煤制120万吨甲醇及转化烯烃项目工艺技术方案.docx
《煤制120万吨甲醇及转化烯烃项目工艺技术方案.docx》由会员分享,可在线阅读,更多相关《煤制120万吨甲醇及转化烯烃项目工艺技术方案.docx(45页珍藏版)》请在冰豆网上搜索。
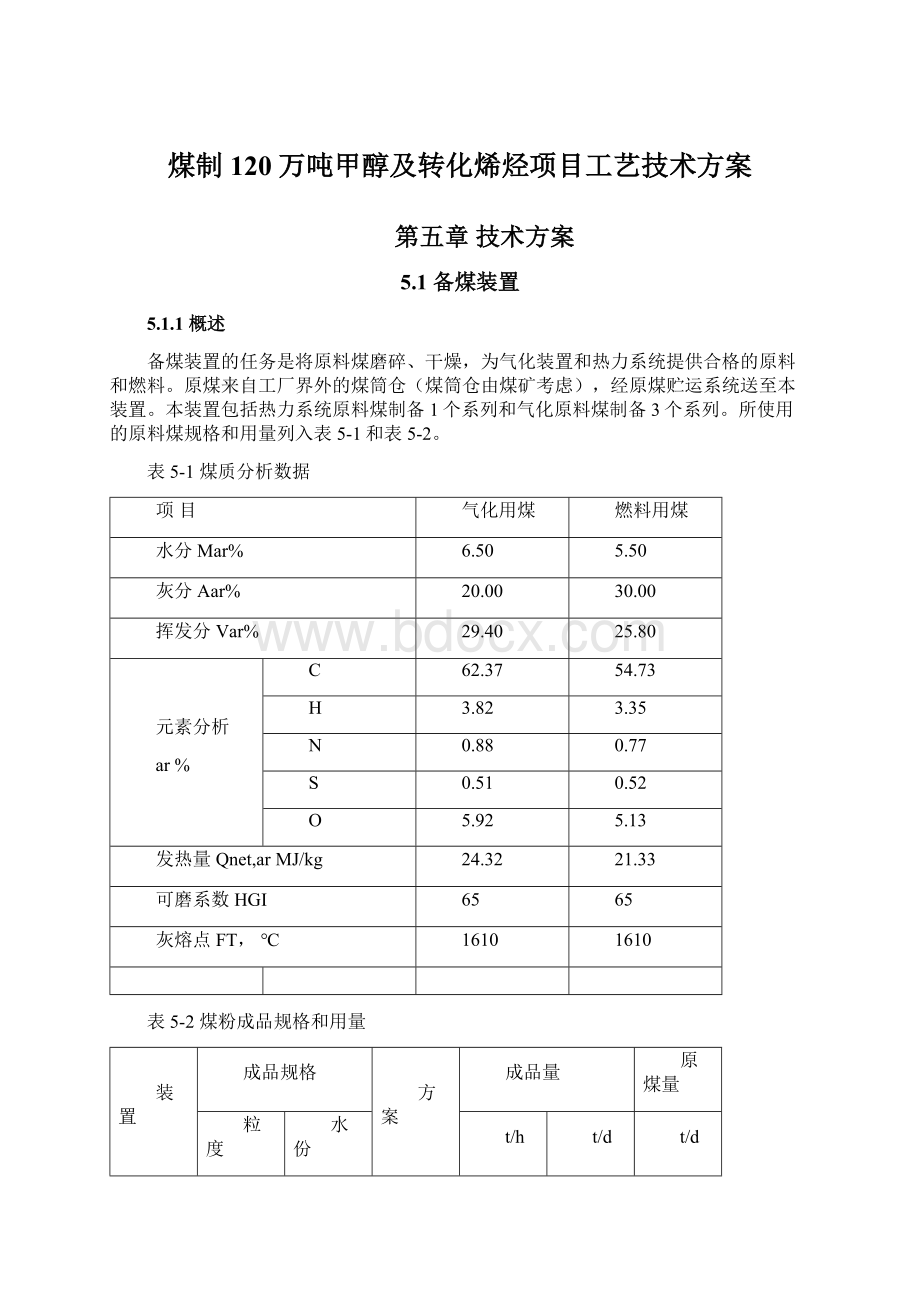
煤制120万吨甲醇及转化烯烃项目工艺技术方案
第五章技术方案
5.1备煤装置
5.1.1概述
备煤装置的任务是将原料煤磨碎、干燥,为气化装置和热力系统提供合格的原料和燃料。
原煤来自工厂界外的煤筒仓(煤筒仓由煤矿考虑),经原煤贮运系统送至本装置。
本装置包括热力系统原料煤制备1个系列和气化原料煤制备3个系列。
所使用的原料煤规格和用量列入表5-1和表5-2。
表5-1煤质分析数据
项目
气化用煤
燃料用煤
水分Mar%
6.50
5.50
灰分Aar%
20.00
30.00
挥发分Var%
29.40
25.80
元素分析
ar%
C
62.37
54.73
H
3.82
3.35
N
0.88
0.77
S
0.51
0.52
O
5.92
5.13
发热量Qnet,arMJ/kg
24.32
21.33
可磨系数HGI
65
65
灰熔点FT,℃
1610
1610
表5-2煤粉成品规格和用量
装置
成品规格
方案
成品量
原煤量
粒度
水份
t/h
t/d
t/d
气化
>94%<250µm
100%<500µm
<2%
方案Ⅰ
209
5010
5251
方案Ⅱ
209
5010
5251
热力
<13mm
方案Ⅰ
167
4013
4013
方案Ⅱ
167
4013
4013
5.1.2工艺技术方案选择
国内外常采用的煤制备流程有中间贮仓式和直吹式两种流程。
采用的磨煤机有以下3种形式:
●低速磨即钢球磨煤机,适用煤种广泛。
一般适用于中、小规模。
●中速磨即辊盘式磨煤机,也称立式磨,适用于磨损性较强的烟煤、贫煤和褐煤,最适宜原煤水分在25%以下,HGI指数在35~100的煤种。
●高速磨如风扇磨,适用于高水分、低灰分、磨损性不强的褐煤。
由于中速磨具有适用性广、能耗低、钢耗低、检修方便、噪音低等特点,因而得到广泛的应用。
不仅在大中型电站,而且在冶金、建材、化工等行业都采用中速磨煤。
我国已有北京、上海、沈阳引进国外技术形成系列生产,并且使用情况良好。
(1)煤粉制备系统型式
本项目气化装置使用GSP粉煤加压气化工艺技术,煤粉需用高压CO2输送,需设置粉煤加压筒仓,因此,煤粉制备系统采用中间贮仓式。
(2)磨机形式
采用辊盘式中速磨煤机。
(3)干燥热源
根据原煤挥发分高、易燃易爆的特点,干燥介质以热风炉烟气为主,并补充部分氮气以控制氧含量,并采用氮气作为系统的消防用气,确保系统安全。
为减少煤尘排放量,节约能耗,干燥热风大部分循环使用,部分排放,以平衡系统的湿含量。
干燥用热风可由燃煤热风炉、燃气热风炉或全厂锅炉提供,三种方案比较见表5-3。
表5-3备煤装置干燥方案比较
项目
燃气热风炉
燃煤热风炉
锅炉烟道气
燃料种类
燃料气
煤粉
450℃烟道气
主要设备配置
燃气热风炉
燃煤热风炉
热烟气鼓风机
电消耗
电耗最低
电耗低
电耗高
工艺流程
简单
复杂
最简单
设备台数
台数少
台数多
台数少
占地面积
占地面积小
占地面积大
烟气管道占地面积大
操作条件
操作条件好
操作条件差
操作条件好
废渣排放
无废渣排放
有废渣排放
不增加废渣排放
对煤粉质量影响
无影响
烟气中灰分会增加煤粉中灰分含量
烟气中灰分会增加煤粉中灰分含量
技术复杂程度
不复杂
较复杂
高温大风量高压头风机难以解决
开车情况
工厂开车时无副产燃料气提供。
为运行,备煤装置开车需用燃料油。
工厂开车时,运行备煤装置,直接用燃料煤。
工厂开车时,因先启动锅炉系统,运行备煤装置,直接用锅炉烟道气。
从表5-3可以看出,燃气热风炉方案流程紧凑,设备少、投资低、生产管理方便、对环境污染少,燃料气的烟气对煤粉的污染轻。
燃煤热风炉方案流程复杂、设备多、投资高、生产卫生及操作条件较差,烟尘混入煤粉中将提高其灰分含量。
锅炉烟道气方案存在高温大风量高压头风机难以解决的技术难题,大直径烟道气管道布置也存在困难。
而本项目后续合成工艺将产生燃料尾气,正好可用作热风炉燃料,因此,本报告推荐采用燃气热风炉方案。
(4)煤粉分离收集方式
国内过去常采用多细粉分离器加多管旋风、袋式收尘器的多级收尘方式,系统流程长、设备多、阻力大、运行故障多、尾气往往难以达到排放标准,现已逐步改进为大型长袋低压喷吹式收尘器一级分离收尘的方式,流程大为简化,设备少、阻力降低、运行故障少,可以保证尾气达到国家排放标准。
该项技术在消化吸收的基础上已日臻成熟,已在各行业推广应用。
本报告推荐采用大型长袋低压喷吹袋式收尘器,一级分离收尘技术。
(5)煤粉的贮存和输送
本项目成品煤粉含水量为<2%,为防止煤粉结拱堵塞,拟采用如下贮存和输送技术方案:
煤粉贮仓、溜管、输送设备均保温伴热,防止结露。
煤粉贮仓锥底出口附近加气流板充N2气流化助流。
气化炉操作压力高,气化用煤粉采用高压CO2气密相输送,输送比400kg/m3。
(6)备煤装置的系列配置和磨机的设置
备煤装置的系列配置和磨机设置基于下述三个方面:
备煤装置两个煤制备系统的系列数与下游气化装置和热力系统的系列数相对应,以便于操作和管理。
磨机能力适当留有富裕量,并设置备用机,以保证工艺生产正常。
为此,气化原料煤制备设置3系列生产线,热力系统原料煤制备设置1个系列。
按照单系列的处理能力,气化原料煤制备系统每个系列设置1台磨机。
5.1.3工艺说明
气化用的原煤由原煤贮运系统的带式输送机送入磨机前碎煤仓中,通过称重给煤机加到辊盘式中速磨中磨粉,从燃气热风炉送来的烟道气与循环气在混合器中混合,用调温风机送来的冷空气将热风调配到需要的温度后,热风送入中速磨将磨粉干燥,合格的煤粉吹入煤粉袋滤器中,分离下来的煤粉经袋滤器排粉螺旋、排粉旋转给料阀、螺旋输送机送入煤粉仓中,煤粉仓可贮存15h用量的煤粉。
经分离后的尾气经循环风机加压后,部分循环至混合器,部分排入大气,排入大气中的尾气量根据煤的湿含量平衡通过比例调节器控制。
干燥后的煤粉通过系列输送系统送至气化炉,输送系统主要由煤粉给料斗、煤粉锁斗、高压煤粉发送斗和煤粉输送管组成。
在煤粉锁斗处于常压状态时,打开上阀使煤粉给料斗中的煤粉通过旋转给料器流入锁斗,料满后关闭上阀,通入高压N2加压至4.5MPa后,打开下阀使煤粉自流进入高压煤粉发送斗,卸完后关闭下阀,排出N2降至常压再重复上述过程。
高压给煤斗可贮存0.5h用量煤粉。
高压煤粉仓中的煤粉用高压CO2经管道送往气化炉顶部喷嘴。
煤粉仓排出的气体、锁斗中排出的气体及给煤斗排出的气体经煤斗仓顶过滤器收尘后排入大气。
分离下来的煤粉经袋滤器排粉螺旋排入煤粉仓。
碎煤仓设有仓顶袋滤器和排风风机,所有袋滤器均采用N2喷吹清灰。
中速磨配备有密封风机和润滑、液压系统,并设置了设备检修用悬挂起重机,整个系统消防用气及助流流化用气均采用N2。
5.1.4主要设备选择
气化装置用原料煤磨煤机选用ZGM113G辊盘式中速磨煤机,配置4台,3开1备。
磨机数量计算如下:
表5-4磨机数量设计
序号
项目
单位
气化原料煤制备系统
1
单台磨机处理能力
t/h
85
2
系统磨机数量
t/h
4(3开1备)
3
系统磨机处理能力
t/h
255
4
系统正常处理量
t/h
227
煤粉袋式收尘器选用国内开发的长袋低压大型脉冲喷吹高浓度煤粉袋式收尘器,过滤气速1m/min,进口含尘浓度小于1000g/Nm3,排出口含尘浓度小于10mg/Nm3。
除气化装置用的煤粉贮仓锁斗的进出口阀门需要进口外,本装置的其他设备及其辅助设备均为国产。
5.2空分
5.2.1概述
空分装置的作用是为气化装置提供所需的氧气和输送煤粉用的高压氮气以及公用工程所需的低压氮气。
本装置的主要产品为:
表5-5空分装置产品一览表
名称
规格
单位
流量
用户
氧气
纯度:
99.6%
压力:
4.8MPa
Nm3/h
112094
煤气化装置
高压氮气
纯度:
99.99%
压力:
5.5MPa
Nm3/h
263
备煤和气化装置
低压氮气
纯度:
99.99%
压力:
0.6MPa
Nm3/h
10506
备煤装置
低压氮气
纯度:
99.99%
压力:
0.6MPa
Nm3/h
7128
酸性气体脱除
本装置采用3套制氧能力为40000Nm3/h的空分设备以与气化装置3个系列3台气化炉相匹配,总的供氧能力为120000Nm3/h。
5.2.2工艺技术方案选择
空分技术经过多年的不断发展,现在已步入大型全低压流程的阶段,能耗不断降低。
大型全低压空分装置整个流程由空气压缩、空气预冷、空气净化、空气分离、产品输送所组成,其特点是:
(1)采用高效的两级精馏制取高纯度的氧气和氮气。
(2)采用增压透平膨胀机,利用气体膨胀的输出功直接带动增压风机以节省能耗,提高制冷量。
(3)热交换器采用高效的铝板翅式换热器,结构紧凑,传热效率高。
(4)采用分子筛净化空气,具有流程简单、操作简便、运行稳定、安全可靠等优点,大大延长装置的连续运转周期。
由于产品氧气的用户对氧气的压力有一定要求,纯氧又是一种强氧化介质,氧气的增压工艺常常成为研究的一个重点。
氧气的增压有两种方式,即采用氧气压缩机和液氧泵,前者压缩介质为气氧,在冷箱外压缩;后者压缩介质为液氧,在冷箱内压缩,分别称为外增压流程和内增压流程。
最近制造厂又推出双泵内增压流程,即根据用户对高压氧气、高压氮气的要求,分别用液氧泵、液氮泵在冷箱内压缩气化后输出,其显著优点是投资省、维修费用低、安全可靠性高。
我国的空分制造厂与拥有世界一流技术的德国林德(LINDE)公司、美国空气产品和化学品公司(APCI)、法国空气液化公司等都建立了技术合作关系,能合作制造大型空分设备。
本项目气化装置要求使用纯度为99.6%,压力为4.8MPa的氧气,氧量为112094Nm3/h,,具有气用量大、压力高的特点。
因此本研究需要对空分装置的氧气增压流程和装置的系列数作出选择。
从能耗上看,相同制氧能力的空分装置,采用内压缩流程和外压缩流程的实际功耗相近。
因为,尽管内增压流程使用了空气增压机来提供系统的部分制冷量,多压缩了氮气,理论上要多消耗了压缩功,但是空气增压机的效率比氧压机高,氧压机实际运行往往偏离其设计工况,两者实际的功耗是很接近的。
从安全方面分析,尽管外增压流程的使用也比较普遍,氧气压缩机的设计和制造水平不断提高,但是统计数据表明,国内用户使用的氧压机(包括进口氧压机)有多台次发生过燃烧事故,而内增压流程从未出现过类似事故。
从投资上看,两种流程相接近,内增压流程稍低一些。
此外,使用液氧泵的内增压流程比使用氧压机的外增压流程操作、管理更为方便,维修工作量少,占地也少。
因此,本研究推荐内增压流程。
本项目的气化装置采用3系列3台气化炉并联运行,为了便于装置的运行和管理,并尽量节约投资,本研究推荐采用3系列3套40000Nm3/h空分装置并联运行的方式。
目前国产40000Nm3/h空分装置运行良好,并正在建设50000Nm3/h级装置,因此建议采用国内厂家的空分设备。
5.2.3工艺说明
从大气吸入的空气经空气过滤器滤去灰尘与机械杂质后,入空气压缩机加压至0.67MPa,然后进入空气冷却塔。
空气在空冷塔下段与被污氮冷却的循环冷却水逆流接触而降温。
然后通过上段与经液氨冷却的冷冻水逆流接触,降温到12℃入分子筛吸附器,清除空气中的水份、二氧化碳和碳氢化合物。
净化空气分成二股:
一股直接进入冷箱经主换热器被冷却至接近露点,入精馏塔下塔进行预分离,另一股导入增压机,入增压机的空气又被分为二股:
一股从增压机的中间级抽出,在高压氮换热器中冷却液化,然后通过节流降压而补充装置运行所需的冷量;其余的从增压机的最终级压出,再分为二路:
一路通过高压氮换热器的上半段冷却后,入膨胀机进行绝热膨胀制冷,然后导入下塔;另一路通过膨胀机的增压透平进一步升压后与高压液氧(一部分与高压液氮)换热而液化,然后节流降压,节流后的气体并入下塔,液体空气直接导入上塔分离或一部分先入下塔预分离。
从精馏塔上塔底部抽出液氧,由液氧泵加压至5.0MPa,复热气化后出冷箱,作为产品氧气送气化装置。
从主冷凝器抽取液氮,经液氮泵加压至6.0MPa,复热气化后出冷箱,去备煤装置输送煤粉用。
由下塔顶部抽出0.6MPa气氮,经主换热器复热后出冷箱,一部分供备煤装置干燥系统用氮,一部分供酸性气体脱除装置用氮,剩余部分供给公用工程用户。
上塔顶部引出的不纯氮气经换热器复热后出冷箱。
由于其干燥无水,一部分作为分子筛再生用氮,一部分入水冷却塔,通过气提使循环冷却水得到冷却;剩余部分送仪表空压站作气源。
5.3煤气化技术
本装置是将原料煤通过煤气化炉,获取以合成气(CO+H2)为主要成分的煤气,装置日处理煤量为5010t,由3台日处理煤量2000t的气化炉组成,设置3个系列,每个系列1台,采用未来能源公司(FUTUREENERGYGmbH,简称FE)的GSP加压粉煤气化技术。
5.3.1煤气化工艺技术选择
现代先进的煤气化技术主要包括:
德国未来能源公司的GSP粉煤加压气化技术、荷兰Shell公司的SCGP粉煤加压气化工艺、美国Texaco公司的水煤浆加压气化工艺、美国CococoPhillips公司的E-gas两段水煤浆加压气化工艺、德国Lurgi公司的Lurgi块煤加压气化工艺和德国的HTW流化床气化工艺。
在水煤浆加压气化工艺中,E-gas工艺的技术指标较好,但操作经验较少,商业应用不多。
Texaco工艺近十年来在中国的化肥和甲醇工业中有四套商业应用的业绩,另有几套装置在建设中。
Lurgi工艺是最早工业化的加压气化工艺,是一种固定床块煤气化工艺。
Lurgi工艺以块煤为原料(粒度6mm~50mm),适用于不粘结或弱粘结性和灰熔点较高的褐煤和活性好的次烟煤煤种。
世界上使用Lurgi工艺的工业装置较多,操作经验比较丰富,氧气消耗较低;但煤气中CH4含量高(约10%,干基),有效气体(CO+H2)含量相对较低,比较适合于城市煤气的生产或多联产系统。
Lurgi工艺副产的煤气水中焦油及酚含量高,污水处理较为复杂。
国内有两家化肥厂和两家城市煤气厂采用此工艺技术。
Shell公司的SCGP工艺和FE公司的GSP工艺都是干煤粉加压气流床气化工艺,是最先进的煤气化工艺之一,二者均已被成功地用于联合循环发电工厂或甲醇联产的商业运营,同时这两种工艺在国内的商业装置也正在兴建或引进中。
流化床气化技术在德国已得到工业应用,在朝鲜、印度也有长期的运行经验。
美国的U-Gas、KRW等技术在气化炉排灰含碳、飞灰循环等方面取得了实际进展,但最成熟的还是德国的HTW工艺技术。
目前国际上技术比较成熟,工艺指标比较先进、业绩较多的GSP工艺、SCGP工艺、HTW工艺、Lurgi工艺和Texaco工艺的比较见表5-6。
表5-6煤气化工艺比较
序号
项目
GSP粉煤
气化
Shell粉煤
气化
Texaco水煤浆
气化
HTW流化床
气化
Lurgi块煤
气化
1
气化工艺
气流床、液态排渣
气流床、液态排渣
气流床、液态排渣
流化床、固态排渣
固定床、固态排渣
2
适用煤种
褐煤、次烟煤、烟煤、无烟煤、油渣等
褐煤、次烟煤、烟煤、无烟煤、油渣等
次烟煤、烟煤、油渣等
次烟煤、烟煤、油渣等
褐煤、次烟煤、无烟煤等
3
气化压力(MPa)
2.0~4.0
2.0~4.0
4.0~6.5
1.0~2.5
2.0~3.2
4
气化温度(℃)
1400~1600
1400~1600
1300~1400
950~1100
950~1250
5
单炉最大处理能力(t/d)
2500
2500
2000
2000
1000~1300
6
1000Nm3有效气耗氧量,(Nm3)
330~360
330~360
380~430
260~340
267~350
7
碳转化率,(%)
99
99
96~98
90~95
88~95
8
冷煤气效率,(%)
78~83
78~83
70~76
68~75
65~75
9
有效气含量,(%)
~90
90~94
~80
70~80
~65
10
总热效率,(%)
90(激冷流程)
98(废锅流程)
90~95
95
80~90
11
操作弹性,(%)
50~130
50~130
70~110
70~110
30~110
12
技术成熟度
高
高
高
高
高
13
建厂投资
较低
较高
较低
低
低
因本项目所使用的原料煤属气煤或1/3焦煤,具有一定的粘结性,不适宜Lurgi炉操作,同时Lurgi工艺受原料粒度的限制、合成气产率较低、气化副产物处理复杂等不利因素,在此不适于采用,因此,只将GSP工艺、SCGP工艺、HTW工艺和Texaco工艺比较说明如下:
(1)HTW流化床气化工艺
HTW流化床气化工艺由德国Rheinbraun-AG(
RWE-Group)开发,
是在常压温克勒气化工艺的基础上改进开发的,主要提高了气化炉操作的温度和压力,主要适合于褐煤气化,其在Wesseling
示范厂最大规模已达到1500t/d,高效而且成本低廉。
其主要特点如下:
直接以粉煤为原料,一般入炉原料煤粒度为0mm~10mm,原料易得,制备简单。
适应煤种范围宽,除一般用于气化的非粘结性煤种,如褐煤、长焰煤、次烟煤等化学活性高的煤种外,经适当处理也可气化具有一定粘结性的煤种。
气化强度高,流化床气化炉的气化强度为等规模固定床气化炉的3倍~4倍,加压气化能改善流态化操作,同时显著提高气化强度。
环境特性好,煤快速干馏,挥发物被充分裂解,因而气化过程不产生焦油类物质,煤气冷凝液中的有机物质较少,净化系统简单。
气化炉在1000℃左右的操作温度下进行气化,对设备、材质无苛刻要求,过程控制及设备可立足国内。
煤气离开流化床气化炉时夹带较多飞灰,且含碳量较高,需进行适当处理。
(2)Texaco水煤浆气化工艺
Texaco公司在渣油部分氧化技术基础上开发出水煤浆气化技术,1978年首次推出此气化工艺。
过去十多年中,在美国、日本和中国相继建成多套生产装置,取得了一定的运行经验。
其主要特点如下:
煤种适应性较强。
各种烟煤和石油焦均能使用,主要以年轻的烟煤为主,对煤的粘结性、热稳定性没有严格的限制。
根据国内运行经验,为保证装置长期稳定操作,气化用煤的灰熔点FT宜低于1350℃,煤的灰份含量最好不超过13%,最高内水分不超过8%,操作温度下的灰渣粘度控制在20Pa·s~30Pa·s时,更有利于操作。
气化压力高。
水煤浆气化压力范围在4.0MPa~6.5MPa之间,提高气化压力,可缩小设备体积,有利于降低能耗。
气化技术成熟。
制备的水煤浆用泵输送,操作安全,便于计量。
气化炉内砌有多层耐火砖,无机械部件,气化装置通常设置备用系列,以提高年运转率,料浆喷嘴和耐火砖磨损消耗高,运行成本较高。
煤气中有效气(CO+H2)较高约80%,冷煤气效率为70%~76%,由于水煤浆含有约35%水分,因而氧耗较高。
气化流程的热回收有激冷和废锅两种形式,可根据产品气的用途加以选择。
气化炉高温排出的融渣,冷却粒化后,性质稳定,可作水泥等建筑材料,排水中不含焦油、酚等污染物,经过处理后可以循环使用或达标后排放。
为保证生产的连续运转,一般需设置备用气化炉。
(3)SCGP气化工艺
Shell公司在渣油气化技术取得工业化成功经验的基础上,于1972年开始从事煤气化的研究。
1978年第一套中试装置在德国汉堡建成并投入运行。
1987年在美国休斯敦附近的日投煤量250t~400t示范装置建成投产。
1993年在荷兰Buggenum的日投煤量2000t的大型商业用气化装置建成投产,用于联合循环发电。
目前正在中国洞庭化肥厂建设一座日处理2000t煤的气化装置,预计2005年建成投产。
其他十多套装置也在建设或设计中。
该气化装置为单系列操作,装置的开工率在90%以上。
这些装置的生产实践证明,SCGP气化技术是先进可靠的。
其主要特点如下:
对气化原料有较宽的适应性,固体原料中的褐煤、烟煤、无烟煤和石油焦均可气化,对煤的活性没有要求,对煤的灰熔点适应范围比其它气化工艺可以更宽。
对于高灰份、高水份、含硫量高的煤种也同样适应。
气化温度约1400℃~1600℃,碳转化率高达99%以上,产品气体洁净,不含重烃,甲烷含量极低,煤气中有效气体(CO+H2)达到90%以上,从而降低了煤的耗量。
由于是干法进料,与水煤浆气化工艺相比,氧耗降低15%~25%,因而与之配套的空分装置规模可减少,投资降低。
单炉生产能力大,目前已投入运转的气化炉气化压力为3.0MPa,单台炉日处理煤量已达2000t~2500t,更大规模装置已能设计。
热效率高,冷煤气效率78%~83%。
其余15%~20%热能被回收为中压或高压蒸汽,气化总的热效率约为98%。
气化炉采用竖管水冷壁结构,无耐火砖衬里,设备维护量较少。
气化炉内也无转动部件,运转周期长,生产装置无需配置备用炉。
气化炉烧嘴及控制系统安全可靠。
Shell公司气化烧嘴设计寿命为8000小时,Demkolec电厂使用烧嘴4年未出现问题。
气化操作采用先进的控制系统,设有必要的安全联锁,使气化操作处于最佳状态下运行。
炉渣可用作水泥渗合剂或道路的建筑材料。
气化炉高温排出的熔渣经激冷后成玻璃状颗粒,性质稳定,对环境几乎没有影响。
气化污水量少,有害组份较低,容易处理,可达标排放。
(4)GSP干煤粉气化工艺
GSP加压气流床气化技术是由前东德的德意志燃料研究所开发,始于上世纪70年代末。
最初的目的是用高灰分褐煤生产民用煤气,并在弗来堡(Freiburg)建立了一套3MW中试装置。
80年代初,在黑水泵电厂建立了一套130MW商业化装置,原料处理能力为30t/h,84年建成并投入运行,该装置运行了10年而气化炉的喷嘴和水冷壁仍可使用。
该工艺在1991到2002年随产权公司的变更,至2002年由FE公司所有。
GSP工艺已经过多年大型装置的运行,已先后气化了80余种原料,不仅可以气化高硫、高灰等劣质煤,而且可以气化工业废料、生物质等,煤气中CH4含量很低,很适合生产合成气,气化过程简单,气化炉装置生产能力大,装置的开工率在95%以上。
这些装置的生产实践证明,GSP气化技术是先进可靠的。
目前国内已有多家企业对GSP技术接触。
其主要特点如下:
对气化原料有较宽的适应性,且可同时气化固体原料和液体原料。
固体原料中的褐煤、烟煤、无烟煤和石油焦均可气化,对煤的活性没有要求,对煤的灰熔点适应范围比其它气化工艺可以更宽。
对于高灰份、高水份、含硫量高的煤种也同样适应。
气化温度约1400℃~1600℃,碳转化率高达99%以上,产品气体洁净,不含重烃,甲烷含量极低,煤气中有效气体(CO+H2)达到90%以上,从而降低了煤的耗量。
由于是干法进料,与水煤浆气化工艺相比,氧耗降低15%~25%,因而配套之空分装置规模可减少,投资降低。
单炉生产能力大,目前已投入运转的气化炉气化压力