数控编程与操作讲义.docx
《数控编程与操作讲义.docx》由会员分享,可在线阅读,更多相关《数控编程与操作讲义.docx(46页珍藏版)》请在冰豆网上搜索。
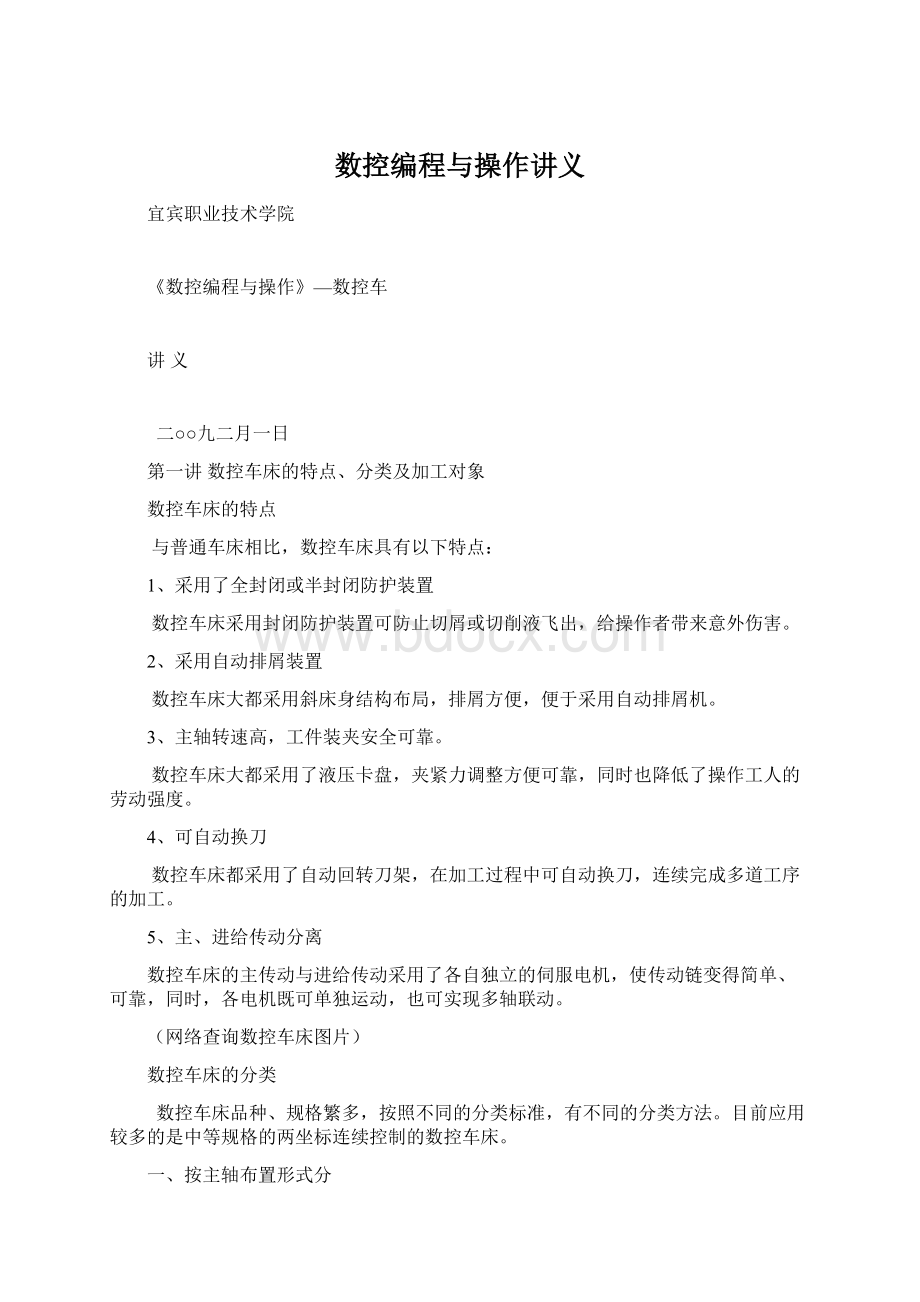
数控编程与操作讲义
宜宾职业技术学院
《数控编程与操作》—数控车
讲义
二○○九二月一日
第一讲数控车床的特点、分类及加工对象
数控车床的特点
与普通车床相比,数控车床具有以下特点:
1、采用了全封闭或半封闭防护装置
数控车床采用封闭防护装置可防止切屑或切削液飞出,给操作者带来意外伤害。
2、采用自动排屑装置
数控车床大都采用斜床身结构布局,排屑方便,便于采用自动排屑机。
3、主轴转速高,工件装夹安全可靠。
数控车床大都采用了液压卡盘,夹紧力调整方便可靠,同时也降低了操作工人的劳动强度。
4、可自动换刀
数控车床都采用了自动回转刀架,在加工过程中可自动换刀,连续完成多道工序的加工。
5、主、进给传动分离
数控车床的主传动与进给传动采用了各自独立的伺服电机,使传动链变得简单、可靠,同时,各电机既可单独运动,也可实现多轴联动。
(网络查询数控车床图片)
数控车床的分类
数控车床品种、规格繁多,按照不同的分类标准,有不同的分类方法。
目前应用较多的是中等规格的两坐标连续控制的数控车床。
一、按主轴布置形式分
1、卧式数控车床
最为常用的数控车床,其主轴处于水平位置。
2、立式数控车床
其主轴处于垂直位置。
立式数控车床主要用于加工径向尺寸大,轴向尺寸相对较小,且形状较复杂的大型或重型零件,适用于通用机械、冶金、军工、铁路等行业的直径较大的车轮、法兰盘、大型电机座、箱体等回转体的粗、精车削加工。
二、按可控轴数分
1、两轴控制
当前大多数数控车床采用的两轴联动,即X轴、Z轴。
2、多轴控制
档次较高的数控车削中心都配备了动力铣头,还有些配备了Y轴,使机床不但可以进行车削,还可以进行铣削加工。
三、按数控系统的功能分
1、经济型数控车床
一般采用开环控制,具有CRT显示、程序储存、程序编辑等功能,加工精度不高,主要用于精度要求不高,有一定复杂性的零件。
2、全功能数控车床
这是较高档次的数控车床,具有刀尖圆弧半径自动补偿、恒线速、倒角、固定循环、螺纹切削、图形显示、用户宏程序等功能,加工能力强,适宜加工精度高、形状复杂、工序多、循环周期长、品种多变的单件或中小批量零件的加工。
3、车削中心
车削中心的主体是数控车床,配有动力刀座或机械手,可实现车、铣复合加工,如高效率车削、铣削凸轮槽和螺旋槽。
数控车床的主要加工对象
一、数控车床主要功能
不同数控车床其功能也不尽相同,各有特点,但都应具备以下主要功能。
1、直线插补功能
控制刀具沿直线进行切削,在数控车床中利用该功能可加工圆柱面,圆锥面和倒角。
2、圆弧插补功能
控制刀具沿圆弧进行切削,在数控车床中利用该功能可加工圆弧面和曲面。
3、固定循环功能
固化了机床常用的一些功能,如粗加工、切螺纹、切槽、钻孔等,使用该功能简化了编程。
4、恒线速度车削
通过控制主轴转速保持切削点处的切削速度恒定,可获得一致的加工表面。
5、刀尖半径自动补偿功能
可对刀具运动轨迹进行半径补偿,具备该功能的机床在编程时可不考虑刀具半径,直接按零件轮廓进行编程,从而使编程变得方便简单。
二、数控车床主要加工对象
数控车床是目前使用比较广泛的数控机床,主要用于轴类和盘类回转体工件的加工,能自动完全内外圆面、柱面、锥面、圆弧、螺纹等工序的切削加工,并能进行切槽、钻、扩、铰孔等加工,适合复杂形状工件的加工。
与常规车床相比,数控车床还适合加工如下工件。
1、轮廓形状特别复杂或难于控制尺寸的回转体零件
2、精度要求高的零件
3、特殊的螺旋零件
如特大螺距(或导程)、变螺距、等螺距与变螺距或圆柱与圆锥螺旋面之间作平滑过渡的螺旋零件,以及高精度的模数螺旋零件和端面螺旋零件。
4、淬硬工件的加工
在大型模具加工中,有不少尺寸大而形状复杂的零件。
这些零件热处理后的变形量较大,磨削加工困难,可以用陶瓷车刀在数控机床上对淬硬后的零件进行车削加工,以车代磨,提高加工效率。
第二讲数控车床的坐标系统及设定
在数控编程时,为了描述机床的运动,简化程序编制的方法及保证纪录数据的互换性,数控机床的坐标系和运动方向均已标准化,ISO和我国都拟定了命名的标准。
通过这一部分的学习,能够掌握机床坐标系、编程坐标系、加工坐标系的概念,具备实际动手设置机床加工坐标系的能力。
一、机床坐标系
1、机床坐标系的确定
(1)机床相对运动的规定
在机床上,我们始终认为工件静止,而刀具是运动的。
这样编程人员在不考虑机床上工件与刀具具体运动的情况下,就可以依据零件图样,确定机床的加工过程。
(2)机床坐标系的规定
标准机床坐标系中X、Y、Z坐标轴的相互关系用右手笛卡尔直角坐标系决定。
在数控机床上,机床的动作是由数控装置来控制的,为了确定数控机床上的成形运动和辅助运动,必须先确定机床上运动的位移和运动的方向,这就需要通过坐标系来实现,这个坐标系被称之为机床坐标系。
例如铣床上,有机床的纵向运动、横向运动以及垂向运动,如图1所示。
在数控加工中就应该用机床坐标系来描述。
图1立式数控铣床
标准机床坐标系中X、Y、Z坐标轴的相互关系用右手笛卡尔直角坐标系决定:
图2 直角坐标系
1)伸出右手的大拇指、食指和中指,并互为90°。
则大拇指代表X坐标,食指代表Y坐标,中指代表Z坐标。
2)大拇指的指向为X坐标的正方向,食指的指向为Y坐标的正方向,中指的指向为Z坐标的正方向。
3)围绕X、Y、Z坐标旋转的旋转坐标分别用A、B、C表示,根据右手螺旋定则,大拇指的指向为X、Y、Z坐标中任意轴的正向,则其余四指的旋转方向即为旋转坐标A、B、C的正向,见图2
(3)运动方向的规定
增大刀具与工件距离的方向即为各坐标轴的正方向,如图3所示为数控车床上两个运动的正方向。
图3 机床运动的方向
2、坐标轴方向的确定
(1)Z坐标
Z坐标的运动方向是由传递切削动力的主轴所决定的,即平行于主轴轴线的坐标轴即为Z坐标,Z坐标的正向为刀具离开工件的方向。
如果机床上有几个主轴,则选一个垂直于工件装夹平面的主轴方向为Z坐标方向;如果主轴能够摆动,则选垂直于工件装夹平面的方向为Z坐标方向;如果机床无主轴,则选垂直于工件装夹平面的方向为Z坐标方向。
图4所示为数控车床的Z坐标。
图4 数控车床的坐标系
(2)X坐标
X坐标平行于工件的装夹平面,一般在水平面内。
确定X轴的方向时,要考虑两种情况:
1)如果工件做旋转运动,则刀具离开工件的方向为X坐标的正方向。
2)如果刀具做旋转运动,则分为两种情况:
Z坐标水平时,观察者沿刀具主轴向工件看时,+X运动方向指向右方;Z坐标垂直时,观察者面对刀具主轴向立柱看时,+X运动方向指向右方。
图4所示为数控车床的X坐标。
(3)Y坐标
在确定X、Z坐标的正方向后,可以用根据X和Z坐标的方向,按照右手直角坐标系来确定Y坐标的方向。
图4所示为数控车床的Y坐标。
图5 数控立式铣床的坐标系
例:
根据图5所示的数控立式铣床结构图,试确定X、Y、Z直线坐标。
(1)Z坐标:
平行于主轴,刀具离开工件的方向为正。
(2)X坐标:
Z坐标垂直,且刀具旋转,所以面对刀具主轴向立柱方向看,向右为正。
(3)Y坐标:
在Z、X坐标确定后,用右手直角坐标系来确定。
3、附加坐标系
为了编程和加工的方便,有时还要设置附加坐标系。
对于直线运动,通常建立的附加坐标系有:
(1)指定平行于X、Y、Z的坐标轴
可以采用的附加坐标系:
第二组U、V、W坐标,第三组P、Q、R坐标。
(2)指定不平行于X、Y、Z的坐标轴
也可以采用的附加坐标系:
第二组U、V、W坐标,第三组P、Q、R坐标。
4、机床原点的设置
机床原点是指在机床上设置的一个固定点,即机床坐标系的原点。
它在机床装配、调试时就已确定下来,是数控机床进行加工运动的基准参考点。
(1)数控车床的原点
在数控车床上,机床原点一般取在卡盘端面与主轴中心线的交点处,见图6。
同时,通过设置参数的方法,也可将机床原点设定在X、Z坐标的正方向极限位置上。
图6车床的机床原点
图7 铣床的机床原点
(2)数控铣床的原点
在数控铣床上,机床原点一般取在X、Y、Z坐标的正方向极限位置上,见图7。
5、机床参考点
机床参考点是用于对机床运动进行检测和控制的固定位置点。
图8数控车床的参考点
机床参考点的位置是由机床制造厂家在每个进给轴上用限位开关精确调整好的,坐标值已输入数控系统中。
因此参考点对机床原点的坐标是一个已知数。
通常在数控铣床上机床原点和机床参考点是重合的;而在数控车床上机床参考点是离机床原点最远的极限点。
图18所示为数控车床的参考点与机床原点。
数控机床开机时,必须先确定机床原点,而确定机床原点的运动就是刀架返回参考点的操作,这样通过确认参考点,就确定了机床原点。
只有机床参考点被确认后,刀具(或工作台)移动才有基准。
二、编程坐标系
编程坐标系是编程人员根据零件图样及加工工艺等建立的坐标系。
编程坐标系一般供编程使用,确定编程坐标系时不必考虑工件毛坯在机床上的实际装夹位置。
编程原点是根据加工零件图样及加工工艺要求选定的编程坐标系的原点。
编程原点应尽量选择在零件的设计基准或工艺基准上,编程坐标系中各轴的方向应该与所使用的数控机床相应的坐标轴方向一致,如图9所示为车削零件的编程原点。
图9确定编程原点
三、加工坐标系
1、加工坐标系的确定
加工坐标系是指以确定的加工原点为基准所建立的坐标系。
加工原点也称为程序原点,是指零件被装夹好后,相应的编程原点在机床坐标系中的位置。
在加工过程中,数控机床是按照工件装夹好后所确定的加工原点位置和程序要求进行加工的。
编程人员在编制程序时,只要根据零件图样就可以选定编程原点、建立编程坐标系、计算坐标数值,而不必考虑工件毛坯装夹的实际位置。
对于加工人员来说,则应在装夹工件、调试程序时,将编程原点转换为加工原点,并确定加工原点的位置,在数控系统中给予设定(即给出原点设定值),设定加工坐标系后就可根据刀具当前位置,确定刀具起始点的坐标值。
在加工时,工件各尺寸的坐标值都是相对于加工原点而言的,这样数控机床才能按照准确的加工坐标系位置开始加工。
图1.12中O3为加工原点。
2、加工坐标系的设定
数控车床坐标系统分为机床坐标系和工件坐标系和编程坐标系。
无论哪种坐标系统都规定与车床主轴轴线平行的方向为Z轴,且规定从卡盘中心至尾座顶尖中心的方向为正)在水平面内与车床主轴轴线垂直的方向为X轴,且规定刀具远离主轴旋转中心的方向为正方向。
1.机床坐标系
以机床原点为坐标原点建立起来的x,z轴直角坐标系,称为机床坐标系。
机床坐标系是机床固有的坐标系,它是制造和调整机床的基础,也是设置工件坐标系的基础。
机床坐标系在出厂前已经调整好,一般情况下,不允许用户随意变动。
机床原点为机床上的一个固定的点。
车床的机床原点为主轴旋转中心与卡盘后的端面之交点(图中的O点)。
参考点也是机床上的一个固定点,该点是刀具退离到一个固定不变的极限点。
2.编程坐标系
在编写加工程序时使用的坐标系,一般是零件图上的设计基准。
3.工件坐标系
工件坐标系是加工时使用的坐标系,零件加工时,首先应该装夹好毛坯,然后在毛坯上确定工件坐标系和工件原点。
零件在设计中有设计基准。
加工坐标系应和设计基准重合,即工件坐标系和编程坐标系重合。
尽量将工艺基准与设计基准统一,该基准点通常称为工件原点。
三坐标系的关系:
作图表示。
3.工件坐标系设定
(1).执行G(50)X(α)Z(β)后,系统内部即对(α,β)进行记忆,并显示在显示器上,这就相当于在系统内部建立了一个以工件原点为坐标原点的工件坐标系。
同一工件由于工件原点变了,所以程序段中的坐标尺寸也随之改变。
因此,在编制加工程序前必须首先确定工件坐标系(编程坐标系)和工件原点(编程原点)。
(2).使用G54设定工件坐标系:
介绍具体操作方法与步骤。
第三讲数控车床加工工艺制定方法及步骤
——数控编程前必须做的事情
在数控车床上加工零件时,应该遵循如下原则:
一、选择适合在数控车床上加工的零件。
选择原则:
主要用于轴类和盘类回转体工件的加工,能自动完全内外圆面、柱面、锥面、圆弧、螺纹等工序的切削加工,并能进行切槽、钻、扩、铰孔等加工,适合复杂形状工件的加工。
与常规车床相比,数控车床还适合加工如下工件。
1、轮廓形状特别复杂或难于控制尺寸的回转体零件
2、精度要求高的零件
3、特殊的螺旋零件
如特大螺距(或导程)、变螺距、等螺距与变螺距或圆柱与圆锥螺旋面之间作平滑过渡的螺旋零件,以及高精度的模数螺旋零件和端面螺旋零件。
4、淬硬工件的加工
在大型模具加工中,有不少尺寸大而形状复杂的零件。
这些零件热处理后的变形量较大,磨削加工困难,可以用陶瓷车刀在数控机床上对淬硬后的零件进行车削加工,以车代磨,提高加工效率。
二、分析被加工零件图样,明确加工内容和技术要求。
1、零件图样尺寸的正确标注
2.保证基准统一的原则
3.分析材料、热处理、公差、技术要求等。
三、确定工件坐标系原点位置。
原点位置一般选择在工件右端面和主轴回转中心交点P,也可以设在主轴回转中心与工件左端面交点O上,如图1所示。
四、制定加工工艺路径,应该考虑加工起始点位置,起始点一般也作为加工结束的位置,起市点应便于检查和装夹工件;应该考虑粗车、半精车、精车路线,在保证零件加工精度和表面粗糙度的前提下,尽可能以最少的进给路线完成零件的加工,缩短单件的加工时间;应考虑换刀点的位置,换刀点是加工过程中刀架进行自动换刀的位置,换刀点位置的选择应考虑在换刀过程中不发生干涉现象,且换刀路线尽可能短,加工起始点和换刀点可选同一点或者不选同点
图1编程原点
五、选择切削参数。
在加工过程中,应根据零件精度要求选择合理的主轴转速、进给速度、和切削深度。
六、合理选择刀具。
根据加工的零件形状和表面精度要求,选择合适的刀具进行加工。
七、编制加工程序,调试加工程序,完成零件加工。
第四讲数控车床编程如何确定加工方案
(一)确定加工方案的原则
加工方案又称工艺方案,数控机床的加工方案包括制定工序、工步及走刀路线等内容。
在数控机床加工过程中,由于加工对象复杂多样,特别是轮廓曲线的形状及位置千变万化,加上材料不同、批量不同等多方面因素的影响,在对具体零件制定加工方案时,应该进行具体分析和区别对待,灵活处理。
只有这样,才能使所制定的加工方案合理,从而达到质量优、效率高和成本低的目的。
制定加工方案的一般原则为:
先粗后精,先近后远,先内后外,程序段最少,走刀路线最短以及特殊情况特殊处理。
(1)先粗后精
为了提高生产效率并保证零件的精加工质量,在切削加工时,应先安排粗加工工序,在较短的时间内,将精加工前大量的加工余量(如图3-4中的虚线内所示部分)去掉,同时尽量满足精加工的余量均匀性要求。
当粗加工工序安排完后,应接着安排换刀后进行的半精加工和精加工。
其中,安排半精加工的目的是,当粗加工后所留余量的均匀性满足不了精加工要求时,则可安排半精加工作为过渡性工序,以便使精加工余量小而均匀。
在安排可以一刀或多刀进行的精加工工序时,其零件的最终轮廓应由最后一刀连续加工而成。
这时,加工刀具的进退刀位置要考虑妥当,尽量不要在连续的轮廓中安排切人和切出或换刀及停顿,以免因切削力突然变化而造成弹性变形,致使光滑连接轮廓上产生表面划伤、形状突变或滞留刀痕等疵病。
(2)先近后远
这里所说的远与近,是按加工部位相对于对刀点的距离大小而言的。
在一般情况下,特别是在粗加工时,通常安排离对刀点近的部位先加工,离对刀点远的部位后加工,以便缩短刀具移动距离,减少空行程时间。
对于车削加工,先近后远有利于保持毛坯件或半成品件的刚性,改善其切削条件。
(3)先内后外
对既要加工内表面(内型、腔),又要加工外表面的零件,在制定其加工方案时,通常应安排先加工内型和内腔,后加工外表面。
这是因为控制内表面的尺寸和形状较困难,刀具刚性相应较差,刀尖(刃)的耐用度易受切削热影响而降低,以及在加工中清除切屑较困难等。
(4)走刀路线最短
确定走刀路线的工作重点,主要用于确定粗加工及空行程的走刀路线,因精加工切削过程的走刀路线基本上都是沿其零件轮廓顺序进行的。
走刀路线泛指刀具从对刀点(或机床固定原点)开始运动起,直至返回该点并结束加工程序所经过的路径,包括切削加工的路径及刀具引入、切出等非切削空行程。
在保证加工质量的前提下,使加工程序具有最短的走刀路线,不仅可以节省整个加工过程的执行时间,还能减少一些不必要的刀具消耗及机床进给机构滑动部件的磨损等。
优化工艺方案除了依靠大量的实践经验外,还应善于分析,必要时可辅以一些简单计算。
上述原则并不是一成不变的,对于某些特殊情况,则需要采取灵活可变的方案。
如有的工件就必须先精加工后粗加工,才能保证其加工精度与质量。
这些都有赖于编程者实际加工经验的不断积累与学习。
(二)加工路线与加工余量的关系
在数控车床还未达到普及使用的条件下,一般应把毛坯件上过多的余量,特别是含有锻、铸硬皮层的余量安排在普通车床上加工。
如必须用数控车床加工时,则要注意程序的灵活安排。
安排一些子程序对余量过多的部位先作一定的切削加工。
(1)对大余量毛坯进行阶梯切削时的加工路线
(2)分层切削时刀具的终止位置
(三)车螺纹时的主轴转速
数控车床加工螺纹时,因其传动链的改变,原则上其转速只要能保证主轴每转一周时,刀具沿主进给轴(多为Z轴)方向位移一个螺距即可,不应受到限制。
但数控车床加工螺纹时,会受到以下几方面的影响:
(1)螺纹加工程序段中指令的螺距(导程)值,相当于以进给量(mm/r)表示的进给速度F,如果将机床的主轴转速选择过高,其换算后的进给速度(mm/min)则必定大大超过正常值;
(2)刀具在其位移的始/终,都将受到伺服驱动系统升/降频率和数控装置插补运算速度的约束,由于升/降频特性满足不了加工需要等原因,则可能因主进给运动产生出的“超前”和“滞后”而导致部分螺牙的螺距不符合要求;
(3)车削螺纹必须通过主轴的同步运行功能而实现,即车削螺纹需要有主轴脉冲发生器(编码器)。
当其主轴转速选择过高,通过编码器发出的定位脉冲(即主轴每转一周时所发出的一个基准脉冲信号)将可能因“过冲”(特别是当编码器的质量不稳定时)而导致工件螺纹产生乱扣。
因此,车螺纹时,主轴转速的确定应遵循以下几个原则:
(1)在保证生产效率和正常切削的情况下,宜选择较低的主轴转速;
(2)当螺纹加工程序段中的导入长度δ1和切出长度δ2(如图所示)考虑比较充裕,即螺纹进给距离超过图样上规定螺纹的长度较大时,可选择适当高一些的主轴转速;
(3)当编码器所规定的允许工作转速超过机床所规定主轴的最大转速时,则可选择尽量高一些的主轴转速;
(4)通常情况下,车螺纹时的主轴转速(n螺)应按其机床或数控系统说明书中规定的计算式进行确定,其计算式多为:
n螺≤n允/L(r/min)式中n允—编码器允许的最高工作转速(r/min);
L—工件螺纹的螺距(或导程,mm)。
第五讲数控车床编程常用指令介绍
——F、S、T、M指令
一、数控车床编程要点
1、在一个程序段中,根据图样上标注的尺寸可以采用绝对值编程或增量值编程,也可以采用混合编程。
2、被加工零件的径向尺寸在图样上和测量时,一般用直径值表示,所以采用直径尺寸编程更为方便。
3、由于车削加工常用棒料作为毛坯,加工余量较大,为简化编程,常用采用不同形式的固定循环。
4、编程时,认为车刀刀尖是一个点,而实际上为了提高刀具寿命和工件表面质量,车刀刀尖常磨成一个半径不大的圆弧。
为提高工件的加工精度,编制圆头刀程序时,需要对刀具半径进行补偿。
使用刀具半径补偿后,编程时可直接按工件轮廓尺寸编程。
5、为了提高加工效率,车削加工的进刀与退刀都采用快速运动。
进刀时,尽量接近工件切削开始点,切削开始点的确定以不碰撞工件为原则。
二、F、S、T、M指令
1.F功能
F功能指令用于控制切削进给量。
在程序中,有两种使用方法。
(1)每转进给量
编程格式G95F~
F后面的数字表示的是主轴每转进给量,单位为mm/r。
例:
G95F0.2表示进给量为0.2mm/r。
(2)每分钟进给量
编程格式G94F~
F后面的数字表示的是每分钟进给量,单位为mm/min。
例:
G94F100表示进给量为100mm/min。
2.S功能
S功能指令用于控制主轴转速。
编程格式S~
S后面的数字表示主轴转速,单位为r/min。
在具有恒线速功能的机床上,S功能指令还有如下作用。
(1)最高转速限制
编程格式G50S~
S后面的数字表示的是最高转速:
r/min。
例:
G50S3000表示最高转速限制为3000r/min。
(2)恒线速控制
编程格式G96S~
S后面的数字表示的是恒定的线速度:
m/min。
例:
G96S150表示切削点线速度控制在150m/min。
(3)恒线速取消
编程格式G97S~
S后面的数字表示恒线速度控制取消后的主轴转速,如S未指定,将保留G96的最终值。
例:
G97S3000表示恒线速控制取消后主轴转速3000r/min。
3.T功能
T功能指令用于选择加工所用刀具。
编程格式T~
T后面通常有两位数表示所选择的刀具号码。
但也有T后面用四位数字,前两位是刀具号,后两位是刀具长度补偿号,又是刀尖圆弧半径补偿号。
例:
T0303表示选用3号刀及3号刀具长度补偿值和刀尖圆弧半径补偿值。
T0300表示取消刀具补偿。
4.M功能
M00:
程序暂停,可用NC启动命令(CYCLESTART)使程序继续运行;
M01:
计划暂停,与M00作用相似,但M01可以用机床“任选停止按钮”选择是否有效;
M03:
主轴顺时针旋转;
M04:
主轴逆时针旋转;
M05:
主轴旋转停止;
M08:
冷却液开;
M09:
冷却液关;
M30:
程序停止,程序复位到起始位置。
5.加工坐标系设置G50
编程格式G50X~Z~
式中X、Z的值是起刀点相对于加工原点的位置。
G50使用方法与G92类似。
在数控车床编程时,所有X坐标值均使用直径值,如图所示。
例:
按图设置加工坐标的程序段如下:
G50X128.7Z375.1
第六讲数控车床编程常用指令介绍
——G00、G01、G02指令
一.快速定位指令G00
G00指令命令机床以最快速度运动到下一个目标位置,运动过程中有加速和减速,该指令对运动轨迹没有要求。
其指令格式:
G00X(U)____Z(W)____;
当用绝对值编程时,X、Z后面的数值是目标位置在工件坐标系的坐标。
当用相对值编程时,U、W后面的数值则是现在点与目标点之间的距离与方向。
如图所示的定位指令如下:
G50X200.0Z263.0;设定工件坐标系
G00X40.0Z212.0;绝对值指令编程A→C
或G