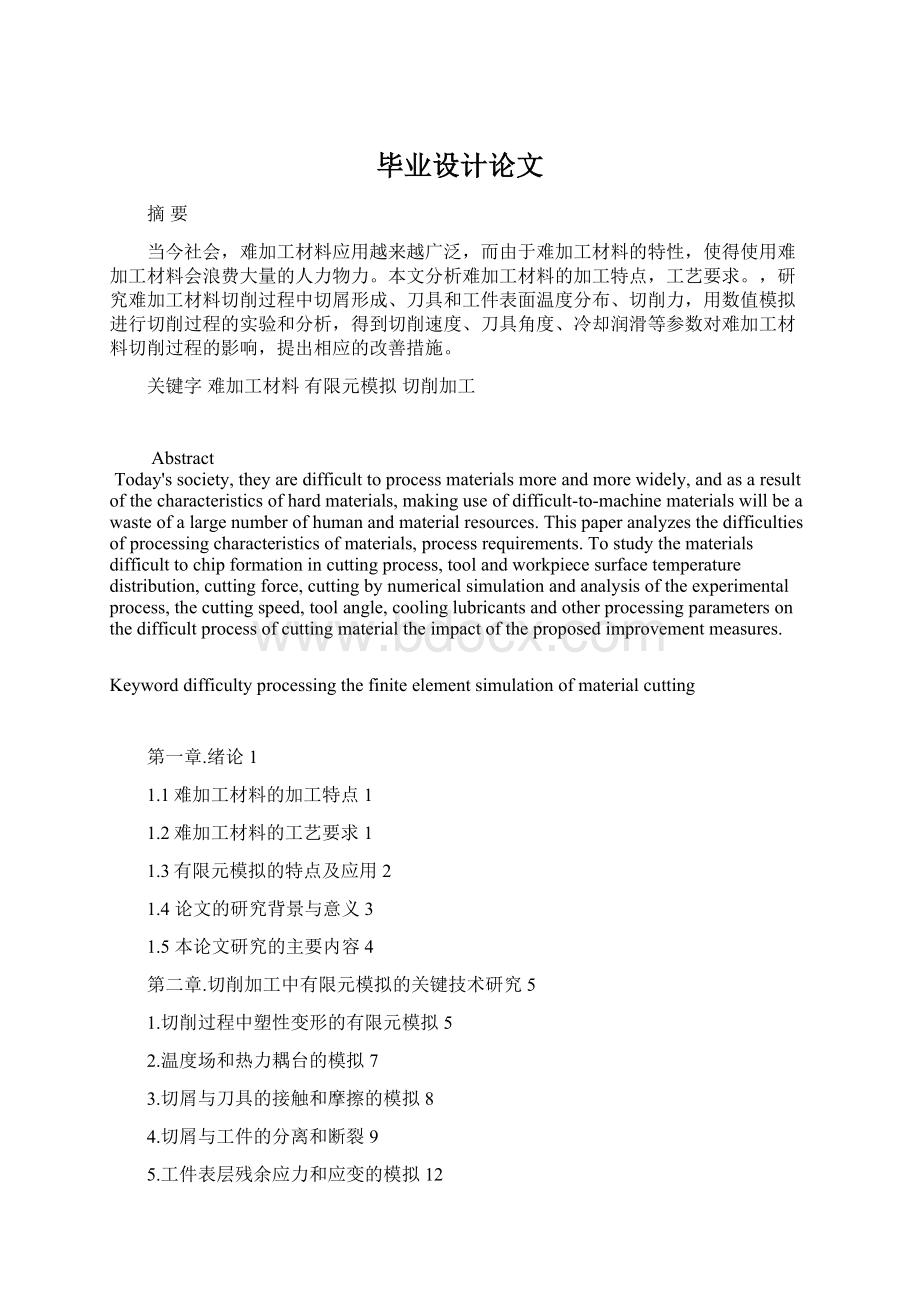
毕业设计论文
摘要
当今社会,难加工材料应用越来越广泛,而由于难加工材料的特性,使得使用难加工材料会浪费大量的人力物力。
本文分析难加工材料的加工特点,工艺要求。
,研究难加工材料切削过程中切屑形成、刀具和工件表面温度分布、切削力,用数值模拟进行切削过程的实验和分析,得到切削速度、刀具角度、冷却润滑等参数对难加工材料切削过程的影响,提出相应的改善措施。
关键字难加工材料有限元模拟切削加工
Abstract
Today'ssociety,theyaredifficulttoprocessmaterialsmoreandmorewidely,andasaresultofthecharacteristicsofhardmaterials,makinguseofdifficult-to-machinematerialswillbeawasteofalargenumberofhumanandmaterialresources.Thispaperanalyzesthedifficultiesofprocessingcharacteristicsofmaterials,processrequirements.Tostudythematerialsdifficulttochipformationincuttingprocess,toolandworkpiecesurfacetemperaturedistribution,cuttingforce,cuttingbynumericalsimulationandanalysisoftheexperimentalprocess,thecuttingspeed,toolangle,coolinglubricantsandotherprocessingparametersonthedifficultprocessofcuttingmaterialtheimpactoftheproposedimprovementmeasures.
Keyworddifficultyprocessingthefiniteelementsimulationofmaterialcutting
第一章.绪论1
1.1难加工材料的加工特点1
1.2难加工材料的工艺要求1
1.3有限元模拟的特点及应用2
1.4论文的研究背景与意义3
1.5本论文研究的主要内容4
第二章.切削加工中有限元模拟的关键技术研究5
1.切削过程中塑性变形的有限元模拟5
2.温度场和热力耦台的模拟7
3.切屑与刀具的接触和摩擦的模拟8
4.切屑与工件的分离和断裂9
5.工件表层残余应力和应变的模拟12
第三章.难加工材料正交切削有限元模型建立13
第四章.难加工材料的正交切削有限元模拟结果分析21
4.1切削速度对切削过程的影响21
4.2进给量对切削过程的影响23
4.3冷却润滑对切削过程的影响24
第五章.结论与展望27
第一章绪论
1.1难加工材料的加工特点
1、凡是硬度强或含有磨料性质的硬质点多或加工硬化严重的材料。
刀具磨损强度大,刀具耐用度低。
还有的材料导热系数小或与刀具材料易未和、粘结,也会造成切削温度高,使得刀具磨损严重。
刀具耐用度低。
2、切削力大。
凡是硬度,强度高,塑性和韧性大,加工硬件严重,亲和力大的材料,消耗功率多,使切削力大。
3、切削温度高。
凡是切削加工硬化严重,强度高、塑性和韧性大,亲和力大或导热系数小的材料,由于切削力和切削功率大,生成热量多,而散热性能卫差,故切削温度商。
4、加工表面粗糙,粗糙不易达到要求。
加工硬化严惩亲和力大、塑性和违性大的工件材料已加工表面粗糙度值大,表面质量和精度均不易边到要求。
5、切屑难于处理
6、加工硬化严重。
由于材料塑性大,韧性高,使加工的硬化倾向极大,造成加工硬化严重。
1.2难加工材料的工艺要求
有文献[1]难加工材料的加工特点,使切削加工难以正常进行,是当今切削加工研究的课题。
解决难加工材料的加工选径是多方面的。
如采用合适的热址理工艺,采用电加工,加热切削,振动切削等特种加工方法,都是有效的途径。
就切削加工而言,对其工艺要求主要有以下几点:
(1)选择合适的刀具材料:
根据难加工金属材料的性能,加工要求和加工方法,选择合适的刀具材料。
一般选择高速钢和硬质台金。
特别是高性能钢和涂层高速钢,碳化钛基硬质台金,涂层硬质合金等。
陶瓷刀具、立方氯化硼刀具.金刚石刀具等新型刀具材料的发展和应用。
为解决难加工金属材料的加工,提供了有利条件。
具体选择刀具材料可参考有关资料。
(2)选择合理的刀具几何参数
刀具几何参数,一定需根据工件材料性能。
刀具材料特点和工艺要求来进行合理选择,以提高刀具耐用度和加工质量。
一般的几何参数选择,可参考有关资料。
(3)优化选用切削用量
切削用量柏优化选用,关系到切削过程中能否充分发挥刀具材料和刀具几何参数的应有作用,具体选择可参考有关资料。
(4)采用适宜的切削液
对难加工盘属材料的切削加工,采用适宜的切削液比切削加工一般材料更为重要,对不同材料应选用不同的切削液和不同的配方以及有效的浇注方法,具体选用可参考有关资料。
1.3有限元模拟的特点及应用
切削工艺和切屑形成的有限元模拟对了解切削机理,提高切削质量是很有帮助的。
这种数值模拟方法适合于分析弹塑性大变形问题,包括分析与温度相关的材料性能参数和很大的应变速率问题。
有限元分析(FEA,FiniteElementAnalysis)的基本概念是用较简单的问题代替复杂问题后再求解。
它将求解域看成是由许多称为有限元的小的互连子域组成,对每一单元假定一个合适的(较简单的)近似解,然后推导求解这个域总的满足条件(如结构的平衡条件),从而得到问题的解。
这个解不是准确解,而是近似解,因为实际问题被较简单的问题所代替。
由于大多数实际问题难以得到准确解,而有限元不仅计算精度高,而且能适应各种复杂形状,因而成为行之有效的工程分析手段。
有限元是那些集合在一起能够表示实际连续域的离散单元。
有限元的概念早在几个世纪前就已产生并得到了应用,例如用多边形(有限个直线单元)逼近圆来求得圆的周长,但作为一种方法而被提出,则是最近的事。
有限元法最初被称为矩阵近似方法,应用于航空器的结构强度计算,并由于其方便性、实用性和有效性而引起从事力学研究的科学家的浓厚兴趣。
经过短短数十年的努力,随着计算机技术的快速发展和普及,有限元方法迅速从结构工程强度分析计算扩展到几乎所有的科学技术领域,成为一种丰富多彩、应用广泛并且实用高效的数值分析方法。
有限元方法与其他求解边值问题近似方法的根本区别在于它的近似性仅限于相对小的子域中。
20世纪60年代初首次提出结构力学计算有限元概念的克拉夫(Clough)教授形象地将其描绘为:
“有限元法=RayleighRitz法+分片函数”,即有限元法是RayleighRitz法的一种局部化情况。
不同于求解(往往是困难的)满足整个定义域边界条件的允许函数的RayleighRitz法,有限元法将函数定义在简单几何形状(如二维问题中的三角形或任意四边形)的单元域上(分片函数),且不考虑整个定义域的复杂边界条件,这是有限元法优于其他近似方法的原因之一[2]。
1.4论文的研究背景与意义
金属切削工艺是制造业中的关键技术,随着电子、光学、微细产品的不断发展,在生产率和加工精度方面对切削工艺提出了更高的要求。
虚拟制造将是解决这一系列问题的重要手段,在虚拟制造中,基于弹性力学、塑性力学、断裂力学、摩擦学、热力学和材料学的切削过程数值模拟将是一种强有力的工具,目前,这项技术已经在学术研究上取得了一些进展,但与其它加工技术,如金属塑性加工)相比,切削模拟还没有大量应用到生产实际,这还需要对实际生产中影响切削加工的各种因素作进一步研究。
在实际切削过程中,例如车削、磨削和钻削等,切削是在三维变形域内进行的;例如,工件和刀刃具有三维的几何形状,工件材料和刀具的相对移动也不总是正交的,另外,一些工件材料也是各向异性的,由于这些因素,切削是在三维状态下成形的,然后获得具有三维几何形状的产品。
另外有些工艺,例如斜刃切削的模拟是不能用二维模型来实现的,必须建立三维模型。
所以,为了揭示实际切削机理,对切削加工进行三维模拟是很有必要的,目前的太多数研究斗都停留在二维模拟上,随着计算机硬件性能的提高,切削工艺的三维模拟将是今后发展的主要方向。
实际上,典型的车削和钻削工件或刀具都是在做回转运动,但是到目前为止,文献中所报道的切削工艺模拟,大多是将工件约束住,让刀具做进给运动,这样实际生产中工件的回转运动对切削质量的影响并没有体现出来,在金属塑性加工中,例如板料的旋压成形,内螺纹管的拉拔成形、轧制成形等都可以模拟工件或模具的回转运动,在高速的车削过程中,工件的转动是不可忽略的。
关于这一点,在今后的切削模拟中还应加强。
切削加工是使工件不断分离出切屑的过程,目前关于切屑断裂和分离的准则还不太成熟,每种分离准则都有不足的地方,形成后的切屑断裂准则也需要进一步研究,目前的模拟结果与实际情况还有一定的差距。
相对于切屑的形成,对于成形工件加工质量的研究较少,今后将会成为重点的研究方向。
其巾包括:
与工件几何尺寸和精度密切相关的残余应力和残余应变的模拟、与工件表面光洁度有关的毛刺形成的模拟、考虑工件加工中夹具的模拟等。
工件切削加工中的毛刺形成和消除的模拟技术还不成熟,因为它涉及的因素较多,对成形工件的表面质量起着至关重要的作用。
月前关于这方面的研究刚刚起步,还没有详细的结果。
切削加工中刀具的磨损和受力、加工中振颤引起的刀跳、工具形状不合适引起的崩刀等现象的模拟也会成为今后切削加工技术模拟的一个方向。
高速切削加工中,冷却液是不可缺少的,目前在切削模拟中,还没有模拟切削过程中的冷却对成形质量的影响。
1.5本论文研究的主要内容
本论文的研究内容为以AISI-1006,COLD[70F(20C)]不锈钢为研究对象,采用数值模拟技术,建立正交切削有限元模型,研究建模过程中切屑形成、刀具和工件表面温度分布、切削力;利用建立的有限元模型分析切削速度、刀具角度、冷却润滑等参数对难加工材料切削过程的影响。
第二章切削加工中有限元模拟的关键技术研究
2.1切削过程中塑性变形的有限元模拟
切削过程可以看作是产生塑性变形并且发生切屑(chIp)与工件(workpiece)分离.所采用的数值方法主要有两种,即弹塑性有限元法和刚塑性有限元法.在此基础上,如果考虑材料加工中的温度、速度变化带来的影响,还有热弹(黏)塑性有限元和热刚(黏)塑性有限元方法。
当工件的尺寸、所用单元个数等条件相同时,弹塑性有限元和刚塑性有限元的应力、应变分析结果几乎相同。
两种有限元方法的区别主要在于,弹塑性有限元方法主要应用在求解残余应力的分布和回弹问题求解,而刚塑性有限元的求解忽略了弹性变形,不能求解残余应力或回弹问题,但它比弹塑}生有限元的求解速度要快3~5倍。
金属切削工艺是一个比较复杂的过程,它涉及到许多方面,例如机床、工件、刀具、夹具、冷却液、动态效应等等,而且这些因素都是相关的在上述各种影响切削质量的因素中,切屑的形成是很重要的因素,因为在切削过程中,切屑的形成对刀具的寿命、加工表面的质量影响很大。
图1是通过采用刚塑性有限元(更新的拉格朗日方法)模拟的切屑变形。
这种模拟过程是一种典型的高梯度问题,在局部区域内材料产生高温、大变形,需要有自适应的网格重划技术.在图中可以看出,切屑的塑性变形是很大的,随着变形的加剧,材料初始网格会产生严重的畸变,这种网格的畸变会对求解产生影响。
一是网格的畸变会降低求解的精度,还会导致出现负的Jacobi矩阵,无法求解。
网格产生畸变的另一后果就是模具会嵌入到材料内部(图2),与实际情况不符,使求解无法进行。
对于这种大的塑性变形问题,应该采用自适应网格重划分技术(Remeshing)。
随着刀具的进给,正在被加工的部分应该实现网格细划,而没有加工的部分和加工过的部分,网格应该粗划,这样既解决了局部变形的精确求解,又节省了求解时间以及内存的消耗。
图1切削过程中切屑塑性变形的有限元模拟
图2切屑形成过程中刀具与材料网格的嵌入
判断是否应该进行网格重划的标准实际上就是一个几何准则。
可以一个绝对的穿透距离来作为标准,也可用刀具穿透深度与被穿透单元长度的比值作为标准,目前应用比较普遍的是以刀具穿透材料区的面积(体积)与被穿透材料单元的整个体积的比值作为标准。
在模拟前可以设定临界值,当准则中的几何量超过这个临界值时,程序自动停下来进行网格重划分。
通过切屑形成过程的模拟,可以得到切削加工中的切削力的变化曲线(图3)。
这对设备和夹具的设计或选用是很有帮助的。
.
图3切削力随刀具行程的变化曲线
2.2温度场和力耦台的模拟
有高温、高速成形的特点。
金属在高速切削下,剧烈的摩擦和断裂使得局部区域的温度在儿秒钟甚至是零点几秒就上升到很高的温度,材料的各种性能参数必然受到温度的影响,另外,高温状态下引起的热应力也对成形质量和刀具的磨损产生影响。
因为切削加工涉及到了与高温、高应变速率耦合的大变形和断裂问题,有限元分析也应该建立在与温度耦合的塑性变形理论基础上。
在金属切削模拟过程中,温度的因素是不可以忽略的,要通过设定摩擦条件、摩擦方式和摩擦系数来计算摩擦生热。
在金属切削工艺中,工件的塑性变形和切屑一刀具界面的摩擦是两个主要的热源。
在金属切削工艺中,工件内部的温度分布主要是由下面的因素决定的:
(1)工件和刀具的初始温度;
(2)成形工件和刀具的状态和环境;
(3)工件塑性变形和切屑一刀具界面的摩擦产生的热源。
为了耦合热载荷和机械载荷的相互影响,可以利用Prandtl—Reuss流动法则和VonMises屈服准则[3]同时将材料考虑为具有各向同性的应变硬化性质,来导出热弹塑性热力耦合本构方程,包括应变、应变速率、和温度。
接下来,应用大变形一大应变理论中的小增量位移,利用更新的Lagrange公式和增量变分原理。
在此基础上,导出热弹塑性大变形耦台方程(式(2.1))。
还可以处理工件和刀具之间以及工件与周围空气之间的热传导。
(2.1)
由于用于机械加工的材料在高温状态下经常是对速度敏感的,所以需要考虑两种因素,一个是材料的速度敏感性影响,另一个是金属流动和热传递分析的耦合影响。
以二维模拟为例,切削工艺中的热传导方程为
(2.2)
(2.3)
式中的J为热功当量
边界条件如下
(1)摩擦生热,工件和刀具之问的摩擦生热通过以下方程来表示:
(2.4)
生成的热量作为热载荷的方式,一半施加给工件,另一半施加给刀具。
(2)热交换,下面公式中的热传递是发生在工件和空气以及工具和空气之间,即
(2.5)
2.3切屑与刀具的接触和摩擦的模拟
由于摩擦力与切屑的形成和刀具的运动密切相关,所以在建立切削模型时,切屑刀具接触现象是应考虑的主要因素。
大量的实验表明,前刀面上的应力分布是不均匀的,正应力随着刀具行程的增加而增加,而剪切应力首先增加,然后达到一个近似的常值。
也就是说,在前刀面上有两个明显的分区:
滑动区和粘着区。
在滑动区中,正应力相对较小,几乎没有于摩擦。
在粘着区,正应力是很高的,摩擦应力近似是—个常数。
基于实验研究的结果,在滑动区域使刷常系数摩擦(即库仑摩擦定律),在粘着区使用常摩擦应力只是一个近似。
可以用下式来表示:
(2.6)
上述的摩擦模型在大部分有限元模拟切削工艺中得到应用。
利用这种方法,常摩擦应力可以通过切削的流动应力获得。
但是,摩擦系数是很难获得的,因为,滑动区的摩擦条件是与传统的摩擦实验不同的。
切屑的底面是伴随着很高的应变硬化而新形成的。
由于产生的塑性变形,切削的硬度高于工件材料的两倍.这个硬度变化可能引起摩擦系数的变化。
2.4切屑与工件的分离和断裂
与一般的金属塑性成形不同的是,切削加工是一个使被加工材料不断产生分离的过程。
切削加工的有限元模拟可以分为两种形式,即更新的Lagrange形式和Euler形式。
在实际模拟过程中,前者使用得更为广泛。
这种方式的有限元模拟需要有一定的分离准则使得切屑从工件中产生分离。
另外,在加工过程中,有的切屑可以产生连续的塑性变形,而有的切屑则产生锯断状的断裂。
所以还要有相应的断裂准则来模拟切屑材料的断裂。
一个合理的分离准则只有真实地反应切削加工材料的力学和物理性质,才能得到合理的结果,例如切削几何形状、切削力、温度和残余应力分布等。
另外,一个好的分离准则的临界值在切削材料确定后,不应该随着切削条件的变化而变化。
到目前为止,在有限元模拟中已经提出了各种切屑分离准则,这些准则可以分为两种类型:
几何准则和物理准则。
几何准则主要通过变形体的几何尺寸的变化来判断分离与否。
而物理准则主要是基于制定的一些物理量的值是否达到了临界值而建立的,主要有基于等效塑性应变准则、基于应变能量密度准则、断裂应力准则等。
在图5中,工件的切屑层和工件层之间预先设定了一个分离线,在分离线上的切屑和工件的点重合。
几何分离准则建立在工件中的点n和切削刃d之间的距离D上,当距离D小于临界值时,点a上的两点不再重台,被认为分开,即工件上的点和切屑上的点.Usui和Shirakashi在切削模拟中,首先提出并采用了切屑的几何分离准则。
ShihJ等人在切削模拟中采用了几何分离准则发现,它是一种很稳定的准则。
Komvopoulos和Erpenbeck指出,交叠点与切削刃之间要有充足的距离,才能避免由于有限元网格过分的扭曲而引起的计算收敛问题。
图5几何分离准则模型
几何准则的优点是比较简单的,判断起来容易。
我们知道,实际切削中上切削刃和分离点的实际距离几乎是零。
但在模拟时,却不能将D值设为零,这就与实际情况有一定的差距,D值的选择也往往会影响模拟计算的收敛性,需要有一定的经验才能选择合适的临界值。
另外,应用这种准则的有限元模型是有一定限制的,必须建立分离线(图6),人为地将工件和切屑的网格分离开。
图6
工件刀具的有限元网格物理准则是由1wata,Osakada和Terasaka等人提出来的,他们首先建立了考虑应力历史的韧性断裂准则,并将模拟结果与实验结果傲了对比,证明是很有效的。
StrebjiwsjUnl和Carroll提出并建立了基于等效塑性应变上的物理准则,并指出当临界值选择为0J25~i.O0时,切屑的形成几乎不受影响,但是工件成形表面的残余应力却随着临界值的增加而增加。
只通过等效塑性应变值来判断是否发生断裂分离是不可靠的,因为当切削条件变化时,例如切削速度、刀具前角和切削深度等变化后,等效塑性应变的值也会发生很大的变化,要想得到一个不随切削条件变化或变化很小的I临界值,必须使等效塑性应变值和其它力学量进行耦台。
由于应变速率也会受到切削条件变化的影响,所以可以使等效塑性应变和应变速率耦合,建立新的准则。
这样,临界值就很少受到切削条件的影响,而成为材料断裂分离的一种属性了。
Zone~ChingLia和Yeou-YihLin等人建立了基于应变能量密度的切屑分离准则,并且说明这个准则的临界值是材料的常数。
它的主要原理如下:
连续介质力学假定工件系统能够划分为有限数量的单元,而且这些单元在一个连续状态下进行联接。
因为每个单元承受的载苛和单元形状材料性质不同,在物体内,存储于每个单元单位体积内的能量也是不同的。
对于物件内的一些单元,应变能密度能够通过下式来获得:
(2.7)
在有限元模拟中假定切削刃溜一直线行走,仅对那些与切削刃相交的点进行是否破坏的判断。
也就是说,假设只有那些在刀具行走轨迹上的点才有可能会产生分离。
当刀具首先切入工件时,工件中各个单元之间存储的单位体积能量都是不同的。
当刀具向前移动时,单元能够逐渐积累应变能密度,即工具每向前移动一个位移增量,切削刃将切过所设汁好路径上的一些点。
从这些变形的点上积累的应变能密度值(aw/d)能够被计算和检查。
一旦切削刃附近点的应变能密度积累值(aw/d)超过了材料I临界值(aw/av),这些点就被认为是已经从工件中分离出来,变成切屑的一部分。
工件材料的能量临界值是一个材料常数,它代表着工件材料的能量吸收能力。
这个值是通过拉伸测试曲线中的应力一应变导出的。
在极限应力曲线下应力一应变的曲线面积被设定为材料的临界应变能密度值(aw/av)。
断裂准则不但可以应用在切屑和工件的分离中,也可以模拟出切屑形成后的断裂,图7是采用CockriftLatham断裂准则所模拟的刀具在不同前角时切屑断裂的形式。
(a)(b)
图7切削断裂时的模拟结果
2.5工件表层残余应力和应变的模拟
切削加工工件表面层的力学状态,例如残余应力和残余应变等,影响着工件的质量。
残余应力引起的变形降低了工件的几何精度。
另外,表层内的残余拉应力降低了工件的疲劳强度。
为了解决这些问题,需要准确地预测工件的残余应力和几何精度,并将它们控制在一定范甩内。
机械加工件的质量将会在此基础上得到提高。
在切削加工工艺中,无论是车削还是磨削,前一道切削工序的影响层经常是被切削掉,新生成的表面层有残余应力和应变,也称为工作硬化。
在重复切削过程中,影响层的切削会引起切削力或剪切角的改变。
在弹塑性有限元模拟中,可以通过逐次卸载的方法,求出工件中的残余应力和残余应变。
逐次卸载可以看作是每次施加一个一△{P}的载荷,直到载荷全部释放完。
计算的方法和步骤与加载过程基本相同,但是卸载中的单元是由塑性状态向弹性状态的转变,各单元的转变次序是不一样的。
在卸载中,有时个别单元可能瞬间处于加载状态,需要对单元处于加载还是卸载状态进行判断。
一般来讲,假如材料处于加载状态,应力一应变关系应该符合材料机械性能曲线.在进入卸载状态后,应力一应变关系符合弹性回复直线。
所以,针对两种状态下的求解过程就有很大的不同。
进入大变形状态时,应变硬化速率变得非常小,几乎为零。
同时等效应力增量也非常小,有时小于计算误差的范围。
为了解决这个问题,可采用最小二乘方法来更精确地确定单元的状态。
第3章.难加工材料正交切削有限元模型建立
利用deform软件建立有限元模型。
1.DEFORM-2D(二维)适用于各种常见的UNIX工作站平台(HP,SGI,SUN,DEC,IBM)和Windows-NT微机平台。
可以分析平面应变和轴对称等二维模型。
它包含了最新的有限元分析技术,既适用于生产设计,又方便科学研究。
DEFORM功能
1.成形分析
冷、温、热锻的成形和热传导耦合分析(DEFORM所有产品)。
丰富的材料数据库,包括各种钢、铝合金、钛合金和超合金(DEFORM所有产品)。
用户自定义材料数据库允许用户自行输入材料数据库中没有的材料(DEFORM所有产品)。
提供材料流动、模具充填、成形载荷、模具应力、纤维流向、缺陷形成和韧性破裂等信息(DEFORM所有产品)。
刚性、弹性和热粘塑性材料模型,特别适用于大变形成形分析(DEFORM所有产品)。
弹塑性材料模型适用于分析残余应力和回弹问题(DEFORM-Pro,2D,3D)。
烧结体材料模型适用于分析粉末冶金成形(DEFORM-Pro,2D,3D)。
完整的成形设备模型可以分析液压成形、锤上成形、螺旋压力成形和机械压力成形(DEFORM所有产品)。
用户自定义子函数允许用户定义自己的材料模型、压力模型、破裂准则和其他函数(DEFORM-2D,3D)。